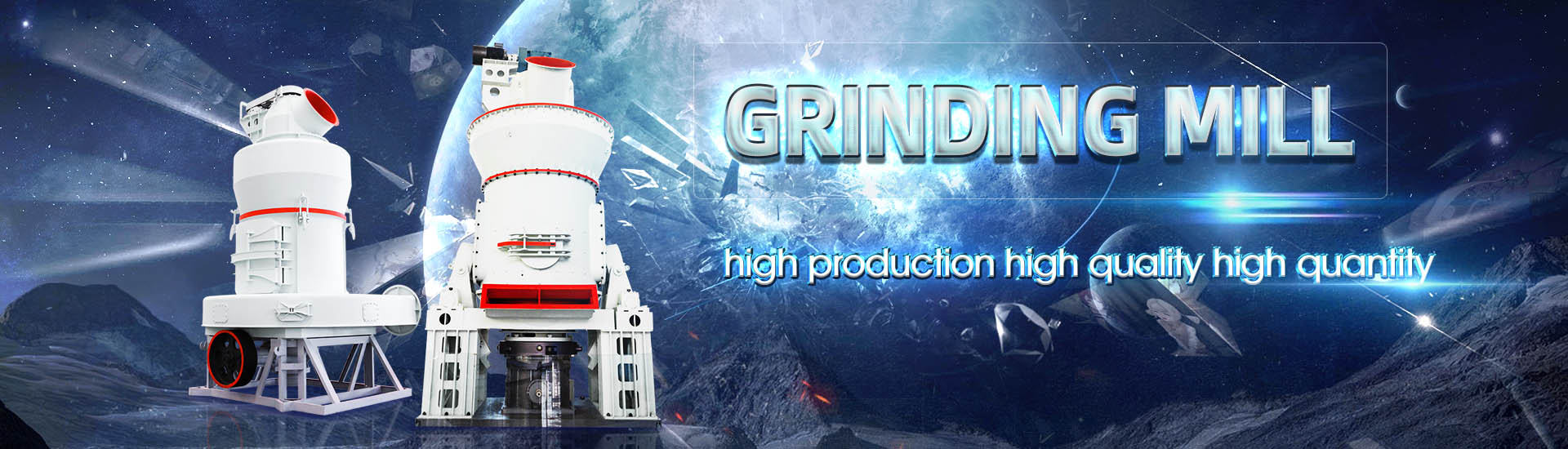
Bituminous coal powder grinding equipment process flow
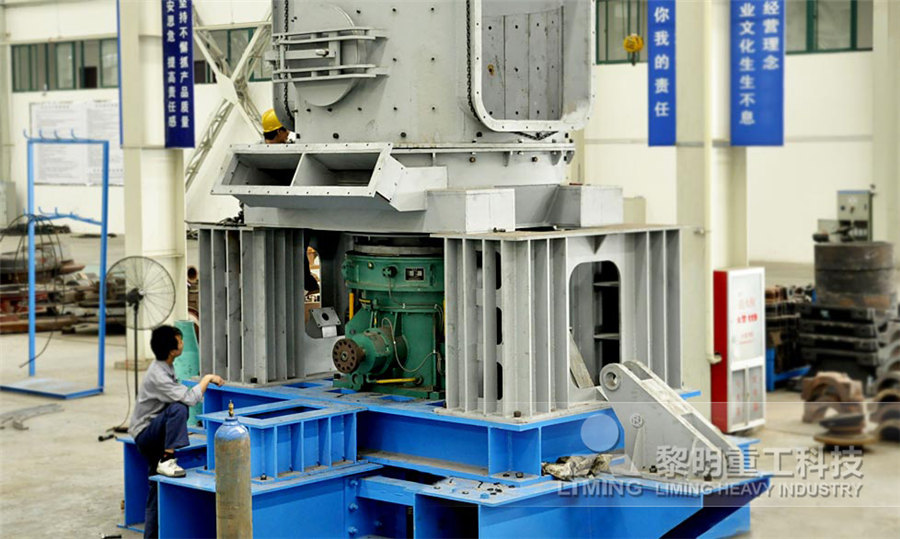
COAL VERTICAL MILL Xinxiang Great Wall Machinery Co, Ltd
Process introduction GRMC coal vertical mill produced by CHAENG adopts a special structure design and production technology, and the quality is up to the leading level in China It is the Vertical Coal Mill is specially used for ultrafine grinding of raw coal and bituminous coal materials in cement, power plants, iron and steel plants and other fields The GRMC coal vertical mill coal grinding machine CHAENGgrinding and drying coal for use in cement plants, power stations and in the steel industry In these plants very different coal types like anthracite, bituminous coal or lignite and also various COAL GRINDING IMPS: more than meets the eye Gebr PfeifferFour coal grinding devices three dry, one wet are discussed with the appropriate ancillary equipment for complete systems The mills examined are the: airswept ball mill, roll or ball Coal grinding technology: a manual for process engineers
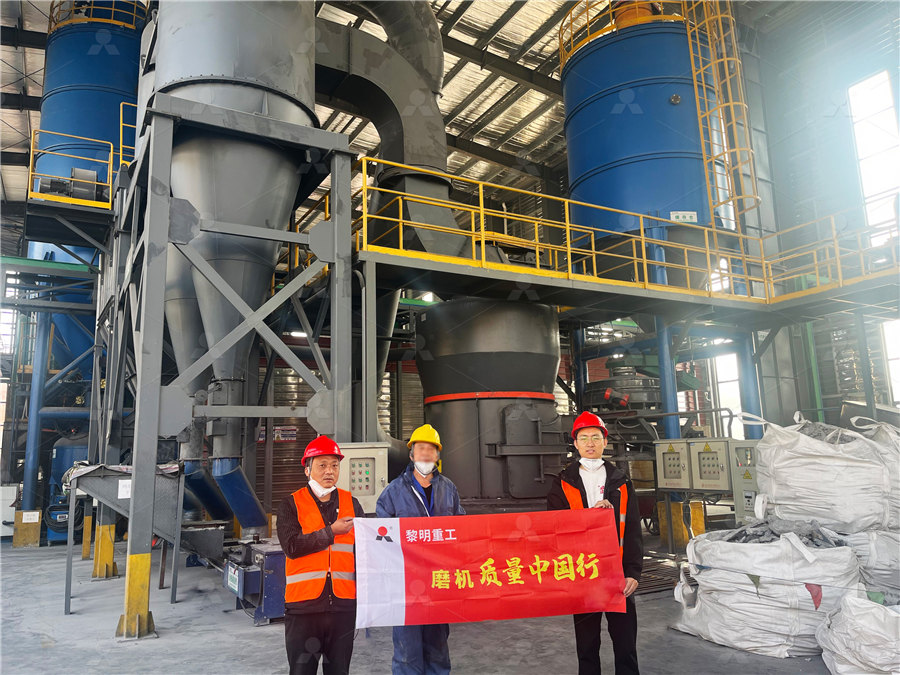
Grinding (Comminution) an overview ScienceDirect Topics
Grinding (Comminution) is the process of reducing rock or ore to a desired size to maximize mineral liberation without altering the chemical and physical properties of the material It 2020年8月12日 Obtained results indicate that grinding pressure, primary air (PA) temperature and mill motor current have a tendency to rise by increasing coal feeding mass flow rates for An investigation of performance characteristics and energetic Grinding of cement clinker and granulated blast furnace slag in roller grinding mills (vertical airswept grinding mills) is a technology introduced by Loesche The first use of a Loesche mill, 2 µm 5 µm Loesche2019年1月1日 Grinding process plays a crucial role in the variation of the physicochemical properties of raw coal In this paper, the different scales of pore structures changing with The effect of the grinding process on pore structures, functional
.jpg)
Application of Ni/MgO catalysts in the pyrolysis of
2024年2月26日 The bituminous coal pyrolysis process is one of the new coal chemical industries that introduces new te chnology and advanced generation processes, which have the advantages of a relatively simple 2013年5月15日 In this study, the effect of fuel type was investigated on the lignite and the bituminous coal and the petroleum coke samples using GÖltas cement factory (Isparta/Turkey) at batch grinding Comparisons of Dry Grinding Kinetics of Lignite, Bituminous Coal2022年2月24日 Before pulverized coal grinding, the wet coal needs to be dried first, and then sent to the grinding chamber of the main engine continuously and evenly for grinding The pulverized fine powder is classified by the classifier How is pulverized coal processed? SBM Ultrafine Coal grinding machine Coal grinding process flow Coal grinding is an essential process in the coal preparation process, energy industry, and cement manufacturing Coal grinding machines are used to achieve particle size reduction and surface area increase, which is crucial for burning efficiency and overall process effectiveness Here's an Coal grinding machine Coal grinding process flow NEWS
]@S0{UDKK%G24F3JGHC.jpg)
Coal grinding technology: a manual for process engineers
Then the coal undergoes pulverization which reduces the top size to 1/8'' and/or grinding which reduces the top size to 1 mm or less This handbook examines the intermediate and fine grinding of coal Four coal grinding devices three dry, one wet are discussed with the appropriate ancillary equipment for complete systems2012年2月1日 Semantic Scholar extracted view of "Evaluation of a laboratory rod mill when grinding bituminous coal" by Hoon Generation of low ash fine clean coal powder by autogenous grinding process powder technology S Sriramoju Powder Technology 2019; 14 Save Effects of flow rate, slurry solid content, and feed size distribution on Evaluation of a laboratory rod mill when grinding bituminous coal2024年1月23日 Gypsum powder is formed by a series of treatments on a large bulk of gypsum, with a finished particle size usually around 80325 mesh In terms of the entire production process of gypsum grinding, the equipment required mainly includes jaw crushers, Raymond grinders, etcGypsum Powder Grinding And Processing Plant Equipment2019年12月1日 Recovery of rare earth elements (REE) from coalrelated resources has recently received significant interest due to supply concerns and their key roles in critical industries and defenserelated technologies An integrated flowsheet consisting of sorting, crushing/grinding, physical separation, acid leaching, solvent extraction, and selective precipitation was designed Enhancement of a Process Flowsheet for Recovering and
.jpg)
Enhancement of a Process Flowsheet for Recovering and
2019年12月1日 Request PDF Enhancement of a Process Flowsheet for Recovering and Concentrating Critical Materials from Bituminous Coal Sources Recovery of rare earth elements (REE) from coalrelated 2024年11月1日 At a coal dosage of 10–15 %, the phosphorus content of DRI obtained from JS anthracite was lower than that of YJL bituminous coal due to the high SiO 2 content in YJL bituminous coal Under low reductant dosage, SiO 2 promoted the reduction of phosphoruscontaining minerals and decomposition of fluorapatite, resulting in an increased phosphorus Utilization of low metamorphic degree bituminous coal in direct 2024年1月11日 The 5step process to pulverize coal efficiently The coal pulverization process involves a precise sequence of steps Each is systematically designed to convert raw coal into a fine, efficient powder But How to Process Coal into Pulverized Coal in 5 Steps?Typical coal thermal power station Typical diagram of a coalfired thermal power station 1 The condensate flow rate at full load in a 500 MW plant is about 6,000 US gallons per minute (400 L/s) coal power plant process flow Capabuild
.jpg)
(PDF) MPS mills for coal grinding ResearchGate
2014年1月1日 This article analyzes the problems of perfecting grinding equipment for largescale production – cement, ore, coal An improved design of a ball mill, equipped with internal energy Exchange The dolomite powder processing adopts the grinding method, and its production line equipment includes jaw crusher, cone crusher, Raymond mill (main part), bucket elevator, electromagnetic vibrating feeder, classifier, pipeline The specific process flow of the device, Bituminous coal powder making plant 200,000 TPY bituminous coal;dolomite processing plant, dolomite grinding machine, dolomite powder the coal particles are dried and heated and the associated physical phenomena are then addressed 21 Moisture in coal Coal being fed into any combustion system normally contains moisture Typically, anthracite has moisture contents between 2 and 45% Bituminous and subbituminous coals have typical values of 1–122% and 141–31%, respectivelyFundamentals of pulverised coal combustion ICSCThe individual coals were mixed after grinding by varying the content of lower rank coal to generate three blends containing 25%, 50% and 75% by weight respectively The Hardgrove Grindability Index (HGI) was measured in accordance with standard procedures [7] The HGIs of the binary coal blends were determined after mixing 060118Effect of the grinding behaviour of coal blends on coal
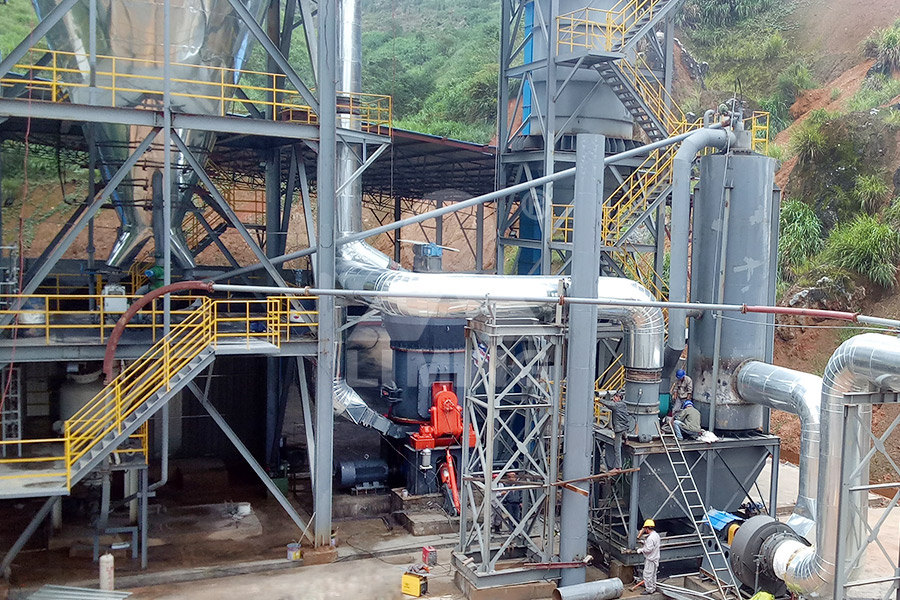
Coal mill pulverizer in thermal power plants PPT SlideShare
2012年11月17日 20 131Fineness Fineness is an indicator of the quality of the pulverizer action Specifically, fineness is a measurement of the percentage of a coal sample that passes through a set of test sieves usually designated at 50, 100, and 200 mesh A 70% coal sample passing through a 200 mesh screen indicates optimum mill performance The mill wear and Qualified fine powder is discharged with the air flow and collected by the system's powder collector The collected powder is the product of the ultrafine vertical grinding When the iron and other debris mixed with the material move to the edge of the grinding table with the material, they cannot be blown up by the wind due to their own weightLM Vertical Coal Mill, coal mill, coal mill price, vertical coal mill 2019年1月15日 Coal is a carbonaceous ore contains maceral and minerals with different properties Due to the presence of high mineral content, the mineral beneficiation process is adopted where the liberation of inorganic minerals plays key role As coal is a soft material, use of impact mills generates coal with homogeneous distribution of minerals In this paper, Generation of low ash fine clean coal powder by autogenous grinding 2022年2月24日 Improving the efficiency of the coal grinding process in ball drum mills at thermal power plants February 2022 EasternEuropean Journal of Enterprise Technologies 1(1 (115)):93105Improving the efficiency of the coal grinding process in ball drum
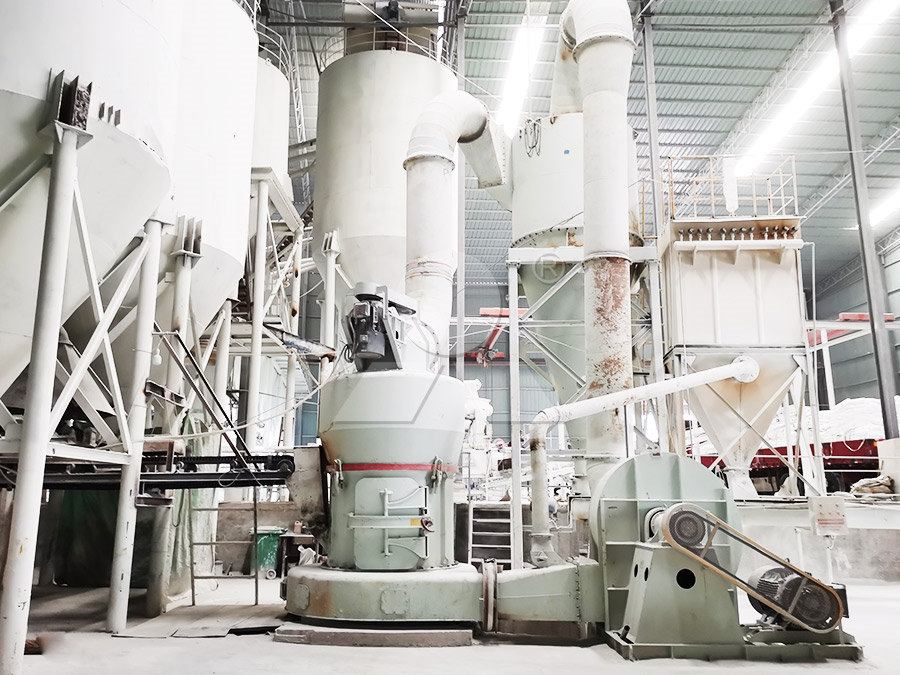
SolidSolid Operations and Processing PowderNotes
211 Section 21 SolidSolid Operations and Processing Bryan J Ennis, PhD President, EG Associates, Inc, and CEO, iPowder Systems, Inc; CoFounder and Member, Particle Technology Forum, American Institute of Chemical EngiCoal grinding mills are specialized equipment designed to break down coal into fine particles suitable for combustion The coal grinding process involves crushing and grinding coal into small particles, which are then heated to high temperatures in a furnace, producing steam that drives a turbine to generate electricityWhat is a Coal Grinding Mill2024年11月1日 The bituminous coal sample used in the experiment is shown in Fig 2 Bituminous coal is a type of coal with a moderate degree of coalification It has a carbon content of 80 %–90 %, a hydrogen content of 4 %–6 %, and an oxygen content of 10 %–15 %Study on suppression of bituminous coal explosion by inert powder Another Coal Powder Preparation Line Installed Successfully Recently, ZENITH vertical mill project team spread the good news that the LM130M coal mill complete system purchased by Vietnam local wellknown nonmetallic ore supply company from ZENITH has been completely installed only taking five months, and formally put into production in October 2015, the project Another Coal Powder Preparation Line Installed Successfully
.jpg)
process flow diagram of coal based power plant Grinding Mill
After coal comes out of the ground, it typically goes on a conveyor belt to a preparation plant that is located at the mining site The plant cleans and processes coal to remove dirt, rock, ash, sulfur, increasing the heating value of the coal During this coal processing, the used industrial equipment can be called coal processing equipments2023年1月1日 The selection of coals mills for power station applications is dependent on a number of process issues such as coal grindability [usually given as Hardgrove Grindability Index (HGI) or bond index], coal moisture, feed size, abrasion index, coal rank (lignite mills, eg, tend to be of very specific design), as well as some practical considerations such as plant layout, Advances in pulverised fuel technology: understanding coal grinding 2019年1月15日 Autogenous grinding is the process in which, the ore is grounded itself without any grinding media As the grinding media is harder than the ore, there is always high impact force applied to the ore, which leads to the breakage throughout the materials but not through the interfaces between the materials present in ore [21]For the present study, two different run of Generation of low ash fine clean coal powder by autogenous grinding 2024年2月1日 Recent years, highconcentration dust has become the greatest threat to coal mine safety production with increases in mining intensity [1, 2]Highconcentration coal dust forms a dust cloud in confined spaces such as the working faces of mines [3]After the dust is ignited with a certain amount of energy, the flame is easily accelerated and transformed into Effect of alkyl glycoside surfactant on the explosion characteristics
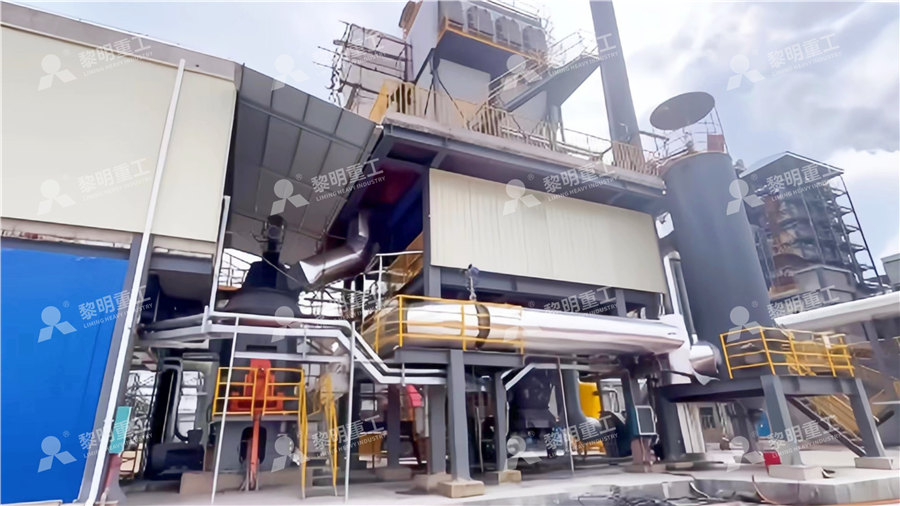
Grinding (Comminution) an overview ScienceDirect Topics
The process flow would be simplified as selective mining such as quartz, can also give rise to abrasion of the grinding equipment or of exposed surfaces in the combustion path the pore volume of coal increases 3953% and 1829% for tested Note: 1 The basic output in the table refers to the grinding capacity of the coal mill under the working conditions of high volatile bituminous coal 8% and low volatile bituminous coal 12%, with the GHI of coal power of 55, coal fineness of 785% passing the 0075mm sieveHP Bowl type millspower plant equipment2024年2月26日 The bituminous coal pyrolysis process is one of the new coal chemical industries that introduces new te chnology and advanced generation processes, which have the advantages of a relatively simple Application of Ni/MgO catalysts in the pyrolysis of 2013年5月15日 In this study, the effect of fuel type was investigated on the lignite and the bituminous coal and the petroleum coke samples using GÖltas cement factory (Isparta/Turkey) at batch grinding Comparisons of Dry Grinding Kinetics of Lignite, Bituminous Coal
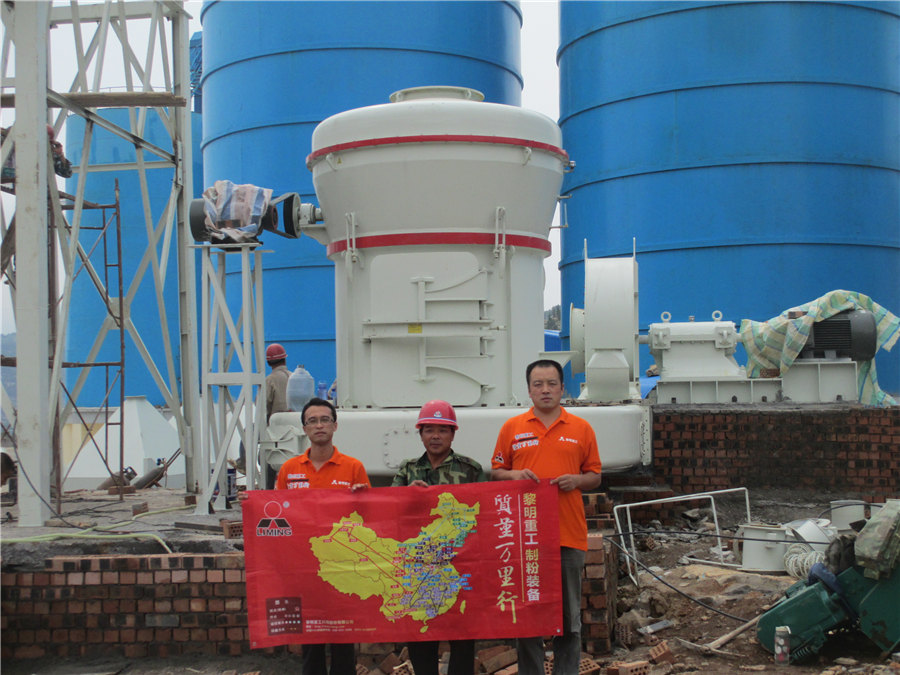
How is pulverized coal processed? SBM Ultrafine
2022年2月24日 Before pulverized coal grinding, the wet coal needs to be dried first, and then sent to the grinding chamber of the main engine continuously and evenly for grinding The pulverized fine powder is classified by the classifier Coal grinding machine Coal grinding process flow Coal grinding is an essential process in the coal preparation process, energy industry, and cement manufacturing Coal grinding machines are used to achieve particle size reduction and surface area increase, which is crucial for burning efficiency and overall process effectiveness Here's an Coal grinding machine Coal grinding process flow NEWSThen the coal undergoes pulverization which reduces the top size to 1/8'' and/or grinding which reduces the top size to 1 mm or less This handbook examines the intermediate and fine grinding of coal Four coal grinding devices three dry, one wet are discussed with the appropriate ancillary equipment for complete systemsCoal grinding technology: a manual for process engineers2012年2月1日 Semantic Scholar extracted view of "Evaluation of a laboratory rod mill when grinding bituminous coal" by Hoon Generation of low ash fine clean coal powder by autogenous grinding process powder technology S Sriramoju Powder Technology 2019; 14 Save Effects of flow rate, slurry solid content, and feed size distribution on Evaluation of a laboratory rod mill when grinding bituminous coal
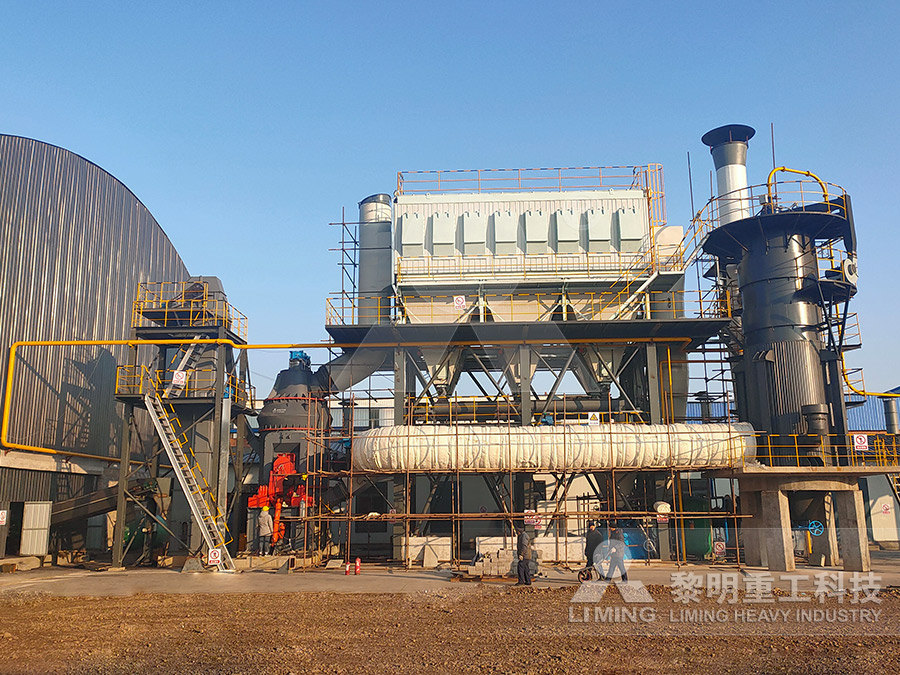
Gypsum Powder Grinding And Processing Plant Equipment
2024年1月23日 Gypsum powder is formed by a series of treatments on a large bulk of gypsum, with a finished particle size usually around 80325 mesh In terms of the entire production process of gypsum grinding, the equipment required mainly includes jaw crushers, Raymond grinders, etc2019年12月1日 Recovery of rare earth elements (REE) from coalrelated resources has recently received significant interest due to supply concerns and their key roles in critical industries and defenserelated technologies An integrated flowsheet consisting of sorting, crushing/grinding, physical separation, acid leaching, solvent extraction, and selective precipitation was designed Enhancement of a Process Flowsheet for Recovering and 2019年12月1日 Request PDF Enhancement of a Process Flowsheet for Recovering and Concentrating Critical Materials from Bituminous Coal Sources Recovery of rare earth elements (REE) from coalrelated Enhancement of a Process Flowsheet for Recovering and 2024年11月1日 At a coal dosage of 10–15 %, the phosphorus content of DRI obtained from JS anthracite was lower than that of YJL bituminous coal due to the high SiO 2 content in YJL bituminous coal Under low reductant dosage, SiO 2 promoted the reduction of phosphoruscontaining minerals and decomposition of fluorapatite, resulting in an increased phosphorus Utilization of low metamorphic degree bituminous coal in direct