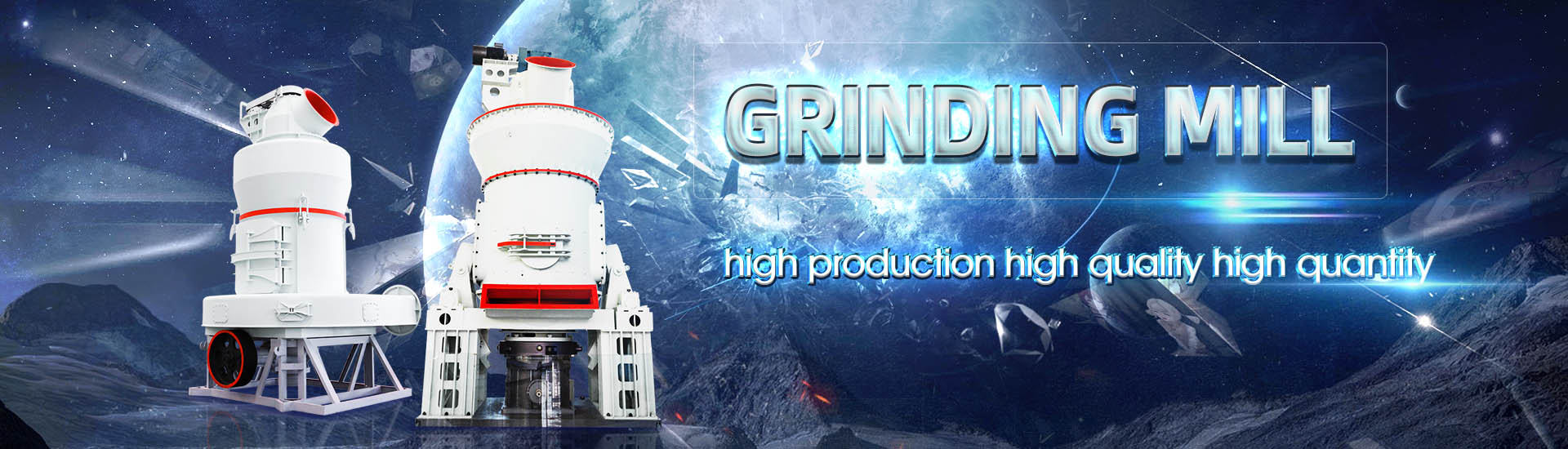
HOME→Cement grinding workshop process drawings Cement grinding workshop process drawings Cement grinding workshop process drawings
Cement grinding workshop process drawings Cement grinding workshop process drawings Cement grinding workshop process drawings
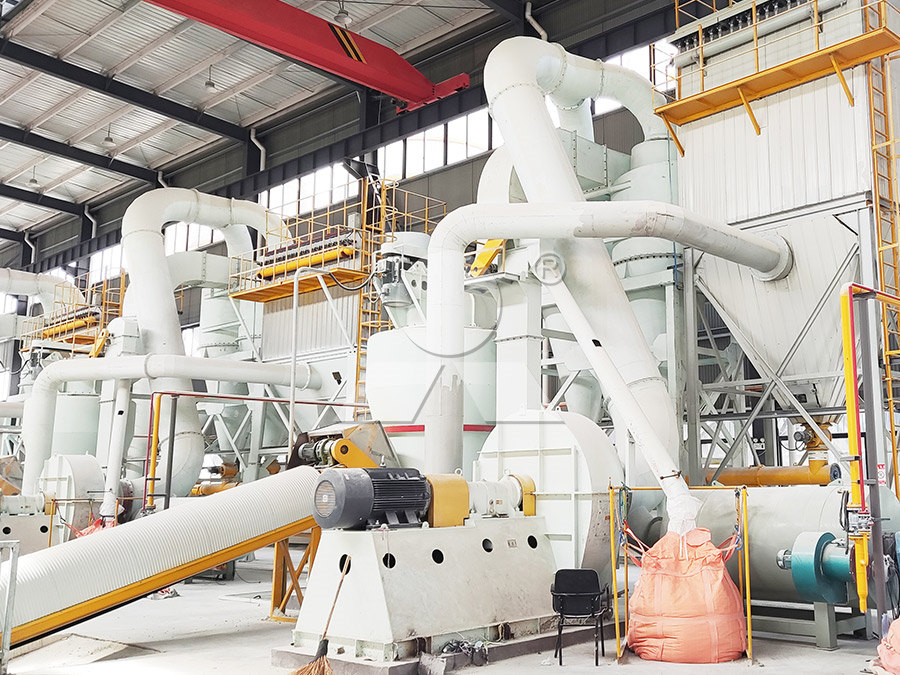
Cement Grinding myPolysiusService
6 Cement Production Technology –Cement Grinding –Mechanical Design and Function of Separator Separators –General Classification of Separating Principles •according to flow process engineering for the cement lime industries mechanical engineering (plant design, piping, process gas handling, environmental controls, nuisance dust collection and materials PROCESS ENGINEERING FOR THE CEMENT LIME INDUSTRIES Highly energy intensive unit operation of size reduction in cement industry is intended to provide a homogeneous and super fine (30004000 Blain) cement Grinding operation is monitored for Cement Grinding Cement Plant OptimizationCement grinding In Table 1, three common cement grinding systems are compared on their electrical consumption for a typical 3500 Blaine ordinary portland cement (OPC) Roller press Thomas Holzinger, Holzinger Consulting, grinding system
.jpg)
CEMENT GRINDING COURSE The Cement Institute
Throughout the course, the lectures are supplemented with exercises and case studies, allowing the participants to relate the course material to their cement grinding facility and, as a result An evaluation of the grinding system and operation includes meaningful and critical inspection of all equipment, components and the process parameters by experts PEC Consulting can help OPTIMIZATION OF CEMENT GRINDING OPERATION IN BALL MILLS2004年11月1日 To optimise cement grinding, standard Bond grinding calculations can be used as well as modelling and simulation techniques based on population balance model (PBM) Cement grinding optimisation ScienceDirectExplore Amrit Cement's stateoftheart cement grinding unit Learn about our cement grinding process and plant stages for high quality cementCement Grinding Unit Process High Quality Cement Grinding
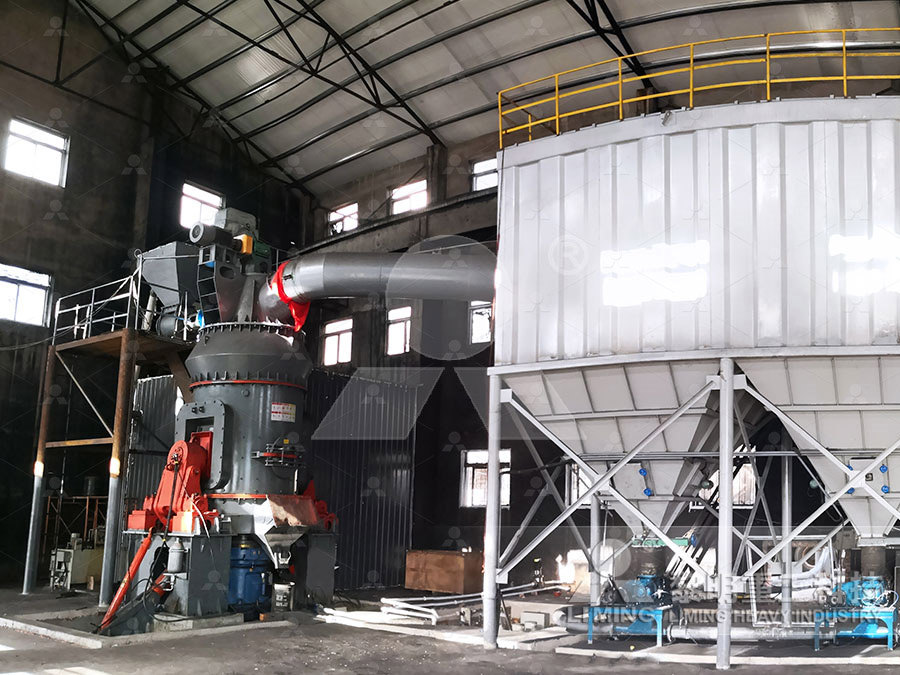
Overview of cement grinding: fundamentals, additives, technologies
2017年5月19日 PDF Grinding is an essential operation in cement production given that it permits to obtain fine powder which reacts quickly with water, sets in few Find, read and 2017年5月19日 Cement industry is characterized by sizeable energy demand which accounts for about 110kWh (375 thm) per ton of cement in modern plants Industry impacts heavily also on CO2 emissionsOverview of cement grinding: fundamentals, 2023年8月21日 Tushar Khandhadia, General Manager – Production, Udaipur Cement Works, discusses the role of grinding in ensuring optimised cement production and a high quality end product How does the grinding process Grinding process is a critical stage in cement 2019年1月3日 Clinker grinding technology is the most energyintensive process in cement manufacturing Traditionally, it was treated as "low on technology" and "high on energy" as grinding circuits use more than 60 per cent of total energy Clinker grinding technology in cement manufacturing
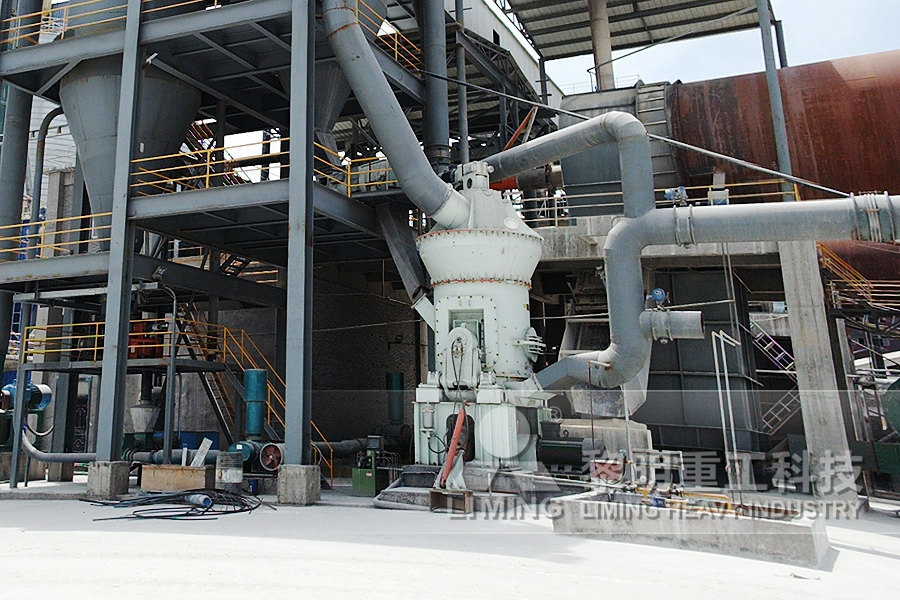
What Do You Know About Wet Process Of Cement Production
2024年1月17日 According to statistics, the dry cement production line grinding operation consumes Power accounts for more than 60% of the power of the whole plant, of which raw material grinding accounts for more than 30%, coal grinding accounts for about 3%, and cement grinding station account for about 40%Stage 2: Grinding, Proportioning, and Blending The crushed raw ingredients are made ready for the cementmaking process in the kiln by combining them with additives and grinding them to ensure a fine homogenous mixture The composition of cement is proportioned here depending on the desired properties of the cement Generally, limestone is 80%, and the remaining 20% How Cement is Made Cement Manufacturing ProcessThe power ingesting of a grinding process is 5060% in the cement production power consumption The Vertical Roller Mill (VRM) reduces the power consumption for cement grinding approximately 3040% associated with other grinding mills The process variables in cement grinding process using VRM are strongly nonlinear and having large timePROCESS CONTROL FOR CEMENT GRINDING IN VERTICAL 2024年9月10日 Cement Manufacturing Process Cement manufacturing is an intricate process involving the extraction and grinding of raw materials, followed by blending and heating in a kiln to produce clinker This clinker is then ground with gypsum to create cement, a Cement Manufacturing Process: Know Extraction, Processing
.jpg)
PROCESS ENGINEERING FOR THE CEMENT LIME INDUSTRIES
process engineering for the cement lime industries mechanical engineering (plant design, piping, process gas handling, environmental controls, nuisance dust collection and materials handling, crushing and grinding systems) in engineering, we offer key disciplines cement lime cemento chimborazo epce ucem minera alumbrera (glencorexstrata The grinding process consumes the most energy in cement production, its energy consumption accounts for more than 70% of the total power consumption in the whole process of cement production There are three main grinding processes in cement production: raw meal grinding, cement grinding, and raw coal grindingBall Mill Roller Press for Cement Grinding ProcessNowadays, the dry process is the most popular cement making process which is widely adopted by cement plants all over the world for its great advantages in energy saving and environmental protection Cement Making Process The cement making dry process includes six phases: Raw material extraction/ Quarry; Proportioning, Blending, and GrindingHow Is Cement Produced in Cement Plants Cement Making Process2022年8月15日 Cement Grinding Technology in Cement Production Process English VersionIn this session I will explain about Cement Grinding Technology for cement productioCement Grinding Technology In Cement Production
.jpg)
cement grinding Unit
AGICO Cement is a cement equipment manufacturer supplies EPC projects for cement grinding station with a simple process, easy operation, low investment Get a FREE quote now! Skip to content +86 info@cement 2024年11月4日 A 6week modular course is designed to give the course attendee a solid understanding of the grinding system and its auxiliary equipment The purpose of the training is to Identify and understands necessary known and unknown information towards the completed cycle of the grinding system, whether it is a ball mill, vertical mill, or crushing processGRINDING TECHNOLOGY COURSE The Cement InstituteGas flow, advantage and disadvantage in the Raw mill and Cement mill installations – Grindability concept and the effects of intergrinding materials of different grindability – Ball mill grinding equations and dimensioning – Describe working principles for a separator – Grinding aids and other tools to boost efficiency – Control concepts – Influence of the grinding process on CEMENT GRINDING COURSE The Cement InstituteThe cement roller press, also known as roller press in cement plant, high pressure grinding roll (HPGR), is a kind of cement equipment for brittle materials, apply for grinding cement clinker, cement raw material, gypsum, coal, quartz sand, iron ore, blast furnace slag, and other materials The cement roller press is generally applied to the cement grinding plant, according to the real Cement Roller Press, Roller Press In Cement Plant HPGR Crusher
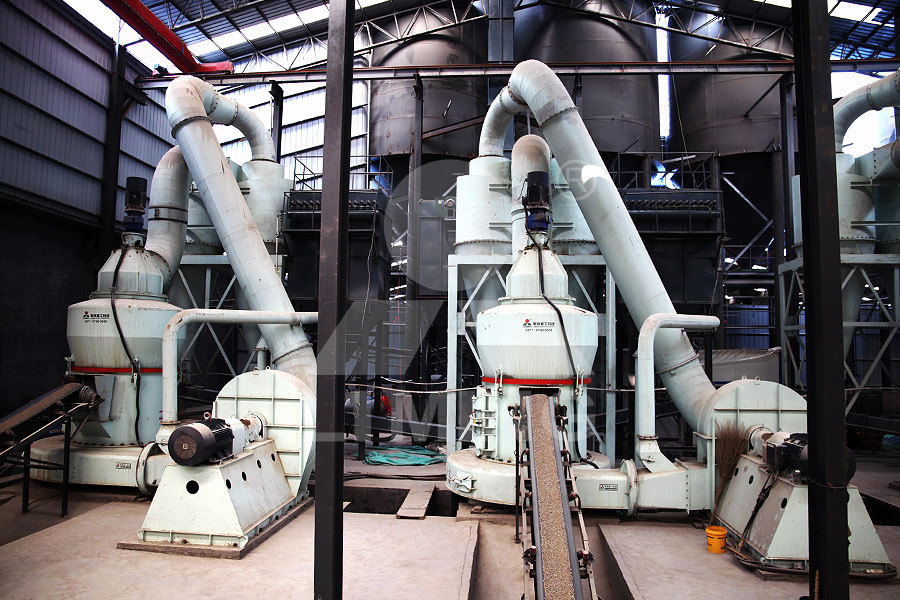
Cement Manufacturing Process The Engineering Community
2018年8月28日 cement manufacturing process phase ii: proportioning, blending grinding; cement manufacturing process phase iii: preheating raw material; cement manufacturing process phase iv: kiln phase; cement manufacturing process phase v: cooling and final grinding; cement manufacturing process phase vi: packing and shipping; cement manufacturing June 2022; ARCHIVE Proceedings of the Institution of Mechanical Engineers Part C Journal of Mechanical Engineering Science 19891996 (vols 203210) 236(2):1107(PDF) A comprehensive review on the grinding process: 2024年1月23日 Is the Grinding Process Expensive? When determining the costeffectiveness of the grinding process, it’s important to consider various factors that contribute to its overall expense Initial Investment: Grinding machines, especially What is Grinding: Definition, Process, Types Specifications2023年8月21日 ICR looks at the inner workings of grinding mills in the cement industry to understand the technological advancements that are reshaping the landscape against the foreground of sustainability Innovations to enhance the grinding processes are aimed at minimising their environmental footprint while increasing efficiency and performance In CuttingEdge Grinding Solutions Indian Cement Review
.jpg)
Cement grinding and packing process Al badia cement
Cement grinding and packing process The clinker is ground with an amount of gypsum to a fine powder in order to regulate the setting time of cement and to gain the most important property of cement, which is compressive strength To produce different types of cement 2023年7月10日 Cement manufacturing is a significant industrial activity that plays a vital role in the construction sector However, the process of cement production is associated with various environmental Cement Manufacturing Process and Its Environmental The power ingesting of a grinding process is 5060% in the cement production power consumption The Vertical Roller Mill (VRM) reduces the power consumption for cement grinding approximately 3040% associated with other grinding mills The process variables in cement grinding process using VRM are strongly nonlinear and having large timePROCESS CONTROL FOR CEMENT GRINDING IN VERTICAL Cement Manufacturing Process Mining Limestone crushing Raw material grinding Homogenisation Preheater and calciner Rotary Kiln and Cooler Cement Grinding Packing; Cement Grinding Clinker is extracted from our clinker tank and transported to the cement mill hopper by belt conveyors A measured Cement Grinding Cement manufacturing process Priya Cement
.jpg)
Mining Activities, Cement Production Process and Quality Control
2022年7月4日 Workshop Manager Laboratory Manager The re are four stages in the manufacture of Portland cement: (1) crushing and grinding the raw The basic principle of blending process is one or 2012年6月1日 Basic kinetic and energy models of the grinding process are described and the most commonly used control strategies are analyzed and discussed +1 Figures uploaded by Vladimir MonovGrinding in Ball Mills: Modeling and Process Control6 天之前 The manufacture of Portland cement is a complex process and done in the following steps: grinding the raw materials, mixing them in certain proportions depending upon their purity and composition, and burning them to sintering in a kiln at a temperature of about 1350 to 1500 ⁰C During this process, these materials partially fuse to form nodular shaped clinker by Manufacturing of Portland Cement – Process and MaterialsThis process was especially evolved to counter the main drawback of the wet process ie high fuel consumption In this process, the raw materials ground in dry condition are homogenized and then nodulised in a pan noduliser of dish or rotary type by adding controlled quantity of water (10 CEMENT MANUFACTURING PROCESS AND ITS SELECTION: WET PROCESS
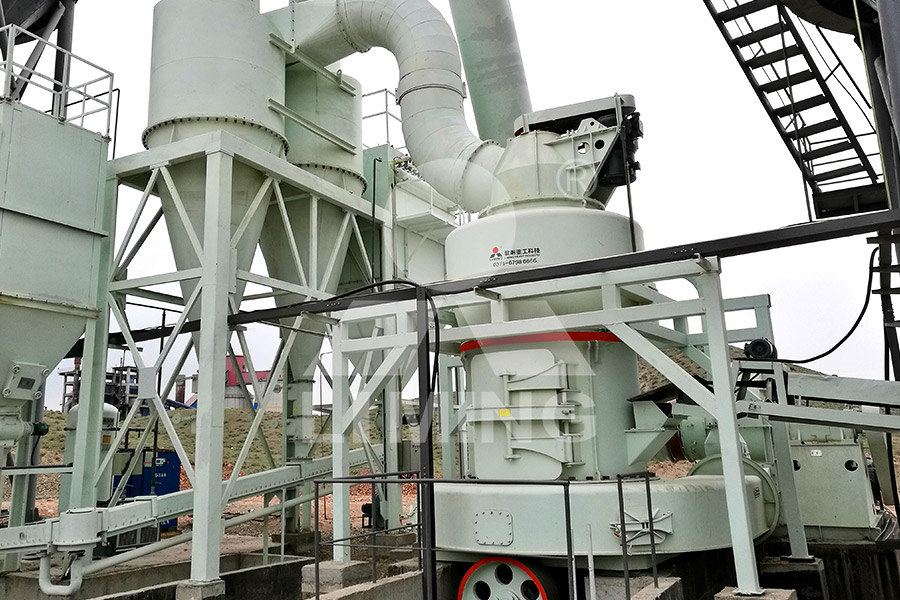
Resistance to Grinding and Cement Paste Performance of Blends
2021年4月19日 Grinding of finished cement is performed in a single stage, intergrinding materials with very different grindabilities This intergrinding process has many different interactions among the different components of the finished cement In a context of developing more sustainable and less energy intensive processes, it is important to understand the 2016年10月23日 The principle of Grate Discharge grinding is nearly universally adapted in the cement grinding industry Grate Discharge Ball Mills are the rule rather than 911 Metallurgist is Only close economic study can determine which process should be used CLINKER GRINDING Clinker, the discharge product from the kiln, is partially cooled Cement Grinding 911MetallurgistThe mill came into use in the 1890s, initially for regrinding rejects, both in dry rawmix and cement grinding Later, they came to be used for the entire grinding process Martin Earles first installed them for autonomous cement grinding in 1899, and in 1904, they were used exclusively at Norman for rawmillingCement Kilns: Size Reduction and Grinding2017年5月19日 Cement industry is characterized by sizeable energy demand which accounts for about 110kWh (375 thm) per ton of cement in modern plants Industry impacts heavily also on CO2 emissionsOverview of cement grinding: fundamentals,
.jpg)
Grinding process is a critical stage in cement
2023年8月21日 Tushar Khandhadia, General Manager – Production, Udaipur Cement Works, discusses the role of grinding in ensuring optimised cement production and a high quality end product How does the grinding process 2019年1月3日 Clinker grinding technology is the most energyintensive process in cement manufacturing Traditionally, it was treated as "low on technology" and "high on energy" as grinding circuits use more than 60 per cent of total energy Clinker grinding technology in cement manufacturing2024年1月17日 According to statistics, the dry cement production line grinding operation consumes Power accounts for more than 60% of the power of the whole plant, of which raw material grinding accounts for more than 30%, coal grinding accounts for about 3%, and cement grinding station account for about 40%What Do You Know About Wet Process Of Cement ProductionStage 2: Grinding, Proportioning, and Blending The crushed raw ingredients are made ready for the cementmaking process in the kiln by combining them with additives and grinding them to ensure a fine homogenous mixture The composition of cement is proportioned here depending on the desired properties of the cement Generally, limestone is 80%, and the remaining 20% How Cement is Made Cement Manufacturing Process
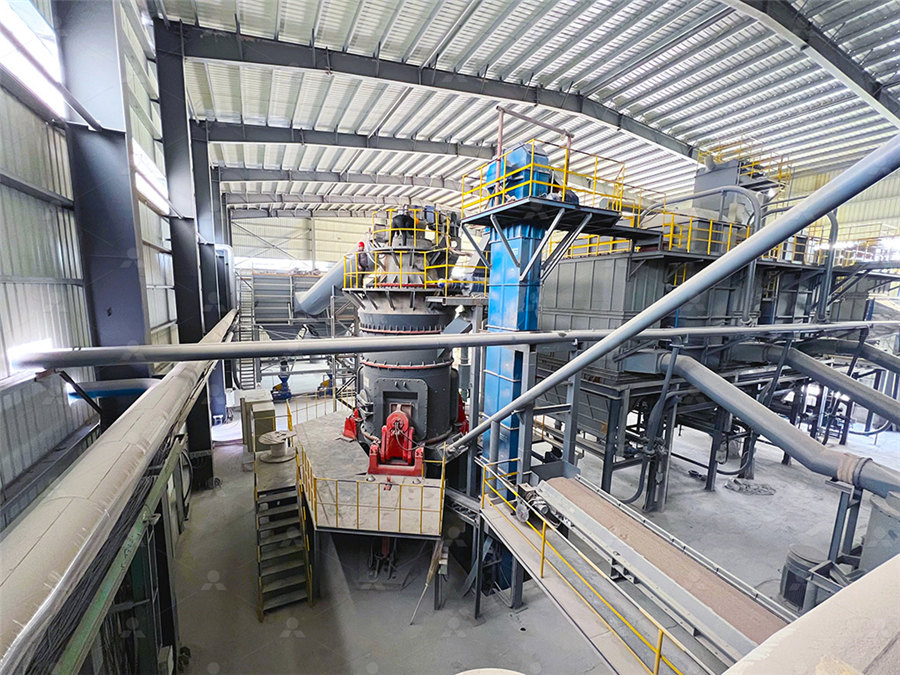
PROCESS CONTROL FOR CEMENT GRINDING IN VERTICAL
The power ingesting of a grinding process is 5060% in the cement production power consumption The Vertical Roller Mill (VRM) reduces the power consumption for cement grinding approximately 3040% associated with other grinding mills The process variables in cement grinding process using VRM are strongly nonlinear and having large time2024年9月10日 Cement Manufacturing Process Cement manufacturing is an intricate process involving the extraction and grinding of raw materials, followed by blending and heating in a kiln to produce clinker This clinker is then ground with gypsum to create cement, a Cement Manufacturing Process: Know Extraction, Processing process engineering for the cement lime industries mechanical engineering (plant design, piping, process gas handling, environmental controls, nuisance dust collection and materials handling, crushing and grinding systems) in engineering, we offer key disciplines cement lime cemento chimborazo epce ucem minera alumbrera (glencorexstrata PROCESS ENGINEERING FOR THE CEMENT LIME INDUSTRIES The grinding process consumes the most energy in cement production, its energy consumption accounts for more than 70% of the total power consumption in the whole process of cement production There are three main grinding processes in cement production: raw meal grinding, cement grinding, and raw coal grindingBall Mill Roller Press for Cement Grinding Process
.jpg)
How Is Cement Produced in Cement Plants Cement Making Process
Nowadays, the dry process is the most popular cement making process which is widely adopted by cement plants all over the world for its great advantages in energy saving and environmental protection Cement Making Process The cement making dry process includes six phases: Raw material extraction/ Quarry; Proportioning, Blending, and Grinding