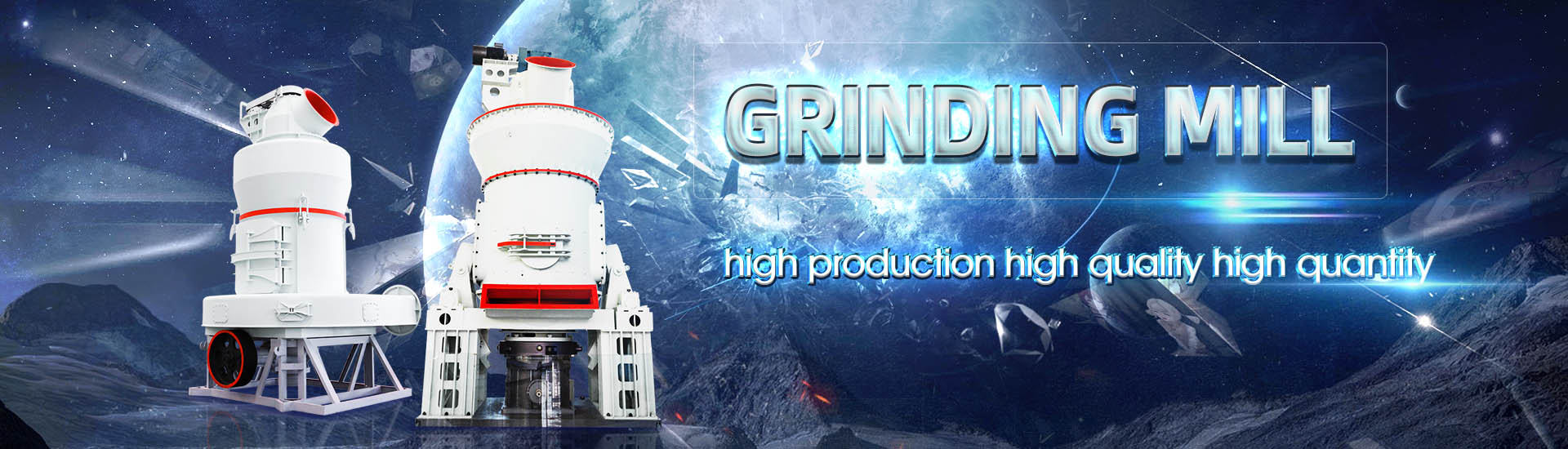
HOME→Changes in fineness of raw material vertical mill after adding calcium chloride liquid Changes in fineness of raw material vertical mill after adding calcium chloride liquid Changes
Changes in fineness of raw material vertical mill after adding calcium chloride liquid Changes in fineness of raw material vertical mill after adding calcium chloride liquid Changes
.jpg)
Analysis of vertical roller mill performance with changes in
2022年5月31日 There is a pair of grinding rollers with a widthtodiameter ratio of 105/340 The MS can be adjusted to generate different product fineness The rotating speed of the millstone 2022年5月31日 The vertical roller mill (VRM) is commonly used for secondary and tertiary crushing processes in numerous industries In this study, the discrete element method (DEM) Analysis of vertical roller mill performance with changes in material The fineness of raw materials used to be controlled at the level of several percents of 90 micron residue in the old wet process or others As the burning method changed toVertical roller mill for raw Application p rocess materialsKey points include: 1) Continuously monitor and adjust process parameters to find the optimum operating conditions of highest capacity and lowest power consumption 2) Relevant process Optimization of Vertical Raw Mill Operation PDF
.jpg)
Optimization of VRM Operation RUCEMRU
Vertical Roller Mills • Do not believe screen values unless you have checked them • Continuously change Process Parameters and document results to find Optimum • Optimum is highest 2023年3月1日 Soft sensor enables computing parameters that can be physically impossible to measure This work aims to develop a soft sensor for raw meal fineness in a vertical roller mill Efficient machine learning model to predict fineness, in a vertical 2017年9月11日 Due to the compact design and material transportation system of vertical roller mills (VRM), some important streams (total mill feed and discharge, dynamic separator feed and reject) remain in the (PDF) Performance Evaluation of Vertical Roller Mill Abstract: The grinding process of vertical mill raw meal in cement industry features nonlinear, strong coupling and long timedelay, which is difficult to model precisely and implement stable control for raw meal fineness Against the problem, a production index prediction model of vertical mill raw meal grindingAdaptive Dynamic Programming in Raw Meal Fineness Control of Vertical
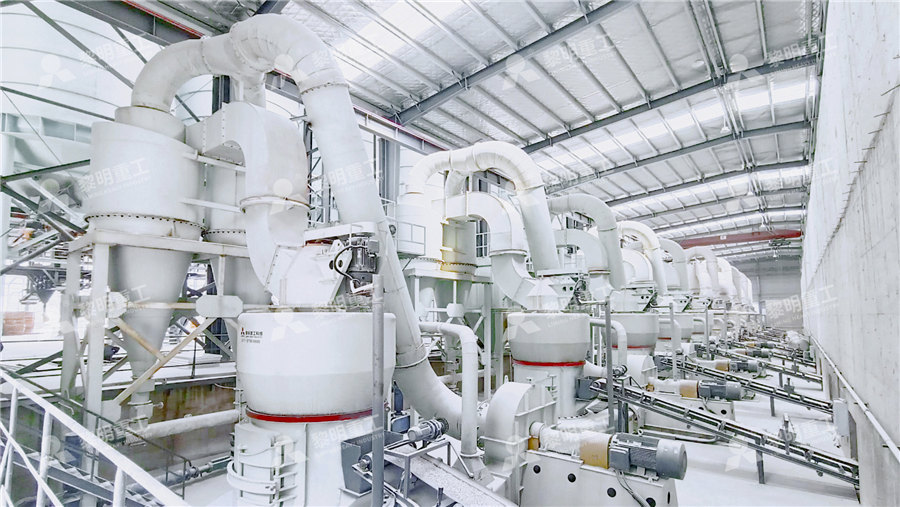
Operational parameters affecting the vertical roller mill
2016年9月1日 In contrast, increasing the separator speed from 60 to 80 rpm at a constant grinding pressure results in a reduced raw material production rate from 240,000 kg/h to 230,000 kg/h and which 2021年1月22日 In the whole process of cement production, the electricity consumption of a raw material mill accounts for about 24% of the total Based on the statistics of the electricity consumption of the raw A Survey and Analysis on Electricity Consumption of Raw Material Mill Vertical Roller Mills What is a Grinding Bed ? Grinding bed is the material layer between the roller and the table It transmits the entire roller force and mill power It is the key issue to successful operating of a VRM !!! Determined by: •Feed Material size •Feed Material Moisture •Dam Ring Height •Grinding Fineness •Air Speed in Optimization of VRM Operation RUCEMRU2019年3月1日 The European cement standard (EN 1971, 2012) defines the requirements of supplementary cementitious materials (SCMs therein) which are the main constituents other than clinker to produce 27 common Portland cements in EuropeThe SCMs are classified according to type and composition A few of them, such as natural pozzolana (P) and limestone (L or LL), Influence of fineness of raw clay and calcination temperature on
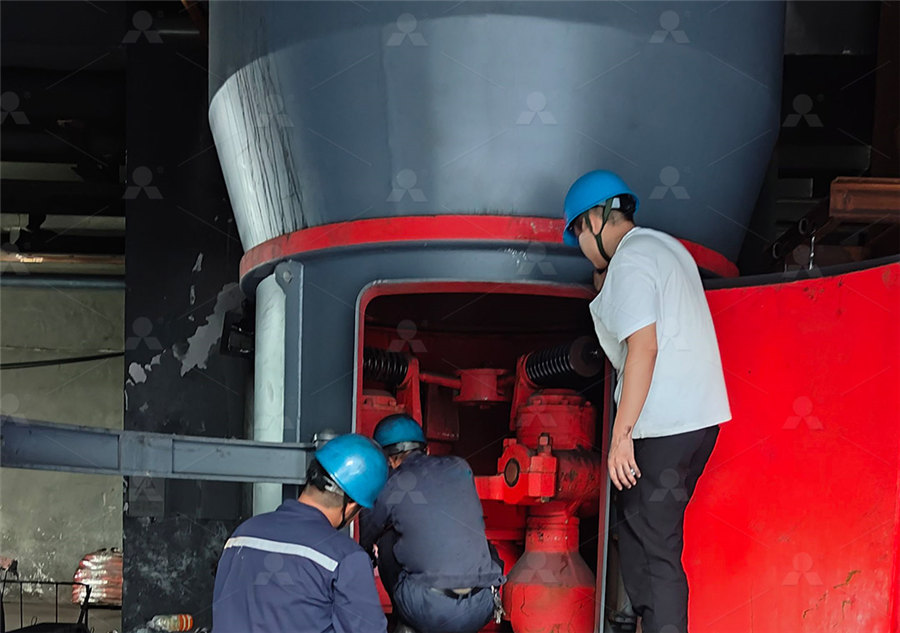
Cements ground in the vertical roller mill fulfil the quality
2013年3月1日 This is referred to as the classifier cut size Generally, the plant operator can control the classifier cut size, and thus the comminuted product fineness by adjusting the classifier rotor speed 2022年5月1日 As shown in Figure 4, included angle between spade and roller is 53°( spade base, point O is the spindle axis, and point O 2 is the roller axis) when the mill is assembledAnalysis of vertical roller mill performance with changes in material • Material grindability • Material temperature • Material moisture • Mixture composition • Composition of raw material • Grinding roller wear • Fineness (Blaine) or residue (VOA) • Mill motor speed • Mill air flow/mill differential pressure • Temperature after the mill • Pressure before the mill • Grinding stock feedPROCESS OPTIMISATION FOR LOESCHE GRINDING PLANTSRaw mill is also called cement raw mill, similar to cement ball mill, it is an important cement milling equipment used in the cement production process Raw mill is mainly used for grinding cement raw meal in the cement factory production process It is also suitable for metallurgical, chemical, electric power and other industrial mining enterprises to grind various ores and other grindable Cement Raw Mill in Cement Plant for Cement Raw Meal Grinding
.jpg)
PROCESS CONTROL FOR CEMENT GRINDING IN VERTICAL ROLLER MILL
Mill motor speed Classifier speed Material temperature Mill air flow Mill fan speed Material moisture Mill differential pressure Water injection Mixture composition Product transport volume Grinding aid injection Composition of raw material Temperature after the mill Hot gas Grinding roller wear Mill vibrations Fresh air Figure22021年7月1日 Vertical stirred mills may be classified according to the speed of the stirrer in two groups: gravityinduced or fluidized mills [[1], [2], [3]]In the gravityinduced mills, the stirrer, generally of the screw type, turns so that the grinding charge exhibits an ascending convective motion at the center, descending from the edges of the screw and close to the mill shell, owing Predicting the effect of operating and design variables in 1 A 5000t/d cement production line EPC turnkey project in South Africa adopts GRMR5341 raw material vertical mill of CHAENG 2 A 5000t/d cement production line in Henan, China adopts GRMR5341 raw material vertical mill of CHAENG 5000t/d cement production line of Henan Meng Electric Group adopts GRMR5341 raw material vertical mill of CHAENGVertical Raw Mill CHAENGVertical Roller Mill Discharge fineness: 1503000 mesh Feed size: 20 mm Output: The material is fed into the main machine of the vertical roller mill through the feed screw and falls into the center of the grinding disc The fineness of the calcium carbonate powder produced can reach 3000 meshesVertical Roller Mill SBM Ultrafine Powder Technology
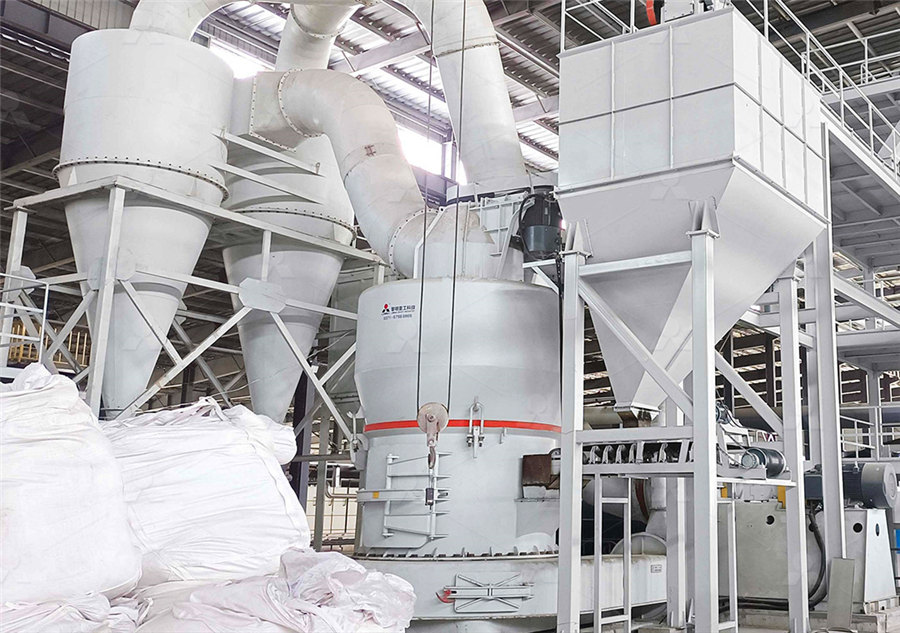
Cement Vertical Mill Vs Ball Mill PDF Mill (Grinding) Scribd
This document compares vertical roller mills to ball mills for cement grinding It discusses that while vertical roller mills have advantages over ball mills for raw material grinding, ball mills remain more commonly used for cement grinding The OK mill is highlighted as a vertical roller mill design that can achieve stable operation for cement grinding due to its patented roller and 2022年5月5日 The main raw material for glass and cement production In addition, it is also used in building materials and poultry feed Shuangfei powder: It is used to produce raw materials such as anhydrous calcium chloride and glass, white fillers for rubber and paint, and building materials Three flying powder:Calcium Carbonate Grinding Mill Powder Modify SBM 2015年1月1日 Vertical grinding mill is the main grinding equipment for the newtype dry cement raw meal production, raw material grinding process in cement industries accounts for approximately 50#8211;60#160;% of the total energy consumption The dynamic characteristics of theModeling Based on the Extreme Learning Machine for Raw Cement Mill FIGURE 4 Particle size distributions of collected samples (Survey 2) Bond work indices and breakage characteristics under compression were determinedPerformance Evaluation of Vertical Roller Mill in Cement
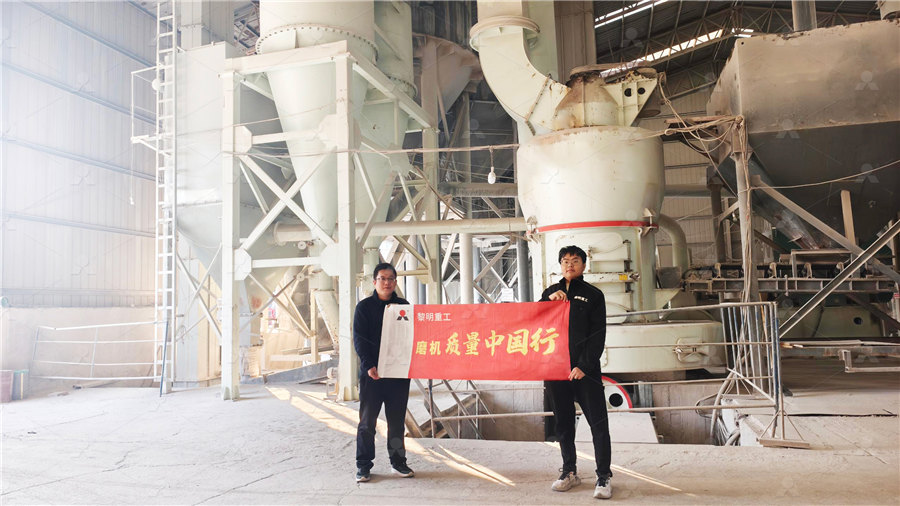
Raw Mill – Raw Mill In Cement Plant AGICO Cement Raw Mill
After the cement raw material is crushed, it will be sent into the raw mill for further grinding until a certain degree of fineness is reached, and then enter the clinker calcination process From the production experience of many cement plants, the selection of cement equipment , especially raw mill, will directly affect the project investment, production schedule and economic benefits2017年1月1日 For decades vertical roller mills have been in use in the cement industry for the grinding of cement raw material and coal Since the 1980's this mill type has also been used for combined or (PDF) Case studies and operational results of modern MVR vertical 2020年10月24日 Raw meal fineness is the percentage content of 80 µm sieving residue after the cement raw material is ground The accurate prediction of raw meal fineness in the vertical mill system is very helpfu Skip to main content You are Prediction of raw meal fineness in the grinding process of cement raw Raw mill is generally called cement raw mill, raw mill in cement plant, it refers to a common type of cement equipment in the cement plantIn the cement manufacturing process, raw mill in cement plant grind cement raw materials Raw mill Cement Plant

PROCESS TRAINING for operators of Vertical RAW Mills
The mill will not run at this time The feed group is stopped when there is sufficient material in the mill The material is then distributed in the mill manually with a shovel When the mill is too full the mill main drive can be overloaded The Great Wall machinery production of independent research and development GRMR6361 vertical roller mill which is the biggest homemade raw material vertical roller mill, millstone effective diameter up to 63m, the quantity of roller is 6, and it can improve the powder milling efficiency greatlyRaw Material Vertical Roller MillBased on nearly 20 years mill research and operation experience, LUM Ultrafine Vertical Mill has been developed as the equipment for ultrafine powder grinding and separation Its production introduces talents in ultrafine powder production and machine manufacturing industry, and absorbs the technologies and experience of ultrafine vertical mills from Germany, Japan and LUM Ultrafine Vertical MillVertical Powder GrinderClirik2023年3月21日 The vertical mill adopts a more advanced analysis machine, Vertical mill heavy calcium production line customer site Processing raw material: calcite Finished fineness: 1501250 mesh Annual output: more than 300,000 tons Finished product use: papermaking, The advantages of ultrafine vertical mill in the processing and
.jpg)
Prediction of raw meal fineness in the grinding process of cement raw
2020年10月24日 Raw meal fineness is the percentage content of 80 µm sieving residue after the cement raw material is ground The accurate prediction of raw meal fineness in the vertical mill system is very In addition, the raw material grinding process will be supported by a QMR² 48/24 For the 4,000 tons per day kiln line Shiva Cement Ltd contracted a quadropol® vertical roller mill for grinding pet coke with a QMK² 32/16 The same mill size QMK² 32/16 is running in Indonesia for years now, grinding and drying lignitequadropol® thyssenkrupp Polysius Grinding TechnologiesThe cement raw material mixtures are ground, dried, and classified in the Pfeiffer vertical roller mill For drying the material, hot gases are directed into the mill Product fineness can be adjusted within a wide range (0063 to 02 mm)Raw mills for all requirements Gebr Pfeiffer2014年4月1日 The newly developed modular roller mill for grinding cement raw material, cement clinker, and additives with an installed power of up to 12,000 kW was specifically designed to meet those needs(PDF) The latest innovative technology for vertical roller mills
.jpg)
(PDF) Performance Evaluation of Vertical Roller Mill
2017年9月11日 Due to the compact design and material transportation system of vertical roller mills (VRM), some important streams (total mill feed and discharge, dynamic separator feed and reject) remain in the Abstract: The grinding process of vertical mill raw meal in cement industry features nonlinear, strong coupling and long timedelay, which is difficult to model precisely and implement stable control for raw meal fineness Against the problem, a production index prediction model of vertical mill raw meal grindingAdaptive Dynamic Programming in Raw Meal Fineness Control of Vertical 2016年9月1日 In contrast, increasing the separator speed from 60 to 80 rpm at a constant grinding pressure results in a reduced raw material production rate from 240,000 kg/h to 230,000 kg/h and which Operational parameters affecting the vertical roller mill 2021年1月22日 In the whole process of cement production, the electricity consumption of a raw material mill accounts for about 24% of the total Based on the statistics of the electricity consumption of the raw A Survey and Analysis on Electricity Consumption of Raw Material Mill
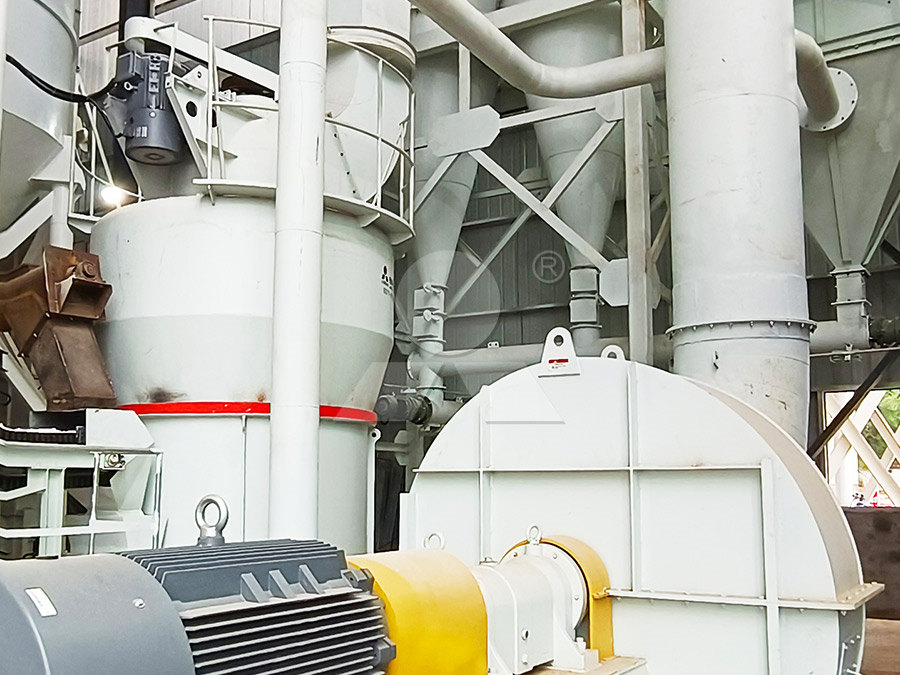
Optimization of VRM Operation RUCEMRU
Vertical Roller Mills What is a Grinding Bed ? Grinding bed is the material layer between the roller and the table It transmits the entire roller force and mill power It is the key issue to successful operating of a VRM !!! Determined by: •Feed Material size •Feed Material Moisture •Dam Ring Height •Grinding Fineness •Air Speed in 2019年3月1日 The European cement standard (EN 1971, 2012) defines the requirements of supplementary cementitious materials (SCMs therein) which are the main constituents other than clinker to produce 27 common Portland cements in EuropeThe SCMs are classified according to type and composition A few of them, such as natural pozzolana (P) and limestone (L or LL), Influence of fineness of raw clay and calcination temperature on 2013年3月1日 This is referred to as the classifier cut size Generally, the plant operator can control the classifier cut size, and thus the comminuted product fineness by adjusting the classifier rotor speed Cements ground in the vertical roller mill fulfil the quality 2022年5月1日 As shown in Figure 4, included angle between spade and roller is 53°( spade base, point O is the spindle axis, and point O 2 is the roller axis) when the mill is assembledAnalysis of vertical roller mill performance with changes in material

PROCESS OPTIMISATION FOR LOESCHE GRINDING PLANTS
• Material grindability • Material temperature • Material moisture • Mixture composition • Composition of raw material • Grinding roller wear • Fineness (Blaine) or residue (VOA) • Mill motor speed • Mill air flow/mill differential pressure • Temperature after the mill • Pressure before the mill • Grinding stock feedRaw mill is also called cement raw mill, similar to cement ball mill, it is an important cement milling equipment used in the cement production process Raw mill is mainly used for grinding cement raw meal in the cement factory production process It is also suitable for metallurgical, chemical, electric power and other industrial mining enterprises to grind various ores and other grindable Cement Raw Mill in Cement Plant for Cement Raw Meal Grinding