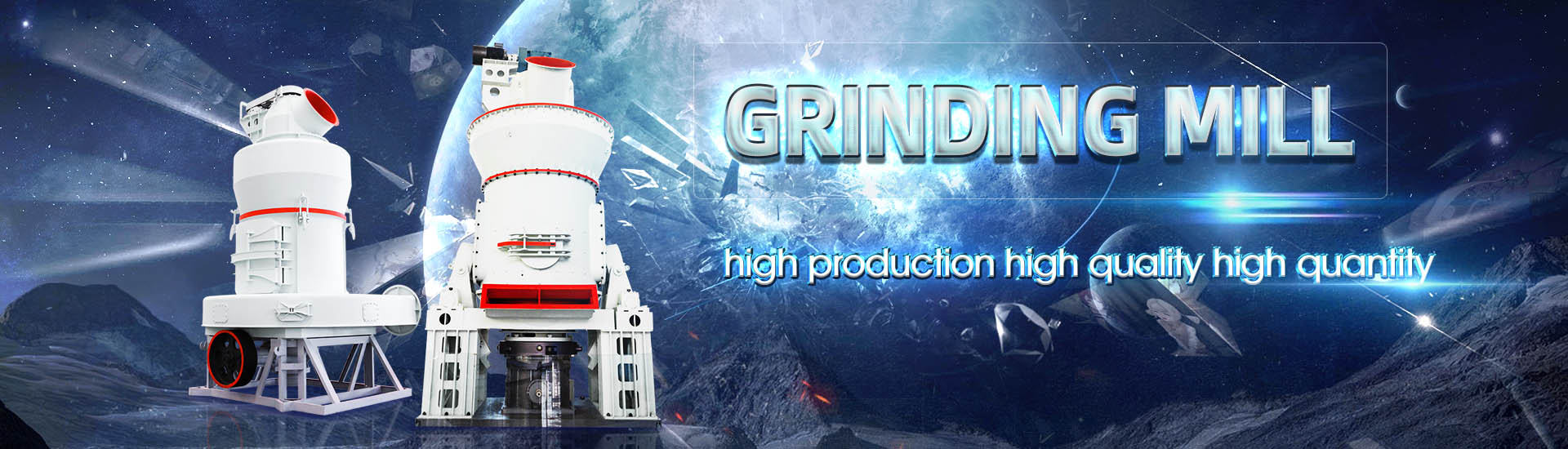
Grinding and selection operation area
.jpg)
Pocket Guide to Grinding Technique Atlas Copco
Grinding is often used as a general term for all kinds of material removal with abrasive tools, regardless of the purpose of the operation It’s certainly a complex subject, difficult to define This chapter provides practical data for the selection of grinding and finishing operations applied to these industrial sectors and includes a guide on the selection of grinding wheels, dressing Grinding Operation an overview ScienceDirect Topics2016年11月22日 Grinding efficiency is one of the most important considerations in the selection of grinding operation conditions because it has a significant impact on the productivity, quality, energy consumption and costEffect of different parameters on grinding efficiency 25 行 Grinding is a term used in modern manufacturing practices to describe machining with highspeed abrasive wheels, pads, and belts Grinding wheels come in a wide variety of Grinding (Machining) an overview ScienceDirect Topics
.jpg)
GRINDING PROCESS
Grinding Fluids The correct selection of grinding fluid can greatly affect the grinding process Grinding fluids serves for – Reduce temperature in the work piece – Lubricate the contact area Highpressure grinding is the optimal process for removing scale, cracks and other surface defects Grinding largescale rounded parts however, requires specific grinding facilitiesTECHNICAL SOLUTIONS FOR CUTTING GRINDING Norton grinding operations are divided into two basic types External cylindrical grinding which is similar to external turning The wheel Internal cylindrical grinding operates somewhat like a boring Lesson 6 GRINDING AND OTHER ABRASIVE PROCESSES KSU2018年4月12日 This paper reviews a selection of areas in which the application of scientific principles and engineering ingenuity has led to the development of new grinding processes, abrasives, tools, machines, and systemsTowards High Productivity in Precision Grinding MDPI
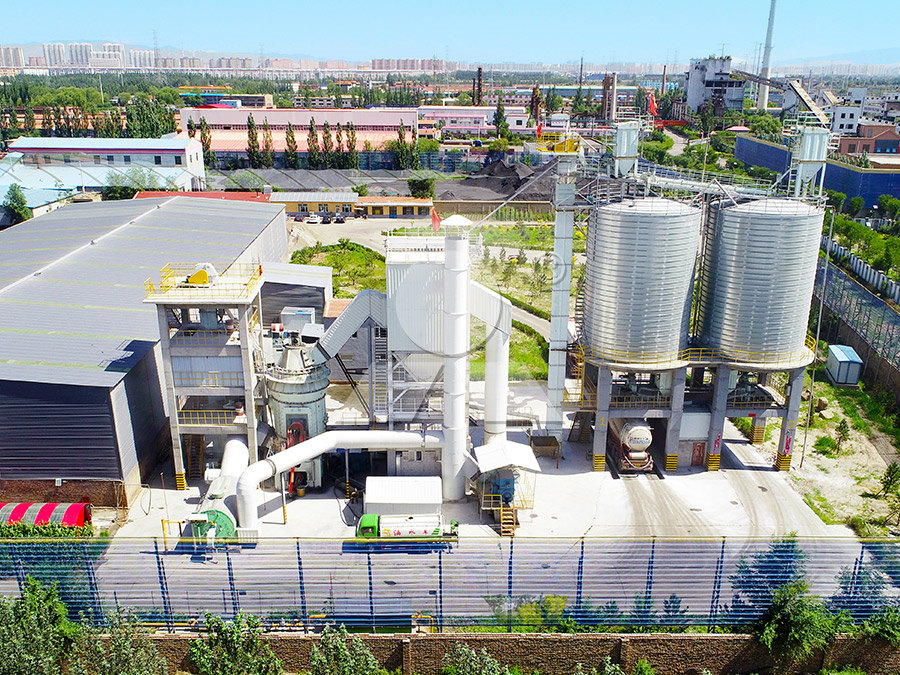
Optimization of grinding processes using multicriteria decision
2024年1月31日 Azizi et al investigated the influences of different dressing and grinding parameters on specific grinding energy, Gratio and SR, and optimized the grinding operation 2021年6月18日 Area of contact, the fourth factor we consider, is in part related to the second factor: severity of operation, in that it considers the amount (or area) of contact between the work and the wheel This factor looks at how the The 7 Factors Used to Determine a Grinding Wheel Grinding – Ex 11 • You are grinding a steel, which has a specific grinding energy (u) of 35 Ws/mm3 • The grinding wheel rotates at 3600 rpm, has a diameter (D) of 150 mm, thickness (b) of 25 mm, and (c) 5 grains per mm2 The motor has a power of 2 kW • The work piece moves (v) at 15 m/min The chip thickness ratio (r) is 10Grinding and Finishing IIT Bombay2024年9月27日 Basic Operations and StepbyStep: Wheel Selection: Choose the grinding wheel based on the workpiece material, type of grinding, and desired surface smoothness Machine Setup: Adjust the grinder to set the wheel What is Grinding: Definition, Types, Uses, and Working
.jpg)
Guidelines for Selecting Grinding Wheels Hindustan Abrasives
The severity of the grinding operation also influences the ‘grade’ Hard grades provide durable wheels for rough grinding such as snagging, while medium and soft grade wheels are generally used for less severe precision grinding operations Selecting right grinding wheel for a specific application, if properly understood, is not difficult2024年1月27日 Clean Work Area: Keep the area around the grinding machine clean and free of debris, which can be a tripping hazard or interfere with the operation of the machine Fire Safety: Be aware of fire hazards, especially when grinding metals that can create sparksWhat is a Grinding Machine: Definition, Types, ComponentsThere are 6 key factors that affect the selection of the right grinding wheel: 1) the material and hardness of the workpiece, 2) the amount of stock removal and required finish, 3) whether grinding is wet or dry, 4) the wheel speed, 5) the area of grinding contact, and 6) the severity of the grinding operation The abrasive, grit size, grade, and bond type must be chosen based on Factors Affect Selection PDF Grinding (Abrasive Cutting)SELECTION OF GRINDING WHEELS Grinding wheels wear unevenly under most general grinding operations due to uneven pressure applied to the face of the wheel when it cuts (Figure 516) Note that the belt and pulleys are exposed; during actual operation, this area should be covered with a guardGrinding process

Precision Grinding Stainless Steel Advance Grinding Services
Wheel Speed and Bond Selection The speed at which the wheel rotates determines the type of bond to be useful in the grinding process Conventional grinding wheels with organic adhesives provide smooth grinding at lower speeds, while vitrified bonds best Optimize your surface grinding operations with expert tips on wheel grades, The point is to research your available options and not settle for second best during the grinding wheel selection process Operational Success A fire suppression system is also a good idea, and might be a safety requirement in your area In either case, How to Master Your Surface Grinding Machining Operation2017年1月25日 1 Compositional specifications Specification of a grinding wheel ordinarily means compositional specification Conventional abrasive grinding wheels are specified encompassing the following parameters 1) the type of grit material 2) the grit size 3) the bond strength of the wheel, commonly known as wheel hardness 4) the structure of the wheel Grinding wheel designation and selection PPT Free DownloadGrinding lowalloy tool steels seldom presents any difficulties When grinding highalloy tool and highspeed steels with high carbide content, however, problems can easily occur For this reason, the grinding parameters must be selected carefully The higher the wear resistance of a steel, the more difficult it is to grindGRINDING FOR TOOLMAKING voestalpine BÖHLER US
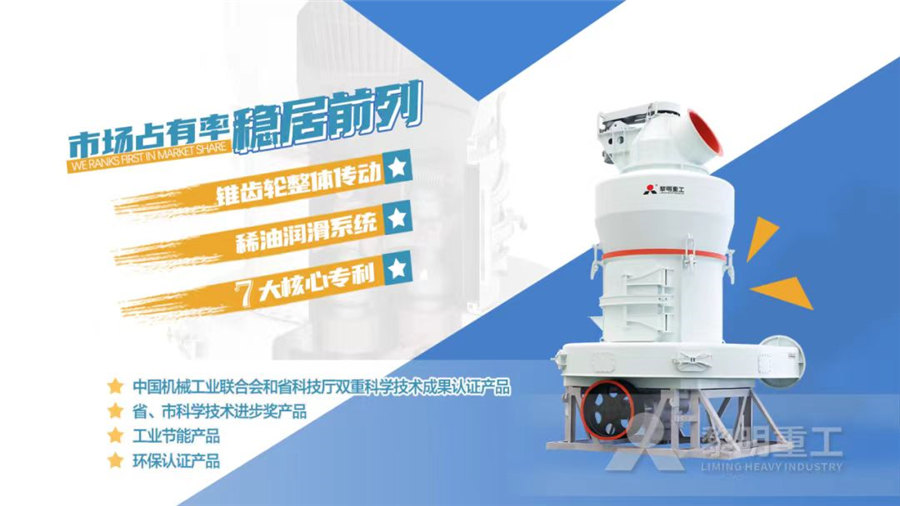
Pocket Guide to Grinding Technique Atlas Copco
a selection guide chart and an illustration of tools in a typical working environment many over lapping areas In fact, the transition from grinding to sanding, cleaning and polishing is gradual, often with no clear What’s the main purpose of the grinding operation?2024年9月2日 The grain size is selected based on the surface finish required on the workpiece ie for a rough grinding, course or medium grain size is selected and for finished grinding fine or very fine grain size will be selected 1024= Grinding MCuiz Objective Question with Answer 2022年7月16日 Mostly grinding wheels are used for metal removal, dimensioning, and finishing Grinding Wheel selection guide will help you choose the right wheel 90 Days Return If Goods Have Problem Select category Select category; If your project requires a closer and more precise operation over a small area of contact, Grinding Wheel Selection Guide Agrindtool2003年1月1日 Mining is typically conducted through a set of interdependent unitoperations, which commonly include drilling, blasting, digging and hauling, in order to deliver the required ore material into (PDF) The Effects of Blasting on Crushing and Grinding
.jpg)
Grinding Process SpringerLink
In the case of some grinding, honing, and free abrasive grinding operations with bonded grains, cutting edge engagement is also force bound It is hereby often the case that the grain remains relatively fixed and penetrates into the workpiece at a predetermined path by the relative movement between the tool and the workpiece (Fig 3)The correct selection of tools, workholding, cutting parameters, and milling techniques can significantly impact the quality, accuracy, and cost of the final part In this section, we will explore the essential aspects of milling, including the types of milling operations, cutting parameters, and milling strategies to achieve optimal resultsMilling Machines and Operations – EngineeringTechnologyCHAPTER SEVEN: Grinding Operation The Grinding Wheel Grinding Wheel Parameters 2002©John Wiley Sons, Inc M P Groover, “Fundamentals of Modern Manufacturing 2/e” −Denser wheel structure = more grits per wheel area Why Specific Energy in Grinding is High 2002 ©John Wiley Sons, Inc M P Groover, Lesson 6 GRINDING AND OTHER ABRASIVE PROCESSES KSUBasic Grinding Theory provides an overview of the general process of grinding Grinding occurs at the point of contact between an abrasive wheel and a workpiece Like any other cutting process, grinding removes material in the form of chips In order for a wheel to grind properly, its abrasive grains must wear and selfsharpen at a consistent rateBasic Grinding Theory 221 Tooling USME
.jpg)
SELECTION AND USE OF GRINDING WHEELS
2020年1月3日 Contact area is probably the chief factor in grade selection on vertical grinders since the stresses arising from contact between wheel and work are greatest in this type of grinding operationA Comprehensive Guide to Tool Grinding Wheel Selection and Usage Proper usage is contingent upon two key areas: Wheel Maintenance and Operational Techniques Wheel Maintenance Thus, the successful performance of A Comprehensive Guide to Tool Grinding Wheel 2021年4月16日 Grinding hand tools A die grinder is a highspeed rotary tool that is typically powered by compressed air The tool has a smalldiameter abrasive bit that rotates to get the job done Check out Choosing the Right Air Intro to Grinding Methods, Machines and ToolsWhen the area of contact in grinding operation is large, total grinding pressure is distributed over a larger area and the pressure per unit area is less and hence a softer wheel is needed for it Thus for internal grinding where arc of contact is Grinding Wheel Selection – Constant and Variable
.jpg)
Selection of Grinding Wheels Machining Industries Metallurgy
When the area of contact in grinding operation is large, total grinding pressure is distributed over a larger area and the pressure per unit area is less and hence a softer wheel is needed for it Thus for internal grinding where arc of contact is more, softer wheel is used and for external grinding, harder wheel Condition of Grinding Machine:2021年7月3日 Made in the USA Season 2 Episode 6: Why, and How, Hardinge is Reshoring Machine Tool Production In this episode of Made in the USA, several executives and senior staff at Hardinge give their firstperson account of how they formulated the plan to shift the manufacturing of its milling and turning product lines from its Taiwan plant to its plant in Elmira, Machining 101: What is Grinding? Modern Machine ShopGrinding Wheel Selection for Cylindrical Grinding The listing of grinding wheel specifications for commonly used materials (on page 80) serves the purpose of general information only It may be used as a first approach in grinding wheel selection for cylindrical grinding operations, should more pertinent data, as from comparable past operations, not be availableGRINDING FEEDS AND SPEEDS ABRASIVE ENGINEERING2013年1月1日 Some areas of grinding technology overlap grinding operations but also for the extensions of grinding into the areas of lapp ing, by selection of suitable grinding conditionsPrinciples of Modern Grinding Technology ResearchGate
.jpg)
Grinding Discs: Different Factors that Can Affect Product Selection
2024年7月12日 Explore key factors affecting grinding discs selection and discover Newlands Fasteners' extensive range of highquality discs for any grinding job while harder grades are used for smaller areas Severity of Operation The severity of the grinding operation, including the grinding pressure and force per grain, Factors Influencing Selection Several factors come into play when selecting the right grinding wheel for a specific application Let’s explore some of the key considerations: Material to be Ground: Different materials require different abrasive grains and bond materialsFor example, grinding steel may necessitate an aluminum oxide wheel, while grinding carbide tools may Choosing the Right Grinding Wheel: A Guide to SelectionFor a broad area of contact, use a wheel with coarser grit and softer grade This ensures a free, cool cutting action under the heavier load imposed by the size of the surface to be ground Smaller areas of grinding contact require wheels with finer grits and harder grades to withstand the greater unit pressureGrinding Wheel Selection Made Easy: Insider Tips and Tricks2021年6月18日 Area of contact, the fourth factor we consider, is in part related to the second factor: severity of operation, in that it considers the amount (or area) of contact between the work and the wheel This factor looks at how the The 7 Factors Used to Determine a Grinding Wheel
.jpg)
Grinding and Finishing IIT Bombay
Grinding – Ex 11 • You are grinding a steel, which has a specific grinding energy (u) of 35 Ws/mm3 • The grinding wheel rotates at 3600 rpm, has a diameter (D) of 150 mm, thickness (b) of 25 mm, and (c) 5 grains per mm2 The motor has a power of 2 kW • The work piece moves (v) at 15 m/min The chip thickness ratio (r) is 102024年9月27日 Basic Operations and StepbyStep: Wheel Selection: Choose the grinding wheel based on the workpiece material, type of grinding, and desired surface smoothness Machine Setup: Adjust the grinder to set the wheel What is Grinding: Definition, Types, Uses, and Working The severity of the grinding operation also influences the ‘grade’ Hard grades provide durable wheels for rough grinding such as snagging, while medium and soft grade wheels are generally used for less severe precision grinding operations Selecting right grinding wheel for a specific application, if properly understood, is not difficultGuidelines for Selecting Grinding Wheels Hindustan Abrasives2024年1月27日 Clean Work Area: Keep the area around the grinding machine clean and free of debris, which can be a tripping hazard or interfere with the operation of the machine Fire Safety: Be aware of fire hazards, especially when grinding metals that can create sparksWhat is a Grinding Machine: Definition, Types, Components
.jpg)
Factors Affect Selection PDF Grinding (Abrasive Cutting)
There are 6 key factors that affect the selection of the right grinding wheel: 1) the material and hardness of the workpiece, 2) the amount of stock removal and required finish, 3) whether grinding is wet or dry, 4) the wheel speed, 5) the area of grinding contact, and 6) the severity of the grinding operation The abrasive, grit size, grade, and bond type must be chosen based on SELECTION OF GRINDING WHEELS Grinding wheels wear unevenly under most general grinding operations due to uneven pressure applied to the face of the wheel when it cuts (Figure 516) Note that the belt and pulleys are exposed; during actual operation, this area should be covered with a guardGrinding processWheel Speed and Bond Selection The speed at which the wheel rotates determines the type of bond to be useful in the grinding process Conventional grinding wheels with organic adhesives provide smooth grinding at lower speeds, while vitrified bonds best Precision Grinding Stainless Steel Advance Grinding ServicesOptimize your surface grinding operations with expert tips on wheel grades, The point is to research your available options and not settle for second best during the grinding wheel selection process Operational Success A fire suppression system is also a good idea, and might be a safety requirement in your area In either case, How to Master Your Surface Grinding Machining Operation
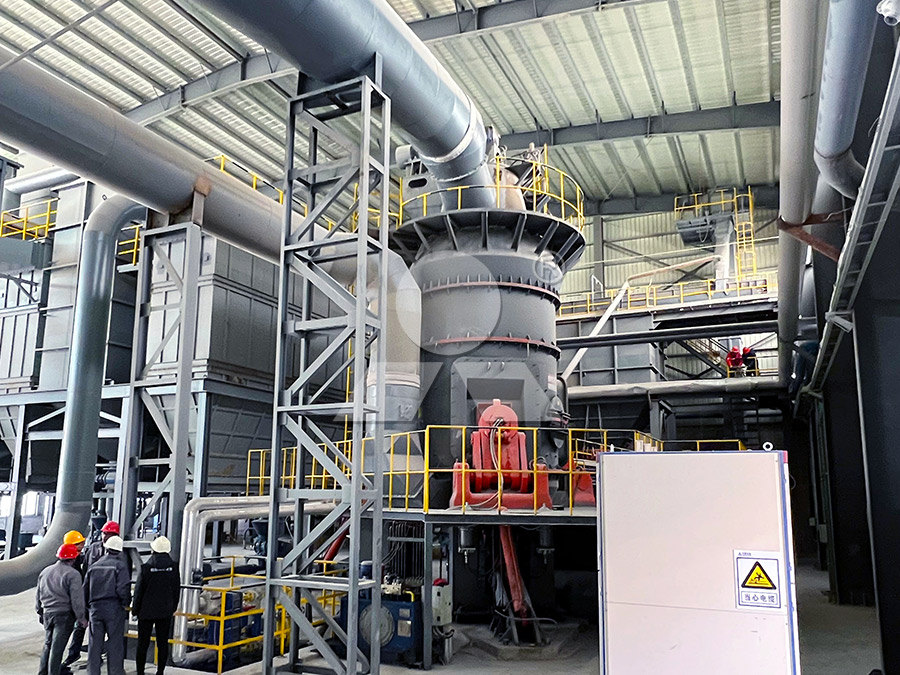
Grinding wheel designation and selection PPT Free Download
2017年1月25日 1 Compositional specifications Specification of a grinding wheel ordinarily means compositional specification Conventional abrasive grinding wheels are specified encompassing the following parameters 1) the type of grit material 2) the grit size 3) the bond strength of the wheel, commonly known as wheel hardness 4) the structure of the wheel