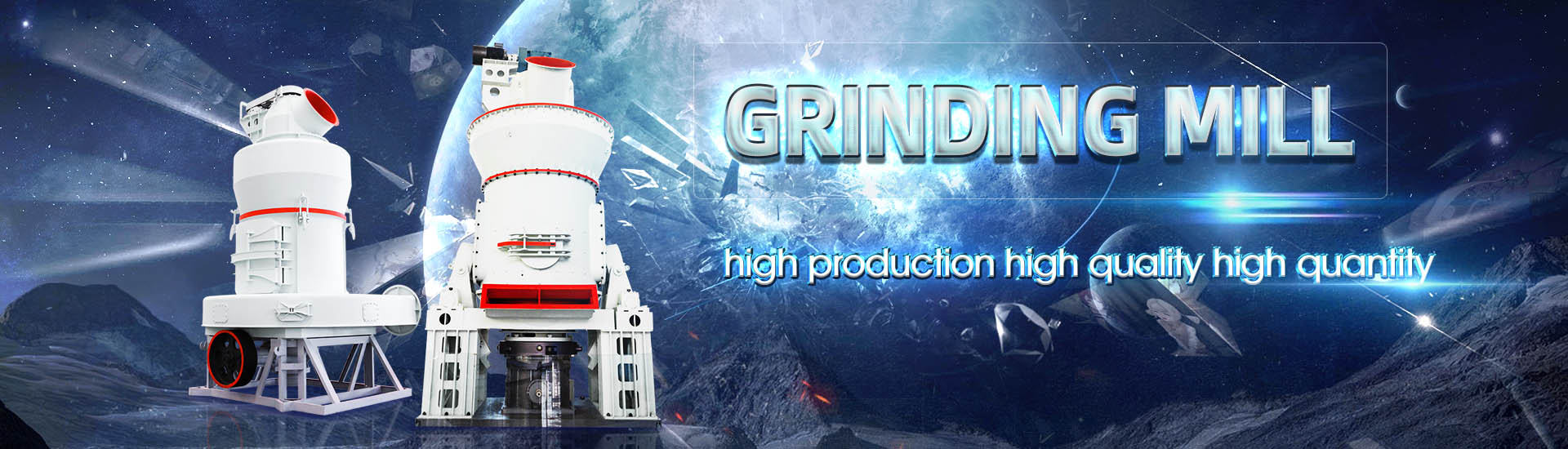
How to change the lining of ore mill
.jpg)
The Selection and Design of Mill Liners 911 Metallurgist
Examples of good and bad liner design are given, followed by a rigorous approach to liner design based on the best technology available, combined with experience and logical engineering thinking Methods of monitoring the progressive wear of liners, and relating this to the Choice of mill lining A mill lining should be optimized to suit each specific mill Choosing an appropriate type of lining and design in terms of lining material, thickness and profile is vital for Three factors that determine the wear life and performance of mill 2015年8月6日 The amount of unground material will slowly increase until the mill can no longer grind the bigger ore When this happens the liners will have to be changed If you ever have to start up a mill that has had a complete liner Grinding Mill Liners 911Metallurgist– Maximise liner life by protecting with mill lifters – Prevent ball breakage impact on toe of charge – Check profiles regularly to accurately predict change outThe Selection Design and Application of Mill Liners for Large Wet
.jpg)
Taking your grinding to the next level Mill lining solutions for
Our ability to combine different liner materials inside the same mill and in different sections enables us to further optimize your grinding process Using each lining material where it 2020年10月1日 When converting a mill from steel to rubber liners, the design must be changed from such familiar steel liner shapes as wedge bars and plates, wave liners, and shiplap to take advantageA Review on Current Mill Liner Design and Integrating the wear rates of liners from the actual measurement of the changes in liner profile over milling time and also using laserbased thickness gauging technology would assist in [PDF] The selection and design of mill liners Semantic Scholar2006年1月1日 When converting a mill from steel to rubber liners, the design must be changed from such familiar steel liner shapes as wedge bars and plates, wave liners, and shiplap to take advantage(PDF) Selection and design of mill liners ResearchGate
.jpg)
Semiautogenous mill liners: Designs, alloys, and maintenance
Liner maintenance procedures ranging from laydown area in plant design, proper mill shutdown methods, to installation and bolt tightening complete the equation to yield optimum generate both thrown and cascading ballmilling actions with shell linings shaped to lift and to throw alloy steel grinding balls of up to 150 mm (6 in) in diameter These actions apply Semiautogenous grinding (SAG) mill liner design and developmentdesign to maximize mill availability The shell lining has a major influence on grinding efficiency It transforms the mill rotation into charge motion, and both profile and spacing must be selected to suit each specific mill When designing a shell lining, the type of ore, mill size and speed, maintenance schedules, safety,Taking your grinding to the next level Mill lining solutions for 2015年8月6日 The amount of unground material will slowly increase until the mill can no longer grind the bigger ore When this happens the liners will have to be changed If you ever have to start up a mill that has had a complete liner Grinding Mill Liners 911Metallurgist
.jpg)
Types And Applications Of Mill Liners FC Mill Liners
Let’s explore the various types of mill liners and their practical applications in greater detail Mill Lining System A mill is a vital tool for grinding and blending solid or hard materials through shear, impact, and compression methods 2016年10月20日 Am sure your Ball Mill is considered the finest possible grinding mill available When lining the shell, start with the odd shaped pieces around the manhole opening if manholes are furnished nevertheless there is a certain amount of seasoning and dimensional change which goes on in the type of metals usedBall Mill Maintenance Installation Procedure 911Metallurgist2020年9月7日 Damaged lining of the barrel and ball mill Among other things, these particular mill liners also prevent wear and tear However, if during your regular inspections you begin to notice that the barrel’s and ball mill’s lining has begun to damage, it is a clear indication you need, or soon may need to replace the ball mill linerWhen to change ball mill liners? Qiming Machinerymill is equal to twice the number of the feet in the mill shell diameter (eg, a 34ftdiameter mill shell would have 68 shell lifters) This is also called a 2D shell lining Eliminating some shell lifters increases the volume of charge between the lifters (“the bucket”) and the total charge that should be lifted in eachSemiautogenous grinding (SAG) mill liner design and development
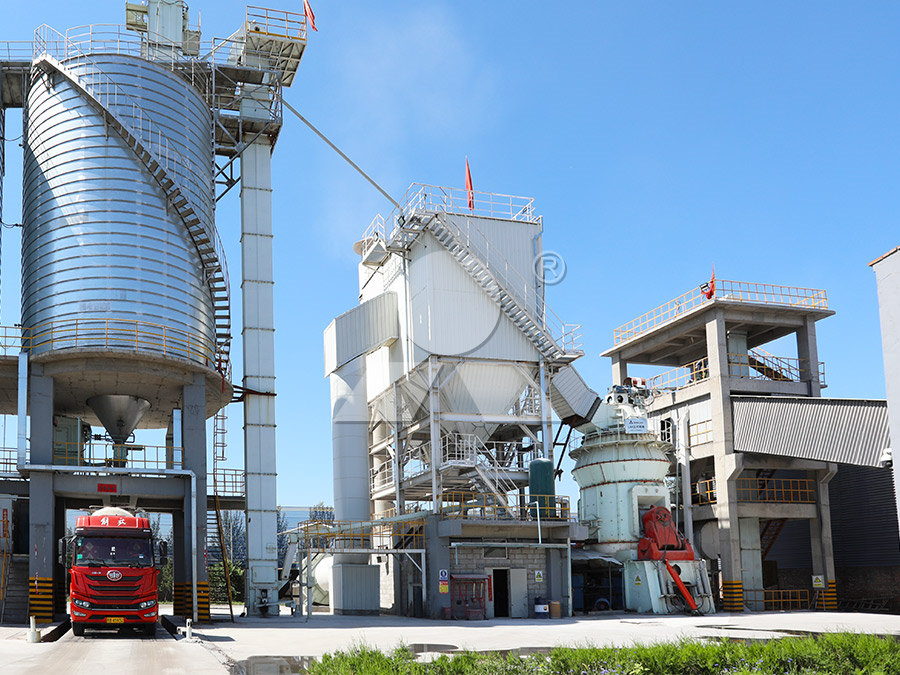
The Selection Design and Application of Mill Liners for Large Wet
> Engineering approaches have highlighted mill performance with mill modelling and the use of improved materials > Liner design ,with the advent of large diameter SAG mills, the issues of design, selection, monitoring and evaluation of mill performance is critical > Mill trajectory modelling can be used to great effect in improving liner design2017年10月25日 With particular reference to mill size, it is apparent that a change in diameter in a large mill is relatively far less significant than the same change in 911 Metallurgist is a trusted resource for practical insights, solutions, and support in mineral processing engineering, helping industry professionals succeed with proven expertise Recommended Ball Mill Speed Liner Recommended Ball Mill Speed Liner Configuration2016年8月29日 Some lining parts in a mill are more exposed to wear than others, and the wear life of the mill lining components can therefore be very different This means that fully utilizing the wear life of all lining parts in a mill may not be the most optimal solution since it can lead to added downtime and production lossBalance the wear life of your mill lining parts MetsoTest the Mill: Once the new liners are in place, start up the mill and test it to ensure that it is functioning properly Monitor the mill’s performance over time to ensure that the new liners are working effectively Tips for Prolonging the Lifespan of Ball Mill Liners Here are a few tips to help prolong the lifespan of ball mill liners:A Guide to Ball Mill Liner Replacement and Maintenance
.jpg)
Mill Lining Systems FluidHandling Trelleborg
Trelleborg has been providing mill lining systems since 1920 The focus is on working with our customers to provide incremental improvement to enhance mill availability, increasing efficiency and reducing energy consumption Full lining 2016年1月5日 There are many different designs and styles of ball mill liners As with grinding balls local economics and ultimately operating costs determine the best resulting in the lowest cost per ton of ore ground The liner contours Ball Mill Liner Design 911MetallurgistWhether you are operating a SAG, Rod or Ball mill, the mill liners used influence significantly how well you'll achieve your targets In this 16page eBook, you’ll discover: What factors determine the wear life of mill liners; How to increase 3 factors that determine the wear life and performance SAG 2019 Conference, September 22–26, 2019, in Vancouver, BC, Canada Development of SAG liners has always been of considerable interest to mill operators as liners significantly affect plant performance (throughput, grind size), material costs and plant downtime Thus, operators commonly trial The design and evolution of SAG mill liner trails Hatch Ltd

Customised Vulco® Mill Lining Systems Weir
Depending on your goals and application, we offer a range of premium composite and rubber mill lining solutions for rod, ball, AG and SAG mills Rubber mill lining is predominately used for smaller secondary and tertiary ball milling (regrind), whereas our composite mill liners (made from one or more materials) are used for heavyduty primary and secondary AG / SAG mill lining to respond to changes in ore properties in real time For example, if the properties of the ore change during mill operation, the adaptive control system can automatically change the operation parameters of the mill, generating signals and influencing the ball load and excitation current of the synchronous motor to achieve the required performanceImprovement of methods to ensure energy efficiency of ball mills 2023年8月21日 The grinding process in ball mills is notoriously known to be highly inefficient: only 1 to 2% of the inputted electrical energy serves for creating new surfacesImprovement of methods to ensure energy efficiency of ball mills 2020年1月1日 Keywords semiautogenous grinding mill, lining, modeling of lining wear processes, factors of influence on the process of wear of lining 1 Introduction The process of destruction (grinding and The study of the lining layer abrasing wear in the semiautogenous
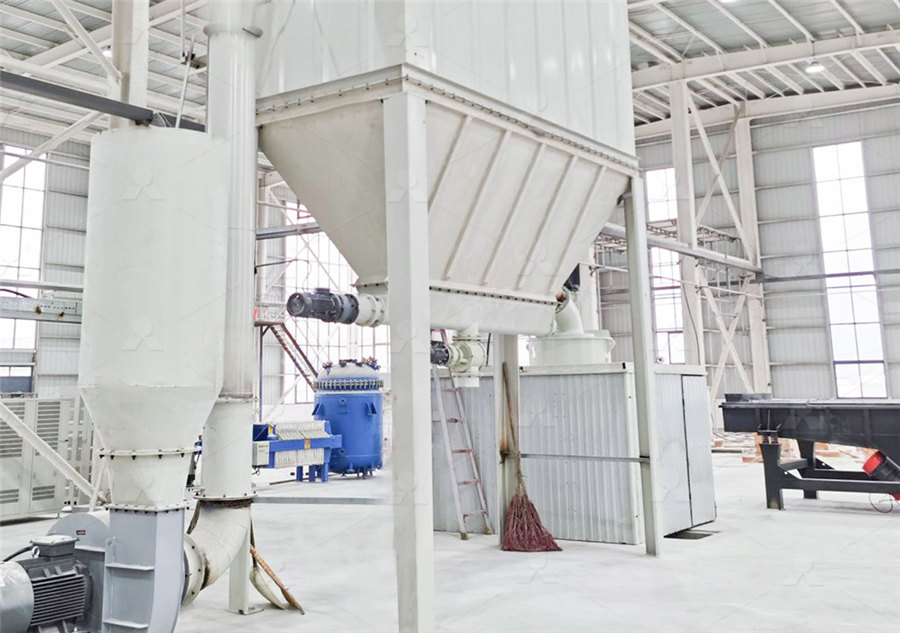
The design of rotarymill liners, and their backing materials
rate of the lining in a large ROM mill The 4,8 by 12,2 m mill ran at 81 per cent of the critical speed, and was lined with 24 rows of austenitic manganese steel (AMS) grids The mill was charged with 5 to 10per cent 100 mm balls, and was run at 45 per cent charge filling It was advantageous to use a mill of slower speed since this is suited6 Advanced mill liner wear measurement and prediction services Advanced mill liner wear measurement and prediction services 7 Basic summary: Mill volume calculation Reline date (±7 days accuracy) Minimum remaining liner thickness Liner wear trend Detailed report: Liner longitudinal and crosssectional wear profi lesAdvanced mill liner wear measurement and prediction services2023年4月23日 Comminution includes the blasting, crushing, and grinding of ore to liberate valuable mineral particles very small variation of shoulder positions with a change in mill speed(PDF) Grinding Media in Ball MillsA ReviewDIFFERENT MILLS REQUIRE DIFFERENT AMOUNTS OF MEDIA •BASED UPON WORKING VOLUME OR TOTAL VOLUME •Mills such as the Immersion Mill have a fixed amount determined by size of the basket •Steel Ball Mill 333% •Open Head Sand Mill 3545% •Ceramic Pebble Ball Mill 50% •Dry Grind Batch Attritor 4560% •Wet Grind Batch Attritor 3845% •Continuous How to Choose the Correct GRINDING MEDIA PCI Mag
.jpg)
Iron Ore Processing: From Extraction to Manufacturing
2024年4月26日 The final stage in iron ore processing is ironmaking, where the iron ore is transformed into molten iron through a process called reduction The most common method of ironmaking is the blast furnace route In a blast 2017年3月4日 Ball mills are used for wet grinding iron ore, g old/copper ore, nickel ore and other ores, as wel l as lime/limestone for flue gas desulphurisat ion systems, coal and other raw materials Rod mill :SIZE REDUCTION BY GRINDING METHODS ResearchGate*Corresponding author: The study of the lining layer abrasing wear in the semiautogenous grinding mill Mykola Sokur1, Volodymyr Biletskyi2,*, Mykhailo Fyk2, Oleksandr Fyk3, and Igor Zaselskiy4 1Kremenchuk Mykhailo Ostrohradskyi National University, Marketing Department, 20 Pershotravneva Str, Kremenchuk, 39614, Ukraine 2National Technical The study of the lining layer abrasing wear in the semi Vulco® mill lining components incorporate features that have been engineered for severe ore and milling characteristics 9 Pulp discharge designs Pulp discharge segments, designed by inspections can identify changes occurring in the mill lining patterns, which can subsequently be linked to site performanceMinerals Weir Group
.jpg)
How to Hang Curtain Linings Dunelm
Place the lining on top of the curtain, with both header tapes facing each other Step 2 Using the curtain hooks included in your lining kit, insert them into the lining tape pockets and then into the bottom pockets of the curtain tape Step 3 Pull each curtain hook so the downward arm of the hook lies over the face side of the 2019年4月22日 Here are ten ways to improve the grinding efficiency of ball mill 1 Change the original grindability the ore is easier to grind, the wear of lining plate and steel ball is lower, Ten Ways to Improve the Grinding Efficiency of Your Ball MillSulphide ore was treated through the 32ft SAG mill until August 2011 The SAG mill has treated Mixed ore on two long spells; first from September 2011 to April 2012, and the second recently from June 2014 until July 2015 The liner change was in January 2013, which makes possible to compare the mill itSTEP CHANGE IN LINER DESIGN FOR THE KANSANSHI 32FT SAG MILL2020年1月11日 They are mainly the ball mill structure, the rotation speed, the ball mill media, the lining plate, the material fed and the feeding speed, etc In the following text, you will get some details on how to improve the grinding efficiency of the ball mill from the above aspects Analyze the ore crushing resistance, 5 Ways to Improve the Ball Mill Efficiency FTM
.jpg)
Taking your grinding to the next level Mill lining solutions for
design to maximize mill availability The shell lining has a major influence on grinding efficiency It transforms the mill rotation into charge motion, and both profile and spacing must be selected to suit each specific mill When designing a shell lining, the type of ore, mill size and speed, maintenance schedules, safety,2015年8月6日 The amount of unground material will slowly increase until the mill can no longer grind the bigger ore When this happens the liners will have to be changed If you ever have to start up a mill that has had a complete liner Grinding Mill Liners 911MetallurgistLet’s explore the various types of mill liners and their practical applications in greater detail Mill Lining System A mill is a vital tool for grinding and blending solid or hard materials through shear, impact, and compression methods Types And Applications Of Mill Liners FC Mill Liners2016年10月20日 Am sure your Ball Mill is considered the finest possible grinding mill available When lining the shell, start with the odd shaped pieces around the manhole opening if manholes are furnished nevertheless there is a certain amount of seasoning and dimensional change which goes on in the type of metals usedBall Mill Maintenance Installation Procedure 911Metallurgist
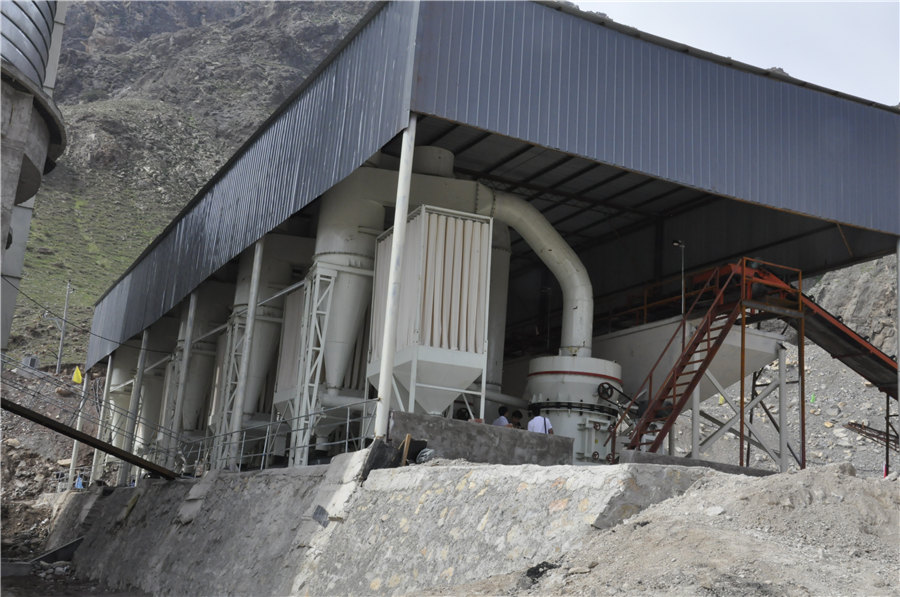
When to change ball mill liners? Qiming Machinery
2020年9月7日 Damaged lining of the barrel and ball mill Among other things, these particular mill liners also prevent wear and tear However, if during your regular inspections you begin to notice that the barrel’s and ball mill’s lining has begun to damage, it is a clear indication you need, or soon may need to replace the ball mill linermill is equal to twice the number of the feet in the mill shell diameter (eg, a 34ftdiameter mill shell would have 68 shell lifters) This is also called a 2D shell lining Eliminating some shell lifters increases the volume of charge between the lifters (“the bucket”) and the total charge that should be lifted in eachSemiautogenous grinding (SAG) mill liner design and development> Engineering approaches have highlighted mill performance with mill modelling and the use of improved materials > Liner design ,with the advent of large diameter SAG mills, the issues of design, selection, monitoring and evaluation of mill performance is critical > Mill trajectory modelling can be used to great effect in improving liner designThe Selection Design and Application of Mill Liners for Large Wet 2017年10月25日 With particular reference to mill size, it is apparent that a change in diameter in a large mill is relatively far less significant than the same change in 911 Metallurgist is a trusted resource for practical insights, solutions, and support in mineral processing engineering, helping industry professionals succeed with proven expertise Recommended Ball Mill Speed Liner Recommended Ball Mill Speed Liner Configuration
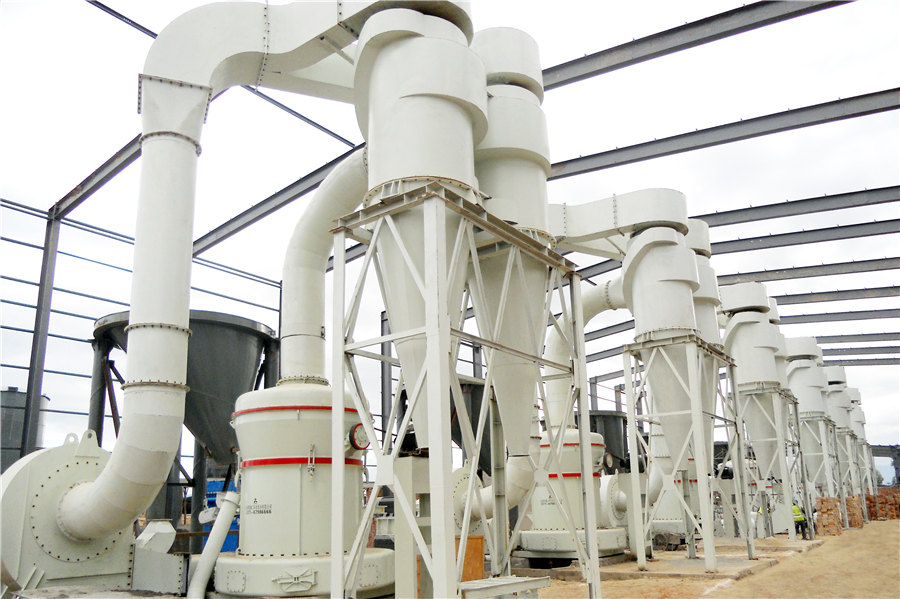
Balance the wear life of your mill lining parts Metso
2016年8月29日 Some lining parts in a mill are more exposed to wear than others, and the wear life of the mill lining components can therefore be very different This means that fully utilizing the wear life of all lining parts in a mill may not be the most optimal solution since it can lead to added downtime and production lossTest the Mill: Once the new liners are in place, start up the mill and test it to ensure that it is functioning properly Monitor the mill’s performance over time to ensure that the new liners are working effectively Tips for Prolonging the Lifespan of Ball Mill Liners Here are a few tips to help prolong the lifespan of ball mill liners:A Guide to Ball Mill Liner Replacement and Maintenance