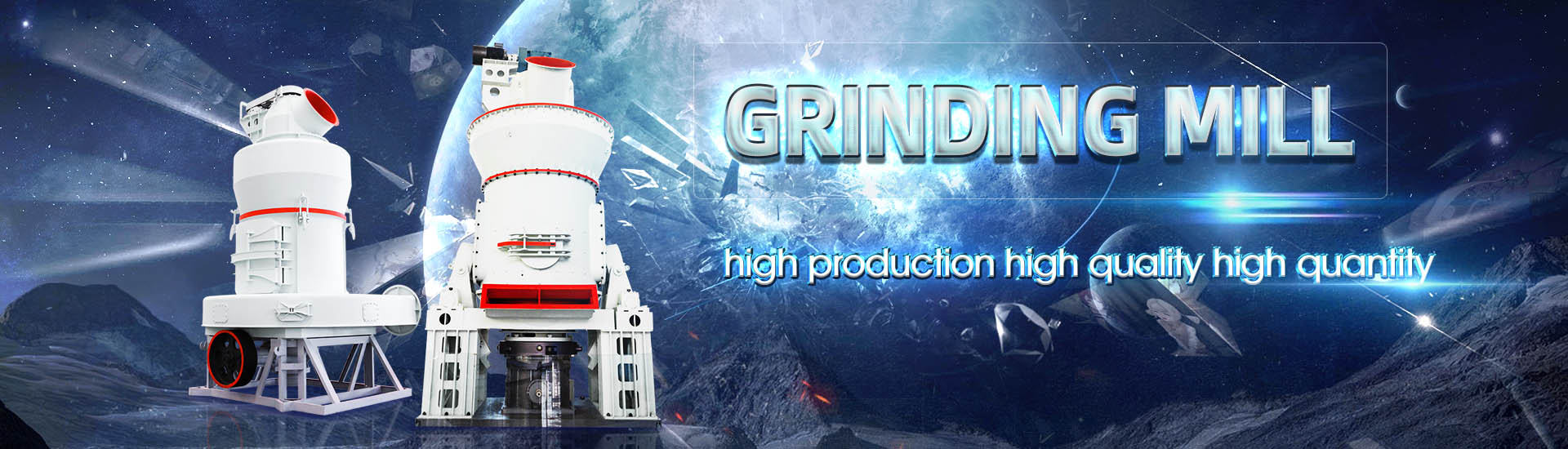
How to reduce iron overload in ore grinding mill
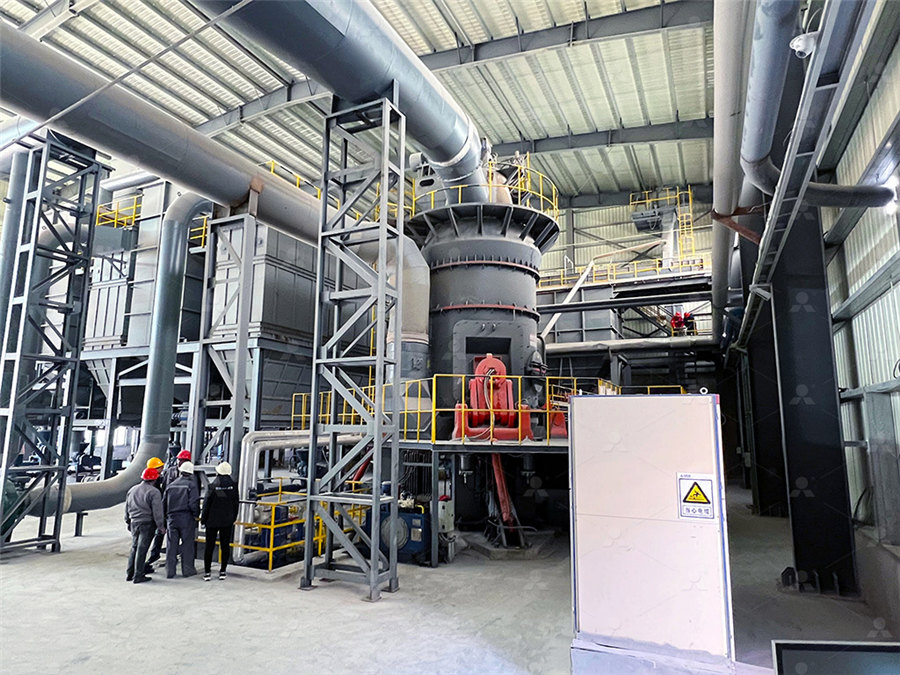
SAG Mill Optimization using Model Predictive Control Andritz
SemiAutogenous Grinding mills can be optimized for maximum ore throughput or maximum grinding energy efficiency In both cases, precise control of the mill weight is critical Model predictive control provides an additional tool to improve the control oSemif Autogenous To get rid of pulp and rocks in the charge, a mill grindout (no ore feed) of 10 to 20 minutes is also performed before mill inspection or relining The complete grindout is required to obtain the Optimization of mill performance by usingpotential overload of the secondary ball mill is to reduce the transfer size from primary ball mill This affects the sorting behaviour and impacts the optimum process as well The micro Quantification of HPGR energy efficiency effects on downstream 2018年4月24日 Two different circumstances must be addressed for the reduction or elimination of overload risk: a) in existing operations, or b) in the design of new grinding circuits The How to Reduce Ball Mill Overload Risk 911Metallurgist
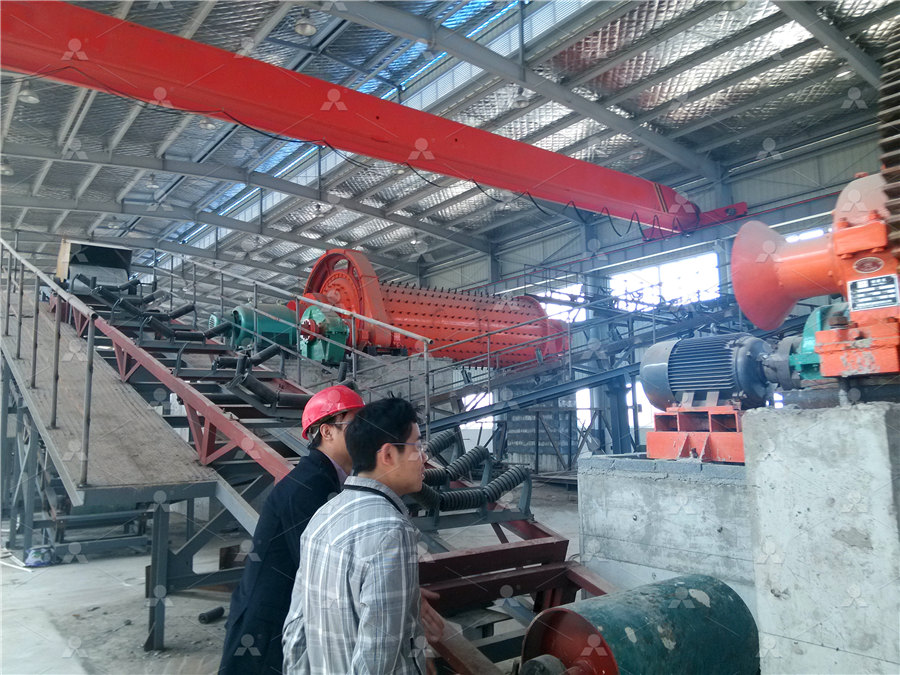
Comminution and classification technologies of iron ore
2022年1月1日 To operate viably and sustainably, there is a need to reduce costs and energy consumption, particularly of the energyintensive grinding required for lowgrade magnetite 2014年1月1日 The work demonstrates the application of the population balance model in the optimization of a fullscale ball mil circuit grinding pellet fines with the aim to evaluate the Population balance model approach to ball mill optimization in 2022年3月16日 The experimental planning with selected key factor like operating gap (X 1), applied load (X 2) and roll speed (X 3) was designed by CCD method to obtain the optimum Potential of HighPressure Grinding Roll (HPGR) for Size Reduction 2013年8月1日 Grinding wear models may also benefit from better instrumentation, including online analyzers of iron in the ore slurry that could potentially give an indication of the Consumption of steel grinding media in mills – A review
.jpg)
Supervisory expert control for ball mill grinding circuits
2008年4月1日 Ball mill grinding circuits are important unit operations in the production of metals from ore The function of the grinding mill is to reduce the particle size of the ore such that the 2022年3月19日 An iron ore concentrate sample was ground separately in a pilotscale HPGR mill in multiple passes and a dry opencircuit ball mill to increase the specific surface area of Grinding iron ore concentrate by using HPGR and ball mills and For instance, iron ore must be ground very fine before it can be used in steel production, while coal requires less fine grinding to produce heat and electricity Effect of ball size on ore grinding performance Ball milling Overall, ball size and shape are important factors to consider when choosing a mill for ore grinding However, Factors affecting ores grinding performance in ball millsGrinding Mills: Ball Mill Rod Mill Design PartsCommon types of grinding mills include Ball Mills and Rod Mills This includes all rotating mills with heavy grinding media loads This article focuses on ball and rod mills excluding SAG and AG Grinding Mills 911Metallurgist
.jpg)
Friction and wear of liner and grinding ball in iron ore ball mill
2017年6月15日 Moreover, smaller particles in the grinding media can lead to coverage of grinding balls and subsequently reduce the efficiency of the milling process in time [75]The calculations below mainly apply to ore mills 1 Workindex What is the workindex of a mill ? The workindex is a parameter used in ore milling processes It is defined as the energy needed to reduce ore from infinite size to the state where 80% of the milled ore will pass through a Grinding power : step by step calculation PowderProcess2022年3月30日 All industries are facing increasing pressure to ensure that carbon emissions are reduced to help achieve the socalled 15 °C future This has led to most of the major mining companies committing to significant reductions in their operational carbon footprint – in many cases by up to 30–40% in the next 10–15 years and to place themselves in a netzero scope Helping to reduce mining industry carbon emissions: A stepby 2017年1月17日 Grinding mills are infamous for their extremely low energy efficiency It is generally accepted that the energy required to produce new mineral surfaces is less than 1% of the electricity consumed Breaking down energy consumption in industrial grinding mills
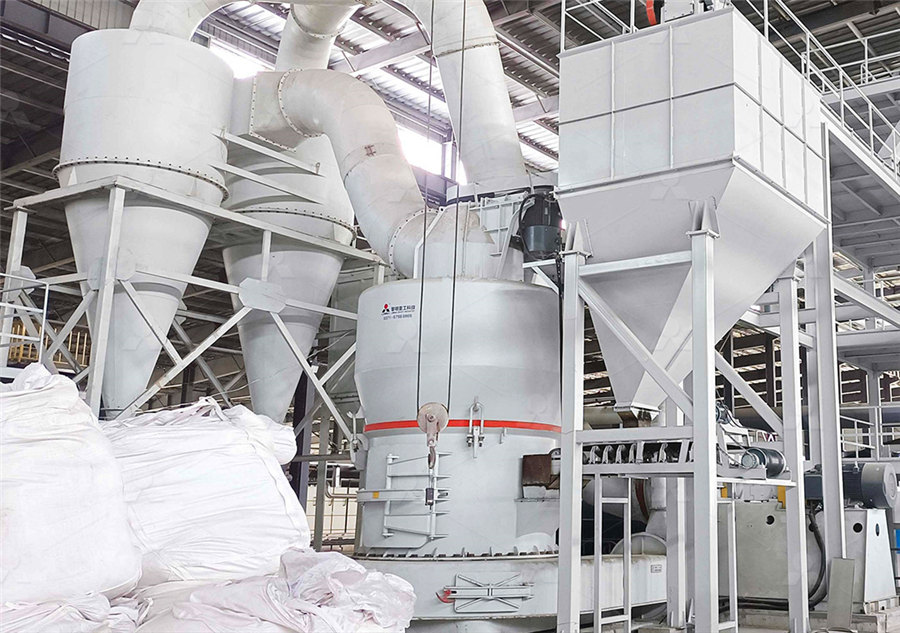
SAG Mill Optimization using Model Predictive Control Andritz
exhibits many of these aspects Maintaining the SAG mill weight at the optimum value is critical for achieving maximum grind rate efficiency and mill production (Powell, MS, van der Westhuizen, AP, Mainza, AN 2009) However, SAG mill weight is difficult to control as the dynamic response changes as the mill approaches maximum capacity2 INTRODUCTION Grinding operations are of great importance to the mineral industries and in particular are one of the most important unit operation in the iron ore pelletizing processPopulation balance model approach to ball mill optimization in iron ore 2015年4月9日 autogenous grinding, ball mill, grinding mills, hammer mill, rod mill, roller mill, SAG, Grinding Mills and Their Types In various fields of the process industry, reduction of size of different materials is a basic unit operation The basic idea is to reduce particle sizes of material under handling by cutting or breaking those to smaller piecesGrinding Mills and Their Types – IspatGuruMILL OPTIMIZATION IN IRON ORE GRINDING* Patrícia Mundim Campos Faria1 Luís Marcelo Tavares 2 Raj K Rajamani 3 Abstract reduce the processing costs This is a topic of special interest to Vale, which has ten pelletizing plants in operation in Brazil and two in OmanPOPULATION BALANCE MODEL APPROACH TO BALL MILL OPTIMIZATION IN IRON ORE
.jpg)
News Iron ore mineral processing with standing grinding or ball
Iron ore dry grinding dry magnetic process of iron ore dressing mill for dry fine grinding, grinding fine reading can guarantee200 above 80%, equivalent to the common process of ball mill and screw grading machine or ball mill and cyclone grinding closed process, at the same time, iron ore dressing mill processing capacity is much higher than the ball mill, low energy consumption, 2019年12月6日 Phlebotomy has been the mainstay for treatment of iron overload when marrow function is normal, but it is not appropriate in the face of ineffective erythropoiesis or marrow failure Red cell exchange transfusion Iron overload in transfusiondependent patients2012年11月1日 Ironmediated organ damage may occur in multiply transfused, lowrisk MDS patients with several reports highlighting that mortality rate is greater in heavily ironoverloaded MDS patients developing hepatic and How I treat transfusional iron overload Blood2023年7月20日 Therefore, the rod mill is mostly used for coarse grinding of the previous period of ball mill, or grinding of brittle materials and materials against overcrushing, such as tungsten and tin ore before gravity separation; and (3) autogenous mill – it refers to the materials which themselves are collided and ground mutually to be crushed when the grinding mill rotates, and Ore Grinding SpringerLink
.jpg)
Corrosion of Cast Iron Mill Plates in Wet Grinding ResearchGate
2010年7月1日 Most locallymanufactured cornmill plates in tropical countries are made of grey cast iron due to its relatively low cost, good wear resistance, good hardness and other mechanical properties in 2015年3月15日 For the grinding tests, a Loesche mill LM45 (table diameter 045 m) is used (Fig 2a) This pilot scale mill is a special development for ore grinding, which is reflected by several features The mill has four rollers, which are able to stress the particle bed with grinding pressures of up to 5000 kN/m 2Research of iron ore grinding in a verticalrollermill2015年6月19日 The basic parameters used in ball mill design (power calculations), rod mill or any tumbling mill sizing are; material to be ground, characteristics, Bond Work Index, bulk density, specific density, desired mill tonnage capacity DTPH, operating % solids or pulp density, feed size as F80 and maximum ‘chunk size’, product size as P80 and maximum and finally the type of Ball Mill Design/Power Calculation 911Metallurgistmore efficient grinding technologies has provided opportunities to further reduce the operating costs associated with grinding At Empire Mines a HPGR is installed for processing crushedReducing Grinding Energy and Cost Magnetite Iron Ore
.jpg)
How to Operate a Grinding Circuit 911Metallurgist
2016年4月25日 Sound of Mill Loud, metallic rattle: Mill is nearly empty of muck; balls banging each other and wearing out liners Raise feed, cut head water if necessary Increase classifier water to build load Thick mushy sound Quiet: Mill choked with muck, not grinding Cut down feed, increase head water carefully Cut classifier water a little #4 2014年10月20日 This paper presents the development of a mill scaleup procedure based on population balance models of grinding circuits Models containing various degrees of details in their representation of Population balance model approach to ball mill optimization in iron ore All ores have an economic optimum particle size which maximizes the difference between net smelter return (NSR) and grinding costs (Chapter 1): too coarse a grind and the inadequate liberation limits recovery (and thus revenue) in the separation stage; too fine a grind and grinding costs exceed any increment in recovery (and may even reduce recovery depending on the Grinding Mill an overview ScienceDirect TopicsChange the grindability of the raw ore, such as heating the minerals, change the mechanical properties of the ore, reduce the hardness of the ore 2 More crushing and less grinding to reduce the feed size into mill The larger feed 10 Ways to Improve the Grinding Efficiency of Your
.jpg)
Hemochromatosis (Iron Overload) Cleveland Clinic
Ask if your parents ever had iron overload, liver disease or other related diseases Ask if you take iron supplements, by mouth or injection Ask if you take extra vitamin C, which can boost absorption of iron Check your joints for pain Listen to your heart for an irregular beatTo achieve this objective an attempt is made to stabilize the operation by principally controlling the process variables The main disturbances in a grinding circuit are: 1 change in ore characteristics (ore feed rate, grindability, feed particle size distribution, mineral composition and mineral characteristics like abrasiveness, hardness), 2Grinding Mill an overview ScienceDirect Topics2023年3月6日 Vertical roller mills (VRM) are commonly used in the processing of iron ore for dry grinding for several reasons: vertical roller mill Energy Efficiency: VRMs are known for their energy efficiencyWhy is vertical roller millbased dry grinding used in iron ore 2019年8月14日 Ball mill is a common grinding equipment in concentrator : hm@gmail Toggle The ball mill liner is intended to protect the barrel of the ball mill in order to reduce and avoid direct impact and friction of the body and abrasive minerals on the barrel of 8 Types of Iron Ore Magnetic Separator (04: The Ultimate Guide to Ball Mills Miningpedia
.jpg)
EnergyEfficient Technologies in Cement Grinding IntechOpen
2016年10月5日 1 Introduction Cement is an energyintensive industry in which the grinding circuits use more than 60 % of the total electrical energy consumed and account for most of the manufacturing cost []The requirements for the cement industry in the future are to reduce the use of energy in grinding and the emission of CO 2 from the kilns In recent years, the production 2011年1月1日 At present we are witnessing large investments in the iron ore industry, fuelled by demand from Asia At the same time, there is a changing landscape in pricing of iron ores, with the recent Calculating the value of iron ores in ironmaking and steelmaking2013年8月1日 In addition, the sphalerite had a more prominent effect on the grinding characteristics of the ore The grinding speed of ore and its component minerals decreased exponentially with the grinding Consumption of steel grinding media in mills – A review2022年8月31日 Grinding plays an important role in mining, construction, metallurgy, chemical, coal and other basic industries In terms of beneficiation, grinding is the most energy consuming operation So, reasonable grinding conditions according to the properties of ores is the key to obtain good grinding results and reduce energy consumption and resource Grinding Modeling and Energy Efficiency in Ore/Raw Material
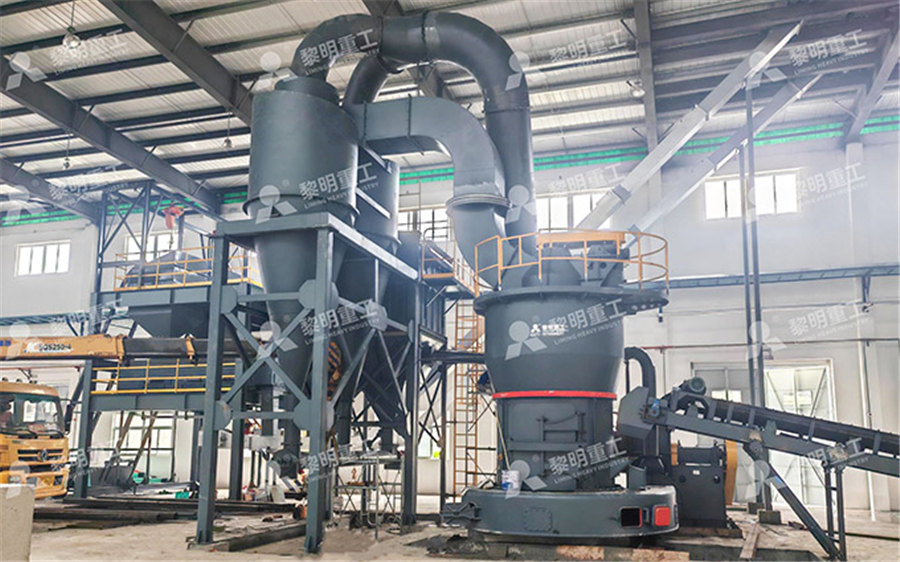
Factors affecting ores grinding performance in ball mills
For instance, iron ore must be ground very fine before it can be used in steel production, while coal requires less fine grinding to produce heat and electricity Effect of ball size on ore grinding performance Ball milling Overall, ball size and shape are important factors to consider when choosing a mill for ore grinding However, Grinding Mills: Ball Mill Rod Mill Design PartsCommon types of grinding mills include Ball Mills and Rod Mills This includes all rotating mills with heavy grinding media loads This article focuses on ball and rod mills excluding SAG and AG Grinding Mills 911Metallurgist2017年6月15日 Moreover, smaller particles in the grinding media can lead to coverage of grinding balls and subsequently reduce the efficiency of the milling process in time [75]Friction and wear of liner and grinding ball in iron ore ball mill The calculations below mainly apply to ore mills 1 Workindex What is the workindex of a mill ? The workindex is a parameter used in ore milling processes It is defined as the energy needed to reduce ore from infinite size to the state where 80% of the milled ore will pass through a Grinding power : step by step calculation PowderProcess
.jpg)
Helping to reduce mining industry carbon emissions: A stepby
2022年3月30日 All industries are facing increasing pressure to ensure that carbon emissions are reduced to help achieve the socalled 15 °C future This has led to most of the major mining companies committing to significant reductions in their operational carbon footprint – in many cases by up to 30–40% in the next 10–15 years and to place themselves in a netzero scope 2017年1月17日 Grinding mills are infamous for their extremely low energy efficiency It is generally accepted that the energy required to produce new mineral surfaces is less than 1% of the electricity consumed Breaking down energy consumption in industrial grinding millsexhibits many of these aspects Maintaining the SAG mill weight at the optimum value is critical for achieving maximum grind rate efficiency and mill production (Powell, MS, van der Westhuizen, AP, Mainza, AN 2009) However, SAG mill weight is difficult to control as the dynamic response changes as the mill approaches maximum capacitySAG Mill Optimization using Model Predictive Control Andritz2 INTRODUCTION Grinding operations are of great importance to the mineral industries and in particular are one of the most important unit operation in the iron ore pelletizing processPopulation balance model approach to ball mill optimization in iron ore
.jpg)
Grinding Mills and Their Types – IspatGuru
2015年4月9日 autogenous grinding, ball mill, grinding mills, hammer mill, rod mill, roller mill, SAG, Grinding Mills and Their Types In various fields of the process industry, reduction of size of different materials is a basic unit operation The basic idea is to reduce particle sizes of material under handling by cutting or breaking those to smaller piecesMILL OPTIMIZATION IN IRON ORE GRINDING* Patrícia Mundim Campos Faria1 Luís Marcelo Tavares 2 Raj K Rajamani 3 Abstract reduce the processing costs This is a topic of special interest to Vale, which has ten pelletizing plants in operation in Brazil and two in OmanPOPULATION BALANCE MODEL APPROACH TO BALL MILL OPTIMIZATION IN IRON ORE