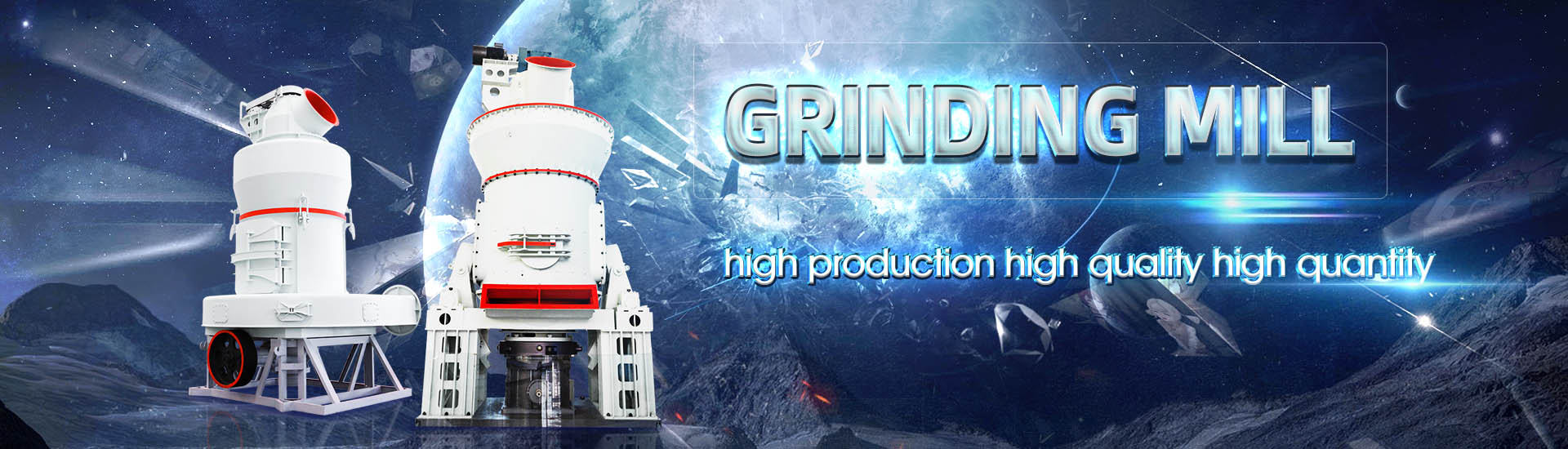
1007 vertical grinding mill
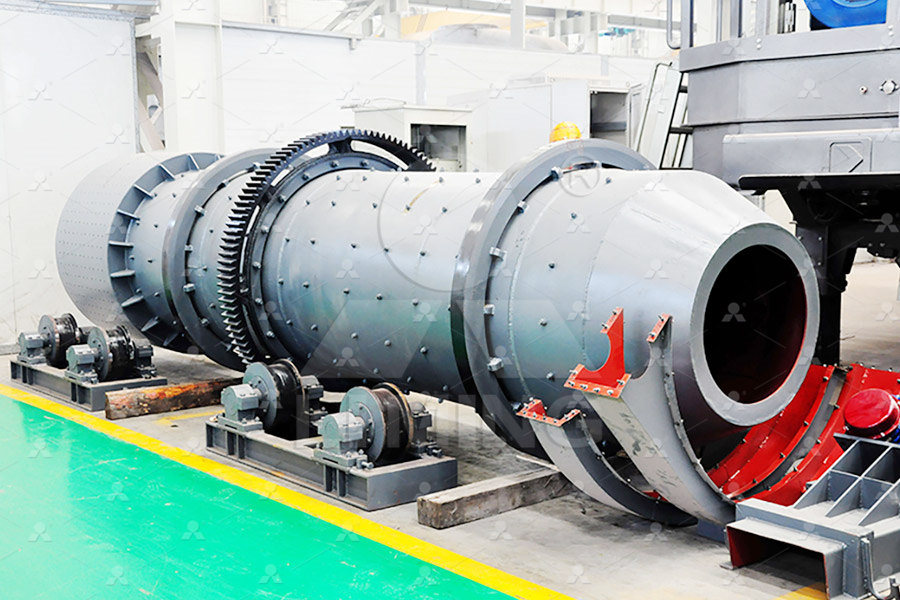
PROCESS OPTIMISATION FOR LOESCHE GRINDING PLANTS
The core elements of these plants are the Loesche vertical mills for drygrinding the abovementioned grinding stock Loesche has developed and built the largest and most efficient MPS vertical mill from Pfeiffer is the ideal allrounder Grinding of coal, petcoke, clay, limestone, quicklime, gypsum, and many other materialsCoal mill, gypsum mill, clay mill, etc Pfeiffer MPS mills2023年12月4日 A vertical roller mill (VRM) is a grinding equipment used for the size reduction of minerals, cement, and ceramics The capacity of the VRM depends not only on the grinding material properties but also on the operational parameters of the VRM This study investigatedNumerical Investigation of Vertical Roller Mill Operation Using is examined in more detail This mill uses conical grinding rollers, which are individually pressed onto a flatformed grinding track through a hydropneumatic spring system viaalevermechanism Duetothementioned arrangement ofthegrindingbodies, itispossibletoadjustazerogapbetween the grinding track and the grinding body AdditionMultiphysics Simulation of a Vertical Roller Mill in Matlab
.jpg)
Operational Failure of Vertical Roller Attached to a Grinding Mill
The schematic of grinding mill and isolated vertical roller assembly is shown in Fig 1 During operation of grinding mill, normal load was maintained below * 70 bar depending on the characteristics of feed material The grinding mill consisted of a table with diameter * 2500 mm and grinding track of * 1600 mm diameter2024年8月7日 Vijayabhaskar, B, Jayalalitha, S: Dual adaptive model predictive controller application to vertical roller mill process used in the cement industry IEEE Access 8, – (2020) Wenhuan, L, et al: Intelligent simulation computation and finite element intelligence analysis for key component of lowvibration vertical millMultiphysics Simulation of a Vertical Roller Mill in 2024年1月1日 After entering the mill body from the lower end under a certain feed pressure, the materials to be ground spiral up and down along the spiral tangent direction under the action of the spiral agitator, and spin spontaneously at the same time, thus achieving the grinding effect For the vertical spiral stirred mill, the maximum feed size is 6 mm Stirred Mill SpringerLinklink of the main components of vertical mill, carried out the antijamming analysis, and solved the problems in the assembly, overall design of vertical mill was completed well and achieved the expect of design Fig 6 Vertical roll grinding explosion Fig 7 Vertical grinding structure Solid Edge’s Application in Vertical Mill Design 1101Solid Edge’s Application in Vertical Mill Design Springer
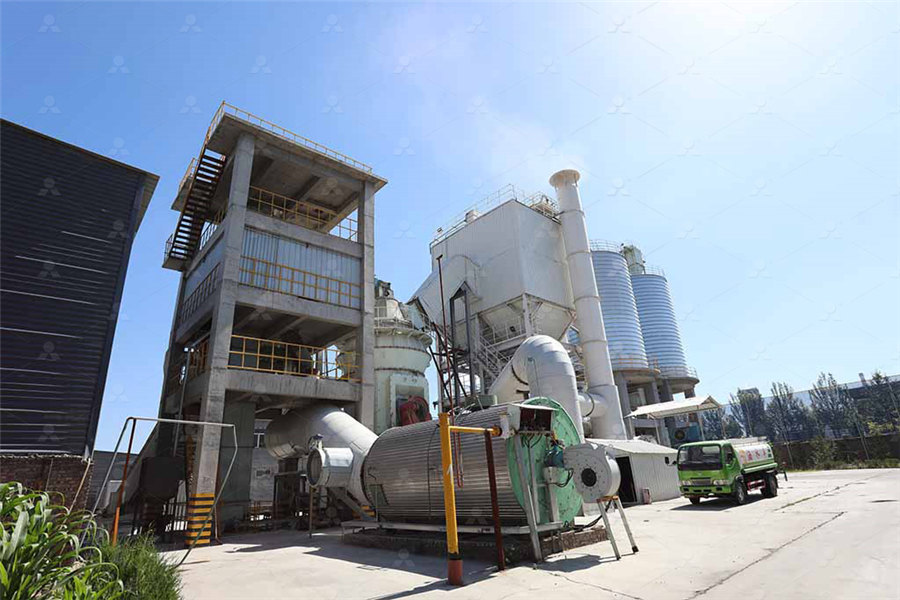
Roller Mill Springer
The basic structure of the roller mill includes the grinding roller, the grinding body, the force generation and transmission mechanism, airflow, and the device for easy replacement It can be divided into vertical roller mill, horizontal cylinderrollermill,highpressurerollermill,Raymond mill, and column mill Vertical Roller Mill2023年7月4日 The column mill is a vertical mill using high speed, medium pressure, and continuous, repeated grinding It consists of the belt pulley, the gearbox, the main shaft, the feeding device, the discharging device, the spreading plate, the Roller Mill SpringerLink2014年6月12日 The article deals with an innovative approach of combining modern simulation techniques with pilot plant testing work with the target to develop a new stirred media grinding mill With the help of discrete element simulation various mill configurations were studied The target was maximizing the interactions between beads and the related power consumption Having Development of an Energy Optimized Stirred Media Grinding Mill2024年1月1日 The column mill is a vertical mill using high speed, medium pressure, and continuous, repeated grinding It consists of the belt pulley, the gearbox, the main shaft, the feeding device, the discharging device, the spreading plate, the Roller Mill SpringerLink
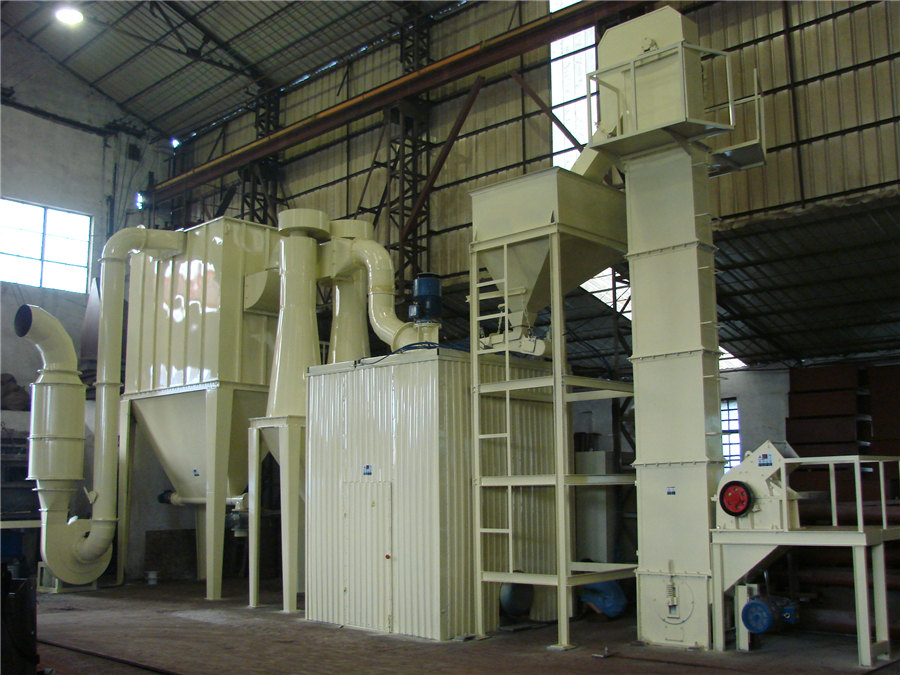
Modeling Based on the Extreme Learning Machine for Raw Cement Mill
2015年1月1日 Vertical grinding mill is the main grinding equipment for the newtype dry cement raw meal production, raw material grinding process in cement industries accounts for approximately 50#8211;60#160;% of the total energy consumption The dynamic characteristics of theWhether grinding raw coal, clinker, cement and/or slag, we have a VRM solution to suit your grinding needs What’s more, our online condition monitoring services enable you to adopt a proactive maintenance strategy for your OK™ and Vertical roller mills FLSmidth Cement2023年5月18日 After entering the mill body from the lower end under a certain feed pressure, the materials to be ground spiral up and down along the spiral tangent direction under the action of the spiral agitator, and spin spontaneously at the same time, thus achieving the grinding effect For the vertical spiral stirred mill, the maximum feed size is 6 mm Stirred Mill SpringerLinkFor a comparison with vertical grinding, corresponding ballgrinding experiments were conducted according to the flow chart shown in Fig 4 Similar to the verticalrollermill grinding experiments, the ballmill grinding experiments were conducted Research on new beneficiation process of lowgrade magnesite
.jpg)
The Influence of Stirred Mill Orientation on Calcite Grinding
tical (Tower Mill, Vertimill, Maxmill, Stirred Media Detritor, ATRVertical Agitated Media Mill) The main difference between vertical and horizontal structures comes from operational variations Additionally, scaling up of mills is also an important parameter for selecting the LUM Ultrafine Vertical Mill Input Size: 020mm Output Size: 3252500 mesh LEARN MORE Hammer Mill Input Size: 040mm Output Size: 03 mesh LEARN MORE Ball Mill SBM is the biggest crushing machine and grinding mill manufacturer in Asia Besides, SBM offer customers comprehensive service, including solution design, Grinding Mill ultrafine grinding mill, vertical ultrafine mill The Vertical Grinding Mill is now CEapproved For very fine grinded coffee on our Diamant Vertical mills, we can supply the mills with special coffee stones in the size 400 mm and 500 mm Our mill in size 400 mm is available in a special version for milling oily products for example mustard – it must be dry and not wetDiamant Vertical Grinding Mill Engsko2019年1月17日 12 Vertical Mill Structure Features (1) The relative sliding difference between the core plate and the grinding roller is small and the speed of the disc is very fast, roller working pressure also very high all this cause relatively high yield and Power saving effect is obviousSolid Edge’s Application in Vertical Mill Design
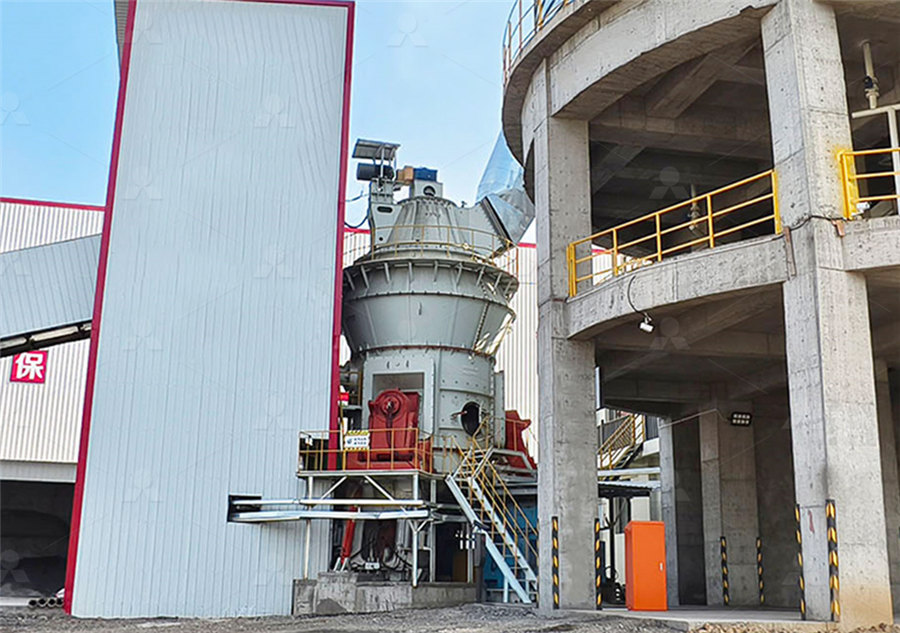
Coal mill, gypsum mill, clay mill, etc Pfeiffer MPS mills
MPS vertical mill from Pfeiffer is the ideal allrounder Grinding of coal, petcoke, clay, limestone, quicklime, MPS 100 GC vertical roller mill for the grinding, drying and calcining of gypsum, Trevo, Brasil MPS 3350 B mill for limestone grinding, China mill isatmiddleandlowrotating speed, whilethe stirred mill of bar type and disc type are at high rotating speed As the most commonly used stirred mill, the vertical spiral type is provided with agitator of spiral blade, and the grinding media are usually steel balls with a diameter of 12–30 mm Running at 30–120 revolutions perStirred Mill Springer2024年3月22日 The vertical roller mill used in the cement industry is a crucial piece of equipment that operates continuously and is essential for production However, frequent breakdowns in its components, particularly the roller ends, have resulted in multiple production stops To address this issue, the concept of analyzing the mill's sound vibrations to identify Soundbased diagnosis of failure in a vertical roller millfine and ultrafine grinding This horizontal mill uses a closed grinding chamber with rubber lined discagitator geometry Grinding media and slurry are centrifuged with slurry back to the feed end by means of a patented media retention device at the end of the mill The mill is run in open circuitDevelopment of an Energy Optimized Stirred Media Grinding Mill
.jpg)
The Influence of Stirred Mill Orientation on Calcite Grinding
2021年4月21日 The purpose of this study was to investigate the dry grindability of calcite powders in a vertically and horizontally orientable laboratory batch type stirred mill The experimental results were evaluated using stress intensity analysis The performance was also compared in terms of mill orientation The results showed that the d50 values decreased with The results show that the optimum process parameters for the vertical roller mill are as follows: a grinding fineness of 816wt% of particles less than 0074 mm, a dodecyl amine (DDA) dosage in magnesite reverse flotation of 100 gt −1 , and dosages of Na 2 CO 3 , (NaPO 3 ) 6 , and NaOL in the positive flotation section of 1000, 100, and 1000 gt −1 , respectivelyResearch on new beneficiation process of lowgrade magnesite For a comparison with vertical grinding, corresponding ballgrinding experiments were conducted according to the flow chart shown in Fig 4 Similar to the verticalrollermill grinding experiments, the ballmill grinding experiments were conducted Research on new beneficiation process of lowgrade magnesite For ball mills grinding OPC to a fineness of up to around 3600 cm2/g (Blaine) grinding aid is usually not required; it may not even be feasible considering the cost of grinding aid However, a vertical roller mill for cement grinding generally requires the use of grinding aid to achieve the most efficient operation with a stable grinding bed Cement grinding Vertical roller mills VS ball mills
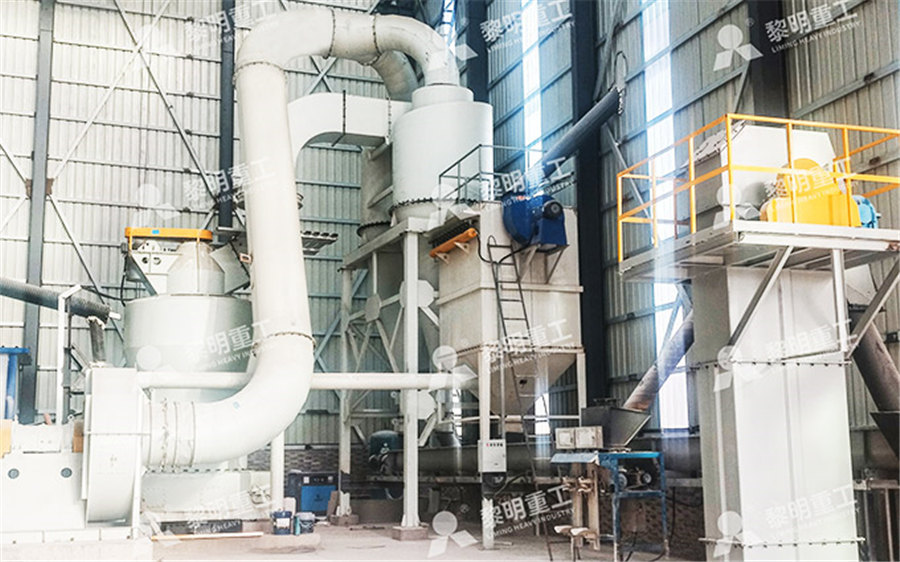
CLUM Ultrafine Vertical Grinding Mill
CLUM series of ultrafine gypsum powder vertical grinding mills are a new type of ultrafine industrial ore grinding equipment that integrates grinding, grading, powder collection and conveying +年10月15日 The working principle of the vertical coal grinding mill is like that of mill, coal mill normal starting procedure can be summarized as Grinding mill motor start: The start working of vertical coal mill is driven by an electric motor At this state the following parameter are controlled: Mill inlet shutoff damper 30% open before feedingCashew Nutshell and Raw Coal Cogrinding for Sustainability Vertical Grinding Mill’s are used to grind various insulation materials, phosphate rocks, cement, activated clay or carbon, limestone, marble, glass, plaster, etc It enables the grinding and processing of more than 280 kinds of nonflammable and nonexplosive materials with a hardness lesser than 7 and humidity less than 6%Vertical Grinding Mill: How it Works, Application And AdvantagesRoller vertical mill Grinding table and reducer Fig 1 Roller vertical mill illustration Source: Cement Elizabeth, 2019 Table 1 Maintenance history in the vertical roller mill in 2022 Source: Author Occurrence Date Component Maintenance 1 April/22 Roller 4 Cylinder repair due to leak 2 April/22 Roller 1 Bearing changeSoundbased diagnosis of failure in a vertical roller mill Springer
.jpg)
Numerical Investigation of Vertical Roller Mill Operation Using
2023年12月4日 A vertical roller mill (VRM) is a grinding equipment used for the size reduction of minerals, cement, and ceramics The capacity of the VRM depends not only on the grinding material properties but also on the operational parameters of the VRM This study investigatedis examined in more detail This mill uses conical grinding rollers, which are individually pressed onto a flatformed grinding track through a hydropneumatic spring system viaalevermechanism Duetothementioned arrangement ofthegrindingbodies, itispossibletoadjustazerogapbetween the grinding track and the grinding body AdditionMultiphysics Simulation of a Vertical Roller Mill in MatlabThe schematic of grinding mill and isolated vertical roller assembly is shown in Fig 1 During operation of grinding mill, normal load was maintained below * 70 bar depending on the characteristics of feed material The grinding mill consisted of a table with diameter * 2500 mm and grinding track of * 1600 mm diameterOperational Failure of Vertical Roller Attached to a Grinding Mill 2024年8月7日 Vijayabhaskar, B, Jayalalitha, S: Dual adaptive model predictive controller application to vertical roller mill process used in the cement industry IEEE Access 8, – (2020) Wenhuan, L, et al: Intelligent simulation computation and finite element intelligence analysis for key component of lowvibration vertical millMultiphysics Simulation of a Vertical Roller Mill in
.jpg)
Stirred Mill SpringerLink
2024年1月1日 After entering the mill body from the lower end under a certain feed pressure, the materials to be ground spiral up and down along the spiral tangent direction under the action of the spiral agitator, and spin spontaneously at the same time, thus achieving the grinding effect For the vertical spiral stirred mill, the maximum feed size is 6 mm link of the main components of vertical mill, carried out the antijamming analysis, and solved the problems in the assembly, overall design of vertical mill was completed well and achieved the expect of design Fig 6 Vertical roll grinding explosion Fig 7 Vertical grinding structure Solid Edge’s Application in Vertical Mill Design 1101Solid Edge’s Application in Vertical Mill Design SpringerThe basic structure of the roller mill includes the grinding roller, the grinding body, the force generation and transmission mechanism, airflow, and the device for easy replacement It can be divided into vertical roller mill, horizontal cylinderrollermill,highpressurerollermill,Raymond mill, and column mill Vertical Roller MillRoller Mill Springer2023年7月4日 The column mill is a vertical mill using high speed, medium pressure, and continuous, repeated grinding It consists of the belt pulley, the gearbox, the main shaft, the feeding device, the discharging device, the spreading plate, the Roller Mill SpringerLink
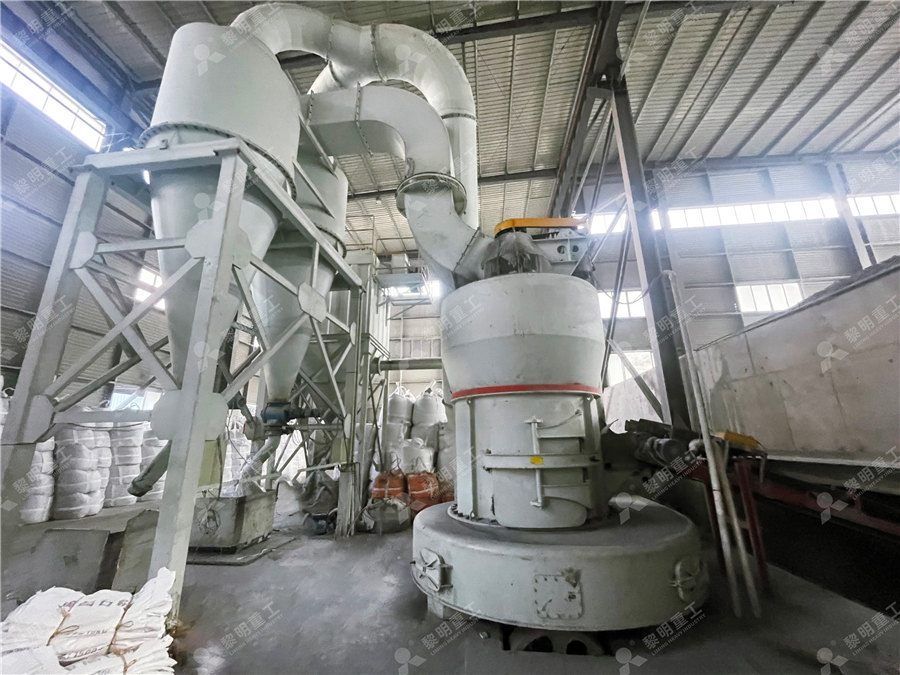
Development of an Energy Optimized Stirred Media Grinding Mill
2014年6月12日 The article deals with an innovative approach of combining modern simulation techniques with pilot plant testing work with the target to develop a new stirred media grinding mill With the help of discrete element simulation various mill configurations were studied The target was maximizing the interactions between beads and the related power consumption Having 2024年1月1日 The column mill is a vertical mill using high speed, medium pressure, and continuous, repeated grinding It consists of the belt pulley, the gearbox, the main shaft, the feeding device, the discharging device, the spreading plate, the Roller Mill SpringerLink