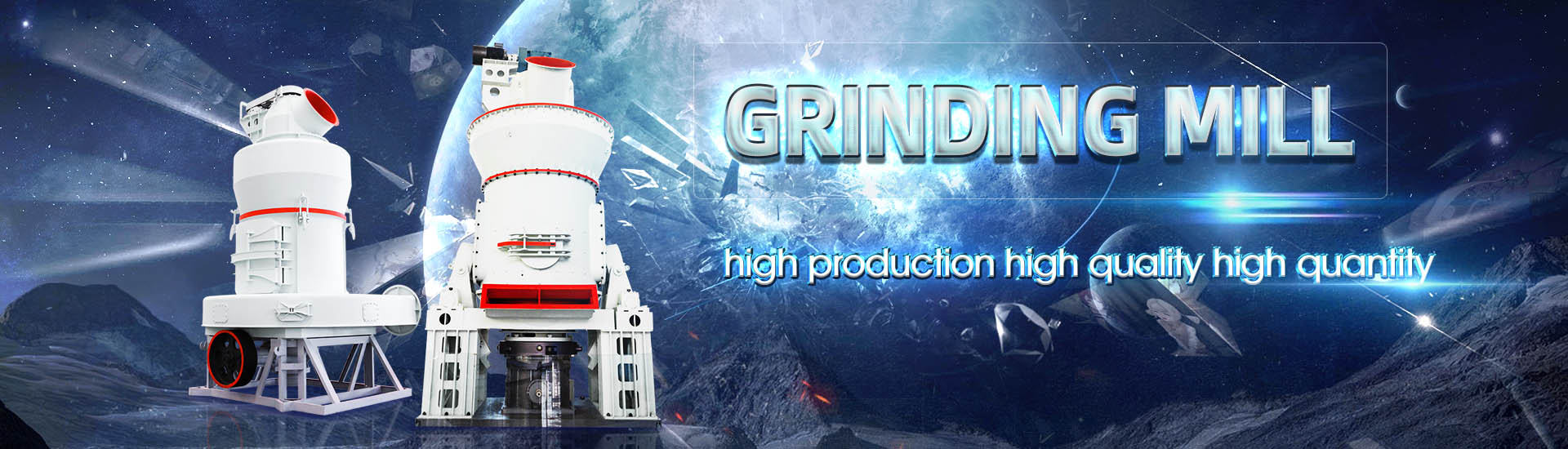
Reasons why cement mill suddenly becomes full of grinding
.jpg)
Ball mill output suddenly decreases? It was probably
2024年1月5日 "Full grinding" is a common abnormal phenomenon during the operation of the ball mill The direct cause is that the incoming and outgoing materials are out of balance In a short period ofAs grinding accounts for a sizeable share in a cement plant’s power consumption, optimisation of grinding equipment such as ball mills can provide significant cost and CO 2BALL MILLS Ball mill optimisation Holzinger ConsultingOptimization of the Cement Ball Mill Operation Optimization addresses the grinding process, maintenance and product quality The objective is to achieve a more efficient operation and OPTIMIZATION OF CEMENT GRINDING OPERATION IN BALL MILLS2021年11月8日 If the cement mill does not start grinding for a long time, starts grinding again, or starts grinding in winter, because the grinding temperature is low and the material is damp, Analysis on the causes of cement mill paste grinding and solutions
CFB石灰石脱硫剂制备96.jpg)
PROCESS DIAGNOSTIC STUDIES FOR CEMENT MILL
A 15 mio t/a cement plant is having a closed circuit ball mill for cement grinding: The mill has been operating with satisfactory performance interms of system availability and output, 2004年11月1日 There is potential to optimise conventional cement clinker grinding circuits and in the last decade significant progress has been achieved The increasing demand for “finer Cement grinding optimisation ScienceDirectGrinding plays a pivotal role in the cement manufacturing process, transforming raw materials into a fine powder suitable for creating cement It’s a crucial step that directly impacts the physical Grinding in Cement Manufacturing: Key Process, Types of Mills, When the mill is receiving clinker that’s too coarse, retention in the first compartment rises (and sometimes backspills) and the second empties and starts to over grind If the clinker becomes Everything you need to know about clinker/cement Grinding
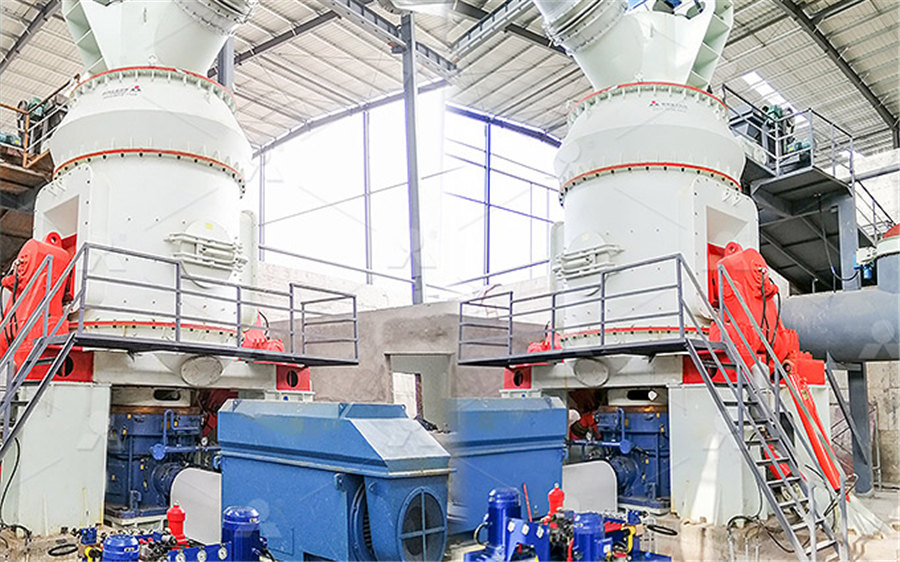
Operational parameters affecting the vertical roller mill
2017年4月1日 Sustainable operations and proven benefits of the technology in cement grinding applications attracted interests of the mineral industry Within the scope of the study, ore 2016年10月5日 In this chapter an introduction of widely applied energyefficient grinding technologies in cement grinding and description of the operating principles of the related equip‐ ments and comparisons over each other in EnergyEfficient Technologies in Cement GrindingFor the cement industry the ball mill was really an epochmaking breakthrough as for almost 80 years it was the predominant mill for grinding of raw materials and coal, and still today is the most used mill for cement grinding Over the last Cement grinding Vertical roller mills VS ball mills2017年9月11日 PDF In this study, an extensive sampling study was carried out at vertical roller mill of ESCH Cement Plant in Luxemburg Samples were collected from Find, read and cite all the research (PDF) Performance Evaluation of Vertical Roller Mill
.jpg)
A comparison of wear rates of ball mill grinding media
2016年1月1日 One of the most popular milling machines is the cement mill, which is used to crush raw materials such as lime, silicate, alumina and iron oxide using grinding balls [3]2022年1月1日 The size of grinding media is the primary factor that affects the overall milling efficiency of a ball mill (eg power consumption and particle size breakage)Effect of grinding media on the milling efficiency of a ball millThe document provides troubleshooting tips for various mechanical and electrical equipment issues that may occur at a cement plant It includes potential causes and solutions for problems with jaw crushers, hammer crushers, mills, dryers, separators, conveyors, compressors, precipitators, packaging machines and other key components The document aims to help TROUBLESHOOTING OF Cement Plant Mechanical and Electrical2023年4月23日 between the ball mill a nd rod mill showed that particles in a ba ll mill h ave a shorter residence time than in a rod mill [5 8] This is because balls offer less resistance to t he flow of (PDF) Grinding Media in Ball MillsA Review ResearchGate
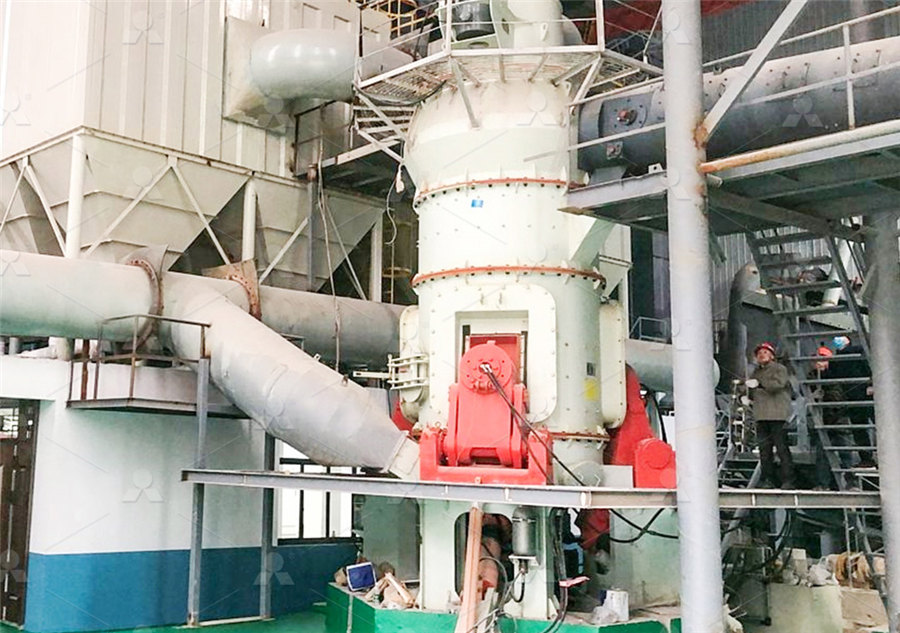
Grinding SpringerLink
2022年2月28日 Comparing dry and wet grinding curves in a ball mill in the same condition (an equal amount of materials and grinding media has been used on each pair of wetdry experiments) (Fig 17) indicated two significant differences at higher power values of wet grinding, specifically when speed exceeded 06 critical speed and for higher ω Pmax in the Most systems in the cement industry work with low oxygen levels They can take air with 3% oxygen from the preconsigner and feed it to the mill, which normally has an inert atmosphere Things can go wrong because the oxygen concentration can drop and suddenly go up, and as soon as it becomes more than 12 or 13%, an explosive atmosphere startsCoal Mill Safety In Cement Production IndustriesThis document summarizes a study evaluating the performance of a vertical roller mill used for cement grinding at a plant in Luxembourg Samples were collected from various points within the mill and surrounding circuit to analyze particle size distributions and calculate mass flow rates The grinding and separation efficiency of the vertical roller mill was assessed and compared to Performance Evaluation of Vertical Roller Mill in Cement GrindingMillGrinding Free download as Word Doc (doc), PDF File (pdf), Text File (txt) or read online for free This document section provides an introduction to mill grinding theory It discusses the importance of grinding materials to a fine Mill Grinding PDF Mill (Grinding) Cement
.jpg)
Session 11 Optimisation of Roller Press System PDF
This document discusses roller presses, which are compaction tools used primarily as pregrinders in cement production to increase grinding capacity Key points: Roller presses apply high pressure to compact and crack raw purpose of testing MAGA/VM 10, one of the newly developed cement grinding additives for vertical rollers mill The present industrial test has been performed with the objective of enhancing the compressive strengths of a blended cement with a high slag content All the main cement characteristics are reported as follows:Improvement of cement performances through the use of grinding o Finished grinding may consume 25 – 50 kWh/t cement, depending on the feed material grindability, additives used, plant design especially the required cement fineness Cement grinding is the single biggest consumer of electricity in the manufacturing process Whichever the mill types, grinding is inherently inefficientImprovements in New Existing Cement Grinding Mills by Tim 2015年10月1日 A fullscale threecompartment FLSmidth® cement grinding ball mill with dimensions of Ø35 × L10 operating in open circuit was sampled to analyse the grinding media effect on specific breakage Analysis of grinding media effect on specific breakage rate
.jpg)
(PDF) Analysis of ball mill grinding operation using mill power
2014年3月1日 The object of the study reported here is the grinding process in a tumbling mill where the mechanism of destruction by crushing is implemented, which is caused by the mechanism of compression loading2019年6月22日 Cement will continue to be the key material to satisfy national and international economic development due to its incidence as a raw material in the construction activity []As a result, the cement industry worldwide faces increasing challenges in conserving material and energy resources, as well as reducing its CO 2 emissions It is now known that the use of Use of Grinding Aids for Grinding Ternary Blends Portland Cement 2023年8月23日 A cement mill is a fundamental component of the cement manufacturing process, playing a vital role in breaking down and grinding cement clinker into fine powder This finely ground powder, when mixed with other materials, produces the building material we commonly know as cement To achieve this crucial transformation, a cement mill comprises What Are the Parts of a Cement Mills? Cement Ball Mill Ceramic balls are used to crush and grind the raw material in the cement mill They are known for their high resistance to wear and tear Importance of Grinding Media in Cement Mills The grinding media play an important role in the grinding process in cement mills Here are some of the key reasons why: 1 Grinding EfficiencyGrinding Media in Cement Mill ball mills supplier
.jpg)
Concrete Grinding: Everything You Need to Know
2023年4月13日 Is Concrete Grinding Worth It For Commercial Properties? While grinding can be costeffective, the longterm effects and risk of additional damage to the concrete may outweigh the upfront lower cost and quick turnaround time Not to mention, the patchiness of grinding can decrease curb appeal, aesthetics, and in turn, property valueWhat Is A Cement Ball Mill The cement ball mill is a kind of cement grinding millIt is mainly used for grinding the clinker and raw materials of the cement plant, and also for grinding various ores in metallurgical, chemical, and electric Cement Ball Mill Cement Grinding MachineA cement mill (or finish mill in North American usage [1]) is the equipment used to grind the hard, nodular clinker from the cement kiln into the fine grey powder that is cement Most cement is currently ground in ball mills and also vertical roller mills which are more effective than ball millsCement mill Wikipedia2021年1月1日 India is the world's second largest producer of cement and produces more than 8 per cent of global capacity Due to the rapidly growing demand in various sectors such as defense, housing, commercial and industrial construction, government initiative such as smart cities PMAY, cement production in India is expected to touch 550–600 million tones per Review on vertical roller mill in cement industry its performance
.jpg)
2 Gypsum dehydration during cement production ZKG
Current research on cement grinding is focussing on proportionate separate ultrafine grinding in a stirred media mill and subsequent mixing of the cement main constituents of their different finenesses However, very little is known about the gypsum dehydration potential of these mills2019年10月11日 AGICO Cement is a cement grinding plant manufacturer, we'd like to helps you learn more about cement grinding plant and cement grinding machines Skip to content +86 Cement Grinding Plant Overview Cement Grinding Unit AGICO Cement[4], [3] Mill feeding increasing together with acceleration wear for Balls, diaphragm and the linings (mill Boiling point of the Grinding Aid and cement mill temperature: The heat is going to be increased when producing cement inside the mill, the reason is obviously because of the impact of balls with lining and clinker inside the mill and this increase in temperature evaporate some `Grinding Aid Effectiveness in Cement Ball Mill AcademiaCement manufacturing brief description of a cement mill Cement clinker is usually ground using a ball mill This is essentially a large rotating drum containing grinding media normally steel balls As the drum rotates, the motion of the balls crushes the clinker The drum rotates approximately once every couple of secondsThe cement mill
.jpg)
INCREASING OUTPUT OF CEMENT GRINDING IN BALL MILL
increases production of cement mill To seal air leakage in SKS Separator with uniform air gap increases output of cement mill Proper distribution of grinding media with appropriate sizes also enhanced productivity of cement mill Target To increase the TPH from 190 to 220 TPH (PPC) with maintaining quality parameter ie 8% residue on +45 micronCement Grinding Optimization Free download as Word Doc (doc / docx), PDF File (pdf), Text File (txt) or read online for free 1 The document discusses optimizing cement grinding circuits It presents tools like the Bond method and population balance models that can be used to analyze and optimize cement grinding 2 It provides details on the typical cement production process Cement Grinding Optimization PDF Mill (Grinding) ScribdBALL MILL INSPECTION PROCEDURE source : thecementgrindingoffice Introduction This document is intended to help the staff of the cement plants On a process point of view, a mill inspection is only representative if the grinding mill circuit is in a steady working condition with a representative cement productCement Ball Mill Maintenance INFINITY FOR CEMENT EQUIPMENT2016年10月5日 In this chapter an introduction of widely applied energyefficient grinding technologies in cement grinding and description of the operating principles of the related equip‐ ments and comparisons over each other in EnergyEfficient Technologies in Cement Grinding
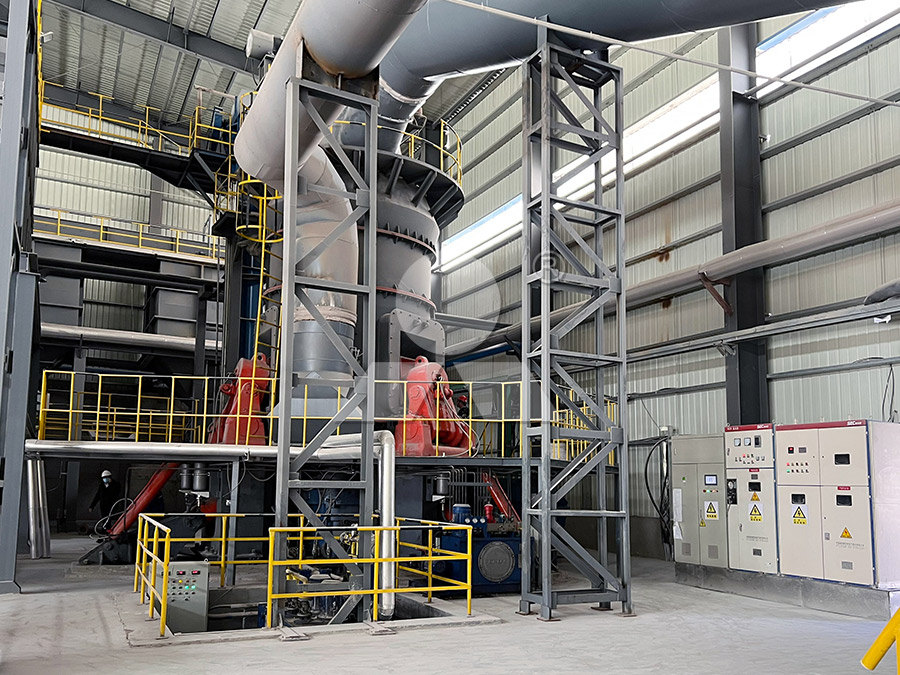
Cement grinding Vertical roller mills VS ball mills
For the cement industry the ball mill was really an epochmaking breakthrough as for almost 80 years it was the predominant mill for grinding of raw materials and coal, and still today is the most used mill for cement grinding Over the last 2017年9月11日 PDF In this study, an extensive sampling study was carried out at vertical roller mill of ESCH Cement Plant in Luxemburg Samples were collected from Find, read and cite all the research (PDF) Performance Evaluation of Vertical Roller Mill 2016年1月1日 One of the most popular milling machines is the cement mill, which is used to crush raw materials such as lime, silicate, alumina and iron oxide using grinding balls [3]A comparison of wear rates of ball mill grinding media2022年1月1日 The size of grinding media is the primary factor that affects the overall milling efficiency of a ball mill (eg power consumption and particle size breakage)Effect of grinding media on the milling efficiency of a ball mill
.jpg)
TROUBLESHOOTING OF Cement Plant Mechanical and Electrical
The document provides troubleshooting tips for various mechanical and electrical equipment issues that may occur at a cement plant It includes potential causes and solutions for problems with jaw crushers, hammer crushers, mills, dryers, separators, conveyors, compressors, precipitators, packaging machines and other key components The document aims to help 2023年4月23日 between the ball mill a nd rod mill showed that particles in a ba ll mill h ave a shorter residence time than in a rod mill [5 8] This is because balls offer less resistance to t he flow of (PDF) Grinding Media in Ball MillsA Review ResearchGate2022年2月28日 Comparing dry and wet grinding curves in a ball mill in the same condition (an equal amount of materials and grinding media has been used on each pair of wetdry experiments) (Fig 17) indicated two significant differences at higher power values of wet grinding, specifically when speed exceeded 06 critical speed and for higher ω Pmax in the Grinding SpringerLinkMost systems in the cement industry work with low oxygen levels They can take air with 3% oxygen from the preconsigner and feed it to the mill, which normally has an inert atmosphere Things can go wrong because the oxygen concentration can drop and suddenly go up, and as soon as it becomes more than 12 or 13%, an explosive atmosphere startsCoal Mill Safety In Cement Production Industries
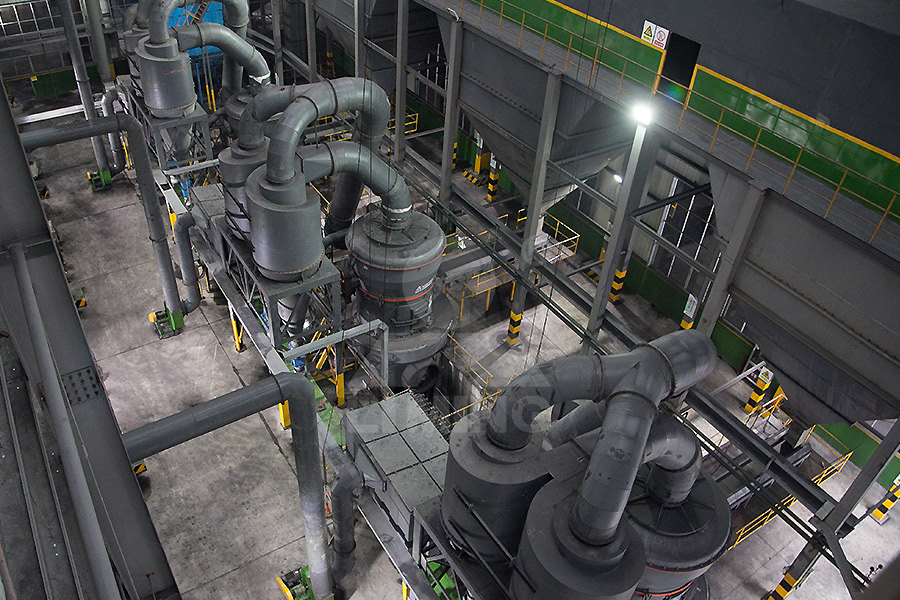
Performance Evaluation of Vertical Roller Mill in Cement Grinding
This document summarizes a study evaluating the performance of a vertical roller mill used for cement grinding at a plant in Luxembourg Samples were collected from various points within the mill and surrounding circuit to analyze particle size distributions and calculate mass flow rates The grinding and separation efficiency of the vertical roller mill was assessed and compared to