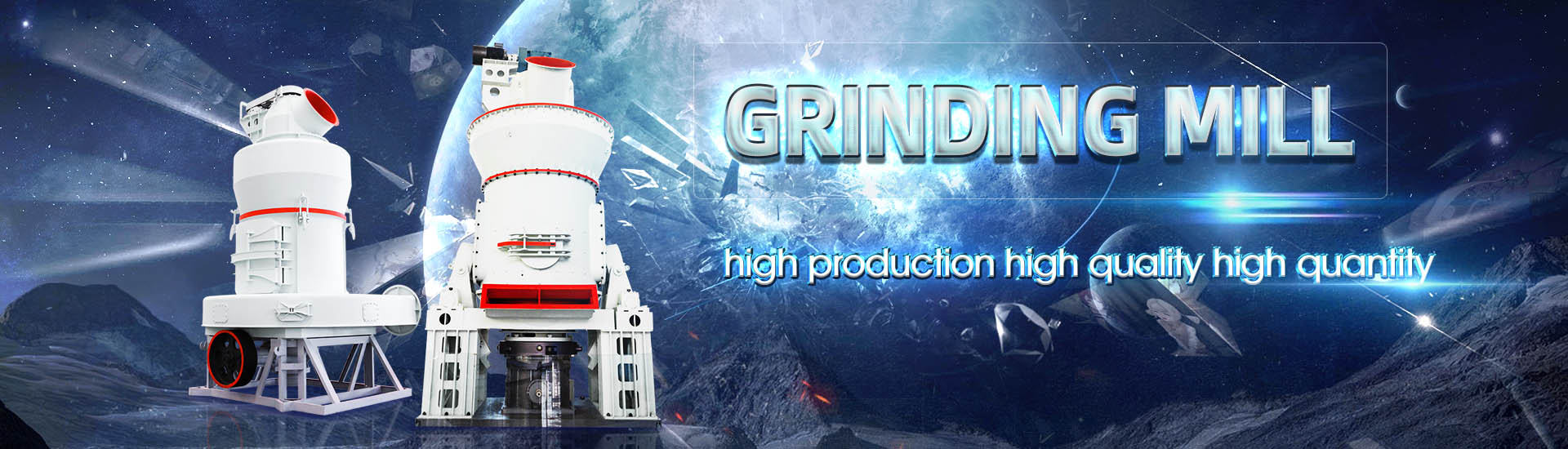
How to calculate the production cost of calcite plant

Calcite Production Cost Analysis Reports 2024 Procurement
The report provides a detailed analysis essential for establishing a Calcite manufacturing plant It encompasses all critical aspects necessary for Calcite production, including the cost of Calcite production, Calcite plant cost, Calcite production costs, and the overall Calcite manufacturing It includes a comprehensive capital cost analysis while covering the cost breakdown of raw materials, utilities, labor, packaging, transportation, land and construction, and machinery The Calcite Production Cost Analysis Syndicated AnalyticsThis report presents a cost analysis of Precipitated Calcium Carbonate (PCC) production from lime and carbon dioxide The process examined is a typical process In this analysis, lime Calcium Carbonate Production from Lime and Carbon DioxideThis report provides an exhaustive cost evaluation of calcite production via mining, crushing, washing, and dry processing The process involves mining calcium carbonate from open pits Calcite Production Cost Analysis via Mining, Crushing, Washing,
.jpg)
GENERAL PROCESS PLANT COST ESTIMATING,
2014年6月1日 Many engineering design projects are developed to provide sizing information from which estimates of capital and operating costs can be made Chemical plants are built to make a profit, and anUse the Chemical Engineering Plant Cost Index (CE index, or CEPCI) or another cost index to update equipment costs: last page of each issue of Chemical Engineering: TP1 C3 For Cost estimating for chemical engineering plant design University 2016年3月1日 This report presents a cost analysis of Precipitated Calcium Carbonate (PCC) production from limestone In this typical process, limestone is first calcinated The product Calcium Carbonate Production from Limestone Cost Analysis2024年6月13日 By calculating and reporting production costs, you can: Track your profitability and performance over time identify areas of improvement and optimization Make informed Cost of Production: How to Calculate and Report the Cost of
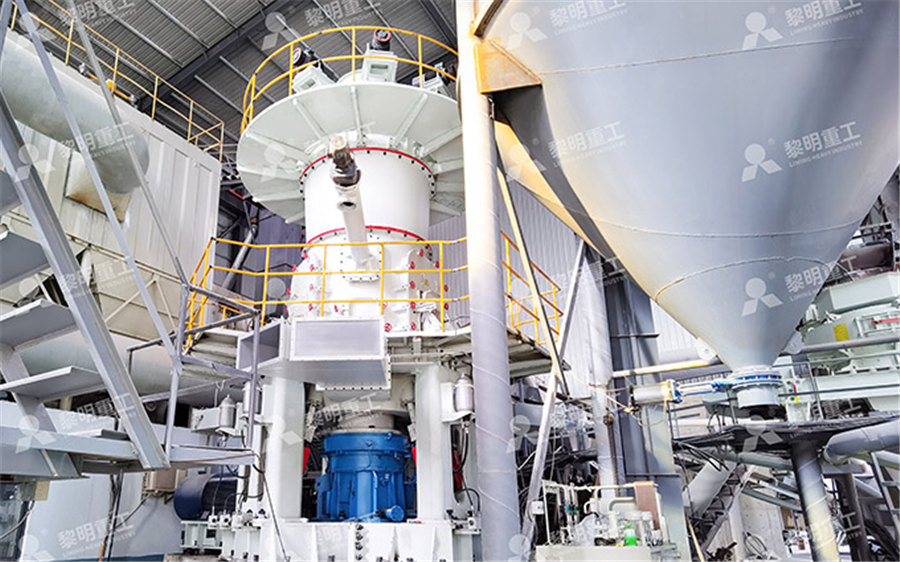
Plant Cost Estimates SpringerLink
Analyze the process carefully to determine what “plant cost factors” should be used, and then prepare a detailed breakdown of the total plant cost package This will be discussed in the Direct labor is simply all of the costs related to the labor that goes into production, including salaries, benefits, workers compensation insurance, and payroll taxes It is calculated in 3 steps: first, calculate the direct hourly labor rate to account How to Calculate Production Cost Matics2024年6月7日 2 Identifying and Calculating Expenses Directly Associated with Production One of the most important aspects of cost of production is identifying and calculating the direct costs associated with the production of goods or services Direct costs are the expenses that can be directly traced to a specific product, service, or activityCost of Production: How to Calculate and Report the Cost of 2008年6月18日 One shorthand method for handling fixed costs is to calculate the amount of variable costs per unit container or bunch and multiply that number by 15 or 2 to yield the total cost per container or bunch For example, the Calculating Crop Costs Greenhouse Grower
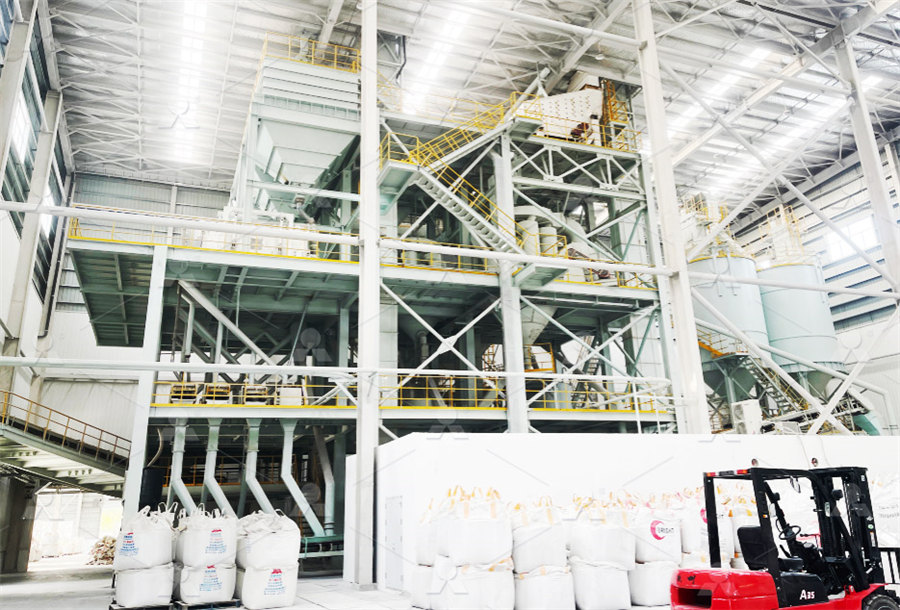
Average Cost of Production Overview, Types, How To Calculate
They are affected by various factors, such as price discrimination, externalities, information asymmetry, and transaction costs How to Calculate Average Cost The first step when calculating the cost involved in making a product is to determine the fixed costs The next step is to determine the variable costs incurred in the production processIn addition to this there are further costs involved in running the power plant: the cost of coal that is burnt and expenses, including labor cost, to keep the plant up and running While the actual costs involved in electricity generation vary with the technology used, we can nevertheless build a general understanding of costs associated with electricity generationOpen Electricity Economics: 3 The cost of electricityFollowing are the methods used to find out the cost of production: 1 Statement of Cost 2 Cost Sheet 3 Tender Statement 4 Production Account Method # 1 Statement of Cost: Statement of cost is a tabulated statement which shows the production cost of fixed quantity of a product, which is related to the production in a fixed time Under this method, cost percent of every step of How to Calculate the Cost of Production? Cost Accounting2019年9月25日 Discover how to calculate product costs the right way (with our template and 4x reallife calculation examples) Stop losing money on your products! Discover how to calculate product costs the right way (with our template and 4x reallife calculation examples) c l e v e r i s m c l e v e r i s m MENUHow to Calculate Product Costs (+4 Examples) Cleverism
]@S0{UDKK%G24F3JGHC.jpg)
Cost of Production: How to Calculate and Use Cost of Production
2024年6月26日 Direct costs can be easily allocated and accounted for in the cost of production calculation, while indirect costs require allocation methods such as cost drivers or activitybased costing 4 Direct costs are essential for determining the cost per unit of a specific product or service, while indirect costs contribute to the overall overhead expenses2023年4月25日 To calculate product costs, you’ll use the following equation: Direct labor + direct material + overhead = Product costs To break this down into a perunit cost, then use this formula: Product costs (the answer from the previous equation) divided by the number of units produced = Perunit cost Let’s apply this formula using a practical What is product cost and how to calculate (with example)Findings The results of implementing the optimization models show that Case 3 turnout the highest freshwater production (1,521 m ³ /day) at a unit cost of 136$/m ³ when compared to Case 1 with Typical water production costs for desalination plants and Raw material to be Purchased = Total Raw Material Required – Beginning Raw Material Inventory Ending Note: The product cost related to direct materials can be determined through a budget that estimates the desired quantity of direct Product Cost What Is It, Formula, Examples Types
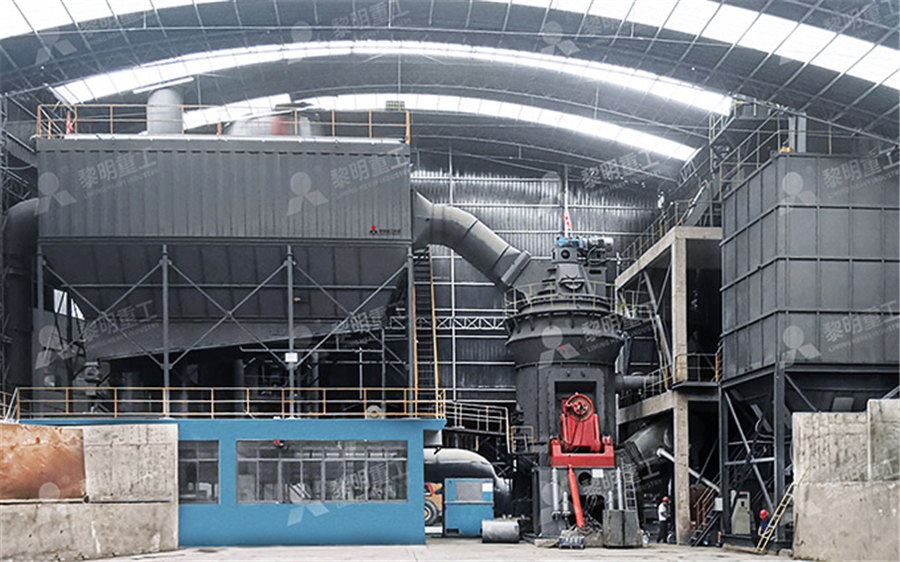
How to Calculate Production Cost in Excel (3
2024年5月30日 Method 3 – Apply User Defined Function to Calculate Production Cost Using VBA To calculate the production cost using a userdefined function made with VBA code, we’ll use the following simplified dataset, 2024年6月26日 (A Guide to Product Costing) How to calculate the cost of production You can calculate the cost of production using the following steps: 1 Establish the direct material cost The direct material cost is the total cost of all the materials, including raw materials and components, used in the manufacturing processWhat Is the Cost of Production Formula? (How to Calculate)2023年9月20日 Every production is made up of steps that turn the raw materials into the finished product Each step should be mapped out 2 Determine the Cycle Time for Each Unit Know the amount of time spent working on an item This should be the time spent working from the raw material stage to the finished product stage 3 Calculate the MachineHour How to Calculate Production Capacity: Formula Examples%PDF17 %âãÏÓ 4974 0 obj > endobj 4985 0 obj >/Encrypt 4975 0 R/Filter/FlateDecode/ID[]/Index[4974 39]/Info 4973 0 R/Length 71/Prev /Root 4976 0 R/Size How to evaluate the cost of the green hydrogen business case?
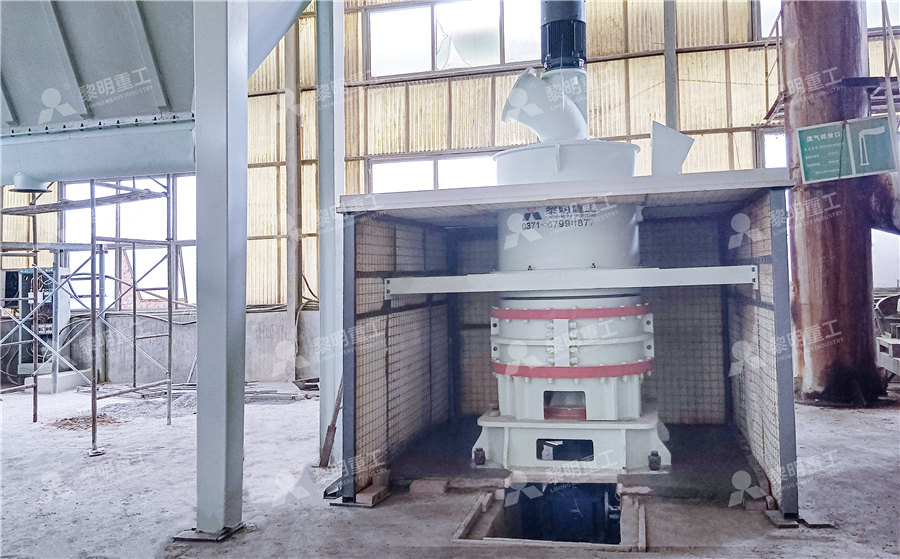
Cost Analysis for Crushing and Screening – Part II
Sandvik SRP has earlier studied a new way of calculating the cost in crushing and screening the results was a satisfactory, Sandvik SRP is now ready to go further in this study2024年6月19日 The process of calculating average total cost involves identifying all fixed and variable costs, calculating the total cost of production, determining the number of units produced, This includes the facility costs and manufacturing equipment purchased, often under the title of plant, property, and equipment (PPE) assetsHow to Calculate Total Cost (With Formulas and Examples)2022年7月8日 How to calculate product cost? Direct Labor + Direct Material + Factory Overheads = Product Cost Formula The expense of plant utilities Manufacturing overhead (other) 1,000 tables got created by Company A The What is Product Cost How to Calculate it? (With Examples)2023年9月28日 By calculating manufacturing costs, manufacturers can better understand the elements that are driving up costs while identifying the most economical way to manufacture a product For instance, if some raw materials are driving up costs, manufacturers can negotiate with other suppliers who may be willing to supply these materials at a lower costManufacturing Costs: Significance, Types, and Cost Calculation
.jpg)
Calculation of production costs in Excel
The production cost calculation of production is the determination of costs in terms of money per unit of goods, works or services The calculation includes direct and indirect costs Direct is the cost of materials, wages of workers, etc Indirect costs: planned profit, transportation, etc2023年3月8日 Multipleitem production capacity = ((amount of product A x throughput of product A) + (amount of product B x throughput of product B)) / machinehour capacity Continuing with the above example, let’s presume our What Is Production Capacity and How to Calculate It?OPEX differentials net of taxes (209 EUR/t steel for DRIH EAF and 37 EUR/t steel for PDSP; Table 2) and the process emis sion factor of 15 tCO 2 for BFBOF would imply CO 2 prices of about 139 Unit costs of different iron and steel production 2024年6月28日 If the reason why a unit product cost is being derived is to determine the lowest price at which to sell a product, then the calculation should not contain an allocation of overhead, and perhaps not even a charge for direct labor costs In many situations, the only direct cost associated with a product is its direct material costHow to calculate unit product cost — AccountingTools
.jpg)
How to Calculate Total Manufacturing Cost ProjectManager
2023年9月19日 Why Manufacturing Cost Is Important Knowing the costs of production is critical for a manufacturer that wants to stay in business As noted, you can’t know your profit margins if you don’t know how much it costs to manufacture your product That means knowing all the costs involved as we’ve already defined2023年3月10日 Related: How To Calculate Fixed Cost in 3 Steps (With Examples) How peritem cost affects production costs and manufacturing costs differently As a company produces more products, the total revenue increases while the fixed costs stay the same This means that the business may become more profitable as the peritem production cost goes downHow To Calculate Manufacturing Cost in 5 Steps Indeed2021年10月18日 Permeate or distillate from desalination processes is typically void of minerals and alkalinity, inherently acidic and therefore corrosive to water distribution infrastructure The reintroduction of both minerals and alkalinity is essential for the stabilization of the water before it is sent to consumers making this the last step of the treatment processRemineralization and Stabilization of Desalinated WaterLearn about production costs and the formula to calculate them See examples of the cost of production in manufacturing of goods for businesses and corporationsProduction Costs Formula Examples What is Cost of Production?
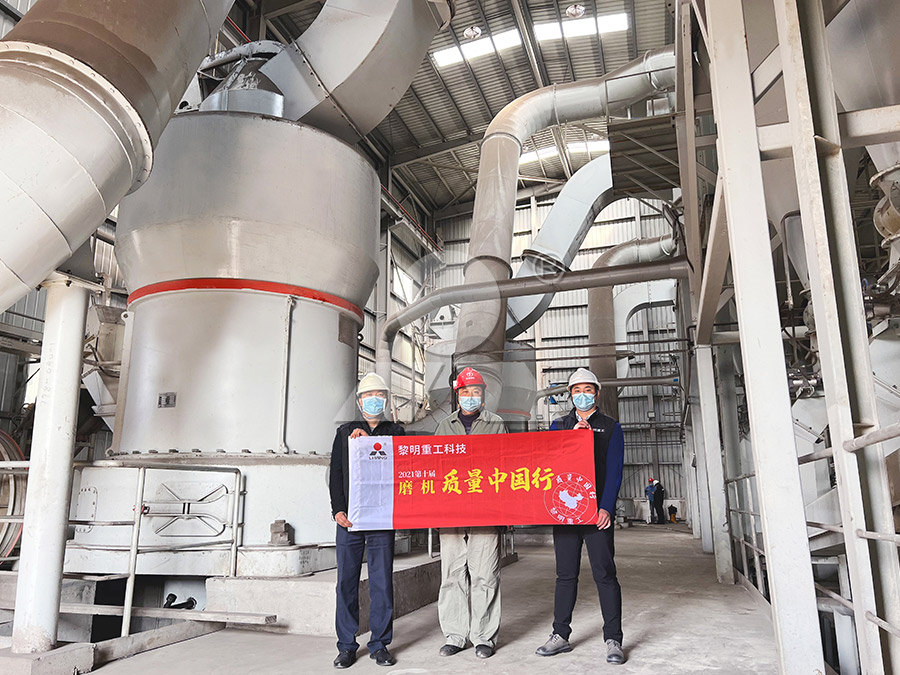
July 2018 of production Euro Chlor
facturing costs at being between € 30 and € 70 per ton Cl2 Overall, the cost range, per tonne Cl2, varies between € 141 and € 505 with the associated electricity costs ranging between € 72 and € 291 Conclusion: The cost of electricity accounts for 2023年7月26日 To calculate a unit product cost, sum the material, labor, and overhead costs, then divide by the number of units produced Unit Product Cost Definition A unit product cost is defined as the total cost per unit that it takes to produce a good Unit Product Cost ExampleUnit Product Cost Calculator2022年4月4日 Introduction World cement production has grown steadily in the last decades and represents an energyintensive industry, which accounts for ~14 Gt of CO 2 emissions per year, corresponding to roughly 6–7% of global anthropogenic GHG emissions ()The cement industry is therefore required to restructure its sector significantly to play a role in mankind's quest to Evaluating the Carbon Footprint of Cement Plants Integrated With Direct labor is simply all of the costs related to the labor that goes into production, including salaries, benefits, workers compensation insurance, and payroll taxes It is calculated in 3 steps: first, calculate the direct hourly labor rate to account How to Calculate Production Cost Matics
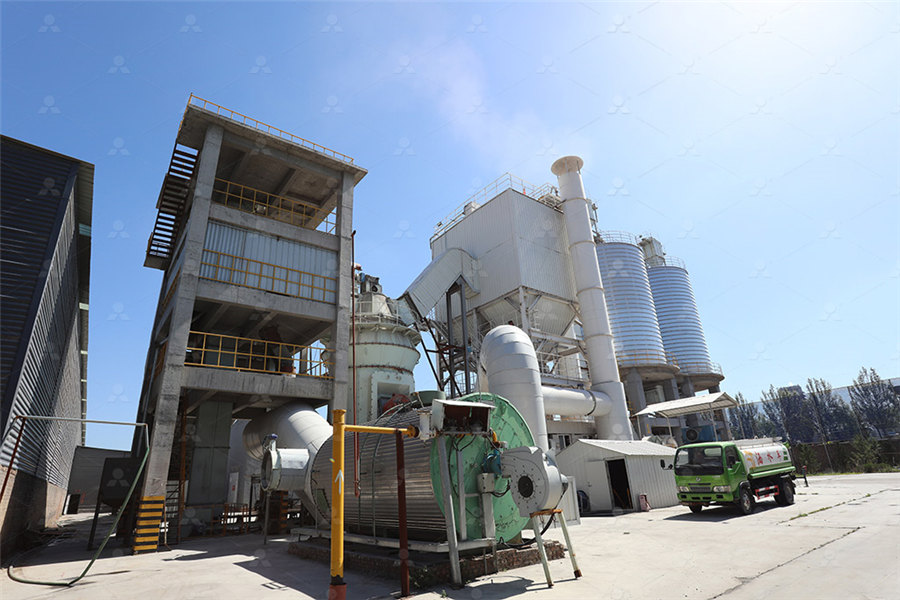
Cost of Production: How to Calculate and Report the Cost of
2024年6月7日 2 Identifying and Calculating Expenses Directly Associated with Production One of the most important aspects of cost of production is identifying and calculating the direct costs associated with the production of goods or services Direct costs are the expenses that can be directly traced to a specific product, service, or activity2008年6月18日 One shorthand method for handling fixed costs is to calculate the amount of variable costs per unit container or bunch and multiply that number by 15 or 2 to yield the total cost per container or bunch For example, the Calculating Crop Costs Greenhouse GrowerThey are affected by various factors, such as price discrimination, externalities, information asymmetry, and transaction costs How to Calculate Average Cost The first step when calculating the cost involved in making a product is to determine the fixed costs The next step is to determine the variable costs incurred in the production processAverage Cost of Production Overview, Types, How To CalculateIn addition to this there are further costs involved in running the power plant: the cost of coal that is burnt and expenses, including labor cost, to keep the plant up and running While the actual costs involved in electricity generation vary with the technology used, we can nevertheless build a general understanding of costs associated with electricity generationOpen Electricity Economics: 3 The cost of electricity
.jpg)
How to Calculate the Cost of Production? Cost Accounting
Following are the methods used to find out the cost of production: 1 Statement of Cost 2 Cost Sheet 3 Tender Statement 4 Production Account Method # 1 Statement of Cost: Statement of cost is a tabulated statement which shows the production cost of fixed quantity of a product, which is related to the production in a fixed time Under this method, cost percent of every step of 2019年9月25日 Discover how to calculate product costs the right way (with our template and 4x reallife calculation examples) Stop losing money on your products! Discover how to calculate product costs the right way (with our template and 4x reallife calculation examples) c l e v e r i s m c l e v e r i s m MENUHow to Calculate Product Costs (+4 Examples) Cleverism2024年6月26日 Direct costs can be easily allocated and accounted for in the cost of production calculation, while indirect costs require allocation methods such as cost drivers or activitybased costing 4 Direct costs are essential for determining the cost per unit of a specific product or service, while indirect costs contribute to the overall overhead expensesCost of Production: How to Calculate and Use Cost of Production2023年4月25日 To calculate product costs, you’ll use the following equation: Direct labor + direct material + overhead = Product costs To break this down into a perunit cost, then use this formula: Product costs (the answer from the previous equation) divided by the number of units produced = Perunit cost Let’s apply this formula using a practical What is product cost and how to calculate (with example)
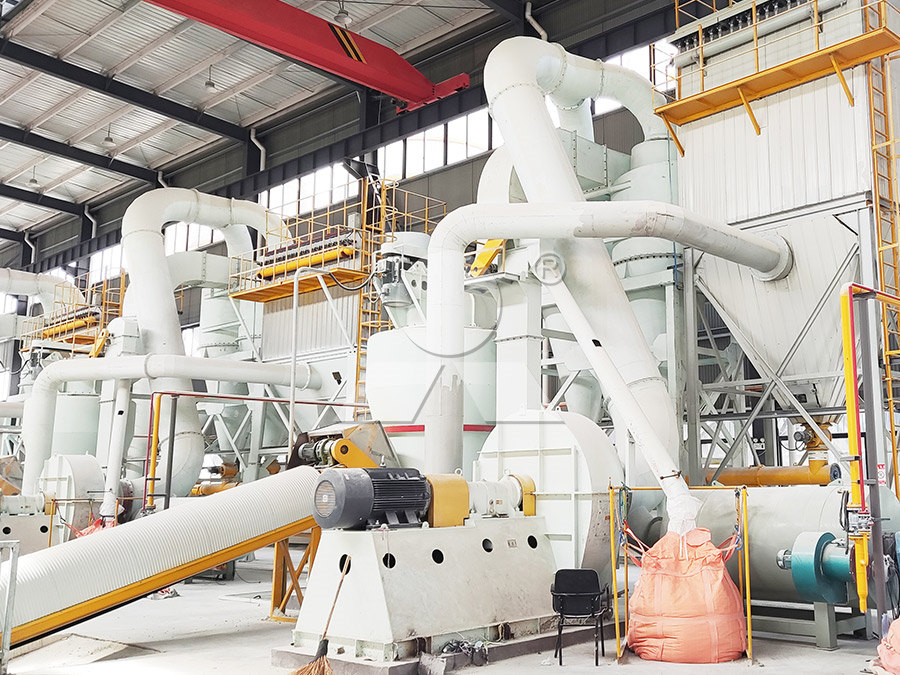
Typical water production costs for desalination plants and
Findings The results of implementing the optimization models show that Case 3 turnout the highest freshwater production (1,521 m ³ /day) at a unit cost of 136$/m ³ when compared to Case 1 with