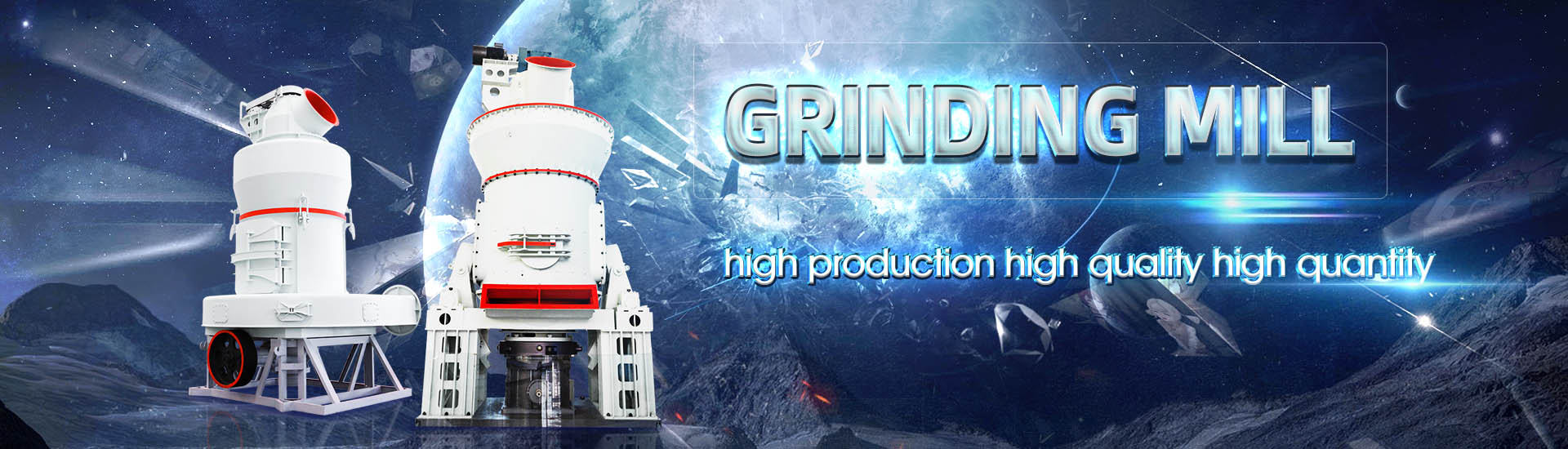
A series machine side immediate crushing and recovery ore mill
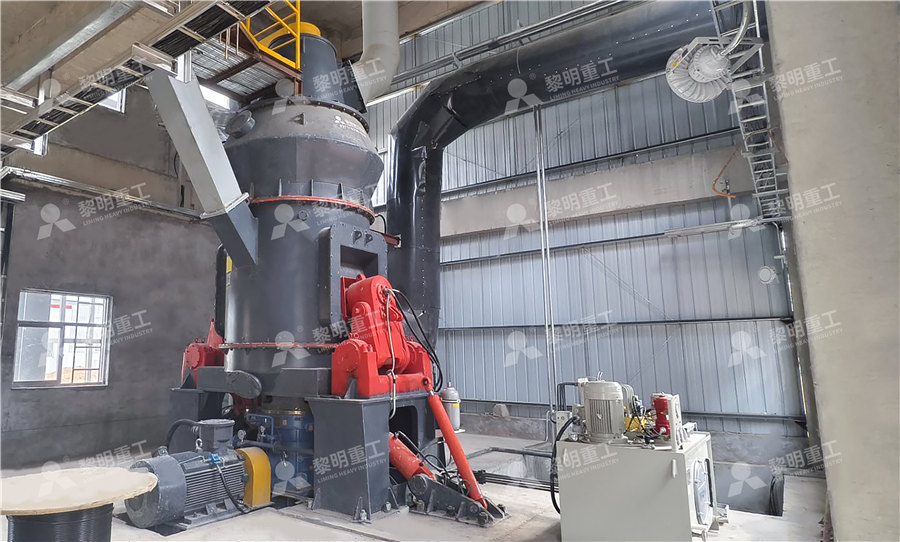
Development of ore sorting and its impact on mineral processing
2014年10月15日 The goal of ore sorting is to reduce the total amount of material sent to the high energy milling circuit, while not significantly impacting total metal recovery In general, ore 2023年6月30日 This article presents a systematic review of the task of improving the energy efficiency of crushing units This is achieved by studying modelling methods and results, the Modeling and Improving the Efficiency of Crushing Equipment2022年9月1日 Selective fragmentation and intergranular microcracks created by blasting can be beneficial to ore recovery incl energy efficiency in crushing and grinding Dry blasting however Towards waterless operations from mine to mill ScienceDirectThis paper describes the objectives of “Mine to Mill” blasting to optimise the system of rock breakage involved in the blasting, crushing and SAG milling of hard, brittle oresBlasting for Mine to Mill Optimisation
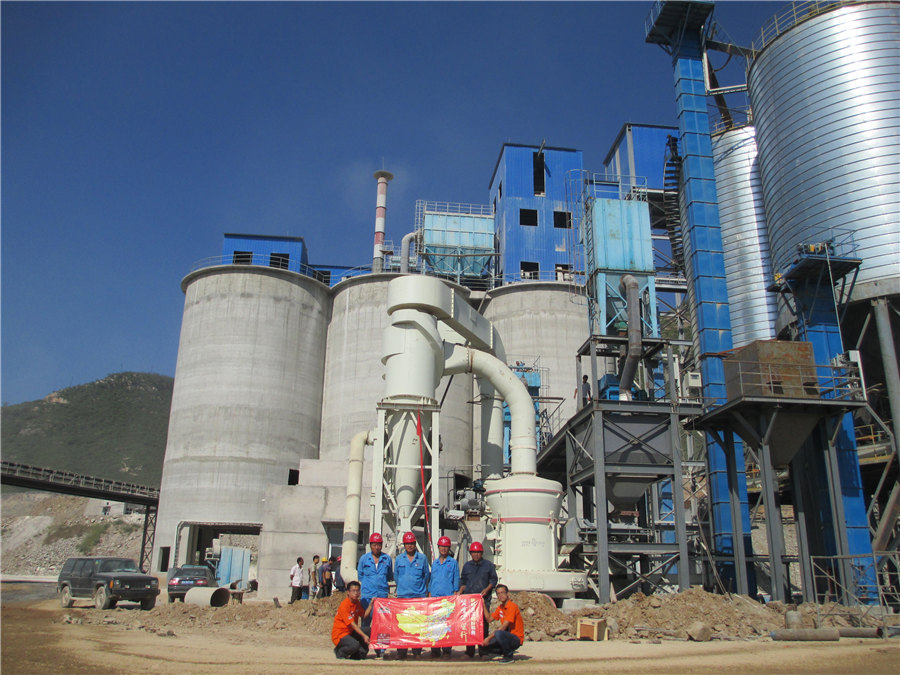
Crushing Plant an overview ScienceDirect Topics
Crushing is the first mechanical stage in the process of comminution in which a principal objective is the liberation of the valuable minerals from the gangue Crushing is typically a dry operation Crushing and grinding are preparatory operations of enrichment and are intended for ore grains separation (opening) of various minerals, contained in the mineral in the form of closely Reengineering of the ore preparation production process in the 2003年1月1日 Blasting has an important impact on mining and milling well beyond the necessary ability to dig and load the ore efficiently There is an increasing body of blasting (PDF) The Effects of Blasting on Crushing and Grinding2022年10月4日 Optimum rock fragmentation from mining to mineral processing must meet the following conditions (Zhang 2016a): (1) minimum cost in the size reduction chain: Reduction of Fragment Size from Mining to Mineral Processing: A
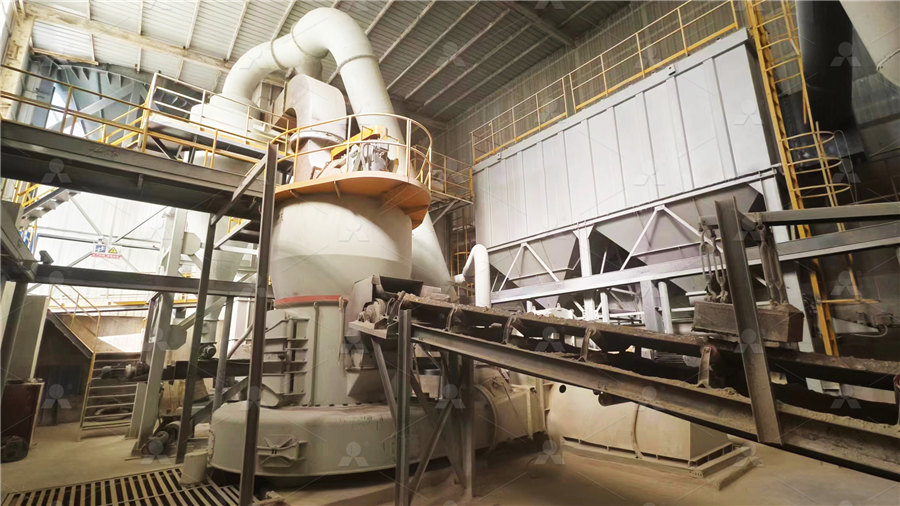
Advanced Analytics for Mineral Processing SpringerLink
2022年2月23日 Crushing, grinding, and milling circuits are used to reduce the ore size to a specific range at which the mineral concentration, with procedures like gravity separation and 2003年1月1日 Mining is typically conducted through a set of interdependent unitoperations, which commonly include drilling, blasting, digging and hauling, in order to deliver the required ore material into (PDF) The Effects of Blasting on Crushing and Grinding 2014年10月1日 In a test performed in the Loesche test center in Germany, copper slag grinding saved 229% energy in an airswept model and 344% energy in an overflow model [13,14]Copper Ore Grinding in a Mobile Vertical Roller Mill Pilot Plant2001年9月1日 Partial secondary crushing of the mill feed is reported for example at Mt Rawdon in Queensland (Putland et al, 2004), Porgera (Thong et al, 2006) and St Ives in Western Australia (Atasoy et al Primary versus secondary crushing at St Ives (WMC) SAG mill circuit
.jpg)
(PDF) Grinding Media in Ball MillsA Review ResearchGate
2023年4月23日 Comminution is a very important and resultdetermining step in mineral processing This is because further downstream processes in the beneficiation chain depend entirely on it2024年4月26日 The crushed ore obtained from the crushing stage is typically in larger size fractions and needs to be further processed through screening 2 Screening Screening is the process of separating the crushed ore into various size fractions It involves passing the crushed ore through a series of screens with differentsized openingsIron Ore Processing: From Extraction to ManufacturingThis means that the number of crushing stages can be reduced depending on the feed size accepted by primary grinding stage Image of a “Classical” 3stage ore crushing prior to rod mill [image: (13551)] Diagram of Typical 12 stage ore crushing prior to AGSAG mill [image: (13552)] Calculation of Reduction Ratio in CrushingAMIT 135: Lesson 5 Crushing – Mining Mill Operator Training2021年7月6日 PDF Comminution: The key to optimizing concentrate, grade and recovery Find, read and cite all the research you need on ResearchGateComminution a Heart of Mineral Processing ResearchGate
.jpg)
Winning the Metal: Ore Mills of the West Western Mining History
Crushing the Ore Mills consisted of machinery and materials set up to recover the valuable contents in ores The mills were typically enclosed in buildings with the equipment arranged in levels, with the lower level last so gravity moved the product downwardIt is normalised based upon the ore resistance to breakage, so it provides feedback about the health' of the milling process under varying operating conditions and ore types Mill grinding efficiency is measured at the same time as CSE through circuit samplingFunctional performance analysis combines CSE and mill grinding efficiency to provide 12th Mill Operators' Conference 2014 AusIMM2019年12月23日 The actual capacity was obtained to be 301 kg/h after the performance evaluation of the machine, and it has a 98 % material recovery rate and 7525 % machine efficiency The machine has a DEVELOPMENT OF A HORIZONTAL SHAFT HAMMER MILL CHAPTER 2022年10月4日 21 Energy Rock drilling, blasting, and comminution (crushing and grinding) consume a vast amount of energy in hard rock mines As mentioned in Sect 1, statistics from hard rock mines indicates that drilling and blasting consumes 2% and comminution does 53% of the total energy input in the whole production chain from mining to mineral processing (Spathis Reduction of Fragment Size from Mining to Mineral Processing: A
.jpg)
Rod Mills: Efficient Grinding Solutions for Mining
2016年6月1日 The pulp discharge from the mill is collected by a housing around the discharge ring and may be directed to either side of the mill or immediately below the mill centerline Dry ROD MILL Grinding No other type of mill is so 2021年4月19日 PDF Published in MATERIA 2021;23:6366 The idea of minetomill optimization has been tested in various mines in last decades, resulting in higher Find, read and cite all the research you (PDF) Feasibility and necessity of mine to mill2009年5月17日 Ore processing and metal recovery involves several key steps: 1 Crushing and grinding the ore to prepare it for separation 2 Separating the valuable minerals from waste rock via techniques like flotation or magnetic separation This produces a concentrate 3 Further processing the concentrate using methods like leaching to extract the Topic 3: Ore processing and metal recovery PPT SlideShare2018年7月19日 The detailed design procedure for a hammer mill machine is presented The system designed is a modification to the conventional hammer mill with a circular bottom casing and a semicircular screen(PDF) Design, construction and performance evaluation of a
.jpg)
(PDF) Sensor‐Based Ore Sorting Technology in Mining—Past,
2019年8月29日 The sensor ‐ based ore ‐ sorting step practically never reaches 100% recovery, and this has to be regarded while evaluating a project and has to be accounted for as costs for lost production The2020年11月8日 Vertical Shaft Impactors Sandvik is a well established market leader in autogenous VSI crushing The CV200 series offers producers economical and reliable crushing solutions that will result in significant reductions in maintenance with improved health safety considerations Mobile Impact CrusherCrusher; Crushing; and Classification Equipment PPT SlideShare2020年8月4日 Optimizing Feed Milling Processes for Enhanced Efficiency and Quality: A Comprehensive Technical Study(PDF) Optimizing Feed Milling Processes for Enhanced Efficiency 2021年10月7日 The actual capacity was obtained to be 301 kg/h after the performance evaluation of the machine, and it has a 98 % material recovery rate and 7525 % machine efficiency The machine has a Design and Performance Evaluation of a Stone Crusher
.jpg)
SIZE REDUCTION BY CRUSHING METHODS ResearchGate
2017年3月4日 A simplified model (kinematic diagram) of the mechanism of the double buckling jaw crusher is shown in Fig 20 The mechanism in question is a six membered mechanism formed by attaching a binary 2016年1月17日 In mineral processing, the reduction of minerals by crushing and grinding may be regarded as having one or other of two main objectives: the attainment of a size appropriate for the direct industrial application of the Crushing Mineral Processing 911Metallurgist2017年2月17日 When making comparisons of the efficiencies of different grinding and crushing machines it is desirable to be able to estimate the work actually done in crushing the ore from a given size of feed to a given size of product, the screen analysis of both feed and product being determined Messrs Klug and Taylor, in a paper on this subject, published in the monthly Difference between Crushing and Grinding 911MetallurgistTherefore, differential blasting is a combination of 'mine to mill' (M2M) (McKee, 2013;Scott et al, 2009; Scott et al, 2002) blasting, to maximise the ore fines with a limited top size, and the Tracking and Quantifying Value from ‘Mine to Mill’
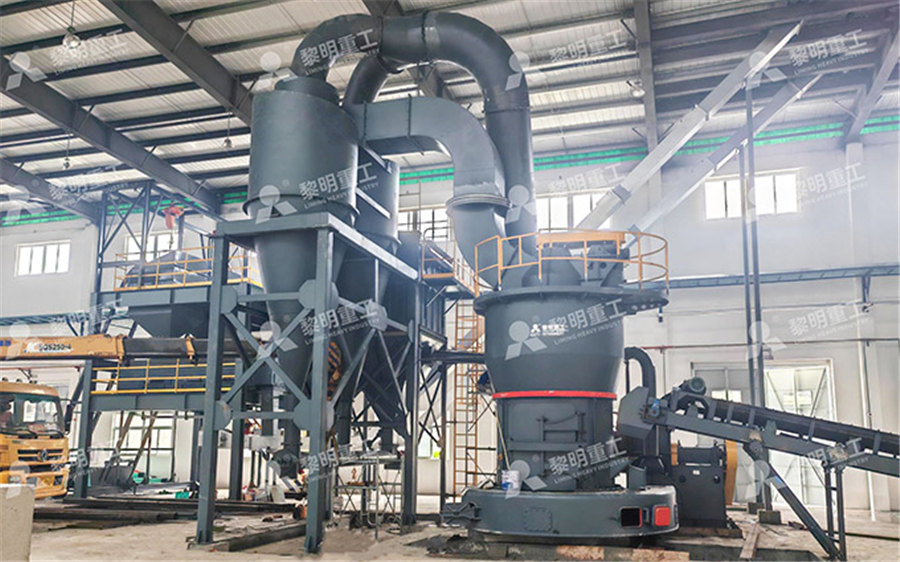
Stone Crushers, Mill and Grinding
K SERIES MOBILE CRUSHING SCREENING PLANT is researched to meet customers’ demand on high quality and high output, 5X Pendulum Roller Grinding Mill 5X Series Pendulum Roller Grinding Mill is new mature and advanced equipment sand making machines, pulverizers and mobile crushing stations Address No169, Science (Kexue) 2023年12月1日 Due to the decreasing reserves of highgrade iron ore and secondary resources used for steelmaking, it has become an important research and development area to improve the grade of iron ore through crushing (Gul et al, 2014)The quality of iron ore crushing directly affects the performance of pellets and sinter, so as to influence the quality and performance of Crushing characteristics and performance evaluation of iron ore 2024年1月31日 This study focuses on the design and construction of an improved crushing machine with a capacity of 015 (150 kg/hr) tons per hour, 15 Hp, and 2910 rpm speedDesign and Fabrication of a Bone Crushing Machine/Hammer Mill Having proved the value of its ore at the Syndicate mill, the Standard Company decided almost immediately to build its own mill at the base of the hill on the east side of town Completed in July 1877, the mill housed 20 stamps, blanket sluices, a series of 20 settlers, 16 pans, and 2 agitators, all for treating pulp discharged from the stampsGold and Tailings: The Standard Mill at Bodie, California
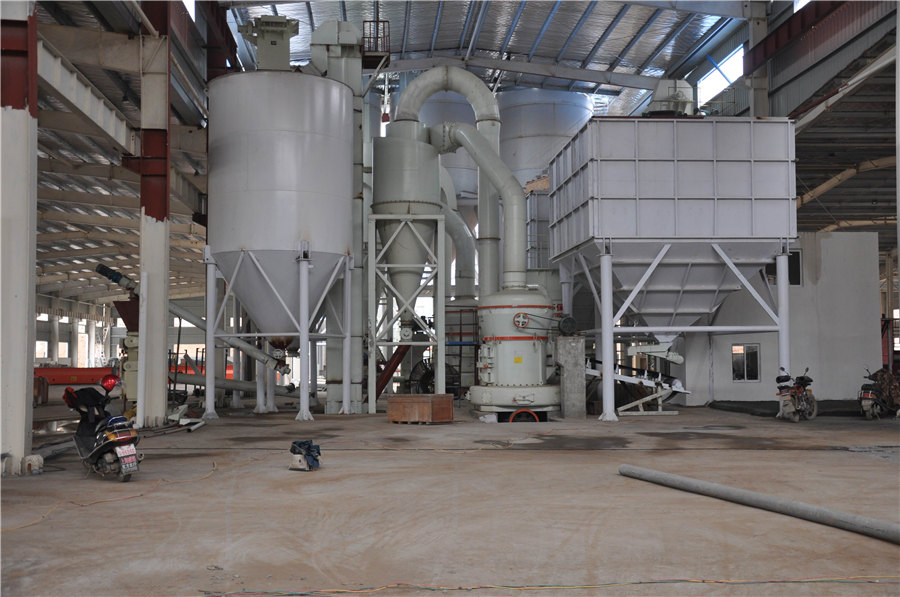
Equipment Sizing: Crusher or Grinding Mill 911Metallurgist
2016年7月8日 * Crushing provides for two 7hour shifts, eighth and sixteenth hours are for cleanup Rod and Ball Milling each provide for three 8hour shifts of continuous operation By referring to equipment manufacturer’s bulletin on crushers, Fig 1, a crusher producing 80% passing 3/4″ requires a close side setting of approximately 5/8″We are usually limited by practicality, finances and permitting to a simple crushing and grinding circuit, with a gravity recovery system for the free milling values and valuecontaining sulfides Mt Baker Mining and Metals is focused on providing a costeffective and durable ore processing plant that includes a jaw crusher, hammer mill, size classification equipment, and sluice/shaker tableOre Milling Mt Baker Mining and Metals2017年6月30日 A review on the design and operations challenges of a single toggle jaw crusher is presented Strength and fracture toughness of the material to be crushed are intrinsic properties that determine DESIGN AND OPERATIONS CHALLENGES OF A SINGLE TOGGLE 2003年1月1日 Mining is typically conducted through a set of interdependent unitoperations, which commonly include drilling, blasting, digging and hauling, in order to deliver the required ore material into (PDF) The Effects of Blasting on Crushing and Grinding
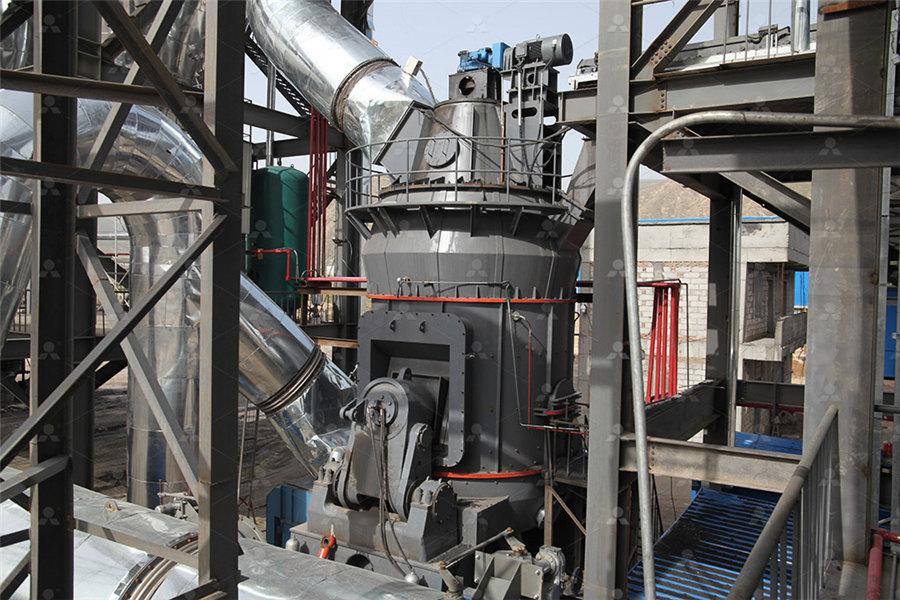
Copper Ore Grinding in a Mobile Vertical Roller Mill Pilot Plant
2014年10月1日 In a test performed in the Loesche test center in Germany, copper slag grinding saved 229% energy in an airswept model and 344% energy in an overflow model [13,14]2001年9月1日 Partial secondary crushing of the mill feed is reported for example at Mt Rawdon in Queensland (Putland et al, 2004), Porgera (Thong et al, 2006) and St Ives in Western Australia (Atasoy et al Primary versus secondary crushing at St Ives (WMC) SAG mill circuit2023年4月23日 Comminution is a very important and resultdetermining step in mineral processing This is because further downstream processes in the beneficiation chain depend entirely on it(PDF) Grinding Media in Ball MillsA Review ResearchGate2024年4月26日 The crushed ore obtained from the crushing stage is typically in larger size fractions and needs to be further processed through screening 2 Screening Screening is the process of separating the crushed ore into various size fractions It involves passing the crushed ore through a series of screens with differentsized openingsIron Ore Processing: From Extraction to Manufacturing
.jpg)
AMIT 135: Lesson 5 Crushing – Mining Mill Operator Training
This means that the number of crushing stages can be reduced depending on the feed size accepted by primary grinding stage Image of a “Classical” 3stage ore crushing prior to rod mill [image: (13551)] Diagram of Typical 12 stage ore crushing prior to AGSAG mill [image: (13552)] Calculation of Reduction Ratio in Crushing2021年7月6日 PDF Comminution: The key to optimizing concentrate, grade and recovery Find, read and cite all the research you need on ResearchGateComminution a Heart of Mineral Processing ResearchGateCrushing the Ore Mills consisted of machinery and materials set up to recover the valuable contents in ores The mills were typically enclosed in buildings with the equipment arranged in levels, with the lower level last so gravity moved the product downwardWinning the Metal: Ore Mills of the West Western Mining HistoryIt is normalised based upon the ore resistance to breakage, so it provides feedback about the health' of the milling process under varying operating conditions and ore types Mill grinding efficiency is measured at the same time as CSE through circuit samplingFunctional performance analysis combines CSE and mill grinding efficiency to provide 12th Mill Operators' Conference 2014 AusIMM
.jpg)
DEVELOPMENT OF A HORIZONTAL SHAFT HAMMER MILL CHAPTER
2019年12月23日 The actual capacity was obtained to be 301 kg/h after the performance evaluation of the machine, and it has a 98 % material recovery rate and 7525 % machine efficiency The machine has a