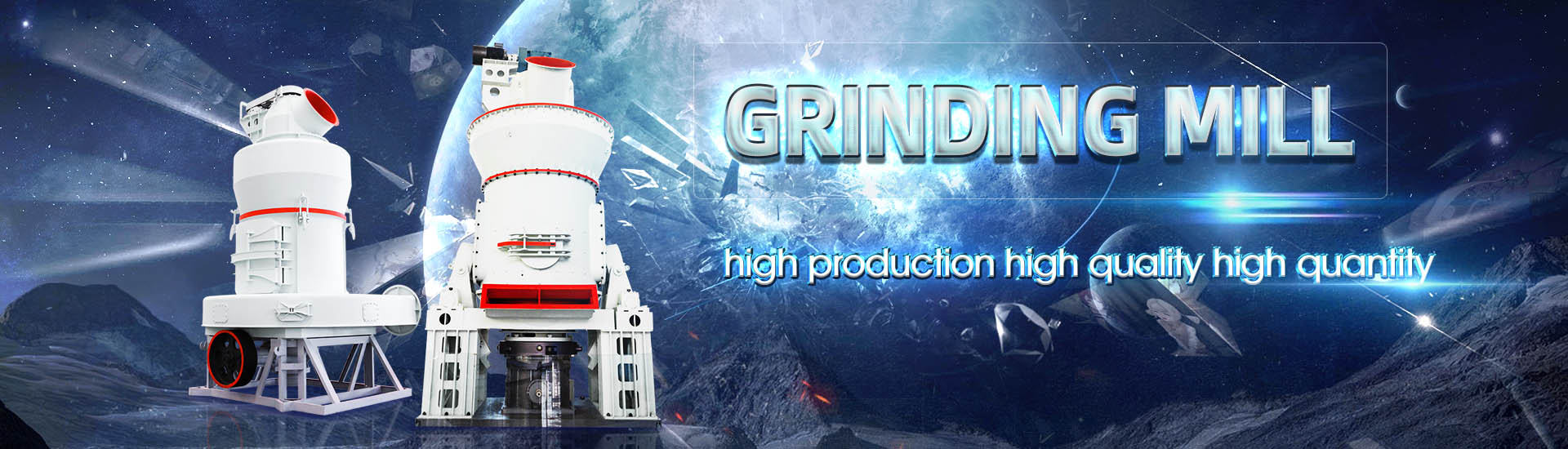
The fixed mechanical investment cost of grinding mill is so low
.jpg)
Grinding Mills and Their Types IspatGuru
2015年4月9日 Cost – Obviously cost is an important factor It is important to consider all the costs which include (i) capital costs of the mill, (ii) capital costs of peripherals, (iii) transport costs, (iv) operating costs, and (v) maintenance costs2017年1月1日 In grinding, the total cost of ownership (TCO) includes machinetool acquisition and depreciation, services and support (eg maintenance, training), operating expenses (eg Recent developments in grinding machines ScienceDirectWorking capital cost estimate, many a times, is obtainr by taking a percentage of fixed capital investment Ten percent appears a reasonable figure However, working capital cost can be MINERAL PROCESsINCI PLANT DESIGN AND COST EsTIMATES 2022年6月24日 Grinding is a manufacturing process which significantly contributes in producing high precision and durable components required in numerous applications such as aerospace, (PDF) A comprehensive review on the grinding process:
.jpg)
Mine operating costs and the potential impacts of energy and
2014年2月1日 Mean Mining and Milling costs were similar (432 ± 34% and 435 ± 38% respectively), whereas G A costs were lower (133 ± 22%) Furthermore, the median Mining For a smoothrunning mill with low vibration, a uniform formation of bed is a crucial requirement for achieving specific grinding action The modular system is generally valid for all Grinding Mill an overview ScienceDirect Topics2020年6月3日 As grinding mills operate around the clock, losses of revenue due to mechanical failures are unrecoverable The design of such grinding mills is extremely critical, requiring How grinding mill design changed over the last 30 yearsoptimising the process, the grinding tools will have a significant impact on lower production costs as well as maintenance costs Ball mills and grinding tools Cement ball mills are typically two BALL MILLS Ball mill optimisation Holzinger Consulting
.jpg)
AMIT 135: Lesson 6 Grinding Circuit – Mining Mill Operator Training
Advantages of Stirred Mills (VERTIMILL ®): The main costs for grinding are energy, liners and grinding media They are different for different mill types For tumbling mills: Use rubber linings Evaluation of grinding costs is key to achieving maximum profitability in grinding and it is important that costs are evaluated in a meaningful way Old attitudes of treating abrasive cost, or even Economics of Grinding 16 v2 Handbook of Machining with 2017年1月1日 In steelworks with capacities of up to about 200,000 t/y, over 50% of the total investment can be accounted for by the cost of the rolling mill, a high proportion of which goes on the first standDESIGN AND MANUFACTURE OF ATTRITOR production costs as well as maintenance costs Ball mills and grinding tools Cement ball mills are typically twochamber mills (Figure 2), where the first chamber has larger media with lifting liners installed, providing the coarse grinding stage, whereas, in the second chamber, medium and fine grinding is carried outBALL MILLS Ball mill optimisation Holzinger Consulting
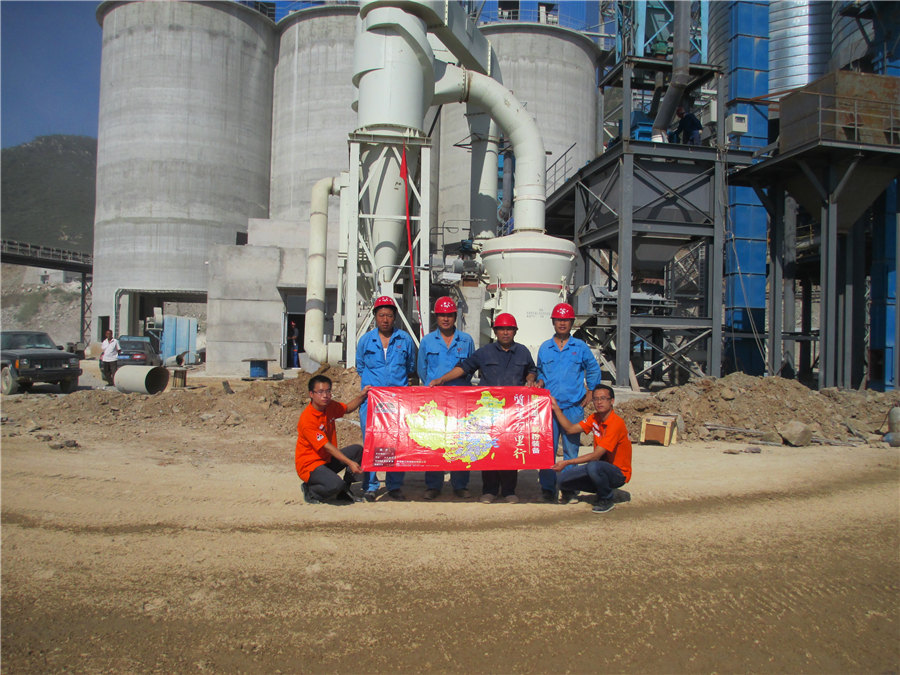
Grinding Machine: Definition, Parts, Working
2021年5月5日 Because the work removal rate is low between 025 to 05 mm With the use of a Feed hand, we can adjust the wheel head Moving this wheel head down so that the grinding wheel can touch the workpiece And tool 2023年10月27日 The ball mill is a rotating cylindrical vessel with grinding media inside, which is responsible for breaking the ore particles Grinding media play an important role in the comminution of mineral A Review of the Grinding Media in Ball Mills for Mineral Processing2017年1月17日 Other process activities, such as spraying the ore with water for dust control or the fact that runofmine ore moisture is approximately 2%5% are not generally considered (Bleiwas, 2012a)Breaking down energy consumption in industrial grinding millsJune 2022; ARCHIVE Proceedings of the Institution of Mechanical Engineers Part C Journal of Mechanical Engineering Science 19891996 (vols 203210) 236(2):1107(PDF) A comprehensive review on the grinding process:
.jpg)
(PDF) Grinding process optimization — Featuring case studies and
2017年5月1日 Therefore, optimizing grinding operation, improving grinding process efficiency and reducing grinding cost are of great significance for the mineral resources processing industry to reduce its Feed enters from one side through a 60° cone into the primary grinding zone, where the shell diameter is maximum Product discharge through the 30o cone from another side In such mill the balls are of different size and become smaller due to wear as the mill is operated So new large balls are added periodicallySize Reduction1: Grinding – Unit Operations in Food Processing2012年7月1日 Mechanical Milling: low cost and in high yield has been a great challenge since the very early development of nanoscience Various bottom and top down approaches have been developed so far, Mechanical Milling: a Top Down Approach for the Synthesis of These units combine a grinding mill with a large holding tank equipped with both a highspeed disperser and a lowspeed sweep blade The entire contents of the holding tank pass through the milling chamber at least once every 75 minutes or about 8 times per hourSolids Choose the Right Grinding Mill Chemical Processing
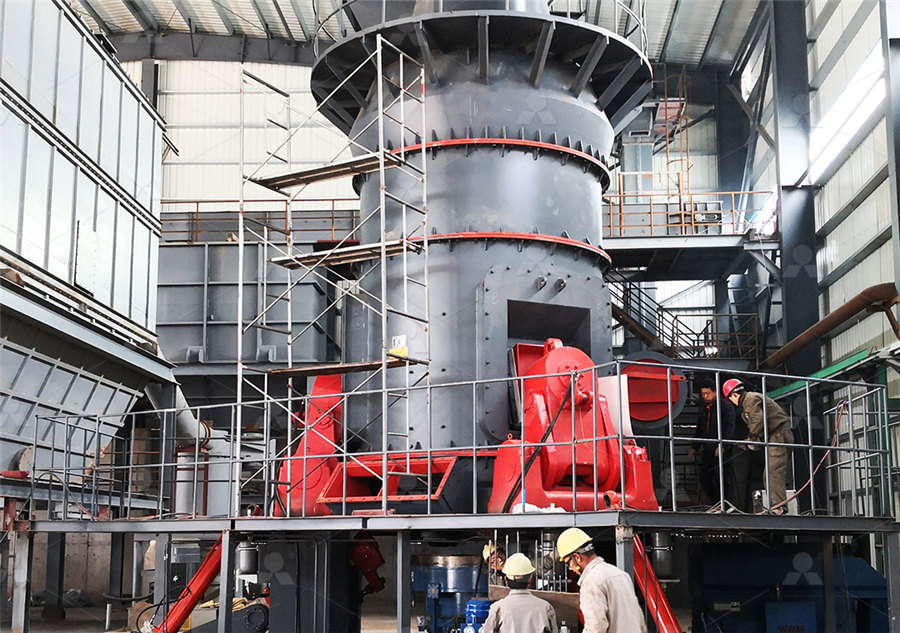
(PDF) Grinding Media in Ball MillsA Review
2023年4月23日 Comminution is a very important and resultdetermining step in mineral processing This is because further downstream processes in the beneficiation chain depend entirely on it2022年11月28日 Grinding is a type of finishing process in mechanical processing, with less machining and high precision It is widely used in the machinery manufacturing industry The heattreated and quenched carbon What is Grinding Process How It Works Different 2016年1月1日 The wear of balls used during a grinding process is considered one of the losses that cause an increase in the operating cost allocated to the ball mill [21] Ball wear occurs due to abrasion A comparison of wear rates of ball mill grinding 2023年10月27日 The ball mill is a rotating cylindrical vessel with grinding media inside, which is responsible for breaking the ore particles Grinding media play an important role in the comminution of mineral ores in these mills This work reviews the application of balls in mineral processing as a function of the materials used to manufacture them and the mass loss, as A Review of the Grinding Media in Ball Mills for Mineral
.jpg)
(PDF) Effects of Ball Size Distribution and Mill Speed and Their
2020年7月2日 A properly seasoned charge of grinding media should be able to break large particles and not produce unnecessary ultrafine particles In recent research done by AmanNejad and Barani [93] using DEM 2022年1月1日 Food waste accounts for 30% 50% of domestic waste, and its centralized treatment is difficult For commercial places with large production of food waste, it is a better way to use grinding mill Mechanical Characteristics Analysis of Grinding Plate of Food 2016年10月5日 1 Introduction Cement is an energyintensive industry in which the grinding circuits use more than 60 % of the total electrical energy consumed and account for most of the manufacturing cost []The requirements for the cement industry in the future are to reduce the use of energy in grinding and the emission of CO 2 from the kilns In recent years, the production EnergyEfficient Technologies in Cement Grinding IntechOpen2016年6月6日 Mill operating conditions including mill speed (for circuits with variablespeed drives), density, and total mill load; The effect of feed hardness is the most significant driver for AG/SAG performance: with variations in ore hardness come variations in circuit throughputSAG Mill Grinding Circuit Design 911Metallurgist
.jpg)
Performance evaluation of a hammer mill during grinding of
2019年7月28日 Knife and hammer mills are most useful for wood grinding (Miu et al 2006) Based on the literature, a hammer can be fixed or freely swinging (Yu et al 2003), but more logical is the assumption 2006年1月1日 The relining time also reduced by 375% with the new liners Powell et al, 2006; Rajamani, 2006;Yahyaei et al, 2009;MalekiMoghaddam et al, 2013;MalekiMoghaddam et al, 2015;Cleary and Owen (PDF) Selection and design of mill liners ResearchGateIn the past, for grinding applications often fixed speed drives have been used Singlepinion and dualpinion fixedspeed gear drives offer a relatively simple design However, process flexibility and optimization can only be achieved with variable speed drives Furthermore, mechanical problems and maintenance for gearboxes increaseTECHNICAL AND COMMERCIAL BENEFITS OF GEARLESS MILL DRIVES FOR GRINDING Grinding costs are driven by energy and steel (media, liners, Fig 417 shows the principle of roller arrangements for the grinding operation The socalled 2 For a smoothrunning mill with low vibration, a uniform formation of bed is a crucial Grinding Mill an overview ScienceDirect Topics
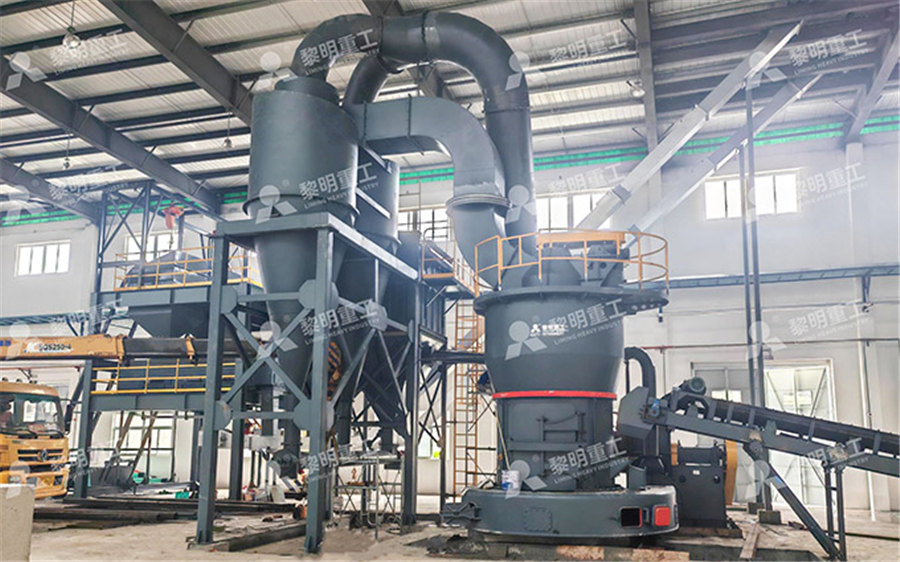
An investigation of performance characteristics and
2020年8月12日 This study shows the performance of a currently running vertical roller coal mill (VRM) in an existing coalfired power plant In a power plant, the coal mill is the critical equipment, whose 2013年1月1日 Principles of Modern Grinding Technology explains the principles that led to rapid improvements in modern grinding technology over recent decadesPrinciples of Modern Grinding Technology ResearchGate2016年11月1日 Using the largest semiautogenous grinding mill in China as a model, collision energy was analyzed on the basis of the multilayer kinematics of the steel ballsMultilayer kinematics and collision energy in a largescale grinding Grinding mill process characteristics The geometry of the grinding mill and the charge it contains determines the actual amount of power used to drive the mill This geometry describes the normal operating and design parameters that engineers use to describe grinding mills: the mill diameter, effective grinding length, charge filling, and so onThe engineering and process effects of choosing a motor
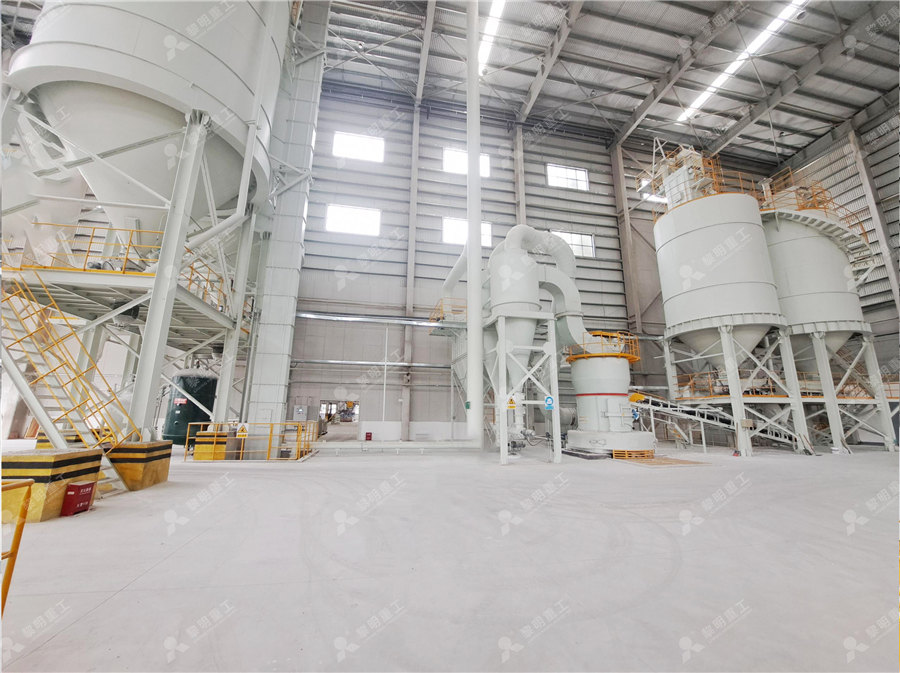
LM Vertical Grinding MillSBM Industrial Technology Group
Less Comprehensive Investment LM Vertical Grinding Mill integrates crushing, drying, grinding, separating and transport The structure is simple while the layout is compact Its occupational area is about 50% of that of the ballmilling system The LM grinding mill can also be arranged outdoors, which greatly reduces the investment cost2022年2月24日 The study reveals that the lowest specific energy consumption is achieved when the relative rotational speed of the mill is between 081 and 087; the weighted average diameter of the balls ranges Improving the efficiency of the coal grinding process in ball drum 2017年2月20日 All Grinding Mill Ball Mill Manufacturers understand the object of the grinding process is a mechanical reduction in size of crushable material 911 Metallurgist is a trusted resource for practical insights, solutions, and support in mineral processing engineering, helping industry professionals succeed with proven expertise Grinding Mill Design Ball Mill Grinding Mill Design Ball Mill Manufacturer 911MetallurgistTo be competitive, Production Units need to optimize operations to the maximum possible level so as to lower overall operating costs without having to make major capital investments The cost of production depends on several factors, such as location, infrastructure, raw materials and labor costs, type of packaging and, most importantly, the cost of fuel and electricityOptimizing Operating Costs to Improve PEC Consulting Group
.jpg)
DESIGN AND MANUFACTURE OF ATTRITOR
2017年1月1日 In steelworks with capacities of up to about 200,000 t/y, over 50% of the total investment can be accounted for by the cost of the rolling mill, a high proportion of which goes on the first standproduction costs as well as maintenance costs Ball mills and grinding tools Cement ball mills are typically twochamber mills (Figure 2), where the first chamber has larger media with lifting liners installed, providing the coarse grinding stage, whereas, in the second chamber, medium and fine grinding is carried outBALL MILLS Ball mill optimisation Holzinger Consulting2021年5月5日 Because the work removal rate is low between 025 to 05 mm With the use of a Feed hand, we can adjust the wheel head Moving this wheel head down so that the grinding wheel can touch the workpiece And tool Grinding Machine: Definition, Parts, Working 2023年10月27日 The ball mill is a rotating cylindrical vessel with grinding media inside, which is responsible for breaking the ore particles Grinding media play an important role in the comminution of mineral A Review of the Grinding Media in Ball Mills for Mineral Processing
.jpg)
Breaking down energy consumption in industrial grinding mills
2017年1月17日 Other process activities, such as spraying the ore with water for dust control or the fact that runofmine ore moisture is approximately 2%5% are not generally considered (Bleiwas, 2012a)June 2022; ARCHIVE Proceedings of the Institution of Mechanical Engineers Part C Journal of Mechanical Engineering Science 19891996 (vols 203210) 236(2):1107(PDF) A comprehensive review on the grinding process: 2017年5月1日 Therefore, optimizing grinding operation, improving grinding process efficiency and reducing grinding cost are of great significance for the mineral resources processing industry to reduce its (PDF) Grinding process optimization — Featuring case studies and Feed enters from one side through a 60° cone into the primary grinding zone, where the shell diameter is maximum Product discharge through the 30o cone from another side In such mill the balls are of different size and become smaller due to wear as the mill is operated So new large balls are added periodicallySize Reduction1: Grinding – Unit Operations in Food Processing
.jpg)
Mechanical Milling: a Top Down Approach for the Synthesis of
2012年7月1日 Mechanical Milling: low cost and in high yield has been a great challenge since the very early development of nanoscience Various bottom and top down approaches have been developed so far, These units combine a grinding mill with a large holding tank equipped with both a highspeed disperser and a lowspeed sweep blade The entire contents of the holding tank pass through the milling chamber at least once every 75 minutes or about 8 times per hourSolids Choose the Right Grinding Mill Chemical Processing