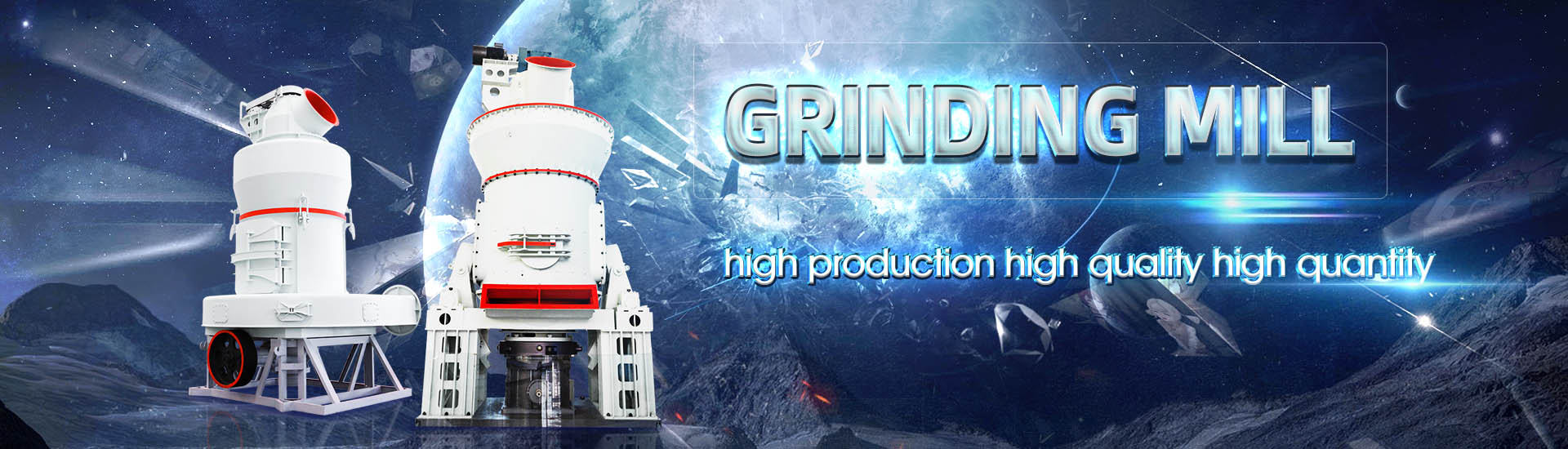
4.3x13 meters cement mill process parameters
.jpg)
The Cement Plant Operations Handbook International Cement
The Cement Plant Operations Handbook is a concise, practical guide to cement manufacturing and is the standard reference used by plant operations personnel worldwide Providing a HOLTEC has undertaken Performance Optimisation of the cement grinding circuits by doing process diagnostic studies in many cement plants The paper describes the approach for the PROCESS DIAGNOSTIC STUDIES FOR CEMENT MILL Abstract Based on a dynamical model of the grinding process in closed circuit mills, efficient efforts have been made to optimize PID controllers of cement milling The process simulation OPTIMIZING THE CONTROL SYSTEM OF CEMENT MILLING: 2011年7月1日 Modeling is based exclusively on long term industrial data sets of five cement mills Not only the dynamics of each mill is estimated but also separate dynamical parameters (PDF) Modeling of Cement Milling Process Based on Long
.jpg)
Cement Mill PDF Air Conditioning Applied And Interdisciplinary
The mill processes 160 tonnes per hour of raw material including 1536 tonnes of clinker and 618 tonnes of gypsum Key parameters noted are the mill diameter of 42 meters, length of 13 2020年2月15日 The most important kiln controlling parameters are clinker production rate, fuel flow rate, specific heat consumption, secondary air temperature, kiln feedend temperature, (PDF) Parametric Studies of Cement Production ProcessesAs grinding accounts for a sizeable share in a cement plant’s power consumption, optimisation of grinding equipment such as ball mills can provide significant cost and CO 2BALL MILLS Ball mill optimisation Holzinger Consulting1987年8月1日 Cement manufacturing process is now operated with the aid of various control systems, such as raw meal composition control, kiln control and mill control Those systems Optimization of Cement Manufacturing Process ScienceDirect
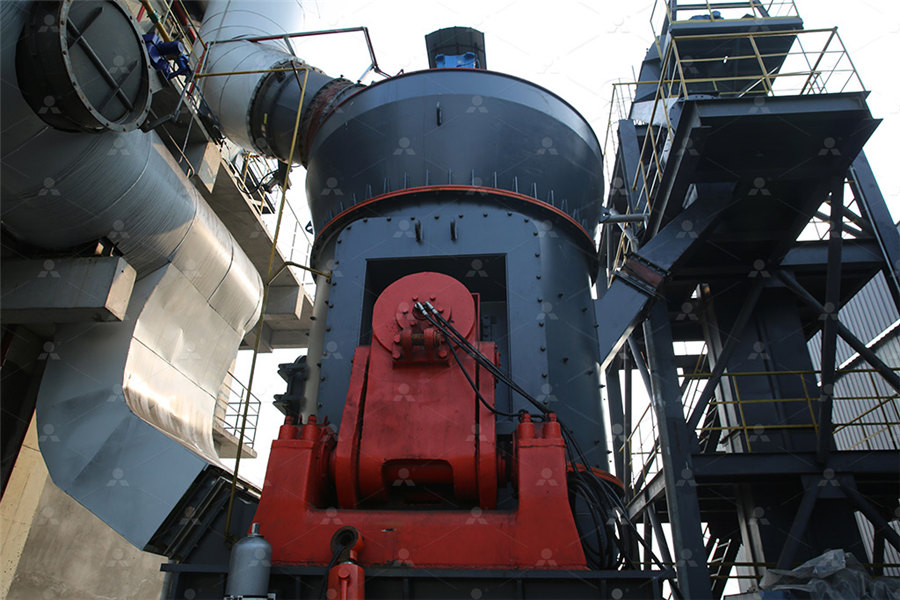
Chapter 4 Cement Manufacturing and Process Control
The most common way to manufacture Portland cement is through a dry process The first step is to quarry the principal raw materials, mainly limestone, clay, and other materials2022年11月1日 Model parameters for the particle breakage and classification action with/without the classifying liner were obtained from the available literature for cement clinker Impact of ball size distribution, compartment configuration, and Stage of Cement Manufacture There are six main stages of the cement manufacturing process Stage 1: Raw Material Extraction/Quarry The raw cement ingredients needed for cement production are limestone (calcium), sand and clay (silicon, aluminum, iron), shale, fly ash, mill scale, and bauxite The ore rocks are quarried and crushed into smaller pieces of about 6 inchesHow Cement is Made Cement Manufacturing ProcessChemical process industries are running under severe constraints, and it is essential to maintain the endproduct quality under disturbances Maintaining the product quality in the cement grinding process in the presence of clinker Predictive Controller Design for a Cement Ball Mill
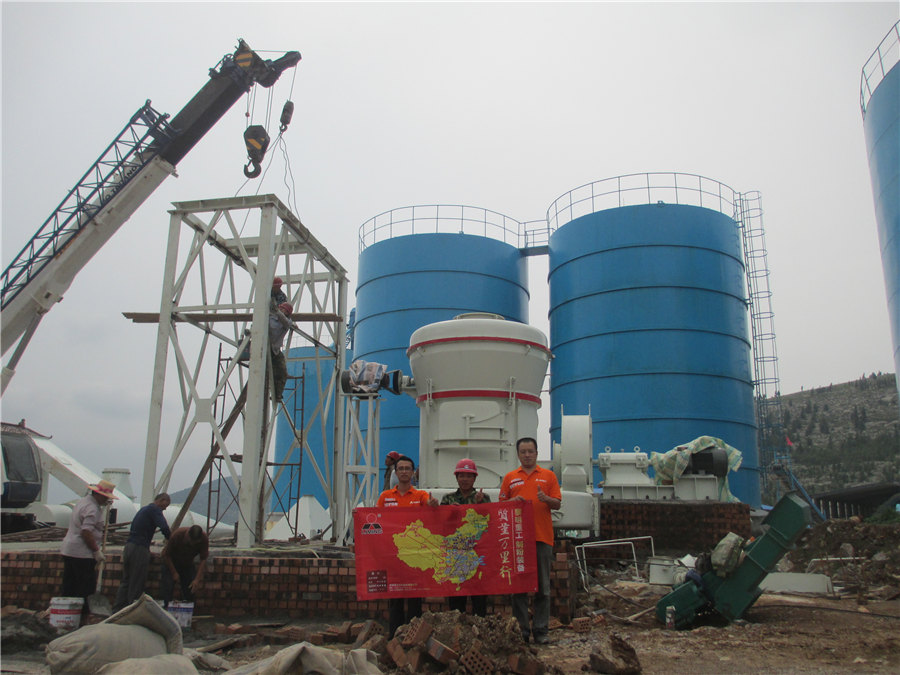
Cement Manufacturing and Process Control SpringerLink
2019年8月27日 The major raw materials used as a source of CaO for cement manufacturing are limestone, chalk, marl, etc These raw materials by virtue of their natural occurrence contains other mineral impurities eg, MgO, SiO 2, Al 2 O 3, Fe 2 O 3, alkali compounds, and sulfidesThese impurities play an important role to influence the cement manufacturing 2014年6月10日 Evolution of the cement Process • Wet process easiest to control chemistry better for moist raw materials • Wet process high fuel requirements fuel needed to evaporate 30+% slurry water • Dry process kilns less fuel requirements • Preheater/Precalciner further enhance fuel efficiency allow for high production ratesCement manufacturing process PPT Free Download SlideShare2014年1月1日 In this work the relation between the change in mill output and cement fineness caused in the ball mill grinding process of composite cement with respect to different operating input parameters Optimization of ball mill operating parameters for their effect on mill criteria, but also to determine optimum conditions of the process parameters KeyWords: Dynamics, Raw meal, Quality, Mill, Model, Variance, PID, Robustness, Homogeneity 1 Introduction In cement industry a huge amount of efforts in process control have been dedicated on raw meal homogeneity as it is the main factor influencing theEffective Optimization of the Control System for the Cement Raw
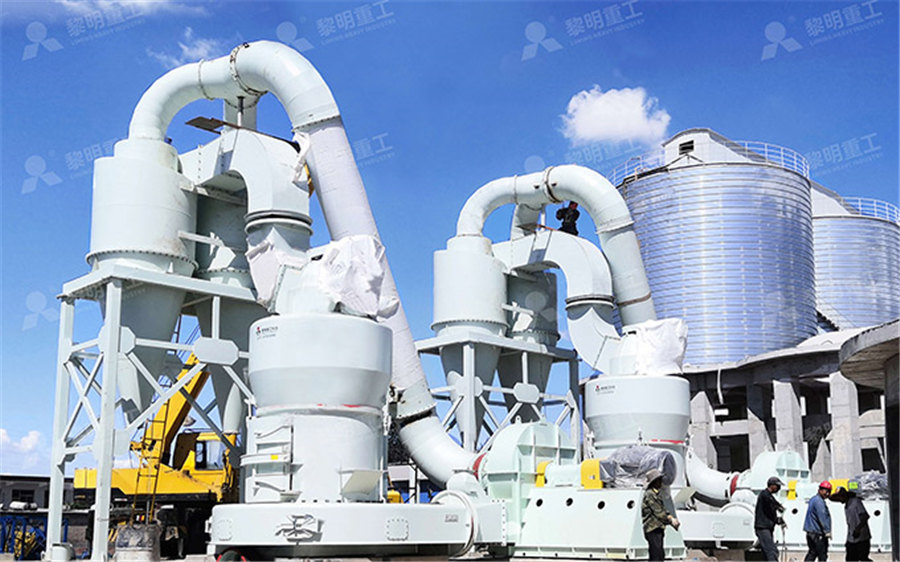
Cement Mill PDF Air Conditioning Applied And
This document provides information about the Binani Cement plant, including specifications for the cement mill and related equipment The mill processes 160 tonnes per hour of raw material including 1536 tonnes of clinker and 618 tonnes of gypsum Key parameters noted are the mill diameter of 42 meters, length of 13 meters, rotation speed of 158 rpm, and total main drive 2019年8月1日 This enhanced model allows the direct prediction of the process parameters of the production mill without labscale experimental process parameter optimization Simulation aided flow sheet optimization of a cement grinding circuit by considering the quality measurements Powder Technol, 301 (2016), pp 12421251Mill, material, and process parameters – A mechanistic model for 2015年2月1日 In this study, the grinding characteristics of waste printed circuit boards (PCBs) were evaluated using a population balance model (PBM) The grinding characteristics under various conditions (PDF) Effects of mill design and process parameters in milling Raw mill is generally called cement raw mill, raw mill in cement plant, it refers to a common type of cement equipment in the cement plantIn the cement manufacturing process, raw mill in cement plant grind cement raw materials into the raw mix, and the raw mix is sent to the cement kiln to make cement clinker, next, clinker and other admixtures will be ground into finished cement by Raw mill Cement Plant
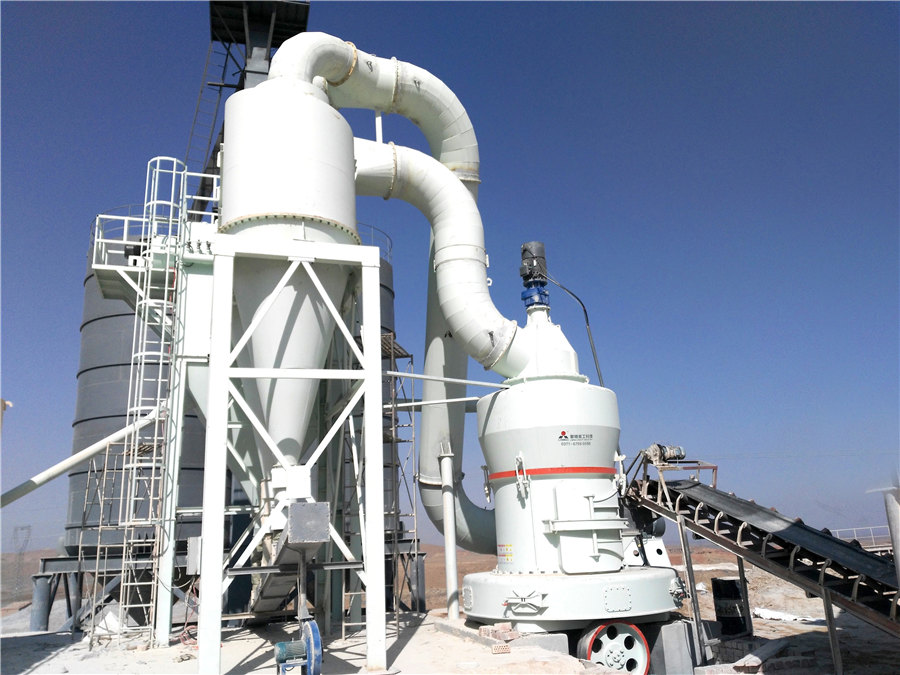
Modeling and Control of Cement Grinding Processes
2003年10月1日 In this study, a nonlinear dynamic model of a cement grinding process, including a ball mill and an air separator in closed loop, is developed2 Process Description The Raw Mill system consists of two process units, namely the Raw Mill and the Separator Raw mill feeds are limestone, siltstone, and iron sand, in which crushing and mixing take place The output of the Raw Mill unit is fed into the Separator to separate raw meal that is not in accordance with the expectedModeling and Simulation study on Cement Raw Mill Process 2012年12月10日 This paper focuses on modelling and solving the ingredient ratio optimization problem in cement raw material blending process A general nonlinear timevarying (GNLTV) model is established for Modeling and Optimization of Cement Raw Clinker density 14 (Dotternhausen) Ball Mill Cement Lafarge max R5% >25mm, Holcim 30mm; Raw Meal max R1% > 30 mm (Lafarge) the process parameters of the grinding circuit will help to decide if a finer ball charge composition will allow an even better mill operationEverything you need to know about clinker/cement Grinding
.jpg)
Analysis of the parameters affecting energy consumption of a
2014年5月1日 grinding the clinker in a cement mill Clinker production in rotary kiln system is the most energy intensive stage in cement production, accounting for about 90% of2013年2月7日 PDF A simulation of the dynamic behavior of an actual cement mill (CM) is described aiming to optimize an existing PID controller The Mconstrained Find, read and cite all the research you (PDF) Robust stabilization of cement milling process using 2013年5月1日 Influence of Process Parameters on Grinding A Review PV Vinay 1 * , Ch Srinivasa Rao 2 1 Department of Mechanical Engineering, G VP College for Degree and PG CoursesInfluence of Process Parameters on Grinding A Review2014年3月1日 The object of the study reported here is the grinding process in a tumbling mill where the mechanism of destruction by crushing is implemented, which is caused by the mechanism of compression loading(PDF) Analysis of ball mill grinding operation using mill power
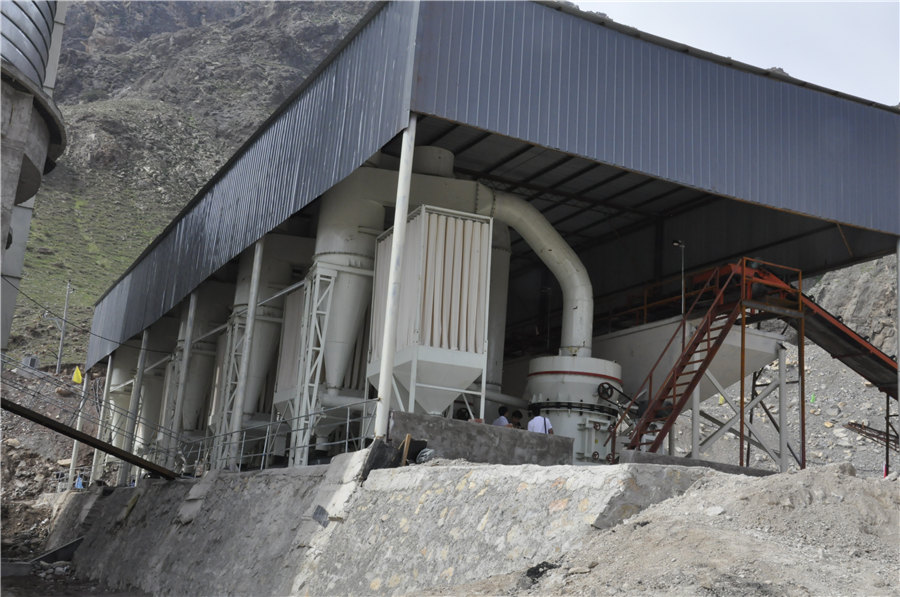
Ball Mill In Cement Plant Selling Various Types Of Cement Mill
The performance parameters of the Ball Mill usually include Different Ball Mill models can be customized according to different production needs In the cement production process, Ball Mill is usually used in conjunction The disc of this type of Ball Mill is usually located below ground and its diameter is usually between 1 and 3 meters4 Tromp curve – 5 Mill critical speed 6 Charge volume loading – 7 Grace factor and other ball mill parameters – 8 Mill power – 9 Ball weight and surface area – 10 Maximum ball size required –11 Measurement of wear – 12 Effects of gypsum upon setting time B5 Kilns and burning 284 1 Cement compounds and ratios – 2 The Cement Plant Operations Handbook International Cement FIGURE 4 Particle size distributions of collected samples (Survey 2) Bond work indices and breakage characteristics under compression were determinedPerformance Evaluation of Vertical Roller Mill in Cement Grinding: 2015年1月1日 The raw material grinding in the cement mill for production of cement is one of the most energydemanding processes in cement industry In cement plants, 50–60 % of the total energy consumption is due to grinding of raw materials The process of parameter adjustment requires too much of human interventionModeling Based on the Extreme Learning Machine for Raw Cement Mill
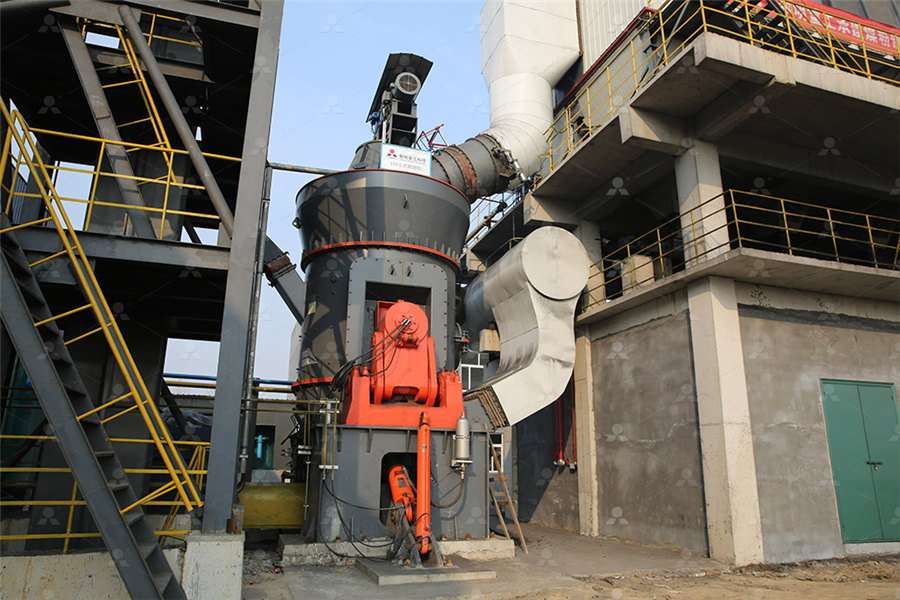
Energy and exergy analyses for a cement ball mill of a new
2020年2月1日 Rather than huge expansion, most industries will focus on maximizing resources for maximum pro tability Consequently, a study of the impact of operational parameters on ball mill energy e ciency 2022年10月1日 This study investigated a mathematical model for an industrialscale vertical roller mill(VRM) at the Ilam Cement Plant in Iran The model was calibrated using the initial survey's data, and the (PDF) A cement Vertical Roller Mill modeling based on2021年1月1日 In dry process technology, crushed limestone and raw materials are ground and mixed without addition of water Dry and semiwet processes are more energyefficient The wet process requires 028 tons of coal and 110 kWh to produce one ton of cement, while the dry process requires only 018 tons of coal and 100 kWh of energy [4]Review on vertical roller mill in cement industry its performance The Tunisian clinkers investigated as part of this study contain four main phases: alite (C3S), belite (C2S), tricalcium, aluminate (C3A) and ferrite (C4AF)(PDF) Influence of raw material's parameters on the clinker's
.jpg)
PROCESS TRAINING for operators of Vertical RAW Mills
Because of this variation it is also not possible to give standard values of the process parameters Furthermore it is necessary that the operators of the mill have an understanding of the process click here to Download the Most Important 13 Books in Cement Industry click here to Download the Most Important 13 Books in Cement Industry2019年3月8日 257 HighEfficiency Fans for Cement Mill V ents use and now account for over 90 percent of cement consumption worldwide (41 monitoring and adjustment of process parameters by IMPROVING THERMAL AND ELECTRIC ENERGY EFFICIENCY AT CEMENT 2014年3月1日 Based on a dynamical model of the grinding process in closed circuit mills, efficient efforts have been made to optimize PID controllers of cement milling The process simulation is combined with an autoregressive model of the errors between the actual process values and the computed ones Long term industrial data have been used to determine the Optimizing the control system of cement milling: process Stage of Cement Manufacture There are six main stages of the cement manufacturing process Stage 1: Raw Material Extraction/Quarry The raw cement ingredients needed for cement production are limestone (calcium), sand and clay (silicon, aluminum, iron), shale, fly ash, mill scale, and bauxite The ore rocks are quarried and crushed into smaller pieces of about 6 inchesHow Cement is Made Cement Manufacturing Process

Predictive Controller Design for a Cement Ball Mill
Chemical process industries are running under severe constraints, and it is essential to maintain the endproduct quality under disturbances Maintaining the product quality in the cement grinding process in the presence of clinker 2019年8月27日 The major raw materials used as a source of CaO for cement manufacturing are limestone, chalk, marl, etc These raw materials by virtue of their natural occurrence contains other mineral impurities eg, MgO, SiO 2, Al 2 O 3, Fe 2 O 3, alkali compounds, and sulfidesThese impurities play an important role to influence the cement manufacturing Cement Manufacturing and Process Control SpringerLink2014年6月10日 Evolution of the cement Process • Wet process easiest to control chemistry better for moist raw materials • Wet process high fuel requirements fuel needed to evaporate 30+% slurry water • Dry process kilns less fuel requirements • Preheater/Precalciner further enhance fuel efficiency allow for high production ratesCement manufacturing process PPT Free Download SlideShare2014年1月1日 In this work the relation between the change in mill output and cement fineness caused in the ball mill grinding process of composite cement with respect to different operating input parameters Optimization of ball mill operating parameters for their effect on mill
.jpg)
Effective Optimization of the Control System for the Cement Raw
criteria, but also to determine optimum conditions of the process parameters KeyWords: Dynamics, Raw meal, Quality, Mill, Model, Variance, PID, Robustness, Homogeneity 1 Introduction In cement industry a huge amount of efforts in process control have been dedicated on raw meal homogeneity as it is the main factor influencing theThis document provides information about the Binani Cement plant, including specifications for the cement mill and related equipment The mill processes 160 tonnes per hour of raw material including 1536 tonnes of clinker and 618 tonnes of gypsum Key parameters noted are the mill diameter of 42 meters, length of 13 meters, rotation speed of 158 rpm, and total main drive Cement Mill PDF Air Conditioning Applied And 2019年8月1日 This enhanced model allows the direct prediction of the process parameters of the production mill without labscale experimental process parameter optimization Simulation aided flow sheet optimization of a cement grinding circuit by considering the quality measurements Powder Technol, 301 (2016), pp 12421251Mill, material, and process parameters – A mechanistic model for 2015年2月1日 In this study, the grinding characteristics of waste printed circuit boards (PCBs) were evaluated using a population balance model (PBM) The grinding characteristics under various conditions (PDF) Effects of mill design and process parameters in milling
.jpg)
Raw mill Cement Plant
Raw mill is generally called cement raw mill, raw mill in cement plant, it refers to a common type of cement equipment in the cement plantIn the cement manufacturing process, raw mill in cement plant grind cement raw materials into the raw mix, and the raw mix is sent to the cement kiln to make cement clinker, next, clinker and other admixtures will be ground into finished cement by