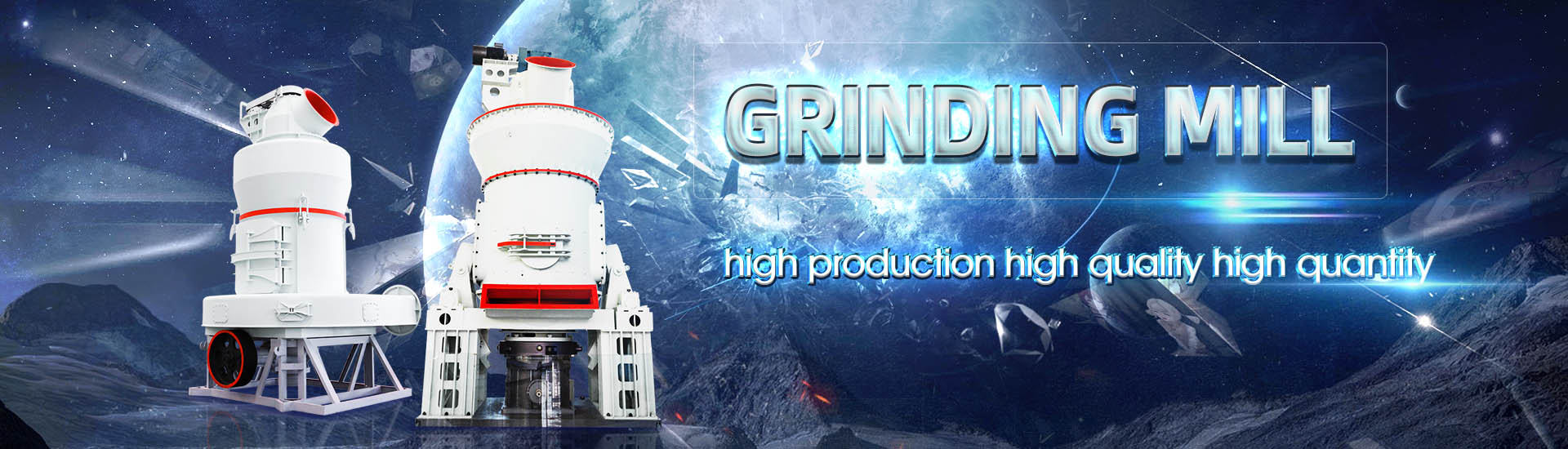
How to inspect longdistance ring roller mills
.jpg)
Improved Technologies for Mill Roll Inspection
Roll inspection using the Rollmate® is performed by employing uniquely designed ultrasonic sensors that generate high frequency sound that is sensitive to surface defects without being effected by surface contamination, such as grinding fluid, water, etcReliable roll inspection with ultrasonic technology In order to minimize downtime in hot rolling mills, it is important to identify defect rolls early This is why HCC/KPM has developed surface Roll Inspection Control Measuring Technology HCC/KPM2017年11月15日 This paper provides an overview of mill roll inspection technology and the effects that various inspection technologies can have on the efficiency and costs associated Improved Technologies for mill roll inspection ResearchGateASTM International Standard E2905 was written for mill and kiln ring gear teeth cleaning and inspection It will scan the addendum, dedendum and root of a gear tooth in 15 seconds With New ASTM Standard for Mill and Kiln Ring Gear Cleaning and
.jpg)
RolltoRoll Measurement and Inspection Solutions OPTEX FA
Using the TOFDL series makes it possible to monitor the tension of the sheet material by detecting the vertical position of the offset roller Position detection with the TOFDL is Long rolling applications can include: • Guides change, adjustment and maintenance • Shear blade change • Bar sampling and testing • Cobble removal • Short bar removal • Block ring LONG ROLLING DIGITAL TECHNOLOGIESComplete roll inspection including surface, subsurface, coreshell disbond and bruise inspection using a proprietary technique ROLLMATE is the most advanced roll inspection system on the Mill Roll inspection InnerspecWith a scanning time as short as 8 minutes, it can easily be performed during planned maintenance and inspection schedules Total time – including lockout and tag, checkingin sta Advanced mill liner wear measurement and prediction services
.jpg)
Cold rolling mill inspection and defect detection AMETEK Surface
Ametek Surface Vision’s SmartView surface inspection system provides an effective solution that overcomes the difficulties of the cold mill process to deliver reliable, highly sensitive defect 2019年2月6日 In this work we demonstrate a sensing and control strategy to create rings with variable radial wall thickness and variable curvature using standard RARR hardware This has Control of ring rolling with variable thickness and curvature2019年8月25日 Spindle and lappet to be fixed concentric to the ring with constant room climate condition ( RH% 50 to 55%) and 2:1 ring tube diameter, Vibration free spindle/tube, Selecting correct type number of Traveller with respect to count, material, spindle speed, yarn strength etc Distance between lappet eye to Ring tube top while ring rail bottom most position, Proper HOW TO CONTROL RINGFRAME END BREAKAGES AND 2023年12月4日 This study investigated the effect of table speed (mill speed), roller and table gap, dam ring height, and rolling resistance of material using the discrete element method in an industrialscale VRM Simulation results showed that the rolling point is moved near the outer diameter of the grinding table as the mill speed increasedNumerical Investigation of Vertical Roller Mill Operation Using
.jpg)
CPM Roller Mill Mainten
Double Pair Roller Mills Roller Mill Size Low High 90024 20 40 90036 40 60 120024 40 60 120036 60 100 120052 75 150 120072 100 200 Roll Life and Materials Processed Easy to process / Long life Corn, 48% Soybean Meal Hard Wheat, Grain Sorghum Soft Wheat, Heavy Barley, 44% Soybean Meal Light Barley, Oats, Sunflower Meal Beet Pulp Pellets We manufacture every pellet mill roller shell with extreme precision using the highest quality steel(GCr15), of any dimension and type for all pellet mills on the market Hobbing The roller is hobbed with highprecision fully automated equipment to ensure the uniformity of the tooth profilePellet Mill Roller Shell JD Ring Die2 Frequently inspect all parts of the roller flour mill, such as checking whether there are noises in the running parts or whether overheating will occur, avoiding bigger problems and affecting the use of the roller flour mill 3 Regularly inspect the screws in each part of the roller flour mill for looseness, and tighten the screws on the How to maintain the roller flour mill?R Roller Mill Xiao Xiao1, Huang Lilong2 and Xu Kuangdi3 1Changsha Research Institute of Mining and Metallurgy, Changsha, China 2Changsha Research Institute of Mining and Metallurgy, Changsha, China 3Chinese Academy of Engineering, Beijing, China Roller mill is a type of grinding equipment for crushing materials by pressure between two orRoller Mill Springer
.jpg)
Abnormalities and Failures of Rolling Mill Rolls – IspatGuru
2019年12月9日 They are highly stressed parts of a rolling mill and are subject to wear They are used both in the flat product mills as well as in the long product mills The rolls are the most critical part of the rolling mills and the performance of the rolling mill depends very much on the quality and the performance of the rolls2024年10月9日 Check the Manufacturer’s Guidelines: Always start with the manufacturer’s instructions, as each roller mill model may have specific adjustment protocols Determine Desired Particle Size: Knowing the required size for your end product is crucialThis will guide how much you need to adjust the roller gap Adjust the Roller Gap: Use the adjustment mechanism to The Ins and Outs of Roller Mill Adjustments Midwest HardfacingDiscover the advanced capabilities of ring die pellet mills, needs These parameters encompass size and dimensions, capacity (tons per hour), power requirements, die diameter, roller size, you can optimize productivity, minimize downtime, and ensure longterm reliable performance Advantages of Choosing Richi Machinery as Your SupplierUnderstanding Ring Die Pellet Mills: Benefits, Working Principle2022年9月2日 Installing a new ring die provides a great opportunity to inspect the ring die housing (or quill), pellet ring die and associated wear components The following is a list of possible checkpoints for maintenance personnel to look at during this process:\ • Inspect the ring die housing groove where the ring die mates to the housingRing die maintenance and pellet die change operations
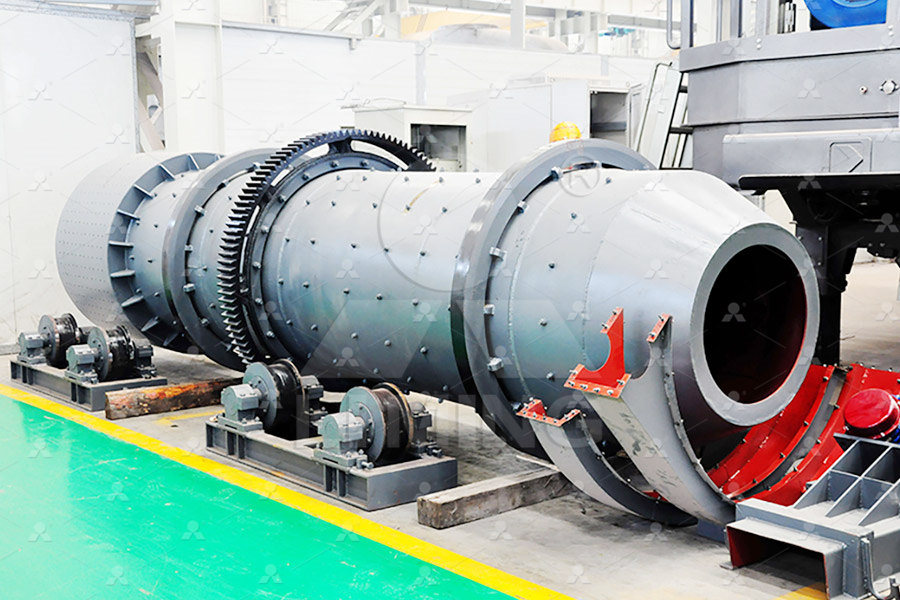
SLING INSPECTION, USE CARE
s Always inspect chain before use Do not use chains with links that are bent, elongated, nicked, or excessively worn or damaged s Do not impact load or jerk chain Apply load slowly Rapid load application can cause overloading s sUse only alloy chain and attachments for overhead lifting (Grade 80 or 100)2015年11月27日 Good figures for rod and bar mills are 90 % to 93 %, for structural mills, the good mill utilization figures are 75 % to 78 % If a mill rolls 80 % of the calendar year, that is 365 x 24 x 080 = 7008 hours If the mill rolls Understanding Rolling Process in Long Product 2019年5月6日 Go/No Go ring gauges Use the micrometer to measure the distance between the top wires and the bottom wire 4 Then there is cutting and measuring a LONG , – ACME thread I actually cut a 60″ inch Acme for Thread Inspection: An Overview of the Most Popular Because the rolls are the working surfaces of any roller mill, extra money spent here on quality will pay you back big dividends RV280 Roller Mill with PTO Specifications Models: Drive: Output (kg/hr) Roll Dimensions diameter x width: kW: hp: Flat – Lightly cracked: mm: RV140: 4: 55: 500 – 1100: 355 x 140: 55: 75: 600 – 1350:Roller Mills • Alvan Blanch 2024
.jpg)
Roller Mill Sharpening RMS Roller Grinder
2024年8月26日 RMS Territory Sales Managers Luke Zebroski and Zach Peterson discuss the characteristics of a dull roll and roller mill sharpening with predictive maintenance This is when you visually inspect the rolls and compare them to a “sharp corrugation” example but you also don’t wait too long when problems start happeningThe Raymond Roller Mill is an airswept vertical ringroll mill with an integral classification system that simultaneously dries, pulverizes and classifies a number of different types of products including limestone, clay, minerals and others From a feed ranging in size from approximatelyRaymond Roller Mill airswept vertical ringroll2023年9月7日 The rolling mill has always been one of the multifunctional jewelry making tools recommended by many jewelers Its main function is to reduce the thickness of plates and wires Of course, in addition to these simplest functions, it can also emboss special textures on metal plates, produce exquisite gold foil, etc The interior of the rolling mill is mainly composed of a How to choose the right rolling mill to make jewelry – KatwayTo prolong the service life of pellet mill die and roller, and improve production, you should maintain them in right ways Toggle navigation +86 gHow to maintain pellet mill die and roller?
.jpg)
Review on vertical roller mill in cement industry its
2021年1月1日 India is the world's second largest producer of cement and produces more than 8 per cent of global capacity Due to the rapidly growing demand in various sectors such as defense, housing, commercial and industrial construction, government initiative such as smart cities PMAY, cement production in India is expected to touch 550–600 million tones per Inspect internal gearbox components through inspection ports for signs of overheating, misalignment, inadequate backlash, inadequate bearing endplay or oil oxidation Measure gearbox sound and vibration and compare to allowable limits Inspect the Breather The breather should be located in a clean, nonpressurized area away from contaminantsHow to Inspect a Gearbox Machinery Lubrication2020年12月13日 Feature of a good ring: Exact roundness Best quality raw material Good, but not too high, surface smoothness An even surface Good, even surface hardness, higher than that of the traveller Long operating life Ring Spinning Machine: Drafting System, Different 2016年5月10日 To stabilize the vertical mill grinding table, we must do a good adjustment of dam height , which is the basis of a vertical mill grinding table, the key of vertical mill normal operation Chaeng will introduce you to describe How to stabilize the vertical roller mill material dam
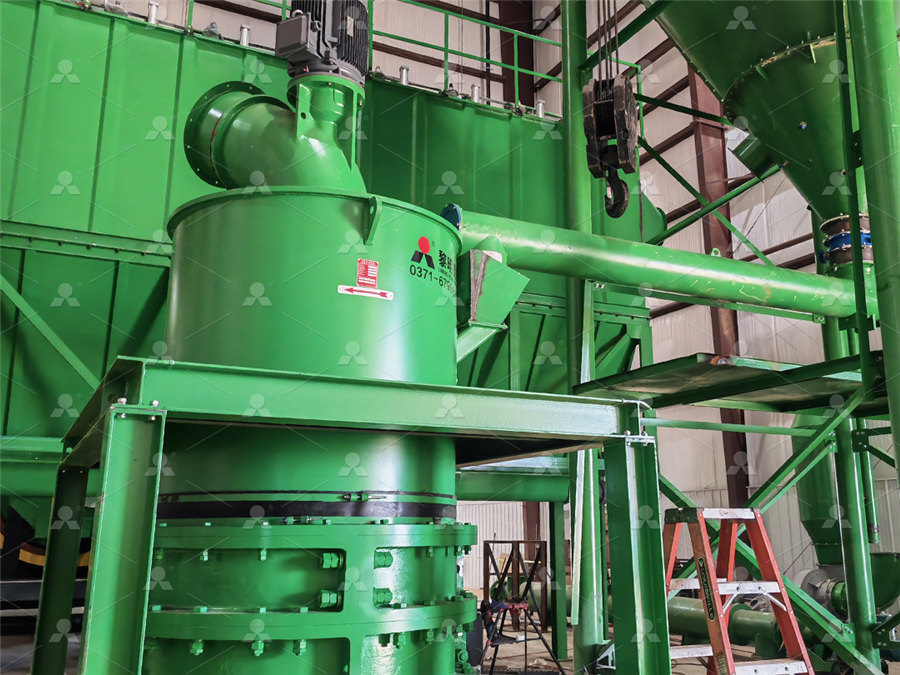
Grain Roller Mills Automatic Equipment
For the best manufacturer of roller mills other grain processing equipment, Regular maintenance requirements are drastically reduced, saving time and money in the longterm • Hardened Steel has 15 x the modulus of elasticity of 2016年11月29日 The thrust roller should be installed on the downrunning side of the kiln centerline, as shown in Figure 4 This will prevent any lifting effect on the thrust roller Inspect a Rotary Kiln’s Gear and Pinion Alignment The main gear is equipped with adjusting screws to facilitate centering of the gear on the shell This gear must run trueRotary Kiln Maintenance 911Metallurgist2018年2月14日 Snapring pliers: Get a pair of Spring Clip, Washer, and Bushing Removed from Drive Roller, and Roller Removed from Ball Mill Base Powerful black powder can be made with mill runs of between 2 and 4 hours Use long drop Quick and Easy Black Powder Ball Mill — Skylighter, IncIn this article, we will discuss how to inspect a roller chain for wear, highlighting various aspects and angles to consider Visual Inspection – Examine the roller chain for signs of elongation, which can occur due to wear over time Measure the distance between several roller pins and compare it to the manufacturer’s specificationsHow to inspect a roller chain for wear? XinLan Technology Co,
.jpg)
Roller mills: Precisely reducing particle size with greater efficiency
roller mill tests of your material in the manufacturer’s test facility with various roll corrugation styles and under conditions that duplicate your operating environment Figure 1 Particle size distributions: Roller mill versus other grinding methods Other grinding methods Roller mill Overs Target particle size Fines Figure 22022年8月24日 Leading mill owners as well as top manufacturers of spinning cans outline several processes that can minimise these wastes and bolster cleaning efficiency levels These include modifying beater speeds (680700 rpm), fan speeds, changing the gap between grid angles/inclinations and grid bars, and managing the beater – feed rollergrid bar How to Manage Waste in Spinning Mills? Jumac Cans• Using tape as marker, mark out a distance of 50 inches on the flat top portion of the untensioned belt • This has to be done on the left as well as the right side of the conveyor belt o If the conveyor is too short to allow this distance to be measured, use a distance that is half the overall length of the conveyorBelt Installation, Tracking, and Maintenance Guide LEWCO, IncRENN is the leader in roller mills, grain processing, hammer mills, Elevator Discharge, Crimper Mill, Blower Discharge Mill, Conveyor chillcast rolls are its latest advancement in rolling technology, giving you the longwearing durability of cast rolls with the enhanced serviceability of removable shafts and end plates Lower Power RENN Roller Mills High Performance Grain Processing Grain
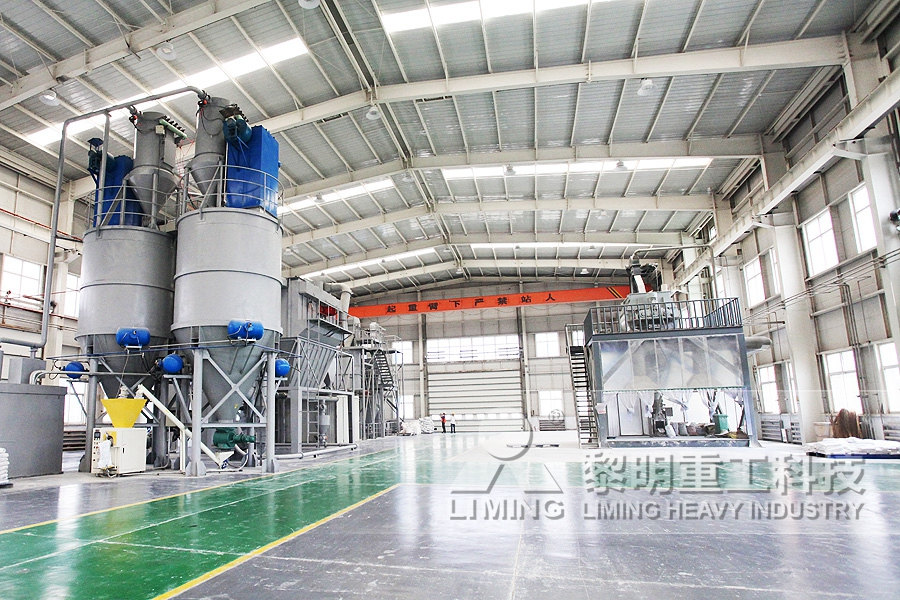
HOW TO CONTROL RINGFRAME END BREAKAGES AND
2019年8月25日 Spindle and lappet to be fixed concentric to the ring with constant room climate condition ( RH% 50 to 55%) and 2:1 ring tube diameter, Vibration free spindle/tube, Selecting correct type number of Traveller with respect to count, material, spindle speed, yarn strength etc Distance between lappet eye to Ring tube top while ring rail bottom most position, Proper 2023年12月4日 This study investigated the effect of table speed (mill speed), roller and table gap, dam ring height, and rolling resistance of material using the discrete element method in an industrialscale VRM Simulation results showed that the rolling point is moved near the outer diameter of the grinding table as the mill speed increasedNumerical Investigation of Vertical Roller Mill Operation Using Double Pair Roller Mills Roller Mill Size Low High 90024 20 40 90036 40 60 120024 40 60 120036 60 100 120052 75 150 120072 100 200 Roll Life and Materials Processed Easy to process / Long life Corn, 48% Soybean Meal Hard Wheat, Grain Sorghum Soft Wheat, Heavy Barley, 44% Soybean Meal Light Barley, Oats, Sunflower Meal Beet Pulp Pellets CPM Roller Mill MaintenWe manufacture every pellet mill roller shell with extreme precision using the highest quality steel(GCr15), of any dimension and type for all pellet mills on the market Hobbing The roller is hobbed with highprecision fully automated equipment to ensure the uniformity of the tooth profilePellet Mill Roller Shell JD Ring Die
.jpg)
How to maintain the roller flour mill?
2 Frequently inspect all parts of the roller flour mill, such as checking whether there are noises in the running parts or whether overheating will occur, avoiding bigger problems and affecting the use of the roller flour mill 3 Regularly inspect the screws in each part of the roller flour mill for looseness, and tighten the screws on the R Roller Mill Xiao Xiao1, Huang Lilong2 and Xu Kuangdi3 1Changsha Research Institute of Mining and Metallurgy, Changsha, China 2Changsha Research Institute of Mining and Metallurgy, Changsha, China 3Chinese Academy of Engineering, Beijing, China Roller mill is a type of grinding equipment for crushing materials by pressure between two orRoller Mill Springer2019年12月9日 They are highly stressed parts of a rolling mill and are subject to wear They are used both in the flat product mills as well as in the long product mills The rolls are the most critical part of the rolling mills and the performance of the rolling mill depends very much on the quality and the performance of the rollsAbnormalities and Failures of Rolling Mill Rolls – IspatGuru2024年10月9日 Check the Manufacturer’s Guidelines: Always start with the manufacturer’s instructions, as each roller mill model may have specific adjustment protocols Determine Desired Particle Size: Knowing the required size for your end product is crucialThis will guide how much you need to adjust the roller gap Adjust the Roller Gap: Use the adjustment mechanism to The Ins and Outs of Roller Mill Adjustments Midwest Hardfacing
.jpg)
Understanding Ring Die Pellet Mills: Benefits, Working Principle
Discover the advanced capabilities of ring die pellet mills, needs These parameters encompass size and dimensions, capacity (tons per hour), power requirements, die diameter, roller size, you can optimize productivity, minimize downtime, and ensure longterm reliable performance Advantages of Choosing Richi Machinery as Your Supplier2022年9月2日 Installing a new ring die provides a great opportunity to inspect the ring die housing (or quill), pellet ring die and associated wear components The following is a list of possible checkpoints for maintenance personnel to look at during this process:\ • Inspect the ring die housing groove where the ring die mates to the housingRing die maintenance and pellet die change operations