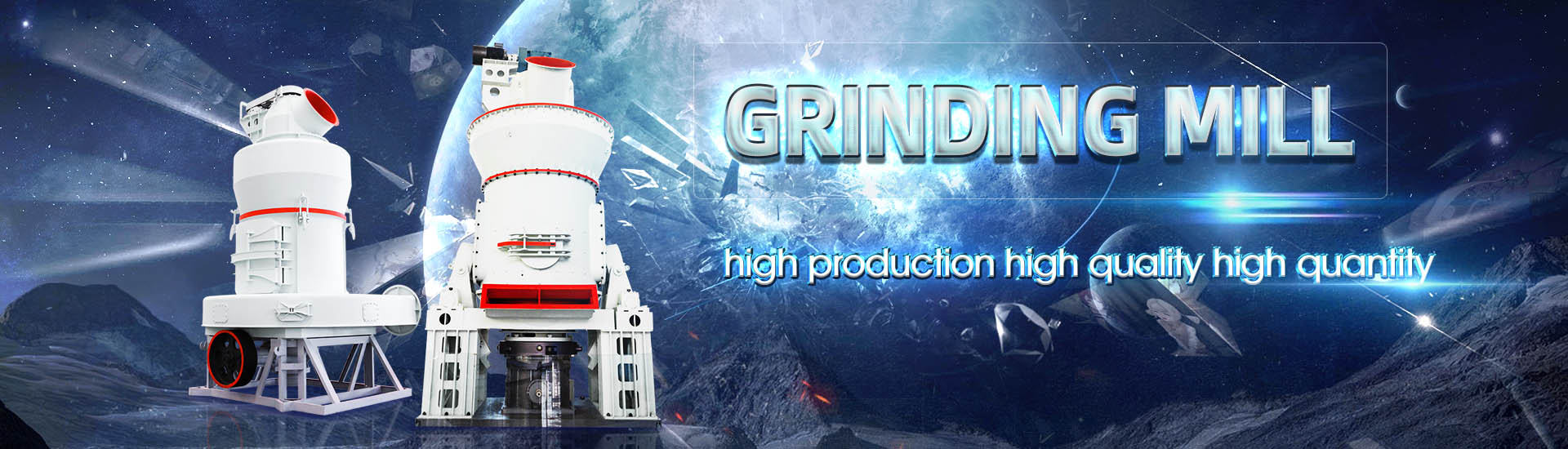
Iron separation from slag
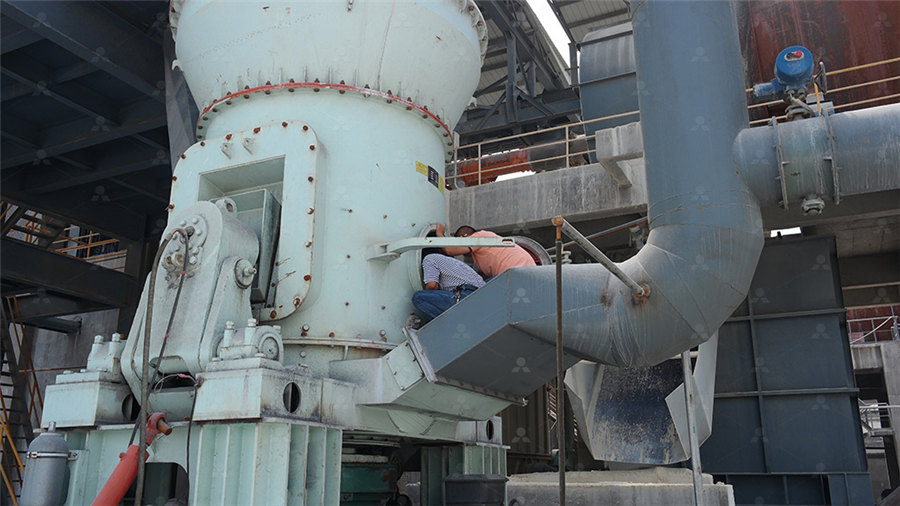
Extraction and separation of copper and iron from copper
2022年9月25日 In this study, a variety of methods for extracting and separating copper and iron from CSS are reported The extraction and separation technologies include physical methods 2014年1月10日 High grade iron compounds are obtained by dry and wet magnetic separations A representative sample of LD slag provided from French steel industry was treated by Recovery of high grade iron compounds from LD slag by2023年2月1日 Basic oxygen furnace (BOF) slag contains a significant amount of ironcontaining species, which is considered to be iron resources and therefore need to be recovered In this Efficient separation of iron elements from steel slag based on 2022年4月11日 At present, there are two common methods for recovering iron and iron oxides from BOF slag: reduction and oxidation The reduction method is mainly to reduce the ironcontaining oxides in the BOF slag to metallic iron, Optimization of Iron Recovery from BOF Slag by
.jpg)
Optimization of magnetic separation process for iron recovery
2017年2月1日 To improve the efficiency of iron recovery from steel slag and reduce the wearandtear on facilities, a new method was proposed by adding a secondary screen sizer to the method to separate and recover iron from steel slag After magnetic separation, the recovered magnetic iron (MFe) particles can be fed back to BOF , E AF or sintering plants for blast Optimization of magnetic separation process for iron recovery 2017年2月1日 Recovering iron and aluminum efficiently is the key route to utilize lowgrade highiron bauxite Aiming to optimize the iron separating process and elevate both Fe and Al Optimization of magnetic separation process for iron recovery 2020年10月31日 At present, the mainstream iron recovery processes from copper slag mainly include the hydrometallurgy route [21], smelting iron alloy [22], and direct reduction (DR) process [23] However, it is inefficient to utilize Recovery of Iron from Copper Slag Using CoalBased
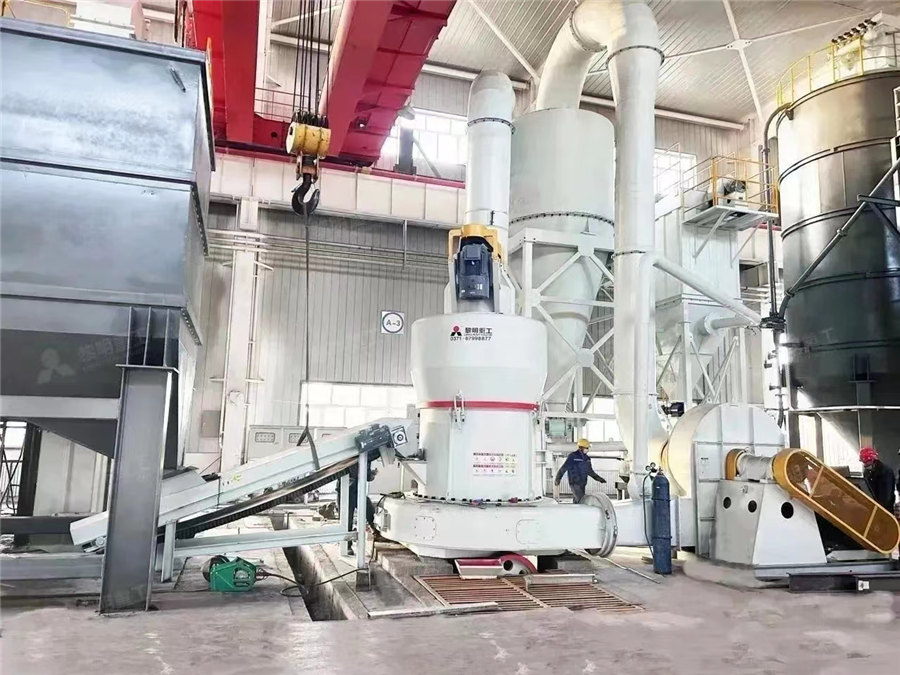
Optimization of magnetic separation process for iron recovery
DOI: 101016/S1006706X(17)300237 Corpus ID: ; Optimization of magnetic separation process for iron recovery from steel slag @article{Lan2017OptimizationOM, title={Optimization of magnetic separation process for iron recovery from steel slag}, author={Yuanpei Lan and Qingcai Liu and Fei Meng and Deliang Niu and Heng Zhao}, 2022年1月13日 The electric arc furnace (EAF) smelting ilmenite concentrate process which produces titania slag, is high energy consumption, high pollution, and low efficiency process An economical and clean process for semimolten reduction followed by magnetic separation to produce titania slag from Panzhihua ilmenite concentrate is proposed In the present study, Recovery of Titania Slag and Iron from Semimolten State 2024年7月16日 The electric arc furnace steelmaking route is essential for sustainable steelmaking through hydrogenbased direct reduced iron About 30% of the global steel production currently follows the scrap/direct reduced iron–electric arc furnace (DRIEAF) route, which is bound to increase given decarburization efforts by the steel industry We investigated Enhancing Recycling Potential: Exploring Reduction and Metal Separation 2024年7月18日 In the current study, the selective reduction and magnetic separation technique was adopted to recover iron from copper slag Calcium salts were used as an additive because studies reported that iron in the slag is difficult to reduce via the reduction method and it is mainly present in the form of Fe 2 SiO 4 in slag; that is why in order to enhance the recovery of iron A novel approach for recovery of iron from copper slag using
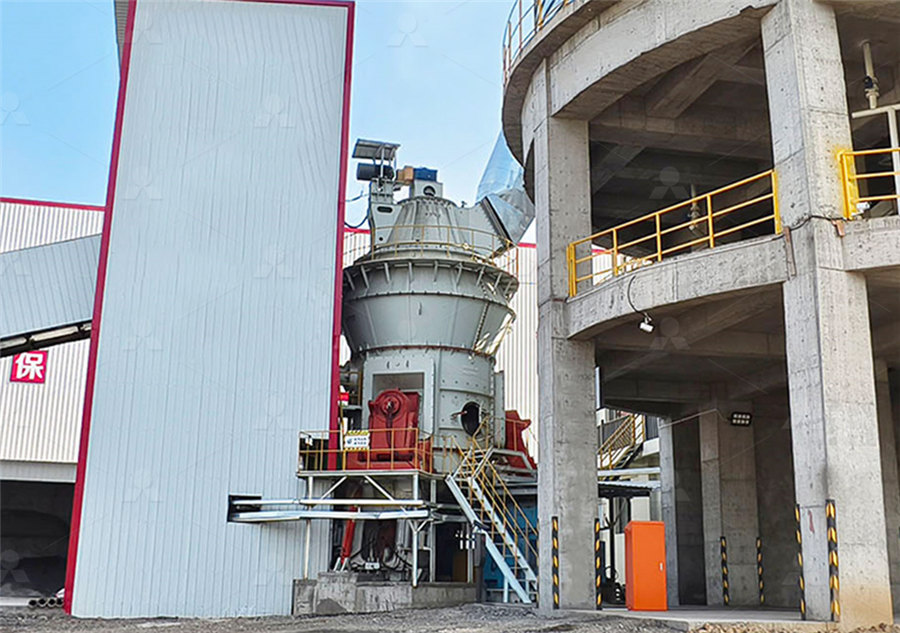
Efficient Separation and Recovery of Vanadium, Titanium, Iron
2022年1月22日 The dumping of a large amount of steel slag not only wastes metal resources, but pollutes the ecological environment In this study, a method for recovery of vanadium, titanium, iron, magnesium, and synthesizing anhydrite from steel slag is proposed The leaching efficiency of V, Ti, Fe, and Mg was 9942%, 9936%, 9989%, and 9995%, respectively, under DOI: 101016/jjmrt202301186 Corpus ID: ; Efficient separation of iron elements from steel slag based on magnetic separation process @article{Liu2023EfficientSO, title={Efficient separation of iron elements from steel slag based on magnetic separation process}, author={Xin Liu and Dazhi Wang and Zhiwei Li and Wei Ouyang and Yanping Bao and Chao Gu}, Efficient separation of iron elements from steel slag based on In order to recycle iron from copper slag with total iron content(TFe) of 3996%(mass fraction),a technique with lignitebased direct reduction followed by magnetic separation was presentedAfter analysis of chemical composition and crystalline phase,according to experimental mechanism,the tests for studying the effects of different parameters on the recovery of iron were carried Iron recovery from copperslag with lignitebased direct reduction 2022年4月27日 Compared with the initial steel slag, the iron grade increased by 822%, and the iron recovery increased by 4638% compared with direct magnetic separation without oxidation [13](PDF) Optimization of Iron Recovery from BOF Slag by
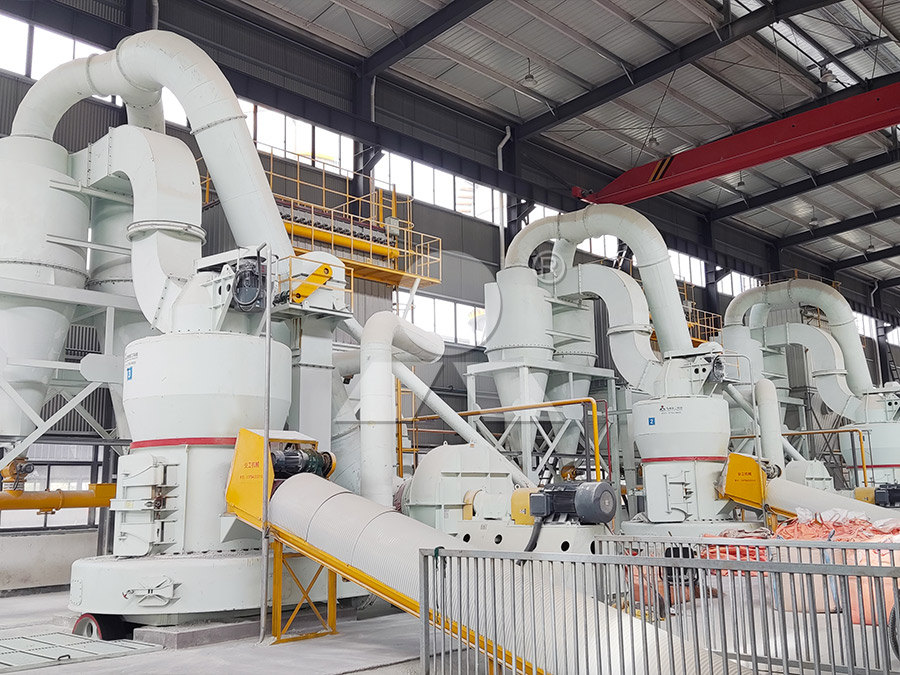
The potential utilization of slag generated from iron and
2019年10月29日 Slag is the byproduct of iron and steelmaking processes Normally, around half to one tonne of slag would be generated for yielding one tonne of rolled iron or steel (Lobato et al 2015)It was reported that the world steel production was 19 billion tonnes in 2016, which suggested that at least around 1 billion tonnes of slag is produced during the year (Worldsteel 2022年5月1日 Abstract Considering the BSSF steelmaking slag generated in a Brazilian steelwork, it would be worth to separate iron and calcium from it, with the objective of increasing its iron content, or Separation of Iron and Calcium from a BSSF Steelmaking Slag 2021年2月20日 The particle size of metallic iron can be increased by adding fluxes, such as CaO and Na 2 CO 3, during carbothermal reduction, thereby favoring the increase of the Fe content in concentrate by grinding–magnetic separation8, 12,13,14,15,16,17 Recent studies on iron recovery from reductively roasted copper slag by grinding–magnetic separation are Liberation and Enrichment of Metallic Iron from Reductively 2022年3月8日 In this work, a new and carbonfree reductant, ie, secondary aluminum dross, is used to replace coal to recycle valuable metals from copper slag by smelting reduction The influence of substitution ratio on slag properties and metal recovery was investigated The results show that the metal recovery is mainly determined by the settlement of the generated metals Iron Recovery from Waste Copper Slag by Using Coal and
.jpg)
Separation of cobalt from slag of nickel pig iron using solvent
DOI: 101063/5 Corpus ID: ; Separation of cobalt from slag of nickel pig iron using solvent extraction method @article{Sudibyo2021SeparationOC, title={Separation of cobalt from slag of nickel pig iron using solvent extraction method}, author={Sudibyo and A S Handoko and Agus Junaedi and Ulin Herlina and Slamet Sumardi and Fika Rofiek Mufakhir and Fajar 2005年2月1日 Steelmaking slag has been considered a potential P source due to its huge production and the increasing P content in slag with the utilization of lowgrade iron ores If the efficient separation (PDF) Industrial uses of slag The use and reuse of iron and 2017年2月1日 To improve the efficiency of iron recovery from steel slag and reduce the wearandtear on facilities, a new method was proposed by adding a secondary screen sizer to the magnetic separation process according to grain size distribution of Optimization of magnetic separation process for iron recovery 2021年2月15日 The valence of V, Cr, and Ti in reduced slag was analyzed by XPS measurements (Thermo Fisher ESCALAB 250Xi) Total iron content in slag was determined by titanium (Ⅲ) chloride reduction potassium dichromate titration method Thus, metallic Fe is difficult to be separated from reduced vanadium slag by magnetic separationCleaner and effective extraction and separation of iron from
.jpg)
Efficient separation of iron elements from steel slag
2023年2月1日 Request PDF Efficient separation of iron elements from steel slag based on magnetic separation process Steel slag is the main industrial solid waste generated from the steelmaking process It Molten slag is carried outside and poured into a dump The general term slag may be a byproduct or coproduct of smelting (pyrometallurgical) ores and recycled metals depending on the type of material being produced [1] Slag is mainly a mixture of metal oxides and silicon dioxideBroadly, it can be classified as ferrous (coproducts of processing iron and steel), Slag Wikipedia2024年3月1日 The presence of magnetic inert minerals (RO phase, Fe 3 O 4, Fe) in steel slag powder 13 enables the separation of these minerals from the slag to enhance its gelling properties and facilitate iron resource recovery, thereby improving the activity of steel slag powder 14 However, during wet magnetic separation operations, hydrated active minerals, such as C 2 S, An airfluidized magnetic separator and its separation In this study, highpurity iron with purity of 99987 wt% was prepared employing a process of direct reduction–melting separation–slag refining The iron ore after pelletizing and roasting was reduced by hydrogen to obtain direct reduced iron The Preparation of HighPurity Iron (99987%) Employing a
.jpg)
A method for recovery of iron, titanium, and vanadium from
2018年2月3日 Optimal roasting conditions for iron/slag separation were achieved with a mixture thickness of 425 mm, a roasting temperature of 1200°C, a residence time of 2 h, a molar ratio of C/O of 17, and a sodium carbonate addition of 70wt%, as 2013年11月14日 A large amount of waste copper slag containing about 35–45 wt% iron is generated every year from pyrometallurgical processes for producing copper from copper concentrateRecovery of iron from the waste copper slag is of great interest for comprehensive use of mineral resource and reduction of environmental problemsA physicochemical separation process for upgrading iron 2017年2月1日 To improve the efficiency of iron recovery from steel slag and reduce the wearandtear on facilities, a new method was proposed by adding a secondary screen sizer to the magnetic separation Optimization of magnetic separation process for iron recovery 2024年10月1日 Iron grain growth during deep reduction roasting is important for iron enrichment from copper slag (CS) through magnetic separation In this work, a novel method of additivefree activation roasting, including oxidation and subsequent reduction roasting, was proposed to increase the iron grain size, then the iron was extracted by magnetic separationIron extraction from copper slag by additivefree activation
.jpg)
(PDF) Recovery of high grade iron compounds from LD slag by
2013年1月1日 Iron grade and recovery rate of iron in magnetic (a) and nonmagnetic (b) fractions obtained from low intensity dry magnetic separation as function of particle size of LD slag2013年4月1日 Successful recovery of limonite from iron fines was achieved by using flocculationhigh intensity magnetic separation (FIMS) and adding hydrolyzed and causticized flocculants according to the (PDF) Recovery of iron from waste slag of pyrite processing using 2021年9月13日 In order to remove phosphorus element from steelmaking slag and decrease iron loss, malic acid was selected as the leaching agent to dissolve steelmaking slag Firstly, the influences of different factors, such as malic acid concentration, slag particle size, temperature, liquid/solid ratio and stirring speed, on the leaching ratios of phosphorus and iron were Leaching process of phosphorus and iron from steelmaking slag 2020年10月31日 The Fe3O4 and Fe2SiO4 in copper slag were successfully reduced to metallic iron by coalbased direct reduction Under the best reduction conditions of 1300 °C reduction temperature, 30 min reduction time, 35 wt% coal dosage, and 20 wt% CaO dosage (075 binary basicity), the Fe grade of obtained iron concentration achieved 9155%, and the Fe recovery Recovery of Iron from Copper Slag Using CoalBased Direct
.jpg)
Steel slag in China: Treatment, recycling, and management
2018年8月1日 In China, after steelmaking, the steel slag is poured from the converter, transported to the slag stacking place, and treated by aging Then the steel slag is magnetically separated to recover the metal iron (Fe) After magnetic separation, the steel slag is irregularly piled on the open groundmaking slag at high temperature have been investigated In this work, 50 kgscale experiments which simulated rotary kiln were conducted to investigate the separation behavior between slag and metal Main results are as follows (1) Molten iron was tapped out from the experimental furnace under the condition that more than 86% iron was reducedDevelopment of Iron Recovery Technique from Steelmaking Slag DOI: 101016/S1006706X(17)300237 Corpus ID: ; Optimization of magnetic separation process for iron recovery from steel slag @article{Lan2017OptimizationOM, title={Optimization of magnetic separation process for iron recovery from steel slag}, author={Yuanpei Lan and Qingcai Liu and Fei Meng and Deliang Niu and Heng Zhao}, Optimization of magnetic separation process for iron recovery 2022年1月13日 The electric arc furnace (EAF) smelting ilmenite concentrate process which produces titania slag, is high energy consumption, high pollution, and low efficiency process An economical and clean process for semimolten reduction followed by magnetic separation to produce titania slag from Panzhihua ilmenite concentrate is proposed In the present study, Recovery of Titania Slag and Iron from Semimolten State
.jpg)
Enhancing Recycling Potential: Exploring Reduction and Metal Separation
2024年7月16日 The electric arc furnace steelmaking route is essential for sustainable steelmaking through hydrogenbased direct reduced iron About 30% of the global steel production currently follows the scrap/direct reduced iron–electric arc furnace (DRIEAF) route, which is bound to increase given decarburization efforts by the steel industry We investigated 2024年7月18日 In the current study, the selective reduction and magnetic separation technique was adopted to recover iron from copper slag Calcium salts were used as an additive because studies reported that iron in the slag is difficult to reduce via the reduction method and it is mainly present in the form of Fe 2 SiO 4 in slag; that is why in order to enhance the recovery of iron A novel approach for recovery of iron from copper slag using 2022年1月22日 The dumping of a large amount of steel slag not only wastes metal resources, but pollutes the ecological environment In this study, a method for recovery of vanadium, titanium, iron, magnesium, and synthesizing anhydrite from steel slag is proposed The leaching efficiency of V, Ti, Fe, and Mg was 9942%, 9936%, 9989%, and 9995%, respectively, under Efficient Separation and Recovery of Vanadium, Titanium, Iron DOI: 101016/jjmrt202301186 Corpus ID: ; Efficient separation of iron elements from steel slag based on magnetic separation process @article{Liu2023EfficientSO, title={Efficient separation of iron elements from steel slag based on magnetic separation process}, author={Xin Liu and Dazhi Wang and Zhiwei Li and Wei Ouyang and Yanping Bao and Chao Gu}, Efficient separation of iron elements from steel slag based on
.jpg)
Iron recovery from copperslag with lignitebased direct reduction
In order to recycle iron from copper slag with total iron content(TFe) of 3996%(mass fraction),a technique with lignitebased direct reduction followed by magnetic separation was presentedAfter analysis of chemical composition and crystalline phase,according to experimental mechanism,the tests for studying the effects of different parameters on the recovery of iron were carried 2022年4月27日 Compared with the initial steel slag, the iron grade increased by 822%, and the iron recovery increased by 4638% compared with direct magnetic separation without oxidation [13](PDF) Optimization of Iron Recovery from BOF Slag by2019年10月29日 Slag is the byproduct of iron and steelmaking processes Normally, around half to one tonne of slag would be generated for yielding one tonne of rolled iron or steel (Lobato et al 2015)It was reported that the world steel production was 19 billion tonnes in 2016, which suggested that at least around 1 billion tonnes of slag is produced during the year (Worldsteel The potential utilization of slag generated from iron and 2022年5月1日 Abstract Considering the BSSF steelmaking slag generated in a Brazilian steelwork, it would be worth to separate iron and calcium from it, with the objective of increasing its iron content, or Separation of Iron and Calcium from a BSSF Steelmaking Slag