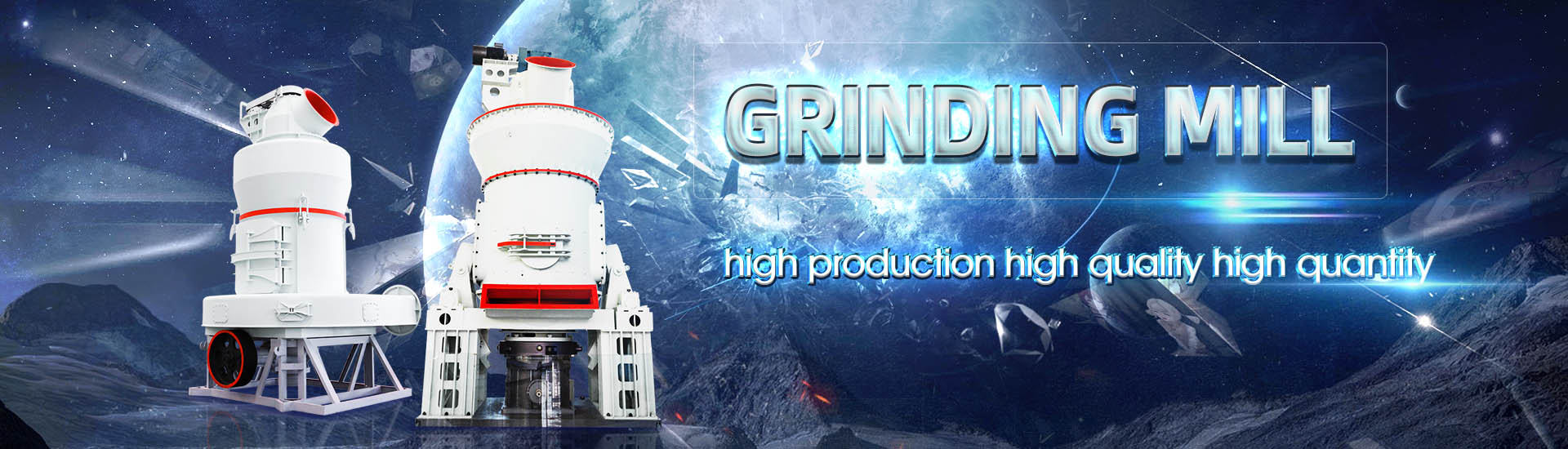
2.8*7.5m cement mill capacity 2.8*7.5m cement mill capacity 2.8*7.5m cement mill capacity
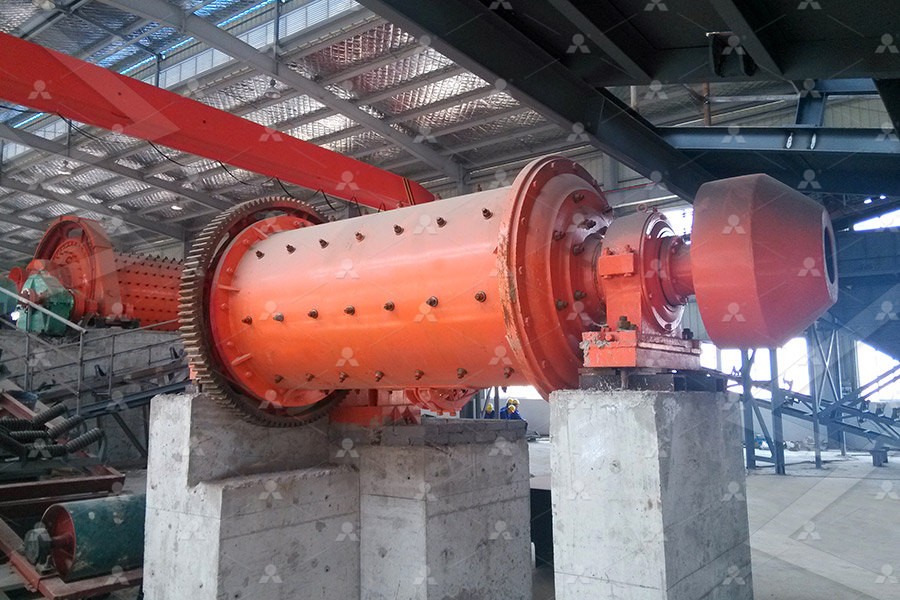
The Greenhouse Gas Emissions Produced by Cement Production
2015年2月1日 The purpose of this study is to investigate and explain the review of cement processing and its impact on cement manufacturing emissions on the environment For instance, the cement industry2023年10月13日 The top five cement producing countries (China, India, Vietnam, United States and Indonesia) account for approximately 682% of global cement production in 2020, with Global database of cement production assets and upstream 2016年1月20日 In the surveyed cement plant, three balances are established between input and output material in the raw mill, clinker production, and cement grinding system 248 t, 469 t, Analysis of material flow and consumption in cement2021年8月28日 This paper presents aspects of monitoring material dust emissions from stationary emission sources (monthly dust measurements performed on cement mill (PDF) Dust Emission Monitoring in Cement Plant Mills: A
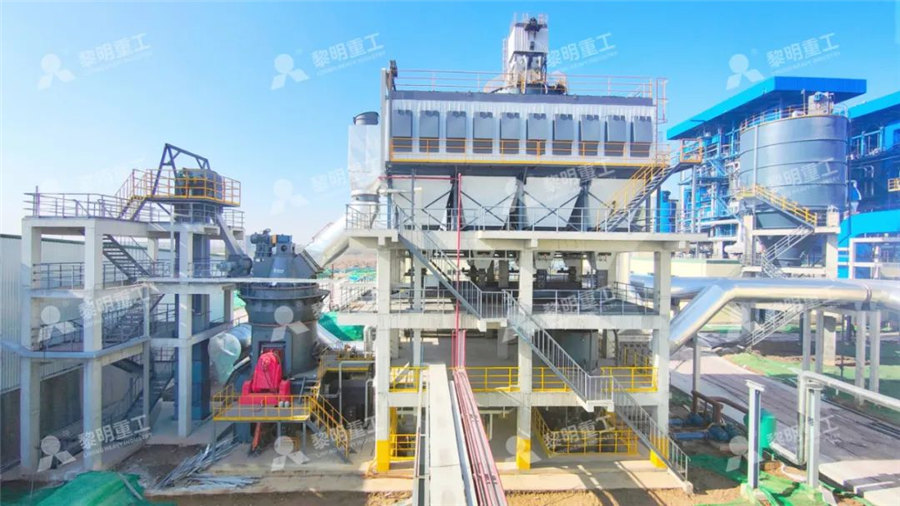
Energy and thermodynamic analysis of a typical cement
2022年10月1日 Cement production is one of the most energyconsuming industries in the world, and the grate cooler plays a vital role in cement quality and energy recovery In this paper, a A 10 MW cement mill, output 270 tonnes per hour A cement mill (or finish mill in North American usage [1]) is the equipment used to grind the hard, nodular clinker from the cement kiln into Cement mill Wikipedia2019年4月1日 The eight countries covered by this article share 567Mt/yr of integrated cement capacity and are home to around 968 million people Cement production is dominated to the Cement in central and eastern EU Member States• Separate clinker cooler and bypass stacks as well as coal mill, cement mill and material dryer stacks measure dust emissions at least once per year Continuous dust measurement at these Cement Environmental Directive Holcim
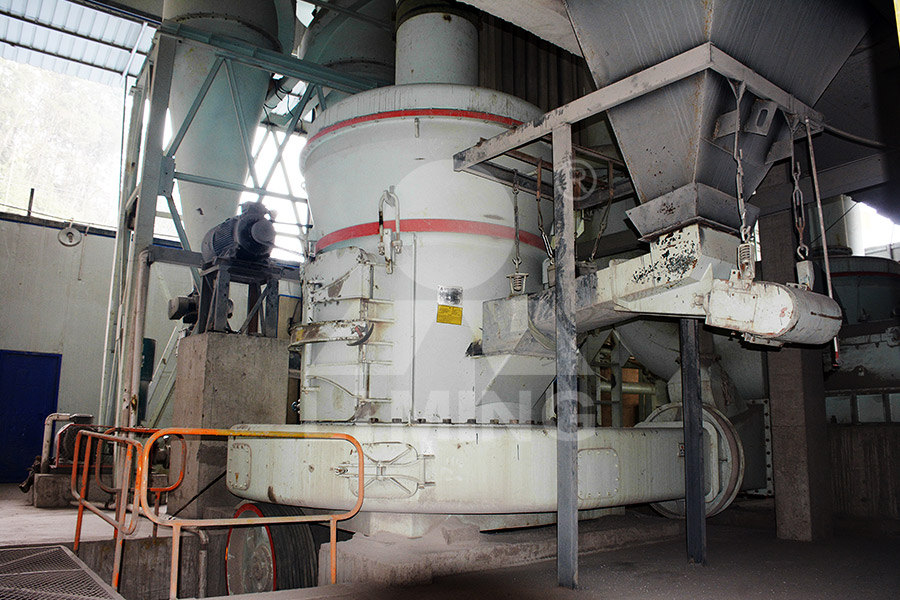
European cement 20202025
The Med rim has the highest cement capacity both integrated and grinding Eastern subregion has the lowest capacity, but the largest average integrated plant size Central/Western and cement plants would increase to 115130 kWh/t cement in 2030 and to 115145 kWh/t cement in 2050 PROCESS OVERVIEW – Cement is a solid material made of clinker, gypsum I03 cement June 2010 GSgct IEAETSAP2019年8月30日 1 Calculation of ball mill capacity they can be selected according to tables 17 and 18 Table 14 Ore Grinding Difficulty Coefficient (K’1) Ore hardness: Ore Grinding Difficulty Coefficient (K’1) Ore hardness: the Ball Mill Parameter Selection Calculation JXSCthe clinker grinding circuit was depicted in Fig 2 The capacity of the cement mill during the sampling time was 130 t/h and the specific energy consumption was 32 kW h/tOpen and closed circuit dry grinding of cement mill rejects in a
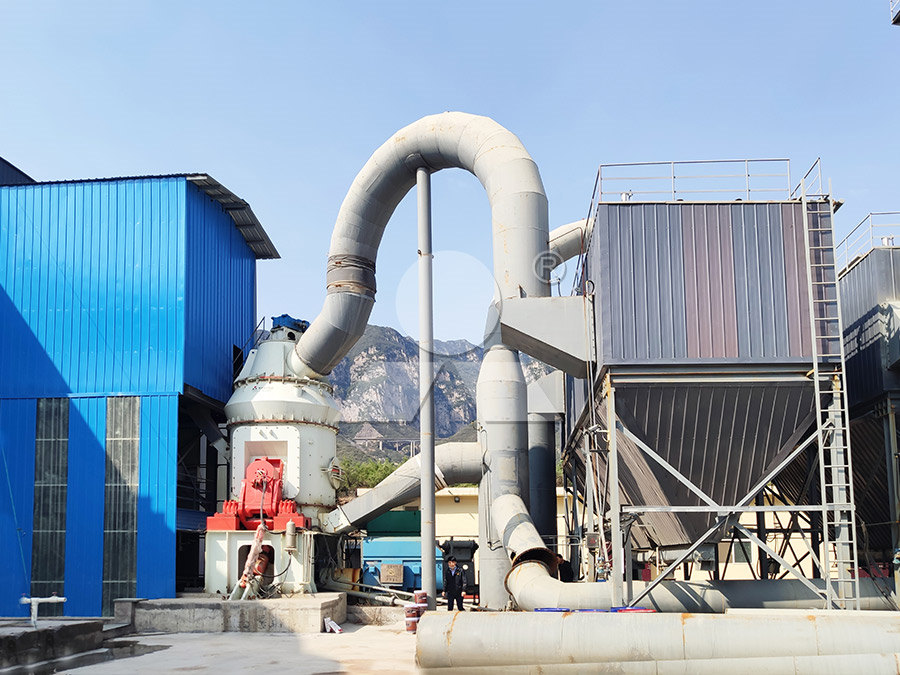
Brazil A resilient cement industry
2014年4月23日 Brazilian cement plants are typically highly energyefficient, resulting in reduced CO 2 emissions 15 Brazil has no countrywide limit to the levels of SO 2 and NO x produced by cement plants, although industry contacts state that these emissions are limited on a statebystate basis 16 However, mercury emissions are limited to 005mg/Nm 3 (with reference to 7% 1% additional water = 10% less capacity, when no excess of drying capacity Greater than 78% definitely requires a drying chamber; For a cement mill: intermediate or outlet diaphragm For the case of; cement mills with a drying chamber see raw mills Mill working conditions:Everything you need to know about clinker/cement Grinding2023年4月23日 P80 as shown in Figure 2 [7] However, of cement clinkers was higher with cylpebs grinding media than with steel balls in a ball 27 Effect of grinding media on the mill energy consumption (PDF) Grinding Media in Ball MillsA Review ResearchGateThe most energyefficient mill for cement grinding OK™ CEMENT MILL FS Cement ˜smidtement OK™ 2 OK ™ cement mill and slag grinding Actual capacity depends on product fineness, grindability, width 5,0 8,2 7,3 7,9 8,6 9,4 10,2 10,9 11,6 12,4 13,3 14,2 Motor size, OK™ CEMENT MILL
.jpg)
(PDF) Dust Emission Monitoring in Cement Plant Mills: A
2021年8月28日 Distribution of dust emissions at bag filters in the cement mill section no1 (mill filterpoint A and separator filterpoint B, Figure 1) of the analyzed cement plant2019年3月8日 257 HighEfficiency Fans for Cement Mill V ents between $16 million and $2 million per MW of capacity 35 RELEVANT FACTORS FOR IMPLEMENT ATIONIMPROVING THERMAL AND ELECTRIC ENERGY EFFICIENCY AT CEMENT Mill Type Overview Three types of mill design are common The Overflow Discharge mill is best suited for fine grinding to 75 – 106 microns; The Diaphram or Grate Discharge mill keeps coarse particles within the mill for additional grinding and typically used for grinds to 150 – 250 microns; The CenterPeriphery Discharge mill has feed reporting from both ends and the product AMIT 135: Lesson 7 Ball Mills Circuits – Mining Mill Operator 2015年1月7日 3 ~ Nael Shabana 20103~ 60 Ventilation 70 Grinding and Generation of Heat 71 Heat Generation in Tube Mills 72 Cooling Procedures During Finish Grinding 73 Heat Balance for Mill Cooling 80 Cement Mill Specific Power Consumption 81 Calculation of Cement Mill Power Consumption 82 Calculation of the Specific Consumption of Energy per Ton of Cement mill notebook PDF Free Download SlideShare
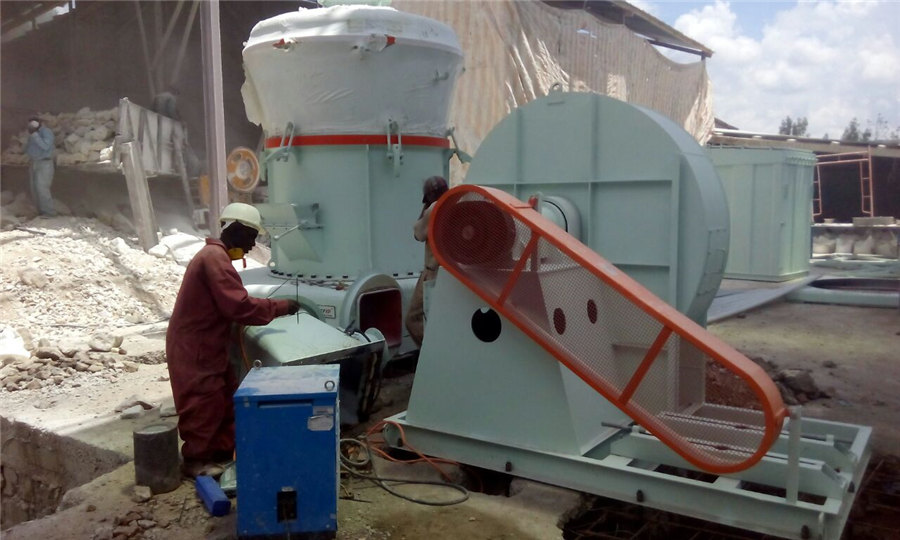
(PDF) Performance Evaluation of Vertical Roller Mill
2017年9月11日 PDF In this study, an extensive sampling study was carried out at vertical roller mill of ESCH Cement Plant in Luxemburg Samples were collected from Max fan capacity (kW) 175012 Objectives 1 3 20 PROJECT DEVELOPMENT PLAN 4 30 PROCESS FLOWSHEET AND PLANT LAYOUT 31 Generating design concept 32 Advantages and Disadvantages of Filter Baghouse System 33 Characteristics of Particulate Matter 34 Cleaning Mechanisms 7 7 8 8 40 DETAIL DESIGN WORK 41 Design Procedure 42 AutoCAD Drawing 10 13OPTIMIZING THE PERFORMANCE OF FILTER BAGHOUSES AT PORTLAND CEMENT RAW MILLPRESTRESSED CEMENT CONCRETE POLES (FOS 25) FOR 11 KV AND LT LINES 1 SCOPE This Specification covers PCC poles with an overall length of 75 M, 80 M and 90 M suitable for use in overhead 11 KV and LT power lines and double pole structures for 11/04 KV substations 2 APPLICABLE STANDARDS1 Technical Specification PRESTRESSED CEMENT CONCRETE POLES (FOS 2Air speed in mill – Open circuit : 08 to 12 m/sec – Closed circuit : 12 to 15 m/sec **Min 05 m/s —> tend to result inefficient over grinding and excessive heat generation with possible coating problem **Max > 14 m/s —> drag particle out of mill before they have been sufficiency ground Agglomeration and ball coatingCement Separator Ball Mill Optimization
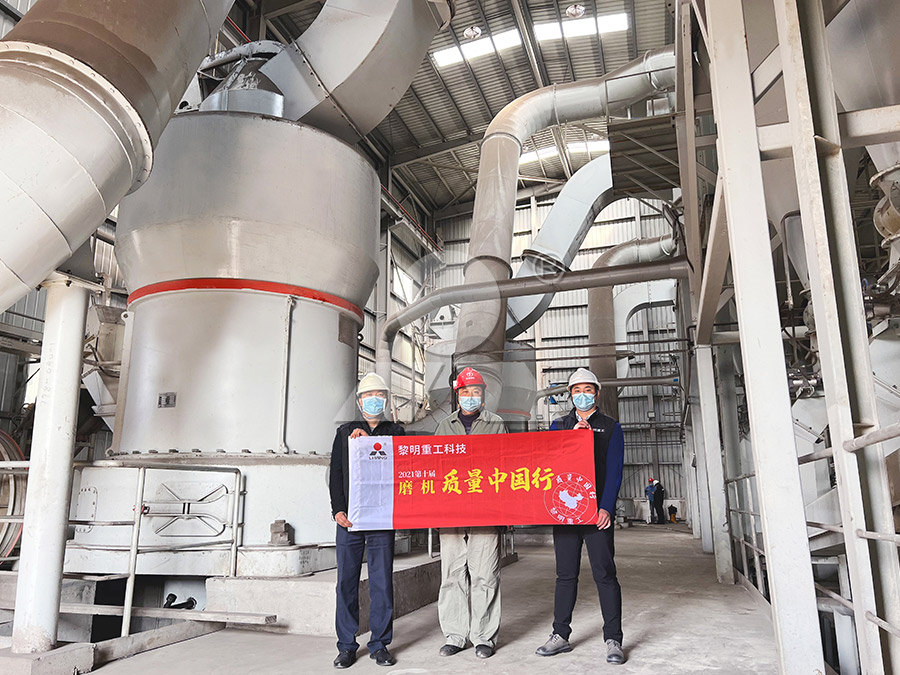
Ball millPMG series high efficient ball mill China Pengfei
Jiangsu Pengfei Group Co, Ltd has the great comprehensive ability to provide the best quality services on turnkey basis with the complete equipment、 the installation and the debugging for the new type dry process rotary kiln cement factories under the daily capacity of 8000ton、5000ton and 2500ton and compound fertilizer plants under the annual capacities of the 8872: 8347: 810586: Total coal: 77639: 80755: 80225 Similarly, in October 2014, Misr Beni Suef Cement announced plans to build a US$279m coal mill by the end of 2015 Next, in November 2014, Titan Cement ordered a Gebr This alone is expected to reduce China’s cement capacity by 340Mt/yr, or around 11%Coal for cement: Present and future trendsThe largest planetary gears for ball mill drives in the cement industry supplied at this writing by the Maag Gear Wheel Co, have a transfer capacity of 8 MW Since 1967 to 1982, about 70 planetary gears for central drive for the cement industry were manufac turedMill drives INFINITY FOR CEMENT EQUIPMENTGroup Installed Capacity (Clinker) 140 MTPA Plant Installed Capacity (Clinker) 20 MTPA Installed Capacity (Cement) 25 mMTPA Captive Power Plant 30MW WHR Power Plant 73 MW Solar Power Plant 30 MW Product Range OPC, PPC Max Crete Chettinad Kallur works is the first green field cement manufacturing unit with a capacity of 20 MTPA at KallurChettinad Cement Green Business Centre
.jpg)
Cement Environmental Directive Holcim
• Separate clinker cooler and bypass stacks as well as coal mill, cement mill and material dryer stacks measure dust emissions at least once per year Continuous dust measurement at these stacks is recommended, in particular at the clinker cooler stack2015年5月12日 The TCMA reported that in the first 11 months of 2014, cement production fell by 241% yearonyear to 652Mt, while clinker production grew by 292% to 565Mt 2 Given that 456Mt of cement was produced in December 2013, Turkey's cement production for the entirety of 2014 is unlikely to have exceeded 70MtTurkey’s cement industry: Onwards and upwards2022年4月7日 Fig 2 9: Shayona blending silo 30m high, 14m diameter and 5000 metric tons capacity COAL MILL SECTION Coal is the main source of fuel in cement production(PDF) CEMENT PRODUCTION PROCESS REPORT AJiangsu Pengfei Group Co, Ltd has the great comprehensive ability to provide the best quality services on turnkey basis with the complete equipment、 the installation and the debugging for the new type dry process rotary kiln cement factories under the daily capacity of 8000ton、5000ton and 2500ton and compound fertilizer plants under the annual capacities of the diameter 42*145m cement mill China Pengfei Group Co,Ltd
.jpg)
‘Build, Build, Build’ing in the Philippines Global Cement
2020年1月6日 In 2019 a third line was added, providing an additional 20Mt/yr of capacity The producer will shortly add a further 15Mt/yr of clinker grinding capacity to the plant to fully unleash its integrated plant’s capabilities and take its overall capacity to 84Mt/yr It is also building a 20Mt/yr plant in Cebu2013年4月1日 Mahendran (2013) have reported the use of fly ash and mill scale in OPC concrete as alternative building materials The compressive strength for control concrete was found to be at most 44 MPa and (PDF) Use of fly ash and steel mill scale in cement concrete as Cement Ball Mill Description: MQ series ball mills are mainly used in grinding operations in mining, 467 : Φ42 * 13: 8 closed circuit: 163: 224: YRKK9008: 3150: MFY320: 47 : Reliable operation, continuous operation, large production capacityBall Mill for Cement Grinding ProcessThe most energyefficient mill for cement grinding OK™ CEMENT MILL FS Cement ˜smidtement OK™ 2 OK ™ cement mill and slag grinding Actual capacity depends on product fineness, grindability, width 5,0 8,2 7,3 7,9 8,6 9,4 10,2 10,9 11,6 12,4 13,3 14,2 Motor size, OK™ CEMENT MILL
.jpg)
EnergyEfficient Technologies in Cement Grinding IntechOpen
2016年10月5日 In this chapter an introduction of widely applied energyefficient grinding technologies in cement grinding and description of the operating principles of the related equipments and comparisons over each other in terms of grinding efficiency, specific energy consumption, production capacity and cement quality are given A case study performed on a 2018年11月11日 Kufa Journal of Engineering Vol 10, No 4, October 2019, PP 115 Received 11 November 2018, accepted 14 January 2019 IMPROVING PRODUCTIVITY BASED ON THEIMPROVING PRODUCTIVITY BASED ON THE MOVEMENT OF2013年12月9日 8: 9: 56: Lucky Cement Ltd: Pakistan: 75: 2: 57: SECIL: Portugal: 74: 7: 58: Penna Cement: however various news reports show that it has continued to expand and diversify through 2013 with the purchase of a new cement mill in Iraq and multiple subsidiary includes cement capacity of 928Mt/yr at plants that were due to be Top 75 global cement companies21 Cement Industry and Cement Production Energy Fog et al (1983)stated that the energy sources in a cement plant can be classified as primary sources, ie oil, coal, gas, other fuels and electricity, and secondary sources, ie waste heat from one phase of the process which can be recovered and utilized in another phaseCHAPTER II LITERATURE REVIEW 21 Cement Industry and Cement
.jpg)
Ball Mill Parameter Selection Calculation JXSC
2019年8月30日 1 Calculation of ball mill capacity they can be selected according to tables 17 and 18 Table 14 Ore Grinding Difficulty Coefficient (K’1) Ore hardness: Ore Grinding Difficulty Coefficient (K’1) Ore hardness: the the clinker grinding circuit was depicted in Fig 2 The capacity of the cement mill during the sampling time was 130 t/h and the specific energy consumption was 32 kW h/tOpen and closed circuit dry grinding of cement mill rejects in a 2014年4月23日 Brazilian cement plants are typically highly energyefficient, resulting in reduced CO 2 emissions 15 Brazil has no countrywide limit to the levels of SO 2 and NO x produced by cement plants, although industry contacts state that these emissions are limited on a statebystate basis 16 However, mercury emissions are limited to 005mg/Nm 3 (with reference to 7% Brazil A resilient cement industry1% additional water = 10% less capacity, when no excess of drying capacity Greater than 78% definitely requires a drying chamber; For a cement mill: intermediate or outlet diaphragm For the case of; cement mills with a drying chamber see raw mills Mill working conditions:Everything you need to know about clinker/cement Grinding
.jpg)
(PDF) Grinding Media in Ball MillsA Review ResearchGate
2023年4月23日 P80 as shown in Figure 2 [7] However, of cement clinkers was higher with cylpebs grinding media than with steel balls in a ball 27 Effect of grinding media on the mill energy consumption The most energyefficient mill for cement grinding OK™ CEMENT MILL FS Cement ˜smidtement OK™ 2 OK ™ cement mill and slag grinding Actual capacity depends on product fineness, grindability, width 5,0 8,2 7,3 7,9 8,6 9,4 10,2 10,9 11,6 12,4 13,3 14,2 Motor size, OK™ CEMENT MILL2021年8月28日 Distribution of dust emissions at bag filters in the cement mill section no1 (mill filterpoint A and separator filterpoint B, Figure 1) of the analyzed cement plant(PDF) Dust Emission Monitoring in Cement Plant Mills: A2019年3月8日 257 HighEfficiency Fans for Cement Mill V ents between $16 million and $2 million per MW of capacity 35 RELEVANT FACTORS FOR IMPLEMENT ATIONIMPROVING THERMAL AND ELECTRIC ENERGY EFFICIENCY AT CEMENT
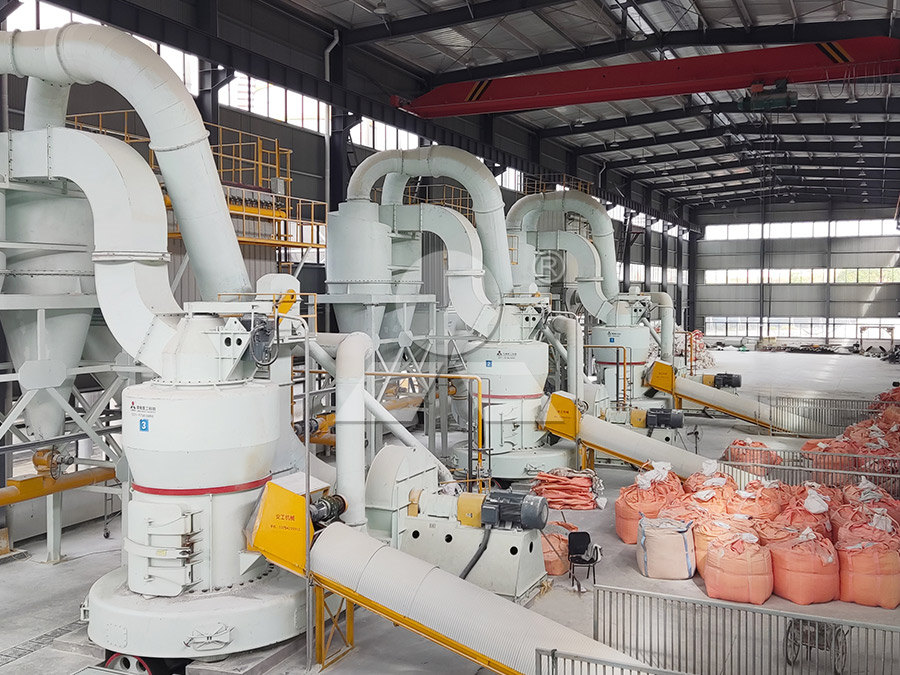
AMIT 135: Lesson 7 Ball Mills Circuits – Mining Mill Operator
Mill Type Overview Three types of mill design are common The Overflow Discharge mill is best suited for fine grinding to 75 – 106 microns; The Diaphram or Grate Discharge mill keeps coarse particles within the mill for additional grinding and typically used for grinds to 150 – 250 microns; The CenterPeriphery Discharge mill has feed reporting from both ends and the product 2015年1月7日 3 ~ Nael Shabana 20103~ 60 Ventilation 70 Grinding and Generation of Heat 71 Heat Generation in Tube Mills 72 Cooling Procedures During Finish Grinding 73 Heat Balance for Mill Cooling 80 Cement Mill Specific Power Consumption 81 Calculation of Cement Mill Power Consumption 82 Calculation of the Specific Consumption of Energy per Ton of Cement mill notebook PDF Free Download SlideShare