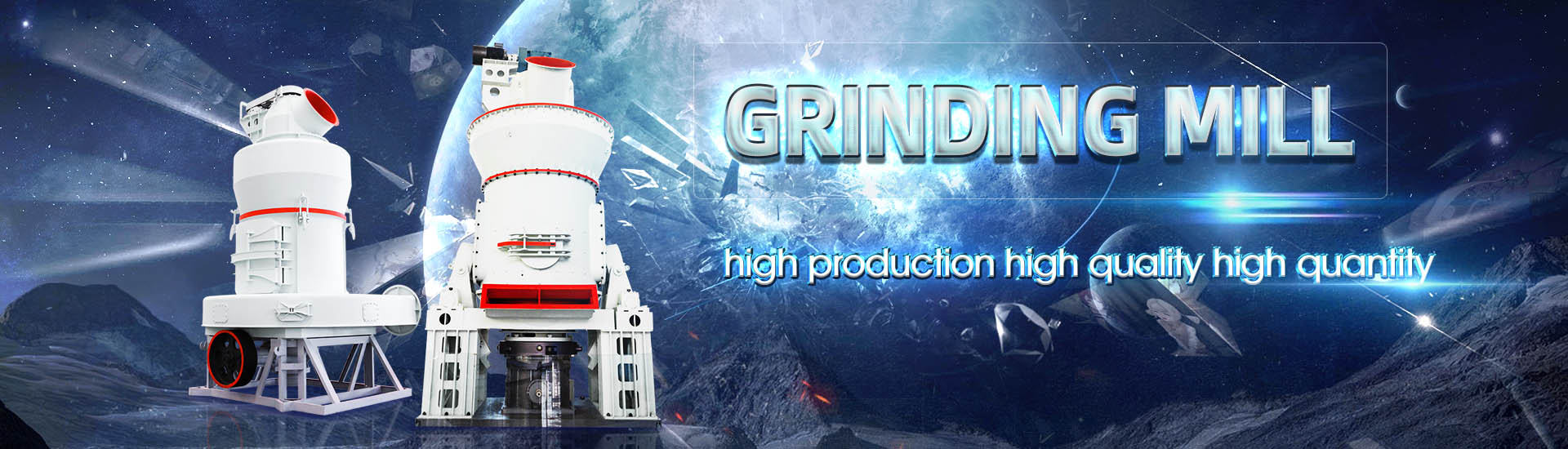
The role of alumina ore grinding mill sintering knowledge questions and answers
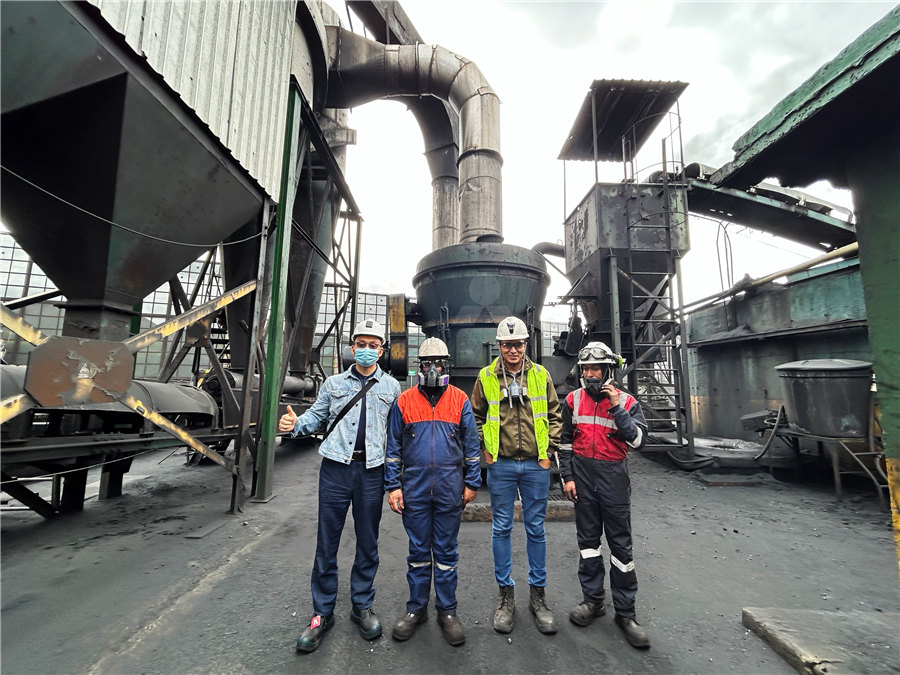
Short communicationSintering behavior and mechanical
2021年8月15日 The effect of oscillatory pressure on the sintering behavior and mechanical properties of alumina ceramics was studied at different stages of sintering Compared to ceramics prepared via conventional hot pressing, samples consolidated by hot oscillatory pressing 2021年5月1日 On account of the analysis of alumina occurrence in the based iron ore, the effect of alumina occurrence, including free alumina, gibbsite, kaolinite and aluminous goethite, on Effect of alumina occurrence on sintering performance of iron ores 2021年6月14日 From the statistical analysis, linear and nonlinear models with added firstorder interaction were developed for prediction and optimization of densitydependent variables: (PDF) Optimization of Sintering Process of Alumina Ceramics Using This paper deals with the influence of alumina in iron ore on sinter properties and sinter productivity formed by both the conventional and selective granulation process Literature (PDF) Influence of Alumina on Iron Ore Sinter Properties and
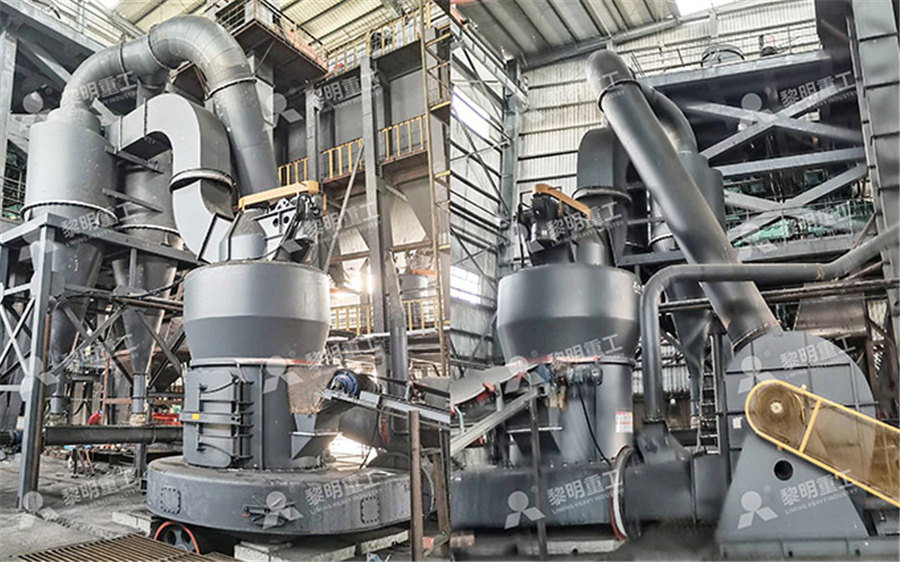
Effect of sintering aids on mechanical properties and
2023年6月1日 According to the action mechanism of sintering aids in traditional alumina ceramics, liquid phase sintering aids CaO, solid solution sintering aids TiO 2 and rare earth 2024年8月22日 This study systematically investigated the impact of increasing the proportion of highalumina iron ore on sintering performance through sinter pot tests The detailed Effect of increasing the proportion of highalumina iron ore on 2007年4月22日 Sintering in air of an ultra pure αalumina powder has been investigated Isothermal experiments have been conducted on green samples shaped by slip casting The Sintering of an ultra pure αalumina powder: I Densification, grain 2007年4月4日 This paper attempts to clarify the role of different types of alumina present in iron ore fines and their effects on melt formation, sinter structure and sinter quality, as well as theEffects of Alumina on Sintering Performance of Hematite Iron Ores
.jpg)
Influence of Alumina on Iron Ore Sinter Properties and
2010年4月23日 In the present work laboratory sintering experiments have been carried out with iron ore fines of different alumina level (200 to 546 mass%) to know the influence of alumina 2005年5月24日 The microstructure evolution and densification of alumina containing 10 vol% calcium aluminosilicate glass and 05 wt% magnesium oxide sintered at 1600°C were Liquid Phase Sintering of Alumina, I Microstructure Evolution and pure Alumina TABLE 1 OBSERVATIONS OF SINTERING OF PURE ALUMINA Sample Sl No Sintering Temperature °C Duration (Hours) 1 1500 3 2 1600 3 3 1700 3 1700 5 5 1700 7 6 1700 14 D Sintering of Alumina with Magnesia Three samples were cut and the green specimens of alumina + 1% MgO (by wt) were sintered at the sameStudy on Sintering Characteristics of Alumina2006年6月2日 Ceramic laminates were produced by thermal pressing of pure alumina (Al2O3) and TiO2‐MnO‐doped alumina (d‐Al2O3) tapes and subsequently sintered at temperatures ranging from 1100 to 1250°CRole of Structural Defects in Sintering of Alumina and Magnesia
.jpg)
Sintering behavior and mechanical properties of alumina ceramics
2021年8月15日 Independently of the step of sintering, the oscillatory pressure was beneficial to improve the sintering behavior of alumina ceramics Moreover, the higher was the temperature at which the oscillatory pressure was applied, the better were the mechanical properties of samples, which was especially pronounced for ceramics subjected to oscillatory pressure during the all ID : MPT2016R00118AB1 Abstract: Depletion of high grade iron ores with low alumina and silica content has forced the steel industry to utilize low grade iron ores with high gangue contentOptimization of pelletization process for iron ore with high alumina 2005年10月6日 In the current work, high strength alumina (Al2O3) thin tapes were prepared by a novel geltape casting method The waterbased slurries were gelled by the polymerization of the epoxy monomersThe Role of MgO in the Sintering of Alumina Request PDF2012年5月1日 An Intelligent Mill Load Switching Control of the Pulverizing System for an Alumina Sintering Process May 2012 Control Systems Technology, IEEE Transactions on 20(99):1 11(PDF) An Intelligent Mill Load Switching Control of the Pulverizing
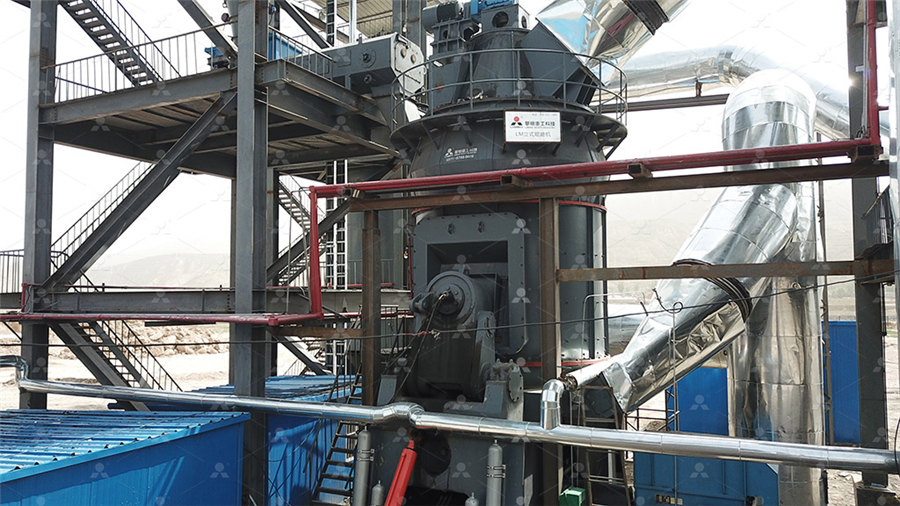
Roles of Alumina and Magnesia on the Formation of SFCA in Iron Ore
The roles of A1 2 O 3 and MgO on the evolution of phases in iron ore sinters have been investigated by simulated sintering in the laboratory using natural ores, commercial grade limestone and analytical grade A1 2 O 3 and MgO A1 2 O 3 may not be necessary for the formation of SFCA in sinters if the sintering temperature is below 1300°C and the sintering 2005年5月24日 The microstructure evolution and densification of alumina containing 10 vol% calcium aluminosilicate glass and 05 wt% magnesium oxide sintered at 1600°C were quantified by measuring the evolution of poresize distribution, the redistribution of liquid phase, and the fraction of closed and open poresLiquid Phase Sintering of Alumina, I Microstructure Evolution and The high aluminum content of kaolin (2040%) makes it more attractive for alumina production and as a substitute for bauxite (Seyed et al, 2011;ElDeeb and Brichkin, 2018;Ali et al, 2019)Alumina % and alumina extraction % from sintering Download 2016年10月28日 Sintering is an agglomeration process that fuses iron ore fines, fluxes, recycled products, slagforming elements and coke The purpose of sintering is to obtain a product with suitable Iron Ore Sintering: Raw Materials and Granulation ResearchGate
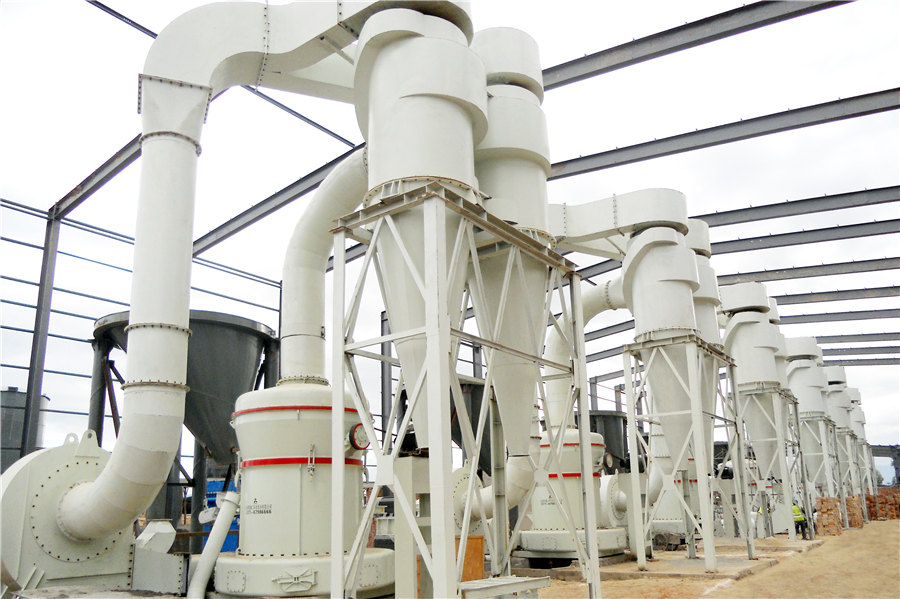
Ore Assimilation and Secondary Phases by
2019年2月22日 During the iron ore sintering process, two types of particles are present in the sinter bed: (1) fines, which are actively taking part in melting and the formation of secondary phases, and (2) coarse ores, which are partially 2024年9月9日 Highalumina iron ore sintering is characterized by poor sinter indices and high carbon emission due to the limited formation amount of liquid phase In this study, the conventional Cabearing flux (ie, burnt lime) was substituted by a new Cabearing flux with low melting point (ie, prefabricated calcium ferrite) for the improvement of the formation ability of Promoting the Utilization of HighAlumina Iron Ores During Sintering Iron ore fines for sintering largely differ in the alumina content with different particle size In Indian iron ore fines alumina is distributed more in finer fraction, ie 100# The size analysis (+1mm and 1mm) and sizewise chemical (PDF) Influence of Alumina on Iron Ore Sinter 2010年4月23日 In the present work laboratory sintering experiments have been carried out with iron ore fines of different alumina level (200 to 546 mass%) to know the influence of alumina on mineralogy, productivity, physical and metallurgical properties of sinter prepared by the conventional and the selective granulation processInfluence of Alumina on Iron Ore Sinter Properties and
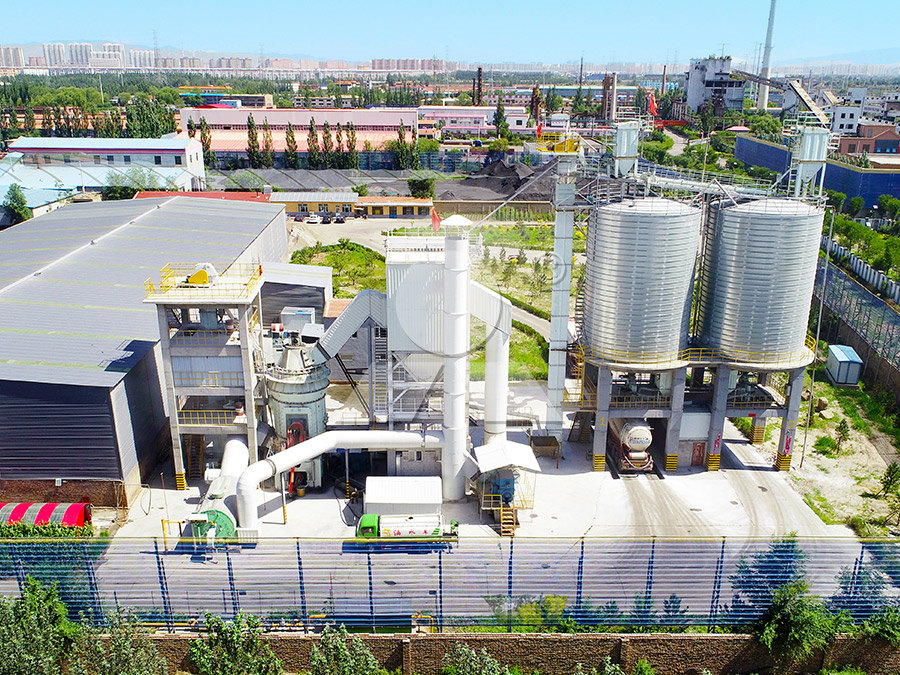
The effects of ore blending on comminution behaviour and
2018年8月17日 The concept of ore blending is a very relevant notion in modern high tonnage production mines It is not only essential for the prolongation of the mine life of the concerned mine but as well as a 2020年12月17日 The effect of the sintering temperatures on the percent recovery of alumina from kaolin ore was investigated in the range from 800 to 1400°C The obtained sinters at different sintering temEffect of sintering temperature on the alumina extraction from 2016年11月1日 The effect of addition of yttria (0–3000 ppm) on the grain growth and densification of high purity αalumina was studied [9] at temperatures of 1450 °C, 1550 °C and 1650 °CYttrium doping inhibited densification and coarsening at 1450 °C, but had very little effect on the same at 1550 °C and no effect at 1650 °CThis change in densification behavior is Rationalizing the role of magnesia and titania on sintering of α 2011年1月1日 Infect only a few investigators worked on the kinetics of mill scale reduction [24][25][26][27][28][29][30]In previous studies on the use of the catalyst for iron ore or mill scale reduction (PDF) Recycling of mill scale in sintering process Science of
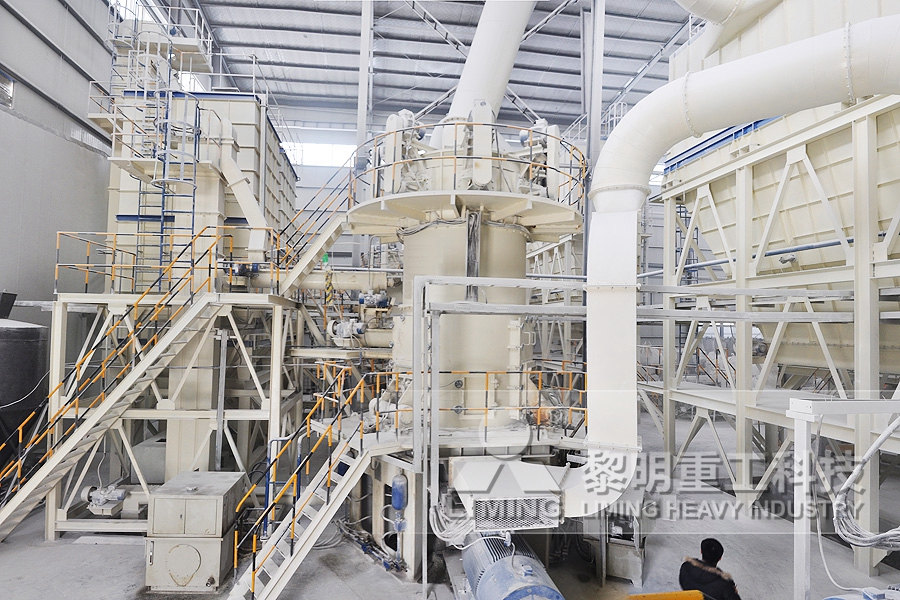
Sintering: A Step Between Mining Iron Ore and Steelmaking
2019年6月11日 World resources are estimated to be greater than 800 billion tons of crude ore containing more than 230 billion tons of iron The only source of primary iron is iron ore, but before all that iron ore can be turned into steel, it must go through the sintering process Sinter is the primary feed material for making iron and steel in a blast furnace2013年7月8日 Fig 1 Flowsheet of sintering process The iron ore fines are natural ore of size 0 mm to 10 mm The raw mix (also called sinter mix) is made with the weighed amount of iron ore fines, limestone, dolomite, sand or quartzite fines (flux), solid fuel (coke breeze or anthracite) and metallurgical wastes (collected dusts, sludge and mill scale etc)Factors influencing Sinter and Sintering Process – IspatGuru2020年5月14日 The concentration of lowgrade iron ores is vital to the continued availability of iron and steel in our everyday lives (Eisele and Kawatra, 2003;Kawatra and Claremboux, 2021a;Zhang et al, 2021)THE GROWING IMPORTANCE OF PELLETIZING FOR minerals Article Ore Assimilation and Secondary Phases by Sintering of Rich and HighGangue Iron Ores Roland Mežibrický 1, *, Mária Fröhlichová 1 , Róbert Findorák 1 and Valerie Sue Goettgens 2 1 2 * Institute of Metallurgy, Technical University of Košice, Letná 9, 04200 Košice, Slovakia; (MF); (RF) Institute of (PDF) Ore Assimilation and Secondary Phases by Sintering of Rich
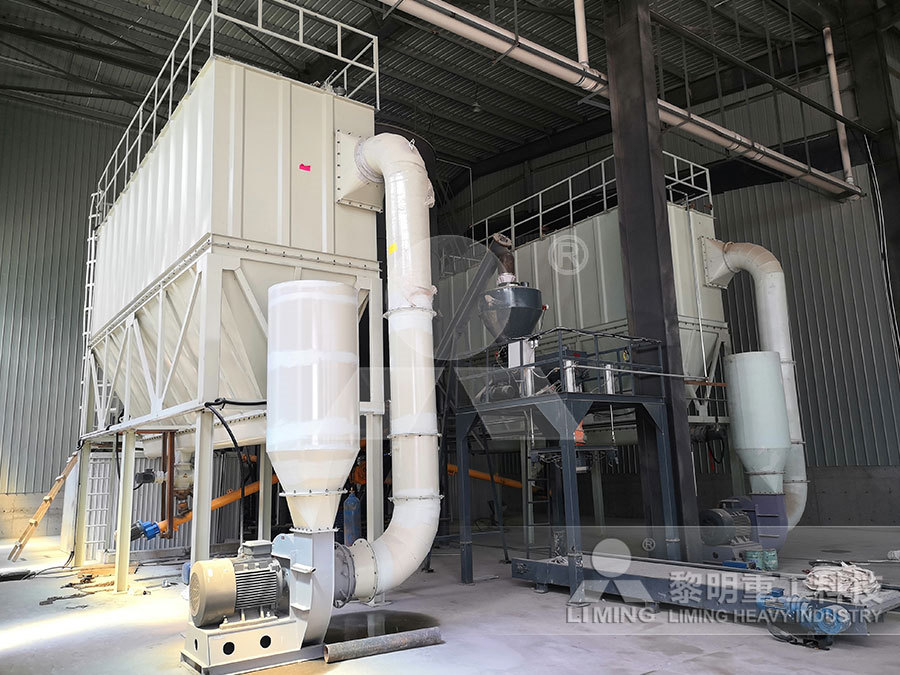
Ore Grinding SpringerLink
2023年7月20日 Therefore, the rod mill is mostly used for coarse grinding of the previous period of ball mill, or grinding of brittle materials and materials against overcrushing, such as tungsten and tin ore before gravity separation; and (3) autogenous mill – it refers to the materials which themselves are collided and ground mutually to be crushed when the grinding mill rotates, and was Sintering and heating reduction processes of alumina containing The ratio between the optimum moisture (W) and moisture capacity (mc) of a raw mix was determined as: W = 694 + 012 mc (2) The experimental data indicated a very high correlation between W and mc Continuing with this research [49], the following equation has been proposed, based on earlier work [44], to calculate the optimum moisture (W) as a function of the nature, (PDF) Iron ore sintering Part 1 Theory and practice of the sintering 2023年2月13日 The iron and steel industry has made an important contribution to China’s economic development, and sinter accounts for 70–80% of the blast furnace feed charge However, the average grade of domestic iron ore is low, and imported iron ore is easily affected by transportation and price The intelligent ore blending model with an intelligent algorithm as Research Progress of Intelligent Ore Blending Model MDPI
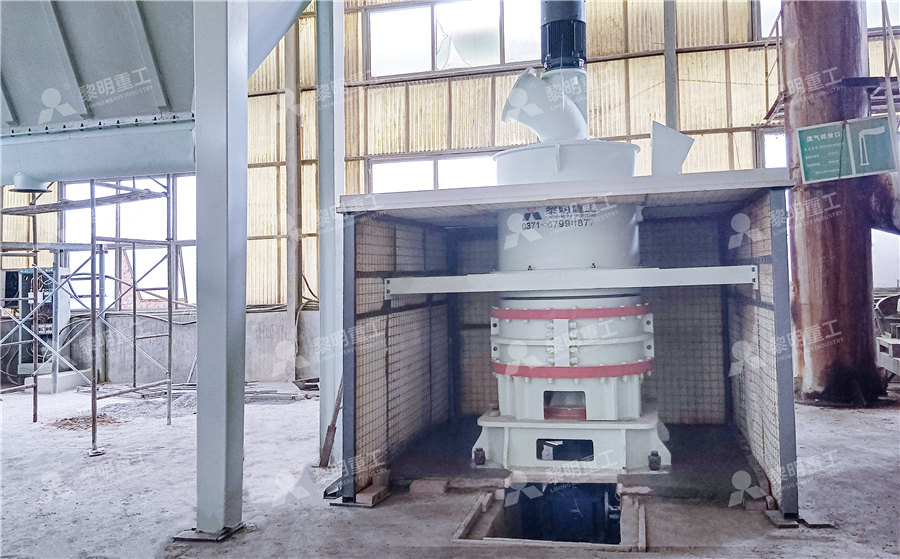
The Role of MgO in the Sintering of Alumina Semantic Scholar
Semantic Scholar extracted view of "The Role of MgO in the Sintering of Alumina" by A Heuer Skip to search form Skip to main content Skip to account menu Semantic Scholar's Logo 222,568,840 papers from all fields of science Sign In Create Free AccountAddition of TiO2 AC C decreases the grain size and increases roundness of spinel grains [45, 46] The role of TiO2 on the reactionsintering of both magnesiarich and aluminarich magnesium aluminate spinel was investigated to discern its specific effect on spinelisation and densification under dynamic and static heating conditionsRole of different rare earth oxides on the reaction sintering of 2024年8月22日 The silicoferrite of calcium and aluminium, known as SFCA phases, are considered the most favourable bonding phases in iron ore sintering due to their excellent characteristics, including high reducibility, stronger mechanical strength, and minimal reduction degradation 11 These properties play an important role in influencing the productivity and Effect of increasing the proportion of highalumina iron ore on 2024年4月26日 These mills utilize the ore itself as the grinding media, reducing the need for additional grinding media AG/SAG mills are typically used for coarse grinding, where large pieces of ore are efficiently broken down The grinding process reduces the ore size, which enhances the efficiency of subsequent beneficiation processes by increasing the Iron Ore Processing: From Extraction to Manufacturing
.jpg)
Study on Sintering Characteristics of Alumina
pure Alumina TABLE 1 OBSERVATIONS OF SINTERING OF PURE ALUMINA Sample Sl No Sintering Temperature °C Duration (Hours) 1 1500 3 2 1600 3 3 1700 3 1700 5 5 1700 7 6 1700 14 D Sintering of Alumina with Magnesia Three samples were cut and the green specimens of alumina + 1% MgO (by wt) were sintered at the same2006年6月2日 Ceramic laminates were produced by thermal pressing of pure alumina (Al2O3) and TiO2‐MnO‐doped alumina (d‐Al2O3) tapes and subsequently sintered at temperatures ranging from 1100 to 1250°CRole of Structural Defects in Sintering of Alumina and Magnesia2021年8月15日 Independently of the step of sintering, the oscillatory pressure was beneficial to improve the sintering behavior of alumina ceramics Moreover, the higher was the temperature at which the oscillatory pressure was applied, the better were the mechanical properties of samples, which was especially pronounced for ceramics subjected to oscillatory pressure during the all Sintering behavior and mechanical properties of alumina ceramics ID : MPT2016R00118AB1 Abstract: Depletion of high grade iron ores with low alumina and silica content has forced the steel industry to utilize low grade iron ores with high gangue contentOptimization of pelletization process for iron ore with high alumina
.jpg)
The Role of MgO in the Sintering of Alumina Request PDF
2005年10月6日 In the current work, high strength alumina (Al2O3) thin tapes were prepared by a novel geltape casting method The waterbased slurries were gelled by the polymerization of the epoxy monomers2012年5月1日 An Intelligent Mill Load Switching Control of the Pulverizing System for an Alumina Sintering Process May 2012 Control Systems Technology, IEEE Transactions on 20(99):1 11(PDF) An Intelligent Mill Load Switching Control of the Pulverizing The roles of A1 2 O 3 and MgO on the evolution of phases in iron ore sinters have been investigated by simulated sintering in the laboratory using natural ores, commercial grade limestone and analytical grade A1 2 O 3 and MgO A1 2 O 3 may not be necessary for the formation of SFCA in sinters if the sintering temperature is below 1300°C and the sintering Roles of Alumina and Magnesia on the Formation of SFCA in Iron Ore 2005年5月24日 The microstructure evolution and densification of alumina containing 10 vol% calcium aluminosilicate glass and 05 wt% magnesium oxide sintered at 1600°C were quantified by measuring the evolution of poresize distribution, the redistribution of liquid phase, and the fraction of closed and open poresLiquid Phase Sintering of Alumina, I Microstructure Evolution and
.jpg)
Alumina % and alumina extraction % from sintering Download
The high aluminum content of kaolin (2040%) makes it more attractive for alumina production and as a substitute for bauxite (Seyed et al, 2011;ElDeeb and Brichkin, 2018;Ali et al, 2019)2016年10月28日 Sintering is an agglomeration process that fuses iron ore fines, fluxes, recycled products, slagforming elements and coke The purpose of sintering is to obtain a product with suitable Iron Ore Sintering: Raw Materials and Granulation ResearchGate