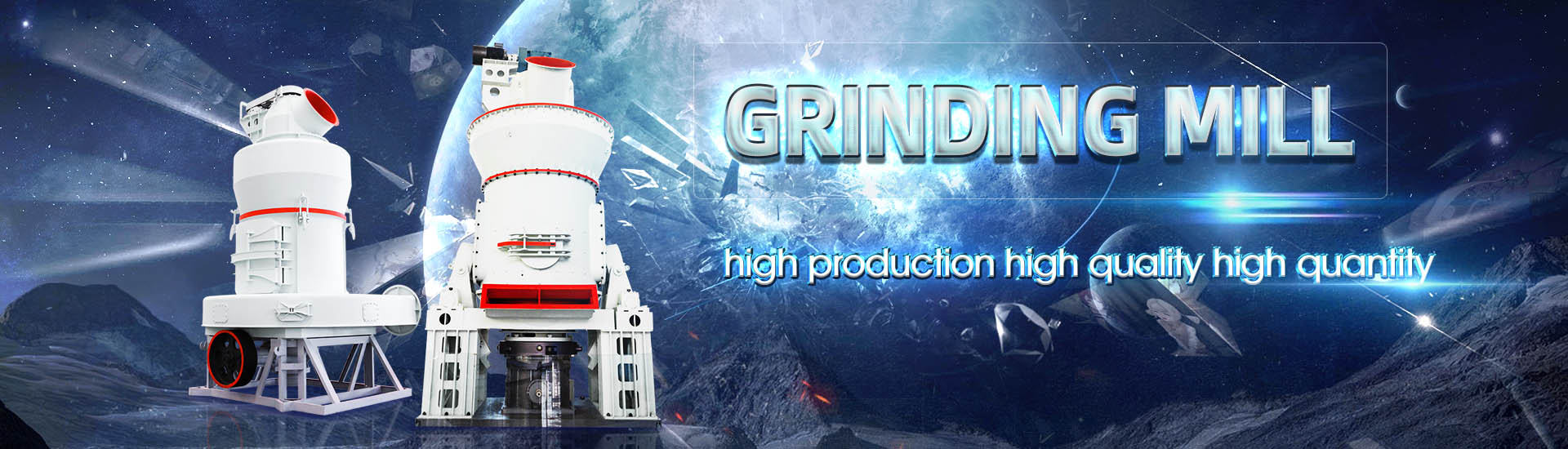
Layer grinding Layer grinding Layer grinding Layer grinding

New layering strategy and the gradient microstructure distribution
2024年1月16日 The grinding surface metamorphic layer needs a certain grinding depth to appear, and the gradient distribution of microstructure in the metamorphic layer is also affected by the grinding depth The increase in grinding depth raises the area of the grinding arc zone, Foeckerer et al developed a triangular heat source model, taking into account grinding forceA study on the grinding subsurface metamorphic layer influencin2023年10月17日 Foeckerer et al developed a triangular heat source model, taking into account grinding force, grinding depth, and feed rate, and examined the influence of microstructure on A study on the grinding subsurface metamorphic layer influencing 2024年10月16日 In the article, the simulation and experiment were used to study the grinding force, grinding temperature field, stress field, strain field, and the characteristics of the Study on the formation of surface affected layer in grinding ultra

Fabrication of a gradient nanomicrostructured surface layer on
2008年9月1日 By using a novel surface nanocrystallization technique, surface mechanical grinding treatment at cryogenic temperatures, we synthesized a gradient nanomicrostructure 2023年12月1日 In this study, we subjected βGa 2 O 3 to deformation using nanoindentation and nanogrinding techniques under gradient loads and various grinding conditions The Abrasive machining induced surface layer damage behavior and 2023年3月1日 Surface formation in laserassisted machining highstrength alloy is revealed Smaller scratching force and improved material removal efficiency is achieved in laser Surface formation in laserassisted grinding highstrength alloys2021年12月14日 As the common final process, grinding can generate special metamorphic layer on the surface of workpiece and change the initial corrosion resistance of workpiece In order Experiment study on the corrosion resistance of the surface
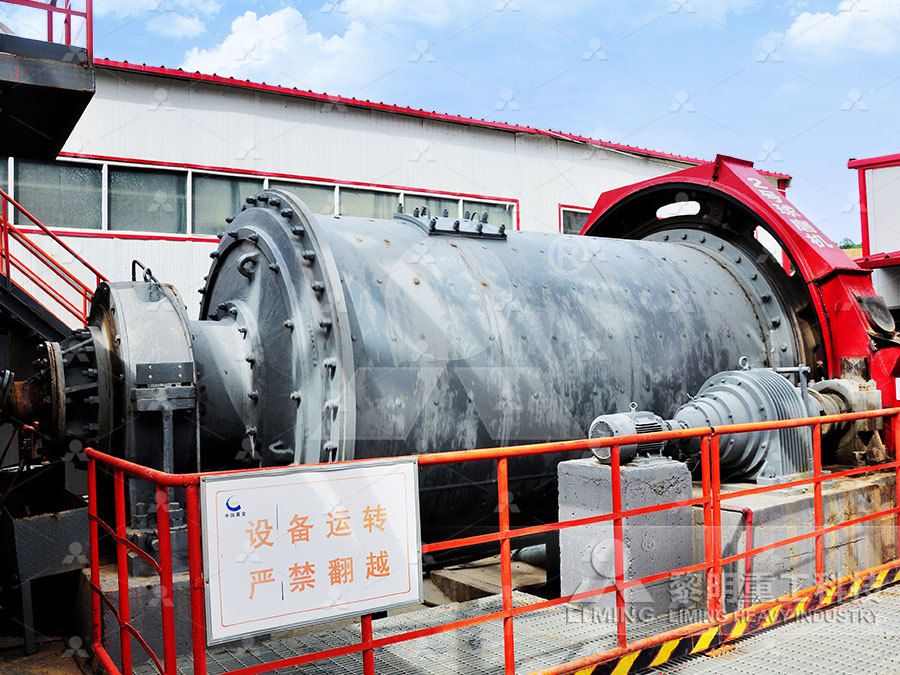
Stereolithography 3D printing gyroid triply periodic minimal
1 天前 By grinding the SiC ceramics, the material removal rate, grinding temperature, The solidified layer thickness was measured by a spiral micrometer DLS (China Deli Group)As the common final process, grinding can generate special metamorphic layer on the surface of workpiece and change the initial corrosion resistance of workpiece In order to study theExperiment study on the corrosion resistance of the surface2024年1月16日 The grinding heat is utilized to induce martensitic phase transformation and strengthen the surface layer of alloy steel by raising surface temperature higher than austenitic New layering strategy and the gradient microstructure distribution 2016年11月1日 Using the largest semiautogenous grinding mill in China as a model, collision energy was analyzed on the basis of the multilayer kinematics of the steel ballsMultilayer kinematics and collision energy in a largescale grinding

A study on the grinding subsurface metamorphic layer
2023年10月17日 Grindingshot peening composite processing will aggravate the shear fracture degree of γ phase and γ′ phase, forming a deeper surface plastic deformation layer; the surface microhardness 2024年10月16日 An affected layer will be formed on workpiece surface in grinding process, which affects the fatigue strength and life The simulation and experiment were used to study the grinding force, grinding temperature field, stress field, strain field, as well as the characteristics of the affected layer (residual stress, microhardness, and microstructure) in grinding AerMet100 Study on the formation of surface affected layer in grinding ultra 2023年3月1日 During the machining of highstrength alloys, the interactions between the tool and workpiece can easily lead to surface alterations over different scales, inducing a series of surface damages [9]When cutting, the crosssection of the machined surface observed via scanning electron microscopy (SEM) can be divided into three layers: a highly perturbed Surface formation in laserassisted grinding highstrength alloys2015年6月20日 In order to improve the grinding surface integrality of the superalloy GH4169, which usually be used in the aeroengine, the metamorphic layer is investigated by optical microscope, transmission Microstructure of Plastic Deformation Layer on Grinding Surface
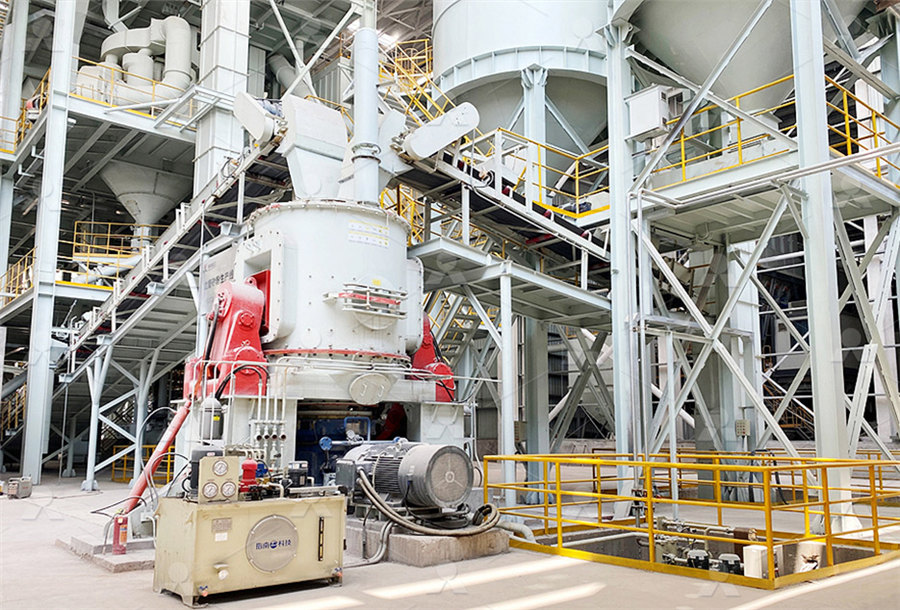
An experimental investigation on surface layer damage in high
2019年11月8日 Rail grinding is an important part of rail maintenance However, the processing efficiency of rail grinding by corundum grinding wheel is low due to the limitation of grinding thermal damage In this work, a slotted singlelayer brazed CBN grinding wheel is used to repair the rail surface replacing corundum grinding wheel, because the CBN abrasive has better heat 2021年7月28日 It was found that the increase in cutting depth and feed speed led to higher level of grinding burn [3] Sun et al [8] reported that a white layer structure was generated on the surface layer Grain refinement mechanism of metamorphic layers by abrasive grinding 2021年4月18日 Carbon nanotubes (CNTs) were added into the electrolyte to improve electrolytic dressing grinding performance of a brazed multilayer diamond wheel containing titanium The effect of CNTs on the electrolytic dressing performance of the grinding wheel was studied The grinding force, residual stress, roughness and morphology of the machined surfaces were Precision grinding of cemented carbides based on a multilayer 2024年3月1日 To achieve efficient grinding, a singlelayer electroplated diamond grinding wheel with a size of φ15 × 12 mm and a grit size of 80# was used in the grinding test In this paper, the process analysis of the rough grinding stage was mainly carried outOptimization of grinding process for hard and brittle materials
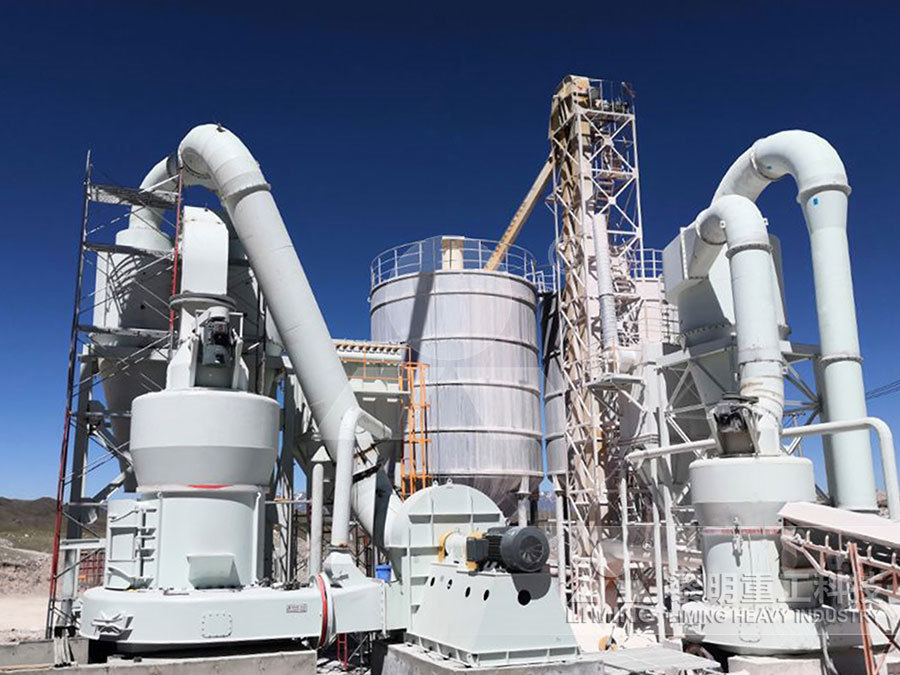
Microstructure Characteristics of the Compound Layer Cracked
2023年4月4日 Download Citation Microstructure Characteristics of the Compound Layer Cracked during Grinding on QPQ‐Treated Cr‐Containing Steel Shafts Cr‐containing structural steels with quench 2015年3月15日 Ground white layer structure is an untempered martensitic due to grinding heat and plastic deformation Many researchers have studied the formation of white layers at low grinding speed However, few studies were found on white layer at high grinding speed Therefore, to minimize white layer, it would be very useful to know the formation of white layer Experimental study on white layers in highspeed grinding of 2021年9月1日 1 Introduction The grinding is a mostly utilized high precision removal method in engineering [[1], [2], [3]], which always generates much heatWhen the machining material is transformed by grinding heat, the abrasive grinding hardening is proposed [4]The material transformation mechanism is based on the machining heat generation, which is like additive Grain refinement mechanism of metamorphic layers by abrasive grinding metamorphic layer of grinding Xiaoliang Shi 1* , Shichao Xiu 1 Xiao Liu 2 Workpiece will face corrosive problems during its application after the manufacturing processExperiment study on the corrosion resistance of the surface
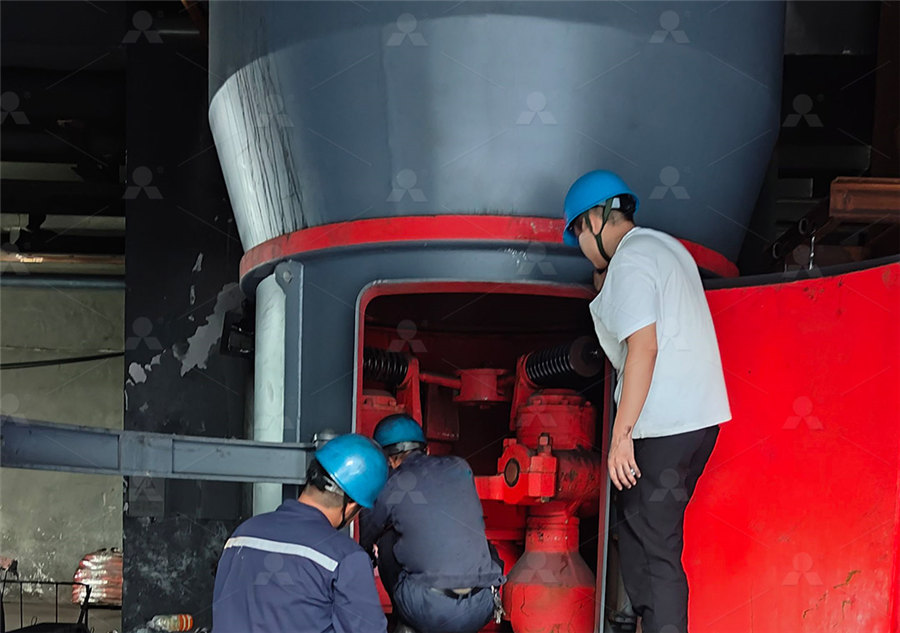
An experimental investigation of affected layers formed in grinding
2011年5月1日 However, few studies were found on white layer at high grinding speed Therefore, to minimize white layer, it would be very useful to know the formation of white layer in the highspeed grinding2017年8月26日 As a relatively new grinding technology, ELID (electrolytic inprocess dressing) is widely used in some businesses The oxide layer plays an important role in ELID grinding performance The purpose of this work is to investigate the state of the oxide layer on ELID grinding wheel surfaces based on workpiececathode and toolcathode The thickness and A comparative study on state of oxide layer in ELID grinding with 2008年7月1日 The properties of the white layer in the surface grinding are described The influences of heat treatment, carbon content and grinding conditions on the white layer formation are discussed It is found that the white layer in the hardened steel is thicker and harder than that in the annealed steel, and there is not a softer transition zone in the annealed steel Higher The Properties and the Influence Factors of the White Layer in the 2017年9月2日 Two types of diamond wheel with a mesh size of 20,000 are developed A novel approach for mechanical chemical grinding (MCG) is proposed using the diamond wheels developed A wear layer of 56 nm in thickness is obtained on a silicon wafer, which is ground by the diamond wheel with ceria at a feed rate of 20 μm/min It consists of an amorphous layer at Nanoscale Wear Layers on Silicon Wafers Induced by Springer

Effect of Grinding Passes on Hardened Layer Uniformity of HT250
2024年2月25日 Huang studied the influence of grinding methods on the grinding of the hardened layer and its uniformity of 65Mn steel, and the results showed that using reverse grinding + downgrinding or downgrinding + reverse grinding + downgrinding could not only increase the depth of the grinding hardened layer, but also improve Microstructure and microhardness are interrelated variables, which remarkably affecting the wear resistance and fatigue life of materials This work aims to establish a relationship between theMicrostructure of Plastic Deformation Layer on Grinding Surface Electrodischarge Grinding: Energy Consumption and Internal Stresses in the Surface Layer AGolabczak, RSwiecik Technical University of Lodz, Department of Production Engineering, Stefanowskiego Electrodischarge Grinding: Energy Consumption and Internal 2022年2月22日 Microstructure and microhardness are interrelated variables, which remarkably affecting the wear resistance and fatigue life of materials This work aims to establish a relationship between the microstructure evolution and microhardness in the grinding surface layer of Inconel 718 The microstructure of the grinding surface layer was characterized by optical Mechanism of gradient strengthening layer formation based on
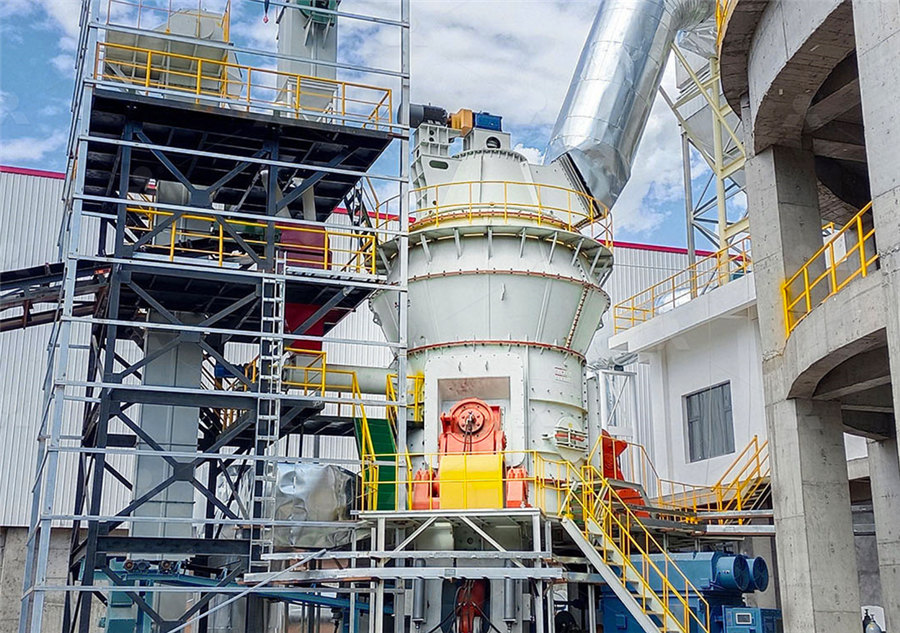
Induction Hardened Layer Characterization and Grinding Burn
2017年3月18日 The quality of the ball screw shafts used in the aeronautical sector has to be controlled and certified with the most advanced nondestructive techniques The capacity of magnetic Barkhausen noise (MBN) as a nondestructive technique to control the quality of ball screw shafts by assuring the appropriate induction hardened layer depth and detecting local 2022年8月17日 Subsurface residual stress and damaged layer play a vital role in determining the accuracy maintenance and fatigue performance of parts Due to the advantages of machining quality and efficiency, highspeed grinding technology is being applied to the machining of precision parts At present, the influence of highspeed grinding on the damaged layers Subsurface residual stress and damaged layer in highspeed grinding 2021年8月30日 Creep feed grinding induced gradient microstructures in the superficial layer of turbine blade root of single crystal nickelbased superalloy, Qing Miao, Wenfeng Ding, Jiuhua Xu, Lijie Cao, Hongcai Wang, Zhen Yin, Chenwei Dai, Weijie Kuang Creep feed grinding induced gradient microstructures in the superficial layer of turbine Creep feed grinding induced gradient microstructures in the 2015年9月14日 Heat flux changes in grindhardening process resulting in uneven distribution of grindhardening layer depth, making it more difficult to produce a hardened layer in the grinding cuttingin and cuttingout area, leading to uneven distribution of the hardening layer depth in grinding stable region This paper firstly studied the grinding force Secondly, grinding The study for variable grinding depth to control plane grind
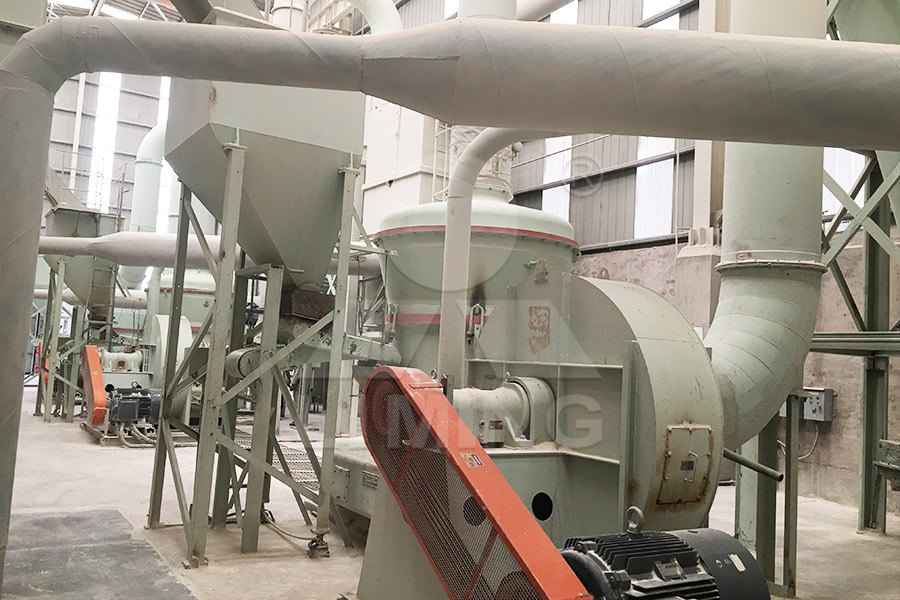
Molecular dynamics study on the thickness of damage layer in
Damage layer Multiple grinding abstract The molecular dynamic (MD) simulation of monocrystalline silicon under multiple grinding is carried out to study the effect of multiple grinding on the thickness of damage layer Four grinding processes are conducted on (0 0 1) along 〈 100〉 direction The depth of grinding of the first grinding is 20 2018年9月1日 In the abrasive grinding hardening (AGH) of metal materials, the microstructure of the surface changes under the action of the intense grinding heat and forms the evolution layer covering the Prediction about ground hardening layers distribution on grinding heataected layers in tooth prole crosssection after gear prole grinding Keywords Gear profile grinding Grinding temperature Heataffected layer Analytic modeling 1 Introduction Gear is one of the most crucial transmission parts in the transmission system Analytical modeling and experimental verification of the depth of 2023年9月4日 In the formula, v s is the wheel speed, v w is the feed rate, a p is the grinding depth, d eq is the diameter of the grinding wheel, and λ s is the perimeter of the grinding wheel 22 Plastic mechanism of subsurface During the grinding process, the workpiece is subject to the tangential force exerted by the abrasive particles, often resulting in subsurface crystal slips Plastic deformation mechanism of grinding subsurface of nickel
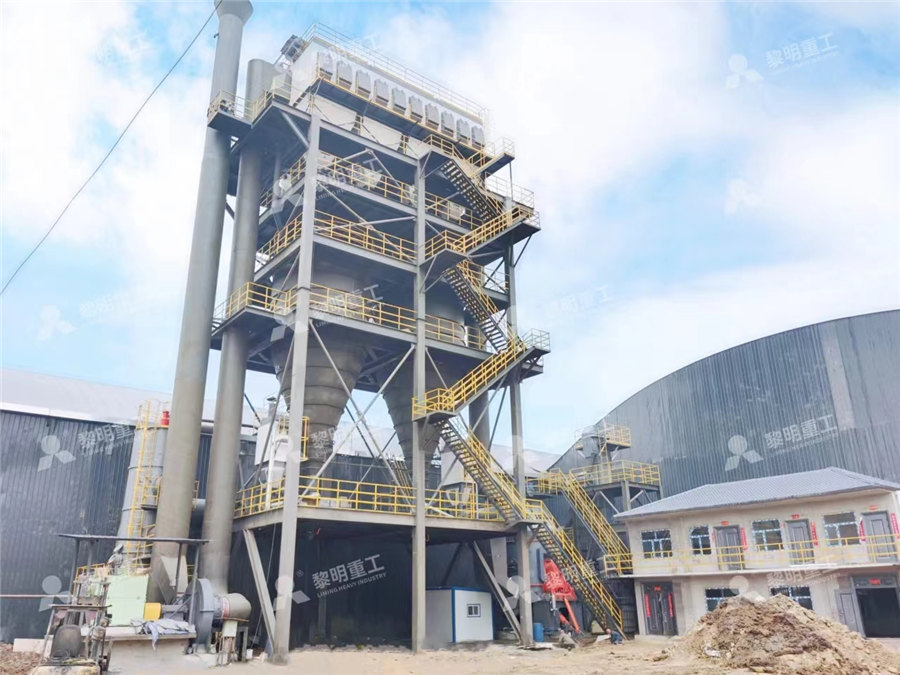
Analytical modeling and experimental verification of the depth of
2022年7月4日 The excessive grinding temperature usually causes grinding burns characterized by hardness change, microstructure change, and residual tensile stress, and the grinding damage commonly exists in a specific depth range below the ground surface In order to examine the depth of the heataffected layer on the gear tooth profile after grinding, the grinding 2016年11月1日 Using the largest semiautogenous grinding mill in China as a model, collision energy was analyzed on the basis of the multilayer kinematics of the steel ballsMultilayer kinematics and collision energy in a largescale grinding 2023年10月17日 Grindingshot peening composite processing will aggravate the shear fracture degree of γ phase and γ′ phase, forming a deeper surface plastic deformation layer; the surface microhardness A study on the grinding subsurface metamorphic layer 2024年10月16日 An affected layer will be formed on workpiece surface in grinding process, which affects the fatigue strength and life The simulation and experiment were used to study the grinding force, grinding temperature field, stress field, strain field, as well as the characteristics of the affected layer (residual stress, microhardness, and microstructure) in grinding AerMet100 Study on the formation of surface affected layer in grinding ultra
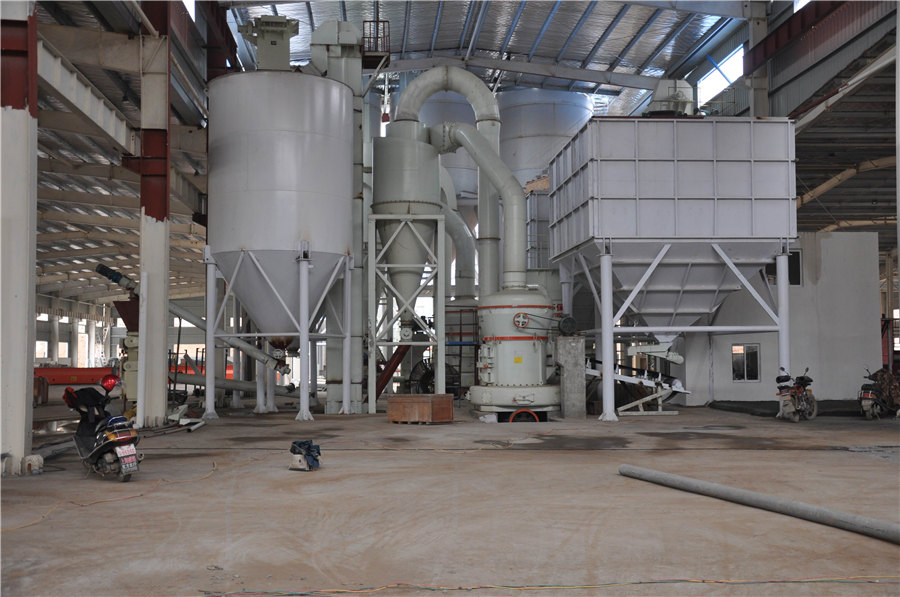
Surface formation in laserassisted grinding highstrength alloys
2023年3月1日 During the machining of highstrength alloys, the interactions between the tool and workpiece can easily lead to surface alterations over different scales, inducing a series of surface damages [9]When cutting, the crosssection of the machined surface observed via scanning electron microscopy (SEM) can be divided into three layers: a highly perturbed 2015年6月20日 In order to improve the grinding surface integrality of the superalloy GH4169, which usually be used in the aeroengine, the metamorphic layer is investigated by optical microscope, transmission Microstructure of Plastic Deformation Layer on Grinding Surface 2019年11月8日 Rail grinding is an important part of rail maintenance However, the processing efficiency of rail grinding by corundum grinding wheel is low due to the limitation of grinding thermal damage In this work, a slotted singlelayer brazed CBN grinding wheel is used to repair the rail surface replacing corundum grinding wheel, because the CBN abrasive has better heat An experimental investigation on surface layer damage in high 2021年7月28日 It was found that the increase in cutting depth and feed speed led to higher level of grinding burn [3] Sun et al [8] reported that a white layer structure was generated on the surface layer Grain refinement mechanism of metamorphic layers by abrasive grinding
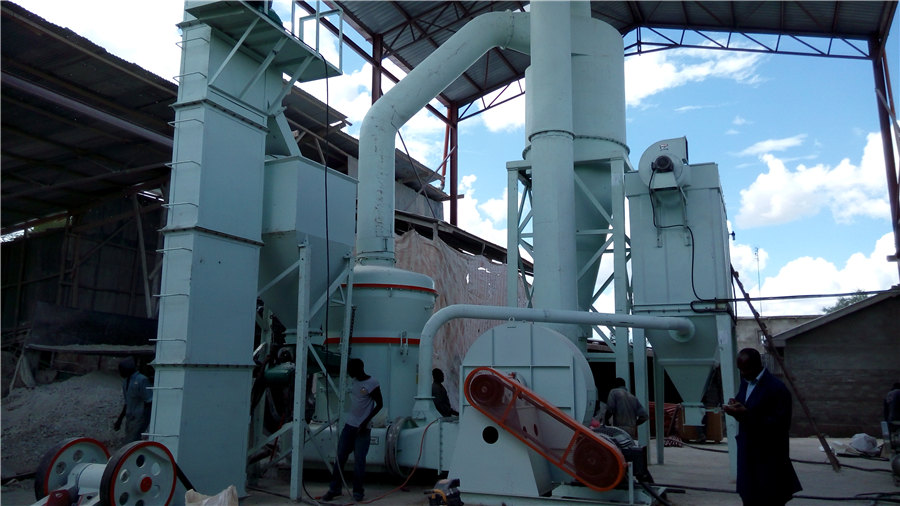
Precision grinding of cemented carbides based on a multilayer
2021年4月18日 Carbon nanotubes (CNTs) were added into the electrolyte to improve electrolytic dressing grinding performance of a brazed multilayer diamond wheel containing titanium The effect of CNTs on the electrolytic dressing performance of the grinding wheel was studied The grinding force, residual stress, roughness and morphology of the machined surfaces were 2024年3月1日 To achieve efficient grinding, a singlelayer electroplated diamond grinding wheel with a size of φ15 × 12 mm and a grit size of 80# was used in the grinding test In this paper, the process analysis of the rough grinding stage was mainly carried outOptimization of grinding process for hard and brittle materials 2023年4月4日 Download Citation Microstructure Characteristics of the Compound Layer Cracked during Grinding on QPQ‐Treated Cr‐Containing Steel Shafts Cr‐containing structural steels with quench Microstructure Characteristics of the Compound Layer Cracked