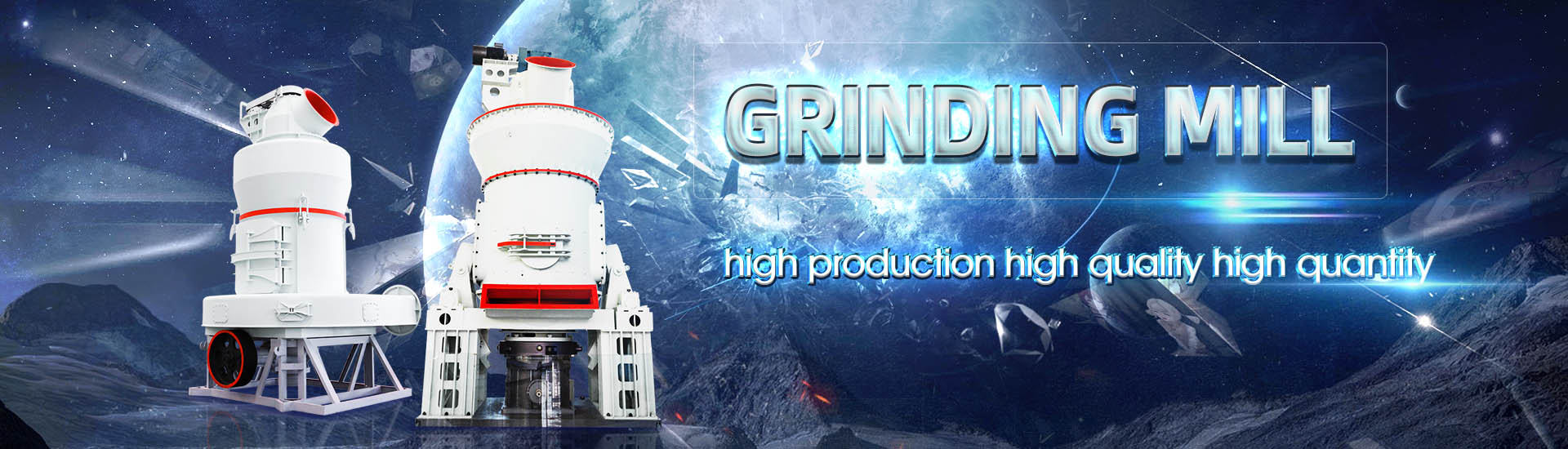
Centrifugal Grinding Mill Principle
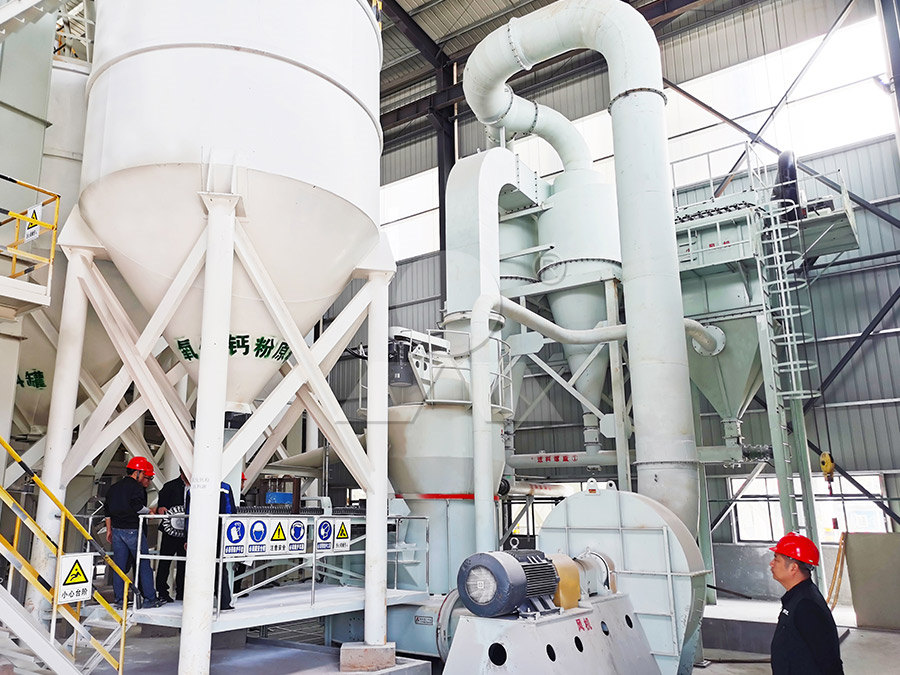
Ultra Centrifugal Mill – Effective Sample Preparation
2024年4月8日 Function Principle of Ultra Centrifugal Mill The working principle of the Ultra Centrifugal Mill is tailored to ensure efficient and precise grinding of samples This instrument achieves a twostage crushing process using the 2022年7月4日 Learn more https://retsch/zm300 The powerful Ultra Centrifugal Mill ZM 300 provides maximum grinding performance combined with ease of use The variable speed from 6,000 to 23,000 rpmUltra Centrifugal Mill ZM 300 Assembly Function The powerful Ultra Centrifugal Mi ll ZM 300 provides maximum grinding performance at high speed while, at the same time, ensuring operator convenience and safety The ZM 300 New Ultra Centrifugal Mill ZM 300 RETSCHFunction Principle In the Ultra Centrifugal Mill ZM 200 size reduction takes place by impact and shearing effects between the rotor and the fixed ring sieve The feed material passes through Ultra Centrifugal Mill ZM 200 ATS Scientific
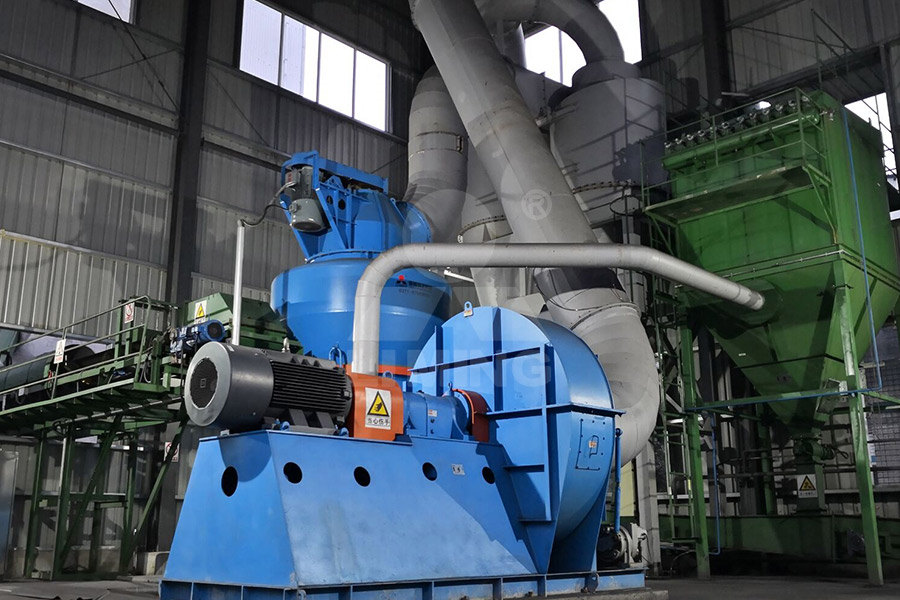
ZM 200 Ultra Centrifugal Mill Glen Mills, Inc
Function Principle In the Ultra Centrifugal Mill ZM 200 size reduction takes place by impact and shearing effects between the rotor and the fixed ring sieve The feed material passes through the hopper (with splashback protection) onto 1988年4月1日 Based on the principle of a highspeed nutating motion of the grinding chamber, grinding rates in the mill are intensified by the action of a mechanicallyinduced rotating Highintensity centrifugal milling — A practical solution2004年12月10日 The centrifugal tube mill is a singletube mill with a grinding tube length of 2200 mm and a diameter of 350 mm, which describes a defined oscillatory circuit of 150 mm at a Centrifugal tube mill for finest grinding ScienceDirectPlanetary ball mills are used for the pulverization of soft, hard, brittle, and fibrous materials in dry and wet mode Extremely high centrifugal forces result in very high pulverization energy and therefore short processing timesPlanetary Ball Mills RETSCH fine grinding of materials
.jpg)
CENTRIFUGAL IMPACT MILLS (PIN MILLS) FloDyn
Munson’s Pin Mill, or “Centrifugal Impact Mill,” reduces bulk materials into narrow particle size ranges without the need for screens, hammers, knives or rolls Instead, it relies on material Rotation of base plate provides the centrifugal force to the grinding balls and independent rotation of shell to make the balls hit the inner wall of the shell The operating principle of the ball mill consists of the following steps In a Ball Mill Principle, Construction, Working, and MoreA centrifugal mill is used for the very fine grinding of a wide range of products Dinnissen centrifugal mills provide a final fineness of 700 to 30 microns and reach depending on the product a capacity of 100 to 11,500 kg per hourCentrifugal Mill Contact us Dinnissen BVULTRA CENTRIFUGAL MILL ZM 300 Rotor mills are used for highspeed size reduction of soft to mediumhard as well as temperaturesensitive or ibrous materials The powerful Ultra Centrifugal Mill ZM 300 provides maximum grinding performance combined with ease of use The variable speed from 6,000 to 23,000 rpm allows for gentle, neutralto ULTRA CENTRIFUGAL MILL ZM 300
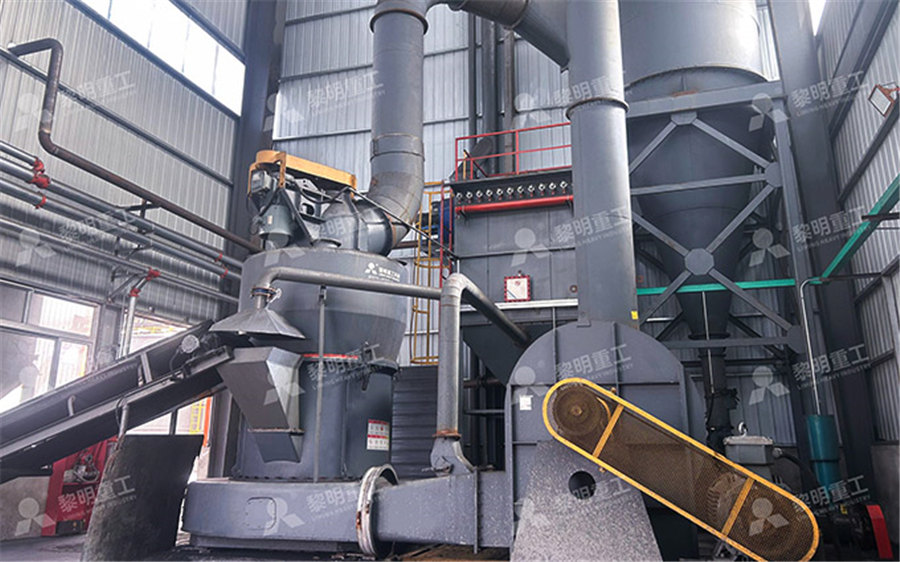
Retsch Ultra Centrifugal Mill ZM 200, 6251,00€
Function Principle In the Ultra Centrifugal Mill ZM 200 size reduction takes place by impact and shearing effects between the rotor and the fixed ring sieve Ultra Centrifugal Mill ZM 200: Applications: fine grinding: Field of application: agriculture, biology, chemistry / plastics, construction materials, 2019年5月22日 The ball mill consists of a metal cylinder and a ball The working principle is that when the cylinder is rotated, the grinding body (ball) and the object to be polished (material) installed in the cylinder are rotated by the cylinder under the action of friction and centrifugal forceThe working principle of ball mill Meetyou CarbideRead this indepth blog to learn about the working principle of Vertical Grinding Mill, its application, and its advantages +91 226796 9655 sales@macawberindia 130131, Hindustan Kohinoor Complex, LBS Road, Vikhroli, Mumbai Home; The centrifugal blower is made of a thick MS plate lined inside with suitable types of liners, Vertical Grinding Mill: How it Works, Application And AdvantagesGrinding Mills Barry A Wills, James A Finch FRSC, FCIM, PEng, in Wills' Mineral Processing Technology (Eighth Edition), 2016 71 Introduction Grinding is the last stage in the comminution process where particles are reduced in size by a combination of impact and abrasion, either dry, or more commonly, in suspension in waterGrinding Mill an overview ScienceDirect Topics
.jpg)
Raymond Grinding Mill: The Ultimate Guide From SMAT Machinery
2023年9月18日 What is the Raymond mill working principle? The Raymond mill’s basic operating principle is as follows: Material is sent by the blade to grind between the grinding roller and the grinding ring while the grinding roller is tightly pressed against the grinding ring by the action of centrifugal forceThe correct sizes are often determined by trial and error, primary grinding usually requiring a graded charge of 105 cm diameter balls, and secondary grinding requiring 52 cm Concha et al (1988) have developed a method to calculate ball mill charge by using a grinding circuit simulator with a model of ball wear in a tumbling millBall Mill an overview ScienceDirect Topics2023年7月4日 The Raymond grinding mill, Raymond mill for short, is a roller mill in which the central spindle drives the multiple grinding rollers installed on the plumblossom rack to swing outwardly under the action of centrifugal force and press the grinding ring on the inner wall of the casing to grind the materialRoller Mill SpringerLink2004年12月1日 Download Citation Centrifugal tube mill for finest grinding The achievable particle size distribution can in principle be influenced by design parameters Centrifugal tube mill for finest grinding ResearchGate
.jpg)
Grinding Mills and Their Types IspatGuru
2015年4月9日 Installing a grinding mill which is suitable for the purpose, The general principle of operation in a fluid energy mill is that the material to be ground is fed into a grinding chamber in a high speed, A centrifugal Working Principle of Pin Mill Pin mills or centrifugal impact mills (CIM) function on the principle of impact and are used for the achievement of fine and ultra (micro) fine particles At slower speeds, they are used for dismantling clusters of particles They work without the use of external knives, hammers, screens or rollsWhat is Pin Mill? Working Principle, Construction, Diagram, 2024年1月8日 For each air classifier, working principles allow them to be used in standalone processes as both a feeding implement and a dust collection system They’re also wellsuited for integration into closedcircuit conventional grinding and milling systems For both types of Prater air classifier, working principles entail:Air Classifier Working Principle PraterRaymond mill or raymond grinder, raymond grinding mill adopts advanced grinding technology to crush and finely grind raw materials into required powder products It is a powder grinding machine widely used in mining, metallurgy, building materials, coal Raymond Mill JXSC Machinery
.jpg)
Industrial Vertical Grinding Mill
Industrial vertical grinding mill is an ideal largescale grinding equipment, integrating crushing, drying, grinding, and which is the same as the classification principle of the centrifugal separator It has high classification accuracy and easy fineness control c The highefficiency combined powder separator combines the dynamic The ZM 200 UltraCentrifugal Grinding Mill rapidly reduces soft to mediumhard and fibrous materials to analytical sample size Grinding takes place by impact and shearing action between the rotor and the fixed ring sleeve Feed material passes through the funnel with splashback protection onto the rotorUltra Centrifugal Mill ZM 200 Thomas Scientific2020年6月15日 Industrial hammer mills are employed in particle reduction applications for processing material Though machine designs vary, the basic hammer mill working principle remains the same—uniform size reduction of Understanding the Working Principle of Hammer Mills The powerful Ultra Centrifugal Mill ZM 300 provides maximum grinding performance combined with ease of use The variable speed from 6,000 to 23,000 rpm allows for gentle, FUNCTIONAL PRINCIPLE In the Ultra Centrifugal Mill ZM 300 size reduction takes place by impact and shearing effects between the rotor and the ixed ring sieveULTRA CENTRIFUGAL MILL ZM 300
.jpg)
How does grinding mill work?working principle of micro powd
The second working principle for grinding mill is our previous working theory of ultrafine grinding mill, but not so detailed: The high pressuredcentrifugal blower will inhale air from outside and blow the materials, which are ground in the third ring, to powder classifierRaymond Mill The Raymond grinding mill, Raymond mill for short, is a roller mill in which the central spindle drives the multiple grinding rollers installed on the plumblossom rack to swing outwardly under the action of centrifugal force and press the grinding ring on the inner wall of the casing to grind the materialRoller Mill Springer2023年10月27日 The critical speed of a ball mill is the speed at which the grinding medium reaches the centrifugal force required to stick to the inner wall of the mill At this speed, the grinding medium will rotate around the mill with the shell, and there will be no grinding action To achieve effective grinding, the ball mill must operate above its Ball Mills working principle advantages Across International2023年4月30日 When the ball mill rotates at a certain speed, the grinding medium such as steel ball (rod) or gravel in the cylinder rises to a certain height with the rotation of the cylinder under the action of its own gravity, the friction between the cylinder liner and the centrifugal force generated by the rotation of the ball millBall Mill SpringerLink
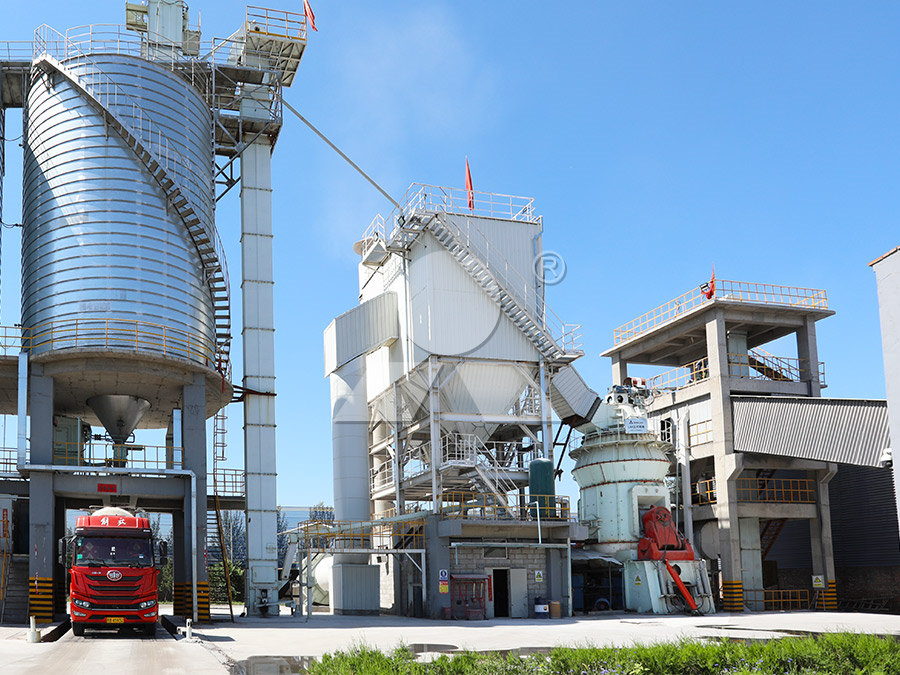
Working principle and application of rod mill Grinding Ball
2021年2月18日 Working principle of rod mill Rod mills run along the outside gear Materials spirally and evenly enter the crushing chamber along the input hollow axis by input devices Steel rods of different specifications are installed in the crushing chamber When the frame rotates, centrifugal force is producedUltra Centrifugal Mill FM200 applies to a wide range of samples Based on its high efficiency grinding technology and rich accessories, with twosteps grinding of rotating knife – ring screen system ,it can process dry and wet grinding in a very short time for Ultra Centrifugal Mill FM200 Beijing Grinder Instrument Co,LtdRotation of base plate provides the centrifugal force to the grinding balls and independent rotation of shell to make the balls hit the inner wall of the shell The operating principle of the ball mill consists of the following steps In a Ball Mill Principle, Construction, Working, and MoreA centrifugal mill is used for the very fine grinding of a wide range of products Dinnissen centrifugal mills provide a final fineness of 700 to 30 microns and reach depending on the product a capacity of 100 to 11,500 kg per hourCentrifugal Mill Contact us Dinnissen BV
.jpg)
ULTRA CENTRIFUGAL MILL ZM 300
ULTRA CENTRIFUGAL MILL ZM 300 Rotor mills are used for highspeed size reduction of soft to mediumhard as well as temperaturesensitive or ibrous materials The powerful Ultra Centrifugal Mill ZM 300 provides maximum grinding performance combined with ease of use The variable speed from 6,000 to 23,000 rpm allows for gentle, neutralto Function Principle In the Ultra Centrifugal Mill ZM 200 size reduction takes place by impact and shearing effects between the rotor and the fixed ring sieve Ultra Centrifugal Mill ZM 200: Applications: fine grinding: Field of application: agriculture, biology, chemistry / plastics, construction materials, Retsch Ultra Centrifugal Mill ZM 200, 6251,00€2019年5月22日 The ball mill consists of a metal cylinder and a ball The working principle is that when the cylinder is rotated, the grinding body (ball) and the object to be polished (material) installed in the cylinder are rotated by the cylinder under the action of friction and centrifugal forceThe working principle of ball mill Meetyou CarbideRead this indepth blog to learn about the working principle of Vertical Grinding Mill, its application, and its advantages +91 226796 9655 sales@macawberindia 130131, Hindustan Kohinoor Complex, LBS Road, Vikhroli, Mumbai Home; The centrifugal blower is made of a thick MS plate lined inside with suitable types of liners, Vertical Grinding Mill: How it Works, Application And Advantages
.jpg)
Grinding Mill an overview ScienceDirect Topics
Grinding Mills Barry A Wills, James A Finch FRSC, FCIM, PEng, in Wills' Mineral Processing Technology (Eighth Edition), 2016 71 Introduction Grinding is the last stage in the comminution process where particles are reduced in size by a combination of impact and abrasion, either dry, or more commonly, in suspension in water2023年9月18日 What is the Raymond mill working principle? The Raymond mill’s basic operating principle is as follows: Material is sent by the blade to grind between the grinding roller and the grinding ring while the grinding roller is tightly pressed against the grinding ring by the action of centrifugal forceRaymond Grinding Mill: The Ultimate Guide From SMAT MachineryThe correct sizes are often determined by trial and error, primary grinding usually requiring a graded charge of 105 cm diameter balls, and secondary grinding requiring 52 cm Concha et al (1988) have developed a method to calculate ball mill charge by using a grinding circuit simulator with a model of ball wear in a tumbling millBall Mill an overview ScienceDirect Topics