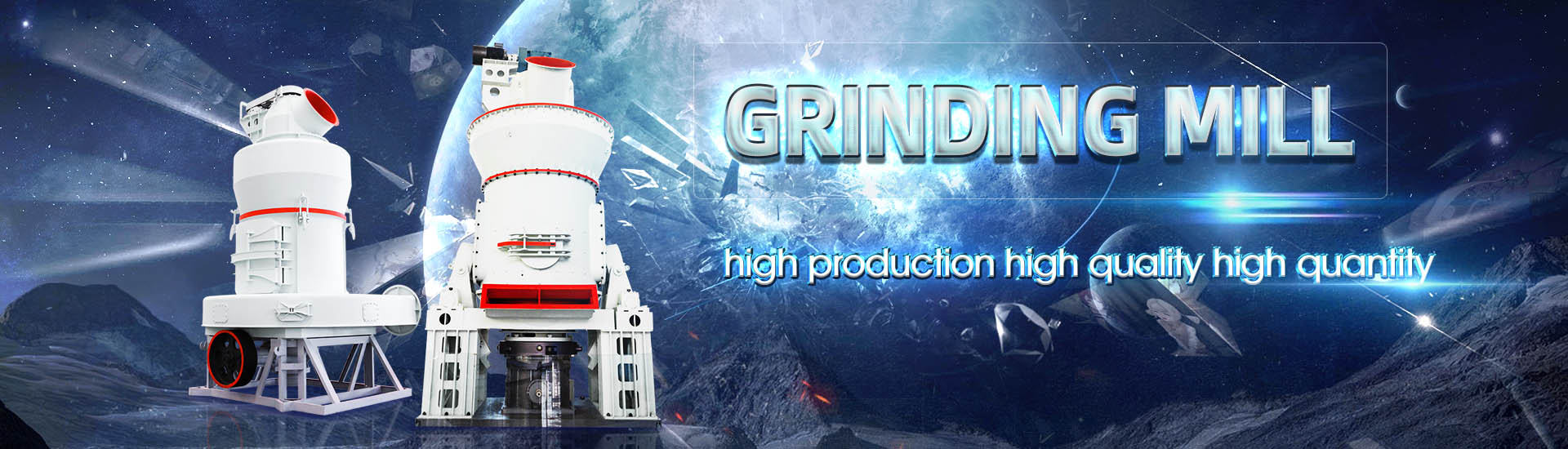
Pictures of coal chemical raw material grinding mill
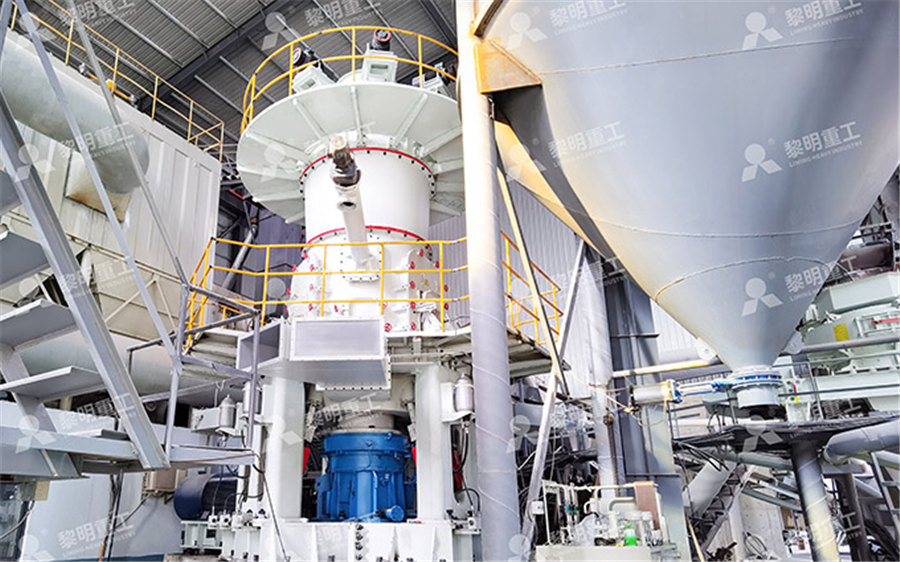
2 µm 5 µm Loesche
The springloaded roller grinding mill for grinding coal was intro duced by Loesche in the 1920’s Since the end of the 1930’s Loesche mills have also been used for grinding cement raw Grinding media are essential components of coal grinding mills, as they are responsible for crushing and grinding the coal material into small particles Grinding media can be made of various materials, including steel balls, ceramic balls, and cylpebs, depending on the specific application and grinding requirementsWhat is a Coal Grinding MillVertical raw mill is one kind of raw mill, generally used to grind bulk, granular, and powder raw materials into required cement raw meal in the cement manufacturing plantVertical raw mill is an ideal grinding mill that crushing, drying, grinding, Vertical raw mill Cement PlantRaw coal flotation The raw coal and lump coal are coarsely crushed by the crusher and crushed to 3mm to meet the feed size of the CWS ball mill The cleaned coal obtained by flotation is mixed and stirred in a mixing tank by Coal Water Slurry Ball Mill
.jpg)
FOR CEMENT RAW MATERIAL
dustfired largescale power plant in Berlin for coal grinding with a raw coal rate of approx 12 t/h 1934 Loesche mills are increasingly also used worldwide for limestone and cement raw material 1937 400 Loesche mills have already been sold for coal, phosphate and cement raw material 1939 The largest Loesche mill at this time is an LM 16A raw mill is the equipment used to grind raw materials into "rawmix" during the manufacture of cement The history of the development of the technology of raw material grinding defines the early history of cement technology The chemical analyses of these rawmixes would be: Oxide Mix 1 Mix 2 Mix 3 SiO 2: 1346: 1391: 1555 Rawmill Wikipediaa Loesche mill, with a grinding track diameter of only 11 metres, was used as long ago as 1935 However, the breakthrough in grinding this type of material on the vertical roller mill did not take place until the beginning of the 1990’s 1935 The first Loesche mill for grinding cement clinker, an LM 11, was commissioned in Joao Pessao, Brazil2 µm 5 µm LoescheJapan to manufacture supply stateoftheart UBE Vertical Roller Mills for grinding applications related to Raw material, Coal, Clinker and Slag Reliable Performance performs drying grinding classification and pneumatic transportation simultaneously The mill consists of the lower casing, upper casing, tableVERTICAL ROLLER MILLS AMCL
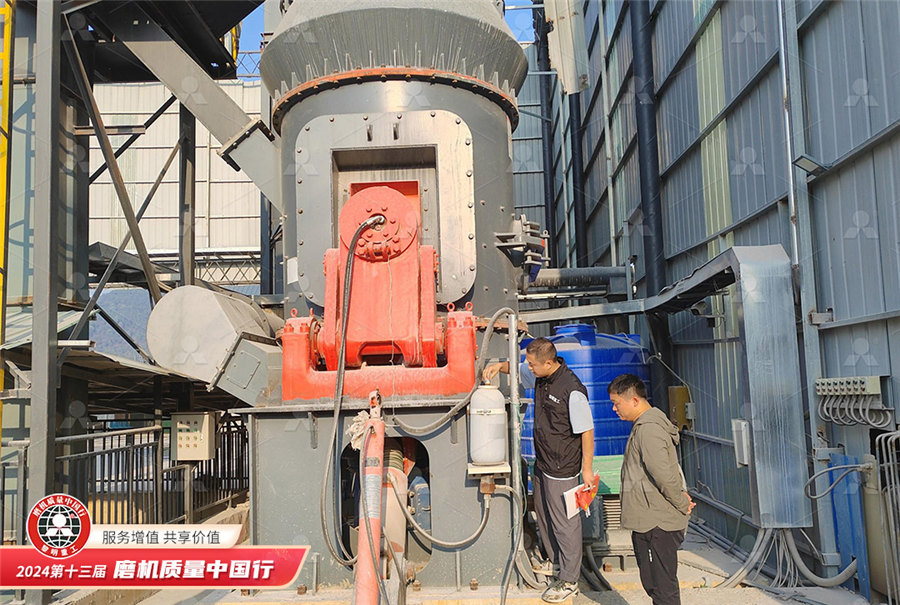
Cement Raw Mill in Cement Plant for Cement Raw Meal Grinding
Raw mill is also called cement raw mill, similar to cement ball mill, it is an important cement milling equipment used in the cement production process Raw mill is mainly used for grinding cement raw meal in the cement factory production process It is also suitable for metallurgical, chemical, electric power and other industrial mining enterprises to grind various ores and other grindable 2014年1月1日 R0090 mm Thus, the MPS coal grinding mill MPS 3070 BK installed in India The commissioning was troublefree and no different from grinding plants for cement raw material, limestone or coal(PDF) MPS mills for coal grinding ResearchGate2024年2月23日 The operation of the cement raw mill is a critical step in cement production By grinding the raw materials into a fine powder, these powders can be more easily mixed with other cement ingredients and burn more evenly during the cement clinker process Therefore, the efficient operation of the cement raw mill directly impacts the production efficiency and quality How Does a Raw Mill Work in a Cement IndustryThe coal grinding mill housing has three parts: the lower housing, The feeding device of the vertical raw mill adopts rotary feeder, Bulk Material Handling; Chemical Industry; EcoFriendly; Contact Us Mr Chen / Ms Qian Coal Mill Coal Grinding Mill Producer SINOMALY
.jpg)
An investigation of performance characteristics and
2020年8月12日 As one of the three major forces of coal mills, the grinding force exerts a significant impact on the working process of coal mills and parameters like mill current and outlet temperatureCrushed material continues to move to mill edge, until being taken away by the wind ring in strong turbulence, and larger particles material again fell to the mill to continue to crush, the flow of materials through the upper part of the Raw mill Cement Plant2005年2月1日 A raw material grinding circuit was modeled using plant data Samples were collected from around the circuit and, following a crash stop, from inside the millModeling and simulation of a fully air swept ball mill in a raw There were some problems with the service life of grinding elements, especially in the case of quartzcontaining raw materials, but because of improvements in wearresistant engineering materials, the service life has been substantially increased and, depending on the abrasiveness of the raw material, values of up to 16,000 h are reported 8 These mills have rollers as shown in Grinding Mill an overview ScienceDirect Topics
.jpg)
Fire and explosion protection of coal grinding systems Where
Safe operation of coal grinding systems: Raw coal silo protection against fire and explosions Safe operation of coal grinding systems: Raw coal yard management The purchasing process for coal grinding systems needs changes Talk at a virtual seminar, November 2023 Accept the probability that the fire and explosion safety of your coal grinding system is nothing more than a mirageBy continuously classifying out fines and returning oversize material to the mill, such systems can very efficiently provide sharp particlesizedistribution grinds As a rule of thumb, dry grinding generally will achieve particle sizes of 3–5 microns To Solids Choose the Right Grinding Mill Chemical ProcessingCement raw material is the mixture of mainly Limestone other constituent such Iron oxide, Shale etc having different moisture contain depending on composition deposit We offer the mills with optimized process technology to evaporate the moisture by employing the hot gases and intricate mill design provides efficient grindingVRM – AMCL Machinery Limited2019年10月1日 Request PDF Wet and dry grinding of coal in a laboratoryscale ball mill: Particlesize distributions In this study, experimental data for wet and dryground coal samples under wet and dry Wet and dry grinding of coal in a laboratoryscale ball mill: Particle
.jpg)
Vertical roller mill for raw Application p rocess materials
vertical roller mill Application process Raw material process Background In the vertical roller mill which is widely used in the raw material grinding process, raw materials input grinding table are crushed and pulverized on it and transported to separator by kiln exit gas introduced into the mill as drying, transporting and separating purpose2021年1月1日 Stacking Reclaiming of Raw material: Swing type stacker Reclaimer: Limestone other raw material are stored in open area into a longitudinal storage unit called stockpile through Stacker These are then extracted transversely from the stockpile through reclaimer: 3: Raw Meal Grinding Homogenization: Grinding Mill Vertical Roller Mill Review on vertical roller mill in cement industry its performance vertical roller grinding mills for grinding: • Coal • Cement raw material • Clinker / granulated slag • Industrial minerals, and • Ores • Pressure before the mill • Grinding stock feed • Classifier speed • Mill fan speed • Water spraying • Hot gas • Fresh PROCESS OPTIMISATION FOR LOESCHE GRINDING PLANTScement mills with a drying chamber see raw mills Mill working conditions: ventilation air speed through the mill Bigger or smaller than 12 [m/s] Material abrasivity The [%] of slag or pouzzolana content on the fresh mill feed for Everything you need to know about clinker/cement
.jpg)
Vertical Coal Mill for Coal Grinding in Cement Plant Power Plant
Vertical coal grinding mill integrates crushing, drying, grinding, powder selection and conveying; It has simple system and compact structure Vertical coal mill covers an floor area about 50% of the coal ball mill with the same specification; Coal vertical mills can work in openair environments, greatly reducing the cost of investment The design of the vertical coal mill system is simple Safe operation of coal grinding systems: Raw coal silo protection against fire and explosions Safe operation of coal grinding systems: Raw coal yard management The purchasing process for coal grinding systems needs changes Talk at a virtual seminar, November 2023 Accept the probability that the fire and explosion safety of your coal grinding system is nothing more than a mirageCoal Mill Safety In Cement Production IndustriesPart Three: Raw Mill Process of Raw Mill The proportioned raw material is feed first to a grinding mill In the mill, particles ground in to very fine sizes In the grinding unit, drying, grinding and mixing takes place simultaneously Hot gas from clinker burning unit is passed into the grinding unit to assist the drying and grinding processCement Manufacturing Process INFINITY FOR CEMENT EQUIPMENT2021年1月22日 In the whole process of cement production, the electricity consumption of a raw material mill accounts for about 24% of the total Based on the statistics of the electricity consumption of the raw A Survey and Analysis on Electricity Consumption of Raw Material Mill
.jpg)
Coal grinding mill, Coal grinding grinding mill All industrial
Find your coal grinding mill easily amongst the 48 products from mill solution for grinding virtually any type of raw coal Our ATOX® Coal Mill is a compact vertical roller mill Grinding at a medium fineness (0÷5 mm) of low and medium hardness minerals (gypsum, talc, lime, dolomite, clay, coal, etc); chemical products; scraps of Almost any plant for the grinding of cement raw material is a combination of machines specially adapted to the particular physical properties of the material to be ground As our solutions are designed to suit the customers’ requirements, we can guarantee that our mills work efficiently without any troubleRaw mills for all requirements Gebr PfeifferVideo credit: shsbjq / CC BYSA 40 Specifications Important specifications when selecting grinding mills and pulverizers include, The size of the mill can range from pilot/lab to production, eg, 35 to 1600 cu ft; Feed size, material, and hardness of feed must be considered; Output size ranges; Mills can handle dry or wet input, or both; Mills operate in batches or continuouslyGrinding Mills and Pulverizers Selection Guide: Types, Features Grinding media are essential components of coal grinding mills, as they are responsible for crushing and grinding the coal material into small particles Grinding media can be made of various materials, including steel balls, ceramic balls, and cylpebs, depending on the specific application and grinding requirementsWhat is a Coal Grinding Mill
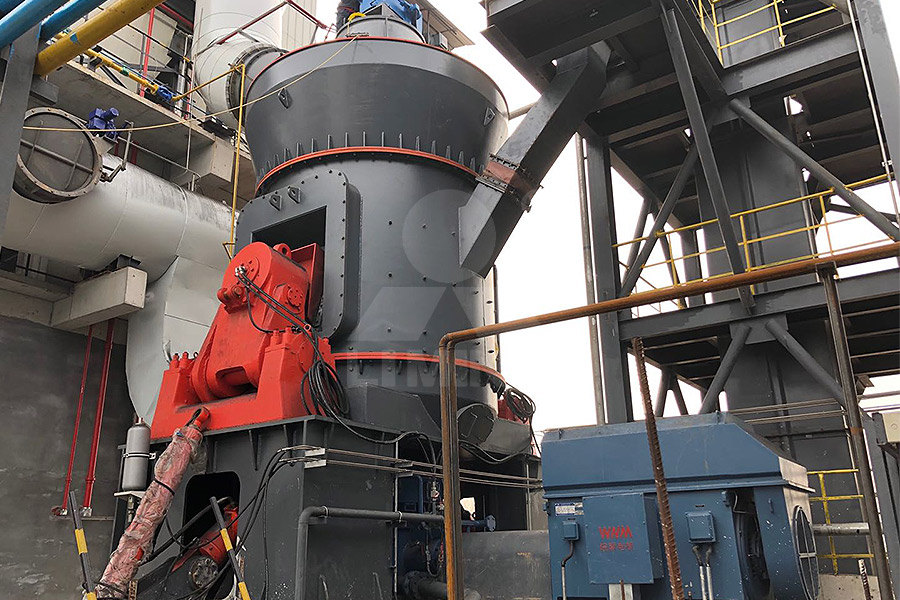
Vertical raw mill Cement Plant
Vertical raw mill is one kind of raw mill, generally used to grind bulk, granular, and powder raw materials into required cement raw meal in the cement manufacturing plantVertical raw mill is an ideal grinding mill that crushing, drying, grinding, Raw coal flotation The raw coal and lump coal are coarsely crushed by the crusher and crushed to 3mm to meet the feed size of the CWS ball mill The cleaned coal obtained by flotation is mixed and stirred in a mixing tank by Coal Water Slurry Ball Milldustfired largescale power plant in Berlin for coal grinding with a raw coal rate of approx 12 t/h 1934 Loesche mills are increasingly also used worldwide for limestone and cement raw material 1937 400 Loesche mills have already been sold for coal, phosphate and cement raw material 1939 The largest Loesche mill at this time is an LM 16FOR CEMENT RAW MATERIALA raw mill is the equipment used to grind raw materials into "rawmix" during the manufacture of cement The history of the development of the technology of raw material grinding defines the early history of cement technology The chemical analyses of these rawmixes would be: Oxide Mix 1 Mix 2 Mix 3 SiO 2: 1346: 1391: 1555 Rawmill Wikipedia
.jpg)
2 µm 5 µm Loesche
a Loesche mill, with a grinding track diameter of only 11 metres, was used as long ago as 1935 However, the breakthrough in grinding this type of material on the vertical roller mill did not take place until the beginning of the 1990’s 1935 The first Loesche mill for grinding cement clinker, an LM 11, was commissioned in Joao Pessao, BrazilJapan to manufacture supply stateoftheart UBE Vertical Roller Mills for grinding applications related to Raw material, Coal, Clinker and Slag Reliable Performance performs drying grinding classification and pneumatic transportation simultaneously The mill consists of the lower casing, upper casing, tableVERTICAL ROLLER MILLS AMCLRaw mill is also called cement raw mill, similar to cement ball mill, it is an important cement milling equipment used in the cement production process Raw mill is mainly used for grinding cement raw meal in the cement factory production process It is also suitable for metallurgical, chemical, electric power and other industrial mining enterprises to grind various ores and other grindable Cement Raw Mill in Cement Plant for Cement Raw Meal Grinding2014年1月1日 R0090 mm Thus, the MPS coal grinding mill MPS 3070 BK installed in India The commissioning was troublefree and no different from grinding plants for cement raw material, limestone or coal(PDF) MPS mills for coal grinding ResearchGate
.jpg)
How Does a Raw Mill Work in a Cement Industry
2024年2月23日 The operation of the cement raw mill is a critical step in cement production By grinding the raw materials into a fine powder, these powders can be more easily mixed with other cement ingredients and burn more evenly during the cement clinker process Therefore, the efficient operation of the cement raw mill directly impacts the production efficiency and quality