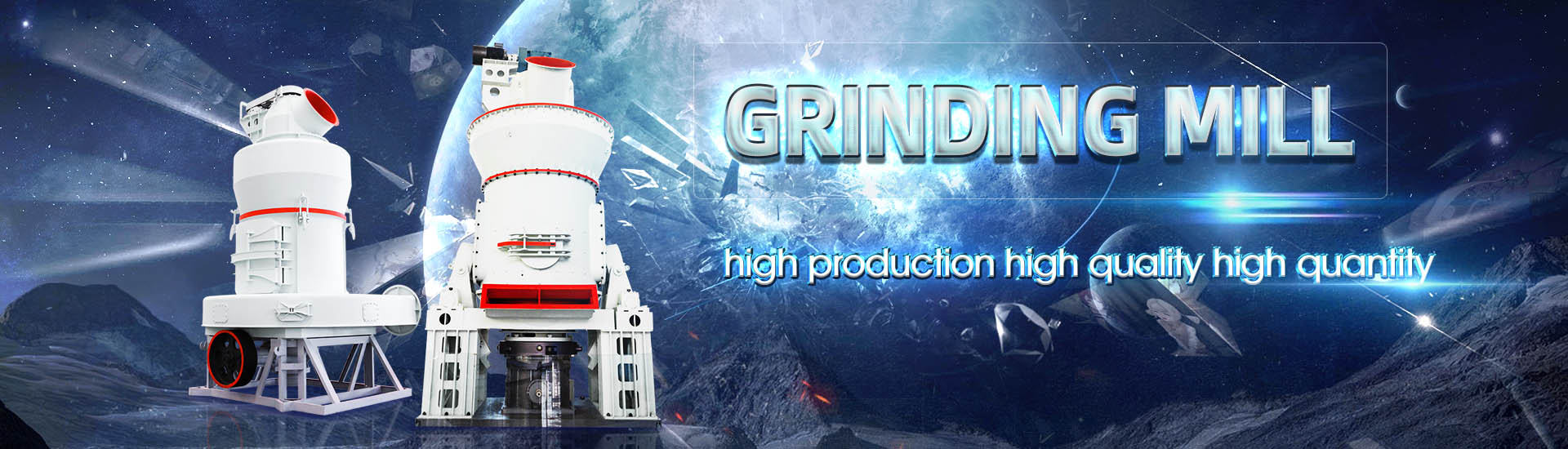
Clinker mill production cement formula

Clinkerization Cement Plant Optimization
The process of clinkerization signifies conversion of raw meal into clinker minerals mainly consisting of C4AF(Aluminoferite), C3A(Aluminite), C2S(Belite) and C3S (Alite) phases along with small percentage of free lime CaO, MgO, Alkalies, Sulphates etcThis section provides an indepth review of major solutions deployed to decarbonize cement manufacturing, including alternative formulations of clinker, alternative fuels for cement Clinker Production an overview ScienceDirect TopicsCement production and concrete as building material The properties of concrete make it a primary building material where reliability and durability are required Depending on the application ~ Process characteristics of clinker and cement production SINTEFClinker, made from magnesiarich feed must be very rapidly cooled once it has been burned, to guard against production of unsound clinker Plants faced with this problem usually locate the burning zone very close to the discharge end EVERYTHING YOU NEED TO KNOW ABOUT THE
.jpg)
The Cement Plant Operations Handbook International Cement
High freelime clinker must be blended into mill feed with circumspection to ensure that the resulting cement is not expansive A maximum composite free lime for the cement should be Table 1 represents the main sintering parameters and properties of ecocement in various studies conducted on sewage sludge utilization in cement clinker productionCement Clinker Production an overview ScienceDirect TopicsThe clinker keeps cooling and a ball mill grinds it with gypsum or other ingredients into fine cement—about 150 billion grains per pound Blending in higher ratios of limestone or SCMs can reduce a plant’s carbon footprint by up to 10%How Cement is Made Portland Cement Association2020年9月9日 The most significant process of the cement production chain, in terms of energy efficiency and quality of the product, is represented by the production of the main component Optimization of the Clinker Production Phase in a Cement Plant
.jpg)
Process characteristics of clinker and cement production SINTEF
Cement production process: Thermal energy demand and CO 2 emissions 30% fuel emissions thermal energy prod process emissions from calcination of limestone 60% 10% electric power consumption, indirect emissions Limestone Quarry Filter Clinker Cement Cement Mills Raw Mill Calcination Cement Constituents Crusher FanDrying Rotary Kiln Preheater2020年9月9日 An APC system in a clinker production unit of a cement plant must lead to productivity and efficiency increase, while assuring the desired quality Lange, T, Frewin, N: Next generation controllers for kiln/cooler and mill applications based on model predictive control and neural networks In: IEEE/PCA 42nd Cement Industry Optimization of the Clinker Production Phase in a Cement A review of the effectiveness of Life Cycle Assessment for gauging environmental impacts from cement production Oluwafemi E Ige, Collins Obiora, in Journal of Cleaner Production, 2021 223 Production of clinker The clinker production stage is where the raw material (the raw meal) converts into clinker The raw meal is fed into a rotary kiln through a preheater at about 1450 Clinker Production an overview ScienceDirect TopicsThe standard Bogue calculation refers to cement clinker, rather than cement, but it can be adjusted for use with cement Although the result is only approximate, the calculation is an extremely useful and widelyused calculation in the cement industry The calculation assumes that the four main clinker minerals are pure minerals with compositions:Portland cement clinker: the Bogue calculation Understanding Cement
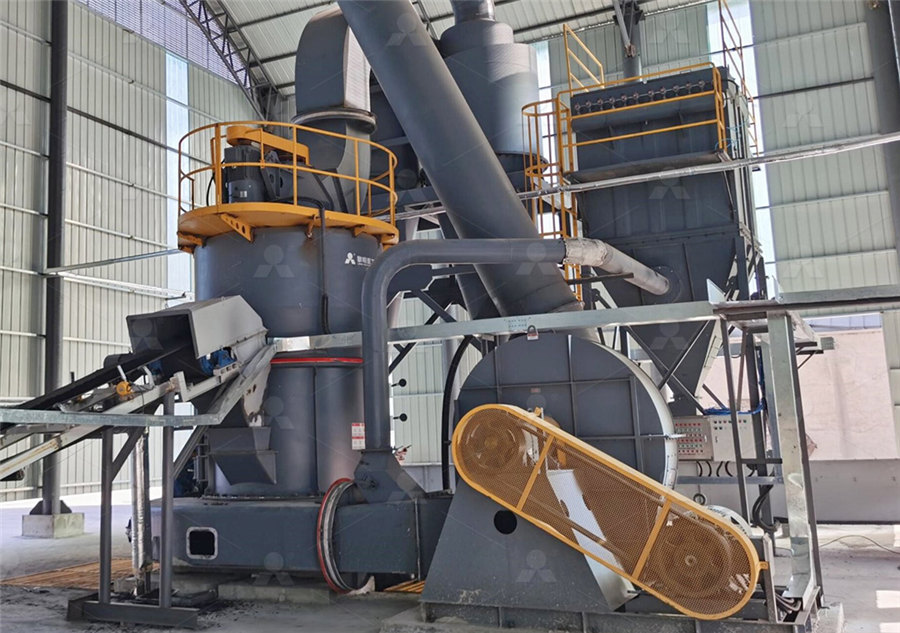
Quality Composition of cement clinker
Production of clinker in a reducing atmosphere in a cement kiln can seriously degrade the quality of clinker and the cement produced from the clinker However, an industrial cement kiln is tolerant of reducing conditions without these adverse effects manifesting themselves, provided that the clinker falls into the cooler at a temperature above 1250°C and is cooled in air13 Ball Mill Study Data 105 14 Ball Mill Formulas 111 15 BIS Specification of Additives 113 16 Cement Testing 115 17 BIS Specifications for various Cements 120 18 Thermo Physical Properties of Different Insulating Materials 124 19 Environmental Standards (Stack, Ambient Air and Water) 125 20 COCEMENT FORMULAE HANDBOOK Green Business Centre2013年1月1日 Studies on cement production optimisation have been carried out on clinker simulation using AspenTech [36], cement raw materials blending using a general nonlinear timevarying model [37], cement Modelling the cement process and cement clinker quality2023年10月19日 Clinker is a critical component in the production of cement and forms the intermediate product during the cement manufacturing process It can be best described as a nodular material, usually grayish in color, which is produced by sintering limestone and aluminosilicate materials such as clay at high temperatures in a cement kilnUnderstanding the Role of Clinker Grinding in Cement Production
.jpg)
The Cement Plant Operations Handbook International Cement
refractories – 9 Clinker cooling – 10 Kiln mechanical – 11 Emergency power – 12 Plant control systems 6 Cement milling process summary data – 8 Typical equipment downtime 110 1 Storage of clinker and other components – 2 Cement milling – 3 Separators (classifiers) – 4 Ball mill circuit control – 5 Cement storage – 6Cement Kiln In Cement Plant AGICO offers different types of cement kilns from 105000t/d with steady running, high efficiency and large output We adopt the most advanced calcination technology so that the production investment of clinker is small and the income is highClinker Production Clinker Manufacturing Cement Raw Materials Crushing, Storing and Grinding Clinker calcination is the most crucial part of the whole process of cement manufacturing At this stage, ground raw materials will be sent into the cement kiln and be heated at a high Cement Clinker Calcination in Cement Production Chemical compositional parameters used to describe Potland cement clinker (LSF, SR, AR, SR) Understanding Cement Interpreting Limestone can be quantified by measuring the CO 2 content and the formula adjusted reading Chemicl parameters defining clinker composition
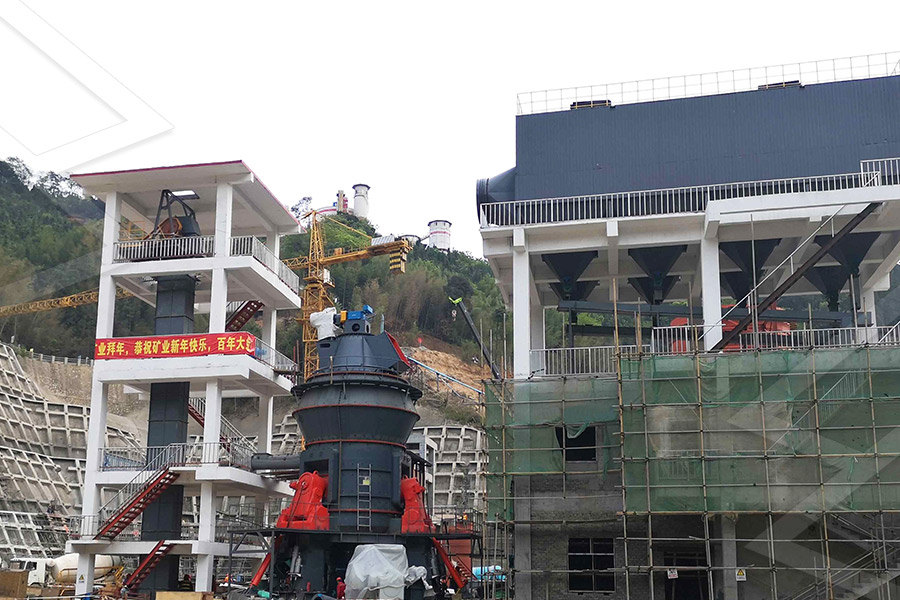
Cement Clinker: Production, Composition, Types, and
2023年6月6日 Production Process of Clinker Cement manufacturers create clinkers through a multistep process that includes ingredient selection, heating, and grinding Raw Mineral Preparation – The main ingredients in clinker 2022年9月21日 The study explores the indirect mechanosynthesis process for cement and clinker production, highlighting its impact on global cement outputCement and Clinker Production by Indirect Mechanosynthesis Energy Consumption Benchmark Guide: Cement Clinker Production 8 • Blue Circle Cement’s Bowmanville facility replaced the inlet fan damper in its coal mill with a variable inlet vane damper The resulting reduction in power consumption saved the Energy Consumption Benchmark Guide: Cement Clinker Production A 10 MW cement mill, output 270 tonnes per hour A cement mill (or finish mill in North American usage [1]) is the equipment used to grind the hard, nodular clinker from the cement kiln into the fine grey powder that is cementMost cement is currently ground in ball mills and also vertical roller mills which are more effective than ball millsCement mill Wikipedia
.jpg)
Cement Clinker an overview ScienceDirect Topics
Report of UNEP SBCI WORKING GROUP ON LOWCO2 ECOEFFICIENT CEMENTBASED MATERIALS Ellis Gartner, Tongbo Sui, in Cement and Concrete Research, 2018 1 Introduction The term “alternative cement clinker ” as used here refers to a manmade mineral material that, when ground to a fine powder, is capable of reacting sufficiently rapidly with water and/or CO 2 Lime Saturation Factor (LSF) is the ratio of the actual amount of lime in raw meal/clinker to the theoretical lime required by the major oxides (SiO 2, Al 2 O 3 and Fe 2 O 3) in the raw mix or clinkerIt is practically impossible to complete the reaction to 100%, in a reactor like rotary kiln, therefore there will always be some unreacted lime (CaO f) known as free limeLime Saturation Factor Cement Plant OptimizationCement Quality calculations forClinker C3S, C2S, C3A, C4AF calculations, Cement Quality, Burnability index, Burning temperature (minimum) Optimization; Clinker C3S, C2S, C3A, C4AF : Please Enter / Stepto Input Values CaO % Al2O3% SiO2% Fe2O3% CaO free % Mn2O3% Na2O% SO3 Clinker C3S, C2S, C3A, C4AF calculations, Cement Quality, 2015年1月1日 clinker production in cement industry’, Int J Exergy, Vol 16, existing raw mill in a cement plant to reduce the amount of energy consumption in Process Chemical formula Exergetic assessment of a rotary kiln for clinker production in cement
.png)
Portland Cement Clinker an overview ScienceDirect Topics
Portland cement PC Aïtcin, in Science and Technology of Concrete Admixtures, 2016 Abstract Portland cement is at the same time the fruit of simple technology and a complex science It consist in firing at 1450 °C very simple pulverized raw materials having a very specific composition to produce an intermediate product called Portland cement clinker or simply clinker2019年2月21日 Earlier we considered a mixture of which materials is used in cement production The base of this mixture is a clinker In this article, we will consider the composition of clinker and its impact on grinding balls CLINKER GRINDING IN CEMENT PRODUCTION2021年2月11日 As a general rule, there should be less than 25% of clinker that is below 1mm in size Coarse clinker is more of an issue for ball mills Some cement groups use a formula, such as Bond’s, to calculate the maximum ball size required in a Clinker size and cement grinding GCP Applied TechnologiesArticle Cement and Clinker Production by Indirect Mechanosynthesis Process Othmane Bouchenafa 1, * , Rabah Hamzaoui 1 , Céline Florence 1 and Sandrine Mansoutre 2 1 2 * Institut de Recherche en Constructibilité IRC, ESTP, Université ParisEst, 28 Avenue du Président Wilson, 94234 Cachan, France Groupe Vicat, 4 Rue Aristide Bergès, Les Trois Vallons, 38080 Cement and Clinker Production by Indirect Mechanosynthesis
.jpg)
Cement Clinker: Its Composition, Types Uses?
2020年8月15日 Clinker is a nodular material produced during the furnace phase during the production of cement and is used as a binder in many cement products Clinker nodes or nodules are usually 3–25 mm in diameter and dark brown It is produced by heating limestone and clay at a point of liquefaction in a rotary kiln at about 1400 ° C – 1500 ° CCement production line: Cement Mill Separator is mainly used in the clinker mill system of the cement production line to separate ground cement clinker and cement powder Separator efficiency can be calculated by the following formula: Efficiency = (Output Mass/ Input Mass) * Cement Separator HighEfficiency Cement Mill Separator2021年3月24日 Cement manufacturing requires cooling down of hot clinker at temperature of about 1350o C to temperature lower than 100 o C in a cooling system known as clinker coolerModelling of clinker cooler and evaluation of its performance in The annual cement consumption in the world is around 17 billion tonnes and is increasing by 1% every year []Cement industries consume 5% of the total industrial energy utilised in the world []A total of 40% of the total energy consumption of a cement plant is used in clinker grinding in a ball mill to produce the final cement product [] Predictive Controller Design for a Cement Ball Mill Grinding
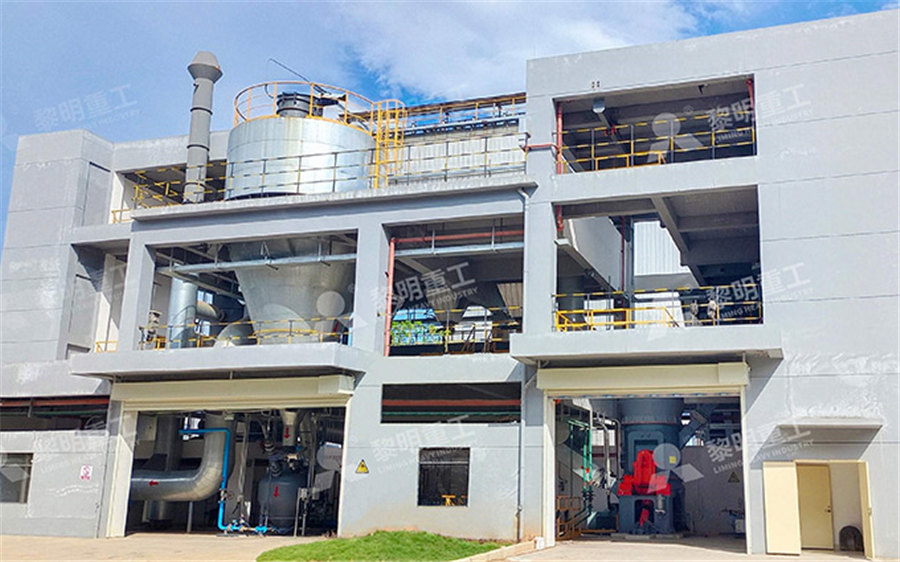
Energy Consumption Benchmark Guide: Cement Clinker Production
Canadian cement clinker production capacity is about 141 million tonnes per year In 1998, clinker production totalled 12 million tonnes for a capacity use of 85 percent With more than 1100 readymixed and other plants across the country using Portland cement to make concrete, the industry employs some 22 000 people and generates more than $3 billion in annual salesCheck fuel consumption, sulfur absorption in clinker, material balances, and NOx formation; Clinker analysis to check kiln operation and clinker quality and material balances; Analysis of finished cement to check mill operation, gypsum and SCM additions as well as the quality of the finished cement (example EN 197, ASTM C150, ASTM C595, and Sustainable Clinker and Cement Production by Using Alternative Fuels Cement production process: Thermal energy demand and CO 2 emissions 30% fuel emissions thermal energy prod process emissions from calcination of limestone 60% 10% electric power consumption, indirect emissions Limestone Quarry Filter Clinker Cement Cement Mills Raw Mill Calcination Cement Constituents Crusher FanDrying Rotary Kiln PreheaterProcess characteristics of clinker and cement production SINTEF2020年9月9日 An APC system in a clinker production unit of a cement plant must lead to productivity and efficiency increase, while assuring the desired quality Lange, T, Frewin, N: Next generation controllers for kiln/cooler and mill applications based on model predictive control and neural networks In: IEEE/PCA 42nd Cement Industry Optimization of the Clinker Production Phase in a Cement
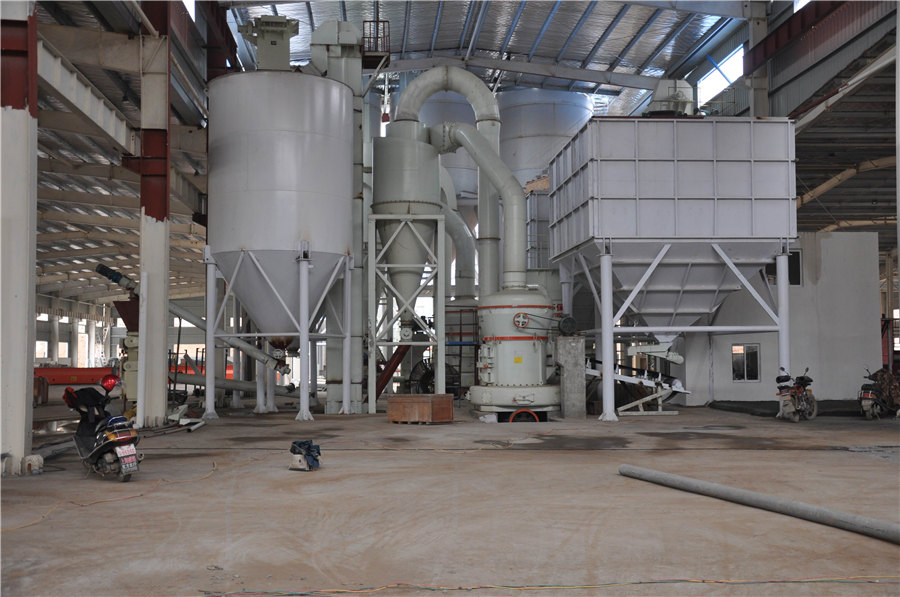
Clinker Production an overview ScienceDirect Topics
A review of the effectiveness of Life Cycle Assessment for gauging environmental impacts from cement production Oluwafemi E Ige, Collins Obiora, in Journal of Cleaner Production, 2021 223 Production of clinker The clinker production stage is where the raw material (the raw meal) converts into clinker The raw meal is fed into a rotary kiln through a preheater at about 1450 The standard Bogue calculation refers to cement clinker, rather than cement, but it can be adjusted for use with cement Although the result is only approximate, the calculation is an extremely useful and widelyused calculation in the cement industry The calculation assumes that the four main clinker minerals are pure minerals with compositions:Portland cement clinker: the Bogue calculation Understanding CementProduction of clinker in a reducing atmosphere in a cement kiln can seriously degrade the quality of clinker and the cement produced from the clinker However, an industrial cement kiln is tolerant of reducing conditions without these adverse effects manifesting themselves, provided that the clinker falls into the cooler at a temperature above 1250°C and is cooled in airQuality Composition of cement clinker13 Ball Mill Study Data 105 14 Ball Mill Formulas 111 15 BIS Specification of Additives 113 16 Cement Testing 115 17 BIS Specifications for various Cements 120 18 Thermo Physical Properties of Different Insulating Materials 124 19 Environmental Standards (Stack, Ambient Air and Water) 125 20 COCEMENT FORMULAE HANDBOOK Green Business Centre
.jpg)
Modelling the cement process and cement clinker quality
2013年1月1日 Studies on cement production optimisation have been carried out on clinker simulation using AspenTech [36], cement raw materials blending using a general nonlinear timevarying model [37], cement 2023年10月19日 Clinker is a critical component in the production of cement and forms the intermediate product during the cement manufacturing process It can be best described as a nodular material, usually grayish in color, which is produced by sintering limestone and aluminosilicate materials such as clay at high temperatures in a cement kilnUnderstanding the Role of Clinker Grinding in Cement Productionrefractories – 9 Clinker cooling – 10 Kiln mechanical – 11 Emergency power – 12 Plant control systems 6 Cement milling process summary data – 8 Typical equipment downtime 110 1 Storage of clinker and other components – 2 Cement milling – 3 Separators (classifiers) – 4 Ball mill circuit control – 5 Cement storage – 6The Cement Plant Operations Handbook International Cement Cement Kiln In Cement Plant AGICO offers different types of cement kilns from 105000t/d with steady running, high efficiency and large output We adopt the most advanced calcination technology so that the production investment of clinker is small and the income is highClinker Production Clinker Manufacturing Cement