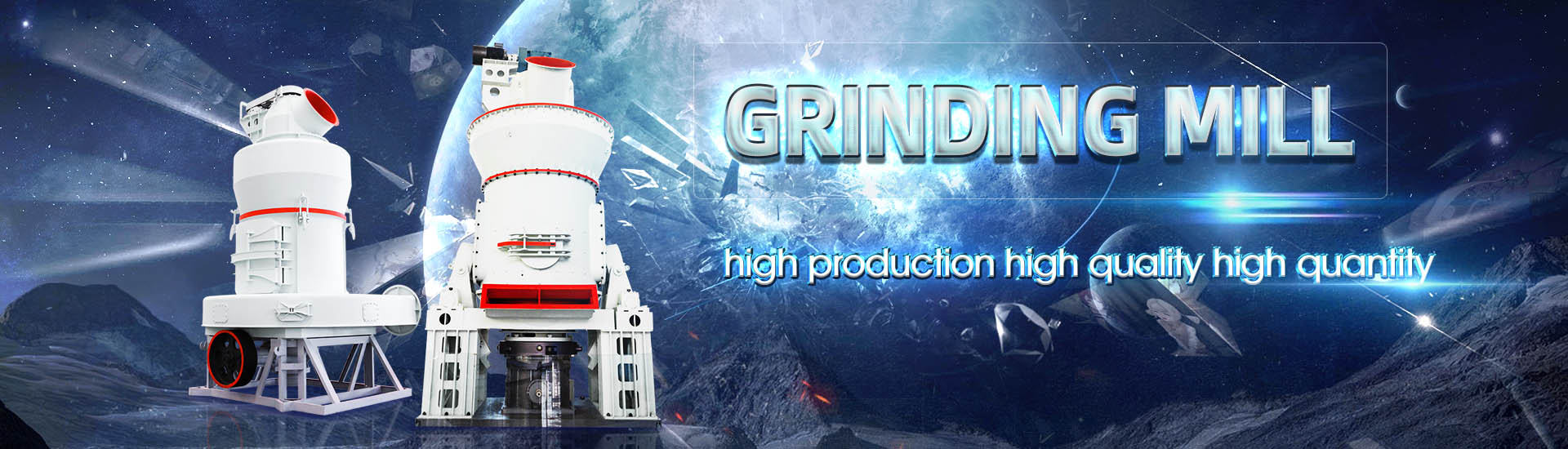
Ultraprecision grinding
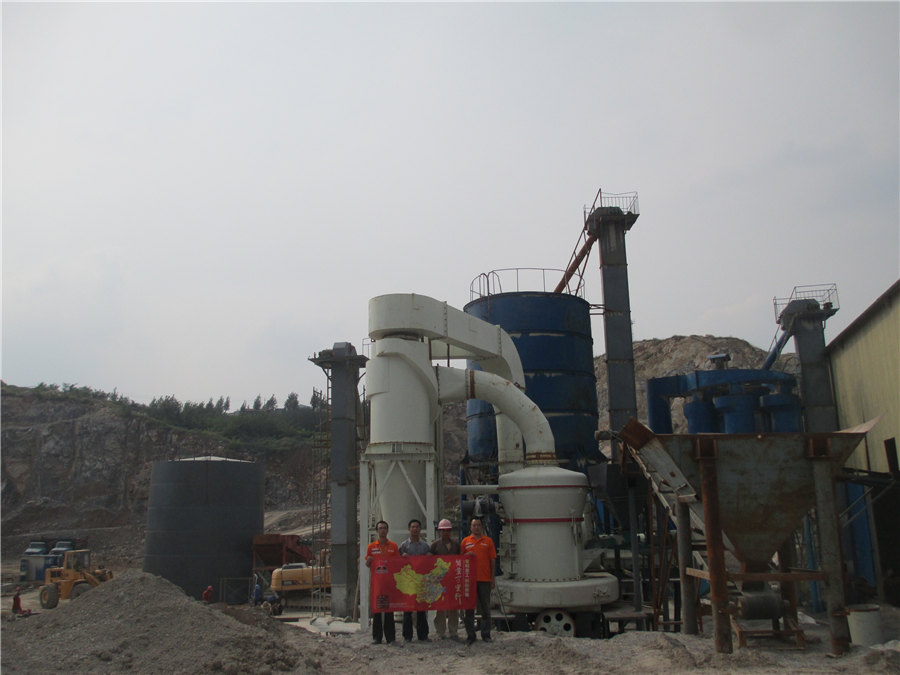
Ultraprecision grinding ScienceDirect
2010年1月1日 Ultraprecision grinding is primarily used to generate high quality and functional parts usually made from hard and difficult to machine materials The objective of ultra 2017年6月9日 The conception, applications and history of ultraprecision machining are introduced in this article, and the developments of ultraprecision machining technologies, especially ultraprecision grinding, ultraprecision Review on the progress of ultraprecision machining 2019年7月1日 Ultraprecision grinding is an abrasive process, providing high surface quality but hardly up to that of ultraprecision diamond cutting It is primarily adopted for machining Advances in ultraprecision machining of microstructured 2018年11月27日 Ultraprecision grinding machine design and application in grinding the thinwalled complex component with small ballend diamond wheel ORIGINAL ARTICLE; Ultraprecision grinding machine design and application in
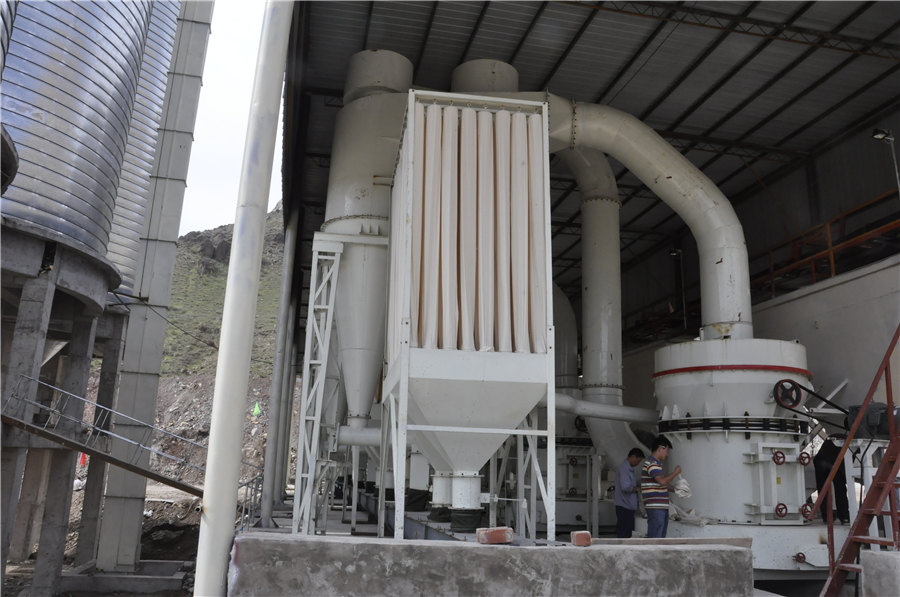
Ultraprecision grinding and polishing processing
2023年4月25日 Whether the fine grinding process can obtain better surface shape accuracy and low surface/subsurface damage suppression determines the processing efficiency, and the ultraprecision processing manufacturing This paper presents advanced tools for ultra precision grinding which offer a high wear resistance and can be used to generate highquality parts with an ultraprecise surface finish The first Ultraprecision grinding Semantic ScholarUltraprecision grinding is primarily used to generate high quality and functional parts usually made from hard and difficult to machine materials The objective of ultraprecision grinding is Ultraprecision grinding 百度学术We report on the development of a novel industrial process, embodied in a new robotic polishing machine, for automatically grinding an polishing aspheric optics The machine is targeted at [PDF] Ultraprecision grinding and polishing processing
.jpg)
Grinding Ultra Precision Fives Group
OVER 120 YEARS OF EXPERIENCE delivering exceptional precision, reliability and performance DIVERSE GRINDING TECHNOLOGIES to2024年11月1日 25D carbon fiber reinforced silicon carbide composites (25DC f SiCs) are extensively applied in the aerospace industry based on excellent properties However, surface quality is an important challenge This study proposes a new method to improve the surface quality by coating the surface with resin and extending the surrounding edges, followed by Ultraprecision grinding damage suppression strategy for 25D 2021年6月12日 With the development of machine tools, conventional grinding has evolved into ultraprecision grinding Ultraprecision grinding, as an efficient and economical manufacturing technology for optical elements, is an important technology for generating optics with low surface roughness, high form accuracy and high surface integrity [16,17,18,19,20 Experimental study on surface integrity and subsurface SpringerLarge optical freeform grinding components The Cranfield Precision OGM delivers ultraprecision freeform grinding of large optic components Featuring ultimate stiffness and thermal stability, the OGM has the flexibility to meet the needs of your highend optics application for components up to 2,500mm Cranfield Precision OGMUltraprecision machining from industry leader Cranfield Precision
.jpg)
Advances in ultraprecision machining of microstructured functional
2019年7月1日 Ultraprecision grinding is an abrasive process, providing high surface quality but hardly up to that of ultraprecision diamond cutting It is primarily adopted for machining difficulttocut materials with a grinding wheel of frequentlyused diamond or cubic boron nitride grits [15]Ultraprecision polishing is also an abrasive process for machining difficulttocut materials 2020年10月29日 Ultraprecision grinding is a common method to obtain high quality surfaces It is widely used in the area of large wafer thinning and optical elements manufacturing The working principle of ultraprecision grinding is removing the material by means of rotation motion and axial feed motion of the grinding wheel UltraPrecision Machining Technologies Encyclopedia MDPI2022年11月23日 Freeform optics made of hard and brittle materials possesses the reflection and imaging functions that are difficult to be achieved by traditional optics and are widely used in various high energy space optical systems However, freeform optics made of hard and brittle materials poses great challenges to ultraprecision machining due to its extreme demands of Ultraprecision Ductile Grinding of OffAxis Biconical FreeForm 2017年6月9日 Ultraprecision machining technologies are the essential methods, to obtain the highest form accuracy and surface quality As more research findings are published, such technologies now involve complicated systems engineering and been widely used in the production of components in various aerospace, national defense, optics, mechanics, Review on the progress of ultraprecision machining technologies
.jpg)
Residual stress and subsurface damage in sapphire ultraprecision grinding
2024年7月1日 Understanding residual stress is crucial for guiding the ultraprecision machining process In ultraprecision grinding, lattice stresses on the grinding surface impact the geometric accuracy of the component, while surface quality is determined by defects in the crystalline surface (Choudhary et al, 2021; Piao et al, 2024)Chemical etching has been employed to 2022年5月15日 Ultraprecision grinding based on the wafer selfrotation principle is essential for rapidly removing silicon material during blank wafer fabrication and patterned wafer backthinning [4], [5] The cup wheel is used as the grinding tool, while the diamond grains on the wheel surface deform the silicon material to produce chips [6]The material removal and surface generation mechanism in ultra grinding: technology and requirements, concept of critical depth of cut, sizeeffect in form and fine grinding, Elid grinding, Elastic emission grinding; mechanochemical polishing of Si wafers, principles and models; Ultraprecision polishing: Principles of ultraprecision polishing of block gauges, balls and aspherical lenses Course StructureME 730: UltraPrecision Machining IIT Bombay2019年10月1日 Ultraprecision grinding is an efficient method for finishing the surface of hard and brittle materials to optical level [[14], [15], [16], [17]]The mechanisms during ultraprecision grinding are mainly related to the material removal modes, such as ductile removal, brittle fracture, and phase transformation, etc, which are crucial to the surface quality [[18], [19], Ultraprecision grinding of AlON ceramics: Surface finish and
.jpg)
Surface and subsurface microscopic characteristics in sapphire ultra
2022年10月1日 As a matter of fact, in the MPCM, the accumulated material removal depth of ultraprecision grinding was only 125 µm, which was less than the subsurface damage depth (20 µm) generated by rough grinding as shown in Fig 18 a, so the subsurface damage observed after ultraprecision grinding was actually generated by the rough grinding with D25 wheelMany years of expertise in ultraprecision machining For more than 30 years, Fraunhofer IPT has been researching the machining of components with diamond tools, especially ultraprecision milling, grinding and turningUltraprecision machining Fraunhofer IPTGrinding Ultra Precision 法孚将参展2024中国制动年会暨展览会,期待您的莅临! 法孚将参展于2024年10月2324日(周三至周四)在中国上海汽车会展中心举办的2024中国制动年会暨展览会,法孚展位:236。Grinding Ultra Precision Fives Group2024年1月17日 Ultraprecision grinding allows for smaller grinding depths, feed speed, and grit sizes, and the fully hydrostatic grinding system provides better system rigidity and vibration absorption [27] As a result, ultraprecision grinding offers superior damage suppression and favors the generation of ductile grinding surfacesStudy on subsurface damage behavior in ductile ultraprecision grinding
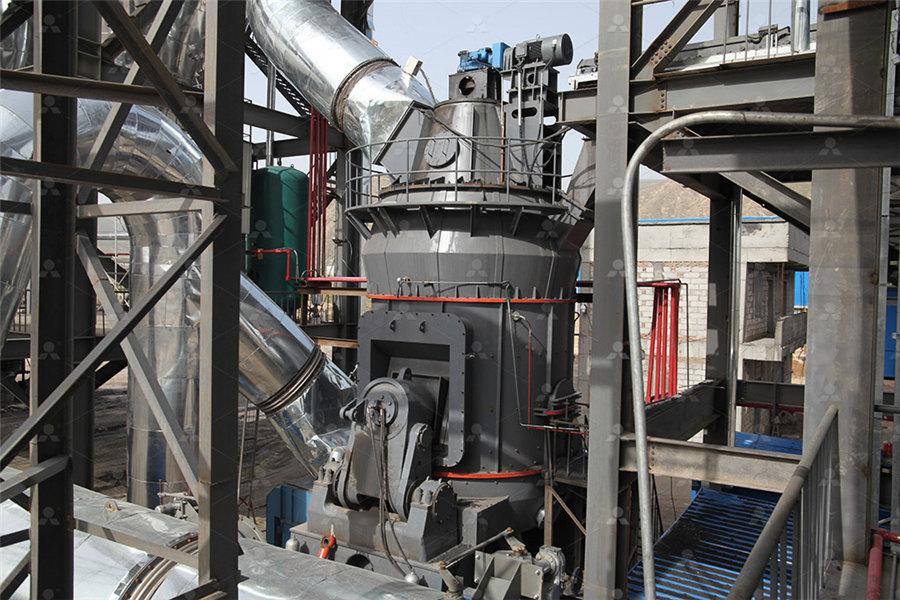
Grinding marks on ultraprecision grinding spherical and aspheric
2017年10月7日 Grinding marks are regard as a great obstacle to manufacture spherical and aspheric surfaces with higher surface quality, lower energy and wastage The scallopheight was studied for optimizing the grinding parameters firstly to reduce its effect on grinding marks Secondly, the expression of grinding points distribution was established to characterize the Ultraprecision grinding is primarily used to generate high quality and functional parts usually made from hard and difficult to machine materials The objective of ultraprecision grinding is to generate parts with high surface finish, Ultraprecision grinding 百度学术2018年12月31日 Here, the ultraprecision grinding of hard and brittle materials with coarsegrained grinding wheels was investigated in order to reveal the performance of these coarsegrained grinding wheels 31 Ductile Grinding Mechanism of Conditioned CoarseGrained WheelsUltraprecision Machining of Hard and Brittle Materials with It features a single molding chamber with a 170mm diameter capacity This machine complements Nanotech’s 450UPL and 650FG systems which can be configured for ultraprecision grinding of mold components in various materials such as WC and SiC Together, the combination of systems forms a next generation glass press molding cellNanotech Ultraprecision Machining Systems
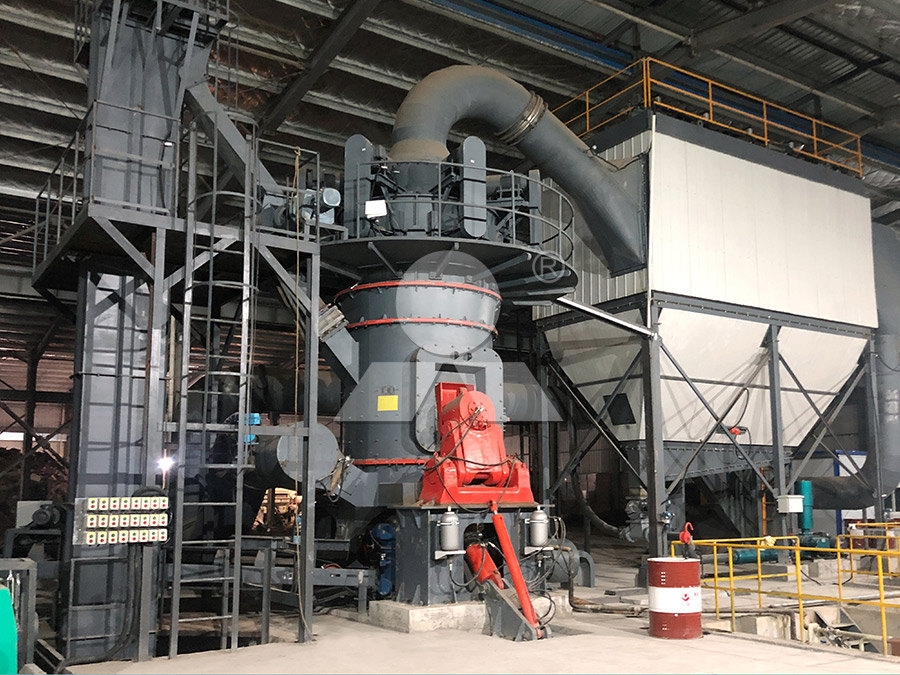
Freeform optics grinding for highend optics and
With high stiffness, damping, and thermal stability built in, the Cranfield Precision TTG is the ultraprecision aspheric and freeform optics grinding solution Engineered specifically for speciality optics and molds, medical and 2023年3月24日 The process of sapphire ultraprecision grinding can be regarded as the result of the joint action of the massive number of single abrasive grains scratching, and its material removal mechanism can be explained by the action of single abrasive grain cutting as Evaluation of grinding characteristics for sapphire ultraprecision This ultraprecision grinding machine uses a combination of mechanical and electrical methods to achieve a highly accurate and smooth surface finish on the workpiece Here is a breakdown of the main steps: Workpiece Setup: • The workpiece is securely mounted on the machine table using a fixture or chuckUltraPrecision Grinding MachineWe are not just another grinding shop We are a passionate team of smart solution finders obsessed with every detail Besides producing a reliably high level of quality work, our ultraprecision centerless grinding services always come with an unmatched level of responsiveness attuned to your C Precision Centerless Grinding Companies Guidewire Grinding
.jpg)
Ultraprecision grinding machine design and application in grinding
2018年11月27日 Zhong ZW, Venkatesh VC (2009) Recent developments in grinding of advanced materials Int J Adv Manuf Technol 41:468–480 Article Google Scholar Shore P, Morantz P, Luo X, Tonnellier X, Collins R, Roberts A, MayMiller R, Read R (2005) Big OptiX ultra precision grinding/measuring system Proc SPIE 5965:241–248Ultra Precision Machining and Grinding is an ISO 9001: 2015 AS9100D certified machine shop specializing in government contract work Ultra Precision Machining is your onestopshop for precision machined parts and small assemblies Our manufacturability expertise often results in cost savings for our customersMachine Shop in Palm Bay, FL Ultra Precision Machining1998年1月1日 Ultraprecision grinding system of noneaxissymmetric aspherical surface was developed In this system, a resinoid bonded diamond wheel was scanned on the workpiece surface 3dimentionally (PDF) Study on UltraPrecision Grinding of Micro Aspherical Surface 2023年8月4日 Ultraprecision grinding technology has a long history and is mature up to now, such as the OAGM 2500 from CUPE (Cranfield unit of precision engineering) in the UK, which can achieve ultraprecision grinding of optical components with a size of 25 m and a flatness of 1 μm when grinding flat surfaces [6], [7]At present, for commercial ultraprecision grinding Ultraprecision timecontrolled grinding for flat mechanical parts
.jpg)
Productive Modes for UltraPrecision Grinding of Freeform Optics
[1] Shore P, Morantz P Ultra Precision – ”enabling our future”, Trans Royal Society, Phil Trans R Soc A 2012 370 39934014 [2] Tonnellier X, Shore P, Morantz P Subsurface damage evaluation in grinding of 2008, 8486 [3] Tonnellier T, Howard K, Morantz P, Shore P Surface integrity of precision groundOVER 120 YEARS OF EXPERIENCE delivering exceptional precision, reliability and performance DIVERSE GRINDING TECHNOLOGIES toGrinding Ultra Precision Fives Group2024年11月1日 25D carbon fiber reinforced silicon carbide composites (25DC f SiCs) are extensively applied in the aerospace industry based on excellent properties However, surface quality is an important challenge This study proposes a new method to improve the surface quality by coating the surface with resin and extending the surrounding edges, followed by Ultraprecision grinding damage suppression strategy for 25D 2021年6月12日 With the development of machine tools, conventional grinding has evolved into ultraprecision grinding Ultraprecision grinding, as an efficient and economical manufacturing technology for optical elements, is an important technology for generating optics with low surface roughness, high form accuracy and high surface integrity [16,17,18,19,20 Experimental study on surface integrity and subsurface Springer
.jpg)
Ultraprecision machining from industry leader Cranfield Precision
Large optical freeform grinding components The Cranfield Precision OGM delivers ultraprecision freeform grinding of large optic components Featuring ultimate stiffness and thermal stability, the OGM has the flexibility to meet the needs of your highend optics application for components up to 2,500mm Cranfield Precision OGM2019年7月1日 Ultraprecision grinding is an abrasive process, providing high surface quality but hardly up to that of ultraprecision diamond cutting It is primarily adopted for machining difficulttocut materials with a grinding wheel of frequentlyused diamond or cubic boron nitride grits [15]Ultraprecision polishing is also an abrasive process for machining difficulttocut materials Advances in ultraprecision machining of microstructured functional 2020年10月29日 Ultraprecision grinding is a common method to obtain high quality surfaces It is widely used in the area of large wafer thinning and optical elements manufacturing The working principle of ultraprecision grinding is removing the material by means of rotation motion and axial feed motion of the grinding wheel UltraPrecision Machining Technologies Encyclopedia MDPI2022年11月23日 Freeform optics made of hard and brittle materials possesses the reflection and imaging functions that are difficult to be achieved by traditional optics and are widely used in various high energy space optical systems However, freeform optics made of hard and brittle materials poses great challenges to ultraprecision machining due to its extreme demands of Ultraprecision Ductile Grinding of OffAxis Biconical FreeForm
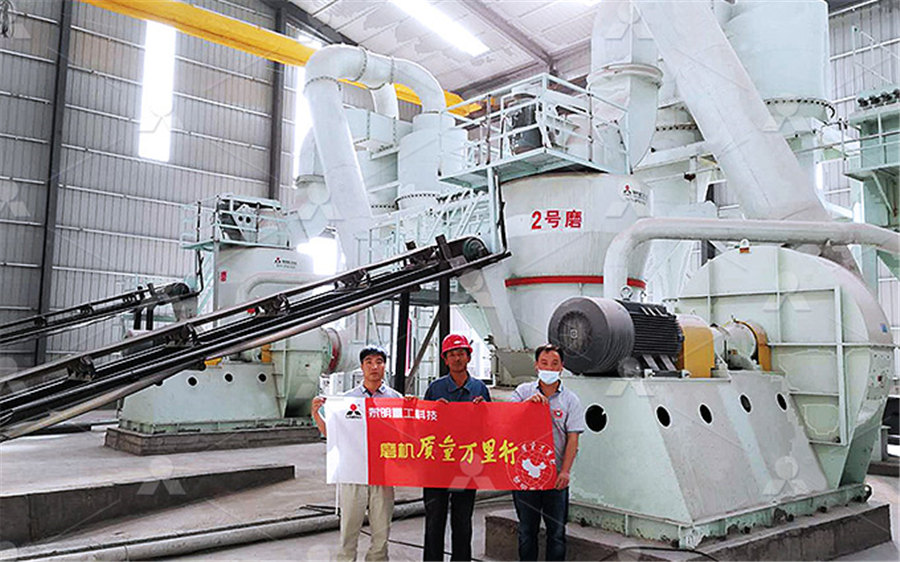
Review on the progress of ultraprecision machining technologies
2017年6月9日 Ultraprecision machining technologies are the essential methods, to obtain the highest form accuracy and surface quality As more research findings are published, such technologies now involve complicated systems engineering and been widely used in the production of components in various aerospace, national defense, optics, mechanics, 2024年7月1日 Understanding residual stress is crucial for guiding the ultraprecision machining process In ultraprecision grinding, lattice stresses on the grinding surface impact the geometric accuracy of the component, while surface quality is determined by defects in the crystalline surface (Choudhary et al, 2021; Piao et al, 2024)Chemical etching has been employed to Residual stress and subsurface damage in sapphire ultraprecision grinding2022年5月15日 Ultraprecision grinding based on the wafer selfrotation principle is essential for rapidly removing silicon material during blank wafer fabrication and patterned wafer backthinning [4], [5] The cup wheel is used as the grinding tool, while the diamond grains on the wheel surface deform the silicon material to produce chips [6]The material removal and surface generation mechanism in ultra