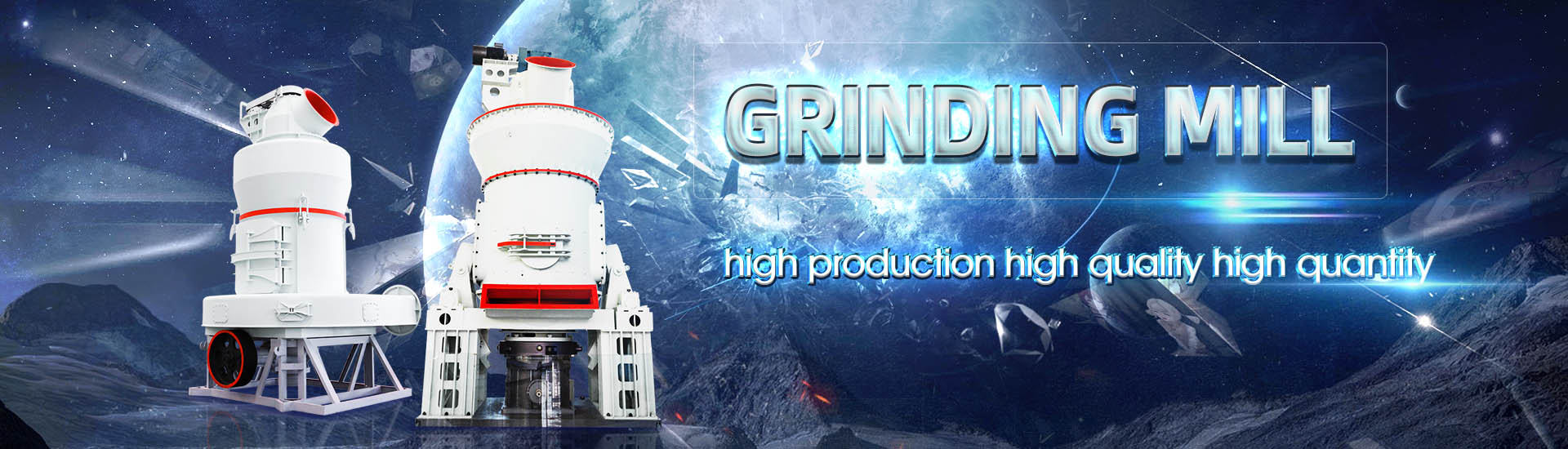
How to process the raw materials of calcite ore
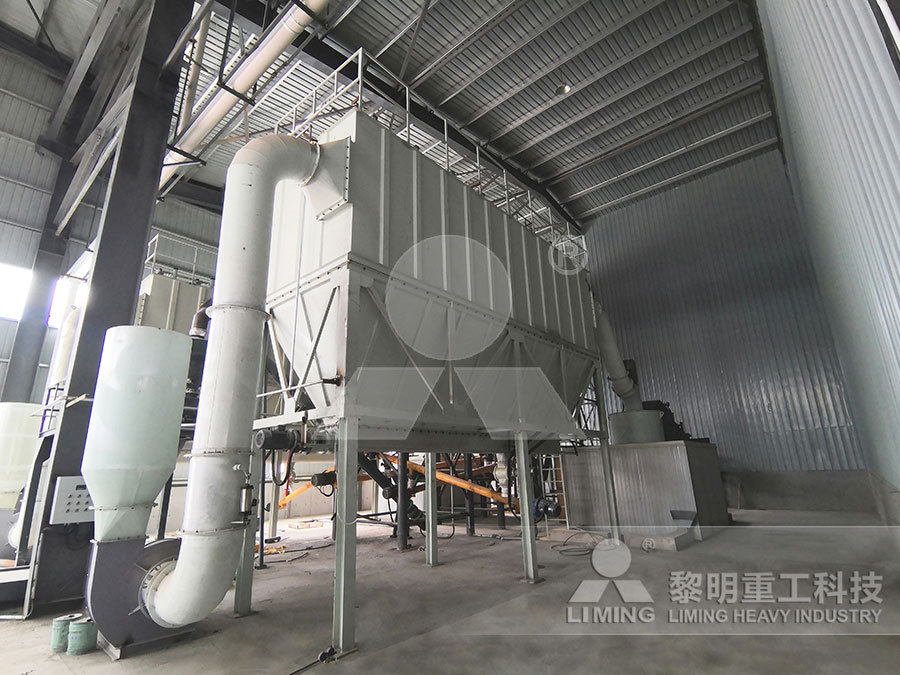
How calcite is mined and processed
Calcite mining and processing involve several steps to transform raw calcite into usable materials Here’s an overview of the typical process: Geologists conduct surveys to locate calcite deposits Various techniques, including satellite imagery and core sampling, are used to evaluate the 2020年9月23日 A tremendous amount of research has been performed on refining the flotation process for calcite ores and designing the reagents An Overview of Calcite Recovery by Flotation2020年12月1日 Calcite ores typically contain metal sulphide, silicate, or other calciumcontaining impurity minerals, which can be removed by flotation A tremendous amount of research has been performed onAn Overview of Calcite Recovery by Flotation2024年4月1日 Case studies are provided from quartz and quartzites used for silicon production, the production of calcite marble as filler in paper, and deep sea mineral depositsProcess mineralogy of unconventional mineral deposits examples
.jpg)
An Overview of Calcite Recovery by Flotation Springer
Calcite ores typically contain metal sulphide, silicate, or other calciumcontaining impurity minerals, which can be removed by flotation A tremendous amount of research has been 2024年4月1日 Bastnaesite, monazite, mixed RE ores, and ionadsorption clays are the main raw materials in the world to date REbearing ores (except ionadsorption minerals) are generally Recent process developments in beneficiation and metallurgy of Calcite is a common mineral occurring in many mineral veins but was treated as waste in former metal mining operations Only rarely does it occur in sufficient concentrations to be eco Mineral Planning Factsheet CalciteCalcite, crystallizing in the rhombohedral crystal system is the thermodynamically stable phase of calcium carbonate Aragonite, calcite's orthorhombic polymorph, is about 15 times more Calcite an overview ScienceDirect Topics
.jpg)
Blast Furnace Ironmaking SpringerLink
2023年10月6日 The smelting process of blast furnace is carried out in the shaft furnace of a closed countercurrent reactor and heat exchanger The complex physical changes and chemical reactions are completed in the process of the countercurrent movement of the charge and gas in which the raw materials containing iron oxide (sinter, pellets, etc), coke, slag flux (limestone) For example: carbon dioxide (greenhouse effect); carbon monoxide (poisonous); sulphur dioxide from the sulphur content of the ores (poisonous, acid rain) Disposal of slag, some of which is just dumped Transport of the finished iron IRON AND STEEL chemguide2023年2月15日 Talc chemical formula: Mg 3 Si 4 O 10 (OH) 2 Talc hardness: 1 on Mohs scale Color of talc: Talc minerals are colorless, white, green, brown or gray Talc powders are white or gray Transparency: Translucent Talc luster: How to Process Talc (the Softest Mineral)? FTM 2016年9月3日 The raw materials for an integrated steelworks can be classified into four categories, which are iron ores, fluxes, Mill scales are able to provide heat in the iron ore sintering process owing to the oxidation of FeO to Fe 2 O 3, and save some fuel Water guns are installed for descaling from slab, Sinter Plant Operations: Raw Materials SpringerLink
.jpg)
All Stages of Cement Manufacturing from The Cement Mining Process
2024年2月11日 A few everyday materials are great for calcium carbonate in cement manufacturing Manufacture mine and process different kinds of raw materials put them via a chemical reaction procedure to make cement They required an understanding of the chemical composition of all the raw materials so that the reaction in their procedure takes place 2024年4月26日 The EAF process uses electricity to melt scrap steel and other raw materials, including iron ore, to produce steel 08 Conclusion Back Iron ore processing is a complex and vital process that transforms raw iron ore into usable steel Iron Ore Processing: From Extraction to Manufacturing2016年1月8日 The first commercial production of phosphate rock began in England in 1847 A wide variety of techniques and equipment is used to mine and process phosphate rocks in order to beneficiate lowgrade ores and remove impurities The eighth chapter of this book deals with mining and beneficiation of phosphate ore The principle and operating conditions of important Mining and Beneficiation of Phosphate Ore IntechOpenCalcite mining and processing involve several steps to transform raw calcite into usable materials Here’s an overview of the typical process: Exploration and Site Selection: (the surface material covering the calcite ore)How calcite is mined and processed
.jpg)
Iron ore sintering Part 1 Theory and practice of the sintering process
2013年8月1日 Sintering is a process by which a mixture of iron ores, can process sticky raw materials continuously for 24 hours without operators A fuel coke reduction of 38 kg Next, we dissect the wet process, where raw materials are ground into a slurry and then heated in a kiln to form a clinker Through detailed explanations and visual aids, students will comprehend the stepbystep process involved in wet cement productionFrom Raw Materials to Concrete: The Science of Portland Cement 2023年11月2日 Cement, a fundamental building block of construction, plays an important role in erecting structures ranging from houses to monumental bridges and towering skyscrapers It's the binding agent that unites aggregates like Exploring How Cement is Made: From Rock to magnesium processing, preparation of magnesium ore for use in various products Magnesium (Mg) is a silvery white metal that is similar in appearance to aluminum but weighs onethird less With a density of only 1738 grams per Magnesium processing Techniques Methods
.jpg)
2 Major Roles of Limestone in Cement Manufacturing
2023年5月27日 Limestone is one of the key raw materials of cement clinker Around 8090% of the raw material for the kiln feed is limestone Limestone is also a favored mineral admixture in cement for sustainability Let's start with 2023年1月1日 According to the raw materials consumption and enterprise operation data of extracting lithium from ores, Peng JZ (2019) estimated that the processing cost of spodumene sulfuric acid method is about 3030 $/t (20000 RMB/t), which is equivalent to the processing cost of projects in Europe and North America to extract lithium from ores, such as Cínovec (2914 $/t) Lithium extraction from hard rock lithium ores (spodumene, Copper processing is a complicated process that begins with mining of the ore (less than 1% copper) and ends with sheets of 9999% pure copper called cathodes, which will ultimately be made into products for everyday useThe most common types of ore, copper oxide and copper sulfide, undergo two different processes, hydrometallurgy and pyrometallurgy, respectively, Copper Mining and Processing: Processing Copper Ores2021年12月16日 For several decades, the metallurgical industry and the research community worldwide have been challenged to develop energyefficient and lowcost titanium production processes The expensive and energyconsuming Kroll process produces titanium metal commercially, which is highly matured and optimized Titanium’s strong affinity for oxygen Titanium: An Overview of Resources and Production Methods
.jpg)
The Making of Iron Steel SEAISI
12 Raw Materials The basic raw materials of largescale steelmaking are: • iron ore, treated in some way after it comes from the mine; • coal, which must be converted to coke; • limestone; • steel scrap important both to the integrated steelworks as secondary feed to theThis process is also responsible for converting carbonate and hydroxide into their respective oxides Calcination is also referred to as a thermal process that is used to convert ores and other solid materials by providing thermal decomposition The word calcination came from the Latin word ‘calcinare’ which means ‘to burn lime’Iron Extraction by Blast Furnace Metallurgy Vedantu2018年7月11日 Pelletizing process and raw materials The iron ore is mined mostly from open pit deposits through mining operations and the raw product, “ run of mine, ” is subjected to mineral processingIron Ore Pelletizing Process: An Overview ResearchGateThe primary methods used to extract minerals from the ground are: Underground miningSurface (open pit) miningPlacer mining The location and shape of the deposit, strength of the rock, ore grade, mining costs, and current market price of the commodity are some of the determining factors for selecting which mining method to useHighergrade metallic ores found in veins How do we extract minerals? US Geological Survey
.jpg)
Manufacture of Cement Materials and Manufacturing
Table shows the raw materials for Portland cement manufacture The mixing procedure of the manufacture of cement is done in 2 methods, Dry process; Wet process; a) Dry Process The both calcareous and argillaceous raw materials 2020年9月23日 In general, precipitated calcium carbonate (PCC) is used as a mineral filler in paper industries; while natural calcite (CaCO3) ore is also suitable for industrial use if it is a finely ground highgrade material Naturally, calcite is An Overview of Calcite Recovery by Flotation2015年12月9日 Iron ore Calcite Sand Fly the chemical elements of the raw materials are subjected to 2015) • Quarry The process of obtaining raw materials for cement manufacturing involves mining (PDF) Cement Manufacturing ResearchGateTatarin A, Vogt R (2013) Test methods for heavy clay ceramic raw materials: raw material composition (primary properties)—part 1 Brick and Tile Industry International, pp 20–34 Tomeczek J, Palugniok H (2002) Kinetics of mineral matter transformation during coal combustion Fuel 81(10):1251–1258 Article Google ScholarClay calcination technology: stateoftheart review by the
.jpg)
How to Smelt Iron: The 6 Steps to Iron Smelting The Crucible
Our community came together to smelt twentyfive pounds of iron Every aspect of the smelt was a team effort, from collecting magnetite sand from a local beach, to building the bloomery furnaceSpace Age expansion exclusive feature Calcite is an ore found in deposits located on VulcanusCalcite plays a large role in smelting metals, getting petroleum products, obtaining water and creating some explosives Calcite in space is also necessary for the advanced thruster fuel and advanced thruster oxidizer recipes Alternative recipesCalcite Factorio Wiki2021年3月8日 The Utilization of Bauxite Residue with a CalciteRich Bauxite Ore in the Pedersen Process for Iron and Alumina Extractionpdf Available via license: CC BY 40 Content may be subject to copyrightThe Utilization of Bauxite Residue with a CalciteRich Bauxite Ore 2023年2月15日 Hematite, also spelled haematite, is a weakly magnetic iron ore with better floatability than magnetite and wide distributionIt is one of the most important raw materials for the extraction of iron Its composition is complex In addition to containing a small amount of magnetite, the impurity embedding of haematite has uneven particle size and high content of How to Extract Iron from Hematite: Methods and Plants
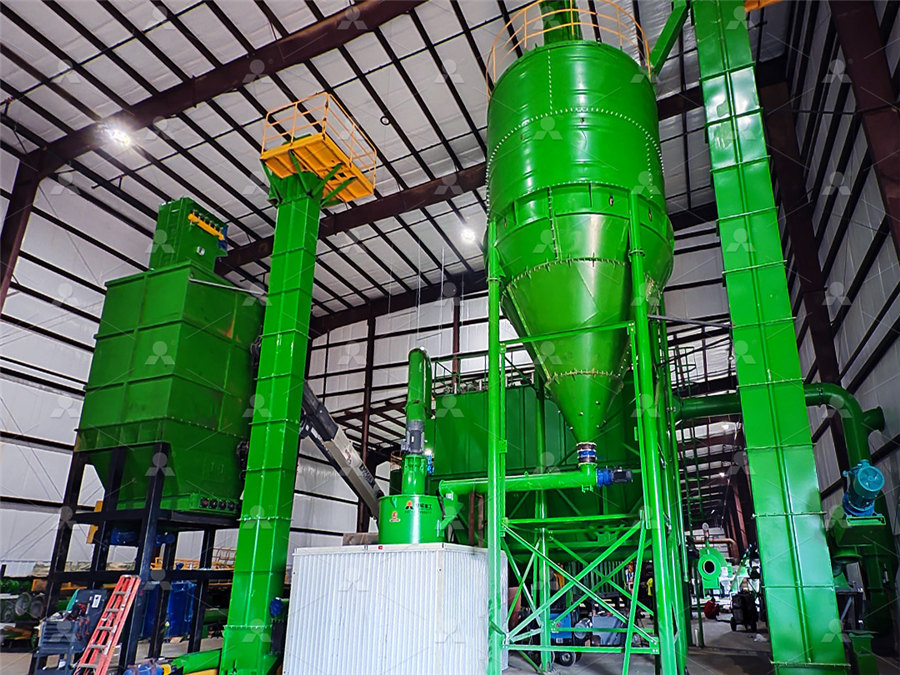
233: Metallurgy of Iron and Steel Chemistry LibreTexts
As the ore, lime, and coke drop into the furnace (Figure \(\PageIndex{1}\)), any silicate minerals in the ore react with the lime to produce a lowmelting mixture of calcium silicates called slag, which floats on top of the molten iron Molten iron is then allowed to run out the bottom of the furnace, leaving the slag behind2023年1月19日 The RKEF process has strong adaptability of raw materials and all kinds of laterite ores can be used for production The quality of ferronickel products is excellent and the nickel content generally reaches 10–30 wt%, which can be used to An Overview of Nickel Utilization from Laterite Ore2023年10月6日 The smelting process of blast furnace is carried out in the shaft furnace of a closed countercurrent reactor and heat exchanger The complex physical changes and chemical reactions are completed in the process of the countercurrent movement of the charge and gas in which the raw materials containing iron oxide (sinter, pellets, etc), coke, slag flux (limestone) Blast Furnace Ironmaking SpringerLinkFor example: carbon dioxide (greenhouse effect); carbon monoxide (poisonous); sulphur dioxide from the sulphur content of the ores (poisonous, acid rain) Disposal of slag, some of which is just dumped Transport of the finished iron IRON AND STEEL chemguide
.jpg)
How to Process Talc (the Softest Mineral)? FTM
2023年2月15日 Talc chemical formula: Mg 3 Si 4 O 10 (OH) 2 Talc hardness: 1 on Mohs scale Color of talc: Talc minerals are colorless, white, green, brown or gray Talc powders are white or gray Transparency: Translucent Talc luster: 2016年9月3日 The raw materials for an integrated steelworks can be classified into four categories, which are iron ores, fluxes, Mill scales are able to provide heat in the iron ore sintering process owing to the oxidation of FeO to Fe 2 O 3, and save some fuel Water guns are installed for descaling from slab, Sinter Plant Operations: Raw Materials SpringerLink2024年2月11日 A few everyday materials are great for calcium carbonate in cement manufacturing Manufacture mine and process different kinds of raw materials put them via a chemical reaction procedure to make cement They required an understanding of the chemical composition of all the raw materials so that the reaction in their procedure takes place All Stages of Cement Manufacturing from The Cement Mining Process 2024年4月26日 The EAF process uses electricity to melt scrap steel and other raw materials, including iron ore, to produce steel 08 Conclusion Back Iron ore processing is a complex and vital process that transforms raw iron ore into usable steel Iron Ore Processing: From Extraction to Manufacturing
.jpg)
Mining and Beneficiation of Phosphate Ore IntechOpen
2016年1月8日 The first commercial production of phosphate rock began in England in 1847 A wide variety of techniques and equipment is used to mine and process phosphate rocks in order to beneficiate lowgrade ores and remove impurities The eighth chapter of this book deals with mining and beneficiation of phosphate ore The principle and operating conditions of important Calcite mining and processing involve several steps to transform raw calcite into usable materials Here’s an overview of the typical process: Exploration and Site Selection: (the surface material covering the calcite ore)How calcite is mined and processed2013年8月1日 Sintering is a process by which a mixture of iron ores, can process sticky raw materials continuously for 24 hours without operators A fuel coke reduction of 38 kg Iron ore sintering Part 1 Theory and practice of the sintering processNext, we dissect the wet process, where raw materials are ground into a slurry and then heated in a kiln to form a clinker Through detailed explanations and visual aids, students will comprehend the stepbystep process involved in wet cement productionFrom Raw Materials to Concrete: The Science of Portland Cement