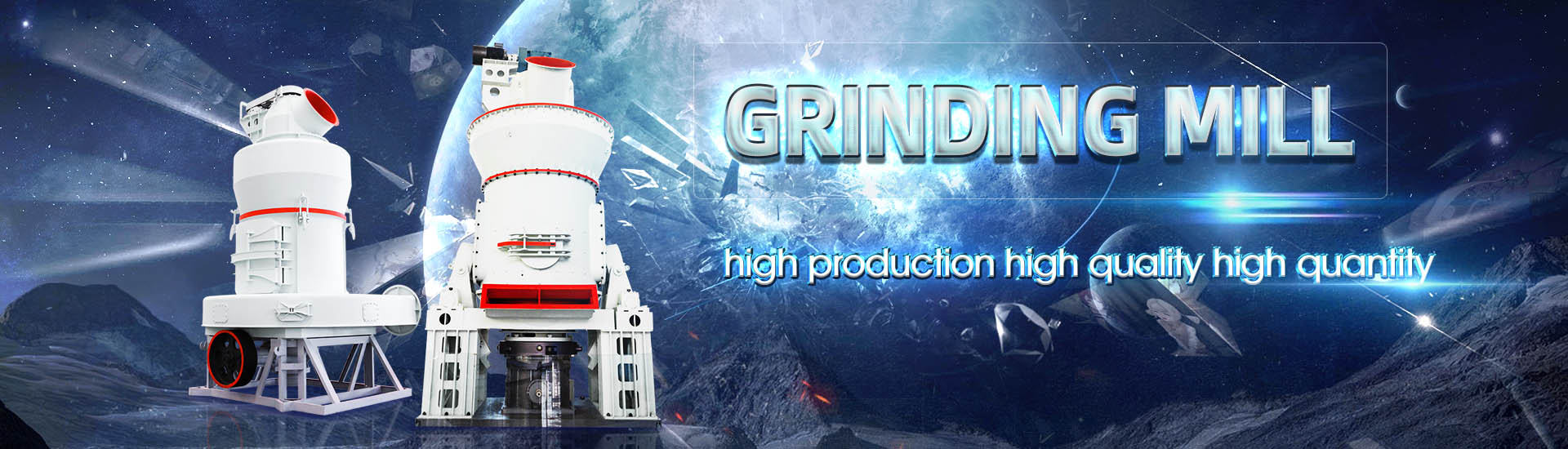
Electrolytic aluminum overhaul slag grinding machine
.jpg)
Research Progress of Electrolytic Aluminum Overhaul Slag Disposal
2023年4月25日 This article analyzes and summarizes the composition and hazards of the overhaul slag and the current development status of domestic and international electrolytic 2024年2月1日 In this paper, an innovative process of sulfuric acid roasting and water leaching is proposed, which can efficiently and environmentally recover F, Al and Li from overhaul slag A novel approach for extracting lithium from overhaul slag by low 2024年2月1日 The electrolytic aluminum industry generates a large amount lithium (Li)containing electrolytic aluminum slag (EAS) annually, and this can result in severe Efficient lithium recovery from electrolytic aluminum slag via an 2022年10月10日 In this work, electrolytic aluminum carbon anode slag was separated by flotation Using the selectivity index ( SI ) as an indicator, the influencing factors of the carbon Recovery of carbon and cryolite from spent carbon anode slag of
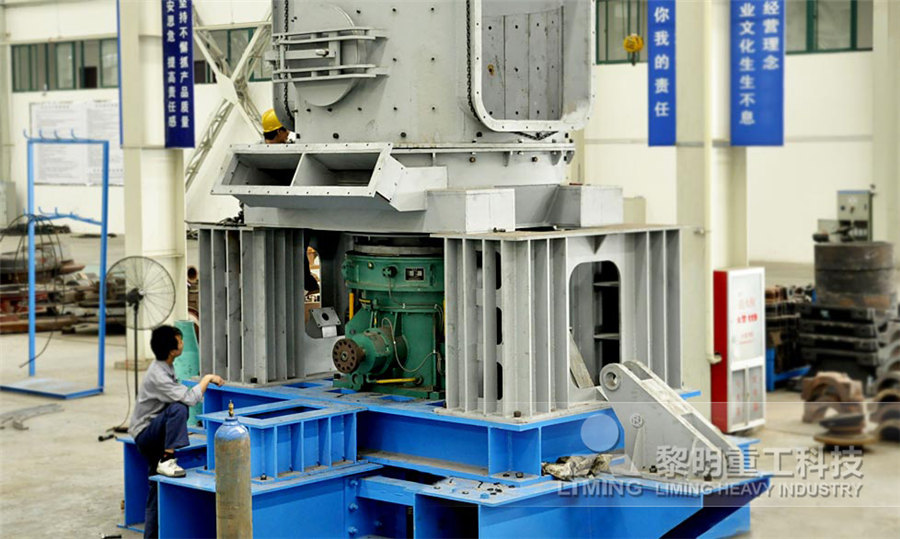
(PDF) Study on Harmless and Resources Recovery Treatment
2012年12月31日 Spent pot lining (SPL) is a hazardous solid waste generated after overhauling the aluminum electrolytic cell SPL contains carbon resources with high graphitization and 2024年7月24日 The lithium was selectively recovered and enriched from spent aluminum electrolyte slag by using calcium salt roasting transformation followed by HBL121solvent Cleaner Process for the Selective Extraction of Lithium from Spent 2023年4月25日 This article analyzes and summarizes the composition and hazards of the overhaul slag and the current development status of domestic and international electrolytic 电解铝大修渣处置研究进展This article analyzes and summarizes the composition and hazards of the overhaul slag and the current development status of domestic and international electrolytic aluminum overhaul slag 电解铝大修渣处置研究进展
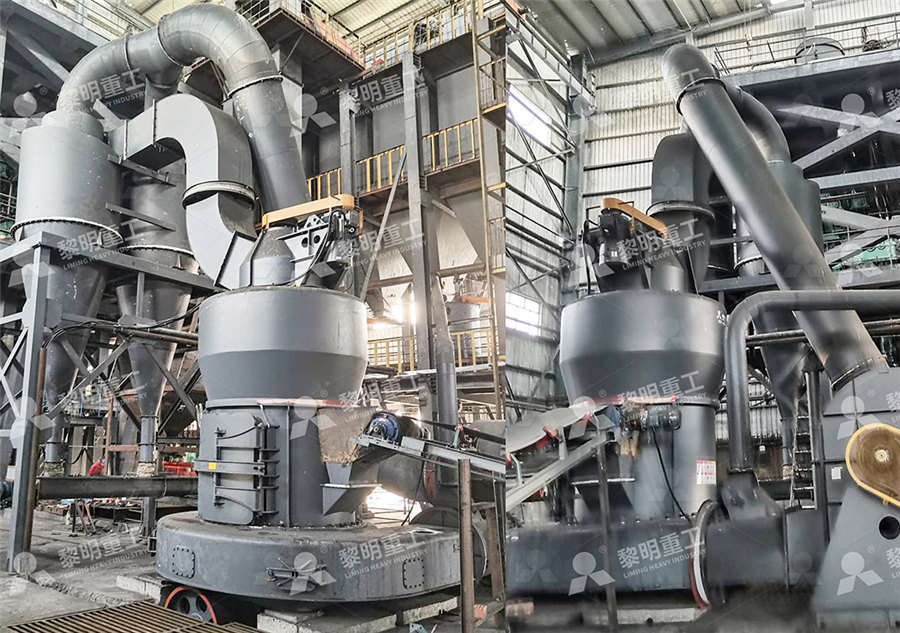
A novel approach for extracting lithium from overhaul slag by low
2024年2月1日 Overhaul slag, as one of the main hazardous solid wastes generated in the electrolytic aluminum, has high research value [12]The electrolytic cell lining is eroded by continuous chemical corrosion of hightemperature molten metal and salt, resulting in expansion and peeling off, leading to low production efficiency and degradation of performance [13]2012年12月31日 An aluminum fluoride film covered by graphite fluoride on metallic aluminum was prepared by reaction in the ternary system of aluminum graphite and fluorine gas at 450550 degree C(PDF) Study on Harmless and Resources Recovery 2016年10月24日 The industrial aluminum reduction cell is an electrochemistry reactor that operates under high temperatures and highly corrosive conditions However, these conditions have restricted the measurement of key control parameters, making the control of aluminum reduction cells a difficult problem in the industry Because aluminum electrolysis control Progress in Aluminum Electrolysis Control and Future Direction 2024年2月1日 Overhaul slag, as one of the main hazardous solid wastes generated in the electrolytic aluminum, has high research value [12] The electrolytic cell lining is eroded by continuous chemical corrosion of hightemperature molten metal and salt, resulting in expansion and peeling off, leading to low production efficiency and degradation of performance [13]A novel approach for extracting lithium from overhaul slag by low
.jpg)
Selective preparation of lithium carbonate from overhaul slag by
2024年5月1日 Fig 2 (a) shows that the ΔG θ of fluorine, aluminum and lithium in the overhaul slag reacting with sulfuric acid is less than zero at 600 °C–900 °C, indicating that fluorine can volatilize in the form of HF, and aluminum and lithium can transfer into soluble matter in 2014年1月1日 Experimental setup for ELID grinding of silicon wafer, proposed by Ohmori, H; Nakagawa, T Mirror Surface Grinding of Silicon Wafers with Electrolytic Inprocess Dressing Ann CIRP 1990, 39 (1 Electrolytic InProcess Dressing (ELID) Grinding for Nano 2020年4月7日 ZG35Cr25Ni20 electrolytic aluminum slag grab, with its excellent high temperature resistance and corrosion resistance, is unique in the electrolytic aluminum industry The grapple is made of highquality 310S heatresistant steel castings, which maintain excellent stability in hightemperature environments, ensuring that the grapple can operate stably in Electrolytic Aluminum Slag Grab Sino Machine2024年5月1日 Selective preparation of lithium carbonate from overhaul slag by high temperature sulfuric acid roasting 2018) Lithium has important applications in many industries, such as electronics, chemicals, medicine, aerospace, and machinery manufacturing (Zhang et al, 2018) Especially in modern In electrolytic aluminum, Selective preparation of lithium carbonate from overhaul slag by
.jpg)
A novel approach for lithium recovery from waste lithium
2021年10月1日 Meanwhile, when the highlithium alumina is added into the aluminum electrolytic cell, separation of chromium and vanadium by calcification roasting–sodium carbonate leaching from high chromium vanadium slag and V 2 O 5 preparation Sep Pirif Technol, 230 (2020), p , 101016/jseppur2019 View PDF View article electrolytic aluminum production process, including waste cathode carbon block, waste anode material Generally, electrolytic aluminum production enterprises will overhaul the electrolytic cell every five years, with a large amount of waste generated in this process Electrolytic aluminum scrap mainly contains NaF, Na 3 AlF 6, CaF 2Research on the Coprocessing of Mixed Electrolytic Aluminum Request PDF On Feb 1, 2024, Liangmin Dong and others published A novel approach for extracting lithium from overhaul slag by low temperature roasting – water leaching Find, read and cite all A novel approach for extracting lithium from overhaul slag by low 2023年3月12日 Aluminum has a variety of uses in the building, transportation, electric power, packaging, national security, and hightech industries due to its unique chemical and physical properties []Cryolitealumina molten salt Recovery of Carbon and Cryolite from Spent Carbon
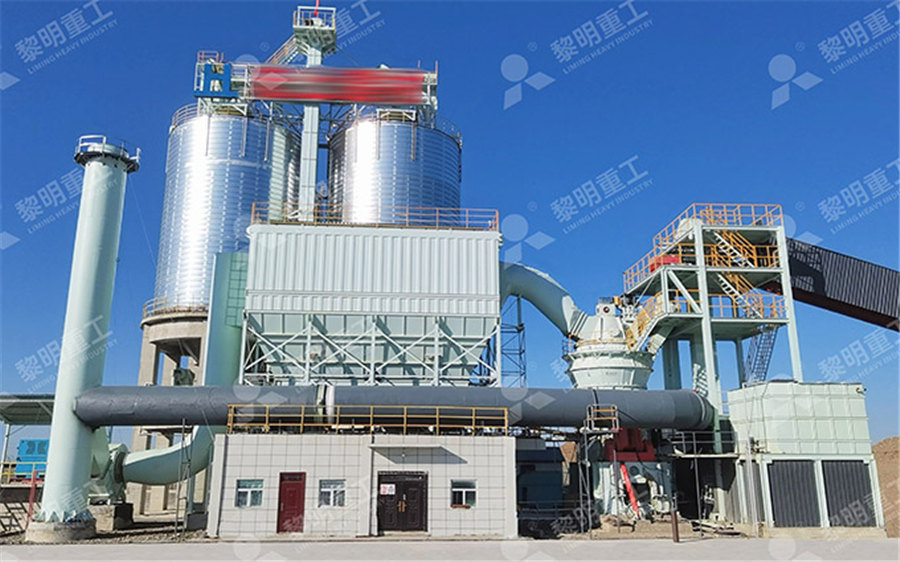
LectroPol electrolytic preparation equipment
A timesaving automatic microprocessorcontrolled machine for electrolytic polishing and etching of metallographic specimens A highthroughput semiautomatic grinding/polishing machine with up to 350 mm (14”) dia disc size 2021年6月16日 Aluminum and aluminum alloys are among the most used metals in fabrication,construction, and in the creation of good all around you It is such a useful and versatile metal, but there are some special considerations you need to make when working with it We have put together this expert guide to fabricating, grinding, and finishing aluminum to Ultimate Guide – Aluminum Fabrication, Grinding, and Finishing During a longterm operation of the aluminum electrolysis cell, the molten salts continuously infiltrate and corrode the pot lining, resulting in a huge amount of hazardous waste after the overhaulElectrolytic cell spent lining Fig 2 Overhaul slags of the On August 2nd, China Nonferrous Metals Industry Association organized an expert meeting on scientific and technological achievements in Kunming, Yunnan Province, and completed the “electrolytic aluminum overhaul slag” jointly completed by Zhengzhou Hongyue Environmental Protection Technology Co, Ltd, Hunan Zhongda Metallurgical Design Co, Ltd and Electrolytic aluminum overhaul slag harmless technology

A Review of Electrolytic InProcess Dressing (ELID) Grinding
ELID Grinding, since its introduction over two decades ago, has helped in material removal of hard and difficulttocut engineering materials A gist of the important research milestones on the process has been organized in this report The hybrid process of ELID Grinding has a simultaneous electrolytic reaction and grinding action2023年3月12日 The aluminum electrolysis industry continually and unavoidably produces hazardous solid waste in the form of carbon anode slag Carbon anode slag poses a serious environmental pollution risk, and (PDF) Recovery of Carbon and Cryolite from Spent Carbon Anode Slag 2022年1月10日 Selective comminution and grinding mechanisms of spent carbon anode from aluminum electrolysis using ball and rod mills January 2022 Physicochemical Problems of Mineral Processing 58(3):Selective comminution and grinding mechanisms of spent carbon 2024年2月1日 The electrolytic aluminum industry generates a large amount lithium (Li)containing electrolytic aluminum slag (EAS) annually, and this can result in severe environmental pollution and wasting of Li resources This paper proposes a method for recovering Li from the slag using AlCl 3 as the leaching agent The effects of the leaching temperature, AlCl 3 Efficient lithium recovery from electrolytic aluminum slag via an
.jpg)
Grinding Slag Removal Apex Machine Group
These services also help processing operations meet deadlines with minimal risk of failure and downtime To meet our clients’ needs, the professionals at Apex Machine Group offer dependable grinding and slag removal solutions What Is Grinding Slag Removal? Slag is a specific type of sand that’s traditionally made from steel2022年10月10日 Recovery of carbon and cryolite from spent carbon anode slag of electrolytic aluminum by flotation based on the evaluation of selectivity index Yemin Wang, 1 Xuexia Wang, 1 , * and The sample was ground to −0074 mm using an HLXPMΦ120 × 3 threeheaded grinding machine (Wuhan Hengle Mineral Engineering Equipment Co, Ltd Recovery of carbon and cryolite from spent carbon anode slag of A highthroughput semiautomatic grinding/polishing machine with up to 350 mm (14”) dia disc size for fast and efficient preparation For special investigations on aluminumbased materials, an electrolytic etching forming an anodized Metallographic etching insight Struers2024年1月1日 @article{Cui2024EfficientLR, title={Efficient lithium recovery from electrolytic aluminum slag via an environmentally friendly process: Leaching behavior and mechanism}, author={Li Cui and Weihong Wang and Xi Chao and Jianming Gao and Fangqin Cheng}, journal={Journal of Cleaner Production}, year= {2024 Efficient lithium recovery from electrolytic aluminum slag via an

What is Electrochemical Grinding and How it’s done?
A circular metal plate serves as the grinding wheel and consists of abrasive particles of diamond dust, aluminum oxide, boron carbide, and silicon carbide When, between the grinding wheel and the workpiece, electrolytic fluid is pumped, there is a reactionThe results showed that apart from the overhaul slag of electrolytic cell, unorganized flue gas and carbon slag were the key points of fluoride emission in electrolytic aluminum production The fluoride content of unorganized flue gas was 0374 kg/t per unit product, which was about 37 times of that of organized emissionsResearch on fluoride wholeprocess prevention and control in the 2009年1月1日 Electrolytic inprocess dressing (ELID) grinding and electrodischarge machining (EDM) are among major nontraditional machining processes used in manufacturing industriesA Review of Electrolytic InProcess Dressing (ELID) Grinding2024年6月6日 These protruding abrasive particles also remove the unactive layers formed on the work by abrasion to make the surface more receptive It can be seen that the process is similar to conventional grindingIn that, an abrasive grinding wheel is used and the work is fed against the rotating wheel 10% of the work metal is removed by abrasive cutting, and 90% by Electrochemical Grinding: Parts, Working, Application, Advantages
.jpg)
Research on the Coprocessing of Mixed Electrolytic Aluminum
electrolytic aluminum production process, including waste cathode carbon block, waste anode material Generally, electrolytic aluminum production enterprises will overhaul the electrolytic cell every five years, with a large amount of waste generated in this process Electrolytic aluminum scrap mainly contains NaF, Na 3 AlF 6, CaF 22023年10月1日 Abundant carbon resides in spent cathode carbon (SCC) of aluminum electrolysis and its highpurity carbon powder is conducive to highvalue recyclingHarmless recovery and utilization of electrolytic aluminum spent 2024年2月1日 Overhaul slag, as one of the main hazardous solid wastes generated in the electrolytic aluminum, has high research value [12]The electrolytic cell lining is eroded by continuous chemical corrosion of hightemperature molten metal and salt, resulting in expansion and peeling off, leading to low production efficiency and degradation of performance [13]A novel approach for extracting lithium from overhaul slag by low 2012年12月31日 An aluminum fluoride film covered by graphite fluoride on metallic aluminum was prepared by reaction in the ternary system of aluminum graphite and fluorine gas at 450550 degree C(PDF) Study on Harmless and Resources Recovery
.jpg)
Progress in Aluminum Electrolysis Control and Future Direction
2016年10月24日 The industrial aluminum reduction cell is an electrochemistry reactor that operates under high temperatures and highly corrosive conditions However, these conditions have restricted the measurement of key control parameters, making the control of aluminum reduction cells a difficult problem in the industry Because aluminum electrolysis control 2024年2月1日 Overhaul slag, as one of the main hazardous solid wastes generated in the electrolytic aluminum, has high research value [12] The electrolytic cell lining is eroded by continuous chemical corrosion of hightemperature molten metal and salt, resulting in expansion and peeling off, leading to low production efficiency and degradation of performance [13]A novel approach for extracting lithium from overhaul slag by low 2024年5月1日 Fig 2 (a) shows that the ΔG θ of fluorine, aluminum and lithium in the overhaul slag reacting with sulfuric acid is less than zero at 600 °C–900 °C, indicating that fluorine can volatilize in the form of HF, and aluminum and lithium can transfer into soluble matter in Selective preparation of lithium carbonate from overhaul slag by 2014年1月1日 Experimental setup for ELID grinding of silicon wafer, proposed by Ohmori, H; Nakagawa, T Mirror Surface Grinding of Silicon Wafers with Electrolytic Inprocess Dressing Ann CIRP 1990, 39 (1 Electrolytic InProcess Dressing (ELID) Grinding for Nano
.jpg)
Electrolytic Aluminum Slag Grab Sino Machine
2020年4月7日 ZG35Cr25Ni20 electrolytic aluminum slag grab, with its excellent high temperature resistance and corrosion resistance, is unique in the electrolytic aluminum industry The grapple is made of highquality 310S heatresistant steel castings, which maintain excellent stability in hightemperature environments, ensuring that the grapple can operate stably in 2024年5月1日 Selective preparation of lithium carbonate from overhaul slag by high temperature sulfuric acid roasting 2018) Lithium has important applications in many industries, such as electronics, chemicals, medicine, aerospace, and machinery manufacturing (Zhang et al, 2018) Especially in modern In electrolytic aluminum, Selective preparation of lithium carbonate from overhaul slag by 2021年10月1日 Meanwhile, when the highlithium alumina is added into the aluminum electrolytic cell, separation of chromium and vanadium by calcification roasting–sodium carbonate leaching from high chromium vanadium slag and V 2 O 5 preparation Sep Pirif Technol, 230 (2020), p , 101016/jseppur2019 View PDF View article A novel approach for lithium recovery from waste lithium electrolytic aluminum production process, including waste cathode carbon block, waste anode material Generally, electrolytic aluminum production enterprises will overhaul the electrolytic cell every five years, with a large amount of waste generated in this process Electrolytic aluminum scrap mainly contains NaF, Na 3 AlF 6, CaF 2Research on the Coprocessing of Mixed Electrolytic Aluminum