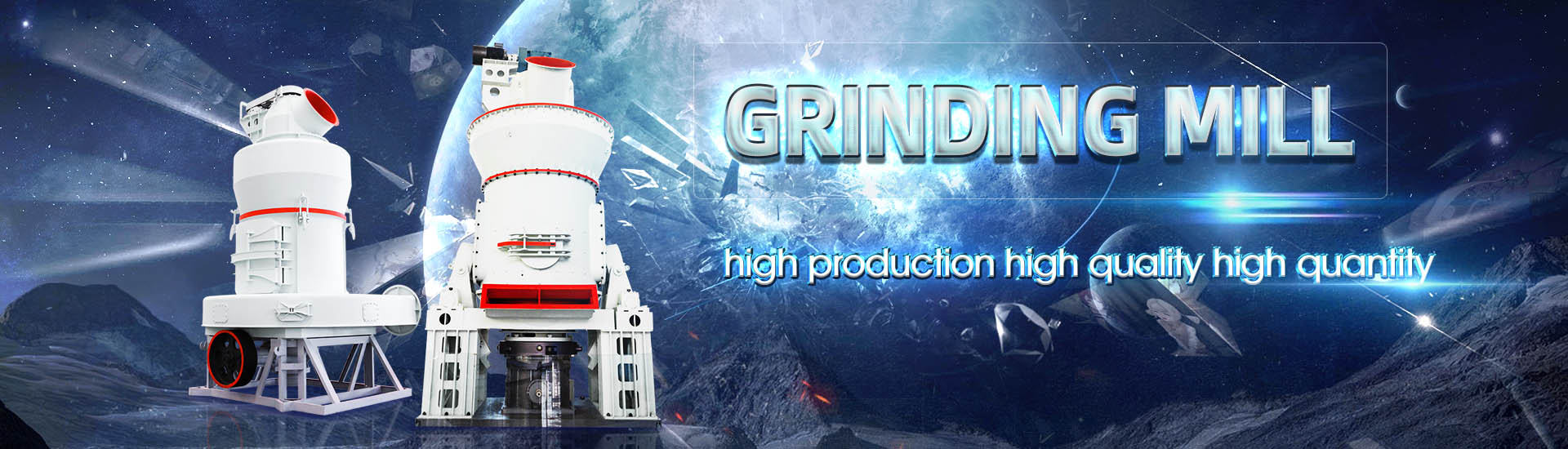
Introduction to the performance of coal mill roller sleeves
.jpg)
An investigation of performance characteristics and energetic
2020年8月12日 This study shows the performance of a currently running vertical roller coal mill (VRM) in an existing coalfired power plant In a power plant, the coal mill is the critical 2024年1月15日 This study is concerned with evaluating the performance of a novel roller mill, in which the crushing platen is a vertical wall over which cylindrical rollers rotate, thereby Optimisation of the performance of a new vertical roller mill by 2022年5月31日 The vertical roller mill (VRM) is commonly used for secondary and tertiary crushing processes in numerous industries In this study, the discrete element method (DEM) Analysis of vertical roller mill performance with changes in material 2020年8月12日 To understand the performance of a vertical roller coal mill, the real operational tests have been performed considering three different coal sources Obtained results indicate An investigation of performance characteristics and energetic
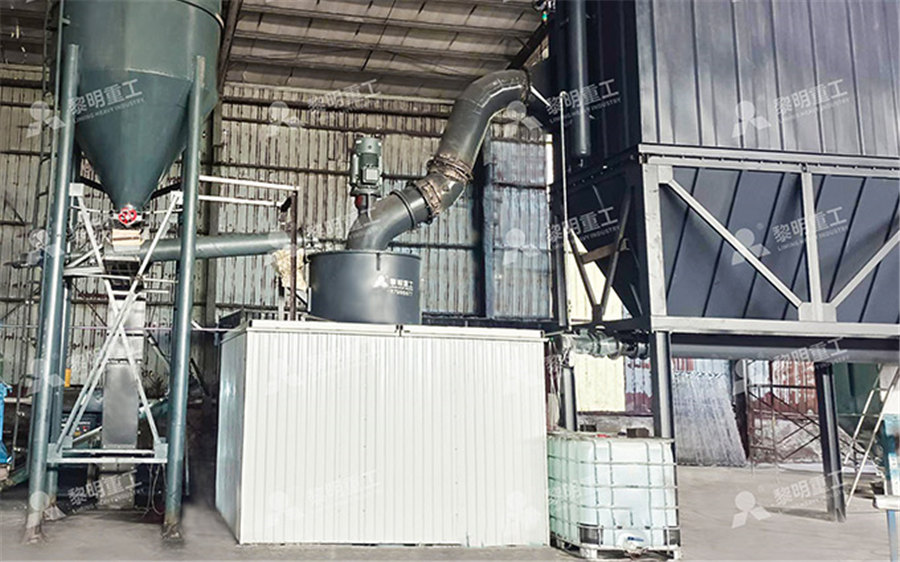
Numerical Study of Flow Field and Particle Motion Characteristics
2024年11月1日 Bhambare et al (Bhambare et al, 2010) developed a computational fluid model for MPS roller mills that considered the evaporation of moisture The authors used the Euler 2016年9月1日 This paper investigates the milling behavior of two industrial wood pellet qualities (designated I1 and I2 as per ISO 172252:2014) in largescale coal roller mills, each equipped Operational parameters affecting the vertical roller mill 2012年2月28日 For an industrial scaleup, we conducted a demonstration test using a vertical roller mill equipped in a 700MW thermal power plant consisting of a pulverized coal firing boiler A Demonstration Study on a High Performance Vertical Roller Mill spindle coal pulverising mill’s performance to facilitate optimal plant performance Plant design and mill’s acceptance test data was analysed to understand the design and subsequent Performance optimisation of vertical spindle coal pulverisers
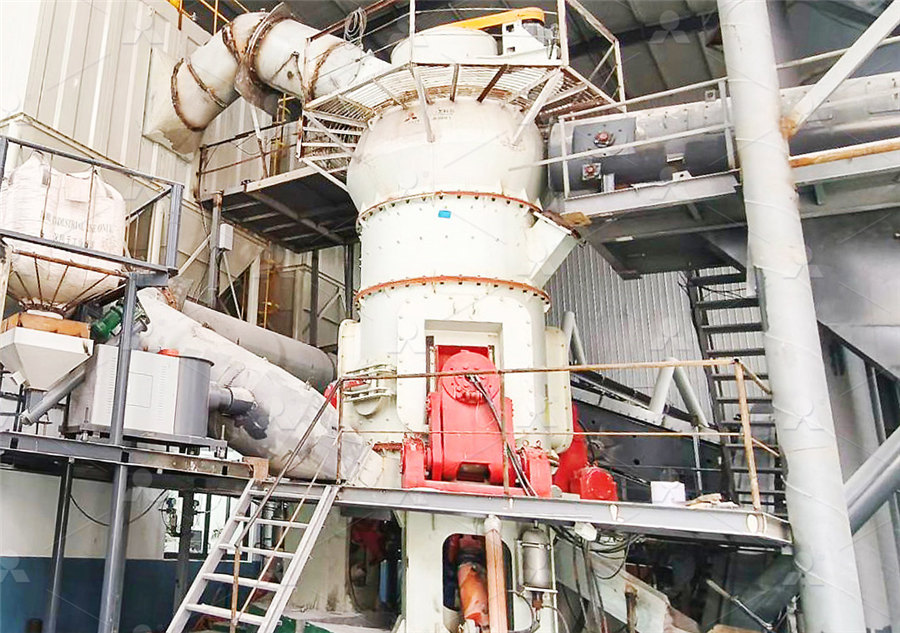
An investigation of performance characteristics and energetic
To understand the performance of a vertical roller coal mill, the real operational tests have been performed considering three diferent coal sources Obtained results indicate that2020年8月12日 ABSTRACT This study shows the performance of a currently running vertical roller coal mill (VRM) in an existing coalfired power plant In a power plant, the coal mill is the critical equipment, whose effectiveness impacts the overall power plant efficiency Uniform coal feeding mass flow rate and required particle size and temperature at the outlet channel An investigation of performance characteristics and energetic INTRODUCTION As part of the continuing effort to improve combustion performance commensurate with reduced emissions in coalfired power plants, Riley Power Inc (RPI), a Babcock Power Inc (BPI) company has been actively developing mill system technology to achieve better coal fineness, increased capacity, greater reliability, and longer wear lifeCoal Pulverizer Design Upgrades to Meet the Demands of Low spindle coal pulverising mill’s performance to facilitate optimal plant performance Plant design and mill’s acceptance test data was analysed to understand the design and subsequent changes over the years of the mill’s operation The mill outputs, pulverised coal fineness andPerformance optimisation of vertical spindle coal pulverisers
.jpg)
Coal vertical roller millVertical roller millPRODUCTTongli
Grinding Rollers: Grinding roller is the main part for crushing and grinding materials The grinding roller is composed of cast steel roller sleeve, forging shaft and wearresistant surfacing bushing The grinding roller is installed on the rocker arm of the coal vertical roller mill, under the action of external force, it is pressed tightly on the material of the grinding table, as the Introduction UBE Machinery Corporation Ltd (UBE) Coal, Clinker and Slag Reliable Performance performs drying grinding classification and pneumatic transportation simultaneously Vertical Roller Mill 1 Rotary Lock 2 Separator 3 Chute 4 Roller 5 Swing Lever 6 Table 7VERTICAL ROLLER MILLS AMCL2012年1月23日 Roller Bowl Coal Mill : A Controller of Combustion Time Coal 10 to 25 mm Size Hot Air ~ 2500C Sizing of Pulverizers • Feeder capacity is selected to be125 times the pulverizer capacity • Required fineness, is selected to be • 60% through a 200 mesh screen for lignite(75 mm), • 65% for subbituminous coal, • 7075% for bituminous coal, and • 8085% for anthracitePERFORMANCE ANALYSIS OF COAL MILLS SlideServePrimary air is admitted through the mill, which carries the finest coal particles to mill outlet The air and coal mixture passes through a classifier, located at the upper part of the mill, where an additional particle separation takes place Coarser particles return to the coal chute and fine particles are carried to the classifier outletAnalysis of the Coal Milling Operations to the Boiler Parameters
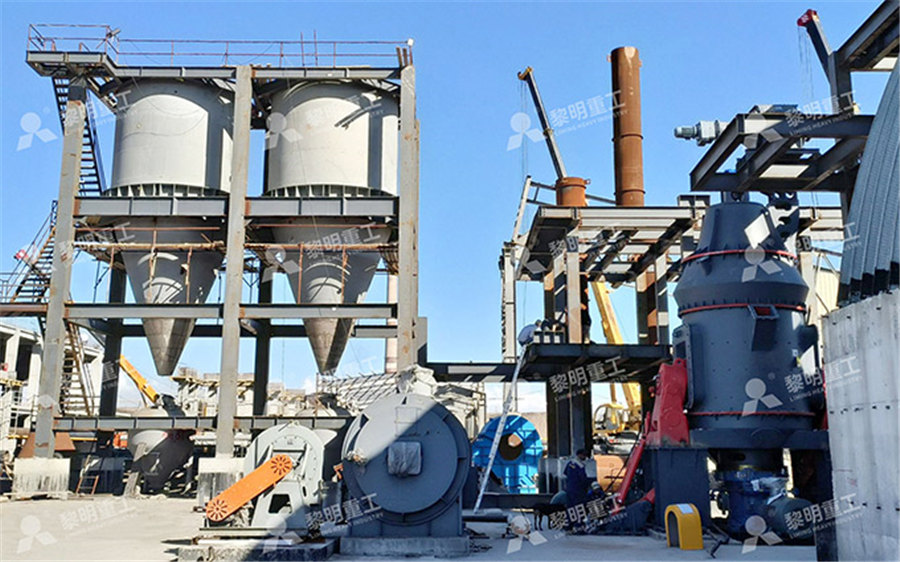
Analysis of the Coal Milling Operations to the Boiler Parameters
2020年4月2日 as mill roller, grin der and mill Coal mill motor power (kW) 0 4171 4548 4390 4586 The performance calculation and rectification measures are essential for performance 2021年11月4日 including the dropweight test machine, the roller test machine, and the Hardgrove mill Using the attrition test machine, presented in Figure 2 , is the only integrated testing methodTechnique to Investigate Pulverizing and Abrasive Performance of Coals 2009年1月1日 Coal pulverizers play a critical role in the functioning and performance of a PCfired boiler The main functions of a pulverizer are crushing, drying and separating the fine coal particles CFD Modeling of MPS Coal Mill for Improved Performance and SafetyDownload scientific diagram Technical specifications of vertical roller coal mill from publication: An investigation of performance characteristics and energetic efficiency of vertical roller Technical specifications of vertical roller coal mill
.jpg)
CFD Modeling of MPS Coal Mill for Improved Performance and
Introduction MPStype mills, with a roll wheel pulverizer, are widely used in the power generation industry to crush, dry and separate the fine coal particles towards combustion in the furnaceIntroduction The coal mills grind and dry the moisturized raw coal practice as control inputs to improve the coal mill performance internal structure such as roller and rotating table, etcModeling and Parameter Identification of Coal Mill ResearchGateINTRODUCTION As part of the continuing effort to improve combustion performance commensurate with reduced emissions in coalfired power plants, Riley Power Inc (RPI), a Babcock Power Inc (BPI) company has been actively developing mill system technology to achieve better coal fineness, increased capacity, greater reliability, and longer wear lifeCOAL PULVERIZER DESIGN UPGRADES TO MEET THE DEMANDS 2017年9月11日 In this study, an extensive sampling study was carried out at vertical roller mill of ESCH Cement Plant in Luxemburg Samples were collected from mill inside and around the circuit to evaluate the Performance Evaluation of Vertical Roller Mill in Cement
.jpg)
Analysis and Optimization of Grinding Performance of Vertical Roller
2022年1月23日 mill, coal mill, Clinker Mill and cement mill, and the vertical mill occupies a large energy consumption unit Therefore, it is necessary to optimize the multiobjective parameters of2020年11月4日 Effects of Blade Parameters on the Flow Field and Classification Performance of the Vertical Roller Mill via Numerical Investigations November 2020 Mathematical Problems in Engineering 2020(4):115Effects of Blade Parameters on the Flow Field and Classification mill's unique roller loading arrangement as a modification to its MB mill predecessor Shortly thereafter, DBW became the first licensee of Gebruder Pfeiffer in Europe for coal applications This particular mill was chosen because of DBW's successful track record not only in their worldwide installation of 6 to 100 TPHWorldProven Coal Pulverizer Technology Debuts in the USThe ball mill is a traditional coal pulverizer machine, which has been widely used since it was invented In the cement plant, the new dry process cement manufacturing requires the moisture content of coal powder to be 05% ~ 15%, while that of raw coal is 15% ~ 40%Coal Mill in Cement Plant Vertical Roller Mill AirSwept Ball Mill
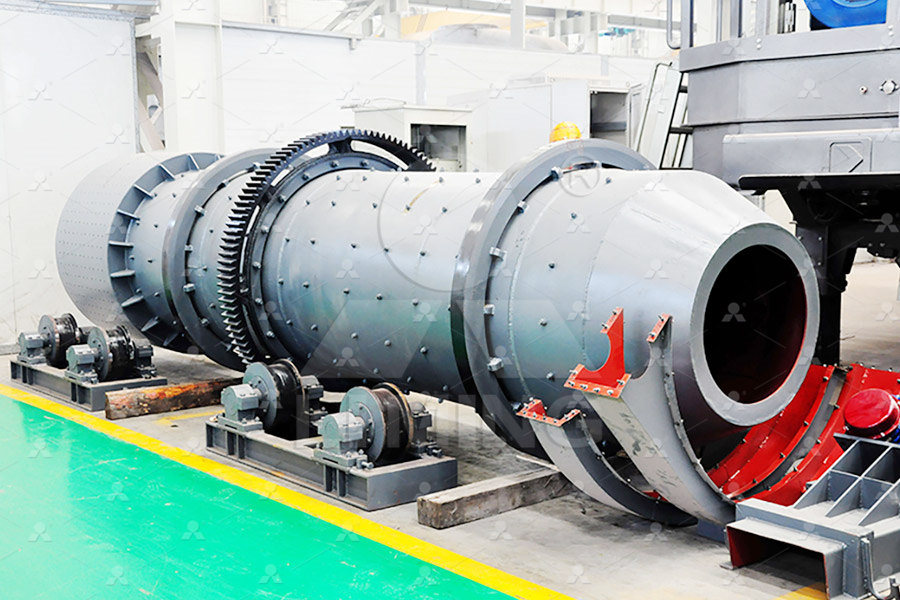
Milling Characteristics of Coal and Torrefied Biomass Blends in a
2021年10月28日 To ensure stable operation of the roller mill and an effective reduction in the size of the coal–TP blend, the selection and use of uniformly and sufficiently torrefied wood pellets are importantIntroduction As a result of the worldwide attention in recent years to energy efficiency improvement and CO 2 In March 2013 mill performance acceptance was completed Table 2 shows an actual operation data comparison 1 set of coal mills Figure 4 Roller mill design From left to right: raw mill, cement mill 10% downsizing 20% downsizingYasuhiro Shigemoto, Hirofumi Kasai and Tatsuya Hinauchi,2021年1月1日 Grinding Mill Vertical Roller Mill or Ball Mill: The reclaimed raw mix fed to Raw Mills, for drying and fine grinding of Raw meal for kiln feed: 4: Coal Grinding: Grinding Mill Vertical Roller Mill or Ball Mill: Coal is ground in Coal mill, which is a fuel for use in Kiln firing: 5: Pyro Section, Clikerization: In line calciner six stage Review on vertical roller mill in cement industry its performance 2021年11月9日 Introduction Replacing some of the coal by biomass is an effective way to reduce CO 2 emissions from pulverizedcoalfired power plants and integrated coal gasificationcombined cycle power plants However, compared with coal, biomass has lower grindability in the existing roller mills 1 and a lower calorific value per weight 2,3 The maximum biomass co Milling Characteristics of Coal and Torrefied Biomass Blends in a
.jpg)
(PDF) Fault analysis and optimization technology of HP
2021年8月1日 A root cause failure analysis of coal mill vertical shaft used in thermal power plant has been carried out The failed parts of the shaft showed the signature of fatigue failuresHRM1700MVRM Free download as PDF File (pdf), Text File (txt) or read online for free The document provides installation and operation instructions for the HRM1700M Vertical Roller Coal Mill It describes the mill's technical parameters, components, structure, working principles, and installation process Key aspects include grinding rollers that can be removed for Operation Manual: HRM1700M Vertical Roller Coal Mill2018年6月15日 Vertical roller mill (VRM) is widely used in coal power plants to prepare PF, and flow direction of coal in VRM is shown in Fig 1 Particle breakage and classification happens in closed phenomenon First, coal particles on grinding Effect of particle properties on the energysize reduction of coal 700 Journal of Power Electronics, Vol 9, No 5, September 2009 JPE 954 Modeling and Parameter Identification of Coal Mill HwiBeom Shin *, Xinlan Li , InYoung Jeong **, JongMan Park **, and Soonyoung Lee † †*Department of Electrical Engineering, Gyeongsang National University, Korea ** Korea Western Power Co, Ltd, KoreaModeling and Parameter Identification of Coal Mill

Vertical Roller Mills LNV TECHNOLOGY
Vertical Cement Mill: A vertical cement mill is used for the finishgrinding of cement Its grinding table liners and roller sleeves are made from wearresistant hard facing material or ceramic material Blades of the separator use highquality and wearresistant platesVertical Roller Mill The vertical roller mill (VRM) shown in Figure 4 is an air swept, mediumspeed, vertical pulverizer with integral classifier It pulverizes coal by applying hydraulicallyloaded grinding pressure through three grin ding rollers onto a rotating bed of coal Grinding pressure can be adjusted to account for variations in coalA Comparison of Three Types of Coal Pulverizers Babcock Power1999年11月1日 The test device is designed like a roller table mill with, however, only one roller Fig 1Fig 2 show a scheme and a sketch The grinding table (1) is shaped like an annular trough and driven with the motor (2) The conical grinding roller (3) fits in the trough The roller and its bearings are mounted at the lever system (4) with the spring (5)Labscale roller table mill for investigating the grinding behaviour 2020年8月12日 ABSTRACT This study shows the performance of a currently running vertical roller coal mill (VRM) in an existing coalfired power plant In a power plant, the coal mill is the critical equipment, whose effectiveness impacts the overall power plant efficiency Uniform coal feeding mass flow rate and required particle size and temperature at the outlet channel An investigation of performance characteristics and energetic
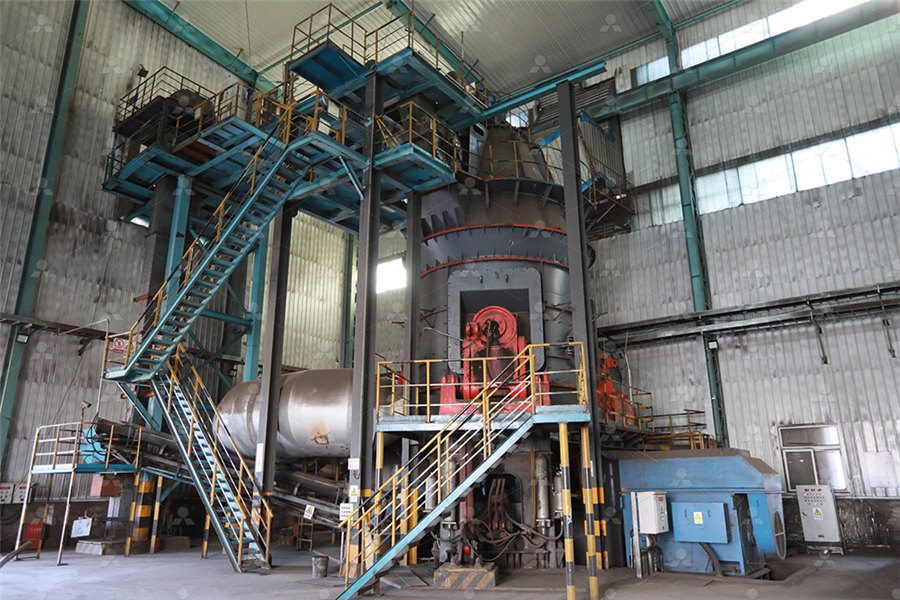
Coal Pulverizer Design Upgrades to Meet the Demands of Low
INTRODUCTION As part of the continuing effort to improve combustion performance commensurate with reduced emissions in coalfired power plants, Riley Power Inc (RPI), a Babcock Power Inc (BPI) company has been actively developing mill system technology to achieve better coal fineness, increased capacity, greater reliability, and longer wear lifespindle coal pulverising mill’s performance to facilitate optimal plant performance Plant design and mill’s acceptance test data was analysed to understand the design and subsequent changes over the years of the mill’s operation The mill outputs, pulverised coal fineness andPerformance optimisation of vertical spindle coal pulverisersGrinding Rollers: Grinding roller is the main part for crushing and grinding materials The grinding roller is composed of cast steel roller sleeve, forging shaft and wearresistant surfacing bushing The grinding roller is installed on the rocker arm of the coal vertical roller mill, under the action of external force, it is pressed tightly on the material of the grinding table, as the Coal vertical roller millVertical roller millPRODUCTTongli Introduction UBE Machinery Corporation Ltd (UBE) Coal, Clinker and Slag Reliable Performance performs drying grinding classification and pneumatic transportation simultaneously Vertical Roller Mill 1 Rotary Lock 2 Separator 3 Chute 4 Roller 5 Swing Lever 6 Table 7VERTICAL ROLLER MILLS AMCL
.jpg)
PERFORMANCE ANALYSIS OF COAL MILLS SlideServe
2012年1月23日 Roller Bowl Coal Mill : A Controller of Combustion Time Coal 10 to 25 mm Size Hot Air ~ 2500C Sizing of Pulverizers • Feeder capacity is selected to be125 times the pulverizer capacity • Required fineness, is selected to be • 60% through a 200 mesh screen for lignite(75 mm), • 65% for subbituminous coal, • 7075% for bituminous coal, and • 8085% for anthracitePrimary air is admitted through the mill, which carries the finest coal particles to mill outlet The air and coal mixture passes through a classifier, located at the upper part of the mill, where an additional particle separation takes place Coarser particles return to the coal chute and fine particles are carried to the classifier outletAnalysis of the Coal Milling Operations to the Boiler Parameters2020年4月2日 as mill roller, grin der and mill Coal mill motor power (kW) 0 4171 4548 4390 4586 The performance calculation and rectification measures are essential for performance Analysis of the Coal Milling Operations to the Boiler Parameters2021年11月4日 including the dropweight test machine, the roller test machine, and the Hardgrove mill Using the attrition test machine, presented in Figure 2 , is the only integrated testing methodTechnique to Investigate Pulverizing and Abrasive Performance of Coals
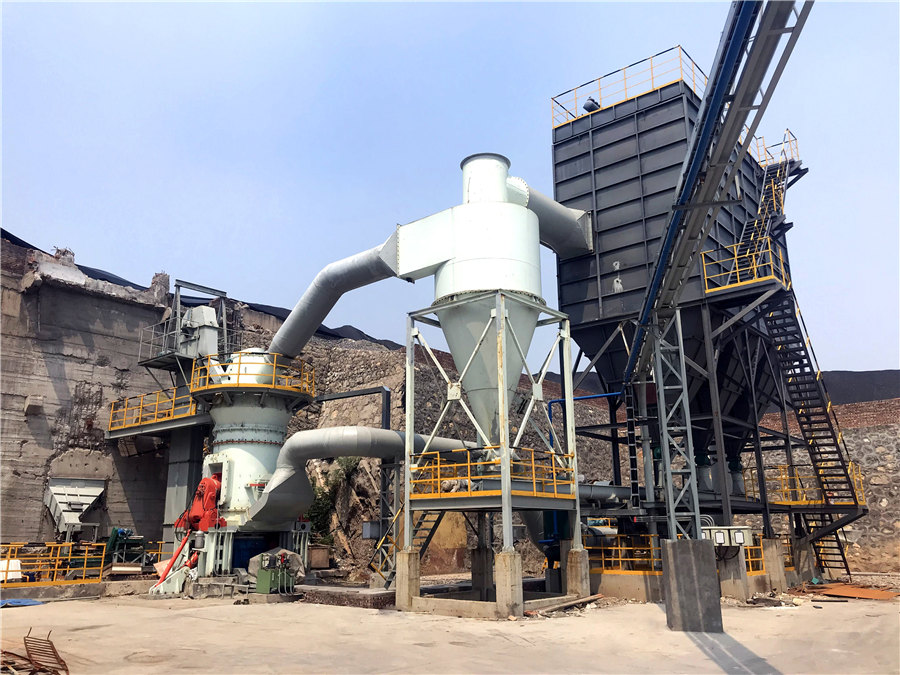
CFD Modeling of MPS Coal Mill for Improved Performance and Safety
2009年1月1日 Coal pulverizers play a critical role in the functioning and performance of a PCfired boiler The main functions of a pulverizer are crushing, drying and separating the fine coal particles