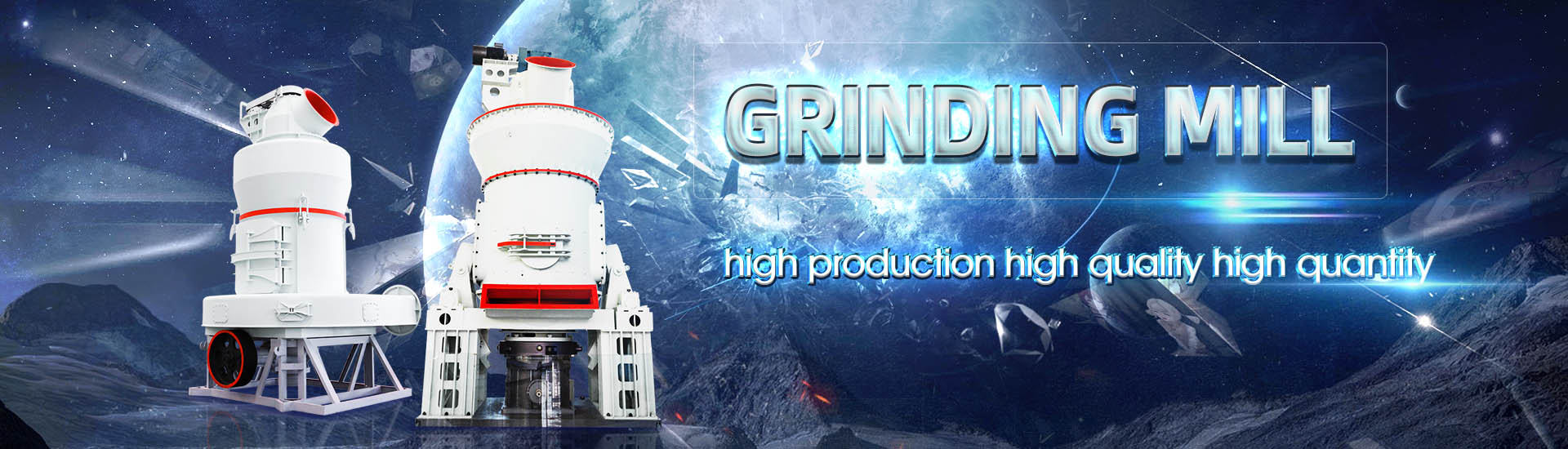
The principle of chemical raw material grinding machine
.jpg)
Grinding Machine: Definition, Parts, Working Principle,
2021年5月5日 A grinding machine is a production machine tool used in the manufacturing industry in which the grinding wheel is attached in the tool post and the workpiece is fixed to the work table and when the operation starts it 2022年6月24日 Grinding is a manufacturing process which significantly contributes in producing high precision and durable components required in numerous applications such as aerospace, (PDF) A comprehensive review on the grinding process: The basic principle of ELID grinding is explained in the previous section with Figure 3 This technology was first proposed by Murata et al (10) back in 1985 They applied the technology Grinding (Machining) an overview ScienceDirect Topics2023年7月4日 The highpressure roller mill, also called the roller presser or the extrusion mill, is a grinding equipment based on the principle of material layer crushingRoller Mill SpringerLink
.jpg)
Principles of Modern Grinding Technology ScienceDirect
Initial considerations include types of inaccuracy, principles of machine design to achieve high machine stiffness and low deflections levels due to grinding forces, temperature rise or This chapter illustrates the different centerless processes and then gives detailed insights into external plunge grinding and the effects of machine design Centerless grinding is a fast and Principles of Modern Grinding Technology ScienceDirectGrinding is the common collective name for machining processes that utilize hard, abrasive particles as the cutting medium The grinding process of shaping materials is probably the Grinding Processes SpringerLink2022年2月28日 Comminuting raw materials are extensively utilized in various industries such as food, cosmetics, electronics, pharmaceutical, cement, recycling, and mineral processing Grinding SpringerLink
.jpg)
Ball mill Wikipedia
A section cutthrough of ball mills A ball mill is a type of grinder filled with grinding balls, used to grind or blend materials for use in mineral dressing processes, paints, pyrotechnics, ceramics, and selective laser sinteringIt works on the June 2022; ARCHIVE Proceedings of the Institution of Mechanical Engineers Part C Journal of Mechanical Engineering Science 19891996 (vols 203210) 236(2):1107(PDF) A comprehensive review on the grinding process: The article discusses prediction and assessment of environmental impacts (effects) on the design and interdisciplinary arts cotton textile environment for industry 30 cotton roller ginning processWORKING PRINCIPLE OF THE COTTON ROLLER 2023年7月4日 It is widely applied in chemical raw materials, nonmetallic processing, refractory materials, and other industries, and is suitable for dry fine grinding of mineral raw materials with Mohs hardness below 6 (such as talc, causticburned magnesia powder, kaolin, wollastonite, gypsum, lime, bentonite, etc), and the particle size can be adjusted between 10 and 100 mmRoller Mill SpringerLink
.jpg)
EnergyEfficient Technologies in Cement Grinding IntechOpen
2016年10月5日 In this chapter an introduction of widely applied energyefficient grinding technologies in cement grinding and description of the operating principles of the related equipments and comparisons over each other in terms of grinding efficiency, specific energy consumption, production capacity and cement quality are given A case study performed on a 2022年1月12日 This machining process is not magic, but scientifically practical This process uses a strongly acidic or alkaline chemical reagent to remove material from the workpiece This is an ageold process prior to 400 BCE when organic chemicals such as citric acids and lactic acids were used to etch metals to manufacture the desired shape of armorsChemical Machining: Definition, Working Principle, Types, A grinder, commonly referred to as a grinding machine, is a power tool designed for grinding materials This machine utilizes an abrasive wheel to cut and shape materials As the wheel rotates, each abrasive grain on its surface removes small amounts of material through a process of shear deformationSize Reduction Equipment: Principle, Types, Uses Benefits IQS Chemical analysis of raw mix, generally on hourly basis Product fineness (Residues) on 90micron and 212micron sieves However, it would be seen that the most significant process and types used for raw material grinding operations in modern cement industry are: Process: Dry Closed circuit drygrinding Type of mill: Ball and tube millsRaw Material DryingGrinding Cement Plant Optimization
.jpg)
Wheat Milling and Flour Testing SpringerLink
2015年1月1日 Flour milling is a technology which combines food science and engineering with the art of the practical miller This chapter aims to help define the science and the art of a process which produces one of the most versatile of bakery raw materials and aims to provide a background to the link between wheat, the milling process and the properties of the final flour2021年11月23日 This is a small grinder operated with electric power It can be easily carried anywhere Grinding can be done by holding it in hand It is used for cleaning heavy welding jobs On one end of the motor shaft, a grinding wheel is fitted and on the other end, a handle or switch for operating the machine is fixed according to our convenience14 Types of Grinding Machines [Working, Diagram PDF] The 2015年1月1日 Separator speed The speed of the separator directly affects the raw material fineness index Either separator speed is too large or too small, it will directly affect the quality of the final collection of the raw material grinding particles (5) Circulating air valve opening Size of the wind also directly affects the raw material fineness indexModeling Based on the Extreme Learning Machine for Raw ture, and the like This requires the choice of suitable machines for grinding [4] An analysis of the machines used for grinding plant raw material in pharmaceutical chemical fac tories has shown that their selection is not the best in many cases and is made without taking into accountMachines for grinding medicinal plant raw material
.jpg)
Principles of Sample Preparation by Grinding or Comminution
material or grinding system is needed to prevent sample loss or promote efficient grinding • Purity of required material: grinding methods often create exposure to other materials of the grinding system or other previously ground materials The most efficient grinding system is a system that applies the minimum amount of energy to rupture 2023年3月21日 A lathe machine is a machine tool which removes the undesired material from a rotating workpiece in the form of chips with the help of a tool which is traversed across the work and can be feed deep into the work A lathe is a machine which is one of the most versatile and widely used machine tool all over the worldLathe Machine: Definition, Parts, Types, Operation, Specification 2 Raw materials management system – 22 Concrete problems 16 1 Raw materials – 2 Raw mix – 3 Reserves – 4 Crushing – 5 Drying – 6 Preblending – 7 Storage and handling 3 Raw milling and blending 3 Computerised Maintenance Management Systems 30 1 Raw milling – 2 Blending – 3 Kiln feed 4 Flames and fuels 38 1The Cement Plant Operations Handbook International Cement It is an essential piece of equipment in many industries, including mining, construction, and chemicals The impact grinding mill works by transferring energy to the materials through impact, resulting in particle size reduction Principles of Operation: 1 Feed material is introduced into the mill: The material to be ground is feed into the The application and principle of impact grinding machine
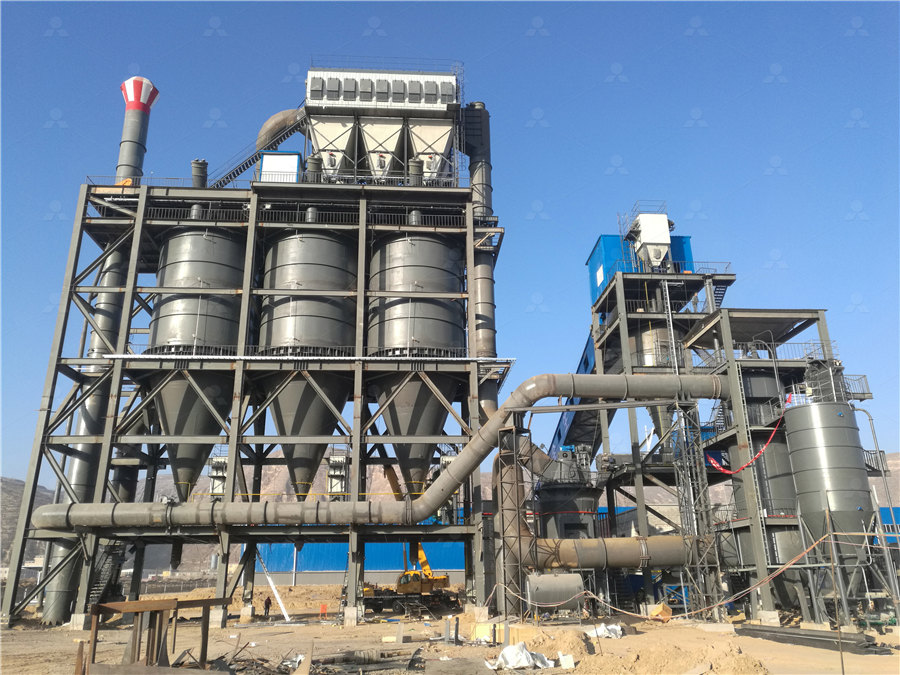
Cement Manufacturing Process INFINITY FOR CEMENT EQUIPMENT
Each raw material has a variety of chemical and mineralogical compositions Weigh feeder is a machine which allows the raw material to the required quantity from the hopper and sent it to the required area Working principle Raw mills uses pressure and shear generated between the rollers and rotating table to crush and grind 2018年8月17日 As is quite evident (Marty knows that you know!), the ultimate objective of processing a mineral is to extract the maximum value from a raw material There are two end results that one is trying toGrinding Mills — Types, Working Principle Applications2024年4月19日 Discover the inner workings of grinding machines and learn how they transform raw materials into finished products 899 Sheridan Dr, West Chester, Pennsylvania Mon – Sat: 9:00am–18 Surface grinding is the most common operation performed on a grinder machine It involves grinding the flat surface of a workpiece to achieve a The Grind: Understanding The Processes Of Grinding MachinesGrinding is the common collective name for machining processes that utilize hard, abrasive particles as the cutting medium The grinding process of shaping materials is probably the oldest in existence, dating from the time prehistoric humans found that they could sharpen their tools by rubbing them against gritty rocksGrinding Processes SpringerLink
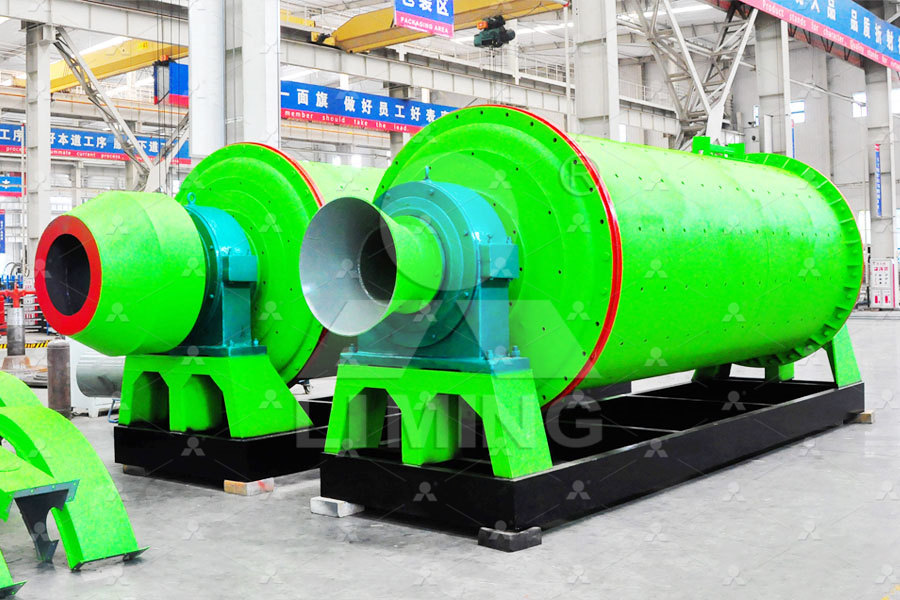
How it Works: Crushers, Grinding Mills and Pulverizers
2017年6月2日 Autogenous grinding (AG) and semiautogenous grinding (SAG) mills use the material to be ground as the grinding media Autogenous grinding mills use larger rocks to impact and break smaller rocks as the mill rotates 2019年10月31日 Definition of pulverization "Pulverization" (comminution, crushing, grinding) is the process of applying an external force to a (solid) material of a certain Definition of pulverization PRODUCT THINKYMIXER; Pulverization 1: Definition and purpose THINKY The grinding disc is not confined to a cylindrical form and is able to come up with a multitude of possibilities That will be useful for moving various geometries in accordance with the objects Read More :Types of Grinding Machine Types Surface Grinding Machine: Types, Parts Working Raw Materials Two important also balance large wheels to reduce the vibration that will be generated when the wheel is spun on a grinding machine Once wheels materials made of diamond or cubic boron nitride—will make such tools a viable option for shaping hard materials Also, advances in the chemical vapor deposition of How grinding wheel is made material, history, used, parts,
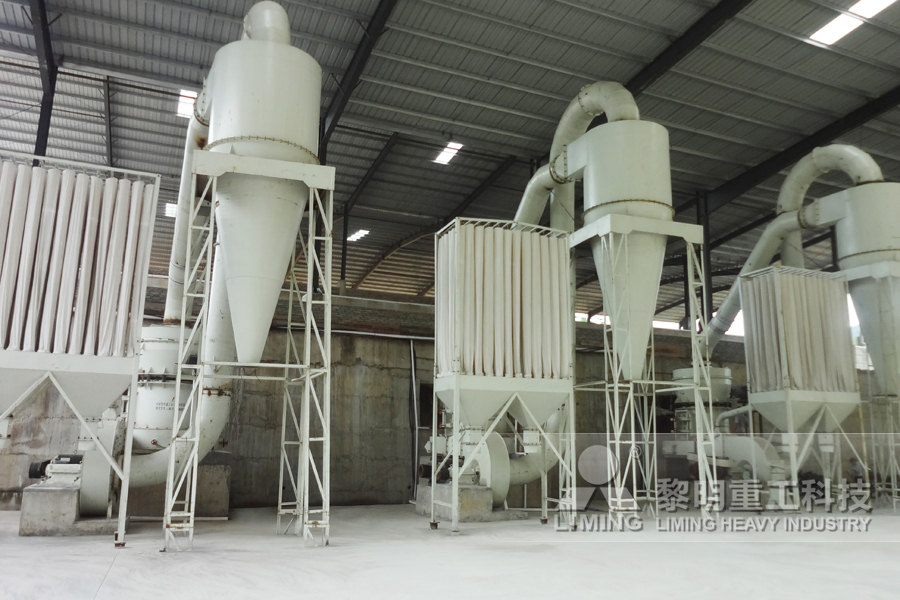
Cement Extraction, Processing, Manufacturing Britannica
2024年11月23日 Soft materials are broken down by vigorous stirring with water in wash mills, producing a fine slurry, which is passed through screens to remove oversize particles Blending A first approximation of the chemical composition required for a particular cement is obtained by selective quarrying and control of the raw material fed to the crushing and grinding plant2023年7月13日 The process of pulping, which turns raw materials like wood chips or recycled paper into pulp slurry, is a basic one in the production of paper Mechanical and chemical pulping are the two main types While mechanical pulping separates fibers from raw materials by grinding them, it may not be appropriate for all types of paperPaper Making Process: From Raw Materials to Finished ProductsElectrochemical Machining Introduction: Electrochemical Machining (ECM): Definition, Parts, Working, Materials, Applications, Principles, Benefits Limitations: – Electrochemical machining utilizes both an electrolyte solution and an electrical flow to alter the workpiece Since electrical conductivity is important for electrochemical machining, the workpiece material should be Electrochemical Machining (ECM): Definition, Parts, Working, Materials materials Therefore, grinding ratio of different kinds of composting materials (4 raw materials and compost samples with different maturity degrees) and affected factors will be encompassed in this study The objectives of this study were to: a) compare grinding ratios of the raw materials of sewage sludge,Relationships Among Raw Materials, Grinding Ratios, and
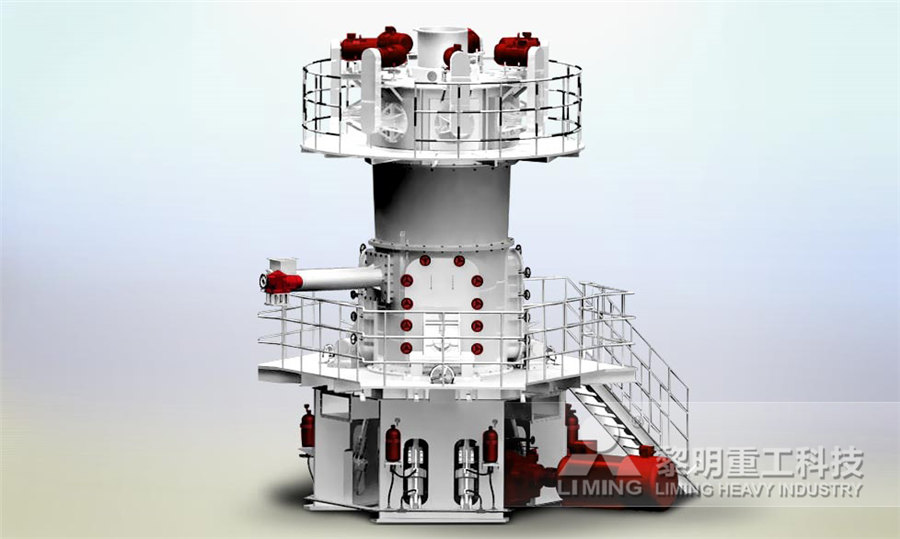
Working principle and characteristics of vertical mill
They are capable of handling different types of materials and producing highly uniform products The working principle of these machines involves force grinding, which ensures consistent results while minimizing energy consumption The characteristics unique to force grinding also make these mills stand out among other milling equipment2015年8月1日 The results show that approximately 248t, 469t, and 341t of materials are required to produce a ton of the product in raw material preparation, clinker production, and cement grinding stages (PDF) Analysis of material flow and consumption inA section cutthrough of ball mills A ball mill is a type of grinder filled with grinding balls, used to grind or blend materials for use in mineral dressing processes, paints, pyrotechnics, ceramics, and selective laser sinteringIt works on the Ball mill WikipediaJune 2022; ARCHIVE Proceedings of the Institution of Mechanical Engineers Part C Journal of Mechanical Engineering Science 19891996 (vols 203210) 236(2):1107(PDF) A comprehensive review on the grinding process:
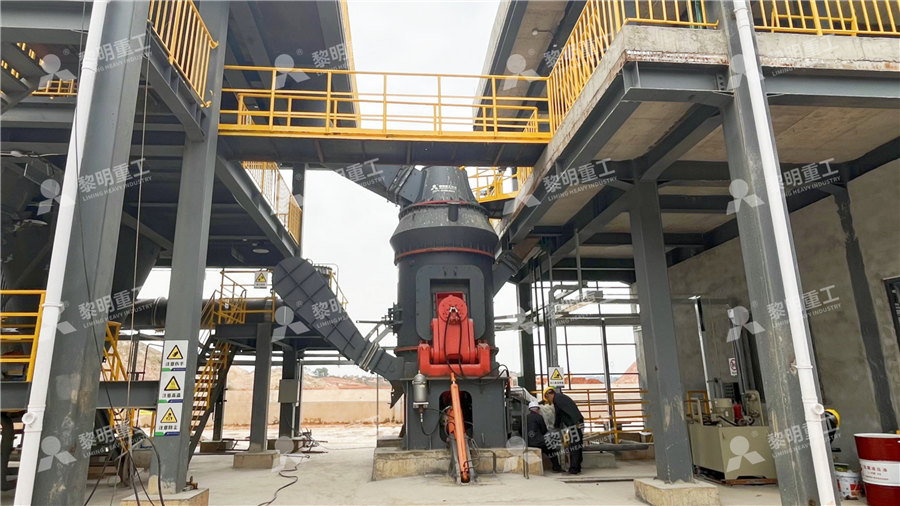
WORKING PRINCIPLE OF THE COTTON ROLLER
The article discusses prediction and assessment of environmental impacts (effects) on the design and interdisciplinary arts cotton textile environment for industry 30 cotton roller ginning process2023年7月4日 It is widely applied in chemical raw materials, nonmetallic processing, refractory materials, and other industries, and is suitable for dry fine grinding of mineral raw materials with Mohs hardness below 6 (such as talc, causticburned magnesia powder, kaolin, wollastonite, gypsum, lime, bentonite, etc), and the particle size can be adjusted between 10 and 100 mmRoller Mill SpringerLink2016年10月5日 In this chapter an introduction of widely applied energyefficient grinding technologies in cement grinding and description of the operating principles of the related equipments and comparisons over each other in terms of grinding efficiency, specific energy consumption, production capacity and cement quality are given A case study performed on a EnergyEfficient Technologies in Cement Grinding IntechOpen2022年1月12日 This machining process is not magic, but scientifically practical This process uses a strongly acidic or alkaline chemical reagent to remove material from the workpiece This is an ageold process prior to 400 BCE when organic chemicals such as citric acids and lactic acids were used to etch metals to manufacture the desired shape of armorsChemical Machining: Definition, Working Principle, Types,
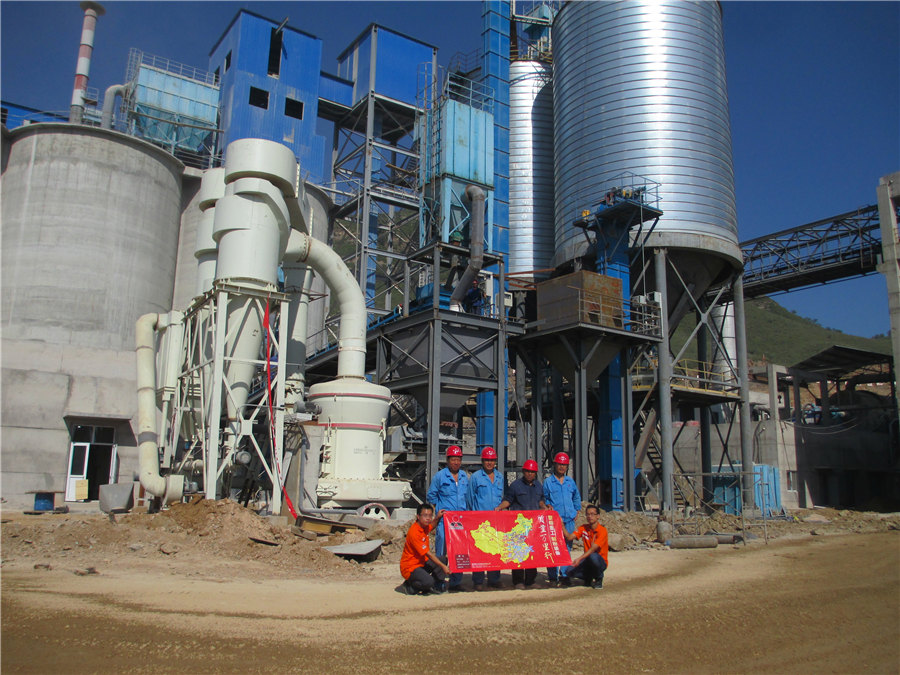
Size Reduction Equipment: Principle, Types, Uses Benefits IQS
A grinder, commonly referred to as a grinding machine, is a power tool designed for grinding materials This machine utilizes an abrasive wheel to cut and shape materials As the wheel rotates, each abrasive grain on its surface removes small amounts of material through a process of shear deformationChemical analysis of raw mix, generally on hourly basis Product fineness (Residues) on 90micron and 212micron sieves However, it would be seen that the most significant process and types used for raw material grinding operations in modern cement industry are: Process: Dry Closed circuit drygrinding Type of mill: Ball and tube millsRaw Material DryingGrinding Cement Plant Optimization2015年1月1日 Flour milling is a technology which combines food science and engineering with the art of the practical miller This chapter aims to help define the science and the art of a process which produces one of the most versatile of bakery raw materials and aims to provide a background to the link between wheat, the milling process and the properties of the final flourWheat Milling and Flour Testing SpringerLink2021年11月23日 This is a small grinder operated with electric power It can be easily carried anywhere Grinding can be done by holding it in hand It is used for cleaning heavy welding jobs On one end of the motor shaft, a grinding wheel is fitted and on the other end, a handle or switch for operating the machine is fixed according to our convenience14 Types of Grinding Machines [Working, Diagram PDF] The