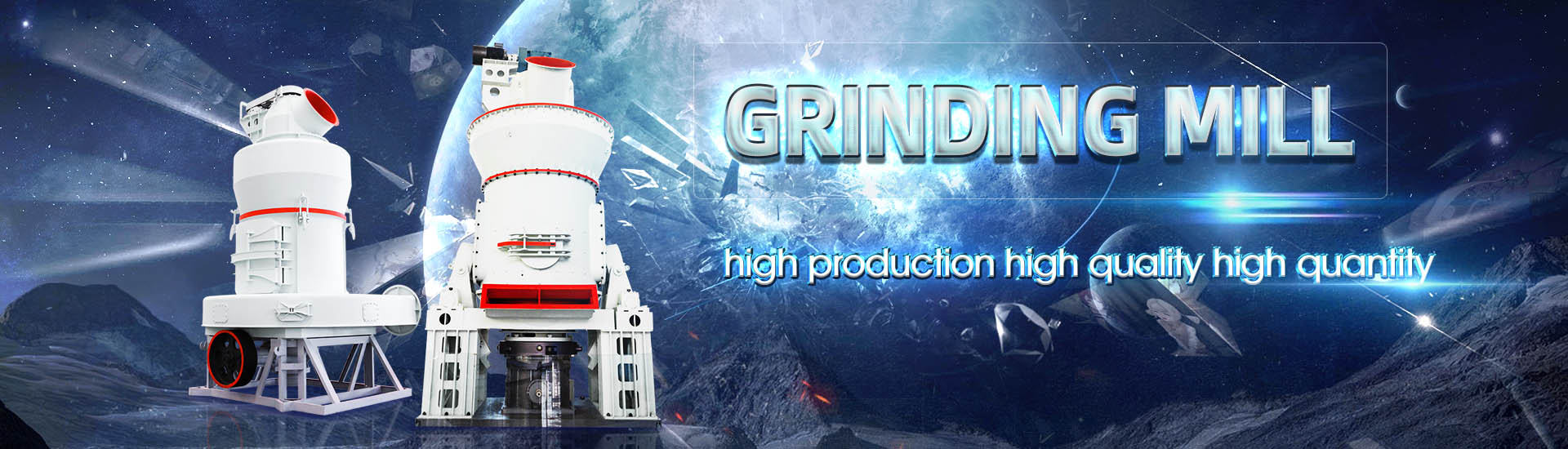
EM coal mill installation plan
.jpg)
010Method Statement of Coal Mill Instattalation PDF
This document provides a method statement for installing a coal mill at a project site It outlines the general components and purpose of the coal mill It then describes the responsibilities of personnel overseeing the installationFully automatic sampling system Coal to be installed in the CHP Coal from conveyor A4B4 will be collected by the sampler at pre determined intervals by cutter type samplers to assess the quality of the coal being dispatched The coal samplers will be installed on the conveyors A4B4 at suitable location 127 OTHER ASSOCIATED SYSTEMSPLANNING, DESIGN, SUPPLY, ERECTION, TESTING AND Ofering high reliability, low installation costs and a wide range of sizes, the ATOX grinds and dries all types of coal – while providing excellent economy in terms of specific energy consumption The ATOX coal mill is suited for various installation types, whether inert or noninert, and direct or indirect firing systemsATOX COAL MILLLoesche designs, plans and constructs everything from individual machines to turnkey drygrinding installations for all solid fuels Loesche is certified in accordance with EN ISO 9001, and our grinding plants meet both national and international safety regulationsLOESCHEMILLS
.jpg)
en/162/vertical coal mill installation planmd at main
Contribute to lbsid/en development by creating an account on GitHubvertical roller grinding mills for grinding: • Coal • Cement raw material • Clinker / granulated slag • Industrial minerals, and • Ores The core elements of these plants are the Loesche vertical mills for drygrinding the abovementioned grinding stock Loesche has PROCESS OPTIMISATION FOR LOESCHE GRINDING PLANTSRaw Mill Baghouse Fan Kiln Exhaust Fan Clinker Cooler Fan Coal Mill Fan Typical Data volume flow: 100450 m 3/s temperature: ca 150 °C mech design plan and calculate the suitable fans, components and systems Installation of wear protection (composite hardfaced plates) with a hardness of aboutFans in Cement Plants BrownleeMorrow CompanyCoal grinding is a critical process in various industries, particularly in power generation and cement production However, the process involves significant safety risks due to the combustible nature of coal dust and the mechanical hazards posed by the operation of the mill Ensuring safety during coal grinding is essential to prevent accidents, exAspects of Coal Mill Safety Coal Mill Safety, Explosion and Fire
.jpg)
Ball Mill Maintenance Installation Procedure
2016年10月20日 On Mill Installation and Maintenance Before starting the erection of the mill, adequate handling facilities should be provided or made available, bearing in mind the weights and proportions of the various parts and O serviço do Google, oferecido sem custo financeiro, traduz instantaneamente palavras, frases e páginas da Web do português para mais de cem outros idiomasGoogle TradutorThe document is a technical manual that describes a coal mill CO gas analyzing system It provides instructions for installing, operating, and maintaining the system The system samples gas from a coal mill outlet, pumps it to a measuring chamber with an infrared gas analyzer, and is able to detect carbon monoxide levels to monitor for fires in the mill The manual covers Coal Mill CO Analyzer Codel ManualThe ATOX mill will grind and dry coal containing more than 20% moisture in one operation The possibility of customersupplied parts, along with the low civil costs that accompany compact mill installation, add to the excellent economy of the ATOX coal mill Working principles The raw coal enters the mill via a rotary sluice and feed chuteATOX COAL MILL
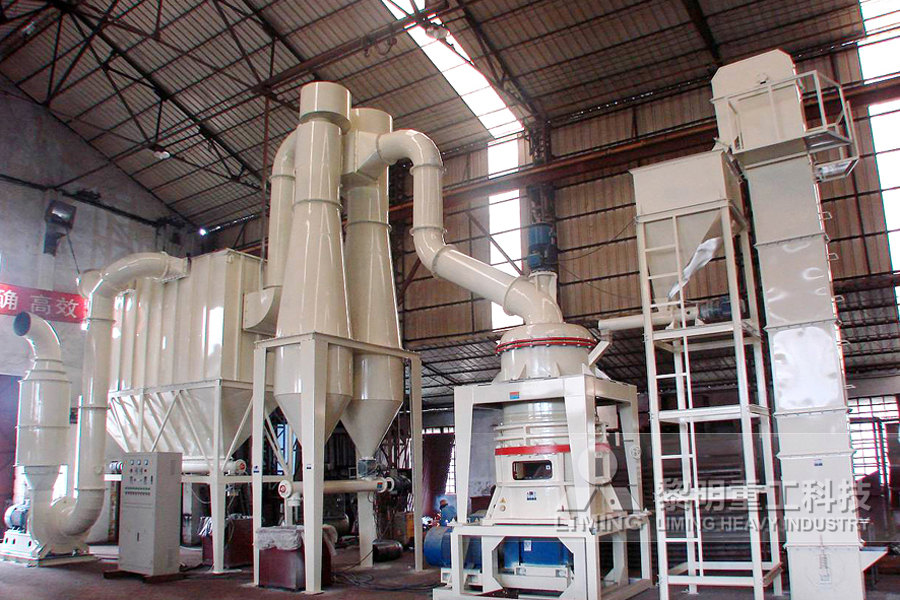
Analysis of the Coal Milling Operations to the Boiler Parameters
2020年4月2日 A differential pressure measurement was install ed Coal mill motor power (kW) 0 4171 4548 4390 4586 The key input to the coal fired power plan t is the coalCOAL MILL COAL MILL Derek Stuart, AMETEK Land, and Todd Collins PE, Hoosier Energy, US, discuss available techniques for detecting early signs of mill fires and explosions Hoosier Energy Merom power plant Reprinted from World Coal March 2014 March 2014 COAL MILL Land Instruments InternationalOur ATOX® Coal Mill has large rollers with great grinding capability of virtually all types of raw coal The rollers work harmoniously with a highlyefficient separator and feed sluice to consistently and reliably deliver coal meal to your desired fineness and moisture levelATOX® Coal Mill FLSmidth CementOverhaul Procedure for Coal Mill Free download as Powerpoint Presentation (ppt / pptx), PDF File (pdf), Text File (txt) or view presentation slides online The document outlines the steps for an overhaul procedure of a coal mill It involves 21 steps to remove, inspect, replace, and reinstall components Key steps include removing the mill cover, inspecting and replacing grinding Overhaul Procedure For Coal Mill PDF Scribd
.jpg)
Roller Mills Installation Report Williams Crusher
Blast Furnace Injection at ArcelorMittal Granular Coal Injection Preparation System Two (2) Williams DF90 Roller Mill Systems with patented inert gas drying reduce 2" x 0 high volatile bituminous coal with 105% moisture, to minus 4 Grinding of coal, petcoke, clay, limestone, quicklime, Installation and commissioning; Technical service and maintenance; Service contracts for mills and grinding plants; MPS 200 BK coal mill, Krimzement Bakhchisarayski, Coal mill, gypsum mill, clay mill, etc Pfeiffer MPS millsAs a leading innovator with power station technologies – and other industries that need to process coal, Magotteaux is the ideal firm to turn to when seeking cuttingedge vertical coal mill technologyOur tires and tables mean that vertical coal mills can run more efficiently than ever beforeIn many cases, there is a compromise that needs to be made between the length of Vertical Coal Mill Magotteaux2019年9月28日 The use of condensers in air conditioning units is more common in largecapacity units than in ones with a smaller capacity Air conditioning provides comfort and freshness to an airconditioned room(PDF) Detecting classifiercoal mill damage using a
.jpg)
Air Swept Coal Mill Coal Mill In Cement Plant AGICO GROUP
Air Swept Coal Mill Working Principle First, the raw coal is fed into the feed chute by the feeding device Then, the hot air with a temperature of about 300 ℃ enters through the air intake pipe and begins to dry the raw coal while they are fallingCOAL HANDLING Protecting the coal mill by monitoring CO and O 2 CO and O 2 measurement in the coal mill is important for early warning of a smoldering fire and/or a leak in the inerting system The MKAS analyzer system equipped with an explosionprotected sampling probe is the ideal solution for this The MKAS can be configured to sequentiallyPOWER SICKHRM1700MVRM Free download as PDF File (pdf), Text File (txt) or read online for free The document provides installation and operation instructions for the HRM1700M Vertical Roller Coal Mill It describes the mill's technical parameters, components, structure, working principles, and installation process Key aspects include grinding rollers that can be removed for Operation Manual: HRM1700M Vertical Roller Coal Millmills A typical con trol strategy for a coal mill is based on receiving a coal feeder reference The con trol loop for the coal feeder is used to trac k this reference while feedbac k and feedforw ard loops are used to main tain the primary air o w according to the mill load line, as w ell as the dynamic classi er sp eed in case it is availableCoal Mill Modeling for Monitoring and Control
.jpg)
Steel Mill track plan ModelRailroadForums
2010年4月9日 I don't plan on having the entire series due to space, I don't want to get rid of my ethanol tanks I did some more research, and I have the manuals for the structures, and I have all the correct demensions now One thing I just realize was the rolling mill needs 3 tracks So I did some tweaking to the plan I'm ordering the book as wellThe four most common coal pulverizers types are: BallTube Mills This type of mill consists of a rotating tube filled with cast alloy balls Coal is introduced through two hollow trunnions on each side of the tube As the tube rotates, the balls tumble onto the coal, crushing and pulverizing it Coal Pulverizer – Power Plant Pall Corporation2020年8月12日 Coalfired power plants play an important role in the worldwide power generation and Vertical Coal Mill (VCM) is equipment for grinding and pulverizing coal into micron sizeAn investigation of performance characteristics and In this article, we will discuss the work that needs to be done after the installation of a ball mill and the precautions that need to be taken to ensure safe and efficient operation Inspection of the ball mill After installing a ball mill, it is important to conduct a thorough inspection of the equipment to ensure everything is in orderBall Mill Installation Essential Work and Precautions
.jpg)
Coal mills for all requirements Gebr Pfeiffer
Hard coal is a sedimentary rock which was formed by deposition and carbonization of plant remains It is hard and resistant More than 50% of its weight is made up by carbon Therefore it is classified as highrank coal for controlling the coal flow at the discharge of a centrifugal classifier The model was based on an existing installation of a Riley Power standalone classifier, and included ductwork from the discharge of the ball tube mill up to the classifier and coal pipes The full length of the coal pipes was replaced by13045 Coal Distributor Paper:Layout 1 Babcock PowerThe information gained will include coal pipe balance, coal fineness, air/coal ratios, as well as the condition of the grinding components, mill throat, classifier, springs, and other components This information is then provided to the Power Plant in a comprehensive report and is used as a tool to determine which modifications are required to meet their specific target or performance goalsCE RB Coal Mill Modernization Components and ServicesRequest PDF On Nov 11, 2023, G Khankari and others published Utilization of mill rejects with biomass pellets in the existing coal power plants a novel approach towards sustainability fuel Utilization of mill rejects with biomass pellets in the existing coal
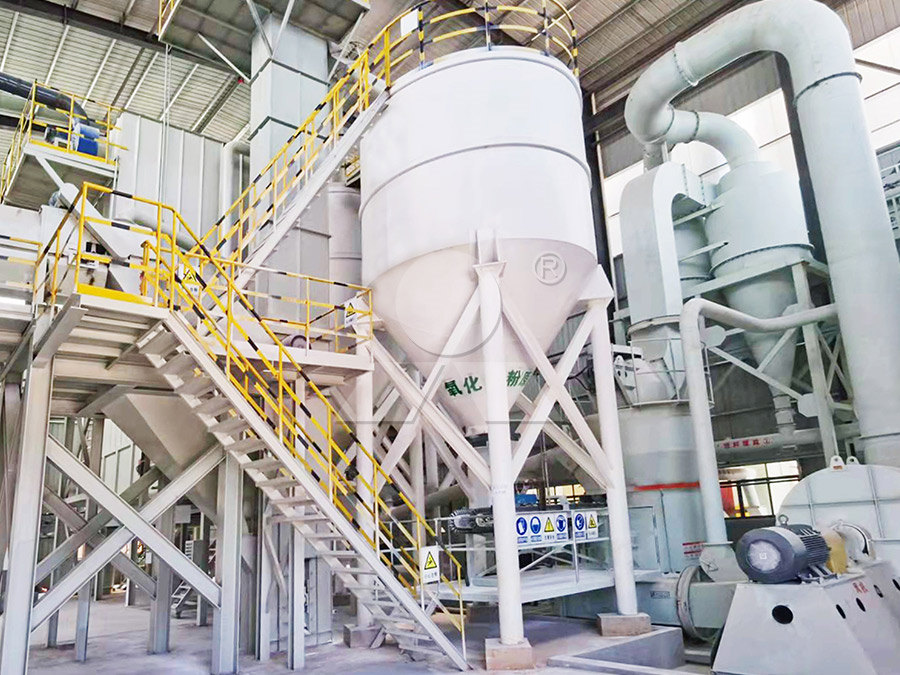
Loesche Grinding Technology for the Power Industry
1980 Delivery of first modular coal mill (LM 263 D) 1965 Construction of first pressure mill (LM 122 D) 1961 Introduction of hydraulic spring assembly system 1953 th500 coal mill plant sold worldwide 1927 First Loesche coal mill delivered for the Klingenberg power station in Berlin We have been successfully involved in the grinding of solid2 IEA Coal Research A/C air to cloth ratio BACT Best Available Control Technology 414 Mill inerting 26 42 Coal and air distribution system 27 5 Primary pollution control 30 51 Process optimisation 30 Retrofitting is limited to the installation ofProspects for upgrading coalfired power plants ICSC2021年2月1日 Installation ca pacity of coalfired power In 2 016 and 2017, the i nstal led capacity of coalfired power is s lightly higher than the planned values H owe ver, due to the effect of regulation Comparative analysis of actual and planned utilization hours of coal Mill Plant (Coal meal) Process Instructions Nyumba Ya Akiba, DR Congo Process Instruction T e x t r e f e r e n ce is m a d e t o t h e f o llo w in g in st r u ct io n m a n u a l: Precaution when using coal and lignite (doc no 12861) Date: Created by: Pages: 30072015 BIDE 24 Doc No: 10 Mill Plant, coal meal Process Instruction: List of con t e nt s: 1Mill Plant (Coal meal) Process Instructions Academia
.jpg)
Fans in Cement Plants BrownleeMorrow Company
Raw Mill Baghouse Fan Kiln Exhaust Fan Clinker Cooler Fan Coal Mill Fan Typical Data volume flow: 100450 m 3/s temperature: ca 150 °C mech design plan and calculate the suitable fans, components and systems Installation of wear protection (composite hardfaced plates) with a hardness of aboutCoal grinding is a critical process in various industries, particularly in power generation and cement production However, the process involves significant safety risks due to the combustible nature of coal dust and the mechanical hazards posed by the operation of the mill Ensuring safety during coal grinding is essential to prevent accidents, exAspects of Coal Mill Safety Coal Mill Safety, Explosion and Fire 2016年10月20日 On Mill Installation and Maintenance Before starting the erection of the mill, adequate handling facilities should be provided or made available, bearing in mind the weights and proportions of the various parts and Ball Mill Maintenance Installation ProcedureO serviço do Google, oferecido sem custo financeiro, traduz instantaneamente palavras, frases e páginas da Web do português para mais de cem outros idiomasGoogle Tradutor
.jpg)
Coal Mill CO Analyzer Codel Manual
The document is a technical manual that describes a coal mill CO gas analyzing system It provides instructions for installing, operating, and maintaining the system The system samples gas from a coal mill outlet, pumps it to a measuring chamber with an infrared gas analyzer, and is able to detect carbon monoxide levels to monitor for fires in the mill The manual covers The ATOX mill will grind and dry coal containing more than 20% moisture in one operation The possibility of customersupplied parts, along with the low civil costs that accompany compact mill installation, add to the excellent economy of the ATOX coal mill Working principles The raw coal enters the mill via a rotary sluice and feed chuteATOX COAL MILL2020年4月2日 A differential pressure measurement was install ed Coal mill motor power (kW) 0 4171 4548 4390 4586 The key input to the coal fired power plan t is the coalAnalysis of the Coal Milling Operations to the Boiler ParametersCOAL MILL COAL MILL Derek Stuart, AMETEK Land, and Todd Collins PE, Hoosier Energy, US, discuss available techniques for detecting early signs of mill fires and explosions Hoosier Energy Merom power plant Reprinted from World Coal March 2014 March 2014 COAL MILL Land Instruments International
.jpg)
ATOX® Coal Mill FLSmidth Cement
Our ATOX® Coal Mill has large rollers with great grinding capability of virtually all types of raw coal The rollers work harmoniously with a highlyefficient separator and feed sluice to consistently and reliably deliver coal meal to your desired fineness and moisture levelOverhaul Procedure for Coal Mill Free download as Powerpoint Presentation (ppt / pptx), PDF File (pdf), Text File (txt) or view presentation slides online The document outlines the steps for an overhaul procedure of a coal mill It involves 21 steps to remove, inspect, replace, and reinstall components Key steps include removing the mill cover, inspecting and replacing grinding Overhaul Procedure For Coal Mill PDF Scribd