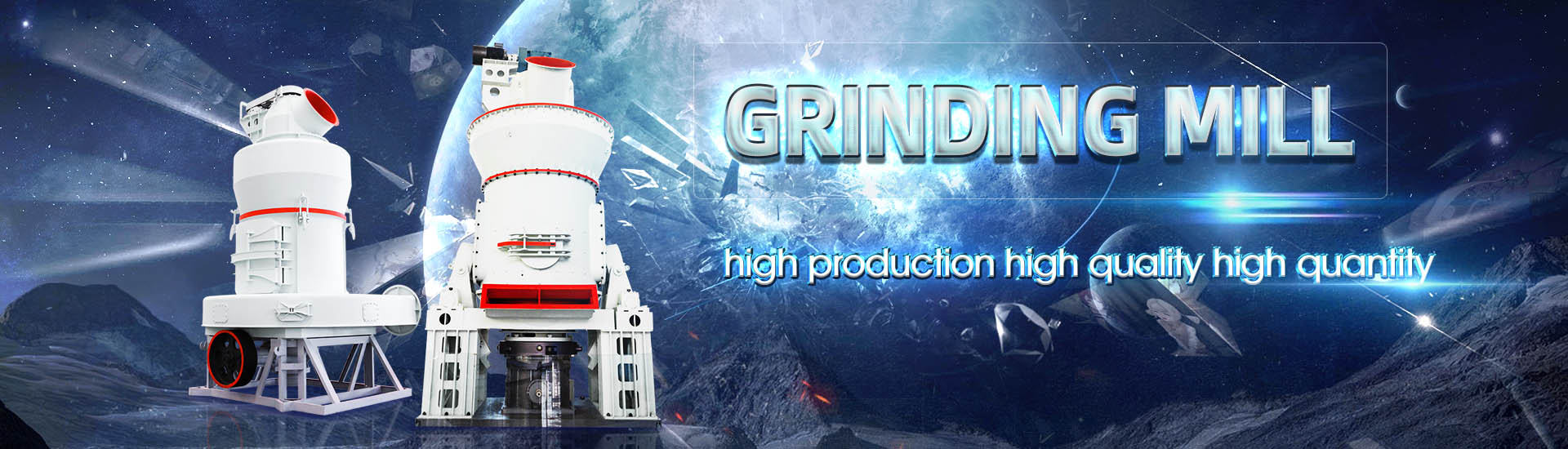
Coking coal ultrafine grinding
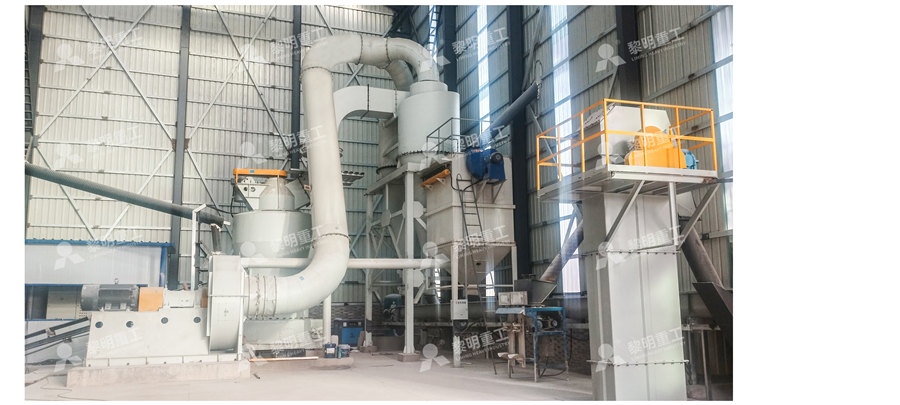
Ultrafine coal grinding and ultraclean coal preparation
The research results showed that the most embedded minerals are clay, which can be sufficiently liberated by coal grinding only down to less than 10 μm; ultraclean coal can be obtained for 2005年4月1日 The research results showed that the most embedded minerals are clay, which can be sufficiently liberated by coal grinding only down to less than 10 μm; ultraclean coal can Ultrafine coal grinding and ultraclean coal preparation2021年5月1日 Ultrafine grinding and decanter centrifugation to recover clean coal from rejects Centrifugation of coalwaterslurry (50% pulp density) produces 19% ash clean coal Extra Sustainability of coal mines: Separation of clean coal from the fine 2021年7月31日 The physical separation method by ultrafine grinding followed by densitygradientcentrifugation resulted in 582% of clean coal yield with coking properties similar to Extraction of clean coal from washery rejects and its effect on
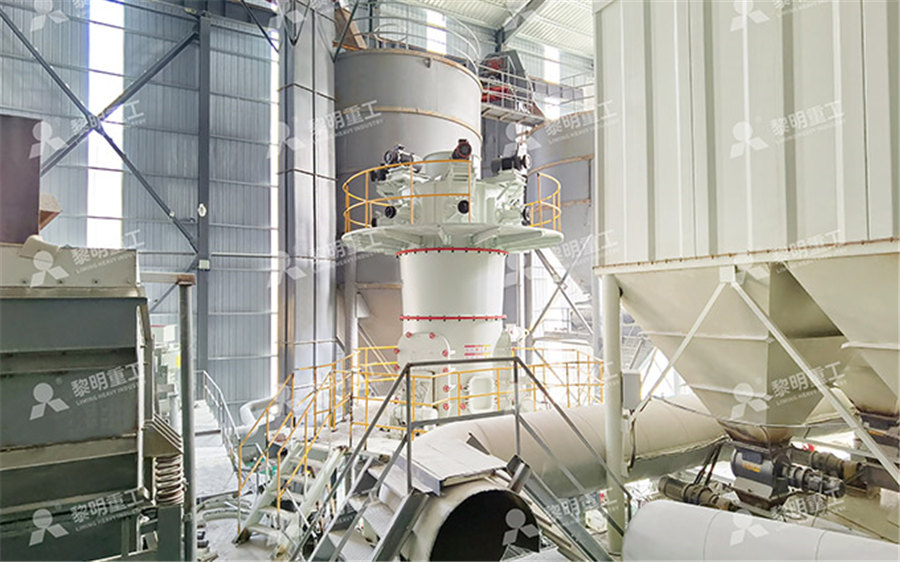
Sustainability of coal mines: Separation of clean coal from the fine
2021年5月1日 However, limited literature is available for ultrafine coal grinding Optimization of some parameters in a modified wateronly cyclone for metallurgical coal production from highash fine coking coals Int J Coal Prep Utiliz, 32 (2012), pp 290297, 101080/20122019年11月1日 Coking coal, which was obtained from the overflow stream of a dense medium cyclone at the Shanghaimiao Central Coal Preparation Plant (Ordos, The kinetics and shape factors of ultrafine dry grinding in a laboratory tumbling ball mill Part Part Syst Charact, 7 (1990), pp 242247 Crossref View in Scopus Google Scholar [32]Differences in dry and wet grinding with a high solid DOI: 101016/jpowtec201909062 Corpus ID: ; Wet and dry grinding of coal in a laboratoryscale ball mill: Particlesize distributions @article{Bu2020WetAD, title={Wet and dry grinding of coal in a laboratoryscale ball mill: Particlesize distributions}, author={Xiangning Bu and Yuran Chen and Guangxi Ma and Yujin Sun and Chao Ni and Guangyuan Xie}, Wet and dry grinding of coal in a laboratoryscale ball mill: 2023年7月10日 The present literature review explores the energyefficient ultrafine grinding of particles using stirred mills The review provides an overview of the different techniques for size reduction and the impact of energy requirements on the choice of stirred mills It also discusses the factors, including the design, operating parameters, and feed material properties, EnergyEfficient Advanced Ultrafine Grinding of Particles Using
.jpg)
Recent advances in the beneficiation of ultrafine coal particles
2018年9月1日 In other cases, ultrafine coal beneficiation is required to achieve low ash content likewise in coking coals When minerals are disseminated finely in the coal, it is necessary to grind coal into small sizes so that organic matters can be liberated from mineral matters Ultrafine coal beneficiation is virtually essential in the later process2021年5月1日 Due to the availability of high ash feedstocks and drift origin, Indian coal washeries face tremendous pressure in maintaining the clean coal yield and handling huge quantities of rejects Since flotation rejects (tailings) discharged in the form of finesized (−500 μ) coalwaterslurry, handling and disposal is an environmental concern and it impacts mine Sustainability of coal mines: Separation of clean coal from the fine 2020年7月1日 Based on the particle size distribution and surface physicochemical characteristics of coal particles, a microenergy consumption model of coal particles in the ultrafine grinding process was Recent developments in beneficiation of fine and ultrafine coal To enhance the utilization rate of coking coal resources, researchers have conducted deep studies on the reseparation of coking coal middlings, which focus on deep dissociation and advanced flotation techniques [3, 4]Due to the gangue that coexists with coal typically having finely embedded particle sizes and complex dissemination characteristics, the flotation Impact of grinding media shape on the dissociation
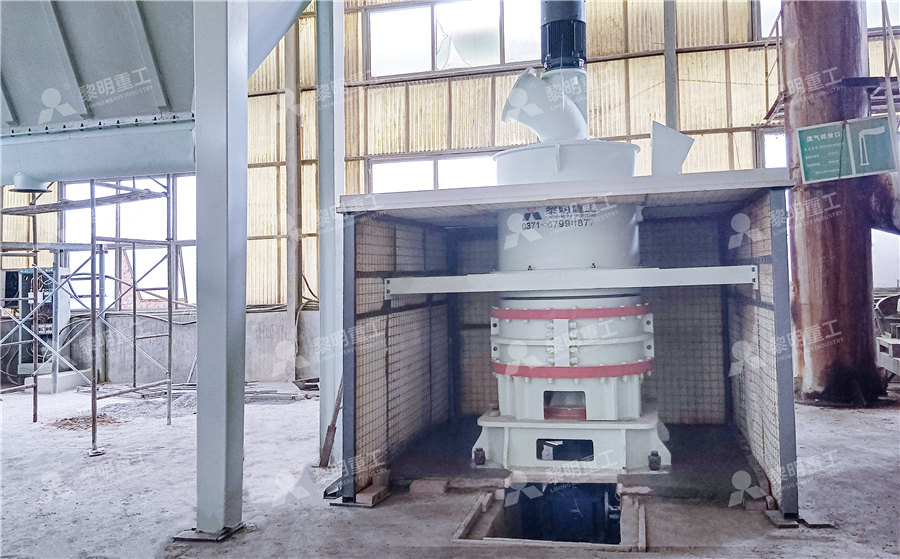
Mechanistic study of the effects of ultrafine grinding on the
2024年9月1日 Additionally, ultrafine coal particles are prone to agglomeration and surface oxidation during ultrafine grinding [10], [11] Consequently, not only achieving finer material granularity, but also considering how to adequately liberate inorganic minerals from coarser particles is important, which can influence both the energy consumption of crushing and 2016年6月8日 Beneficiation of noncoking coal is gaining ground in India It not only reduces the volume of inert content to be transported to the power plant and also lowers the wear in the boiler houses For special applications such as the fuel for integrated gasification combined cycle plant (IGCC), the ash content in the coal should preferably be below 15 % Indian coals are Beneficiation of an Indian noncoking coal by column flotation1999年11月1日 For fine and ultrafine grinding, the Bond work index is an inappropriate measure of grindability, so alternatives are discussed Differences in dry and wet grinding with a high solid concentration of coking coal using a laboratory conical ball mill: Breakage rate, morphological characterization, and induction timeBreakage mechanisms and mill performance in ultrafine grinding2020年3月3日 Kaolinite, as a mineral in fine coal, has an important influence on the flotation of coal particles In this study, the effects of ultrafine kaolinite particles on the flotation recovery of coal particles were investigated Flotation tests were carried out using a mixture of coal particles and different amounts of ultrafine kaolinite particles Combined with the Stefan–Reynold Effect of ultrafine kaolinite particles on the flotation behavior of
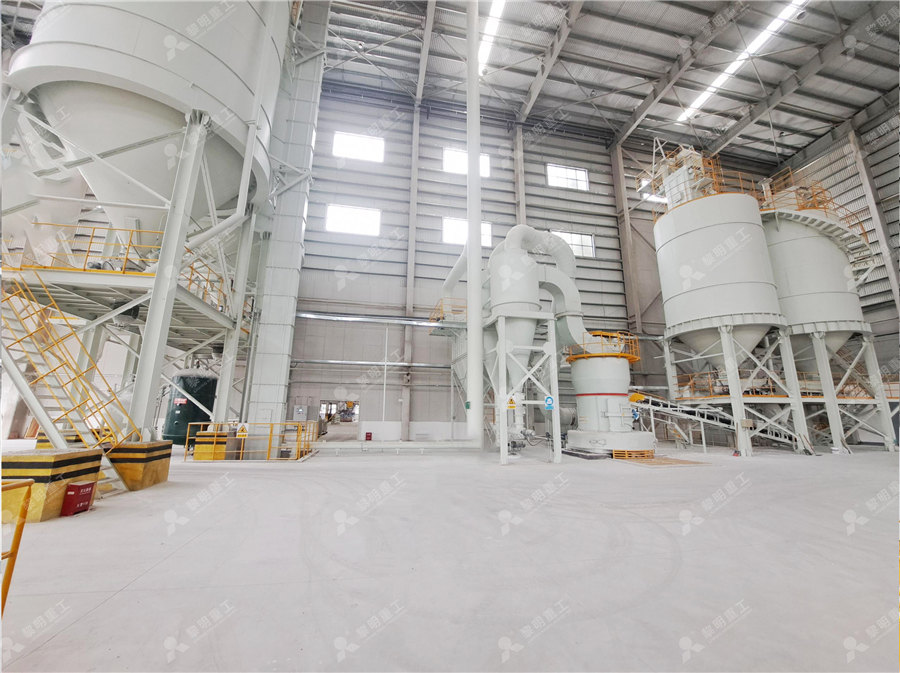
Differences in dry and wet grinding with a high solid
2019年8月1日 Request PDF Differences in dry and wet grinding with a high solid concentration of coking coal using a laboratory conical ball mill: Breakage rate, morphological characterization, and induction 2022年1月1日 The effect of ultrafine dry grinding for up to 1920 min in a planetary ball mill at 300 rpm on size distribution, particle agglomeration and bulk structural changes in a dolomiterich (CaMg(CO3)2 Study on MicroEnergy Consumption Model of Ultrafine Grinding Coal 2019年6月1日 PDF The ultrafine grinding kinetic model for pulverized coal based on the mechanism of grinding process can be used to predict the particle size Find, read and cite all the research you (PDF) Investigation on the ultrafine grinding of coals based on 2018年9月10日 Particle shape has a significant effect on the flotation process of fine mineral and fine coal particles In this paper, the effects of particle shape on the flotation kinetics and behavior of fine coking coal of different size fractions were investigated The coal particles with different shape properties were gained from the grinding and crushing products of the rod mill and jaw Effect of particle shape on the flotation kinetics of fine coking coal
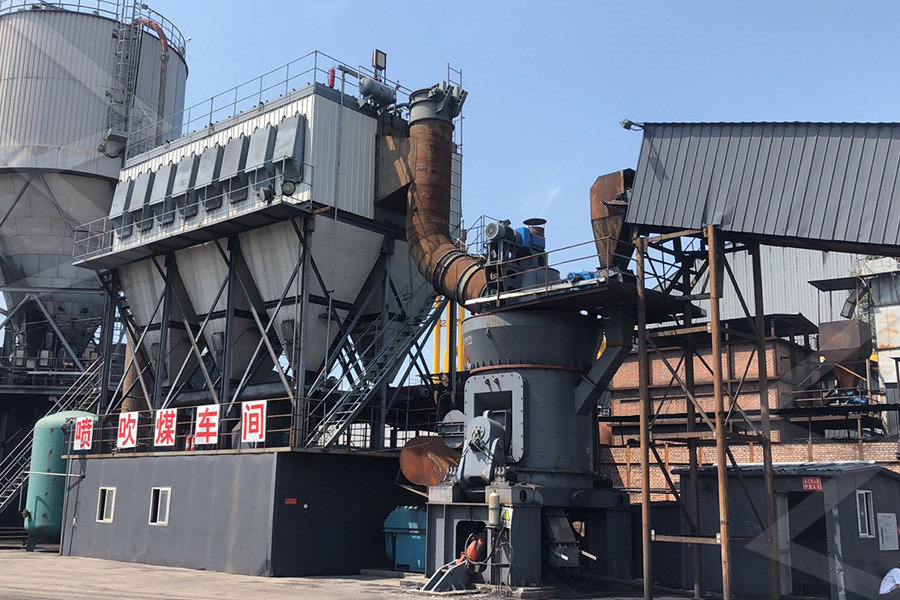
New flotation flowsheet for recovering combustible matter from fine
2019年3月1日 R Chen et al 2018;Wang et al 2019) Moreover, being a type of solid lump waste, coal gangue accounts for more than 25% of the total coal products produced from some coking coal preparation 2020年1月1日 The sample used in this study was coking coal, which was collected from the overflow (clean coal) the breakage mechanism and the performance of the grinding mill [35] However, limited literature is available for ultrafine coal grinding Show abstract Due to the availability of high ash feedstocks and drift origin, Wet and dry grinding of coal in a laboratoryscale ball mill: Particle The experimental coal sample was selected from lowash coking coal from the Shanghaimiao Coal Preparation Plant, Inner Mongolia, China The coal samples were crushed and ground to 05 mm Then, a final coal sample with a size fraction of 025–05 mm and a density less than 1500 kg/ m3 was obtained via the screening test and floatandsink Effect of ultrafine kaolinite particles on the flotation behavior of 2007年3月1日 DOI: 101016/JFUEL200609002 Corpus ID: ; A novel process for preparation of ultraclean micronized coal by high pressure water jet comminution technique @article{Cui2007ANP, title={A novel process for preparation of ultraclean micronized coal by high pressure water jet comminution technique}, author={Longlian Cui and Li Qian An and A novel process for preparation of ultraclean micronized coal by
.jpg)
News How Much Is A Set Of Coking Coal Raymond Mill?
Coking coal is also called metallurgical coal, also known as main coking coal It is a kind of bituminous coal with medium and low volatile content of medium cohesion and strong cohesion In the national standard for coal classification in China, coking coal is the name for bituminous coal with high degree of coalification and good coking In order to give full play to the combustion GENERAL PAPERS A new preparation scheme for a difficulttofloat coking coal by column flotation following grinding Yinfei Liaoa I; Yijun Caoa I; Zhongbo Hub II; Xiuxiang Taoc III I National Engineering Research Center of Coal Preparation and Purification, China University of Mining and Technology, China II Station of Coal Quality Supervision and Inspection, Anhui A new preparation scheme for a difficulttofloat coking coalEffect of ultrafine kaolinite particles on the flotation behavior of coking coal Yijiang Li1 • Wencheng Xia1 • Yaoli Peng1 • Yanfeng Li1 • Guangyuan Xie1 Received: 19 October 2019 Effect of ultrafine kaolinite particles on the flotation behavior of Ultrafine Grinding and the IsaMill™ Technology The IsaMill™ is a largescale energy efficient continuous grinding technology specifically developed for rugged metalliferrous applications Glencore Technology supplies the IsaMill™ technology to mining operations around the world, with over 110 mills installed worldwideUltrafine Grinding and the IsaMill™ Technology
.jpg)
Coking Coal an overview ScienceDirect Topics
Demineralization of low grade coal – A review Pratima Meshram, BD Pandey, in Renewable and Sustainable Energy Reviews, 2015 12 Coking and noncoking coals Coking coals are used for production of coke which is used in steel industries and noncoking coals are required for thermal power plants for steam production Coking coals are hard porous substance that 2003年3月1日 The testing of ultrafine grinding availability as pretreatment prior to leaching for ore must be required A new preparation scheme for a difficulttofloat coking coal from the Kailuan Mine, Preparation of clean coal by flotation following ultra fine liberation2018年5月1日 It has been reported that key factors such as surface roughness, heterogeneity, particle shape, particle size, and contact angle play a role in the wettability of real surfaces [382]Effect of particle shape on the flotation kinetics of fine coking coal float coking coal by column flotation following grinding by Yinfei Liaoa*, Yijun Caoa*, Zhongbo Hub†, and Xiuxiang Taoc ‡ Synopsis A new preparation scheme for a difficulttofloat coking coal from the Kailuan Mine, Tangshan, China was investigated The results showed that grinding followed by column flotation was beneficial for obtaining A new preparation scheme for a difficultto float coking coal by
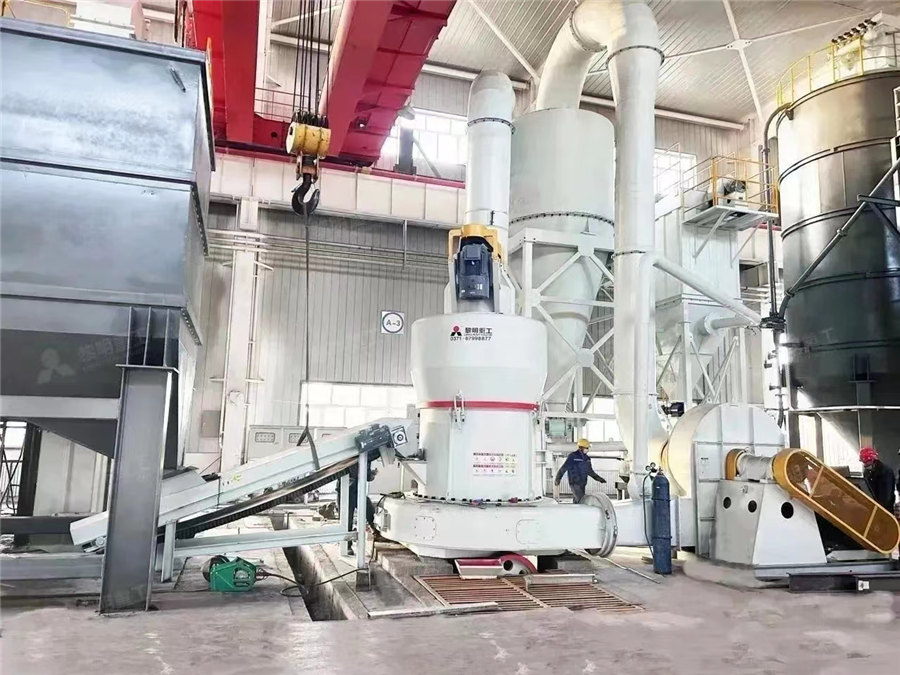
Dewatering of ultrafine coal with Filter Presses
In the past, ultrafine coal (nominally minus 100 micron) was only beneficiated in the former Natal province and in the Waterberg coalfield The coking coals from these areas were amenable to flotation and it was economical to beneficiate the coal using froth flotation (froth flotation was usually employed on the total minus 0,5 mm size fraction)(DOI: 101080/2022) Abstract In this paper, the influence mechanism of grinding fineness on the floatability of coking middings was analyzed by studying the flotation probability, cumulative flotation probability and water recovery in the flotation process The results indicated that in a moderateturbulence intensity flotation environment, the size, density and Study on the influence mechanism of the grinding fineness on the 2021年5月1日 However, limited literature is available for ultrafine coal grinding Optimization of some parameters in a modified wateronly cyclone for metallurgical coal production from highash fine coking coals Int J Coal Prep Utiliz, 32 (2012), pp 290297, 101080/2012Sustainability of coal mines: Separation of clean coal from the fine 2019年11月1日 Coking coal, which was obtained from the overflow stream of a dense medium cyclone at the Shanghaimiao Central Coal Preparation Plant (Ordos, The kinetics and shape factors of ultrafine dry grinding in a laboratory tumbling ball mill Part Part Syst Charact, 7 (1990), pp 242247 Crossref View in Scopus Google Scholar [32]Differences in dry and wet grinding with a high solid
.jpg)
Wet and dry grinding of coal in a laboratoryscale ball mill:
DOI: 101016/jpowtec201909062 Corpus ID: ; Wet and dry grinding of coal in a laboratoryscale ball mill: Particlesize distributions @article{Bu2020WetAD, title={Wet and dry grinding of coal in a laboratoryscale ball mill: Particlesize distributions}, author={Xiangning Bu and Yuran Chen and Guangxi Ma and Yujin Sun and Chao Ni and Guangyuan Xie}, 2023年7月10日 The present literature review explores the energyefficient ultrafine grinding of particles using stirred mills The review provides an overview of the different techniques for size reduction and the impact of energy requirements on the choice of stirred mills It also discusses the factors, including the design, operating parameters, and feed material properties, EnergyEfficient Advanced Ultrafine Grinding of Particles Using2018年9月1日 In other cases, ultrafine coal beneficiation is required to achieve low ash content likewise in coking coals When minerals are disseminated finely in the coal, it is necessary to grind coal into small sizes so that organic matters can be liberated from mineral matters Ultrafine coal beneficiation is virtually essential in the later processRecent advances in the beneficiation of ultrafine coal particles2021年5月1日 Due to the availability of high ash feedstocks and drift origin, Indian coal washeries face tremendous pressure in maintaining the clean coal yield and handling huge quantities of rejects Since flotation rejects (tailings) discharged in the form of finesized (−500 μ) coalwaterslurry, handling and disposal is an environmental concern and it impacts mine Sustainability of coal mines: Separation of clean coal from the fine
.jpg)
Recent developments in beneficiation of fine and ultrafine coal
2020年7月1日 Based on the particle size distribution and surface physicochemical characteristics of coal particles, a microenergy consumption model of coal particles in the ultrafine grinding process was To enhance the utilization rate of coking coal resources, researchers have conducted deep studies on the reseparation of coking coal middlings, which focus on deep dissociation and advanced flotation techniques [3, 4]Due to the gangue that coexists with coal typically having finely embedded particle sizes and complex dissemination characteristics, the flotation Impact of grinding media shape on the dissociation 2024年9月1日 Additionally, ultrafine coal particles are prone to agglomeration and surface oxidation during ultrafine grinding [10], [11] Consequently, not only achieving finer material granularity, but also considering how to adequately liberate inorganic minerals from coarser particles is important, which can influence both the energy consumption of crushing and Mechanistic study of the effects of ultrafine grinding on the 2016年6月8日 Beneficiation of noncoking coal is gaining ground in India It not only reduces the volume of inert content to be transported to the power plant and also lowers the wear in the boiler houses For special applications such as the fuel for integrated gasification combined cycle plant (IGCC), the ash content in the coal should preferably be below 15 % Indian coals are Beneficiation of an Indian noncoking coal by column flotation