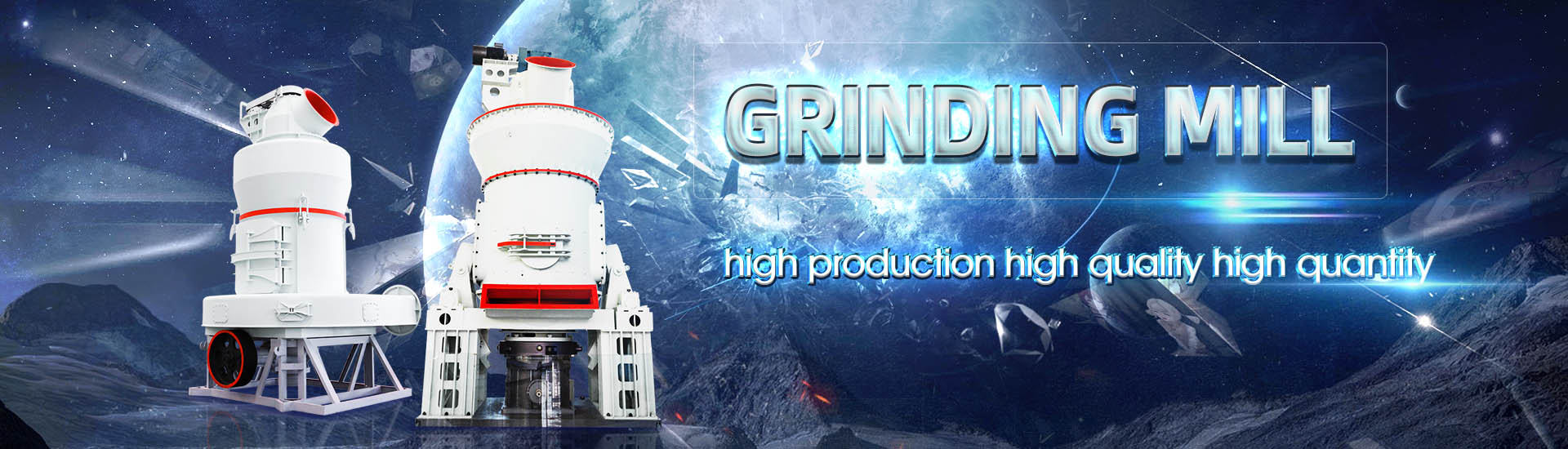
Ore powder making plant industrial project approval process
.jpg)
Guidelines for mineral process plant development studies AusIMM
This paper presents guidelines for studies required for the development of mineral processing facilities from initial feasibility studies through to commissioning Mining project schedule and cost overruns can often be attributed to inadequate metallurgical testwork, engineering and cost 2024年2月10日 To successfully initiate an industrial powder processing plant, a thorough feasibility study is essential This study assesses project viability by examining several key Designing Industrial Powder Processing Plants2012年10月26日 This document discusses the design and optimization of mineral processing plants It provides an overview of the general procedures for plant design which include ore Mineral processing plant design and optimisation PPT SlideShare2024年8月15日 A typical mineral processing plant is able to process various types of ores and mineral materials, including metal ores, nonmetallic ores, clay minerals, building materials Mineral Processing Plants: What You Need to Know
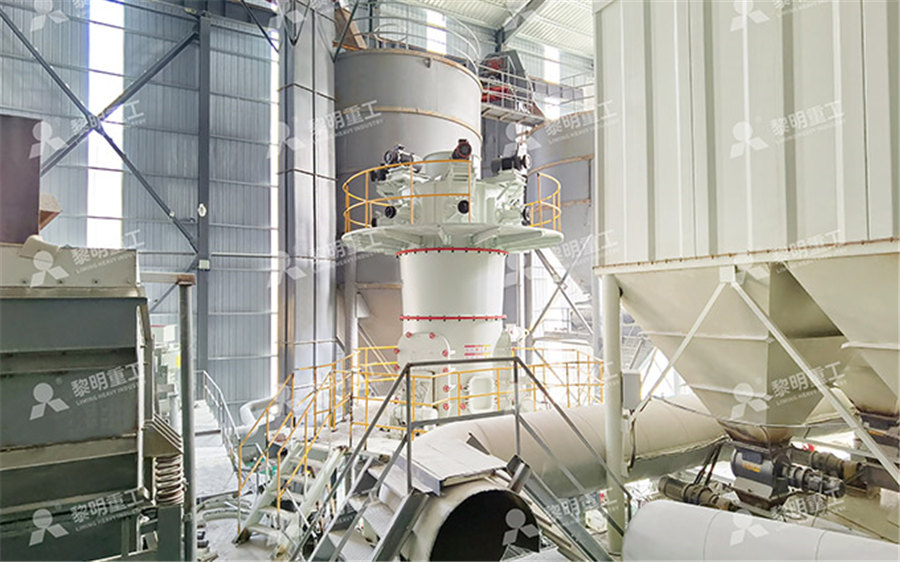
Guidelines for mineral process plant development studies
2010年12月1日 This paper presents guidelines for studies required for the development of mineral processing facilities from initial feasibility studies through to commissioning Mining The iron ore pelletizing process consists of three main steps: 1 Pelletizing feed preparation and mixing: the raw material (iron ore concentrate, additives anthracite, dolomite and binders are Iron Ore Pelletizing Process: An Overview IntechOpen2023年10月9日 Fluidized bed technology has become a crucial method used to process iron ore powder in nonblast furnace ironmaking, such as smelting reduction and direct reduction This Development and Problems of Fluidized Bed Ironmaking Process: 2022年10月20日 Making iron and steel from iron ore requires a long process of mining, crushing, separating, concentrating, mixing, agglomeration (sintering and pelletizing), and Iron Ore Processing, General SpringerLink

Micronsized ore powder production by propulsion and rapid
2021年9月6日 We describe a micronsized ore powder production by propulsion and rapid unloading of highpressure gas The research consists of three parts Firstly, we obtain the 2021年3月15日 This part describes the history, goals of pelletization, and provides a framework so that the chemical factors leading into an effective pelletizing process can be understood Iron Ore Pelletization: Part I Fundamentals: Mineral Processing 2024年8月15日 A typical mineral processing plant is able to process various types of ores and mineral materials, including metal ores, nonmetallic ores, clay minerals, building materials and energy minerals Metallic ores: Gold ore, Mineral Processing Plants: What You Need to Know2023年9月4日 Iron ore pretreatment equipment The pretreatment stage of iron ore mainly includes crushing, screening, grinding, and grading processes Crushing and screening: The raw ore is sent to the crusher by the vibrating Iron Ore Beneficiation Plant Equipment For Mining
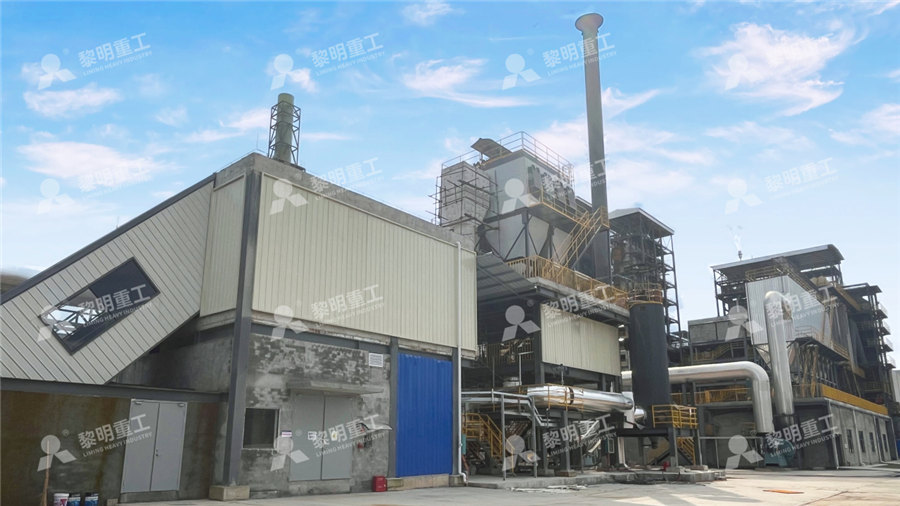
(PDF) i) Direct Reduced Iron: Production
2016年3月30日 In book: Encyclopedia of Iron, Steel, and Their Alloys (pppp 10821108) Chapter: i) Direct Reduced Iron: Production; Publisher: CRC Press, Taylor and Francis Group, New York2009年8月1日 Mill scale is an iron oxide waste generated during steelmaking, casting and rolling Total generation of mill scale at JSWSL is around 150 t/day and contains 60–70%FeO and 30–35%Fe2O3Recycling of steel plant mill scale via iron ore pelletisation process 2020年4月1日 In a research article on chemical beneficiation with the subsequent gravitational beneficiation of chromecontaining slurry tailings of Donskoy OreMining and Beneficiation Plant (DOMBP), which Process optimization of a chrome ore gravity concentration plant 2023年2月15日 Hematite, also spelled haematite, is a weakly magnetic iron ore with better floatability than magnetite and wide distributionIt is one of the most important raw materials for the extraction of iron Its composition is complex In addition to containing a small amount of magnetite, the impurity embedding of haematite has uneven particle size and high content of How to Extract Iron from Hematite: Methods and Plants
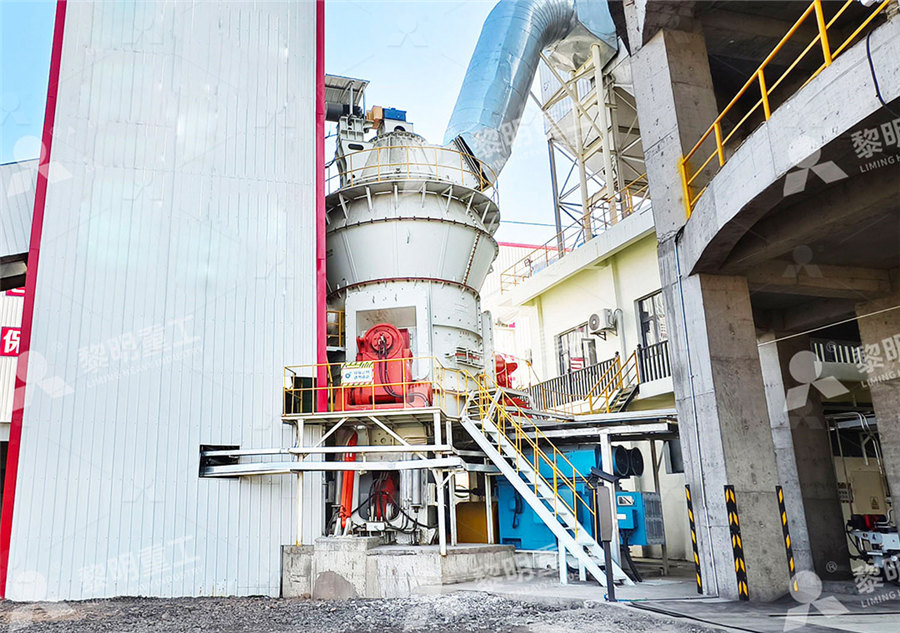
The Powder Coating Plant Process Redline Industries Ltd
pretreatment, is employed for improved bonding of the powder coat to the material being coated to provide a longer life to the coat The method employed usually is a dip in chemicals and water in various tanks Occasionally, the process may be automated through a spray pretreatment process A batch powder coating system:Media Attributions; Metal deposits are mined in a variety of different ways depending on their depth, shape, size and grade Relatively large deposits that are quite close to surface and somewhat regular in shape are mined using openpit mine methods (Figure 815 in Section 81)Creating a giant hole in the ground is generally cheaper than making an underground 82: Mining and Ore Processing Geosciences LibreTextsOur services cover everything from the fabrication of individual components through to complete plant upgrades; we have our own products, procedures and services for every phase in the life of an industrial plant Our process knowhow, which we keep continually up to date, informs the work of our conceptualisation and development teams and Industrial Project Development in Plant Construction Christof Industries2017年3月22日 Introduction In today’s world manufacturers and end users demand steel of an everincreasing quality However, the overall quality of the raw materials (iron ore, coke and coal) is decreasing, because the raw material reserves are not endless and the best materials have mostly been used in the pastSulphur removal in ironmaking and oxygen steelmaking
.jpg)
Mineral processing plant design and optimisation
2012年10月26日 7 Process Design • Process design criteria • A statement of what the plant will be required to do and the framework in which it will have to accomplish it It includes: • The capacity of the plant, • Material to be treated, • published on 17th November 2021 With the Decreto Semplificazioni Bis (Act No 108 of 29 July 2021), the Italian legislator aims to simplify both the procedure for the issuance of approvals for the construction of RE power plants and for conducting the Environmental Impact Assessment to be completed in parallel with the approval processItaly: Approval and EIA process for RE power plants simplified2024年1月23日 Gypsum powder is formed by a series of treatments on a large bulk of gypsum, with a finished particle size usually around 80325 mesh In terms of the entire production process of gypsum grinding, the equipment required Gypsum Powder Grinding And Processing Plant Our various services are: Detailed Project Report, Business Plan for Manufacturing Plant, Startup Ideas, Business Ideas for Entrepreneurs, Start up Business Opportunities, entrepreneurship projects, Successful Business Plan, Industry Trends, Market Research, Manufacturing Process, Machinery, Raw Materials, project report, Cost and Revenue, Prefeasibility study for NIIR Project Consultancy Services:Banana powder Manufacturing Plant
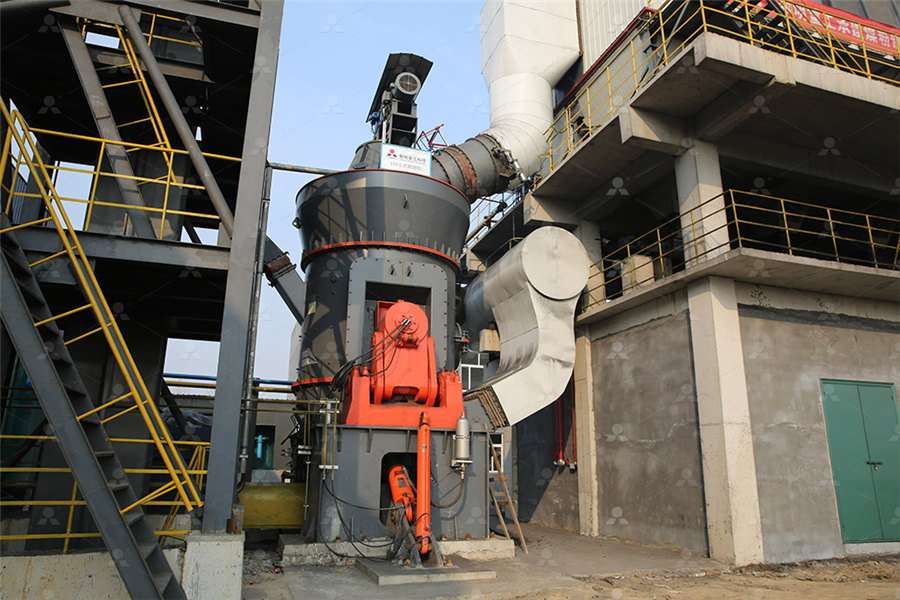
Direct Reduced Iron and its Production Processes – IspatGuru
2013年3月16日 The first plant of Midrex process came into operation in May 17, 1969 at Oregon Steel mills in Portland, Oregon The coal based rotary kiln process combines the Republic SteelNational Lead (RN) process developed in 1920s for beneficiating low grade ores, and the StelcoLurgi (SL) process conceived in the early 1960s for producing highgrade DRI2020年5月14日 The concentration of lowgrade iron ores is vital to the continued availability of iron and steel in our everyday lives (Eisele and Kawatra, 2003;Kawatra and Claremboux, 2021a;Zhang et al, 2021)THE GROWING IMPORTANCE OF PELLETIZING FOR IRON ORE 2013年8月1日 PDF Sintering is a process by which a mixture of iron ores, fl uxes and coke is agglomerated in a sinter plant to manufacture a sinter product of a Find, read and cite all the research you Iron ore sintering Part 1 Theory and practice of the sintering processWe can modify the project capacity and project cost as per your requirement If you need any customized project report and BANKABLE project reports as per your requirement, Click here to CONTACT US Or Call us at +91, +91, +91 011 , , for quick response All reports are prepared by highly qualified Project Report on WASHING POWDER AND WASHING SOAP
.jpg)
How Metal Powder Is Made: Step 1 of the Powder Metallurgy
When most people think of the metalmaking process, they picture a stream of molten metal pouring into a mold it makes a nice visual for films and commercialsBut when you consider making parts with powder metal, it may be a little harder to picture the process or why one would bother with powder metal in the first place2015年8月3日 PDF The first process that most of the ores or minerals undergo after they leave any mine, is mineral processing or mineral/ ore dressing It is a Find, read and cite all the research you (PDF) Overview of Mineral Processing MethodsThis page gives you the main stages of the project approval process, some key benefits, and examples of good and bad ways to go about the process Benefit 2: Better decisionmaking A project approval process can improve decisionmaking by providing a structured framework for evaluating projectsProject Approval Process Made Easy: 5 Steps Best Practices2024年8月2日 The ore is passed through crushers, which break it down into smaller chunks These chunks are then screened to separate the ore from waste material Grinding The crushed ore is then ground into a fine powder This step is crucial as it increases the ore's surface area, making it easier to extract the iron during subsequent processesThe Process of Making Iron: From Ore to Product

Project Report on Iron Ores Pelletization Plant [Eiri1170]
Project Report on Automatic Biscuit Making Plant (Eiri1080) Project Report on BISCUIT (ASSORTED) AUTOMATIC PLANT [CODE NO 1663] Project Report on AUTOMATIC BISCUIT MAKING PLANT (EOU) [EIRI1669] Project Report on AUTOMATIC BREAD MAKING PLANT [Eiri1074] 21 Bakery and Allied Products; Project Reports on Pulses and Dall Mill Dall Mill 2014年9月8日 2 Pelletization Prosess Pelletization is the process of making spheres of high carbon contains uniform quality iron ore Necessity of pelletization The configuration of iron ore powder in the blast furnace is more tightly packed and restricts the air flow For free air flow the powder of iron ore should be in spherespelletization process by Kshirod PPT SlideShareore pelletizing plant The idea of rolling moist fine ore in a drum to form balls and then drying and firing it was first patented by A G Andersson in Sweden in 1912 Further development was performed to bring the idea to reality In 1943, E W Davies and coworkers demonstrated the process using an experimental shaft furnaceIron Ore Pelletizing Process: An Overview IntechOpen2021年3月15日 Iron ore pellets are an essential part of the blast furnace charge, with high grade, good strength, uniform particle size, good metallurgical properties, and so forth 1, 2 Especially, fluxed iron Iron Ore Pelletization: Part I Fundamentals Request PDF
.jpg)
Iron Ore Pelletization FEECO International Inc
Iron ore must go through a lengthy preprocessing stage before it can be pelletized – a series of steps that work to beneficiate and concentrate lowgrade ores This process varies depending on the ore source, but typically involves various stages of crushing and grinding to Egg processing (Egg Powder) 2 Sector (as per the Illustrative List of Enterprises) AHVS 3 Project Capacity1 20,000 eggs/day 4 Key components of the project Processing, packaging and sales 5 Project Address (Village/Ward, Gram Pranchayat/Municipality, Block, District) 6 Products/Output from the project Whole egg powder 7 Total Project Cost Rs on Egg Processing (Egg Powder) APICOLReport Overview: IMARC Group’s report, titled “Iron Powder Manufacturing Plant Project Report 2024: Industry Trends, Plant Setup, Machinery, Raw Materials, Investment Opportunities, Cost and Revenue,” provides a complete roadmap for setting up an iron powder manufacturing plant It covers a comprehensive market overview to microlevel information such as unit operations Iron Powder Manufacturing Project Report 2024 Plant Cost2024年8月15日 A typical mineral processing plant is able to process various types of ores and mineral materials, including metal ores, nonmetallic ores, clay minerals, building materials and energy minerals Metallic ores: Gold ore, Mineral Processing Plants: What You Need to Know
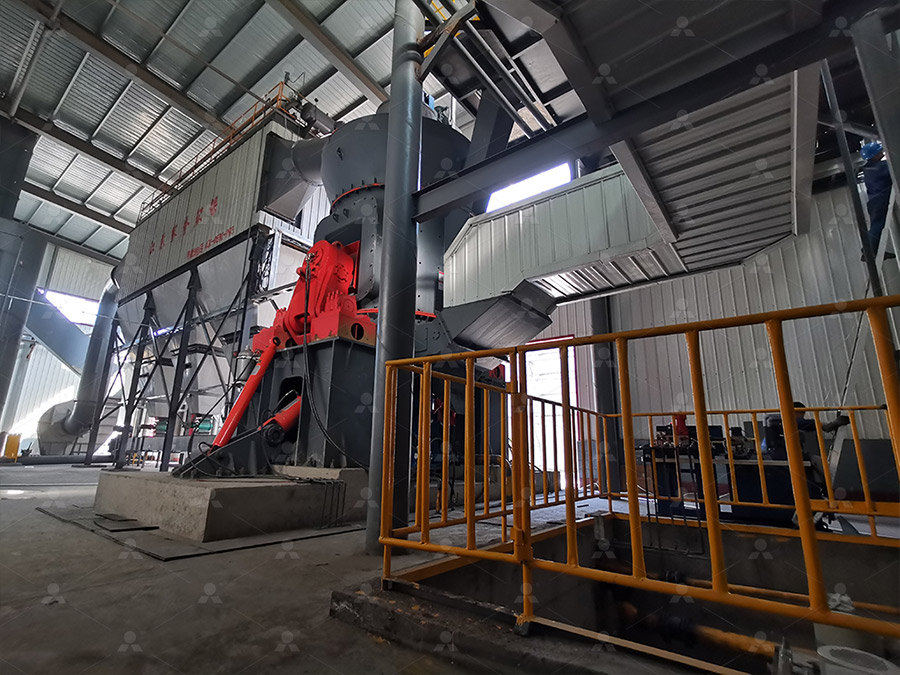
Iron Ore Beneficiation Plant Equipment For Mining
2023年9月4日 Iron ore pretreatment equipment The pretreatment stage of iron ore mainly includes crushing, screening, grinding, and grading processes Crushing and screening: The raw ore is sent to the crusher by the vibrating 2016年3月30日 In book: Encyclopedia of Iron, Steel, and Their Alloys (pppp 10821108) Chapter: i) Direct Reduced Iron: Production; Publisher: CRC Press, Taylor and Francis Group, New York(PDF) i) Direct Reduced Iron: Production2009年8月1日 Mill scale is an iron oxide waste generated during steelmaking, casting and rolling Total generation of mill scale at JSWSL is around 150 t/day and contains 60–70%FeO and 30–35%Fe2O3Recycling of steel plant mill scale via iron ore pelletisation process 2020年4月1日 In a research article on chemical beneficiation with the subsequent gravitational beneficiation of chromecontaining slurry tailings of Donskoy OreMining and Beneficiation Plant (DOMBP), which Process optimization of a chrome ore gravity concentration plant
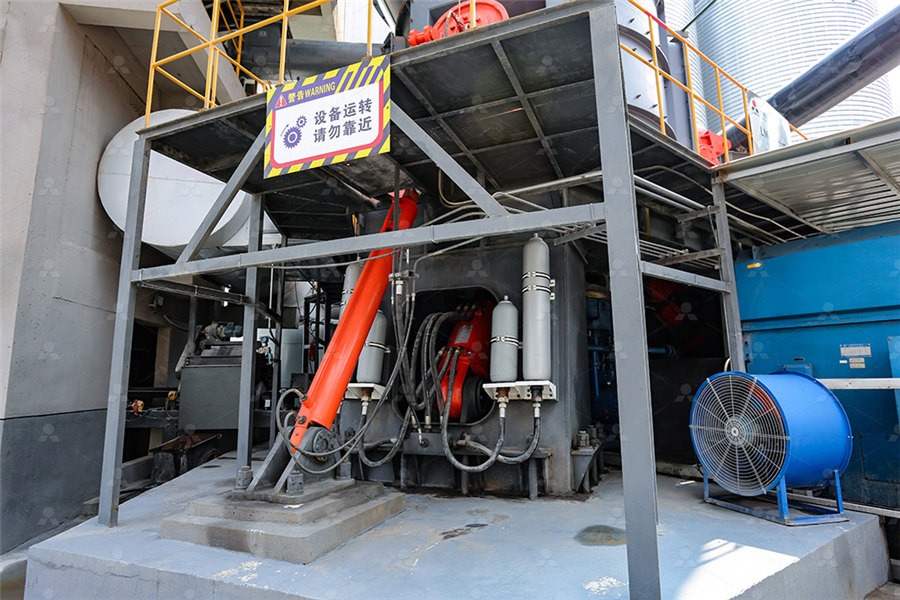
How to Extract Iron from Hematite: Methods and Plants
2023年2月15日 Hematite, also spelled haematite, is a weakly magnetic iron ore with better floatability than magnetite and wide distributionIt is one of the most important raw materials for the extraction of iron Its composition is complex In addition to containing a small amount of magnetite, the impurity embedding of haematite has uneven particle size and high content of pretreatment, is employed for improved bonding of the powder coat to the material being coated to provide a longer life to the coat The method employed usually is a dip in chemicals and water in various tanks Occasionally, the process may be automated through a spray pretreatment process A batch powder coating system:The Powder Coating Plant Process Redline Industries LtdMedia Attributions; Metal deposits are mined in a variety of different ways depending on their depth, shape, size and grade Relatively large deposits that are quite close to surface and somewhat regular in shape are mined using openpit mine methods (Figure 815 in Section 81)Creating a giant hole in the ground is generally cheaper than making an underground 82: Mining and Ore Processing Geosciences LibreTextsOur services cover everything from the fabrication of individual components through to complete plant upgrades; we have our own products, procedures and services for every phase in the life of an industrial plant Our process knowhow, which we keep continually up to date, informs the work of our conceptualisation and development teams and Industrial Project Development in Plant Construction Christof Industries
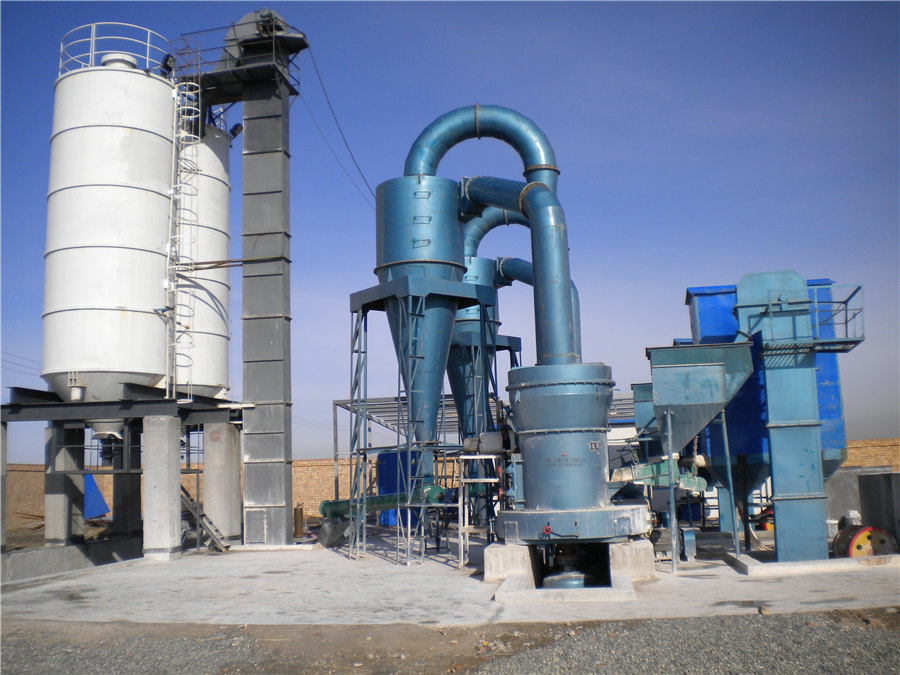
Sulphur removal in ironmaking and oxygen steelmaking
2017年3月22日 Introduction In today’s world manufacturers and end users demand steel of an everincreasing quality However, the overall quality of the raw materials (iron ore, coke and coal) is decreasing, because the raw material reserves are not endless and the best materials have mostly been used in the past