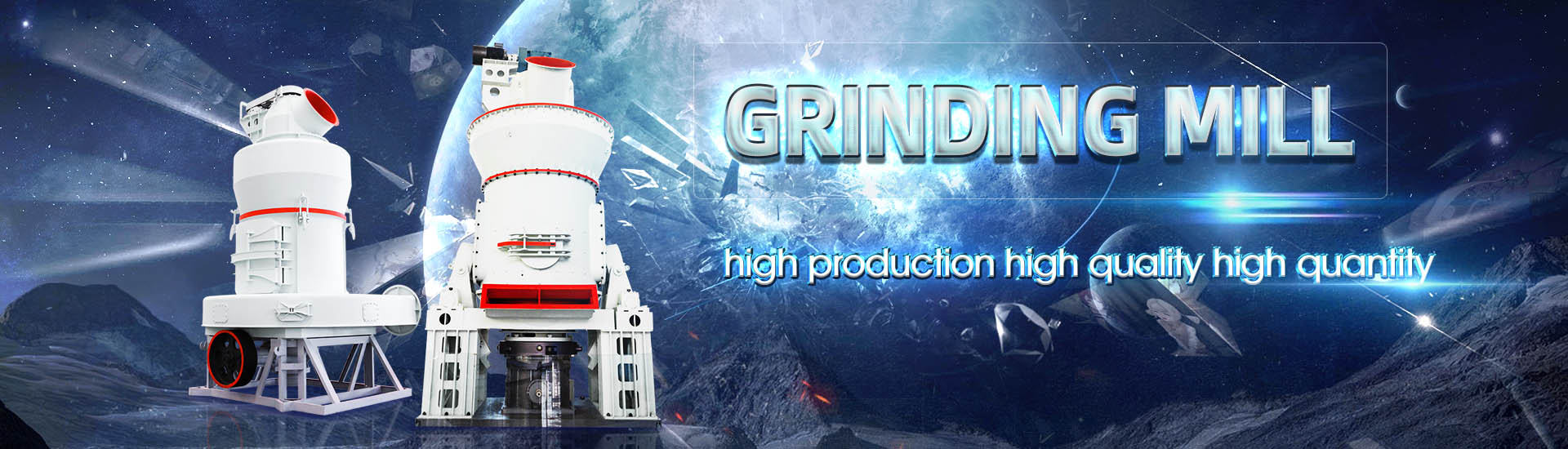
silica grinding production line coarse particles by classification
.jpg)
Silica Powder Processing TechnologyALPA POWDER
particles that meet particle size requirements are through classifier wheel and collected by cyclone and bag filter; the coarse powder drop to the milling area and continue to be milled GRINDING CLASSIFYINGThe milled materials rise to the classification area with air flow, the coarse and fine powder are separated under strong centrifugal force generated by the highspeed rotating classification ALPA Silica Powder Processing Technology DirectIndustry2023年4月28日 The design of a multivortex classifier–separator significantly affects the production of granulometric fractions of silica gel particles Moreover, the fractional Effect of the Design of a MultiVortex Classifier–Separator on the 2020年10月1日 In this paper, we report on a detailed experimental analysis of the longterm grinding behavior of silica sand as a model material in an oscillatory ball mill for a broad range Evolution of grinding energy and particle size during dry ball
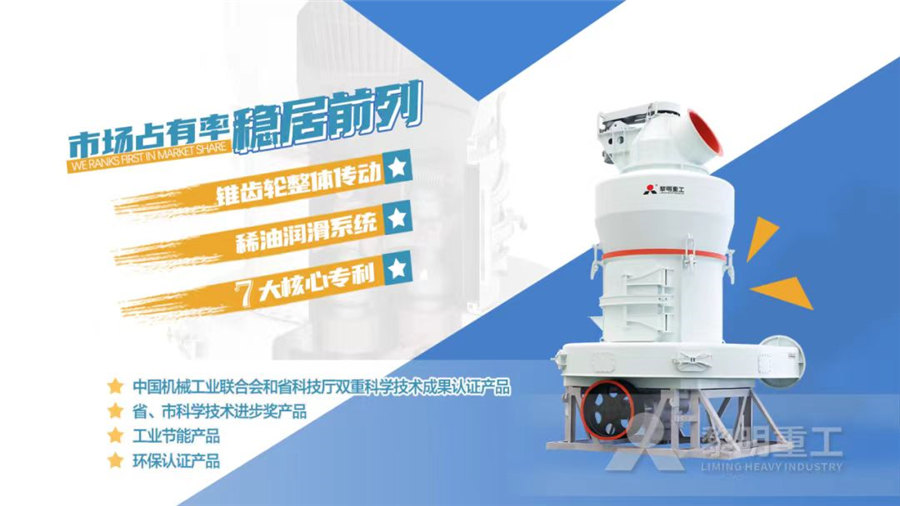
SILICA SAND: FOUNDRY REQUIREMENTS AND CLASSIFICATION
In this study, several silica sand samples from six locations in Terengganu’s state have been investigated for the potential of Terengganu’s silica for foundry use The important properties The qualified fine powder is collected by cyclone collector or dust collector, The coarse particles after classification are discharged from the lower end of the classifier, and then reenter the Ball Mill and Air Classifier Production Line ALPA Powder2017年9月1日 This paper aims to explore these observations further, focusing on the two fine grinding devices and the breakage mechanisms therein, size by size shape characteristics Fine grinding: How mill type affects particle shape characteristics 2023年7月27日 Spherical particles with coarse particles and high density settle rapidly in the medium, while particles with fine particles, low density, and irregular shapes settle slowly in Classification of Grinding Products SpringerLink
.jpg)
Investigation of classification alternatives for grinding circuits
2022年6月1日 In the present work, the performance of a silica sand grinding circuit was evaluated Detailed classification tests were performed using a laboratory scale teetered bed 2023年7月27日 In twostage, threestage, or multistage grindingclassification circuit, influenced by ore property and subsequent process requirements, it can be divided into continuous GrindingClassification Circuit SpringerLink2024年2月22日 Here are some common types of silica grinding mill machines: 1 Ball Mill: A traditional cylindricalshaped mill rotating on its axis, containing steel balls as grinding media Silica is fed into the mill along with the balls, and Silica Powder Grinding Mill MachinesHere are some common types of silica grinding mill machines: 1 Ball Mill: A traditional cylindricalshaped mill rotating on its axis, containing steel balls as grinding media Silica is fed into the mill along with the balls, and as the mill rotates, the grinding media crushes the Silica Powder Grinding Mill Machines carbon black process
.jpg)
The Significance of Fine Grinding The Biodynamic Association
silica preparation have been discussed in these pages from a number of diverse points of view (see BIODYNAMICS #238, p 2ff, p 7ff, #239, p 18ff #241, p 19ff) Continuing this theme, the following article offers a comprehensive perspective on the significance of fine grinding in the production of the horn silica preparation2024年5月30日 Quartz Crushing Jaw crushers are the ideal choice for primary crushing of quartz ore, effectively breaking down the highhardness mineral Subsequently, cone crushers (or impact crushers) further reduce the quartz to below 25 mm Quartz Grinding The finely crushed quartz particles are conveyed by bucket elevators to storage bins, then fed into quartz ball Quartz Processing Mastering the Art of Stone to PowderClassification is the term for industrially sorting particles into different After grinding, the particle size distribution changed to that shown in Figure 113 Clearly, the two different types of plastic displayed different behaviour during crushing Both were crushed: the coarse end of the distribution shown in Figure 112 has 11 Crushing and classificationIn silica sand production line, tormmel screen is often used in combination with hydraulic classifier to control large particle materials Working principle of trommel screen Trommel screen is mainly composed of motor, reducer, trommel, rack, seal cover, inlet and outlet, etcTrommel screenSinonine
.jpg)
(PDF) Classification of Particles Dispersed by Bead Milling Using
2009年10月20日 Classification of Particles Dispersed by Bead Milling Using Electrical FieldFlow FractionationSTOT RE 1, if the crystalline silica (fine fraction) concentration is equal to, or greater than 10% (w/w); STOT RE 2, if the crystalline silica (fine fraction) concentration is between 1,0 and 10% (w/w) If the crystalline silica (fine fraction) content in mixtures and substances is below 1,0% (w/w), no classification is requiredREACH classification and labelling Safe SilicaLab 3 – Particle Size Reduction, Screening and Size Analysis Objective: To 1 examining the particle size reduction of coarse clayey samples using primary, secondary crushing and grinding methods and 2 subsequent separation and size analysis of the obtained polydispersed powders Materials and Equipment 1 Silica sand 2 Balance 3 Sieves 4Lab 3 – Particle Size Reduction, Screening and Size Analysis2024年1月1日 However, in the actual classification, the particle swarm cannot be separated strictly according to the particle size Coarse and fine particles tend to be mixed in overflow and sediment, so different indices and methods for evaluating classification efficiency emerge There are four commonly used classification efficiency indicesClassification of Grinding Products SpringerLink

Limestone crushing and grinding production line
2022年4月20日 Classification: Limestone is processed into finished products of various specifications through impact crushing according to user requirementsThe particle shape is good and can be classified by vibrating 01 Production Background The ball mill classification production line consists of two main equipment: ball mill and air flow classifier The ball mill adds abrasives and liquid so that the main machinery of the ball mill rubs and impacts the raw materials Ball Mill With Classification Production Lineadvantage of this benefit primarily due to the limitation of froth flotation to recover coarse particles New separation technologies for coarse particle recovey have begun to address this limitation, causing major mining companies to seriously evaluate the Coarser Grinding: Economic Benefits and Enabling CiDRAParticles larger than 300 μm however become increasingly difficult to float and to retain in the froth phase For plants using hydrocyclones for classification, the distribution of silica is not even throughout the particle size range The silica often tends to concentrate in (PDF) COARSE AND FINE PARTICLE FLOTATION Academia
.jpg)
BY Carl K Ishito Satoshi Akiyama Dr Zennosuke Tanaka
Using new classification and grinding technology, we discuss the improvement of the classification and grinding performance This discussion includes closed loop grinding classification systems, classification with improved dispersion mechanism and other topics Powder to be discussed in this paper is mainly toner :An air classifier can precisely, predictably, and efficiently sort particles by mass, resulting in a coarse particle fraction and a fine particle fraction A variety of classification rotor are available, and the output can be adjusted; speed of wheel is controlled by Spiral Jet Mill Supplier EPIC Powder Machinery2022年5月22日 In the following, based on the dry grinding method of silica ore, the production process of producing silica by pickling method will be described in detail (1) Silica ore impurity removing The dry ground silica sand is sent to a dry magnetic separator for magnetic separation through a closed belt conveyor to remove Fe2O3 in the silica sandSilica Concentrate Produced by Dry Grinding and Picklingclassification and grinding condition Using new classification and grinding technology, we discuss the improvement of the classification and grinding performance This discussion includes closed loop grinding classification systems, classification with improved dispersion mechanism and other topics Powder to be discussed in this paper is mainlyTHE IMPROVEMENT OF GRINDING AND USING CLOSED CIRCUIT
.jpg)
Hydrocyclone classification optimization using real time coarse
classification of mineral slurries by particle size One input stream is separated into two output streams; an underflow of coarse particles that undergo additional grinding, and an overflow stream of finer particles that typically goes directly into a flotation circuit for recovery of the desiredSilica Particle Size Reduction Ultrafine Grinding and Classifying Production Line, Find Details and Price about Silica Particle Size Reduction Air Classifying Mill Production Line from Silica Particle Size Reduction Ultrafine Grinding and Classifying Production Line Shandong ALPA Powder Technology Co, LtdSilica Particle Size Reduction Ultrafine Grinding and Classifying Shape of particles made by grinding is one of the important measures for determining the utilizations of industrial minerals namely barite, calcite, and talc particles, particularly at production The classification by roundness and sphericity in the 2022年3月18日 A threestage method (grinding, roasting and digestion) was adopted to study the effect of particle size on the desulfurization rate and digestion performance of highsulfur bauxite in the process of producing alumina The results demonstrated that the desulfurization efficiency of coarsegrained bauxite was significant by roasting, the sulfur content of raw ores The Desulfurization and Digestion Property of HighSulfur

Hindered settling machineSinonine
The Hindered settling classifier makes use of the rising water to form turbulent flow in the container, which makes the large or relatively large particles concentrate to the bottom of the container and discharge from the bottom Download scientific diagram Particle size distributions of coarse silica sand (CSS), fine silica sand (FSS) and their mixtures at fine silica sand contents (F s ) of 10%, 20%, 30%, 40% and 50% Particle size distributions of coarse silica sand (CSS), fine silica 2022年4月1日 Beneficiation plants must face up to several serious challenges due to falling mine cutoff grades, including substantial increase in throughputs, extremely fine grinding necessities, massive production of ultrafine particles, progressively dropping mineral liberation degrees, inefficiency of classification apparatuses, maintenance issues and deleterious Technological assessments on recent developments in fine and coarse Silica sand processing equipment In the silica sand production line, Jaw Crusher is the coarse silica sand crushing machine, Impact Crusher and Cone Crusher is the fine sand crusher VSI Crusher is the sand making machine used for sizing and shapingsilica sand grades size chart Grinding Mill China
.jpg)
FineMilling and Air Classification of Ceramic Materials by the
2014年7月12日 In this article, modern methods of fine milling and air classification of materials by the dry method, making possible precise sizing of particles as well as clean processing of the initial product without foreign impurities, are presented Special wearresistant construction of the working units permits the finest milling and classification of even the hardest materials, 2016年11月1日 Grinding is the main process used to control the particle size distribution of SCBA and mitigate the negative effect of the crystalline compounds on its reactivity [3], [5], [6]There are many advantages of ultrafine grinding, especially associated with an increase in specific surface area [4], [5], [6] and introduction of imperfections or active centers on the Improved pozzolanic activity of sugar cane bagasse ash by 2006年10月1日 This paper presents the experimental results of the mechanical production of silica and carbonate colloidal particles below 100 nm using two types of stirred bead mills (ie, DCP Superflow 12 and Production of Carbonate and Silica NanoParticles in Stirred 2005年4月1日 In the dry grinding process, fugitive dust is easily created When people inhale the fine dust of crystalline silica, it can lead to silicosis, a potentially fatal lung disease Wet grinding not only eliminates fugitive dust but also gives higher grinding efficiency The coarse oversize particles have to be separated out and sent back for Classification of silica fine particles using a novel electric
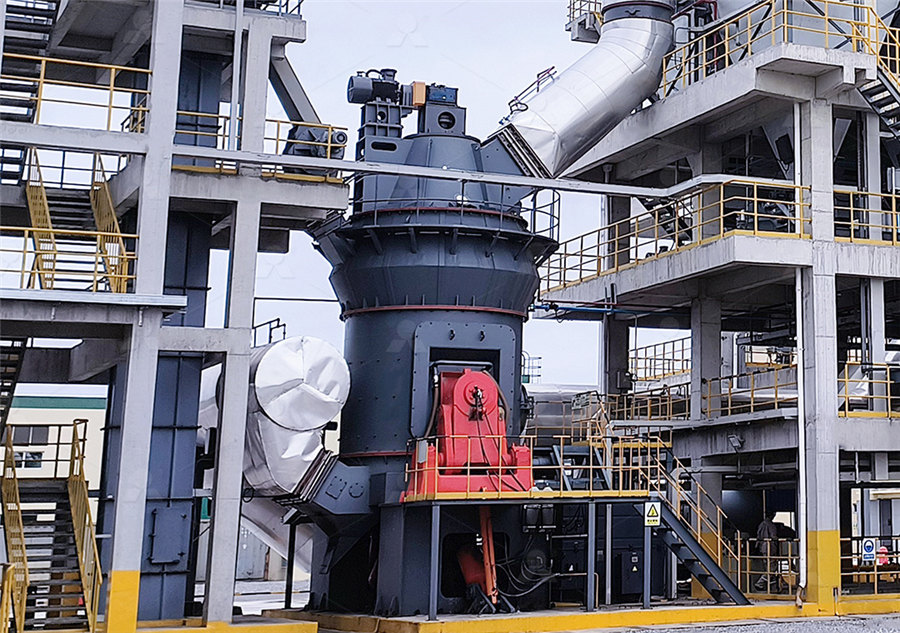
Silica Powder Grinding Mill Machines
2024年2月22日 Here are some common types of silica grinding mill machines: 1 Ball Mill: A traditional cylindricalshaped mill rotating on its axis, containing steel balls as grinding media Silica is fed into the mill along with the balls, and Here are some common types of silica grinding mill machines: 1 Ball Mill: A traditional cylindricalshaped mill rotating on its axis, containing steel balls as grinding media Silica is fed into the mill along with the balls, and as the mill rotates, the grinding media crushes the Silica Powder Grinding Mill Machines carbon black processsilica preparation have been discussed in these pages from a number of diverse points of view (see BIODYNAMICS #238, p 2ff, p 7ff, #239, p 18ff #241, p 19ff) Continuing this theme, the following article offers a comprehensive perspective on the significance of fine grinding in the production of the horn silica preparationThe Significance of Fine Grinding The Biodynamic Association2024年5月30日 Quartz Crushing Jaw crushers are the ideal choice for primary crushing of quartz ore, effectively breaking down the highhardness mineral Subsequently, cone crushers (or impact crushers) further reduce the quartz to below 25 mm Quartz Grinding The finely crushed quartz particles are conveyed by bucket elevators to storage bins, then fed into quartz ball Quartz Processing Mastering the Art of Stone to Powder
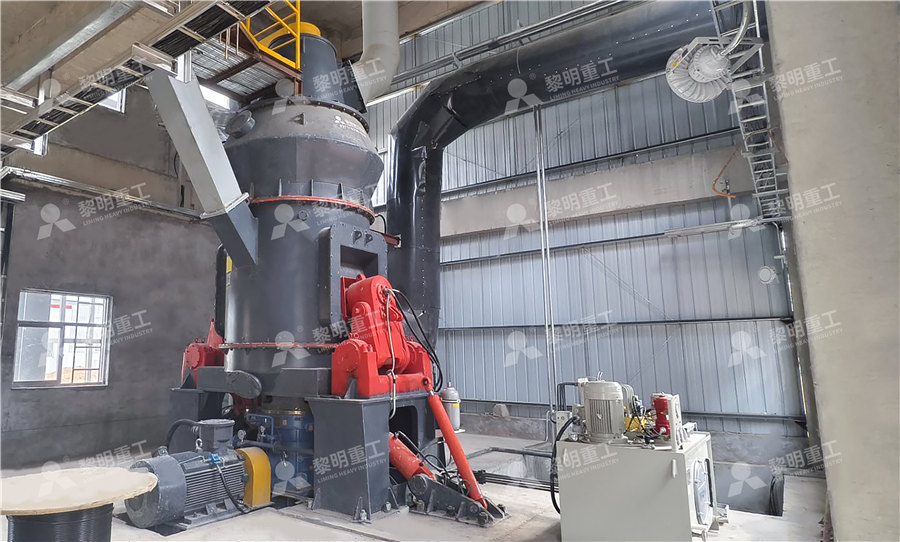
11 Crushing and classification
Classification is the term for industrially sorting particles into different After grinding, the particle size distribution changed to that shown in Figure 113 Clearly, the two different types of plastic displayed different behaviour during crushing Both were crushed: the coarse end of the distribution shown in Figure 112 has In silica sand production line, tormmel screen is often used in combination with hydraulic classifier to control large particle materials Working principle of trommel screen Trommel screen is mainly composed of motor, reducer, trommel, rack, seal cover, inlet and outlet, etcTrommel screenSinonine2009年10月20日 Classification of Particles Dispersed by Bead Milling Using Electrical FieldFlow Fractionation(PDF) Classification of Particles Dispersed by Bead Milling Using STOT RE 1, if the crystalline silica (fine fraction) concentration is equal to, or greater than 10% (w/w); STOT RE 2, if the crystalline silica (fine fraction) concentration is between 1,0 and 10% (w/w) If the crystalline silica (fine fraction) content in mixtures and substances is below 1,0% (w/w), no classification is requiredREACH classification and labelling Safe Silica
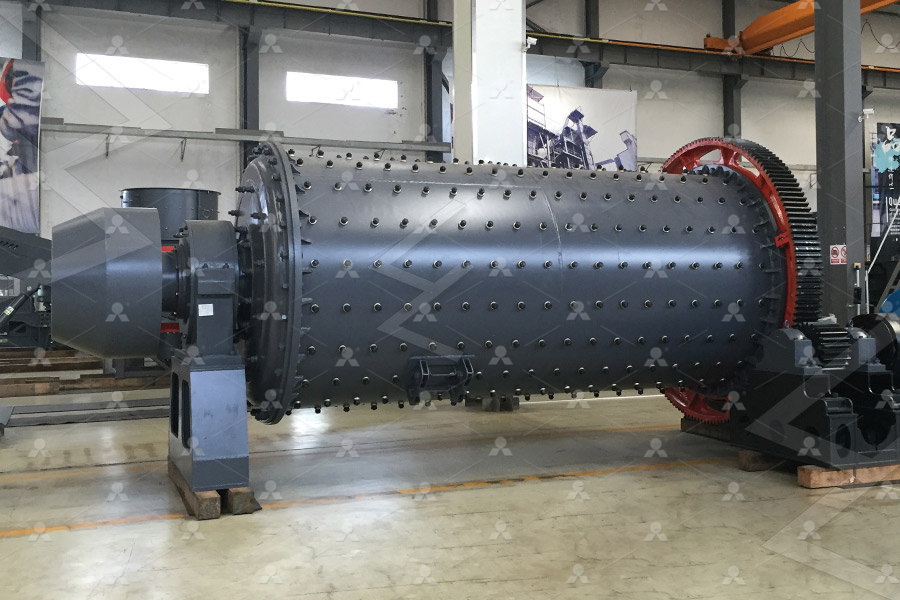
Lab 3 – Particle Size Reduction, Screening and Size Analysis
Lab 3 – Particle Size Reduction, Screening and Size Analysis Objective: To 1 examining the particle size reduction of coarse clayey samples using primary, secondary crushing and grinding methods and 2 subsequent separation and size analysis of the obtained polydispersed powders Materials and Equipment 1 Silica sand 2 Balance 3 Sieves 42024年1月1日 However, in the actual classification, the particle swarm cannot be separated strictly according to the particle size Coarse and fine particles tend to be mixed in overflow and sediment, so different indices and methods for evaluating classification efficiency emerge There are four commonly used classification efficiency indicesClassification of Grinding Products SpringerLink