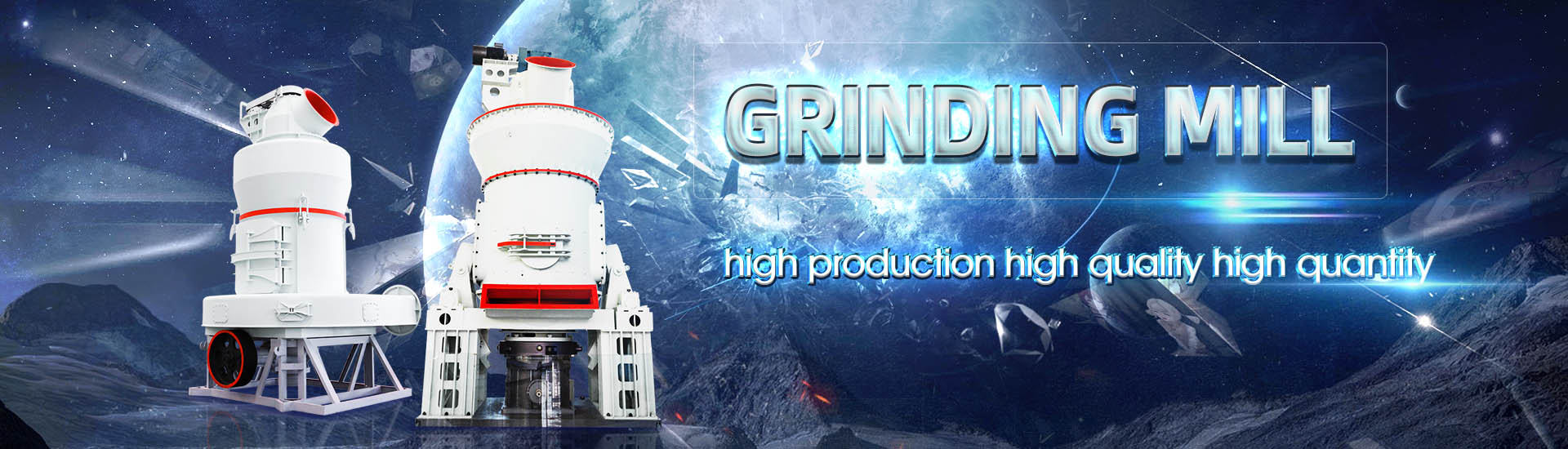
Silicon powder crushing
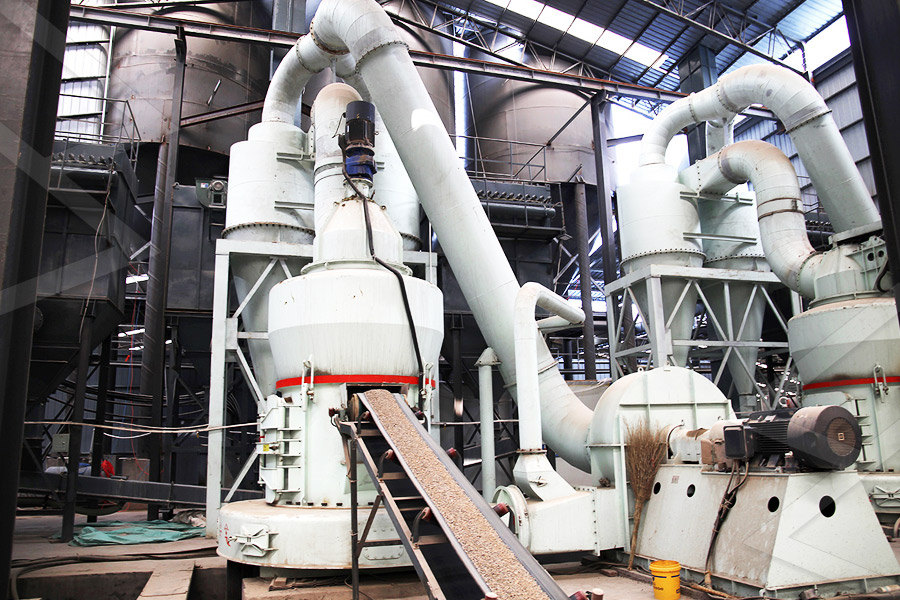
Silicon Powder Properties Produced in a Planetary Ball Mill as a
2020年1月15日 In this study a metallurgical grade silicon quality was milled in a planetary ball mill and the properties of the powder were investigated as a function of grinding time, grinding 2018年8月15日 Highvoltage pulse crushing technology combined with sieving and dense medium separation was applied to a photovoltaic panel for selective separation and recovery Highvoltage pulse crushing and physical separation of It involves reducing quartz (silicon dioxide) at high temperatures to obtain metallic silicon, which is then crushed into silicon powder The steps are: Raw material preparation: Highpurity quartz Overview of Silicon Powder: Preparation, Uses, and ChallengesSilicon powder is produced by crushing, milling and classifying silicon material to obtain the required particle size Silicon powder can be produced with a top cut for customers that only What is silicon powder? Elkem
.jpg)
A comprehensive review on the recycling technology of silicon
2024年4月5日 In this review article, the complete recycling process is systematically summarized into two main sections: disassembly and delamination treatment for siliconbased 2023年5月25日 The mechanical processes for recycling endoflife silicon PV modules typically involve crushing and sorting The modules are broken down into small pieces in the crushing process, and useful materials, such as glass, Review on Separation Processes of EndofLife Silicon 2023年8月20日 Mechanical crushing and electrostatic separation to recover Si from PV panels A nonpolluting, lowcost industrial recycling method is proposed The optimum voltage and Recycling Si in waste crystalline silicon photovoltaic panels after 2019年10月7日 In this study, we have used highenergy ball milling in an inert gas atmosphere to synthesize SiNCs and study their photophysical properties The induced accumulation of high strain, quantum confinement and possibly Photophysical properties of ball milled silicon
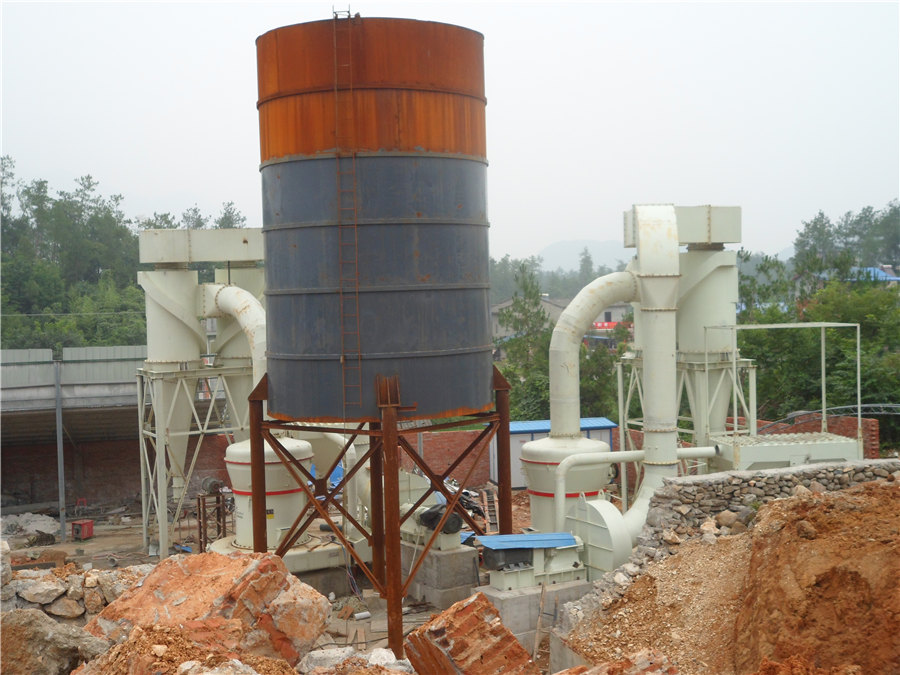
What are the optimal conditions for crushing and grinding silicon
To produce highquality silicon powder, optimal conditions involve careful control of grinding parameters and purification techniques Research indicates that specific grinding methods and 2010年1月1日 Crushing is used to very quickly produce a fine powder from a bulk material or fine particle using mechanical crushing This technique is essentially used to investigate Mechanical Preparation Techniques SpringerLinkSilicon powder 98% pure for all uses include using an FDM printer to print silicon wires, electronics and semiconductors, optics and photonics Silicon powder is a fine, granular form of silicon created by crushing or grinding silicon into small particlesSilicon Powder UniversityWafer, Incshowed that the liberation degree of silicon particles was 7945% (grinding for 15 min), which was 794% higher than that of silicon particles after 5 min grinding time, and 7715% of the silicon particles were fully liberated The flotation recovery of silicon can increase from 105 to 787% with the appropriate collectorEffect of Grinding Liberation on Recovery of Silicon from MGSi
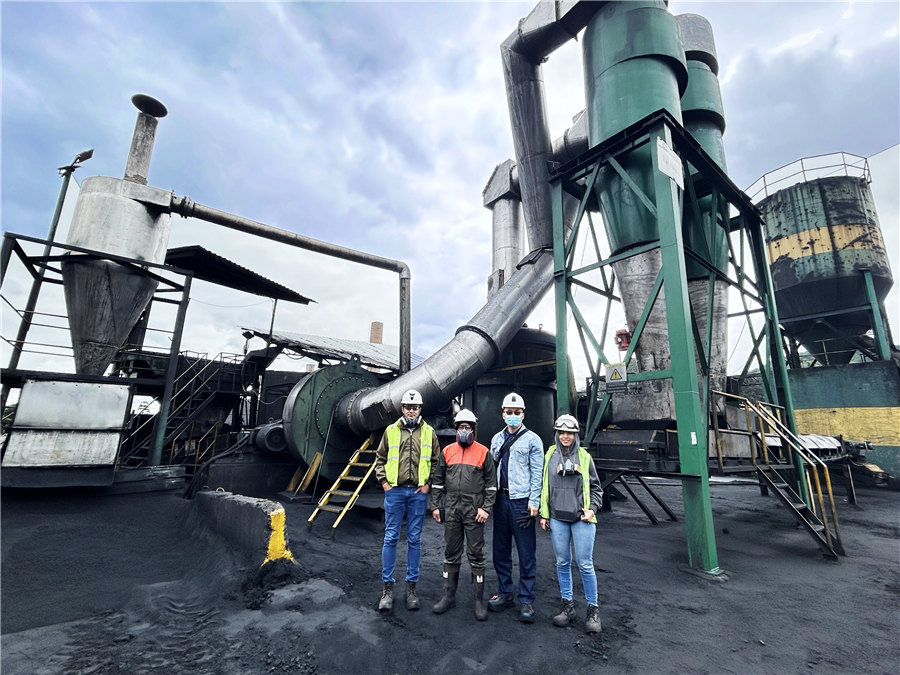
Multiple SELFRAG High Voltage Pulse Power systems for silicon crushing
2018年12月12日 SELFRAG, the leading supplier of High Voltage Pulse Power (HVP) fragmentation equipment is pleased to announce start up and operation of two new systems for crushing high pure polysilicon and 2021年5月5日 Silicon recovered from Kerf waste is typically new silicon, whereas PV recycled silicon in solar cells used for a quite long time of 25–30 years It is, therefore, quite challenging to remove impurities from PV recycled silicon and subsequent conversion to nanosilicon and reuse them by introducing new properties and functionalities at the nanoscaleEnd‐of‐Life Photovoltaic Recycled Silicon: A Sustainable Ultrafine metal silicon powder, advanced airflow crushing production line, uses highquality metal silicon blocks as raw materials The particle shape is smooth and the particle size is uniform Silicon powder and nanosilica powder of various particle sizes and purity specifications can be customized according to customer requirementsUltrafine Silicon Metal PowderZONACEN CO, LIMITED2018年8月15日 After sieving the products obtained from the secondary crushing step of the glass layer, glass was mainly distributed in the size fraction range of 45–850 μm with a small amount of Si powder However, purification of the glass (removal of Si powder) could be achieved by dense medium separation at a specific gravity of 24Highvoltage pulse crushing and physical separation of
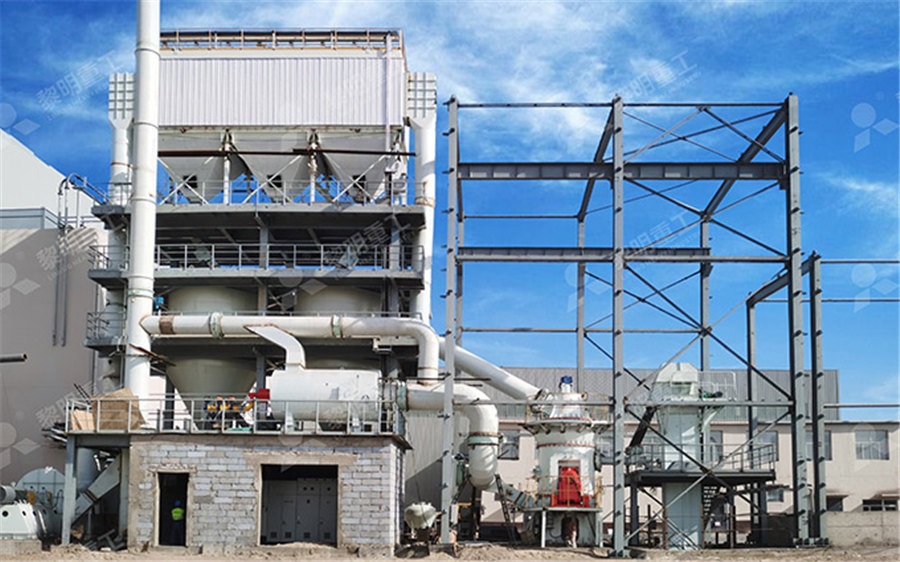
Silicon carbide powder and sintered materials JSTAGE
powders can be obtained by coarse crushing thus avoiding impurity contamination Figure 7 shows a typicalfurnace for the silica reduction process24) Amixture of silica and fine carbon powder is fed from the top of the furnace and reacted inaninert gas atmosphere The synthesized powder is removed through the bottom of the furnace2024年9月30日 The global silicon metal powder market size was USD 10194 million in 2021 and market is projected to touch USD 141238 million by 2031, at a CAGR of 33% during the forecast period Silicon metal powder is made of silicon lumps by sieving, washing, crushing, and other processes It is also known as industrial silicon powderSilicon Metal Powder Market Size Report Global Forecast 2031Green Silicon Carbide Home Previous Next Green Silicon Carbide Purity:SiC≥99%Particle size: F8F240, 01mm, 13mm, 35mm, 58mm, 100 mesh, 200 mesh, 325 meshApplications: Grinding wheel, abrasives, abrasive tools, sandblasting and rust removal, resin grinding wheels, metallurgy, refractory materials, chemical industry, electronics, aerospace, ceramics, and Green Silicon Carbide YafeiteTo produce highquality silicon powder, optimal conditions involve careful control of grinding parameters and purification techniques Research indicates that specific grinding methods and equipment significantly influence the properties of the resulting silicon powder ## Grinding Techniques **Planetary Ball Mill**: The finest silicon powder (d50 of 062 μm) was achieved What are the optimal conditions for crushing and grinding silicon
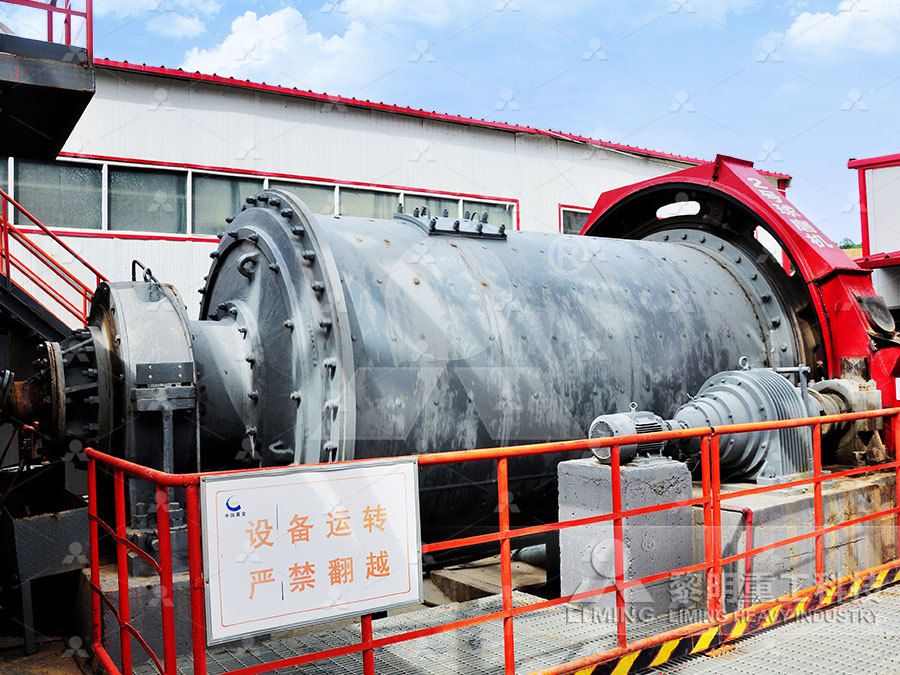
メタルシリコンの粉砕 パウダーになるまで (モース
2020年1月14日 メタルシリコンの粉砕 パウダーになるまで (モース硬度約7) Metal Silicon Crushing process to powder (Morse hardness about 7)本動画では、約10cm角のメタル 2023年5月6日 Therefore, inductively coupled plasma–optical emission spectrometry (ICP–OES) is used to detect the content of various elements in crystallinesilicon PV cells and compared with the industrial silicon powder indicators to determine the impurities that need to be removed in the purification of silicon materialsDevelopment of metalrecycling technology in waste crystallinesilicon 2019年10月15日 Silicon/carbon composite with CMC/SBR as a dual binder can achieve more than 1200 Composite electrodes were made of the resulting silicon powder (0–10 µm) together with carbon black SiliconCarbon composite anodes from industrial battery grade silicon2024年8月13日 Silicon carbide is a highly hard compound, second only to diamond (hardness 15) and boron carbide (hardness 14) Used as a refractory material, its consumption is only surpassed by alumina and magnesia, making it a crucial substance for heat resistance The production of silicon carbide products (silicon carbide powder) consistsComprehensive Guide to SiC Powder Silicon Carbide Ceramic
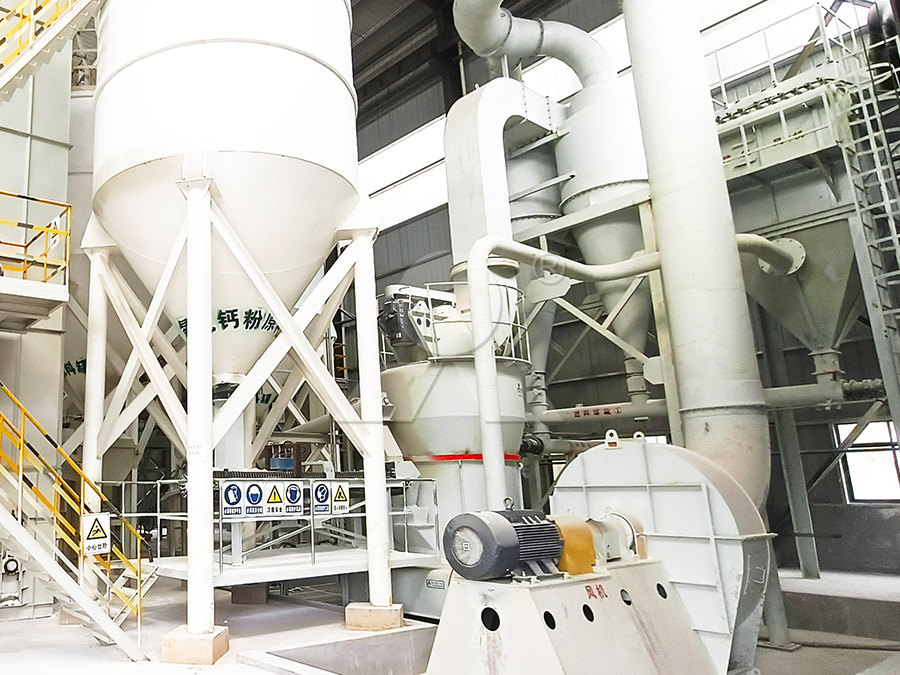
Selective grinding of glass to remove resin for siliconbased
2021年2月1日 Secondary grinding was investigated as a mean of liberating glass from locked particles of glass and resin obtained by the primary shredding from the siliconbased PV panelsIts high hardness can meet the vast majority of metal powder crushing and refining They are extensively applied to in the fields of Metallurgy, Ceramics, Electronics, Light Industry, Paint, Medicine, Geology, Chemical Engineering and so on Choose between 3 mm 25 mm in size for the silicon carbide mediaMSE PRO 100 grams Silicon Carbide (SiC) Grinding Media Balls2024年10月29日 Korean researchers have used thermal and wet gravity separation (WGS) to separate EVA from reclaimed silicon powder in endoflife PV modules with "minimal" chemical usage The proposed technique New tech to recover highpurity silicon powder from endoflife Cooling/Crushing 3 Oxidized material, called slag, is poured off into pots and cooled The silicon metal is cooled in large cast iron trays about 8 ft (24 m In powder form, silicon is packaged in 50lb (23kg) plastic pails or paper bags, 500lb (227kg) steel drums or 3,000lb (1,361kg) large sacks or boxes How silicon is made material, making, history, used, processing
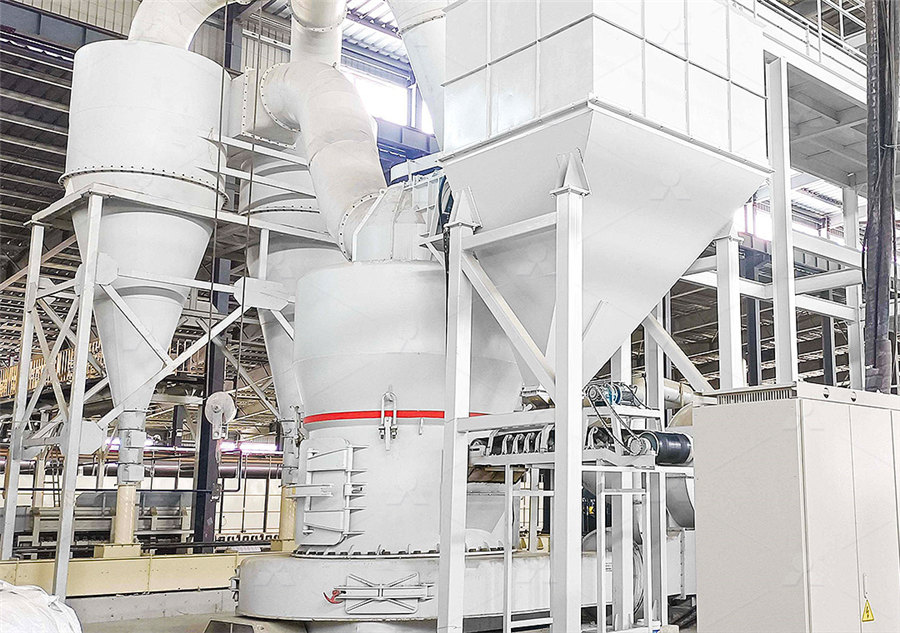
What Is Ferro Silicon Production Process?
This process can be adjusted to produce different grades of ferro silicon with varying silicon content, typically ranging from 15% to 90% silicon What temperature is ferrosilicon produced at? They may wash coke to remove more impurities, then carbonize it through lso grade or mix the coke to meet specific requirements before adding it to the furnace with silicon dioxide to make 2017年8月14日 A major challenge in recycling of silicon powder from kerf loss slurry waste is the complete removal of metal particles The traditional acid leaching method is costly and not green In this paper, a novel approach to recover highpurity Si from the kerf loss slurry waste of solar grade silicon was investigated The metal impurities were removed with superconducting high Recovery of silicon powder from kerf loss slurry waste using 2010年1月1日 Crushing is used to very quickly produce a fine powder from a bulk material or fine particle using The initial material can be in the form of a rough powder obtained by crushing the bulk material or in the form of fibers, platelets (small growth on substrates such as singlecrystal silicon (Figs 46 and 47) Fig Mechanical Preparation Techniques SpringerLink2014年4月17日 In studying the sintering of Ti–Si powder mixtures, it was previously found [] that the volumetric shrinkage occurs only in the range of silicon concentrations that do not go beyond the βTi solid solution (about 5 at%Si at 1200°C [])With further increase in the silicon content of powder mixtures, the shrinkage goes over into progressive volumetric expansionSintering of Titanium, Silicon, and Titanium Silicide Powder Mixtures
.jpg)
SILICON INGOT CRACKING CRUSHING FACILITIES
4) Chunk Crushing Equipment (1/7) Specification • Crushing stage : Material: Stainless steel Crushing head:100 x 100 x 300mm, High pure Silicon block:2 blocks/stage Stage layout: V type vertical layout One stage is fixed and other stage is moveable like hinge Motion driven by hydraulic cylinder Crushing size adjustment range: 1530mm 2022年2月15日 Zhang et al (2020b) recovered silicon from DSSW using a twostep sintering (TSS) and acid leaching process (Fig 13) the results indicated that the introduced TSS process not only increased product density and reduced particle size, but also decomposed the SiO 2 layer of silicon powder and promoted densification, the yield of silicon achieved 9603% as the Review of resource and recycling of silicon powder from 2018年8月15日 After sieving the products obtained from the secondary crushing step of the glass layer, glass was mainly distributed in the size fraction range of 45–850 μm with a small amount of Si powder However, purification of the glass (removal of Si powder) could be achieved by dense medium separation at a specific gravity of 24Highvoltage pulse crushing and physical separation of 2022年1月1日 Currently, the main treatment method of MGSRS is crushing and manual selection However, this method is characterized by the low recovery rate of silicon and lower production efficiency such as microsilicon powder [8], [9], silicon waste powder [10], [11], [12], and metallurgicalgrade silicon refined slag (MGSRS) [13]Electromagnetic separation of silicon from metallurgicalgrade silicon
.jpg)
Simulation and Physical Experiment Study on Powder
2020年3月31日 Simulation and Physical Experiment Study on Powder Metallurgy Preparation of Silicon Composite Powder March 2020; IOP Conference Series Materials Science and Engineering 772(1):;2021年7月9日 Performance and use of silicon powder Silicon powder is finely processed by crushing, purifying, grinding, grading, and other processes using silicon dioxide (SiO2), also known as quartz It has high purity, white color, and reasonable particle size distribution It has unique properties and a wide range of usesPreparation, characteristics and application of silicon powder2023年12月28日 Silicon powder goes by many names – crystalline silicon powder, polysilicon powder, semiconductorgrade silicon powder, solargrade silicon powder, metallurgicalgrade silicon powder, and more At a broad level, silicon powders can be categorized by purity levels, material properties, production methods, particle size ranges, and applicationsSilicon Powder: A Versatile Engineering MaterialSilicon powder 98% pure for all uses include using an FDM printer to print silicon wires, electronics and semiconductors, optics and photonics Silicon powder is a fine, granular form of silicon created by crushing or grinding silicon into small particlesSilicon Powder UniversityWafer, Inc
.jpg)
Effect of Grinding Liberation on Recovery of Silicon from MGSi
showed that the liberation degree of silicon particles was 7945% (grinding for 15 min), which was 794% higher than that of silicon particles after 5 min grinding time, and 7715% of the silicon particles were fully liberated The flotation recovery of silicon can increase from 105 to 787% with the appropriate collector2018年12月12日 SELFRAG, the leading supplier of High Voltage Pulse Power (HVP) fragmentation equipment is pleased to announce start up and operation of two new systems for crushing high pure polysilicon and Multiple SELFRAG High Voltage Pulse Power systems for silicon crushing 2021年5月5日 Silicon recovered from Kerf waste is typically new silicon, whereas PV recycled silicon in solar cells used for a quite long time of 25–30 years It is, therefore, quite challenging to remove impurities from PV recycled silicon and subsequent conversion to nanosilicon and reuse them by introducing new properties and functionalities at the nanoscaleEnd‐of‐Life Photovoltaic Recycled Silicon: A Sustainable Ultrafine metal silicon powder, advanced airflow crushing production line, uses highquality metal silicon blocks as raw materials The particle shape is smooth and the particle size is uniform Silicon powder and nanosilica powder of various particle sizes and purity specifications can be customized according to customer requirementsUltrafine Silicon Metal PowderZONACEN CO, LIMITED
.jpg)
Highvoltage pulse crushing and physical separation of
2018年8月15日 After sieving the products obtained from the secondary crushing step of the glass layer, glass was mainly distributed in the size fraction range of 45–850 μm with a small amount of Si powder However, purification of the glass (removal of Si powder) could be achieved by dense medium separation at a specific gravity of 24powders can be obtained by coarse crushing thus avoiding impurity contamination Figure 7 shows a typicalfurnace for the silica reduction process24) Amixture of silica and fine carbon powder is fed from the top of the furnace and reacted inaninert gas atmosphere The synthesized powder is removed through the bottom of the furnaceSilicon carbide powder and sintered materials JSTAGE2024年9月30日 The global silicon metal powder market size was USD 10194 million in 2021 and market is projected to touch USD 141238 million by 2031, at a CAGR of 33% during the forecast period Silicon metal powder is made of silicon lumps by sieving, washing, crushing, and other processes It is also known as industrial silicon powderSilicon Metal Powder Market Size Report Global Forecast 2031Green Silicon Carbide Home Previous Next Green Silicon Carbide Purity:SiC≥99%Particle size: F8F240, 01mm, 13mm, 35mm, 58mm, 100 mesh, 200 mesh, 325 meshApplications: Grinding wheel, abrasives, abrasive tools, sandblasting and rust removal, resin grinding wheels, metallurgy, refractory materials, chemical industry, electronics, aerospace, ceramics, and Green Silicon Carbide Yafeite
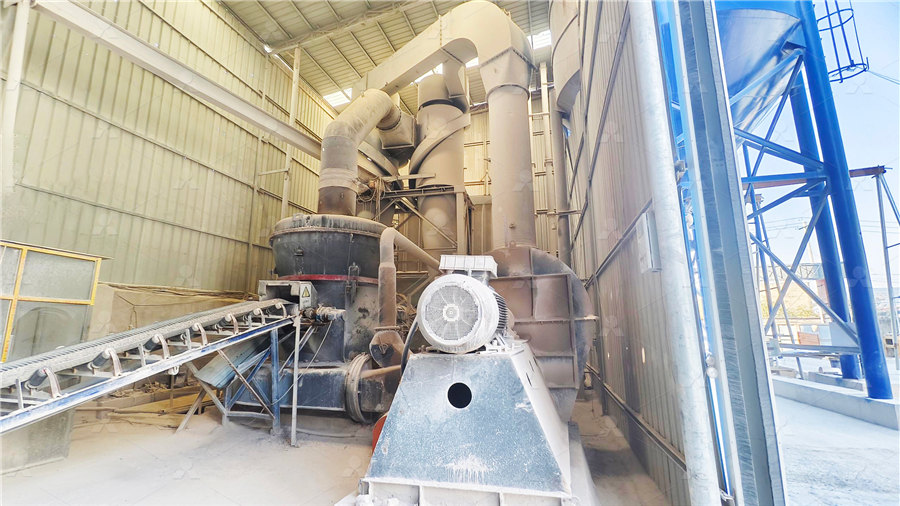
What are the optimal conditions for crushing and grinding silicon
To produce highquality silicon powder, optimal conditions involve careful control of grinding parameters and purification techniques Research indicates that specific grinding methods and equipment significantly influence the properties of the resulting silicon powder ## Grinding Techniques **Planetary Ball Mill**: The finest silicon powder (d50 of 062 μm) was achieved