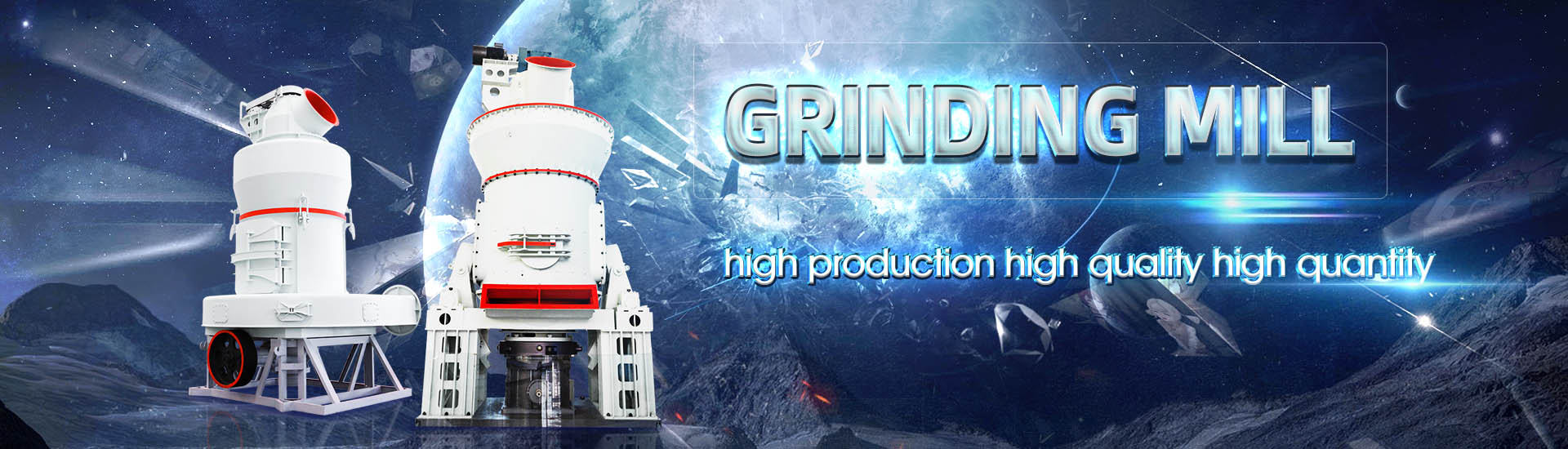
The discharge particle size of the ore mill is ≤ mm.
46.jpg)
Comparison of measured and predicted PSD of mill discharge
In this study, the perfect mixing model was used to investigate its accuracy level, under different laboratory conditions, in predicting the particle size distribution of industrial ball2023年10月27日 From the study, the optimal media size was 40 mm for a feed size of −2 + 045 mm and 30 mm for a feed size of −045 + 015 mm Cayirli also agrees with the fact that larger A Review of the Grinding Media in Ball Mills for Mineral Processing 2020年1月1日 Discharge of desired particle size is directly related to critical speed of the mill Mill with lifters has maximum discharge of desired particle size Mill with lifters has minimum A comparative study on a newly designed ball mill and the 2023年7月20日 Grinding operation quality indices mainly include four aspects (1) Grinding fineness, which is the percentage of the ore particles less than pecified size after being Ore Grinding SpringerLink
.jpg)
All About Particles: Modelling Ore Behaviour in Mineral Elements
events undergone by individual ore particles depend on particle properties such as size, shape, mineralogy, and texture For instance, the largest and smallest particles in a tumbling mill The calculation [810] reveals that when D (size of steel ball) = 25 mm and n (rotation speed of mill) ≤ 1234 rpm, the steel balls inside the mill attain the state of cascading, and the reduction PAPER OPEN ACCESS You may also like IOPscience2020年1月3日 Ball mills are progressively used to grind the ores for particle size reduction and to liberate valuable minerals from the ores The grinding of ore is a highly energyintensive Estimation of Grinding Time for Desired Particle Size Distribution 2017年3月20日 An effect of a grinding method, that is ball mill and high pressure grinding rolls (HPGR), on the particle size, specific surface area and particle shape of an iron ore Physicochemical Problems of Mineral Processing Investigation on
.jpg)
Effect of ball and feed particle size distribution on the milling
2018年6月1日 A number of researchers (Deniz, 2012; Bwalya et al, 2014; Petrakis et al, 2016) carried out studies about the effect of feed particle size and grinding media size on the grinding kinetics of different oresKhumalo et al, 2006 postulated that generally larger sized grinding media would break larger particles quicker but a finer product would be obtained by use of 2023年7月27日 The single grinding circuit composed of mill and grading operation is suitable for grinding products with the required particle size of P 80 ≥ 106 microns (equivalent to particle mass passing 0074 mm sieve less than 65%) There are four types of onestage grindingclassification circuits (Fig 1): onestage closed circuit grinding circuit with integrated preclassification and GrindingClassification Circuit SpringerLink2019年8月14日 • Peripheral ball mill: Discharge the ore through the periphery of the cylinder However,if there are too many large steel balls in the cylinder of ball mill, the grinding particle size will be too coarse, that is undergrinding typically 50150 mm The smooth ball mill liner is used for the fine grinding bin, The Ultimate Guide to Ball Mills MiningpediaThe calculation [810] reveals that when D (size of steel ball) = 25 mm and n (rotation speed of mill) ≤ 1234 rpm, the steel balls inside the mill attain the state of cascading, and the reduction in particle size is induced by the abrasion action Lowspeed grinding tests are performed for pyrite and quartz at threePAPER OPEN ACCESS You may also like IOPscience
.jpg)
(PDF) Power consumption management and simulation of
2022年3月15日 These mills consume enormous amounts of electrical energy (5060%); consequently, comminution costs roughly 60% of the overall investment in a beneficiation plant [2,3]Comminution Characterization studies 1 Introduction Ball mills are progressively used to grind the ores for particle size reduction and to liberate valuable minerals from the ores The grinding of ore is a highly energyintensive process [1–4] In this process, the size of the particle obtained depends on the energy consumption of the ball mill(PDF) Estimation of Grinding Time for Desired Particle Size 2020年5月28日 The feed samples of X, Y, and Z iron ores were ground in the BBM (ball mill refers to a BBM of size 300 mm × 300 mm with smooth liners) to identify the PSD, BWI, and RT of each ore Grinding experiments were conducted according to Bond’s standard test procedure []For each iron ore sample, the RT taken to produce 250% circulating load in the BBM was Investigation on Iron Ore Grinding based on Particle Size Distribution The shape of crushed ore affects the product particle size in a ball mill grinding circuit It has also been proposed that green pellet quality is directly related to the amount of fine particles in a pelletizing plant (Dwarapudi et al, 2008; Umadevi et al, 2008; Gul et al, 2014; Van der Meer, 2015) Particle size distributionInvestigation on the particle size and shape of iron ore pellet feed
.jpg)
Grinding SpringerLink
2022年2月28日 An investigation conducted on magnetite ore grinding with a dry HPGR machine to reduce the particle size from 50 mm to 90 µm has revealed that using two stages HPGR closed circuit with an air classifier can reduce energy consumption by 46% compared to a circuit in which there is a tertiary crushing with a wet ball mill2020年3月20日 Rod mill:The rod mill has the highest efficiency when the feed size is 30mm and the discharge size is about 3mm with uniform particle size and light minerals with mud (can omit ore washing) Feeding size: ≤25mm: ≤50mm: 300400mm: Capacity : 062—180t/h: 065—615t/h: Ball mill: When the particle size of the product What’s the Difference Between Ball Mill, Rod Mill and SAG Mill?2016年6月6日 For circuits classifying mill discharge at a coarse size (coarser than approximately 10 mm), trommels can also be considered to classify mill discharge Four 1067 x 2400 mm vibrating feeders under the coarse ore SAG Mill Grinding Circuit Design 911MetallurgistAs stated, the mill feed size distribution data are summarised into three fractions: the fine fraction is interpreted as minus mill discharge grate size material, the medium fraction as critical size and the coarse fines, minimising the % medium while maintaining adequate % coarse is the objective of mill feed size optimisation ResultsThe Importance of Primary Crushing in Mill Feed Size Optimization
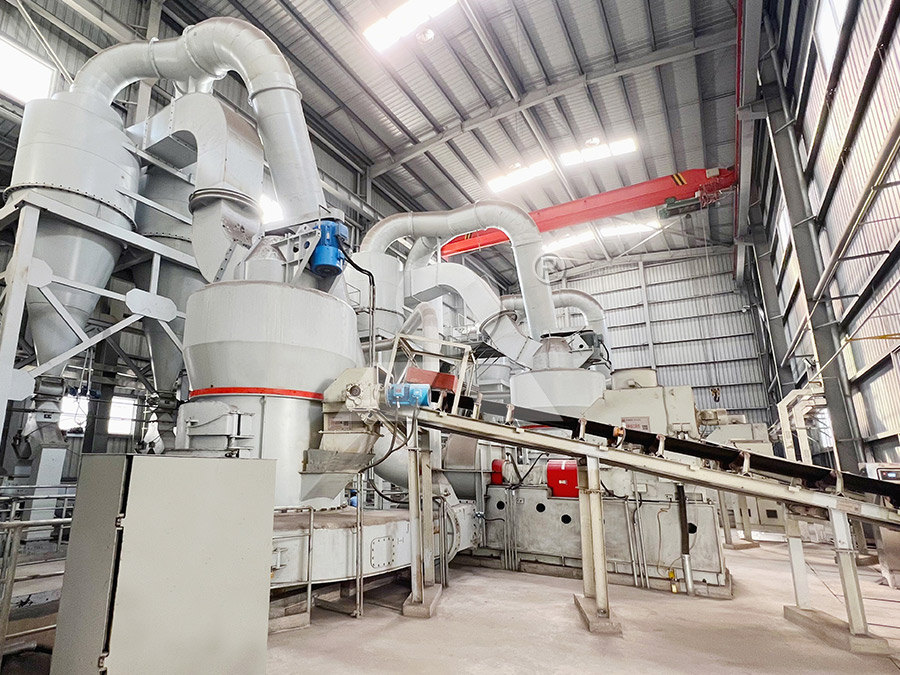
Investigation on the particle size and shape of iron ore pellet feed
Investigation on the particle size and shape of iron ore pellet feed using ball mill and HPGR 909 areas of 500–1600 cm2 g1The concentrate must therefore be reground in order to2016年1月1日 The feed size to the HPGR in some Brazilian mines is 90% passing 1 mm [3], but the use of coarser feed sizes (16–50 mm) was reported by Patzelt et al [15] At Argyle diamonds, (Australia), Maxton [23] reported charging feed size of 80% passing 75 mm with lumps up to Roll Crushers ScienceDirect2015年9月1日 Simulation of overflow ball mill discharge while modelling of the slurry component is best done using a compatible particle fill of ball sizes ranging from 32 – 65 mm The full ball size Simulation of overflow ball mill discharge and trommel flow using finished particle size is the screen Any material that enters the grinding chamber must be reduced to a size small enough to pass through the screen that covers the mill's discharge opening Because of this the screen size generally provides 70% or more of the control over the finished particle sizeIntro to Size Reduction Schutte Hammermill
.jpg)
Jaw Crusher for Primary Crushing Fote Machinery
Maximum feed size: ≤1,200 mm Discharge particle size: 10 – 350 mm Capacity: 1 – 1,200 t/h 2 HD German type jaw crusher HD series jaw crusher is developed by FTM Machinery combined with German crushing technology The large inclination angle of the toggle plate makes the output higher and the particle size more uniform即时翻译文本完整的文档文件。为个人和团队提供准确的翻译。每天有数百万人使用DeepL进行翻译。DeepL翻译:全世界最准确的翻译 DeepL Translate2017年3月4日 Stamp mill ,Crusher , AG mill, SAG mill, Pebble m ill, Ball mill , Rod mill A stamp mill (or stamp battery or stamping mill) is a type of mill machine that cru shes material bySIZE REDUCTION BY GRINDING METHODS ResearchGateThe particles size distribution slope is not affected by the mill speed (see Graph 2) as the curves are mostly overlapping Density These tests were done with a ∅082 x 1 m grate discharge mill with a 30 mm graded ball charge and a 30% filling degree The mill discharge pulp density was increased from 688% to 759% solidsThe influence of mill speed and pulp density on the grinding
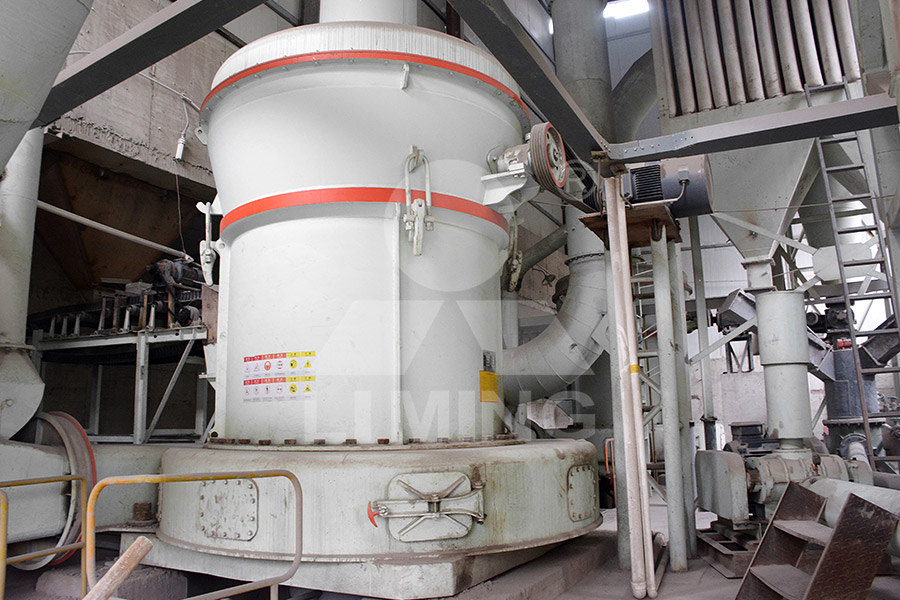
PREDICTING THE PRODUCT PARTICLE SIZE DISTRIBUTION FROM
VTM mill processing copper ore Figure 55 Measured (points) and predicted (dotted lines) product particle size distribution using 950 mm grinding media 89 Figure 61 Breakage and selection functions curves for an aggregate sample Vertimill discharge sample 2021年10月14日 1011 Pulp Feeding Tank In general, the hydrocyclone feed is conveyed by a pumping system coupled to the pulp discharge from a mill The pumping system consists of a tank that receives the pulp discharge from the grinding mill, a centrifugal pump driven by an electric motor, a transmission system of pulleys and trapezoidal belts and a piping systemHydrocyclone System Design SpringerLink2016年7月7日 The ore particle size changed after leaching, compared with the original ore size, the proportion of the same size of 2–5 mm ore decreased to 4464% Ore with particle size of 2–5 mm was most Effect of Particle Size and Grinding Time on Gold Effect of ball and feed particle size distribution on the milling efficiency of a ball mill: An attainable region approach N Hlabangana a, G Danha b, *, E Muzenda b a Department of Chemical Engineering, National University of Science and Technology, P O Box AC 939, Ascot Bulawayo, Zimbabwe b Department of Chemical, Materials and Metallurgical Engineering, College of Effect of ball and feed particle size distribution on the milling

Particle Size Reduction and Enlargement ScienceDirect
2019年1月1日 Particle size reduction and enlargement are regular operations for many industries and discharge of the product is impeded so that the material remains in the crusher for a longer period In the rod mill, high carbon steel rods about 50 mm diameter and extending the whole length of the mill are used in place of balls2021年7月6日 MLA tests showed that the particlebed breakage did not significantly improve the liberation degree compared to the ball mill grinding; the maximum difference of the proportion of 80100% Comminution a Heart of Mineral Processing ResearchGate2020年1月1日 The rotating mill is filled with three steel balls of sizes 25 mm, 40 mm and 50 mm with 45%, 40% and 15% weight percentage, it is fed with −3 mm particles size of iron ore slurry having a slurry density of 21 kg/m 3 which leads to A comparative study on a newly designed ball mill and the VTM mill processing copper ore Figure 55 Measured (points) and predicted (dotted lines) product particle size distribution using 950 mm grinding media 89 Figure 61 Breakage and selection functions curves for an aggregate sample Vertimill discharge sample PREDICTING THE PRODUCT PARTICLE SIZE DISTRIBUTION FROM

Ball Mill Mining Grinding Mill JXSC Machinery
Feeding size: ≤2025 mm Output size: 007406 mm Application: Gold, rock, sand, cement, quartz, center discharge ball mills; Lattice type ball mills: Peripheral row ore type ball mills Batch small ball mill: control the particle size of the material by adjusting the grinding time2015年4月9日 Maximum throughput is about 20 tons per hour The feed size is normally kept fairly small Although final product size can be as low as 0005 mm, this type of mill is often used for less fine applications Product size and shape is a function of the time spent in the mill, media type and size, and frequency of vibration Stirred media millsGrinding Mills and Their Types – IspatGuru2018年6月1日 A number of researchers (Deniz, 2012; Bwalya et al, 2014; Petrakis et al, 2016) carried out studies about the effect of feed particle size and grinding media size on the grinding kinetics of different oresKhumalo et al, 2006 postulated that generally larger sized grinding media would break larger particles quicker but a finer product would be obtained by use of Effect of ball and feed particle size distribution on the milling 2023年7月27日 The single grinding circuit composed of mill and grading operation is suitable for grinding products with the required particle size of P 80 ≥ 106 microns (equivalent to particle mass passing 0074 mm sieve less than 65%) There are four types of onestage grindingclassification circuits (Fig 1): onestage closed circuit grinding circuit with integrated preclassification and GrindingClassification Circuit SpringerLink
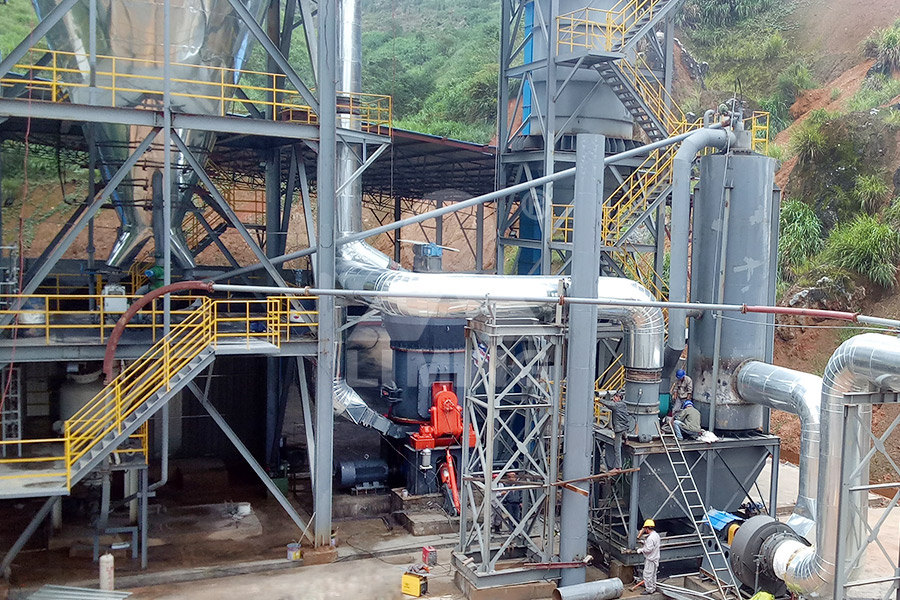
The Ultimate Guide to Ball Mills Miningpedia
2019年8月14日 • Peripheral ball mill: Discharge the ore through the periphery of the cylinder However,if there are too many large steel balls in the cylinder of ball mill, the grinding particle size will be too coarse, that is undergrinding typically 50150 mm The smooth ball mill liner is used for the fine grinding bin, The calculation [810] reveals that when D (size of steel ball) = 25 mm and n (rotation speed of mill) ≤ 1234 rpm, the steel balls inside the mill attain the state of cascading, and the reduction in particle size is induced by the abrasion action Lowspeed grinding tests are performed for pyrite and quartz at threePAPER OPEN ACCESS You may also like IOPscience2022年3月15日 These mills consume enormous amounts of electrical energy (5060%); consequently, comminution costs roughly 60% of the overall investment in a beneficiation plant [2,3](PDF) Power consumption management and simulation of Comminution Characterization studies 1 Introduction Ball mills are progressively used to grind the ores for particle size reduction and to liberate valuable minerals from the ores The grinding of ore is a highly energyintensive process [1–4] In this process, the size of the particle obtained depends on the energy consumption of the ball mill(PDF) Estimation of Grinding Time for Desired Particle Size
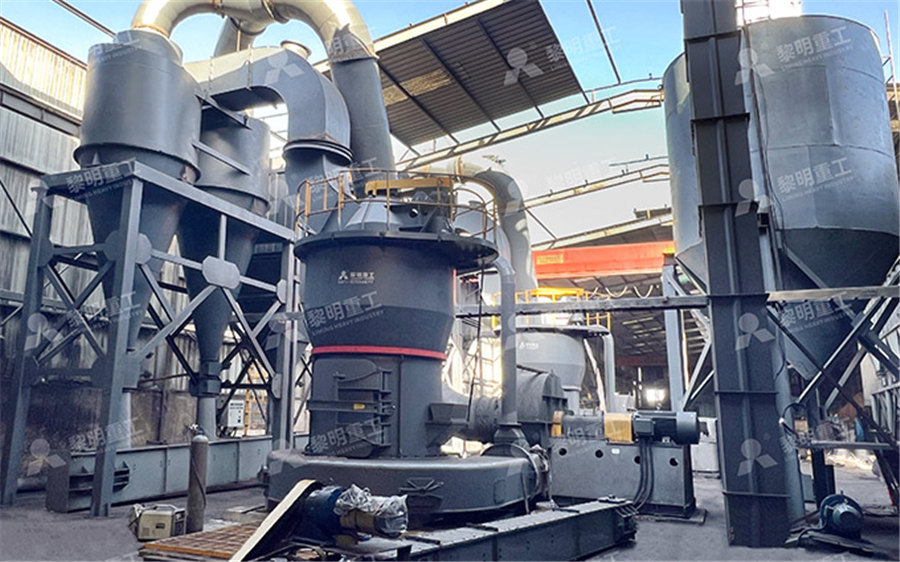
Investigation on Iron Ore Grinding based on Particle Size Distribution
2020年5月28日 The feed samples of X, Y, and Z iron ores were ground in the BBM (ball mill refers to a BBM of size 300 mm × 300 mm with smooth liners) to identify the PSD, BWI, and RT of each ore Grinding experiments were conducted according to Bond’s standard test procedure []For each iron ore sample, the RT taken to produce 250% circulating load in the BBM was The shape of crushed ore affects the product particle size in a ball mill grinding circuit It has also been proposed that green pellet quality is directly related to the amount of fine particles in a pelletizing plant (Dwarapudi et al, 2008; Umadevi et al, 2008; Gul et al, 2014; Van der Meer, 2015) Particle size distributionInvestigation on the particle size and shape of iron ore pellet feed 2022年2月28日 An investigation conducted on magnetite ore grinding with a dry HPGR machine to reduce the particle size from 50 mm to 90 µm has revealed that using two stages HPGR closed circuit with an air classifier can reduce energy consumption by 46% compared to a circuit in which there is a tertiary crushing with a wet ball millGrinding SpringerLink2020年3月20日 Rod mill:The rod mill has the highest efficiency when the feed size is 30mm and the discharge size is about 3mm with uniform particle size and light minerals with mud (can omit ore washing) Feeding size: ≤25mm: ≤50mm: 300400mm: Capacity : 062—180t/h: 065—615t/h: Ball mill: When the particle size of the product What’s the Difference Between Ball Mill, Rod Mill and SAG Mill?