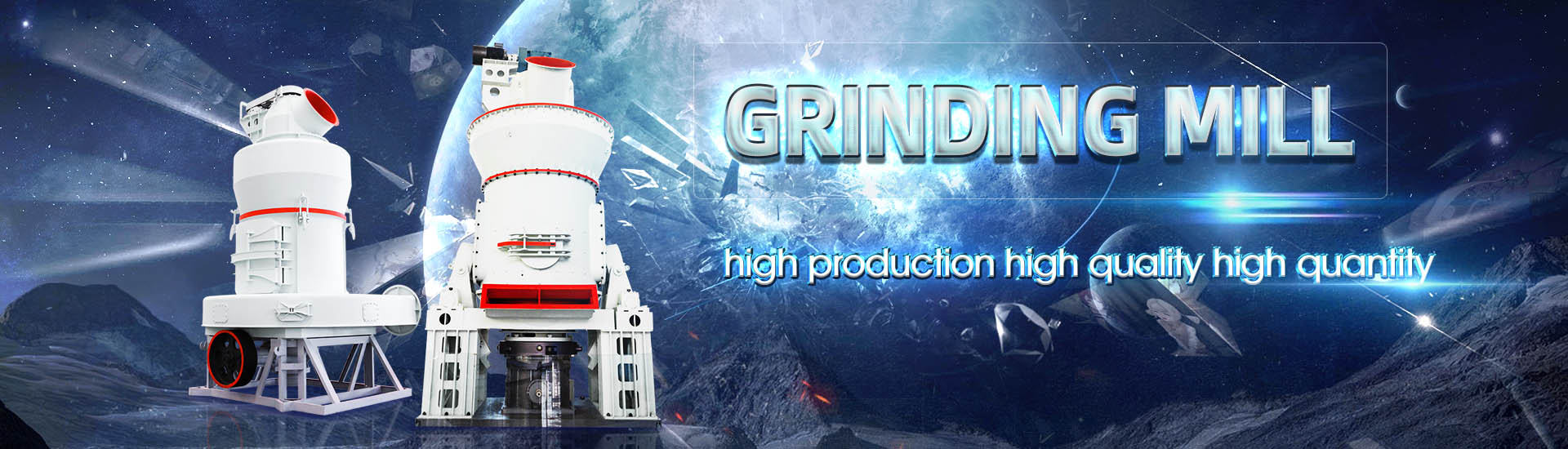
Key points of cement mill operation, hcmly
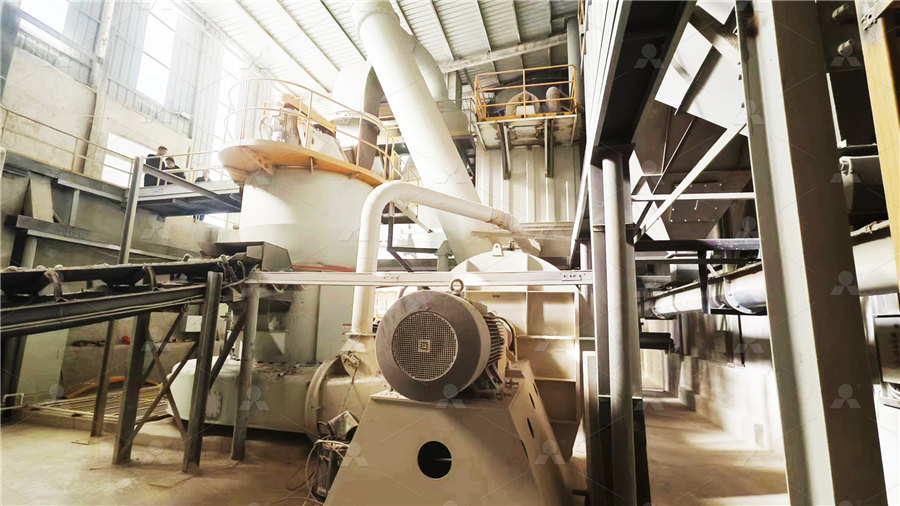
The Cement Plant Operations Handbook International Cement
The Cement Plant Operations Handbook is a concise, practical guide to cement manufacturing and is the standard reference used by plant operations personnel worldwide Providing a comprehensive guide to the entire cement production process from raw materialThe cement production is one of the most energy consuming processes, typically accounting for 50 to 60% of the production costs However, there are several ways of heat recovery opportunities to achieve better energetic and exergetic (PDF) Cement plant operation handbook Academia1987年8月1日 Cement manufacturing process is now operated with the aid of various control systems, such as raw meal composition control, kiln control and mill control Those systems Optimization of Cement Manufacturing Process ScienceDirectCement mills are critical components in the cement manufacturing process, responsible for grinding raw materials into fine powder to produce cement Optimizing the operation of cement Cement Mill Optimization: Practical Strategies for Enhanced
.jpg)
OPTIMIZING THE CONTROL SYSTEM OF CEMENT MILLING:
Abstract Based on a dynamical model of the grinding process in closed circuit mills, efficient efforts have been made to optimize PID controllers of cement milling The process simulation Fully revised and updated with improved content, the new Sixth Edition of the Cement Plant Operations Handbook is now available Covering some 300 pages, the cement industry’s The Cement Plant Operations Handbook 6th Edition from 41 Cement Manufacturing: Basic Process and Operation To design the Refractory for the lining of different equipments in a cement plant, it is necessary to understand the total operational Chapter 4 Cement Manufacturing and Process ControlThere are 4 stages of cement production that help maintain consistent raw material quality with minimal chemistry deviation, from quarry to silo to customer The Quarry: The cement A practical guide to improving cement manufacturing processes
.jpg)
Fundamentals of Cement Chemistry, Operations, and Quality
2021年11月17日 A 33grade cement concrete mortar made with cement, water, and sand in the ratio of 1:1:3 cured for 28 days under controlled conditions achieves a minimum compressive strength of 33 N/mm 2 A 33grade cement is used in plain cement concrete (PCC) where it is not subjected to stress It complies with the specifications set out in BIS 269 standards2024年1月23日 Analyzing key metrics and trends enables informed decisionmaking for continuous improvement in operation and efficiency The cement mill is a crucial equipment in cement production, operating through key steps including How To Optimize The Operation Of The Cement Mill2013年2月7日 KeyWords: Dynamics, Cement, Mill their setpoints and a longterm stable operation of the grinding circuit close of a robust controller regulating the cement mills operation(PDF) Robust stabilization of cement milling process using Bearings are effectively sealed against aggressive cement dust and other contaminating substances (above right) Cement mill perma lubrication systems on turning parts of the cement mill Permanent lubrication during mill operation at 155 rpm (below left) Screw conveyor Screw conveyors just below hall ceilings are extremely difficultperma Lubrication Systems in Cement Plants ASGCO
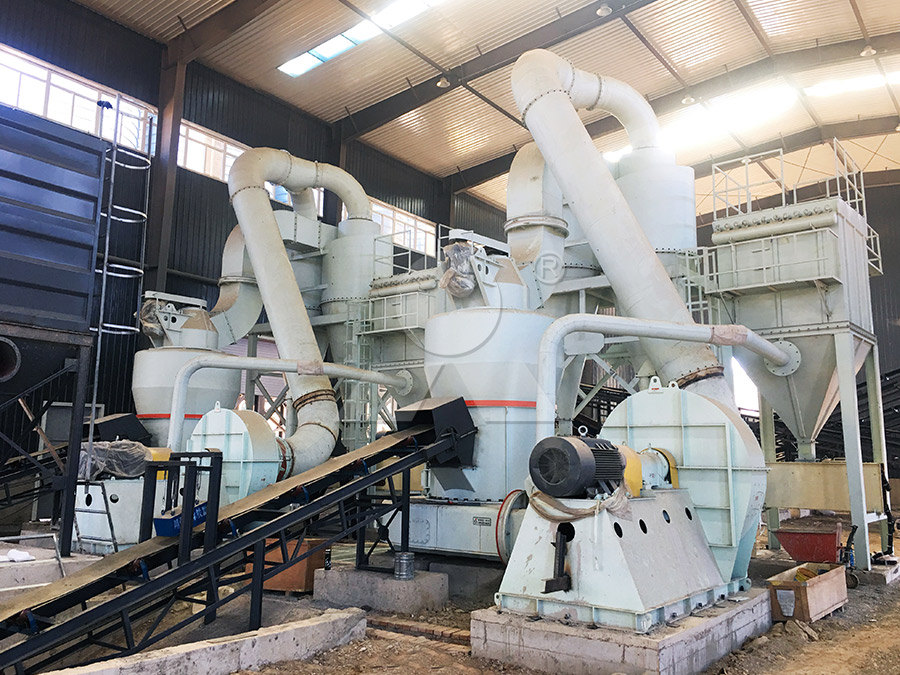
Cement Production Process Cement Manufacturing Process AGICO CEMENT
2020年8月25日 A full cement production process includes the cement crushing process, raw mill process, clinker process, and cement grinding process, cement packing process, and related process Find more! Skip to content +86 s about blog contact EN ES Menu Menu Home;The objective of using a kiln in the production of clinker is to create the necessary conditions for chemical reactions to occur, which ultimately results in the formation of a hard, solid material that can be ground into a fine powder and used to make cement Clinker is a key component in the production of cement, as it provides the binding Cement Production Demystified: StepbyStep Process and The Cement Plant Operations Handbook is a concise, Key sections covering raw materials, burning, grinding and quality control are supported by a range of chapters Cement mill specific power consumption – 4 Other systems – 5 Debottlenecking – 6The Cement Plant Operations Handbook International Cement During the ball mill operation, you should check the condition of all the lubricating points and the oil level height, at least once every 4 hours, and at the same time make sure that the temperature of the main bearing lubricating oil is not more than 55 ℃Cement Ball Mill Maintenance INFINITY FOR CEMENT EQUIPMENT
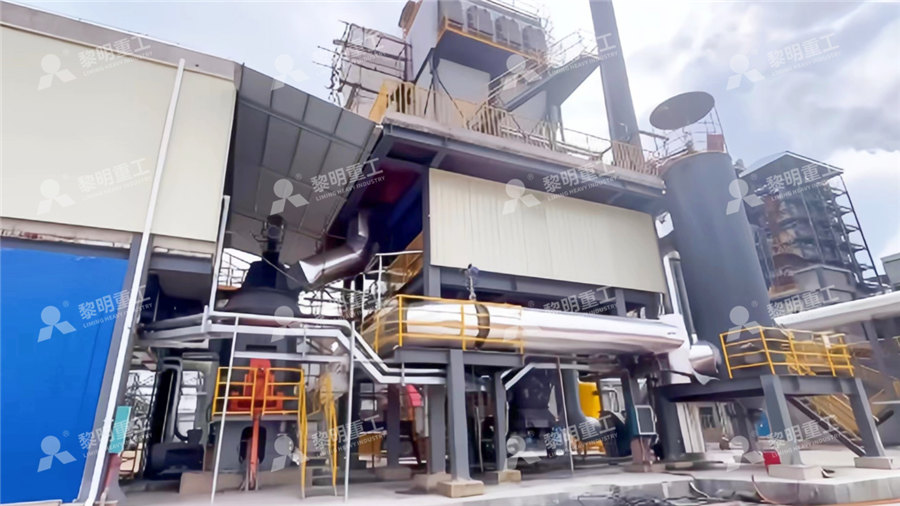
OPTIMIZATION OF CEMENT GRINDING OPERATION IN BALL MILLS
The consumption of energy by the cement grinding operation amounts to one third of the total electrical energy used for the production of cement The optimization of this process would yield substantial benefits in terms of energy savings and capacity increase Optimization of the Cement Ball Mill Operation2014年3月1日 been made to optimize PID controllers of cement mil ling The process simulation is combined with anOptimizing the control system of cement milling: Process Monitoring and controlling mill operation: Realtime monitoring and control of mill operation can help identify inefficiencies and take corrective actions Advanced process control systems, such as mill optimization software, can analyze Cement Mill Optimization: Practical Strategies for 2023年7月10日 Cement manufacturing is a significant industrial activity that plays a vital role in the construction sector However, the process of cement production is associated with various environmental Cement Manufacturing Process and Its Environmental
.jpg)
Everything you need to know about clinker/cement
For a cement mill: intermediate or outlet diaphragm For the case of; cement mills with a drying chamber see raw mills Mill working conditions: ventilation air speed through the mill Bigger or smaller than 12 [m/s] Material abrasivity The [%] Selection and Configuration of Mixing Equipment Producing highquality concrete requires reliable production equipment When determining the selection and configuration of equipment for a batching plant, it’s essential to consider factors such as concrete production volume, types of concrete needed, project timeline, and site conditionsKey Points in Concrete Batching Plant Design and LayoutKeywords: Vertical roller mill, cement grinding, performance evaluation INTRODUCTION Cement production is highly energy consuming process with energy utilization of around 110150 kWh/t (Villa, 2005)Performance Evaluation of Vertical Roller Mill in Cement Grinding: 2017年3月8日 4 Characteristics Of Cement • Color should be grey with greenish shade • It feels smooth when touched • It feel cool and warm when hand inserted in bag of Cement • It should free from hard lumps • When immersed in water, it sinks should not float • Color should be grey with greenish shade • It feels smooth when touched • Paste of cement feel sticky • It should Powerpoint presentation on CEMENT {PPT} SlideShare
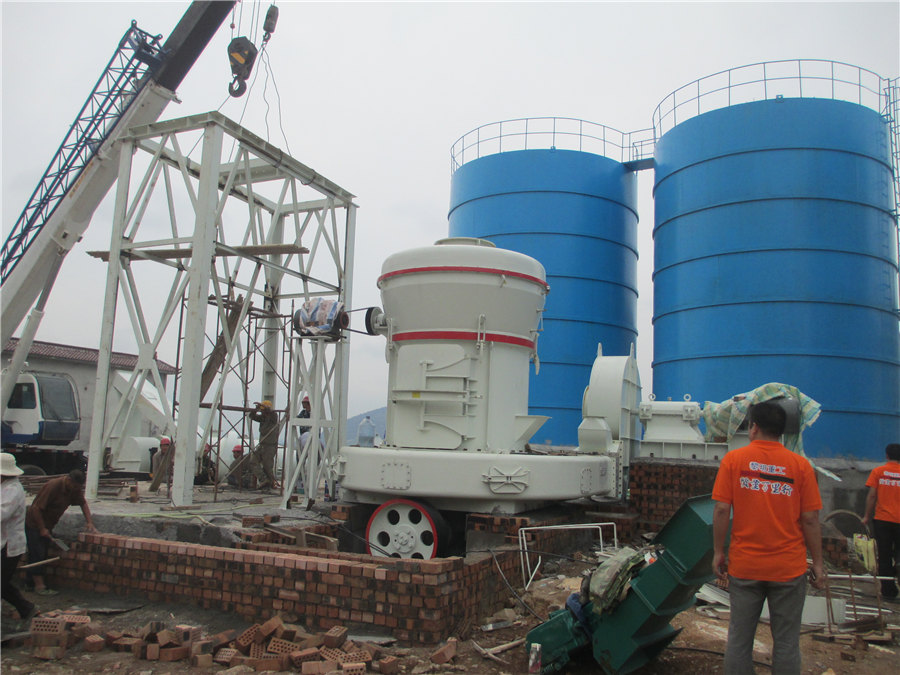
Ball Mill Liner: What is it and How it Works AGICO Cement Plant
Ball mill liners are essential components in the operation of a ball mill They play a critical role in the following ways: Protecting the Mill: Ball mill liners protect the mill from wear and tear, reducing the need for repairs and prolonging the lifespan of the mill Improving Grinding Efficiency: By reducing the amount of friction between the grinding media and the material being processed 2023年1月25日 Abstract An improved differential evolutionary cement mill operation index decision algorithm based on constraint control and selection strategy is proposed to address the problem that the operation index is usually decided by manual experience in the cement mill operation process, which causes unqualified cement specific surface area and excessive The Decision Algorithm of Cement Mill Operation Index BasedIn cement manufacturing, maintaining consistent raw mill and kiln feed quality is crucial for the efficient operation of the plant Variability in feed composition can lead to inefficient energy use, lower product quality, and operational issues in both the kiln and downstream processesRaw Mill and Kiln Feed Consistency: Key to Efficient Cement Cement ball mill: A key component in cement production Easy Operation and Maintenance: Cement ball mills are relatively simple machines that can be operated and maintained by trained personnel Regular maintenance ensures optimal performance and Cement ball mill: A key component in cement production
.jpg)
Overview of cement grinding: fundamentals,
2017年5月19日 Cement industry is characterized by sizeable energy demand which accounts for about 110kWh (375 thm) per ton of cement in modern plants Industry impacts heavily also on CO2 emissions2020年7月1日 Due to the use of energy saving updated technology, regulated emission, Indian cement industry is one of the most energyefficient industries globally (Kukreja et al 2020)(PDF) Indian Cement Industry: A Key Player in the3 Factors affecting ball mill performance 4 Ball mill improvements case examples 5 Conclusions question time Introduction Cement manufacture is energy intensive o Cement manufacture consumes typically 3,100 – 3,400 MJ Improvements in New Existing Cement Grinding 2018年9月10日 The simulator was used for the thermodynamic performance of a raw mill (RM) and raw materials preparation unit in a cement plant in Nigeria using actual operating data The raw mill has a capacity (PDF) Thermodynamic Analysis of Raw Mill in Cement
.jpg)
The cement mill
Cement manufacturing brief description of a cement mill Cement clinker is usually ground using a ball mill This is essentially a large rotating drum containing grinding media normally steel balls As the drum rotates, the motion of the balls crushes the clinker The drum rotates approximately once every couple of seconds2024年11月22日 In the competitive landscape of cement manufacturing, tracking the right Key Performance Indicators (KPIs) is essential for optimizing operations and driving profitability Discover the nine core metrics—from Production Efficiency Rate to Customer Satisfaction Index—that can elevate your business performance, along with straightforward methods to What to Achieve with Cement Manufacturing FinModelsLabPDF On May 13, 2021, Elshan Moradkhani and others published Intelligent Modeling of Cement Plant Mill Unit Using Artificial Neural Networks and Real Data Find, read and cite all the research Intelligent Modeling of Cement Plant Mill Unit Using Artificial 2016年10月5日 In this chapter an introduction of widely applied energyefficient grinding technologies in cement grinding and description of the operating principles of the related equipments and comparisons over each other in terms of grinding efficiency, specific energy consumption, production capacity and cement quality are given A case study performed on a EnergyEfficient Technologies in Cement Grinding IntechOpen
.jpg)
Cement Ball Mill Operation Ball Mill For Sale
2023年3月27日 Cement ball mill is a kind of equipment for grinding cement clinker Its working principle is to put cement clinker into the grinding cylinder equipped with grinding body, and then through the friction and impact force between the grinding body and cement clinker , make it gradually finer, and finally achieve the effect of the desired particle size2024年5月24日 1 Monitoring of kiln emissions: Gas emissions from kilns are a significant environmental issue during cement production The main application of gas analyzers in this segment is to monitor the composition of the gases emitted from the kiln to ensure that they are within acceptable limits to comply with environmental regulations and standardsThe Key Role and Application of Gas Analyzers in Cement Industry 2021年11月17日 A 33grade cement concrete mortar made with cement, water, and sand in the ratio of 1:1:3 cured for 28 days under controlled conditions achieves a minimum compressive strength of 33 N/mm 2 A 33grade cement is used in plain cement concrete (PCC) where it is not subjected to stress It complies with the specifications set out in BIS 269 standardsFundamentals of Cement Chemistry, Operations, and Quality 2024年1月23日 Analyzing key metrics and trends enables informed decisionmaking for continuous improvement in operation and efficiency The cement mill is a crucial equipment in cement production, operating through key steps including How To Optimize The Operation Of The Cement Mill
.jpg)
(PDF) Robust stabilization of cement milling process using
2013年2月7日 KeyWords: Dynamics, Cement, Mill their setpoints and a longterm stable operation of the grinding circuit close of a robust controller regulating the cement mills operationBearings are effectively sealed against aggressive cement dust and other contaminating substances (above right) Cement mill perma lubrication systems on turning parts of the cement mill Permanent lubrication during mill operation at 155 rpm (below left) Screw conveyor Screw conveyors just below hall ceilings are extremely difficultperma Lubrication Systems in Cement Plants ASGCO2020年8月25日 A full cement production process includes the cement crushing process, raw mill process, clinker process, and cement grinding process, cement packing process, and related process Find more! Skip to content +86 s about blog contact EN ES Menu Menu Home;Cement Production Process Cement Manufacturing Process AGICO CEMENTThe objective of using a kiln in the production of clinker is to create the necessary conditions for chemical reactions to occur, which ultimately results in the formation of a hard, solid material that can be ground into a fine powder and used to make cement Clinker is a key component in the production of cement, as it provides the binding Cement Production Demystified: StepbyStep Process and
.jpg)
The Cement Plant Operations Handbook International Cement
The Cement Plant Operations Handbook is a concise, Key sections covering raw materials, burning, grinding and quality control are supported by a range of chapters Cement mill specific power consumption – 4 Other systems – 5 Debottlenecking – 6During the ball mill operation, you should check the condition of all the lubricating points and the oil level height, at least once every 4 hours, and at the same time make sure that the temperature of the main bearing lubricating oil is not more than 55 ℃Cement Ball Mill Maintenance INFINITY FOR CEMENT EQUIPMENTThe consumption of energy by the cement grinding operation amounts to one third of the total electrical energy used for the production of cement The optimization of this process would yield substantial benefits in terms of energy savings and capacity increase Optimization of the Cement Ball Mill OperationOPTIMIZATION OF CEMENT GRINDING OPERATION IN BALL MILLS2014年3月1日 been made to optimize PID controllers of cement mil ling The process simulation is combined with anOptimizing the control system of cement milling: Process