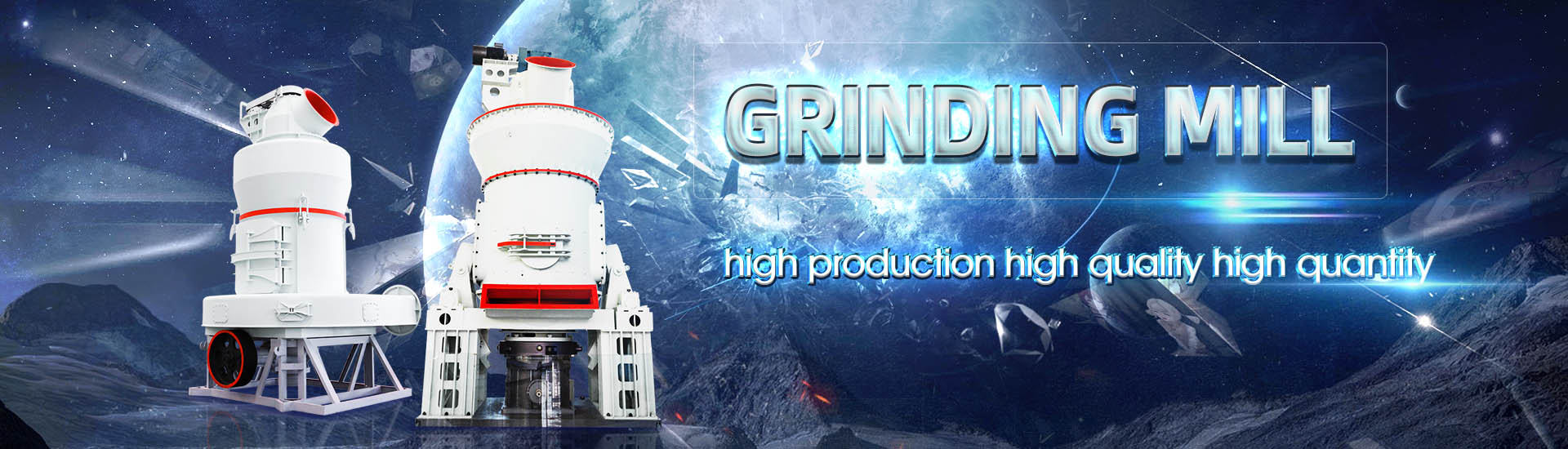
Limestone desulfurization system
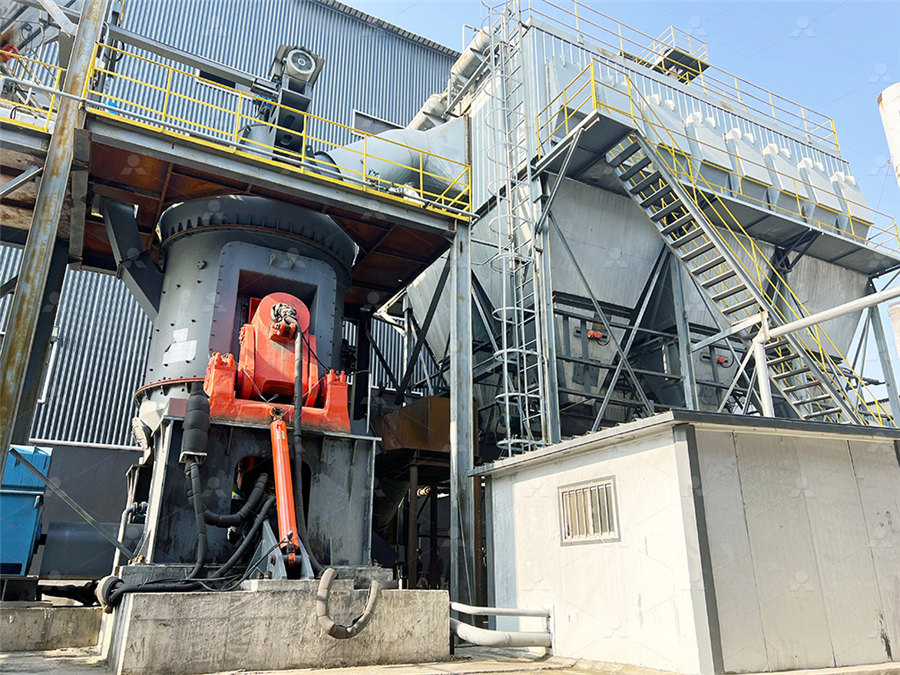
Status of Flue Gas Desulphurisation (FGD) systems from coalfired
2015年3月15日 The two most significant factors in wet limestone FGD systems, for economic reasons, are the desulphurisation efficiency (SO 2 retention) and the residual limestone level Limestone forced oxidation (LSFO) is a newer process based on wet limestone scrubbing which reduces scale In LSFO, air is added to the reaction tank which oxidizes the spent slurry to Air Pollution Control Technology Fact Sheet US EPANew wet FGD systems can be supplied with either forced oxidation or inhibited oxidation Since the mid1980s, limestone forced oxidation has been the leading wet FGD technology This WET FLUE GAS DESULFURIZATION (FGD) SYSTEMSWet scrubbers are used in utilities, paper mills, and chemical plants to remove sulfur dioxide (SO 2) and other pollutants from gas streams Undesirable pollutants are removed by contacting Lime / Limestone Wet Scrubbing System for Flue Gas Desulfurization
.jpg)
Flue Gas Desulfurization Lime
More than ninety percent of US flue gas desulfurization (FGD) system capacity uses lime or limestone This trend will likely continue into the next phase of federally mandated SO 2 2020年11月11日 Wet flue gas desulfurization was simulated to improve gypsum production using lowgrade limestone Highgrade limestone with 94 wt% CaCO 3 content is used for Modeling of the wet flue gas desulfurization system to utilize low 2019年3月13日 Most coalfired power plants in China use wet flue gas desulfurization (WFGD) as the main method for SO 2 removal Presently, the operating of WFGD lacks accurate modeling method to predict outlet Modeling and optimization of wet flue gas 2001年5月19日 A detailed process model of the wet limestone flue gas desulfurization system has been presented This model can be used to calculate indispensable parameters for Model of the Wet Limestone Flue Gas Desulfurization Process for
.jpg)
New LimestoneGypsum Flue Gas Desulfuization Technology
Abstract: A new wet FGD processes which SO 2 was absorbed in the spray tower using granular limestone simultaneously adding acetic acid had been proposed The main difference removal with system availability greater than 995% 2 3 a worldwide leader in supplying limestone forced oxidation units, and we continue to support this technology While limestone forced oxidation technology has proven successful in many worldwide installations, in some applications, the gypsum byproduct is no longer marketable,WET FLUE GAS DESULFURIZATION (FGD) SYSTEMS Babcock2015年3月15日 It can be stated that wet limestone FGD system is the FGD process most widely used because of its high desulphurisation performance and low United States Environmental Protection Agency (US EPA) Flue gas desulfurization system capabilities for coalfired steam generators Vol II Technical Report EPA600/778032b; March 1978 Status of Flue Gas Desulphurisation (FGD) systems from coal Comparing Lime and Limestone SO 2 Wet Scrubbing Processes More than ninety percent of US flue gas desulfurization (FGD) system capacity uses lime or limestone This trend will likely continue into the next phase of federally mandated SO 2 Flue Gas Desulfurization Lime
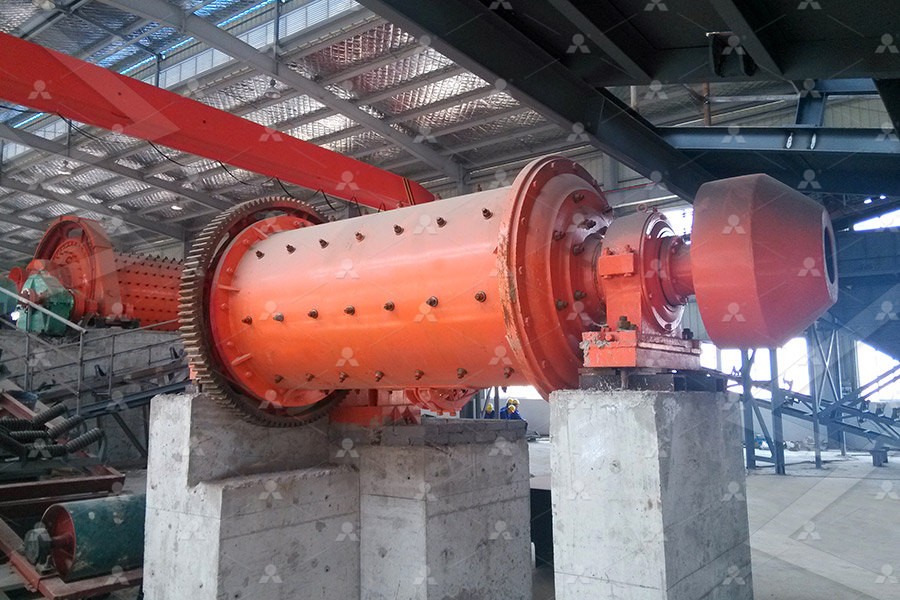
LimestoneGypsum Wet Flue Gas Desulfurization Wastewater Treatment
2021年2月1日 Finally, the effluent quality of the system is better than the discharge requirements of “Discharge standard of wastewater from limestonegypsum flue gas desulfurization system in fossil fuel 2023年3月15日 Numerous researchers have investigated the effects of various buffering additives on the desulfurization of limestone slurries Commercially available buffering additives include organic additives, such as benzoic, adipic, formic, acetic, and citric acids, and inorganic additives, such as sodium, ammonium, and sulfate salts [4], [14], [16]Desulfurization characteristics of limestone slurry with added Max Capacity 1,050 MW Max Inlet SO 2 Concentration 80,000 mg/Nm 3 (Coal fired) Max SO 2 Removal Efficiency 99% High Reliability The flue gas desulfurization (FGD) plant removes sulfur dioxides (SO 2) from flue gas produced by boilers, furnaces, and other sourcesMitsubishi Power effectively contributes to the prevention of air pollution through its wet limestone Flue Gas Desulfurization (FGD) Plants Mitsubishi PowerLimestoneforced oxidation (LSFO), limestoneinhibited oxidation (LSIO), jet bubbling reactor In a oncethrough system, the spent slurry is dewatered to disposal or used as a byproduct ESP + WFGD, or the ESP + DFGD (dry flue gas desulfurization) + FF system, which generally emitted gas with a higher Hg 2+ proportionFlueGas Desulphurization an overview ScienceDirect Topics
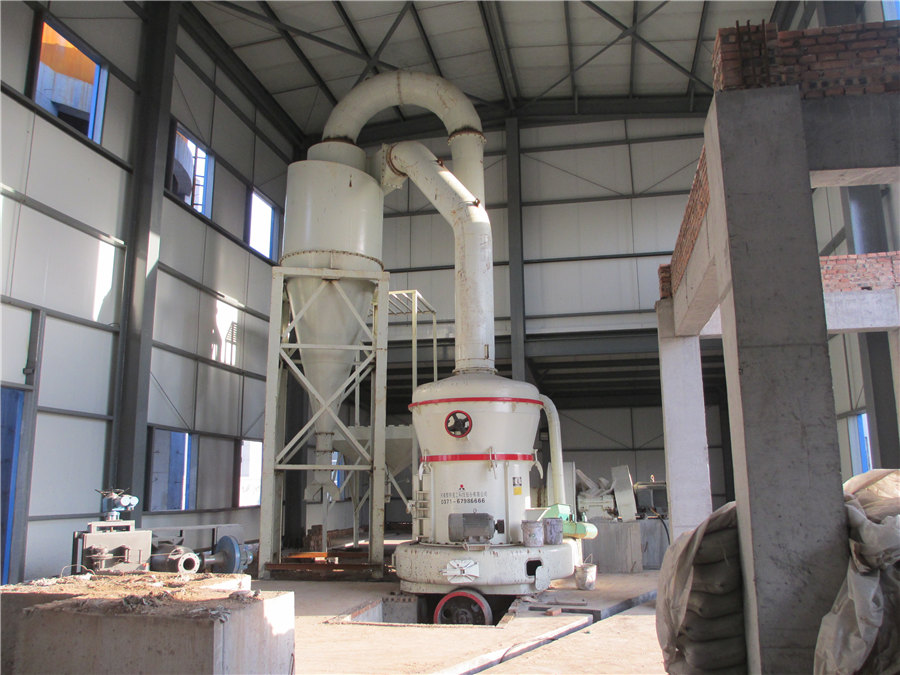
Enhancement of citric acid on lowgrade limestone wet desulfurization
2022年6月15日 However, the desulfurization efficiency would be definitely less optimistic for WFGD process when using lowgrade limestone as absorbent in view of its relatively large contents of impurities including CaMg(CO 3) 2, SiO 2, Al 2 O 3 and Fe 2 O 3 [13]As such, possibly effective attempts to upgrade the lowgrade limestone have been actively studied in 2021年6月1日 Zhong et al (Zhong et al, 2008) developed a model of limestone/gypsum wet flue gas desulfurization (WFGD) system based on unsteady theory The influences of liquidtogas ratio, SO 2 concentration of inlet flue gas, and combination mode of different spray levels to the desulfurization efficiency were analyzedSimulation of SO2 absorption and performance enhancement of wet flue 2008年11月1日 In this paper, a model of limestone/gypsum wet flue gas desulfurization (WFGD) system was developed based on unsteady theory The models of processes of absorption section and oxidation section were developed and incorporated into the WFGD integral modelA model for performance optimization of wet flue gas desulfurization 2002年4月1日 This paper presents a new liquidscreen gasliquid twophase flow pattern with discarded carbide slag as the liquid sorbent of sulfur dioxide (SO2) in a wet flue gas desulfurization (WFGD) systemOptimum Values of Process Parameters of the “Wet Limestone
.jpg)
Analytical Investigation and Design of Flue Gas Desulfurization System
Keywords: Flue Gas Desulfurization, FGD sytem design, SO 2 removal, limestone scrubbing, flue gases 1 Introduction 1The term flue gas desulfurization has traditionally referred to wet scrubbers that remove sulphur dioxide (SO 2) emissions from large boilers (mainly coal and oil fired combustion) However, because of the2024年1月10日 Flue gas desulfurization (FGD) is a critical process for reducing sulfur An investigation by Uddin et al 30 on the limestoneforced oxidation (LSFO) FGD system in a supercritical coalfired Modeling based on machine learning to investigate flue gas The limestonegypsum wet flue gas desulfurization system has been widely used due to its remarkable desulfurization effect, but there are still problems such as high operation and maintenance costs, difficult control of process indicators, and large energy consumption In view of the above problems, this paper proposes to apply the CyberPhysical System (CPS) to the Limestonegypsum wet flue gas desulfurization based on Cyber 2023年2月6日 Limestonegypsum wet flue gas desulfurization (WFGD) process is widely used in coalfired power plants in China because of its technical characteristics of high desulfurization efficiency, mature process, and strong adjustability (Córdoba, 2017; Wang et al, 2010)With the continuous improvement of atmospheric emission standards, the demands for slurry quality Diagnosis and Traceability Analysis of Slurry Foaming of Limestone
.jpg)
Desulphurisation an overview ScienceDirect Topics
This results in calcium compounds enrichment in the end product, which is highly dependent upon the used desulfurization technology (Twardowska, 1999b) In the dry method, limestone or pulverized limestone is injected into the boiler furnace, where the calcium carbonate decomposes thermally to form calcium oxide and carbon dioxide2024年8月13日 The system is based on absorption of SO 2 from the flue gas into a limestone slurry Captured SO 2 is subsequently converted to solid gypsum, a saleable byproduct, and removed from the system The primary unit operations utilized in the LSFO process are as follows: 1,2,3 Limestone Preparation: Limestone (CaCO 3) canFlue Gas Desulfurization: Detailed Process OverviewAquí nos gustaría mostrarte una descripción, pero el sitio web que estás mirando no lo permiteACS PublicationsIn this article the method of cost optimization of the “Wet Limestone Flue Gas Desulfurization System” is presented The optimization calculations include process and cost models The process model describes the most important stage of SO 2 removal that runs in the absorber and in the holding tankOptimum Values of Process Parameters of the “Wet Limestone
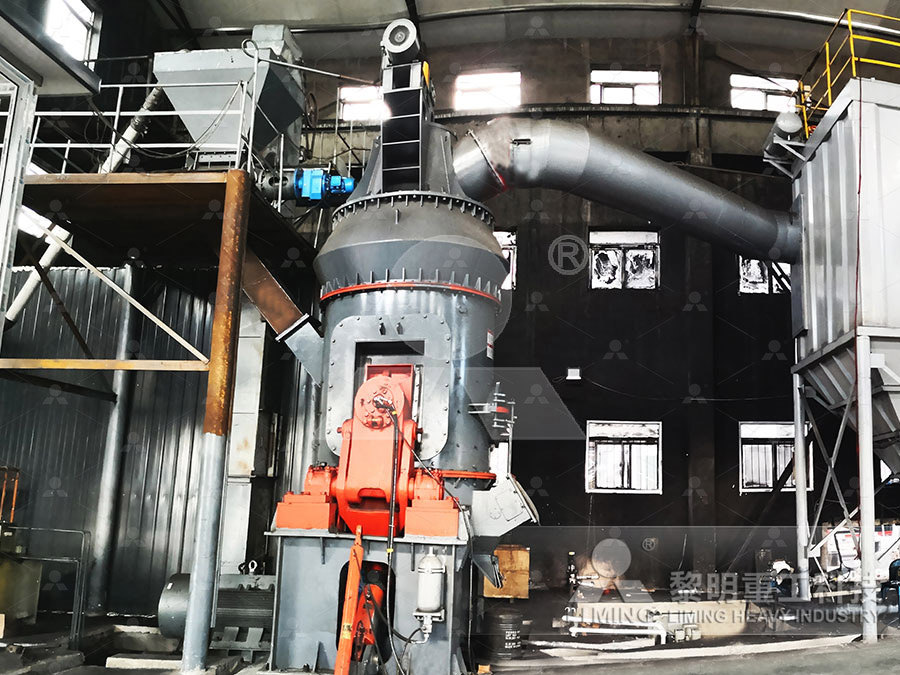
Insights into the desulfurization mechanism of lowgrade limestone
2021年12月1日 From the analysis above, it can be deduced that the desulfurization process by using lowgrade limestone as SO 2 absorbent is divided into three stages: (1) SO 2 dissolves into LGL slurry firstly followed by the formation of SO 3 2−, HSO 3 − and H 2 SO 3 species [21]; (2) continuous dissolution of Cabased compound including CaCO 3 and CaMg 2015年10月30日 A Review of Desulfurization Technology using Limestone in Circulating Fluidized Bed Boiler Type Power Plant October 2015; Journal of the Korean Institute of Resources Recycling 24(5):314;(PDF) A Review of Desulfurization Technology using 2002年4月1日 In this article the method of cost optimization of the Wet Limestone Flue Gas Desulfurization System is presented The optimization calculations include process and cost models The process model describes the most important stage of SO 2 removal that runs in the absorber and in the holding tank It includes absorption of sulfur dioxide, oxidation of SO 3 2 , Optimum values of process parameters of the Wet Limestone 2001年5月19日 A detailed process model of the wet limestone flue gas desulfurization system has been presented This model can be used to calculate indispensable parameters for estimating costs and next to Model of the Wet Limestone Flue Gas Desulfurization
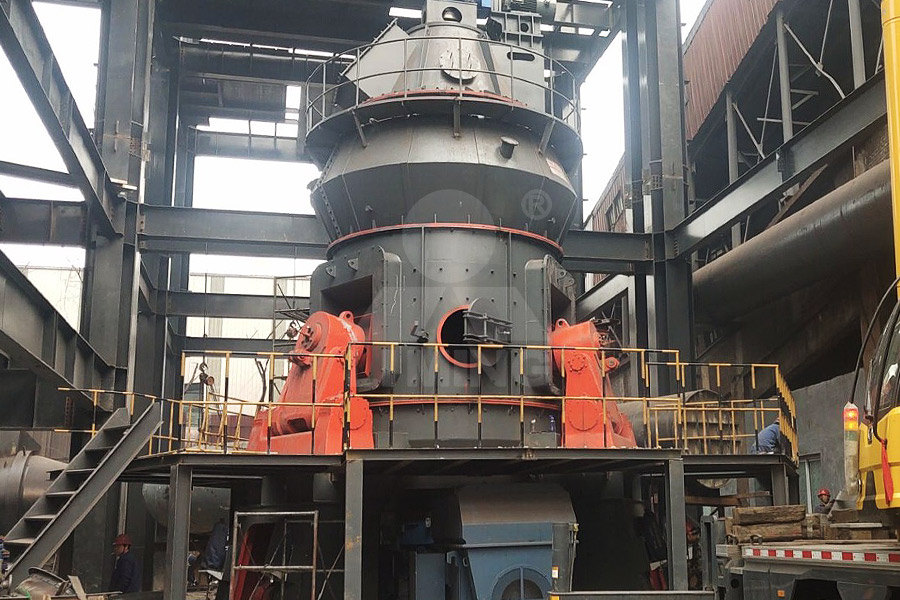
Simulation of the operation of an industrial wet flue gas
2010年12月1日 Gas desulfurization system details and typical operating conditions are summarized in Table 1 Download: Download fullsize image; when the feeding of the system with fresh limestone stops, probably due to inefficient operation of the cyclone sets, the limestone content in the slurry of the feeding tank decreases significantly2021年6月1日 Wet limestone flue gas desulfurisation (WFGD) system is of great significance to prevent atmospheric pollution due to its excellent desulfurization capacity (Wu et al, 2018)The desulfurization process is a typical nonlinear large time delay process and multiobjective optimization control is required for operation (Kiil et al, 1998) Multiobjective economic model predictive control of wet limestone 2020年2月26日 Artificial IntelligenceBased Emission Reduction Strategy for Limestone Forced Oxidation Flue Gas Desulfurization System February 2020 Journal of Energy Resources Technology, Transactions of the Artificial IntelligenceBased Emission Reduction Strategy for Limestone Currently, desulfurization technologies can be categorized into three main types: wet flue gas desulfurization (FGD) [11], [12], [13], semidry desulfurization [14] and dry desulfurization [15]Wet flue gas desulfurization is widely employed in largescale desulfurization processes due to its high efficiency and low energy consumption [16]However, it poses a significant environmental Recent advances in process and materials for dry desulfurization
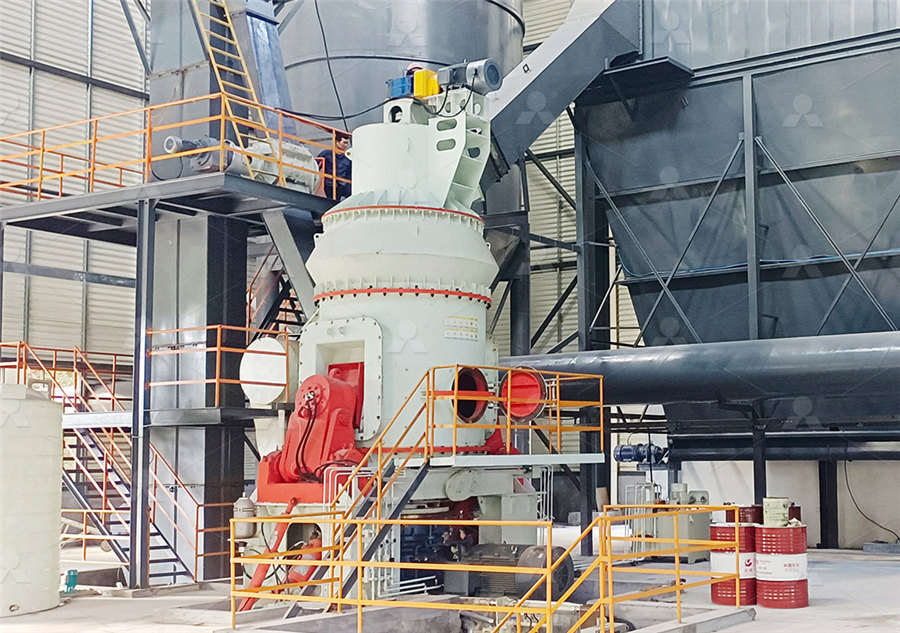
Fine Particle Transformation during the Limestone Gypsum
Special attention is required on the fine particle control after desulfurization because a large quantity of fine particles are emitted into the atmosphere from the coalfired power plants In an attempt to figure out the transformation of fine particles during the limestone gypsum desulfurization, the physical properties of fine particles before and after the desulfurization 2001年5月19日 A detailed process model of the wet limestone flue gas desulfurization system has been presented This model can be used to calculate indispensable parameters for estimating costs and next to minimize capital and operating costs The process model describes most important stage of SO2 removal running in an absorber and a holding tank It includes Model of the Wet Limestone Flue Gas Desulfurization Process maximize the use of lowgrade limestone: gypsum purity=93 wt%, desulfurization efficiency=94%, and total limestone usage=3,710 kg/h MODEL DEVELOPMENT 1 Process Overview Fig 1 shows a workflow chart of the overall WFGD process Initially, the crushed limestone is dissolved in water in the limeModeling of the wet flue gas desulfurization system to utilize low removal with system availability greater than 995% 2 3 a worldwide leader in supplying limestone forced oxidation units, and we continue to support this technology While limestone forced oxidation technology has proven successful in many worldwide installations, in some applications, the gypsum byproduct is no longer marketable,WET FLUE GAS DESULFURIZATION (FGD) SYSTEMS Babcock
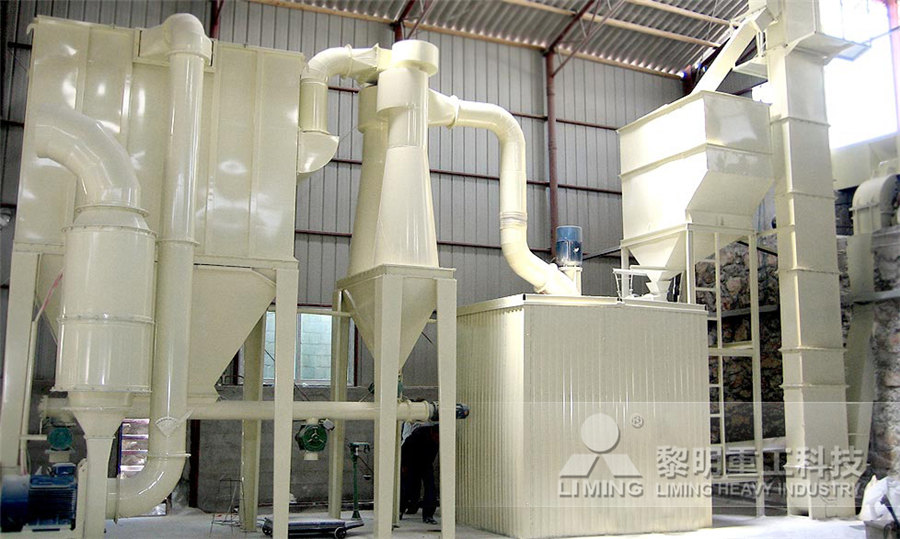
Status of Flue Gas Desulphurisation (FGD) systems from coal
2015年3月15日 It can be stated that wet limestone FGD system is the FGD process most widely used because of its high desulphurisation performance and low United States Environmental Protection Agency (US EPA) Flue gas desulfurization system capabilities for coalfired steam generators Vol II Technical Report EPA600/778032b; March 1978 Comparing Lime and Limestone SO 2 Wet Scrubbing Processes More than ninety percent of US flue gas desulfurization (FGD) system capacity uses lime or limestone This trend will likely continue into the next phase of federally mandated SO 2 Flue Gas Desulfurization Lime2021年2月1日 Finally, the effluent quality of the system is better than the discharge requirements of “Discharge standard of wastewater from limestonegypsum flue gas desulfurization system in fossil fuel LimestoneGypsum Wet Flue Gas Desulfurization Wastewater Treatment2023年3月15日 Numerous researchers have investigated the effects of various buffering additives on the desulfurization of limestone slurries Commercially available buffering additives include organic additives, such as benzoic, adipic, formic, acetic, and citric acids, and inorganic additives, such as sodium, ammonium, and sulfate salts [4], [14], [16]Desulfurization characteristics of limestone slurry with added

Flue Gas Desulfurization (FGD) Plants Mitsubishi Power
Max Capacity 1,050 MW Max Inlet SO 2 Concentration 80,000 mg/Nm 3 (Coal fired) Max SO 2 Removal Efficiency 99% High Reliability The flue gas desulfurization (FGD) plant removes sulfur dioxides (SO 2) from flue gas produced by boilers, furnaces, and other sourcesMitsubishi Power effectively contributes to the prevention of air pollution through its wet limestone Limestoneforced oxidation (LSFO), limestoneinhibited oxidation (LSIO), jet bubbling reactor In a oncethrough system, the spent slurry is dewatered to disposal or used as a byproduct ESP + WFGD, or the ESP + DFGD (dry flue gas desulfurization) + FF system, which generally emitted gas with a higher Hg 2+ proportionFlueGas Desulphurization an overview ScienceDirect Topics2022年6月15日 However, the desulfurization efficiency would be definitely less optimistic for WFGD process when using lowgrade limestone as absorbent in view of its relatively large contents of impurities including CaMg(CO 3) 2, SiO 2, Al 2 O 3 and Fe 2 O 3 [13]As such, possibly effective attempts to upgrade the lowgrade limestone have been actively studied in Enhancement of citric acid on lowgrade limestone wet desulfurization 2021年6月1日 Zhong et al (Zhong et al, 2008) developed a model of limestone/gypsum wet flue gas desulfurization (WFGD) system based on unsteady theory The influences of liquidtogas ratio, SO 2 concentration of inlet flue gas, and combination mode of different spray levels to the desulfurization efficiency were analyzedSimulation of SO2 absorption and performance enhancement of wet flue
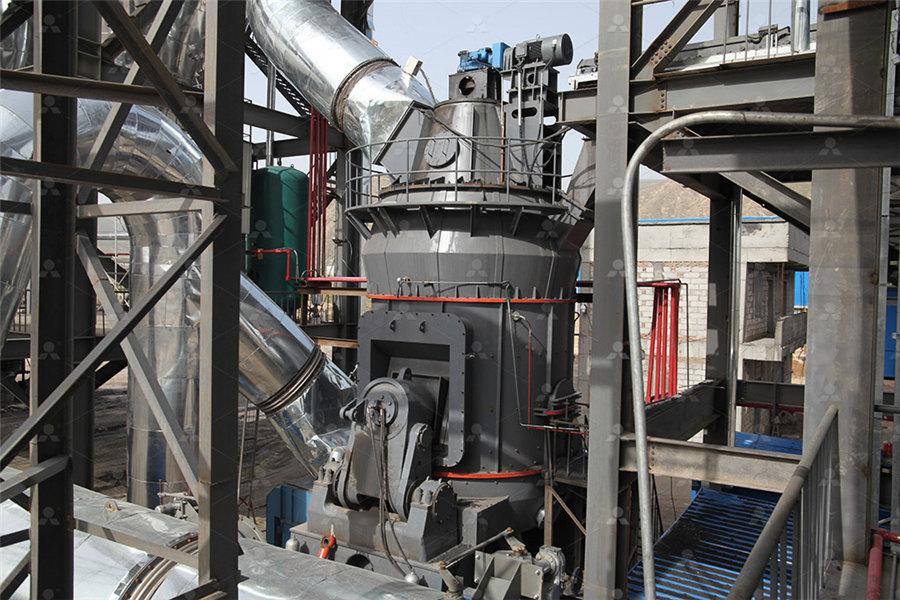
A model for performance optimization of wet flue gas desulfurization
2008年11月1日 In this paper, a model of limestone/gypsum wet flue gas desulfurization (WFGD) system was developed based on unsteady theory The models of processes of absorption section and oxidation section were developed and incorporated into the WFGD integral model