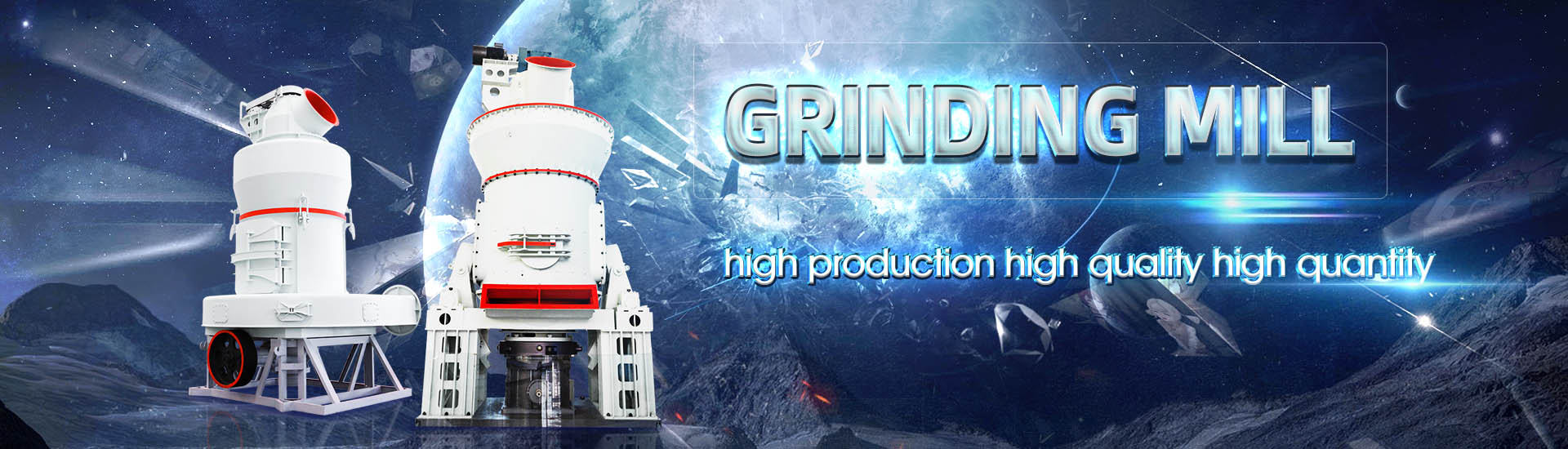
Steel plant sintering machine single roller ore mill installation technical essentials
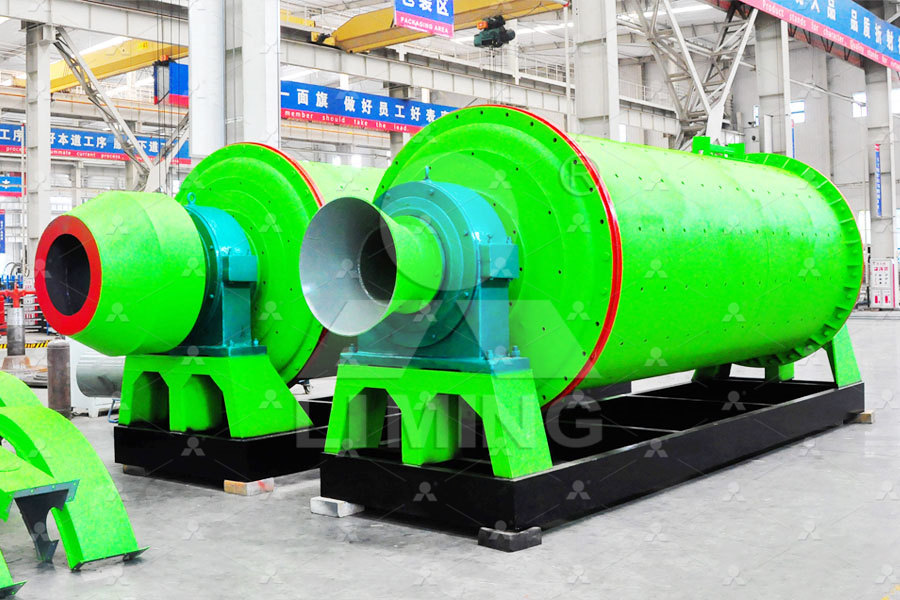
Technical Report UDC 622 341 1 Nippon Steel Corporation
pilot plant for producing and supplying iron ore microparticle binder continuously, a vertical type wettype ball mill was introduced to the Wakayama No 5 Sinter Machine, and the longterm As a leading supplier of complete sinter plants, Primetals Technologies provides engineering, design, and equipment as well as integrated automation solutions Specific technology THE PERFECT SINTER PLANT SOLUTIONS FOR FULLY OPTIMIZED 2020年3月20日 • Bestowed with modern technology VSP has a installed capacity of 3 million tons per annum of liquid steel and 2656 million tons of saleable steel • At VSP, there is emphasis on total automation, seamless Sinter Plant (Vizag Steel Plant) PPT Free DownloadThe Mosaic Embedding Iron Ore Sintering process (MEBIOS) was employed as a new major technology to cope with the possible future need for the use of fine ore in a great quantity in Introduction of New Technologies in Sintering Machine
.jpg)
OPTIMIZATION OF IRON ORE PELLETS PRODUCTION IN SINTER
Sinter plant is one of the major departments of vsp where the iron ore pellets are produced by sintering process By this sintering process the raw materials like limestone, dolomite, coke, 2016年10月19日 The sintering technology is basically an agglomeration process for the iron ore fines which is dependent on heat to melt the surface of the smaller particles together to form larger agglomerates A typical sinter plant consists Sintering Technology for Iron ores and Optimization of In order to break through the bottleneck of ultrathick bed sintering, University of Science and Technology Beijing and Tiangang United Special Steel initiated a cooperation Firstly, by Comprehensive Technologies for Iron Ore Sintering with a Bed Sinter making is an agglomeration process in a steel plant where iron ore fines, coal fines, and fluxes are mixed in a sinter plant to manufacture a product of suitable chemical and physical MET0115TA – Sinter Making Process steeluniversity
.jpg)
Iron Ore Sintering SpringerLink
2024年1月1日 Iron ore sintering is the iron ore powder agglomeration process that changes fine iron ore powder into the lumpy ironbearing raw material used for blast furnace ironmaking 2020年3月20日 Sintering combines iron ore fines in the size range 015–10 mm along with fluxes, solid fuel and various steel plant reverts to form iron ore sinter in the size range of 5–40 Multiobjective Optimization of Integrated Iron Ore Sintering 2015年3月15日 Understanding Sinter and Sinter Plant Operations satyendra; March 15, 2015; 8 Comments ; fluxes, Iron ore fines, SCFA, sinter, sinter plant basic sinter, sintering machine,; Understanding Sinter and Sinter Plant Understanding Sinter and Sinter Plant Operations2022年3月1日 Given the significant contribution of ISI to the emissions of multiple air pollutants, the Chinese central and local governments have formulated a series of policies and standards targeting the ISI, and the emission abatement in the iron and steel sector has been a key focus in the research community (He et al, 2020)At present, most of the studies on the emission Trends in air pollutant emissions from the sintering process of the
.jpg)
Recycling of steel plant mill scale via iron ore ResearchGate
2009年8月1日 Mill scale is an iron oxide waste generated during steelmaking, casting and rolling Total generation of mill scale at JSWSL is around 150 t/day and contains 60–70%FeO and 30–35%Fe2O32014年10月1日 In a test performed in the Loesche test center in Germany, copper slag grinding saved 229% energy in an airswept model and 344% energy in an overflow model [13,14]Copper Ore Grinding in a Mobile Vertical Roller Mill Pilot Plant2019年7月19日 So, the sintering process main objectives are to increase the size of ore additives to a level acceptable to the blast furnace for improving permeability of burden inside the BF; to form a strong agglomerate with high bulk reducibility; to remove volatile matter like CO 2 from carbonates, H 2 O from hydroxides, and sulfur from sulfide type of ore fines along with Sintering: Most Efficient Technologies for Greenhouse Emissions normal feeds that do not contain steel plant wastes, the conventional sintering process is considered as the major source of pollutants within an integrated steel plant The sinter plant produces large quantities of pollutant emissions into air The literature mentions the pollutants: sulphur oxides, nitrogen oxides,RECYCLING OF INTEGRATED STEEL PLANT SOLID WASTES IN THE SINTERING
.jpg)
Maximizing Sintering Plant Heat Recovery 1 Energy Balance in
Maximizing Sintering Plant Heat Recovery 1 Energy Balance in Integrated Steel Mill Fig1 shows a typical energy balance of Japanese Integrated Steel Mill Major energy source are various fuels, steam and electrical power For fuels, 94% is byproduct gases such as blast furnace gas, coke oven gas and LD gas, remaining 6% is purchased fuels2011年1月1日 Red mud (RM), the byproduct generated during the alumina extraction process, is considered a valuable secondary raw material, since iron (2054%) represents its major constituent(PDF) Recycling of mill scale in sintering process Science of lease area is a captive source for Rashtriya Ispat Nigam Ltd (RINL) / Visakhapatnam Steel Plant (VSP) for use of Dolomite in its Iron and Steel making processes The capacity of the mine is to produce 7,80,000 tonnes of Dolomite per annum It is an open cast mechanized mine of VSP to cater to the requirement of DolomiteFUNCTIONS OF VARIOUS DEPARTMENTS OF RINL/VSP MAJOR Vizag Steel2020年3月20日 In the iron ore sintering process, it is desirable to maximize the productivity and quality of sinter while minimizing the fuel consumption for any given raw material (iron ore, flux and solid fuel) quality However, given the complexity of the sintering process and the large number of manipulated variables, it is not practical for operators to identify appropriate set Multiobjective Optimization of Integrated Iron Ore Sintering
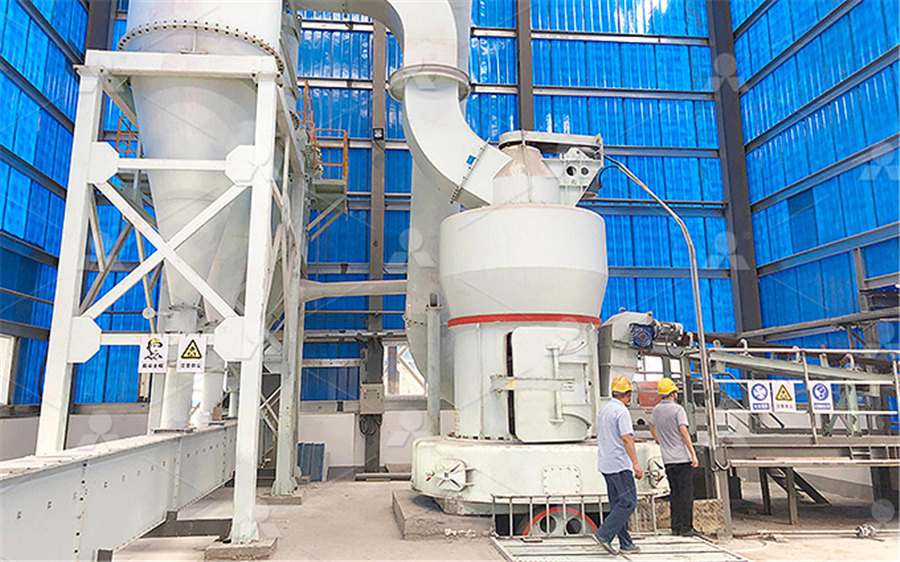
Sintering plant at a glance PPT SlideShare
2014年10月27日 10 10 STOCK BINS AND PROPORTIONING SECTION A TO STOCK RAW MATERIALS : There are three similar series of over head bunker and conveyors to feed three sinter machines at a time Each series contains Metso's Outotec Steel Belt Sintering Furnace is an effective, multicompartment furnace through which pellets are conveyed on a perforated steel belt This treatment gives the pellets a strong structure that can withstand mechanical Steel Belt Sintering Plant Metso2010年6月15日 We had 5 coke oven batteries, a sintering plant, iron ore prep and blending, a power plant and an oxygen generation plant I left the Blast Furnaces for the Power Plant where I spent the rest of my time,19yrs, till the An HO Scale MultiDeck Steel Mill Layout PlanThe document provides technical details for a proposed 150,000 tonne per year profile steel production line in Syria, including specifications for the equipment, processes, raw materials, and finished products It describes a process using continuous casting billets that are reheated and rolled through roughing and tandem mills to produce angle steel, channel steel, and flat steel Technical Specification of Steel Rolling Mill
.jpg)
SINTERING AND PELLETISATION OF INDIAN IRON ORES
High grade iron ore less than 10% of the total reserves ROM iron ore with Fe less than 58 – 60% discarded as waste After beneficiation iron ore availability can improve by about 50% Steel community and the country demand technological solutions for utilising low grade ores The technology task that would be imperative: 12013年7月8日 Factors influencing Sinter and Sintering Process satyendra; July 8, 2013; 8 Comments ; alumina, Burn through point, Flame front, Granulated mix, Grate, Iron ore, LTD, mixing drum, RDI, RI, SFCA, sinter, sinter machine, TI,; Factors influencing Sinter and Sintering Process The sintering process is used to agglomerate a mix of iron ore fines, return fines, Factors influencing Sinter and Sintering Process – IspatGuru2024年4月26日 Iron ore processing is a crucial step in the production of steel, one of the most essential materials in modern society Iron ore, a naturally occurring mineral composed primarily of iron oxides, is mined and processed to extract iron for various industrial applicationsIron Ore Processing: From Extraction to ManufacturingNIPPON STEEL TECHNICAL REPORT No 123 MARCH 2020 Technical Report UDC 622 785 5 Introduction of New Technologies in Sintering Machine Reinforcement Masahide YOSHIKAWA* Shigeru MORISHITA Chikashi KAMIJO Masaru MATSUMURA Abstract In July 2009 and February 2019, the New No 1 and New No 2 blast furnaces at NipponIntroduction of New Technologies in Sintering Machine
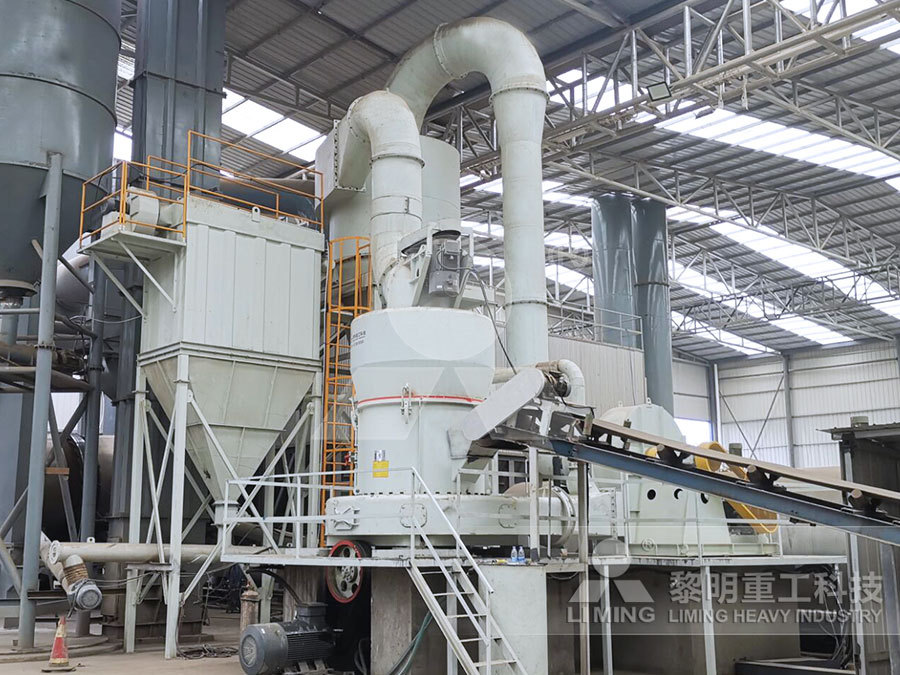
Iron Ore Sintering: Raw Materials and Granulation ResearchGate
2016年10月28日 Sintering is an agglomeration process that fuses iron ore fines, fluxes, recycled products, slagforming elements and coke The purpose of sintering is to obtain a product with suitable 2018年4月11日 2 About SAIL RSP • Rourkela Steel Plant (RSP) is the first of the three integrated steel plants set up by Government of India in 1959 • The first Steel Industry set up under Hindustan Steel limited on 19th January 1954 which paved way for laying up of infrastructure for rapid industrialization of the countrySAIL ROURKELA SINTER PLANT PPT SlideShareSinter Plant Free download as Powerpoint Presentation (ppt), PDF File (pdf), Text File (txt) or view presentation slides online The document discusses the sintering process at a steel plant Key points include: 1) Sintering Sinter Plant PDF Combustion Sintering2020年10月1日 Iron ore sinter plants are energyintensive components of integrated iron and steel production (see Table 1), where the iron ore fines (5 mm) lump sinter cakes with greater gas permeability, which are the most important burden materials for iron making in blast furnaces (BFs) [7]The main process is shown in Fig 2 and described in Recent progress in sustainable and energyefficient technologies
.jpg)
Steel Mills/Works Oil Maintenance
Steel Mill Screw Down Gear System ASIN5037UK Steel / Aluminium 24032009 CJC™ Application Study CCJENSEN A/S Løvholmen 13 DK5700 Svendborg Denmark Phone: +45 6321 2014 Fax: +45 6222 4615 cjcdk Application Study written by: Bryan Holden CCJENSEN Ltd United Kingdom In cooperation with: Charlie Mcginty CorusSintering emissions and their mitigation technologies L Lu, X Li, in Iron Ore, 2015 182251 Sinter plant heat recovery Heat recovered from the waste gas of a sinter plant can be used to preheat the combustion air for the burners and to produce highpressure steam, which can then be used in steam turbines to generate power Various systems exist for new plants (eg, the Sinter Plant an overview ScienceDirect Topics2023年1月15日 When a mixture of mill scale of 5 % was added with 95 % of high barite iron ore concentrate, limestone, sinter return and 12 % of moisture, both the productivity of the sintering machine and the productivity at the blast furnace yard increased with an increase of the coke breeze up to 5 %Reductants in iron ore sintering: A critical review ScienceDirectBall mill is common used grinding plant in the industry, This machine can be can grind all kinds of ores and other materials, which Compare this product Remove from comparison tool ball grinding mill Ф2200×5500 horizontal for ore for cement The POITTEMILL pendulum roller mill is a vertical mill that works by compressing the Ore mill, Ore grinding mill All industrial manufacturers
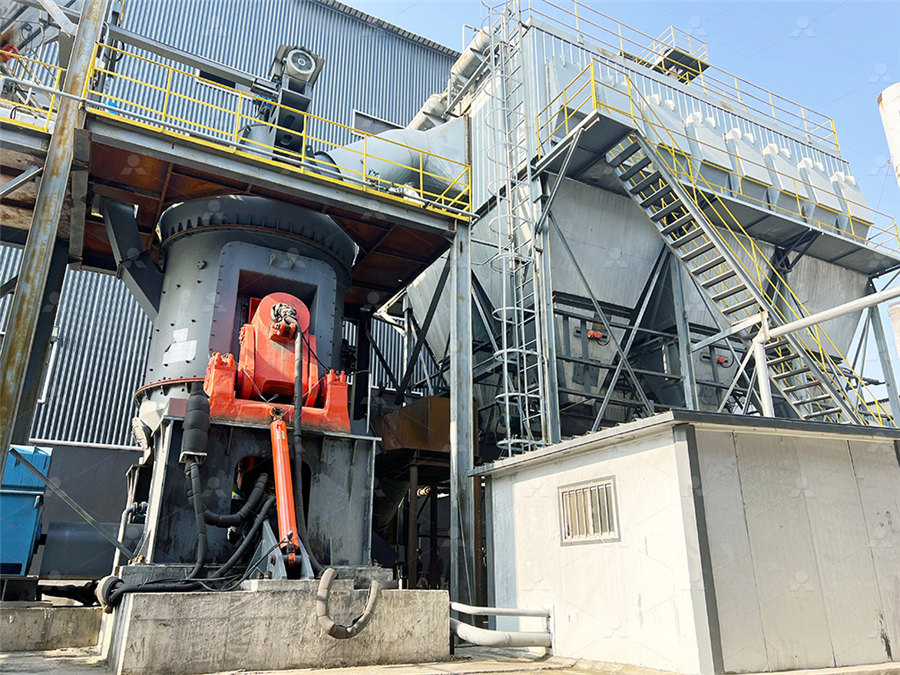
Comparative review on the technologies of briquetting, sintering
ents for agglomeration methods of iron ore via sintering and for the conveyor sintering machine [4] were obtained in Germany in 1902 and in USA in 19071909 Owing to insufficient strength of briquettes and low productivity of briquetting machines, the sintering method was widely applied in the iron and steel industry and nonferrous metalogy of Sintering Machine Large sintering machine with great load, have a high level of automation and installation requirements, which need a serial support of matched technique, and mainly adopt the following techniques: (1) Adjustment technology big and small gates for mixed material Hydraulic system which adopt to working condition wasEfficient and Clean Production Practice of LargeScale Sintering Machine2009年8月1日 Mill scale is an iron oxide waste generated during steelmaking, casting and rolling Total generation of mill scale at JSWSL is around 150 t/day and contains 60–70%FeO and 30–35%Fe2O3 To recover the iron, the mill scale must be smelted in a blast furnace or other reduction furnace; however, it is usually too fine to use without previous agglomeration such Recycling of steel plant mill scale via iron ore pelletisation 5 MODIFICATION OF ROLLER RAIL ARRANGEMENT OF BLENDER RECLAIMER Blender Reclaimer is used for iron ore, lime stone sized iron ore reclaimation in homogenized condition from stock yard in steel plant Blending is a higher level function that aims for obtaining not only the homogeneity of properties over a given productOPTIMIZATION OF IRON ORE PELLETS PRODUCTION IN SINTER PLANT
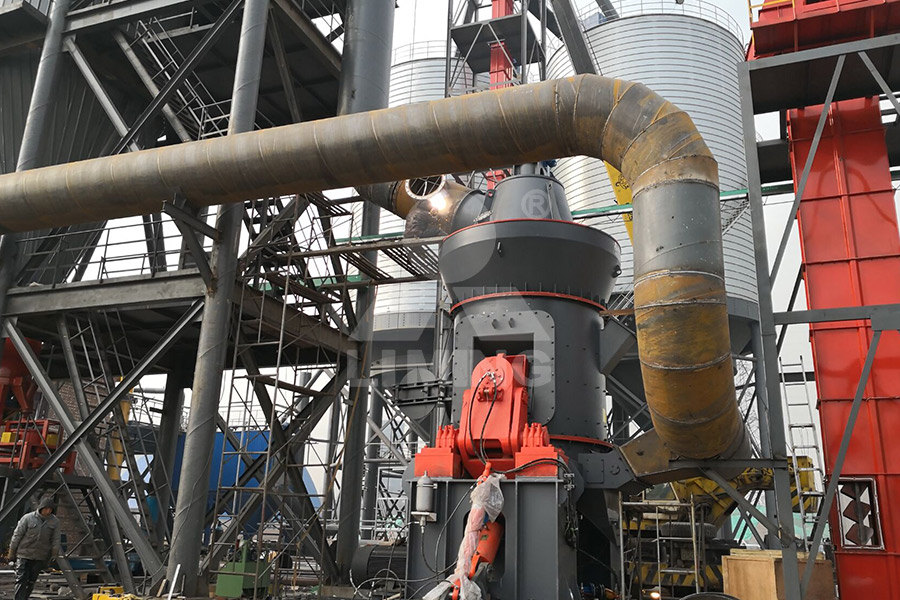
Understanding Sinter and Sinter Plant Operations
2015年3月15日 Understanding Sinter and Sinter Plant Operations satyendra; March 15, 2015; 8 Comments ; fluxes, Iron ore fines, SCFA, sinter, sinter plant basic sinter, sintering machine,; Understanding Sinter and Sinter Plant 2022年3月1日 Given the significant contribution of ISI to the emissions of multiple air pollutants, the Chinese central and local governments have formulated a series of policies and standards targeting the ISI, and the emission abatement in the iron and steel sector has been a key focus in the research community (He et al, 2020)At present, most of the studies on the emission Trends in air pollutant emissions from the sintering process of the 2009年8月1日 Mill scale is an iron oxide waste generated during steelmaking, casting and rolling Total generation of mill scale at JSWSL is around 150 t/day and contains 60–70%FeO and 30–35%Fe2O3Recycling of steel plant mill scale via iron ore ResearchGate2014年10月1日 In a test performed in the Loesche test center in Germany, copper slag grinding saved 229% energy in an airswept model and 344% energy in an overflow model [13,14]Copper Ore Grinding in a Mobile Vertical Roller Mill Pilot Plant
.jpg)
Sintering: Most Efficient Technologies for Greenhouse Emissions
2019年7月19日 So, the sintering process main objectives are to increase the size of ore additives to a level acceptable to the blast furnace for improving permeability of burden inside the BF; to form a strong agglomerate with high bulk reducibility; to remove volatile matter like CO 2 from carbonates, H 2 O from hydroxides, and sulfur from sulfide type of ore fines along with normal feeds that do not contain steel plant wastes, the conventional sintering process is considered as the major source of pollutants within an integrated steel plant The sinter plant produces large quantities of pollutant emissions into air The literature mentions the pollutants: sulphur oxides, nitrogen oxides,RECYCLING OF INTEGRATED STEEL PLANT SOLID WASTES IN THE SINTERING Maximizing Sintering Plant Heat Recovery 1 Energy Balance in Integrated Steel Mill Fig1 shows a typical energy balance of Japanese Integrated Steel Mill Major energy source are various fuels, steam and electrical power For fuels, 94% is byproduct gases such as blast furnace gas, coke oven gas and LD gas, remaining 6% is purchased fuelsMaximizing Sintering Plant Heat Recovery 1 Energy Balance in 2011年1月1日 Red mud (RM), the byproduct generated during the alumina extraction process, is considered a valuable secondary raw material, since iron (2054%) represents its major constituent(PDF) Recycling of mill scale in sintering process Science of

FUNCTIONS OF VARIOUS DEPARTMENTS OF RINL/VSP MAJOR Vizag Steel
lease area is a captive source for Rashtriya Ispat Nigam Ltd (RINL) / Visakhapatnam Steel Plant (VSP) for use of Dolomite in its Iron and Steel making processes The capacity of the mine is to produce 7,80,000 tonnes of Dolomite per annum It is an open cast mechanized mine of VSP to cater to the requirement of Dolomite2020年3月20日 In the iron ore sintering process, it is desirable to maximize the productivity and quality of sinter while minimizing the fuel consumption for any given raw material (iron ore, flux and solid fuel) quality However, given the complexity of the sintering process and the large number of manipulated variables, it is not practical for operators to identify appropriate set Multiobjective Optimization of Integrated Iron Ore Sintering