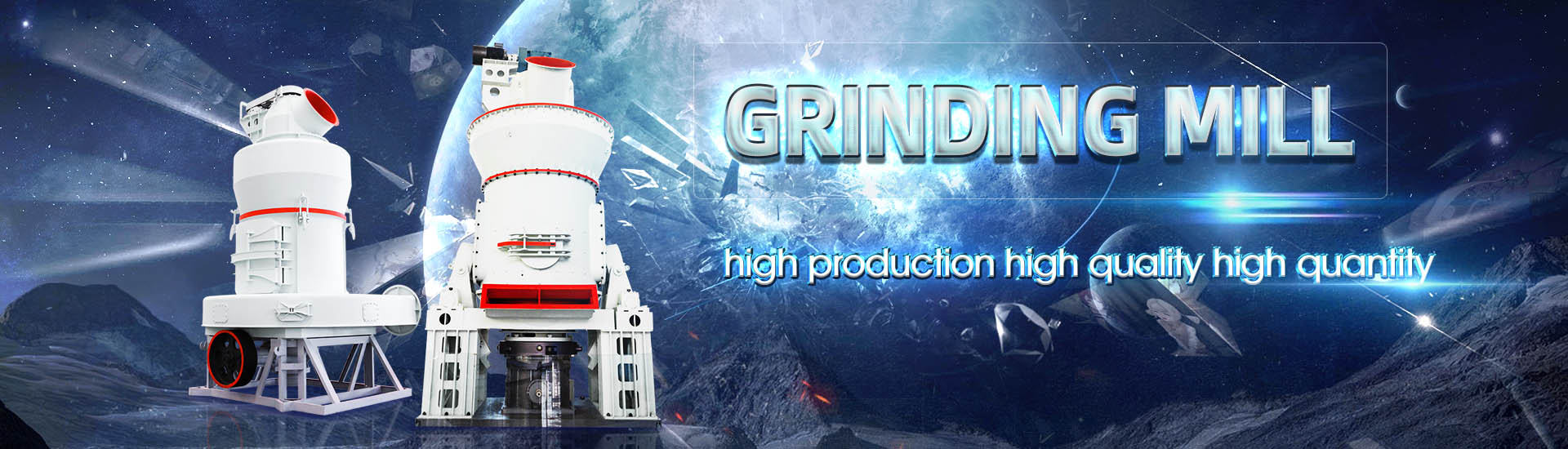
Ore grinding mills are generally started by reducing pressure
.jpg)
Stirred media mills in the mining industry: Material grindability
2020年6月1日 Stirred media mills are used by the mining industry for ultrafine grinding to enhance liberation, and to decrease particle sizes of industrial minerals to tailor functional 2023年7月20日 Ore grinding is a process to further reduce and disperse the ore particle size In the mineral processing industry, ore grinding is the particle size preparation before the Ore Grinding SpringerLinkSize Reduction is mainly done through crushers and mills Crushing and grinding are the two primary comminution processes Crushing is normally carried out on the "runofm ine" oreSIZE REDUCTION BY GRINDING METHODS ResearchGateIt is performed in cylindrical steel vessels that contain a charge of loose crushing bodies—the grinding medium—which is free to move inside the mill, thus comminuting the ore particles Grinding Mill an overview ScienceDirect Topics
.jpg)
Ore Grinding Methods and Process of Ore Grinding
Ore grinding is a process to further reduce and disperse the ore particle size In the mineral processing industry, ore grinding is the particle size preparation before the separation of the 2017年8月24日 Thus, ores must go through a number of different operations to obtain the final products: comminution or size reduction, size separation, concentration or beneficiation, and Mineral Processing SpringerLinkIt is performed in cylindrical steel vessels that contain a charge of loose crushing bodies—the grinding medium—which is free to move inside the mill, thus comminuting the ore particles Chapter 7 Grinding Mills Wills' Mineral Processing Technology, 2023年7月10日 Stirred mills are compressive grinding mills with potential in the mineral and cementbased processing industries for reducing the particle size from a few millimetres to a EnergyEfficient Advanced Ultrafine Grinding of Particles Using
.jpg)
HIGH PRESSURE GRINDING ROLLS—A PROMISING AND COST
High pressure grinding rolls were successfully introduced in the cement industry in the late 1980s and enabled appreciable reduction in energy consumption Promptly enough their potential 2018年8月17日 SemiAutogenous Mills/ SAG Mills (primary grinding mill) — these mills use grinding balls with forces of attrition, impact, and abrasion between grinding balls and ore particles that result in Grinding Mills — Types, Working Principle 2023年4月23日 Harder ores have a larger grinding re sistance than soft ores ther efore, hard ores have lower breakage rates than soft ores Wear resistance depends on the stre ngth of the ore being ground [6 7 ](PDF) Grinding Media in Ball MillsA ReviewThe performance of grinding mills depends on many operating factors among which are the time of grinding, mill speed, grinding media–toore ratio, and filling ratio These factors affect the fraction of energy from the total energy drawn (PDF) Reducing Grinding Energy and Cost
.jpg)
Breaking down energy consumption in industrial grinding mills
2017年1月17日 Grinding mills are infamous for their extremely low energy efficiency It is generally accepted that the energy required to produce new mineral surfaces is less than 1% of the electricity consumed Find your ore mill easily amongst the 42 products from the leading brands (Fritsch GmbH, Retsch, Eriez, ) on DirectIndustry, the industry specialist for your professional purchasesOre mill, Ore grinding mill All industrial manufacturersThe force that keeps the rollers or balls in contact with the bed of feed material on the grinding path may be exerted by gravity, centrifugal force, spring pressure, hydropneumatic action, etc There exist interesting prospects for using these machines as finish grinding mills, ie for clinker grinding 23 Roller mills are characterized by: •Grinding Mill an overview ScienceDirect TopicsOutput: 6 t/h 350 t/h Motor power: 75 kW 3,300 kW Machine length: 2,400 mm 7,200 mm WTM intelligent vertical mill is dedicated to the highefficiency dissociation of minerals, providing users with energysaving, consumptionreducing, qualityenhancing and Highpressure mill, Highpressure grinding mill All industrial
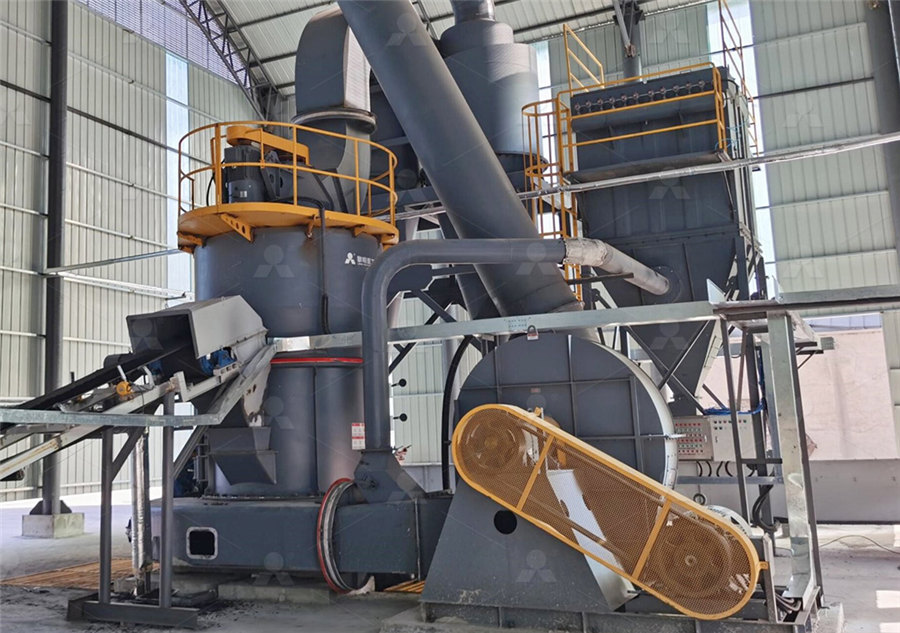
Chapter 7 Grinding Mills Wills' Mineral Processing Technology,
Chapter 7 Grinding Mills Grinding is the last stage in the comminution process where particles are reduced in size by a combination of impact and abrasion, thus comminuting the ore particles According to the ways by which motion is imparted to the charge, grinding mills are generally classified into two types: 2016年7月14日 Thus, some of the finish grinding work is handled by the highpressure grinding roll The throughput of the existing grinding system can be increased by 50 to 70%, while power consumption can be cut by 20 to 30% Additional options for highpressure grinding roll use in gold ore comminution circuits are illustrated in Figure 11HPGR 911Metallurgist2023年7月10日 The present literature review explores the energyefficient ultrafine grinding of particles using stirred mills The review provides an overview of the different techniques for size reduction and (PDF) EnergyEfficient Advanced Ultrafine Grinding of Particles 2012年12月28日 A comparative study was carried out to investigate the effect of highpressure grinding rolls (HPGR) comminution on agitation leaching of gold ore in comparison with the conventional jaw crusher Optimizing the performance of highpressure grinding roll based ore
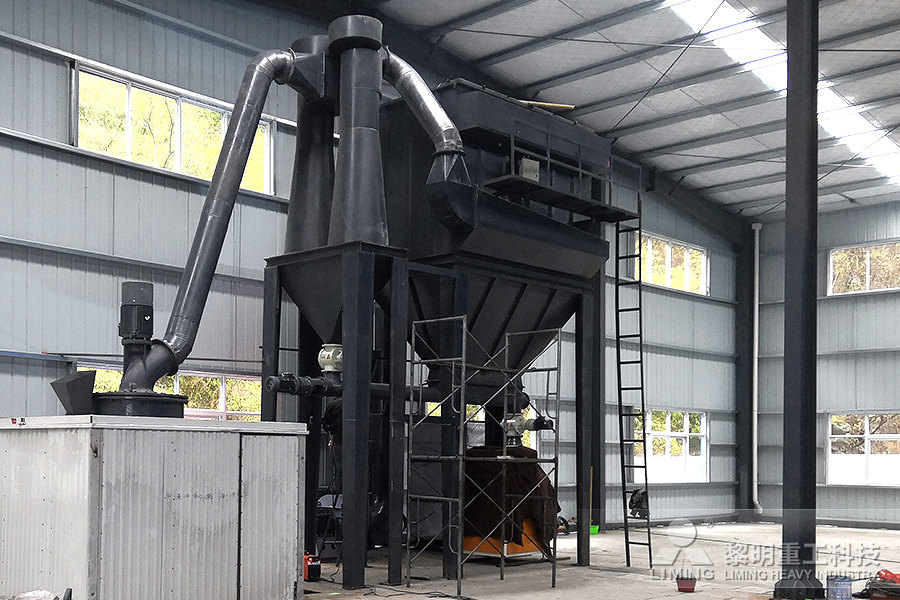
SIZE REDUCTION BY GRINDING METHODS
2017年3月4日 Ball mills are used for wet grinding iron ore, g old/copper ore, nickel ore and other ores, as wel l as lime/limestone for flue gas desulphurisat ion systems, coal and other raw materials Rod mill :The interpretation of the concept of mechanical work in a grinding system used in this paper follows the one postulated by Schellinger (1952), ie it is “the disappearance of energy BREAKING DOWN ENERGY CONSUMPTION IN INDUSTRIAL GRINDING MILLS2023年7月3日 The ores are generally contaminated with earthly or undesired materials (impurities) These are called gangue or matrix The process of metallurgy depends upon the nature of the ore and the impurities present in it Some common steps involved in the metallurgical operations are : 1) Crushing and grinding of the oreCrushing, Grinding and Concentration of the Ore2024年2月26日 To broaden the range of sources of pellet feeds and reduce the production cost of pellets, more steel mills are predicted to use coarse iron ore fines with a relatively low iron grade and low (PDF) Grinding of Australian and Brazilian Iron Ore Fines for Low
.jpg)
HighPressure Grinding Roller Presses for Minerals Processing
HPGR Grinding Process Highpressure comminution of ores with High Pressure Grinding Roller Presses (HPGRs) is predominantly achieved through compression The process takes place between two counterrotating rollers, whereby the ore is chokefed between the rollers The feed material is compressed2024年6月7日 Some of the best grinding mills for achieving fine particle sizes in ore processing include: Ball Mills: Ball mills are commonly used in ore processing for grinding materials into very fine powdersOptimal Grinding Mills for Fine Ore Processing2018年12月24日 According to the desired capacity and the ore communition characteristics observed, a simulation was conducted to determine the size and driving power of the grinding millsEVALUATION OF THE ALTERNATIVES FOR GOLD ORE GRINDING 2014年1月20日 grinding rolls started being the standard used on processing kimberlites, iron ore, copper, gold and other mineral resources The benefits of using the roller presses in ore processing systems(PDF) Effects of High Pressure ORE Grinding on the Efficiency of
.jpg)
(PDF) Control of ball mill operation depending on ball load and ore
2023年12月12日 Ball mills are used for the second stage of ore grinding in mining operations by proportioning ore piles Controlling the operating conditions of ball mills is one of the key factors for optimal 2015年2月2日 High pressure grinding rolls SAG and AG mills are generally installed in a primary milling duty receiving primary crushed (−250 mm) feed the action of reducing size of mineral ore Gangue: invaluable or waste materials AG mill: autogenous grinding mill Comminution SpringerLink2016年6月6日 Common convention generally refers to highaspect ratio mills as SAG mills (with diameter to effective grinding length ratios of 3:1 to 1:1), lowaspect ratio mills (generally, a mill with a significantly longer length than SAG Mill Grinding Circuit Design 911Metallurgist2013年12月18日 Fine grinding, to P80 sizes as low as 7 μm, is becoming increasingly important as mines treat ores with smaller liberation sizes This grinding is typically done using stirred mills such as the Isamill or Stirred Energy Use of Fine Grinding in Mineral Processing
制粉项目-2023.11.17.jpg)
Factors affecting ores grinding performance in ball mills
Effect of media type on ore grinding performance There are many factors that will affect the ore grinding performance in ball mills The type of media, the size and shape of the particles, and the speed at which they are ground are just a few of the factors that can have a significant impactOre Grinding Wu Caibin1 and Xu Kuangdi2 1School of Resources and Environmental Engineering, Jiangxi University of Science and Technology, Ganzhou, China 2Chinese Academy of Engineering, Beijing, China Ore grinding is a process to further reduce and disperse the ore particle size In As for such grinding mills without grinding medium as Ore Grinding Methods and Process of Ore GrindingAutogenous and SemiAutogenous Mills Autogenous (AG) and SemiAutogenous (SAG) milling has seen increased use in recent years, especially in large mineral processing operations These mills typically have a large diameter relative to their length, typically in the ratio or 2 or 25 to 1 AG mills employ ore as the grinding mediaIntroduction to Mineral Processing or Beneficiation2015年8月6日 Ball mills working as the secondary portion of a grinding circuit will utilize the lower profile liners The reason is as lift decreases, friction increases To function effectively they need this type of grinding action to obtain the maximum contact of their high surface areaGrinding Mill Liners 911Metallurgist
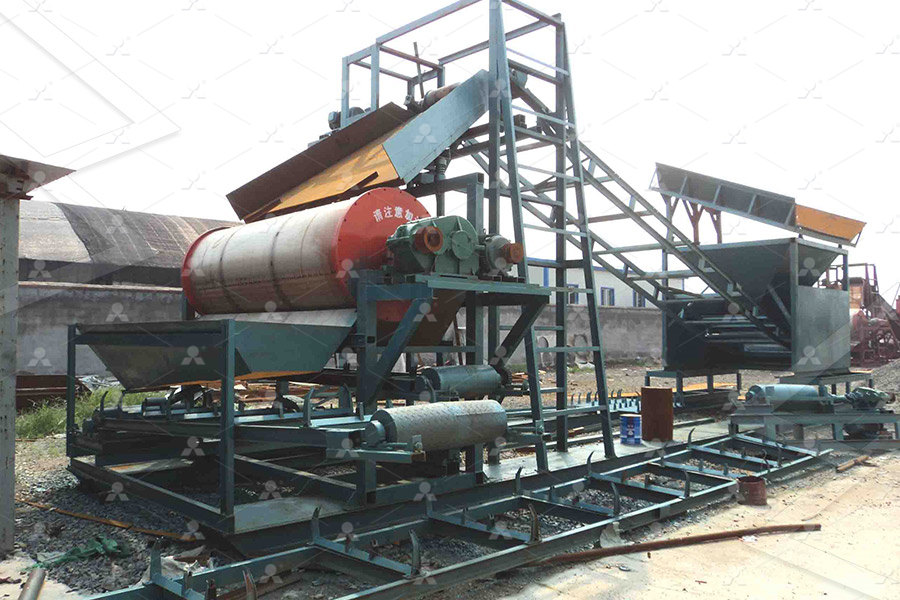
OVERVIEW OF MV DRIVE TECHNOLOGIES IN MINES AND FUTURE
Typical mine has ore processing units at site for grinding of ore This operation is done at site for making product cost effective After grinding and processing, only useful material is transported for further processing Grinding of ore is one of the most power intensive operation in mining For grinding of ore, various mills are2015年3月15日 Hematitedominated ore types had significantly higher P 80 values after the primary grinding step A compared to the other ore types Generally, Fe content increased in finer particle size classes Research of iron ore grinding in a verticalrollermillhighpressure grinding rolls (HPGR) were introduced to the minerals industry approximately three decades ago, and are becoming more common, most concentrators still us e tumbling mills for grinding duties (eg, autogenous grinding [AG], semiautogenous grinding [SAG], rod, or ball mills) While flowsheets have not changed, theFlowsheet of the Future: HighPressure Grinding Rolls, Vertical 2018年8月17日 SemiAutogenous Mills/ SAG Mills (primary grinding mill) — these mills use grinding balls with forces of attrition, impact, and abrasion between grinding balls and ore particles that result in Grinding Mills — Types, Working Principle

(PDF) Grinding Media in Ball MillsA Review
2023年4月23日 Harder ores have a larger grinding re sistance than soft ores ther efore, hard ores have lower breakage rates than soft ores Wear resistance depends on the stre ngth of the ore being ground [6 7 ]The performance of grinding mills depends on many operating factors among which are the time of grinding, mill speed, grinding media–toore ratio, and filling ratio These factors affect the fraction of energy from the total energy drawn (PDF) Reducing Grinding Energy and Cost 2017年1月17日 Grinding mills are infamous for their extremely low energy efficiency It is generally accepted that the energy required to produce new mineral surfaces is less than 1% of the electricity consumed Breaking down energy consumption in industrial grinding millsFind your ore mill easily amongst the 42 products from the leading brands (Fritsch GmbH, Retsch, Eriez, ) on DirectIndustry, the industry specialist for your professional purchasesOre mill, Ore grinding mill All industrial manufacturers
.jpg)
Grinding Mill an overview ScienceDirect Topics
The force that keeps the rollers or balls in contact with the bed of feed material on the grinding path may be exerted by gravity, centrifugal force, spring pressure, hydropneumatic action, etc There exist interesting prospects for using these machines as finish grinding mills, ie for clinker grinding 23 Roller mills are characterized by: •Output: 6 t/h 350 t/h Motor power: 75 kW 3,300 kW Machine length: 2,400 mm 7,200 mm WTM intelligent vertical mill is dedicated to the highefficiency dissociation of minerals, providing users with energysaving, consumptionreducing, qualityenhancing and Highpressure mill, Highpressure grinding mill All industrial Chapter 7 Grinding Mills Grinding is the last stage in the comminution process where particles are reduced in size by a combination of impact and abrasion, thus comminuting the ore particles According to the ways by which motion is imparted to the charge, grinding mills are generally classified into two types: Chapter 7 Grinding Mills Wills' Mineral Processing Technology, 2016年7月14日 Thus, some of the finish grinding work is handled by the highpressure grinding roll The throughput of the existing grinding system can be increased by 50 to 70%, while power consumption can be cut by 20 to 30% Additional options for highpressure grinding roll use in gold ore comminution circuits are illustrated in Figure 11HPGR 911Metallurgist
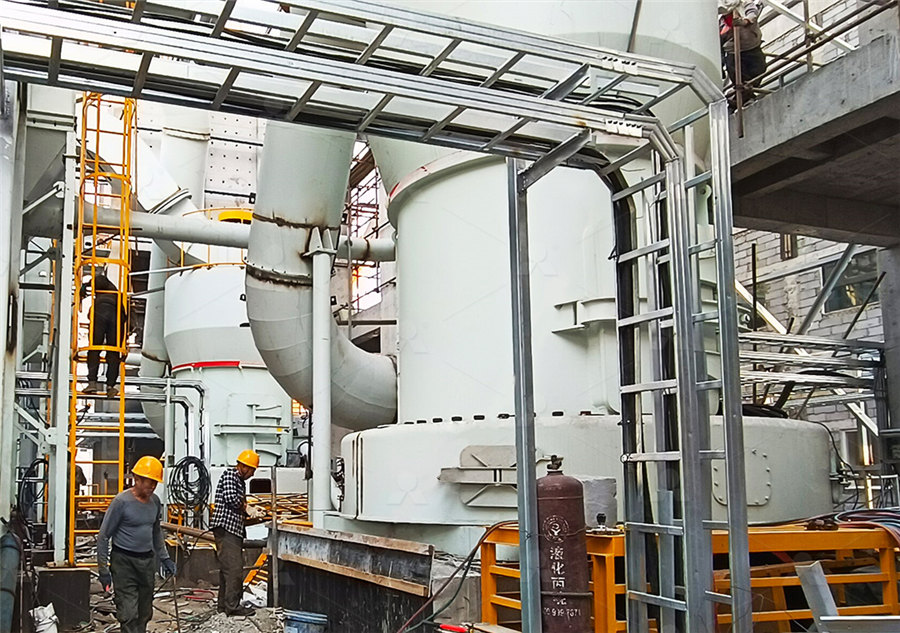
(PDF) EnergyEfficient Advanced Ultrafine Grinding of Particles
2023年7月10日 The present literature review explores the energyefficient ultrafine grinding of particles using stirred mills The review provides an overview of the different techniques for size reduction and