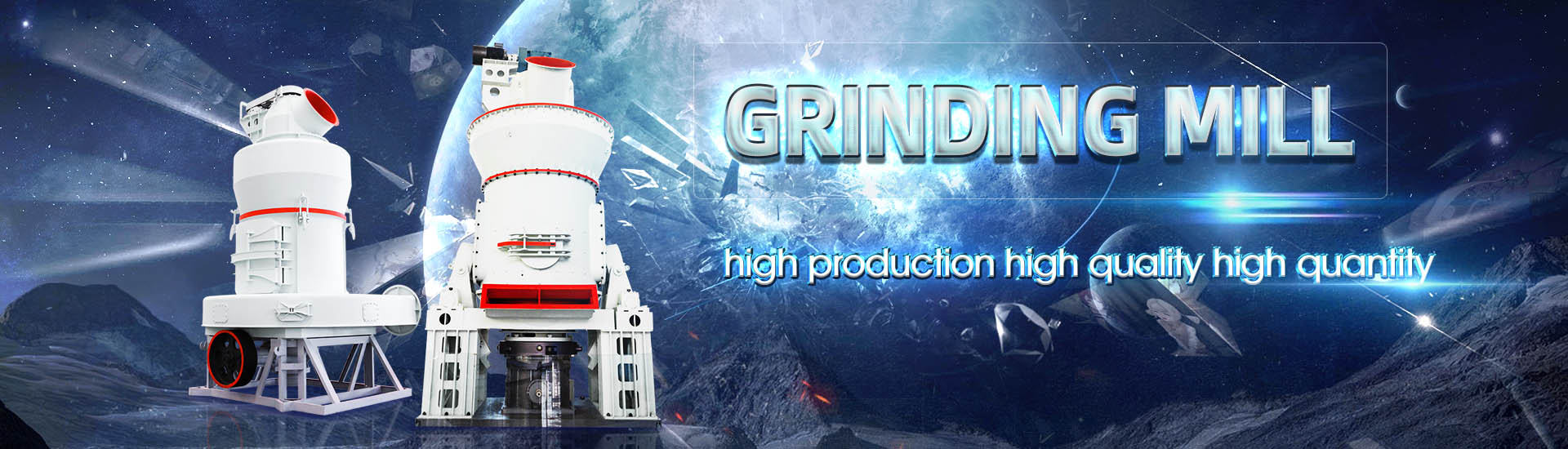
Gypsum grinding mill process flow
.jpg)
Grinding and calcining of gypsum with Pfeiffer grinding plants
One option is direct calcining in a Pfeifer vertical roller mill of the type MPSGC (Fig 2) In this process, the gypsum is dried and ground to the required fineness of the plaster in the mill Gypsum grinding / calcining mills with throughput capacities from 10100t/hr are successfully in operation Mills for much higher throughputs are also available GG: How are your gypsum GLOBAL GYPSUM: GRINDING Gebr Pfeiffer2021年8月4日 CLIRIK gypsum grinding mills are specialized in the production process of 303000 mesh gypsum powder The gypsum powder production process is obtained by grinding CLIRIK gypsum grinding mill for gypsum powder production process2019年8月23日 Gypsum processing description from its geology mineral property to how to extract mineral from rock and placer deposit, related processing plant flow chart and layout designGypsum Processing Equipment, Process Flow, Cases
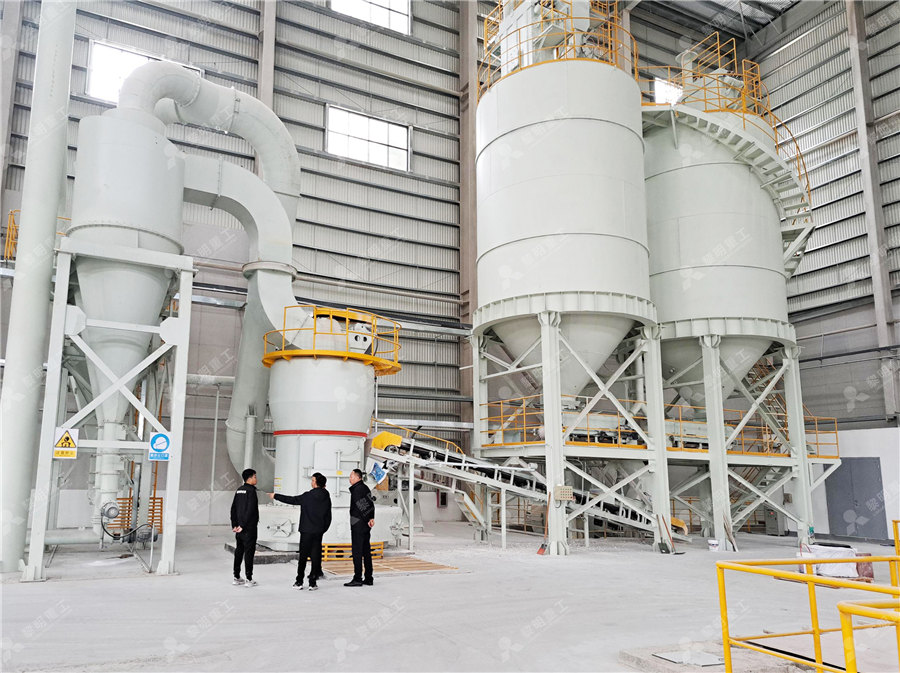
Grinding and calcining of gypsum with Pfeiffer
Grenzebach BSH from Bad Hersfeld/Germany has ordered a Gebr Pfeiffer vertical roller mill of the type MPS 100 GC for a plant in Bou Saada/Algeria The MPS mill is designed for the grinding and more// Grindingcalcining refers to the process of grinding, separating, drying and calcining gypsum to form hemihydrate plaster The MPS mill allows mixes of natural gypsum, FGD gypsum and pre PFEIFFER PRODUCTS FOR THE GYPSUM INDUSTRYThree stationary grinding rollers roll on a rotating grinding table The material is drawn in between grinding rollers and grinding track and ground by pressure and shear The compression force Competence in gypsumThe MPS mill also grinds, dries, calcines, and classifies gypsum without any problem, all in a single machine, for any fineness requested and considering individual requirements The MPS vertical roller mill built to last, reliable and Coal mill, gypsum mill, clay mill, etc Pfeiffer MPS mills
.jpg)
Limestone crushing, sand making and grinding process
2022年7月20日 Process flow of limestone sand production line 1 Process flow of limestone manufactured sand Sand making: Through the crushed limestone, part of it is directly sent to the stockpile as a finished product, and the other 2021年4月19日 Grinding of finished cement is performed in a single stage, intergrinding materials with very different grindabilities This intergrinding process has many different interactions among the different components of the finished cement In a context of developing more sustainable and less energy intensive processes, it is important to understand the Resistance to Grinding and Cement Paste Performance of Blends 2013年5月21日 The gypsum calcining systems are designed to process natural gypsum from the local underground gypsum quarries A greenfield project To take over production from the old three calcining kettles, the new calcining line was designed for a plaster capacity of 14t/hr, utilising a Claudius Peters EM 47568 Gypsum Calcining MillInnovative gypsum processing at GIPS AD2016年1月20日 Fig 4 shows material flows during the cement grinding Clinker, gypsum, and additives are matched in required proportions by a weigh feeder, after which they are conveyed to the mill that performs the remaining grinding The grinding process occurs in a closed system with an air separator that divides the cement particles according to sizeAnalysis of material flow and consumption in cement production process
.jpg)
Gypsum Grinding Mill
Specific gravity is 23 With flexibility and flexibility After Grinding Process by Gypsum Grinding Mill,Gypsum Powder is a widely used industrial materials and building materials Retarder for cement, gypsum building products, model Gypsum Grinding process Flow: Configured Equipment: Hopper+ Bucket Elevator+Vibrating Feeder +Grinding Mill Installing a grinding mill that is appropriate for the objective would be one with the key specifications for costeffective and troublefree material processing if a grinding stage is involved Screening may be defined as a mechanical operation which separates particles as outlined by their sizes and their acceptance or rejection by openings of a screening faceGranite Powder Process Technology, Gypsum Grinding MillThe proportions of gypsum, hemihydrate and anhydrite are individually optimized for each type of cement [7] The dehydration of gypsum to hemihydrate normally takes place during the grinding process in the cement mill Depending on the mill temperature, the gypsum becomes partially or completely dehydrated to hemihydrate or anhydrite respectively2 Gypsum dehydration during cement production ZKGQ Raw mill air seperator 26 R Finish grinding mill feed belt 27 S Finish grinding mill weight hopper 28 T Finish grinding mill air seperator 29 U Preheater kiln 30500622 V Preheater/Precalciner kiln 30500623 The second step in portland cement manufacture is preparing the raw mix, or kiln feed, for the116 Portland Cement Manufacturing US Environmental
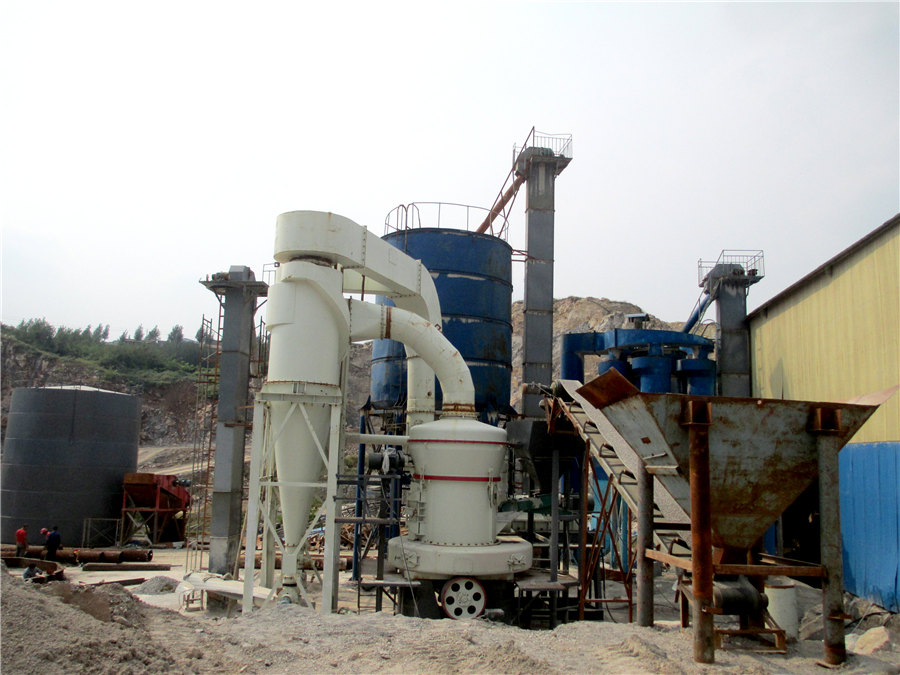
Cement industry : grinding process of ball mill PPT SlideShare
2020年10月5日 12 Working In case of continuously operated ball mill, the material to be ground is fed from the left through a 60° cone and the product is discharged through a 30° cone to the right As the shell rotates, the balls are lifted up on the rising side of the shell and then they cascade down (or drop down on to the feed), from near the top of the shell5 //Heating natural gypsum or gypsum mixes in the MPS mill only until their surface moisture is fully evaporated is called grindingdrying To do this, the mill is operated at a gas temperature of max 90 °C after classifier During grindingdrying the product temperature is approximately 8085 °C, no calcining occurs and the dihydrate contentPFEIFFER PRODUCTS FOR THE GYPSUM INDUSTRYroller mill, where it is ground to the extent that 90 percent of it is less 149 micrometers (µm) (100 mesh) The ground gypsum exits the mill in a gas stream and is collected in a product cyclone Ore is sometimes dried in the roller mill by heating the gas stream, so that drying and grinding are accomplished simultaneously and no rotary dryer 1116 Gypsum Manufacturing US EPAJust 4 % of the energy is used for comminution Nevertheless when grinding is required the ball mill is the most accepted element in the cement grinding The reasons are high reliability, the good possibility of gypsum dehydration, Process Training Ball Mill INFINITY FOR CEMENT
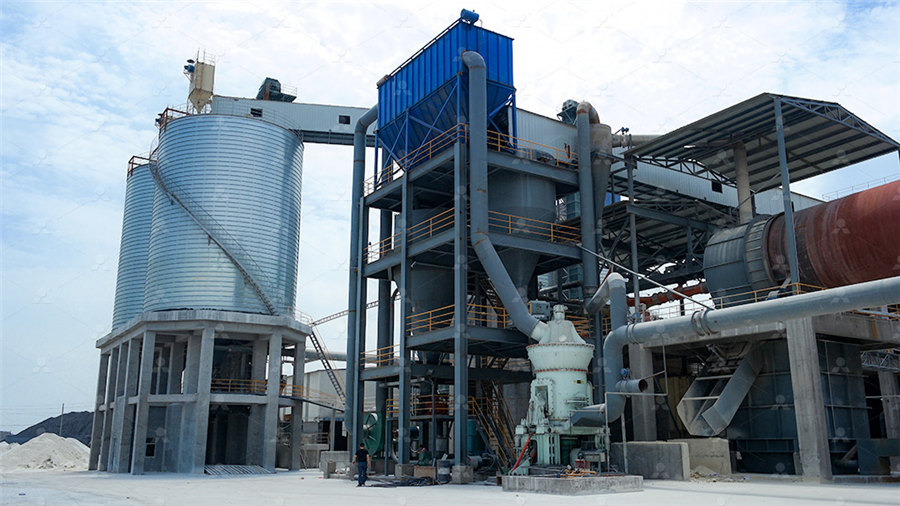
en/115/flow sheet of gypsum process plantmd at main
The process to produce gypsum board generally consists of calcining and or grinding gypsum powder,forming a gypsum panel product and drying off excess waterInnogyps has prepared a training presentation that introduces the gypsum board manufacturing process in detail including: Gypsum and its properties Gypsum chemistryUsed Gypsum Processing Plant Building gypsum is a product that uses gypsum as raw material and is ground after calcination, also known asβType I hemihydrate gypsum is the main raw material for gypsum products such as gypsum plasterboard, fiber gypsum board and gypsum decorative board The main machine in the production equipment of building gypsum powder is gypsum grinding mill equipmentNews Advantages Of Gypsum Vertical Roller Mill As Production Coarse natural gypsum or mixtures of such gypsum with FGD gypsum are ground, dried, calcined, and classified in the Pfeiffer vertical roller mill To be noted that up to 20% of recycling material may be added if required Product fineness and product properties can be adjusted within wide limits (0063 to 05 mm)Gypsum mill for all requirements Gebr PfeifferThis mill at this time produces two types of cement namely Ordinary Portland Cement (OPC) and Pozzolana Portland Cement (PPC) OPC comprises 90%clinker, 5%additive (limestone) and 5 %( gypsum) PPC comprises 70% of clinker, 2529%% pozzolana and 5%gypsum The design capacity of the mill is 120t/h for OPC cement But currentlyManufacturing process flow 1 Quarrying and Crushing Messebo
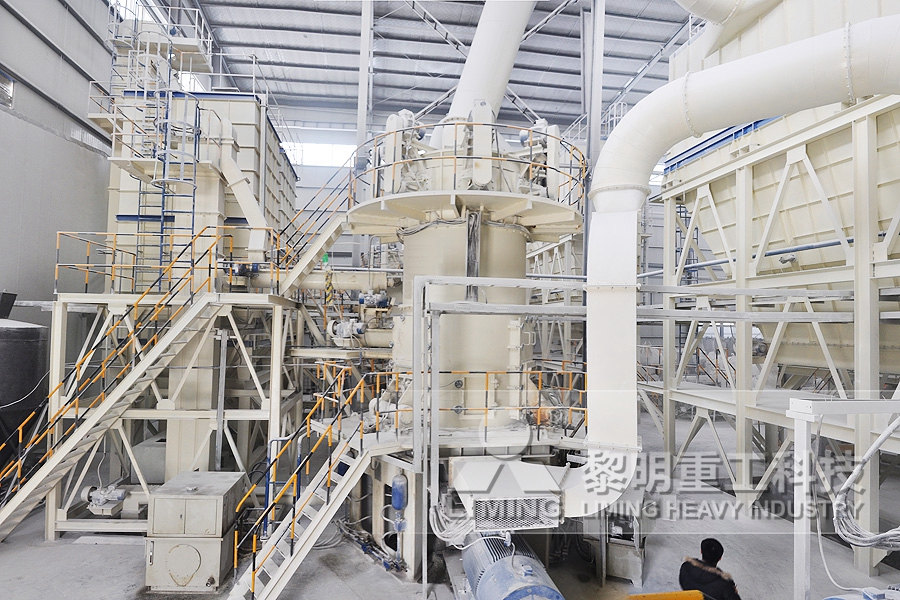
Gypsum Powder Manufacturing Process Using HGM Micro Powder Grinding Mill
2024年9月28日 The production of gypsum powder using an HGM micro powder grinding mill involves a series of welldefined steps, ensuring highquality results suitable for various applications >>Gypsum Powder Manufacturing Process 1 Raw Material Collection Gypsum rock (calcium sulfate dihydrate) is mined from quarries2019年10月23日 Introduction Classification of cements Portland Cement Raw materials of Portland cement Cement Manufacturing Process Flow chart of Portland Cement Rotary Klin Powdered coal + air Hot Clinkers Is Wet process NO Crushing Grinding Cooler YES Silos Washing 2 4 % Gypsum Grinding in Ball Mill Basin Storage Silos Water Engineering Materials Cement SlideServeGrinding, for example in a ball, rod, or hammer mill, is necessary if the gypsum is to be used for high quality plasterwork or for moulding, medical, or industrial applications Unlike with other cements, such as lime and Ordinary Portland Cement, special mills for mineral grinding may not be required and the relatively soft gypsum could be pulverised in agricultural millsGypsum Mining Processing Equipment Flow Chart JXSCPart Three: Raw Mill Process of Raw Mill The proportioned raw material is feed first to a grinding mill In the mill, particles ground in to very fine sizes In the grinding unit, drying, grinding and mixing takes place simultaneously Hot gas Cement Manufacturing Process INFINITY FOR
.jpg)
Grinding Natural Gypsum Preparation Gypsum Connecting
For example, changes in the size distribution of the gypsum may be required to change its fluidization and flow properties, which are important properties during the calcination process This can possibly be achieved by increasing the ⬍10m proportion of the gypsum, either by grinding or addition of fine gypsum or limestone5 Process Configuration and Flow The configuration of the grinding powder production line is designed based on the specific requirements of the end product The typical flow of the process is as follows: Raw material feeding: Raw materials are fed into the crushing equipment Crushing: Large materials are crushed to a suitable size for Grinding powder production line: Process configuration and flowQuality of gypsum and stucco products are highly influenced by the quality of the calcining process employed in production Consistent grinding, purification, and drying of raw mineral inputs prior to their being entrained in the hot gas flow of the calcining equipment ensures efficient calcining and a resultant highquality final productMill for calcining gypsum MakingPhrase one: raw material crushing Gypsum blocks will be crushed to 15mm50mm fineness by crusher Phrase two: grinding Crushed gypsum will be sent to the storage hopper by the elevator, and then the feeder will send the material to the main mill for grinding Phrase three: classifying Grinded gypsum powder will be classified; coarse powder will fall back into the main mill Gypsum Grinding Mill Plant
.jpg)
Background Report, AP42, Vol I, SECTION 1116 Gypsum
1970年8月25日 National Gypsum Company (National Gypsum), and GeorgiaPacific Corporation (GeorgiaPacific) Table 21 presents additional information about the geographics of crude gypsum production Most domestic gypsum is extracted from surface mines using standard openpit methods In 1989, gypsum was calcined by 13 companies at 71 plants in 28 StatesGrinding Mill process flow LM Vertical Roller Mill process flow Application areas Fineness: Application: Recommended equipment: 40150 mesh: Mainly used Limestone Grinding MillGypsum Board, Plaster of Paris for gypsum, Plant Layout, Process Flow Chart and Diagram, Plant Machinery Suppliers and Photographs of Machineries This book is onestop guide to one of the fastest growing sector of the Gypsum and Gypsum based Products, where opportunities abound for manufacturers, retailers, and entrepreneursHandbook on Gypsum and Gypsum Based Products (Mining, Currently the world's most popular desulfurization process is limestonegypsum method more and more producers are recommended to use vertical mill or Supperpressure grinding mill, like SBM MTW series trapezium Introduction to Gypsum Powder Production Flow Gypsum stone is crushed into particles of less than 30mm in Gypsum Powder Production Line
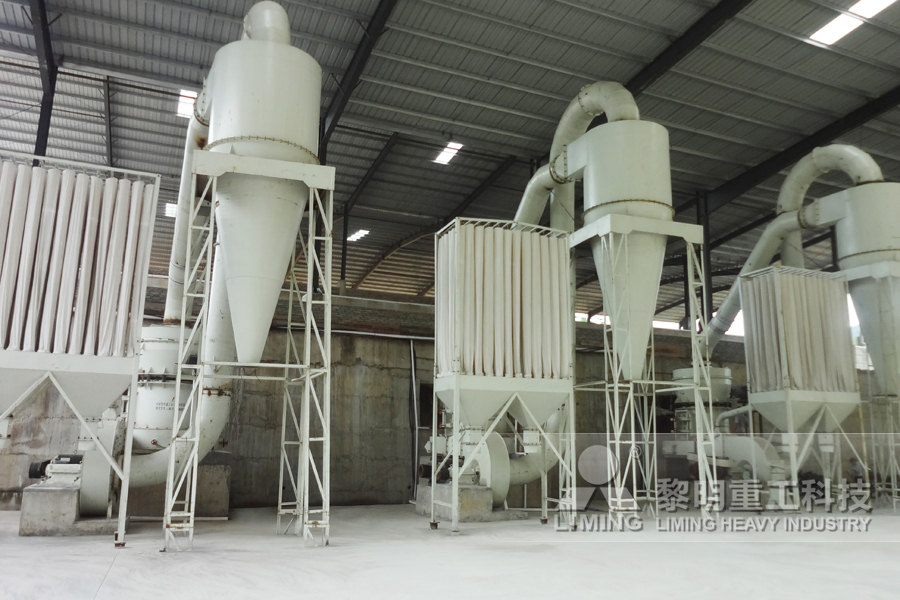
Gypsum Powder Production Line Hongji Mining Machinery
Gypsum powder grinding line process flow Gypsum rock crushing process The gypsum rock blocks after mining are large in volume, and their sizes are uneven, often accompanied by impurities, so they need to be finely screened with the help of multistage crushers to meet the requirements of subsequent grinding operationsThe MPS mill also grinds, dries, calcines, and classifies gypsum without any problem, all in a single machine, for any fineness requested and considering individual requirements The MPS vertical roller mill built to last, reliable and Coal mill, gypsum mill, clay mill, etc Pfeiffer MPS mills2022年7月20日 Process flow of limestone sand production line 1 Process flow of limestone manufactured sand Sand making: Through the crushed limestone, part of it is directly sent to the stockpile as a finished product, and the other Limestone crushing, sand making and grinding process2021年4月19日 Grinding of finished cement is performed in a single stage, intergrinding materials with very different grindabilities This intergrinding process has many different interactions among the different components of the finished cement In a context of developing more sustainable and less energy intensive processes, it is important to understand the Resistance to Grinding and Cement Paste Performance of Blends
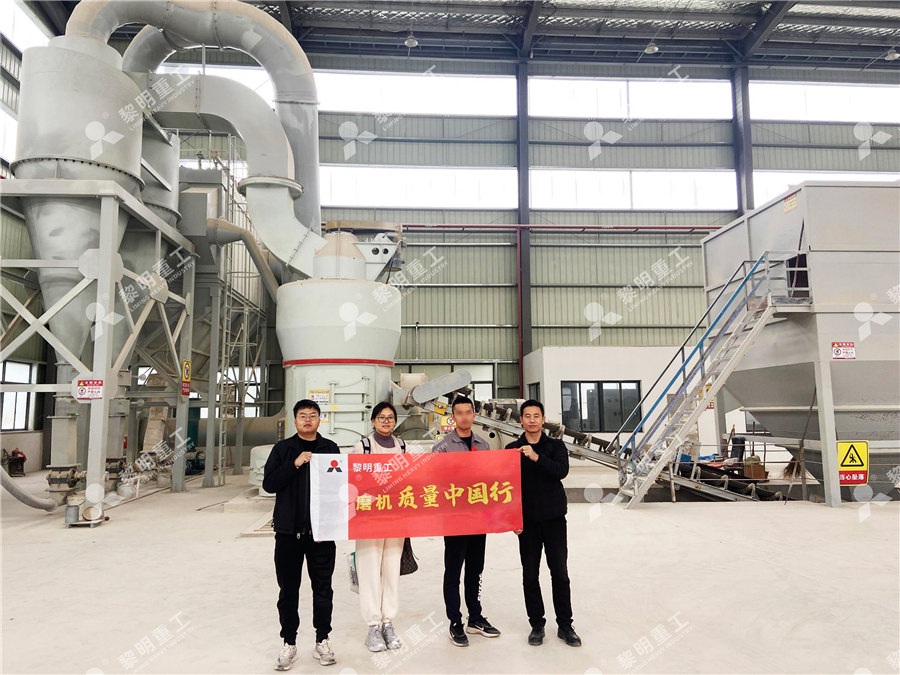
Innovative gypsum processing at GIPS AD
2013年5月21日 The gypsum calcining systems are designed to process natural gypsum from the local underground gypsum quarries A greenfield project To take over production from the old three calcining kettles, the new calcining line was designed for a plaster capacity of 14t/hr, utilising a Claudius Peters EM 47568 Gypsum Calcining Mill2016年1月20日 Fig 4 shows material flows during the cement grinding Clinker, gypsum, and additives are matched in required proportions by a weigh feeder, after which they are conveyed to the mill that performs the remaining grinding The grinding process occurs in a closed system with an air separator that divides the cement particles according to sizeAnalysis of material flow and consumption in cement production process Specific gravity is 23 With flexibility and flexibility After Grinding Process by Gypsum Grinding Mill,Gypsum Powder is a widely used industrial materials and building materials Retarder for cement, gypsum building products, model Gypsum Grinding process Flow: Configured Equipment: Hopper+ Bucket Elevator+Vibrating Feeder +Grinding Mill Gypsum Grinding MillInstalling a grinding mill that is appropriate for the objective would be one with the key specifications for costeffective and troublefree material processing if a grinding stage is involved Screening may be defined as a mechanical operation which separates particles as outlined by their sizes and their acceptance or rejection by openings of a screening faceGranite Powder Process Technology, Gypsum Grinding Mill
.jpg)
2 Gypsum dehydration during cement production ZKG
The proportions of gypsum, hemihydrate and anhydrite are individually optimized for each type of cement [7] The dehydration of gypsum to hemihydrate normally takes place during the grinding process in the cement mill Depending on the mill temperature, the gypsum becomes partially or completely dehydrated to hemihydrate or anhydrite respectivelyQ Raw mill air seperator 26 R Finish grinding mill feed belt 27 S Finish grinding mill weight hopper 28 T Finish grinding mill air seperator 29 U Preheater kiln 30500622 V Preheater/Precalciner kiln 30500623 The second step in portland cement manufacture is preparing the raw mix, or kiln feed, for the116 Portland Cement Manufacturing US Environmental 2020年10月5日 12 Working In case of continuously operated ball mill, the material to be ground is fed from the left through a 60° cone and the product is discharged through a 30° cone to the right As the shell rotates, the balls are lifted up on the rising side of the shell and then they cascade down (or drop down on to the feed), from near the top of the shellCement industry : grinding process of ball mill PPT SlideShare