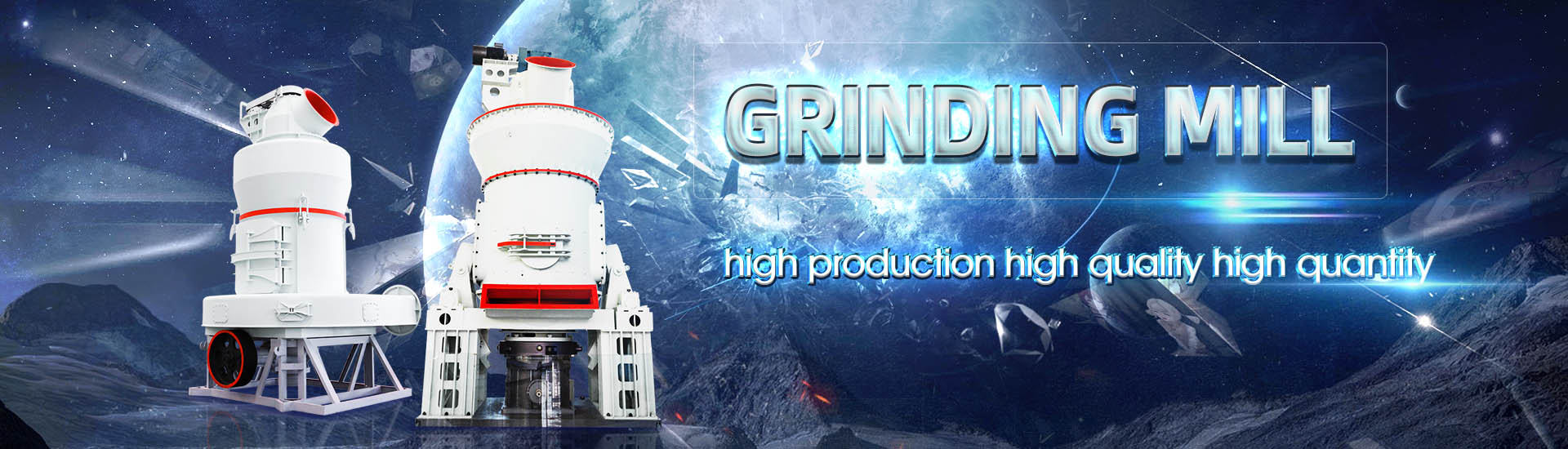
All processes for cement production
.jpg)
How Cement is Made Cement Manufacturing Process
There are six main stages of the cement manufacturing process The raw cement ingredients needed for cement production are limestone (calcium), sand and clay (silicon, aluminum, iron), Cement is manufactured from materials heated together at high temperatures to form a rocklike substance that is ground into a fine powder Limestone, marl, and clay are commonly used sources of these primary elements Other materials How Cement is Made Portland Cement AssociationManufacturing of cement involves various raw materials and processes Each process is explained chemical reactions for manufacture of Portland Cement Cement is a greenish grey colored powder, made of calcined mixtures of clay Manufacture of Cement Materials and Manufacturing micrometres, producing “kiln feed” Cement Plant: The Manufacturing Process worldcementassociation 1 Limestone (CaCO3) is taken from a quarry 2 4 3 The limestone Cement Plant: The Manufacturing Process 4 5 World Cement
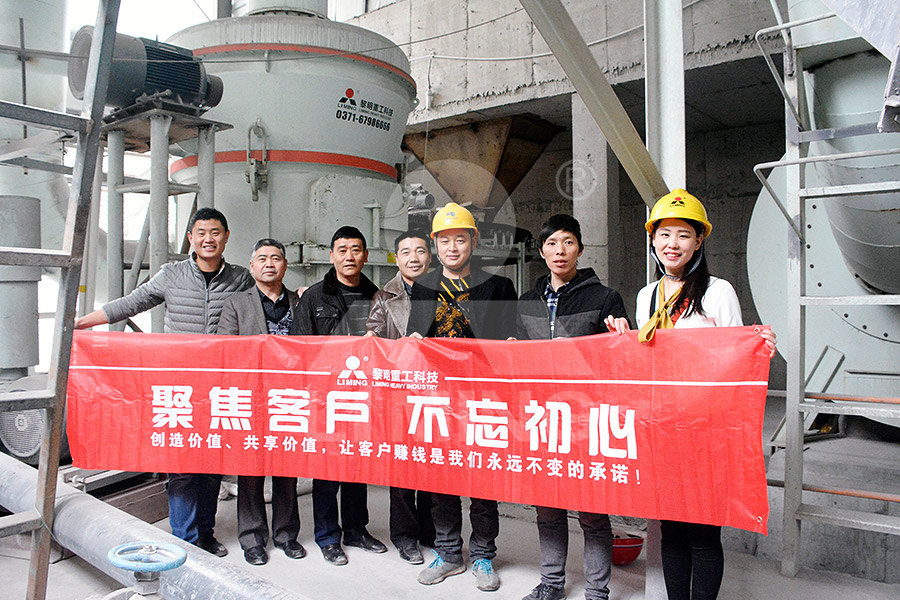
Cement Manufacturing Process The Engineering
2018年8月28日 CEMENT MANUFACTURING PROCESS PHASES Production of cement completes after passing of raw materials from the following six phases These are; Raw material extraction/ Quarry; Grinding, Proportioning and 2023年12月20日 Cement manufacturing is a complex process that begins with mining and then grinding raw materials that include limestone and clay, to a fine powder, called raw meal, which is then heated to a sintering temperature as The Cement Manufacturing Process Thermo Fisher Discover the cement production process Learn how Heidelberg Materials creates highquality cement from raw materialsHow cement is made Heidelberg MaterialsThere are 4 stages of cement production that help maintain consistent raw material quality with minimal chemistry deviation, from quarry to silo to customer The Quarry: The cement A practical guide to improving cement manufacturing processes

A practical guide to improving cement manufacturing processes
The cement production process 1 The Quarry: The cement production process begins with the extraction of limestone and clay from the quarry 2 Crusher and PreBlending: The material is then crushed to reduce particle sizes and blended to reduce variability in composition 3 Raw Mill and Kiln: Raw materials and additives areThe dry process is the most popular industrial cement making process which is widely adopted by cement plants all over the world for its great advantages in energy saving and environmental protection Skip to content The cyclone How Is Cement Produced in Cement Plants Cement 2024年6月1日 The cement industry plays a critical role in global carbon emissions, primarily due to the release of CO 2 during the production of cement The process of cement production involves the transformation of raw materials, such as limestone and clay, into clinker, which is a powdered form of cementDecarbonising cement and concrete production: Strategies, For a more detailed account of the cement production process, see the Understanding Cement book View of a cement kiln (the long nearlyhorizontal cylinder) and preheater tower (Picture courtesy Castle Cement) Summary of production process Cement is typically made from limestone and clay or shaleCement manufacturing components of a cement plant Understanding Cement
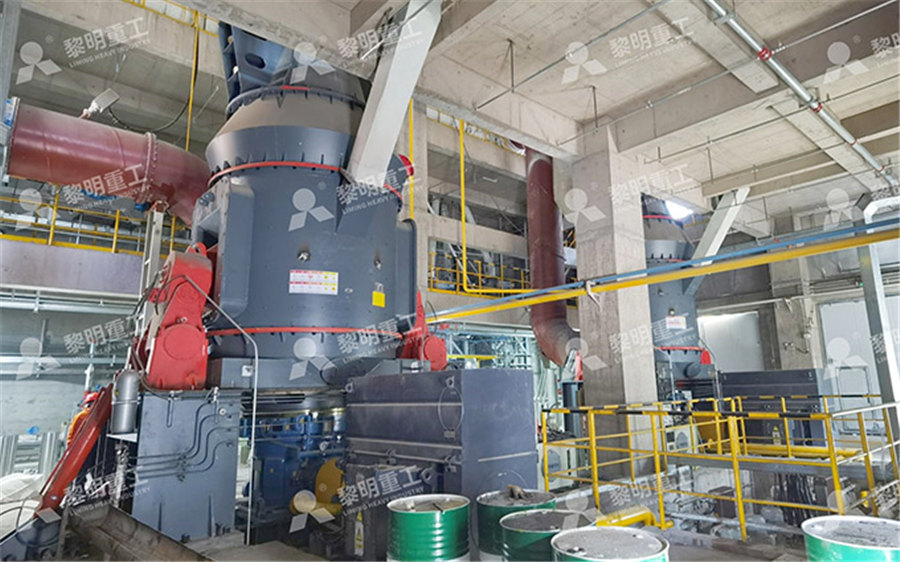
Parametric Studies of Cement Production Processes
2020年2月15日 Most important technologies for clinker (cement) production in regard to RKS configuration, temperature ranges, and functional zones [9, 10] ∗Escape of liquid and adsorbed water ∗∗ 2024年9月10日 Longer Production Time: The wet process generally takes longer for Cement production compared to the dry process, as it involves additional steps such as slurry formation and drying Conclusion This marks an end to the discussion on the wet and dry processes of Cement manufacture and has also enumerated on the major points of difference between dry Cement Manufacturing Process: Know Extraction, Processing sharp decline in cement production over the last 15 years, from a peak of 262Mt in 2007 to 168Mt in 2017, equivalent to a reduction in cement per capita from 05 to 03 tonnes per person (3) The CO 2 intensity of cement production over that period has improved by about 7% (06t of CO 2 emitted per tonne of cement in 2017) (2)Deep decarbonisation of industry: The cement sector EuropaCement production illustrates how process and combustion emissions can be combined in a single unit Just over half of the CO 2 originates for the calcination, while just under half of the emissions originate from the combustion of fuel [64,65] The kiln flue gas takes one of Cement Production an overview ScienceDirect Topics
.jpg)
The Cement Production Process
A range of technologies is employed in all of the processes, and all equipment and machinery have been subject to improvements as the cement industry has evolved Developments in grinding technology have largely been in the dry process technology, and have broader application than ‘raw’ and ‘finish’ milling in cement plants2015年4月14日 Below is a sample band 9 answer to a process task 1 question on concrete production Source: Cambridge English IELTS Past Papers Question– The diagrams below show the stages and equipment used in the cementmaking process, and how cement is used to produce concrete for building purposes AnswerIELTS Task 1 Process Cement and Concrete Production2022年7月1日 Request PDF Decarbonization options for cement production process: A technoeconomic and environmental evaluation The longterm environmental targets require significant cuts of CO2 emissions Decarbonization options for cement production process: A 2023年10月13日 The production process of cement releases large amounts of CO2, mainly due to the hightemperature firing of raw materials, Cement production takes place all around the world, Global database of cement production assets and upstream
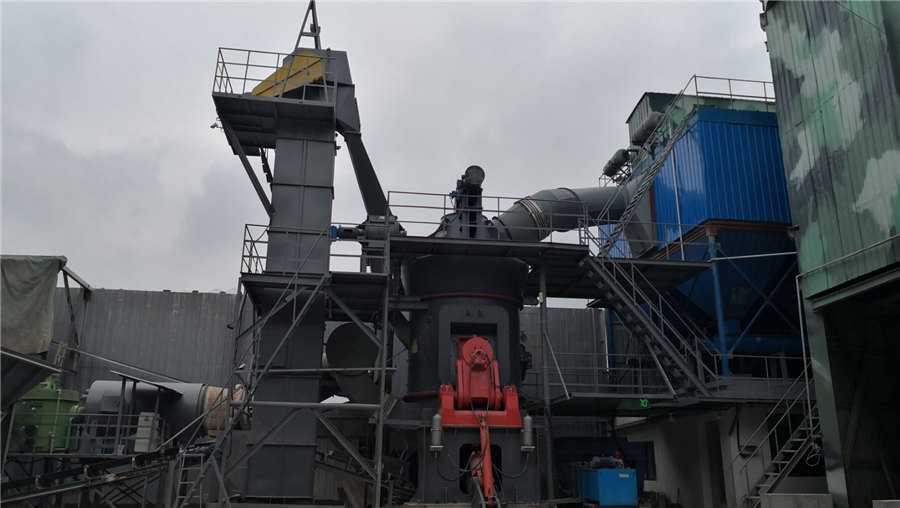
Process technology for efficient and sustainable cement production
2015年12月1日 The reason for the very limited additional potential savings of thermal energy is the necessary heat for the clinker production process Fig 1 shows the heat flows, the thermal input, the use for clinkering and drying, and the remaining waste heat flows that might be utilised However, the remaining waste heat is already used to a high degree, indicated by the already 2024年10月14日 In a new study published in ACS Sustainable Chemistry Engineering, the researchers describe how the new approach could be easily incorporated into existing cementproduction processes, providing a more affordable alternative to existing solutions to decarbonize the industry Cement and concrete: An enormous carbon footprint Ordinary Portland cement, Engineers develop scalable process to decarbonize cement production2024年9月5日 These raw materials are blended in definite quantities to obtain a uniform and homogeneous raw mix which is very crucial in the production of good quality cement The Manufacturing Process of Cement Now, let’s explore the steps involved in the cement production process in more detail: 1 Mining and Crushing The process of making cement A Comprehensive Guide to the Cement Manufacturing Processpassivation – 13 Cement quality – 14 Setting time – 15 ASTM cement types and specifications – 16 European EN 197 cement specification – 17 Composite cements (intergrinds and blends) – 18 Supersulphated cement – 19 Calcium aluminate cement (CAC) – 20 Shrinkagecompensating cements (SCC) – 21 ISO 9001:2000 Quality 8The Cement Plant Operations Handbook International Cement
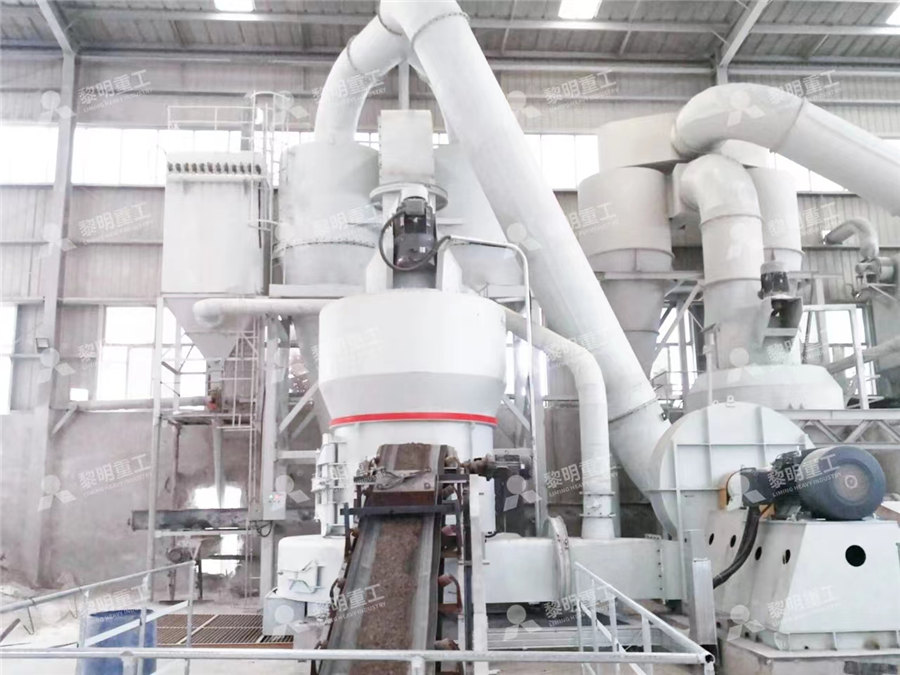
IELTS Diagram: Model Answer Band Score 9 with Tips
The diagrams depict the process of cement production and its usage in making concrete In cement production there are 4 stages involved In the first stage limestone and clay are crushed to powder form This then passes through a mixer into a rotating heater, which is supplied with constant heat at one endThe final step in cement manufacturing is the grinding of clinker into cement powder, followed by the finalization process that ensures the product meets all required specifications and standards This stage is crucial as it defines the physical and chemical properties of the cement, making it suitable for various construction purposesCement Making Guide: Steps, Impact Green Alternatives2021年3月9日 Cement production processes are energyintensive and generate huge greenhouse emissions with the clinker energy intensity of about 34 GJ/t in 2018 [4] generating about 4% of the global CO 2Simulation and Optimization of an Integrated Process Flow Sheet 2015年12月9日 Process Discretion: Wet process, Semidry process, Dry process and Finish process The environmental im pact of the cement production and its variations between different cement plants, using Life (PDF) Cement Manufacturing ResearchGate
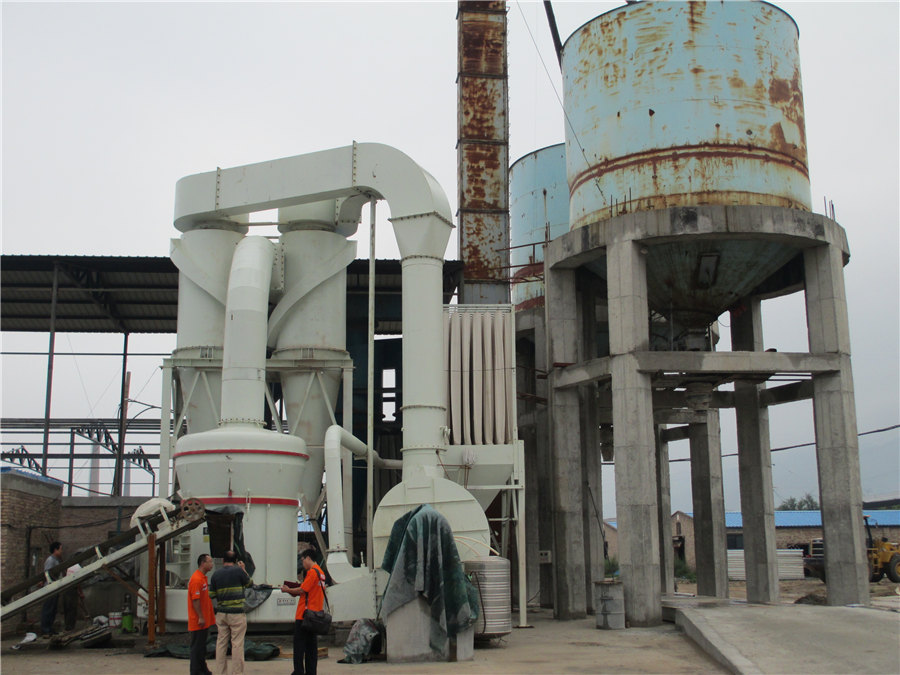
Cement SpringerLink
2021年3月3日 Cement is produced by a hightemperature (about 1500 °C) reaction in a rotary kiln of carefully proportioned and blended ratios of lime (CaO), silica (SiO 2), alumina (Al 2 O 3), and iron oxide (Fe 2 O 3)The production of cement is a chemical process requiring an accurate blend of the previously cited four key organic oxides and the limitation of several undesirable Cement production declined significantly in 2022, down 5% to 4 158 Mt But this number hides contrasting regional trends Brimstone (United States) has announced the development of a new cementmaking process that sources Cement IEA International Energy Agency2024年1月15日 In the conventional cement production process, CO 2 emissions primarily result from the production of clinker, the main component of Portland cement [3]Specifically, two main sources of CO 2 emissions exist: (1) process emissions from the calcination process, where limestone (CaCO 3), a key component in the raw meal for clinker production, decomposes into Decarbonisation pathways of the cement production process via 2021年3月9日 In this study the process flow diagram for the cement production was simulated using Aspen HYSYS 88 software to achieve high energy optimization and optimum cement flow rate by varying the flow rate of calcium oxide and silica in the clinker feed Central composite Design (CCD) of Response Surface Methodology was used to design the ten experiments for Simulation and Optimization of an Integrated Process Flow Sheet
.jpg)
Cement Production: How Cement Is Manufactured CEMEX UK
10 Cement packaging and shipping The cement is then housed in storage silos, from where it is hydraulically or mechanically extracted and transported to facilities where it will be packaged in sacks or supplied in bulk In either case, it can be shipped by rail car, freighter truck or ship2020年1月1日 About half of the emissions are caused by process emissions during the clinker manufacture, 40% by the combustion of fuels to heat the cement kiln, and 10% by power consumption and transportation Assessment on Cement Production Practice and Potential Cement Cement Plant: The Manufacturing Process worldcementassociation 1 Limestone (CaCO3) is taken from a quarry 2 4 3 The limestone is fed into a crusher and then stored until needed The clinker is mixed with additives, such as gypsum, and then ground in a cement mill, which creates cement The cement is then packed and distributed to consumersCement Plant: The Manufacturing Process 4 5 World Cement Cement production involves quarrying limestone and clay, grinding and blending the materials, burning them at high temperatures to form clinker, and finely grinding the clinker to produce cement powder The key steps are: 1) Quarrying limestone and clay and grinding them to powder; 2) Blending the powders in precise proportions; 3) Burning the blend at high heat to form Chapter 1 Introduction To Cement Production PDF Scribd
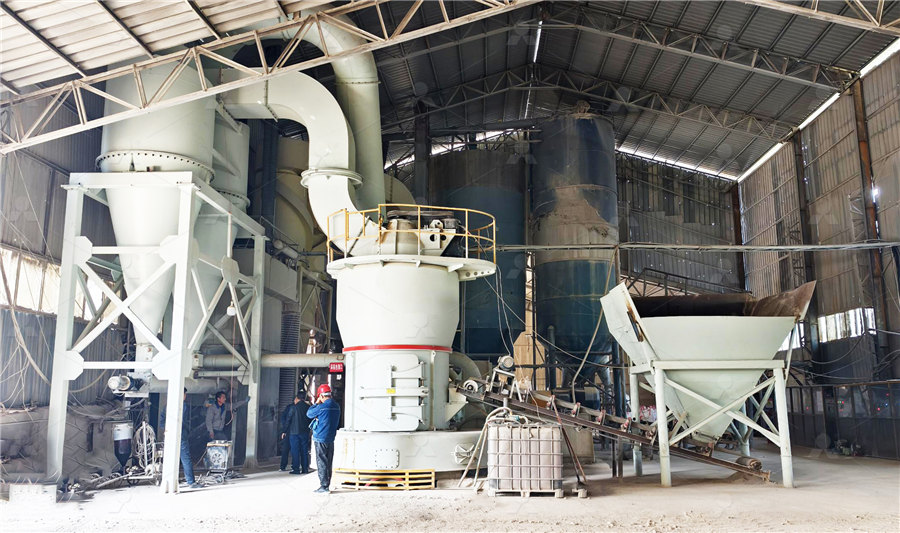
Cement Manufacturing Process Engineering Intro
2012年8月30日 Generally cement plants are fixed where the quarry of limestone is near bye This saves the extra fuel cost and makes cement somehow economical Raw materials are extracted from the quarry and by means of conveyor belt material is transported to the cement plant There are also various other raw materials used for cement manufacturing2024年6月17日 Cambridge Electric Cement is a novel approach to the electrification of cement that integrates cement production with the production of steel in an electric arc furnace (EAF) The process is premised on the fact that spent cement powder from concrete waste has a similar composition to the slag used in the EAF processElectric Cement Production: The TechnologiesThe cement production process 1 The Quarry: The cement production process begins with the extraction of limestone and clay from the quarry 2 Crusher and PreBlending: The material is then crushed to reduce particle sizes and blended to reduce variability in composition 3 Raw Mill and Kiln: Raw materials and additives areA practical guide to improving cement manufacturing processes The dry process is the most popular industrial cement making process which is widely adopted by cement plants all over the world for its great advantages in energy saving and environmental protection Skip to content The cyclone How Is Cement Produced in Cement Plants Cement
.jpg)
Decarbonising cement and concrete production: Strategies,
2024年6月1日 The cement industry plays a critical role in global carbon emissions, primarily due to the release of CO 2 during the production of cement The process of cement production involves the transformation of raw materials, such as limestone and clay, into clinker, which is a powdered form of cementFor a more detailed account of the cement production process, see the Understanding Cement book View of a cement kiln (the long nearlyhorizontal cylinder) and preheater tower (Picture courtesy Castle Cement) Summary of production process Cement is typically made from limestone and clay or shaleCement manufacturing components of a cement plant Understanding Cement2020年2月15日 Most important technologies for clinker (cement) production in regard to RKS configuration, temperature ranges, and functional zones [9, 10] ∗Escape of liquid and adsorbed water ∗∗ Parametric Studies of Cement Production Processes2024年9月10日 Longer Production Time: The wet process generally takes longer for Cement production compared to the dry process, as it involves additional steps such as slurry formation and drying Conclusion This marks an end to the discussion on the wet and dry processes of Cement manufacture and has also enumerated on the major points of difference between dry Cement Manufacturing Process: Know Extraction, Processing
.jpg)
Deep decarbonisation of industry: The cement sector Europa
sharp decline in cement production over the last 15 years, from a peak of 262Mt in 2007 to 168Mt in 2017, equivalent to a reduction in cement per capita from 05 to 03 tonnes per person (3) The CO 2 intensity of cement production over that period has improved by about 7% (06t of CO 2 emitted per tonne of cement in 2017) (2)Cement production illustrates how process and combustion emissions can be combined in a single unit Just over half of the CO 2 originates for the calcination, while just under half of the emissions originate from the combustion of fuel [64,65] The kiln flue gas takes one of Cement Production an overview ScienceDirect TopicsA range of technologies is employed in all of the processes, and all equipment and machinery have been subject to improvements as the cement industry has evolved Developments in grinding technology have largely been in the dry process technology, and have broader application than ‘raw’ and ‘finish’ milling in cement plantsThe Cement Production Process2015年4月14日 Below is a sample band 9 answer to a process task 1 question on concrete production Source: Cambridge English IELTS Past Papers Question– The diagrams below show the stages and equipment used in the cementmaking process, and how cement is used to produce concrete for building purposes AnswerIELTS Task 1 Process Cement and Concrete Production