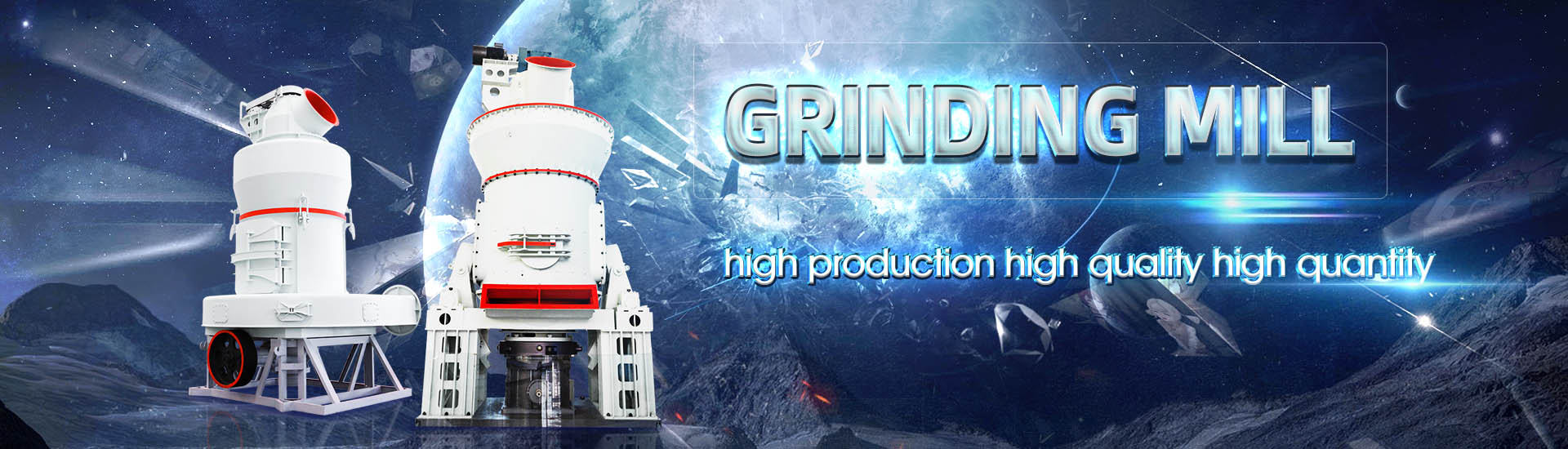
Composition of the hydraulic system of ore grinding mill
.jpg)
A Review of the Grinding Media in Ball Mills for Mineral Processing
2023年10月27日 Grinding media play an important role in the comminution of mineral ores in these mills This work reviews the application of balls in mineral processing as a function of the materials used to manufacture them and the mass loss, as influenced by three basic wear 2023年7月20日 According to the particle sizes of grinding products, the grinding process is divided into coarse grinding, medium grinding, fine grinding, microfine grinding, and ultrafine Ore Grinding SpringerLinkIt is performed in cylindrical steel vessels that contain a charge of loose crushing bodies—the grinding medium—which is free to move inside the mill, thus comminuting the ore particles Grinding Mill an overview ScienceDirect Topicsliberate the valuable minerals in an ore by comminution, and then separate the resulting particles by means of their geometric, compo sitional, and physical propertiesAll About Particles: Modelling Ore Behaviour in Mineral Elements
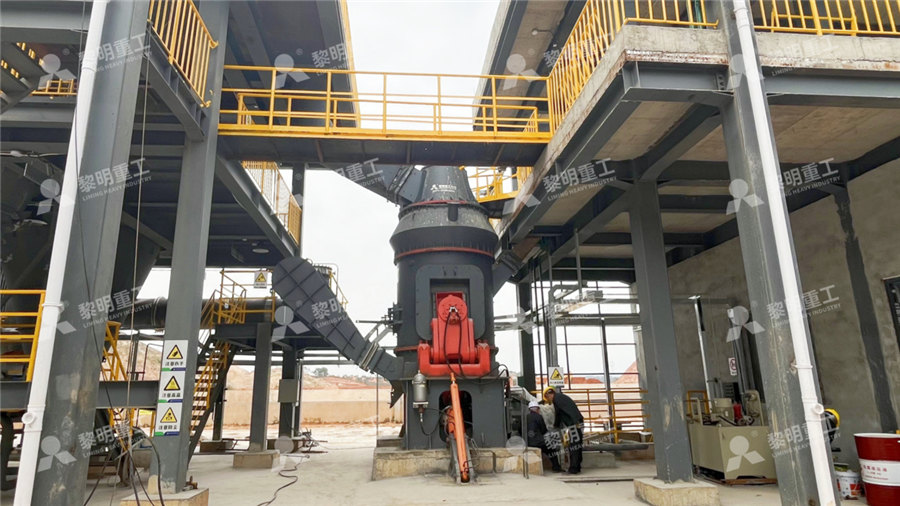
Ore Grinding Methods and Process of Ore Grinding
ore grinding is divided into dry grinding, wet grinding, and moist grinding Dry grinding relies on pneumatic conveying, in which the classification system and gas supply system of grinding 2017年4月1日 In this study, pilot scale tests were performed with a mobile verticalrollermill grinding plant to investigate the relationships between operational parameters The Operational parameters affecting the vertical roller mill the roll movement (roll gap) is a function of the pressing force generated by the hydraulic system in relation to the reaction forces exerted by the processed material This design feature HighPressure Grinding2017年9月1日 The objective of this work is to assess the influence of fine grinding in ball mills and stirred mills on valuable mineral liberation and particle shape characteristics of UG2 ore, a Fine grinding: How mill type affects particle shape characteristics
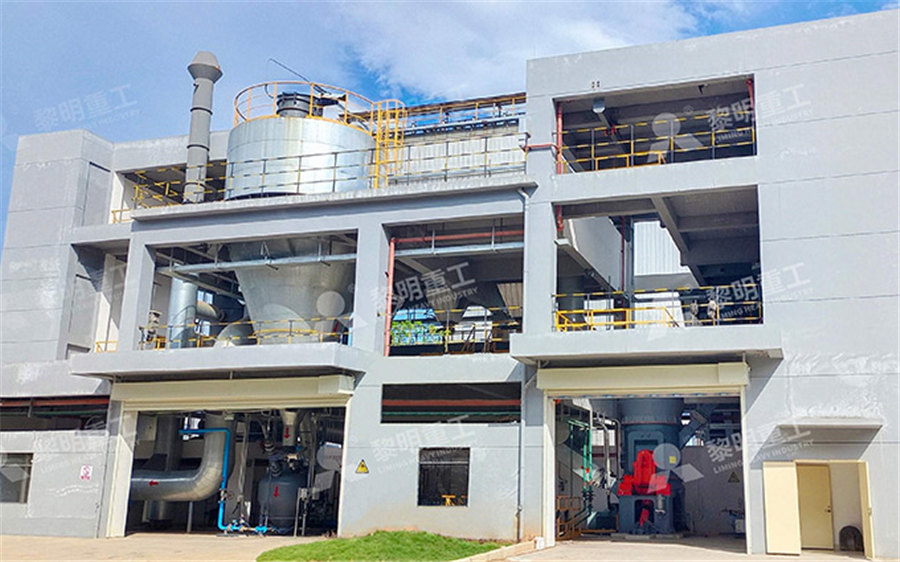
Grinding Contribution and Quantitative Separation of Impact and
2023年8月3日 In summary, the paper proposes for the first time a new grinding analysis method that quantitatively separates and characterizes the grinding contribution of the impact and 2023年11月24日 Factors that influence the grinding efficiency include mill design, liner design, mill speed, mineralogical composition of the ore, charge ratio, and grinding media properties Grinding Media in Ball Mills for Mineral Processing2016年1月10日 On a 11’6” x 22’0” Ball Mill, the trunnion bearing lubrication system provides continuous low pressure flood oil for cooling and lubrication of the bearings, and high pressure oil for hydrostatic lift of the feed and Ball Mill Trunnion Bearing Lube System2024年5月31日 Lean magnetite resources in China are characterized by low iron grade, fine embedded particle size, complex composition, etc, which can only be utilized through complex beneficiation processes [1,2,3]With the increasingly serious problems of lowgrade, fine iron minerals, and difficulttotreat ore properties, the required particle size of ore grinding products High Pressure Grinding Roll and Magnetic Separation for Energy
.jpg)
Physicochemical Problems of Mineral Processing
2017年3月20日 An effect of a grinding method, that is ball mill and high pressure grinding rolls (HPGR), on the particle size, specific surface area and particle shape of an iron ore concentrate was studiedDownload Table Chemical composition of rolling mill scale from publication: Production of sponge iron powder by reduction of rolling mill scale Rolling mill scale is a solid byproduct of the Chemical composition of rolling mill scale Download Table2021年1月22日 Grinding operation is used extensively in the industry of beneficiation, metallurgy, chemical engineering, and electric power Assisted by the impact and abrasion between media (steel ball, steel rod, gravel, ceramic ball) and ore, the grinding operation reduces the particle size in the mill [[1], [2], [3]]To produce the qualified size and high liberation of An innovative approach for determining the grinding media system operation (1) Structure parameters of grinding mill, including its specifications, model, aspect ratio, ore discharging method, and liner form (2) Various working parameters of grinding mill, including fraction of critical speed for grinding mill, filling rate for grinding mill, grinding concentration,grindingcycleload,etc(3)AndgrindOre Grinding Methods and Process of Ore Grinding
.jpg)
Cement Mill Hydraulic Cylinder Brant Hydraulics Corporation
Our cement hydraulic cylinders application include cement process such as vertical grinding mills, crushers, rotary kiln, and more In the systems used during cement grinding and instant cement cooling in the clinker cooling system, the processes are 2015年4月9日 The mill is normally used for grinding of ores The whole system is enclosed in a cylindrical casing The bearing units of one roller can move linearly and are pressed against the material bed by springs or hydraulic cylinders The pressures in Grinding Mills and Their Types – IspatGuruRecently, the vertical roller mill having great grinding performance is widely applied to the raw material grinding process However, tube mill, which has about 30% poor grinding performance as power consumption, has been still used many existing cement plant The improvement of this tube mill grinding system is highly expected DescriptionsVertical roller mill for raw Application p rocess materials2023年12月4日 A vertical roller mill is a grinding equipment for many industries such as minerals, cement, and ceramics It is also used to grind slag and nonmetallic ores The VRM decreases the number of equipment in the grinding circuit by combining the drying, crushing, grinding, and particle segregation in one unit Numerical Investigation of Vertical Roller Mill Operation Using
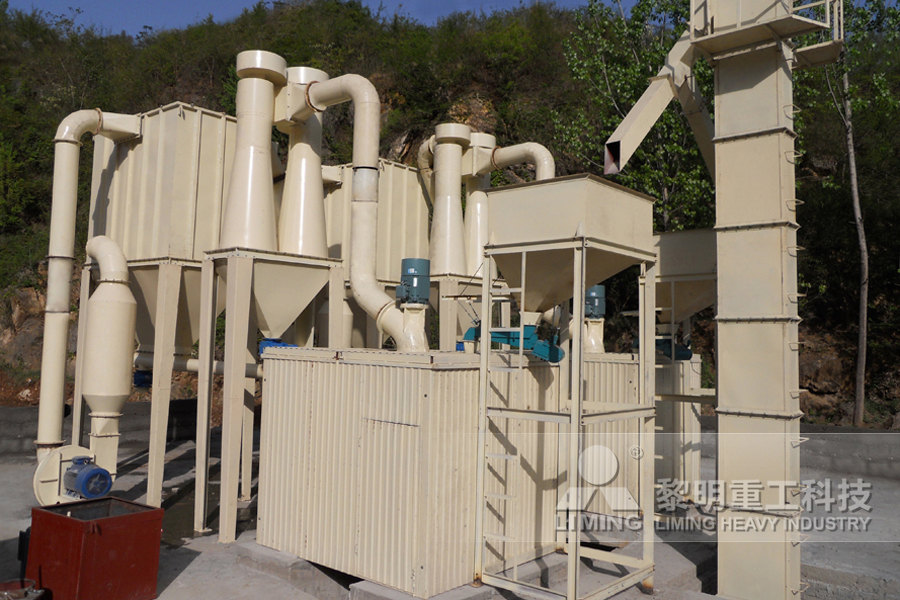
A comparison of wear rates of ball mill grinding
2016年1月1日 The research emphasizes the importance of investigating variables (eg ore heterogeneity) other than ball size, grinding medium composition, and wet or dry grinding that have a substantial impact 2023年10月27日 The ball mill is a rotating cylindrical vessel with grinding media inside, which is responsible for breaking the ore particles Grinding media play an important role in the comminution of mineral ores in these mills This work reviews the application of balls in mineral processing as a function of the materials used to manufacture them and the mass loss, as A Review of the Grinding Media in Ball Mills for Mineral 2012年2月1日 Through the deep analysis of its working principal and the structure, the hydraulic loading system was designed, and the optimum method of the mill hydraulic loading system was researchedThe Optimization Design of the Mill Hydraulic Loading System2023年4月23日 grinding media in a grinding mill with about 2630 wt% chrome by Chen et al [37] using a phosphate ore in a modified ball laboratory ball mill whose electrochemical potential could be controlled(PDF) Grinding Media in Ball MillsA Review ResearchGate
.jpg)
Ore mill, Ore grinding mill All industrial manufacturers
Find your ore mill easily amongst the 42 products from the leading brands (Fritsch GmbH, Retsch, Eriez, hydraulic (1) mobile (1) lowspeed (1) specimen (1) Submit Sectors for accepts grinding set weights of up to 30 kg, the largest grinding jar has a volume of 2,000 ml The closed grinding system guarantees complete processing of the Grinding Mills: Ball Mill Rod Mill Design PartsCommon types of grinding mills include Ball Mills and Rod Mills This includes all rotating mills with heavy grinding media loads This article focuses on ball and rod mills excluding SAG and AG mills Although their concepts are very similar, they are not discussed herePhotographs of a glass ended laboratory ball mill show Grinding Mills 911MetallurgistThe Autogenous Mill, also known as AG Mill, is a type of grinding mill used in the mining industry This machine uses ore and rock itself as grinding media to perform its job Unlike other types of mills that use steel balls or rods for grinding materials, the Autogenous Mill relies on the material being ground to break itself into smaller piecesUnderstanding the SAG Mill in Copper Ore Mining Process2015年3月15日 For the grinding tests, a Loesche mill LM45 (table diameter 045 m) is used (Fig 2a) This pilot scale mill is a special development for ore grinding, which is reflected by several features The mill has four rollers, which are able to stress the particle bed with grinding pressures of up to 5000 kN/m 2Research of iron ore grinding in a verticalrollermill
.jpg)
An innovative approach for determining the grinding media system
2021年1月22日 The energy consumption of grinding is the subject of many studies, especially in the case of ball mills for grinding clinkers [8,9], fuels [10], iron ore [11], hematite ore [12], sulfide ore [13 2013年8月1日 Apart from these cost factors, one of the major unsolved problems in the optimal design of ball mills concerns the equilibrium media size distribution in the mill, which is determined by the rate at which makeup media is added to the mill, as well as the rate at which these grinding media are consumed (Austin and Klimpel, 1985)Reliable prediction of grinding media Consumption of steel grinding media in mills – A review2017年5月1日 Grinding is the preparation of material particle size, and its product's particle size composition will significantly affect the efficiency of subsequent separation operations and the economic and (PDF) Grinding process optimization — Featuring case CLUM series of ultrafine gypsum powder vertical grinding mills are a new type of ultrafine industrial ore grinding equipment that integrates grinding, grading, powder collection and conveying +17CLUM Ultrafine Vertical Grinding Mill
.jpg)
The effects of ore blending on comminution
2018年8月17日 The concept of ore blending is a very relevant notion in modern high tonnage production mines It is not only essential for the prolongation of the mine life of the concerned mine but as well as a 2019年8月14日 Ball mill is a common grinding equipment in concentrator : hm@gmail Toggle navigation • Peripheral ball mill: Discharge the ore through the periphery of the cylinder The wet ball mill forms the closed circuit operation with the hydraulic classification equipment in the closed circuit system • Dry The Ultimate Guide to Ball Mills Miningpedia2022年2月24日 mal power plants running on ball drum mill grinding systems In [2], it is stated that this share of energy is classified as very significant compared to the modern onesImproving the efficiency of the coal grinding process in ball drum Figure 1 presents the design of the clinker grinding system (closed circuit), which consists of a twochamber ball mill and the separator (Plasari and T heraska, 19 81) Cement clinker is usually Design of clinker grinding system; mill and separator
.jpg)
Control of ball mill operation depending on ball load and ore
ore and corresponds to the scheme, including medium and small stage ball grinding provides a comparative analysis of a wide range of ore processing steps and requires 515% energy in a selfgrinding mill [3] 1 Figure 2 Ball mill process control system using ACS (Adaptable Control System) Figure 2 shows that the input and output signalsTherefore, ease of replacement and regeneration is a major feature of the mill The MVR mill has a modern hydraulic system used in operation and for maintenance alike With this new type of roller suspension, the rollers can be swung out of the mill in a controlled way – for ease of replacing the onepart grinding roller tiresMVR vertical roller mill with planetary gearbox Gebr PfeifferRedevelopment of the large mill line 6 HighPressure Grinding Test work materials for grinding: cement clinker, iron ore, blue lead, diamond ore the roll movement (roll gap) is a function of the pressing force generated by the hydraulic system in relation to the reaction forces exerted by the processed materialHighPressure Grindingfrom the ores The grinding of ore is a highly energyintensive process [1–4] In this process, the size of the particle obtained depends on the energy consumption of the ball mill The major challenge encountered in the process of iron ore grinding is to maintain the desired product particle size distribution (PSD) with sufficientEstimation of Grinding Time for Desired Particle Size Distribution
.jpg)
Ball Mill Trunnion Bearing Lube System
2016年1月10日 On a 11’6” x 22’0” Ball Mill, the trunnion bearing lubrication system provides continuous low pressure flood oil for cooling and lubrication of the bearings, and high pressure oil for hydrostatic lift of the feed and 2024年5月31日 Lean magnetite resources in China are characterized by low iron grade, fine embedded particle size, complex composition, etc, which can only be utilized through complex beneficiation processes [1,2,3]With the increasingly serious problems of lowgrade, fine iron minerals, and difficulttotreat ore properties, the required particle size of ore grinding products High Pressure Grinding Roll and Magnetic Separation for Energy 2017年3月20日 An effect of a grinding method, that is ball mill and high pressure grinding rolls (HPGR), on the particle size, specific surface area and particle shape of an iron ore concentrate was studiedPhysicochemical Problems of Mineral Processing Download Table Chemical composition of rolling mill scale from publication: Production of sponge iron powder by reduction of rolling mill scale Rolling mill scale is a solid byproduct of the Chemical composition of rolling mill scale Download Table
.jpg)
An innovative approach for determining the grinding media system
2021年1月22日 Grinding operation is used extensively in the industry of beneficiation, metallurgy, chemical engineering, and electric power Assisted by the impact and abrasion between media (steel ball, steel rod, gravel, ceramic ball) and ore, the grinding operation reduces the particle size in the mill [[1], [2], [3]]To produce the qualified size and high liberation of operation (1) Structure parameters of grinding mill, including its specifications, model, aspect ratio, ore discharging method, and liner form (2) Various working parameters of grinding mill, including fraction of critical speed for grinding mill, filling rate for grinding mill, grinding concentration,grindingcycleload,etc(3)AndgrindOre Grinding Methods and Process of Ore GrindingOur cement hydraulic cylinders application include cement process such as vertical grinding mills, crushers, rotary kiln, and more In the systems used during cement grinding and instant cement cooling in the clinker cooling system, the processes are Cement Mill Hydraulic Cylinder Brant Hydraulics Corporation 2015年4月9日 The mill is normally used for grinding of ores The whole system is enclosed in a cylindrical casing The bearing units of one roller can move linearly and are pressed against the material bed by springs or hydraulic cylinders The pressures in Grinding Mills and Their Types – IspatGuru
.jpg)
Vertical roller mill for raw Application p rocess materials
Recently, the vertical roller mill having great grinding performance is widely applied to the raw material grinding process However, tube mill, which has about 30% poor grinding performance as power consumption, has been still used many existing cement plant The improvement of this tube mill grinding system is highly expected Descriptions2023年12月4日 A vertical roller mill is a grinding equipment for many industries such as minerals, cement, and ceramics It is also used to grind slag and nonmetallic ores The VRM decreases the number of equipment in the grinding circuit by combining the drying, crushing, grinding, and particle segregation in one unit Numerical Investigation of Vertical Roller Mill Operation Using