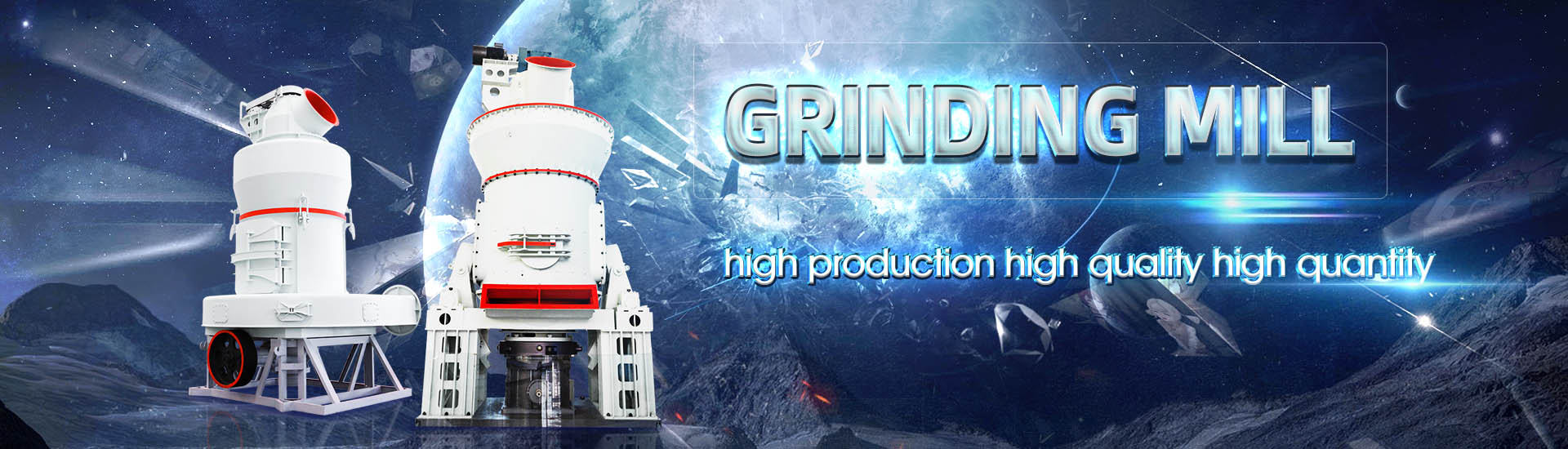
Mine vsi ore grinding mill
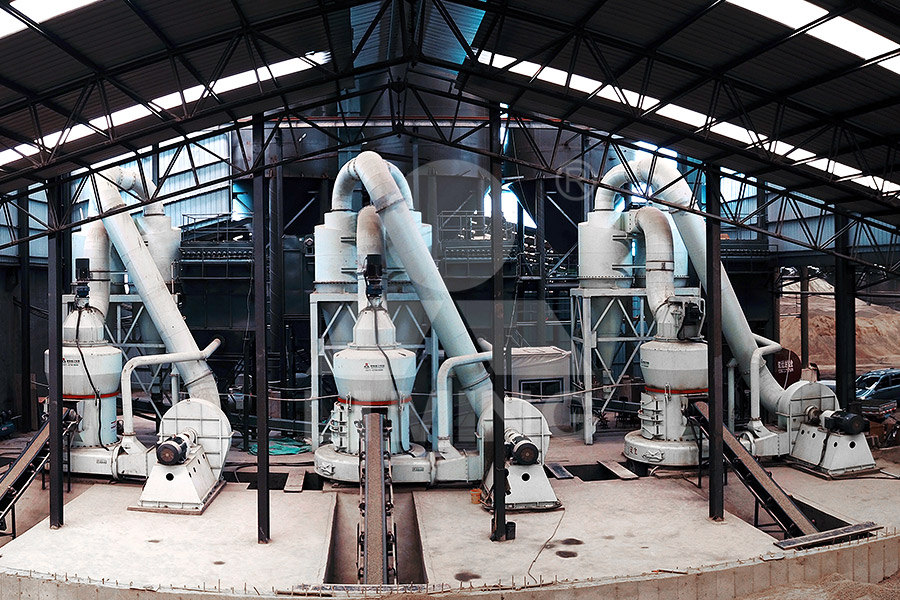
Understanding the SAG Mill in Copper Ore Mining
A SAG mill, also known as a semiautogenous grinding mill, is one of the essential equipment used in copper ore mining It plays a vital role in reducing large chunks of rock into smaller pieces to facilitate easier processing2024年1月10日 Ball and rod mills are widely used grinding equipment in mineral processing plants The two are similar in appearance and grinding principle, but there are differences in structure, performance, use, etc This article will Ball Mill VS Rod Mill: Difference Selection JXSC 2008年8月1日 An alternative energy measure was introduced to assess the value of feeding a finer product to a grinding mill This measure suggests that a VSI can save 2–14% of the Energy considerations in compressive and impact crushing of rock2020年12月1日 Crushing behaviour in a VSI involves multiple mechanisms of impact breakage Particle scale modelling of comminution processes can provide significant insight into the flow Advanced comminution modelling: Part 1 – Crushers
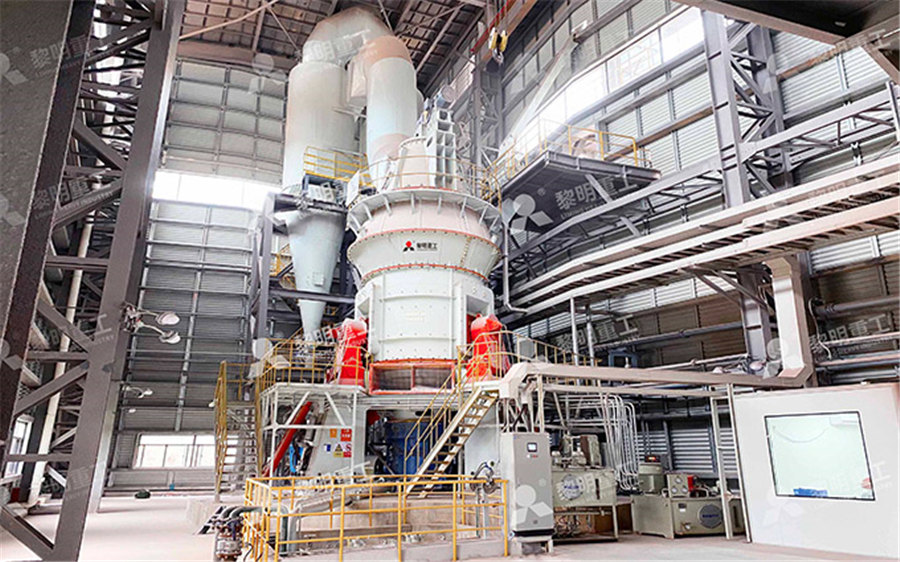
Grinding Metso
Customized grinding mill parts including heads, shells, trunnions and liners, main bearings, gears and pinions, and more! Metallic, PolyMet™, Megaliner™, Rubber and Orebed™ mill liners for A VSI mill throws rock or ore particles against a wear plate by slinging them from a spinning center that rotates on a vertical shaft This type of mill uses the same principle as a VSI crusherMill (grinding) Wikipedia2023年7月20日 Moist grinding, a special grinding method, is used to prepare pellets for smelting According to the grinding medium features, ore grinding is mainly classified into ball grinding Ore Grinding SpringerLinkGE provides flexible and innovative mill solutions across all types of grinding, from single and dual pinion AG, SAG and ball to hPGr This helps you to meet highcapacity demands with less Products Solutions for the Mining Industry GE Vernova
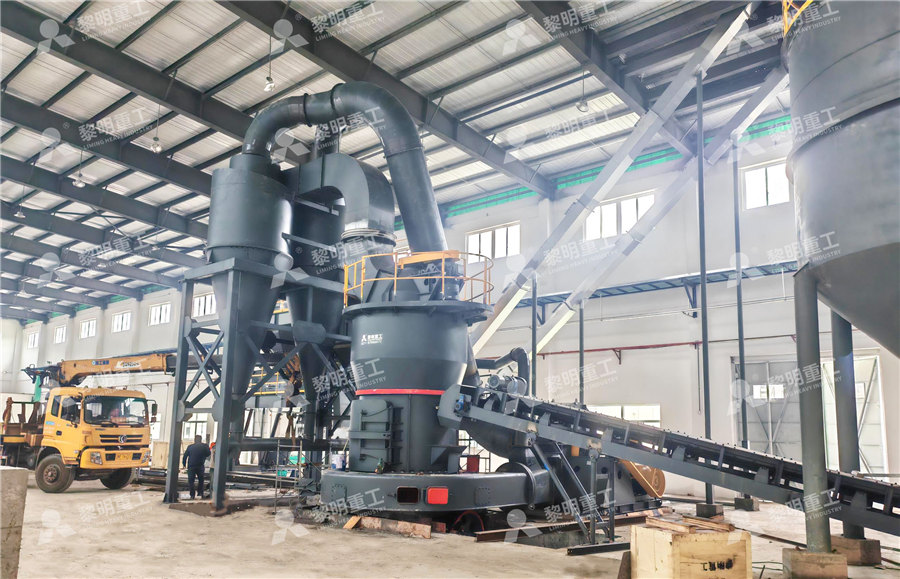
Analysis and validation of a runofmine ore grinding mill circuit
2013年4月1日 A simple and novel nonlinear model of a runofmine ore grinding mill circuit, developed for process control and estimation purposes, is validated The model makes use of 2017年10月26日 The following are factors that have been investigated and applied in conventional ball milling in order to maximize grinding efficiency: a) Mill Geometry and Speed – Bond (1954) observed grinding efficiency to be a Factors Affecting Ball Mill Grinding Efficiency2015年8月6日 Rubber liners absorb the impact of the larger grinding media and thus protecting – the mill structure and prolonging it’s life Weight: Rubber weighs about 15% of an equivalent volume of steel This means that a rubber liner Grinding Mill Liners 911MetallurgistCM Mining Machinery specializes in the manufacture of crushers, grinding mill, mobile crushing plant, vsi and other equipment, and provides services such as production configuration, selection, and price analysis of these different types of equipmentCrusher,Mobile Crusher,Grinding Mill,Vsi Crusher Manufacturer
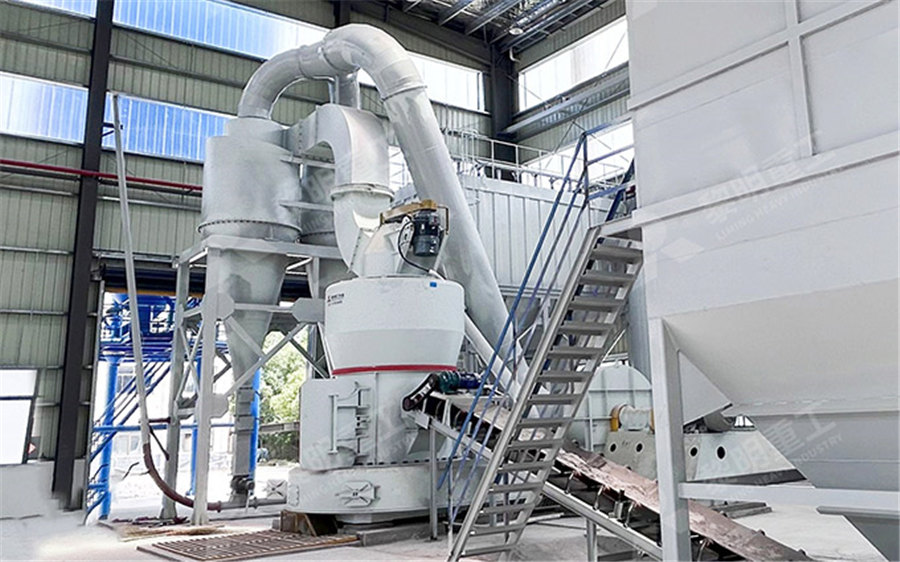
Iron Ore Processing: From Extraction to Manufacturing
2024年4月26日 The choice of grinding mill depends on factors such as the desired product size, capacity requirements, and energy consumption b Autogenous and SemiAutogenous Mills: In some cases, autogenous (AG) and semiautogenous (SAG) mills are used for grinding These mills utilize the ore itself as the grinding media, reducing the need for additional One reason is the dry inbed grinding principle Results of extensive test works with two types of magnetite iron ores in a Loesche VRM are presented here Within these test works, mill parameters like grinding pressure, separator speed and dam ring height were varied, following a factorial design of the experimentsResearch of iron ore grinding in a verticalrollermillCrushing, a form of comminution, one of the unit operations of mineral processing Mineral processing is the process of separating commercially valuable minerals from their ores in the field of extractive metallurgy [1] Depending on the processes used in each instance, it is often referred to as ore dressing or ore milling Beneficiation is any process that improves (benefits) the Mineral processing Wikipedia2022年9月1日 Waste rocks occupy space from ore in the grinding mill, thus lowering the mill’s ore grinding capacity and mineral concentrator’s concentrate production Moreover, in most cases, waste rock is harder and, consequently, more difficult to grind than the ore which is often found in the weaker areas of the rockTowards waterless operations from mine to mill ScienceDirect
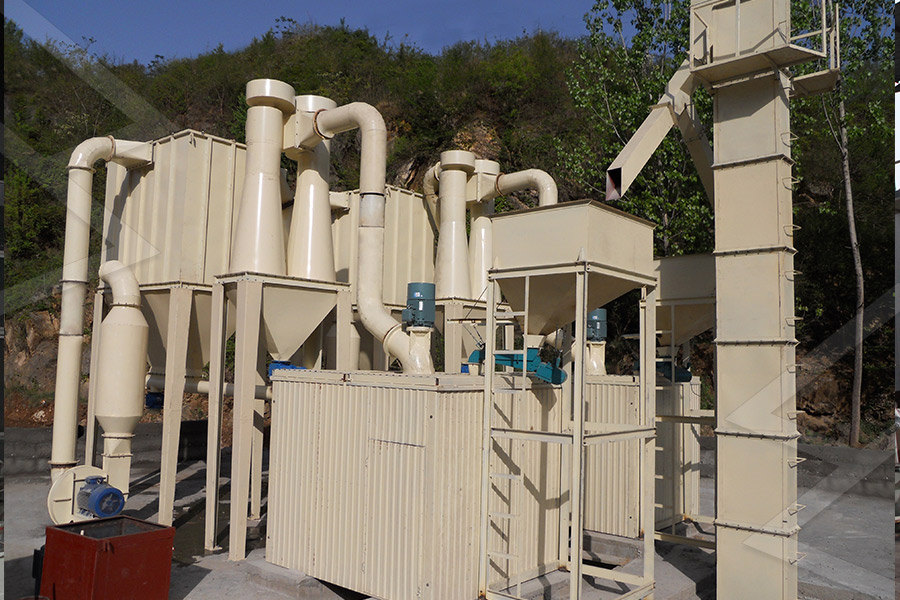
Understanding the operation of grinding mills in the mining and
1 Grindability: The grindability of the ore affects the efficiency of the grinding mill Harder ores require more energy and longer grinding times, which can impact the mill's performance and operational costs 2 Media andliner Wear: The condition of the grinding media and liners affects the mill's efficiency2020年6月3日 Grinding mills are some of the most important equipment in mines, processing over a few thousand tons of ore every hour It is not uncommon to see these days that a single line of a grinding circuit consisting of a Semi Autogenous Grinding (SAG) mill followed typically by two ball mills generating over USD $1 million of revenues per dayHow grinding mill design changed over the last 30 yearsUnderstanding Mine to Mill is presented in five parts Part A – Setting the Scene provides some definitions of Mine to Mill (M2M) and the historical background A chronology of Mine to Mill developments is followed by brief descriptions of the very wide range of Mine to Mill applications which have been implemented over the last 15 yearsUNDErsTaNDINg MINE TO MILL 911 Metallurgist2016年7月14日 HPGR test results published by Grier (1992) on gold ores from the Mt Todd project showed significant energy savings for a HPGR/Ball Mill circuit as compared to a SAG/Ball Mill plant By adding a Polycom high HPGR 911Metallurgist
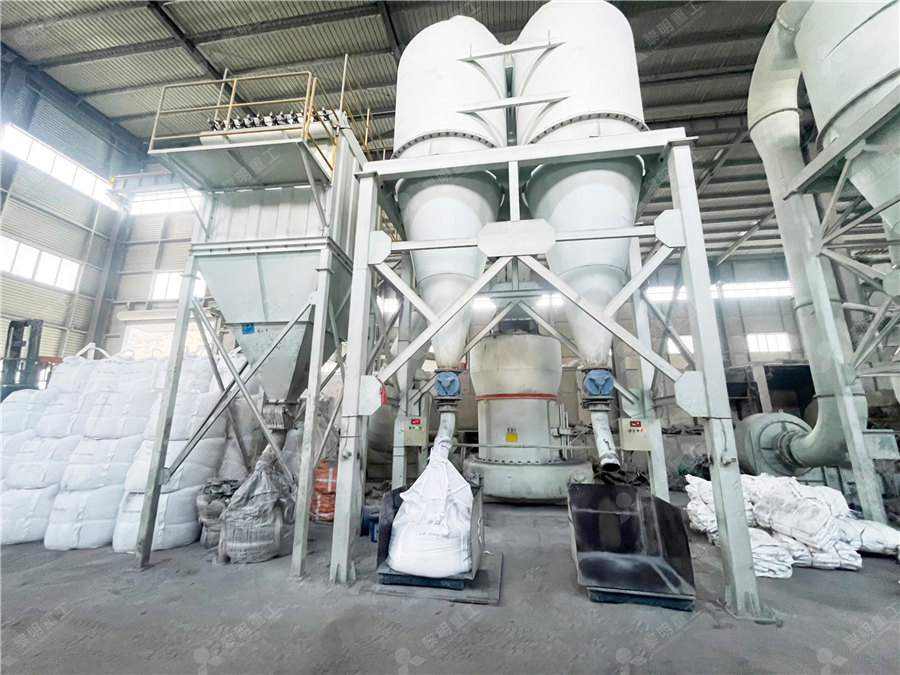
Mine operating costs and the potential impacts of energy and grinding
2014年2月1日 Mines typically produce more ore during these stages than the mill is able to process, in order to maintain a constant stockpile for the mill in the event of disruptions in the mine operations The end of mine pattern, where relative Milling costs increase and relative Mining costs decrease, may be explained in light of the phaseout of mining operationsSmall ore mine ₡6,500: Ore grinding mill ₡20,000: Sand storage ₡6,000: Don’t forget to factor in the money for building roads, water pipes, and power lines to supply the area Manufacturing metals requires the ore grinding mill, which Complete Ore Industry Area Guide for Cities: Skylines2013年12月18日 Fine grinding, to P80 sizes as low as 7 μm, is becoming increasingly important as mines treat ores with smaller liberation sizes This grinding is typically done using stirred mills such as the Isamill or Stirred Media Detritor While fine grinding consumes less energy than primary grinding, it can still account for a substantial part of a mill’s energy budget Overall Energy Use of Fine Grinding in Mineral Processing2020年1月16日 This could be achieved through closer monitoring of the primary crusher performance and proper control of the ratios for the SAG mill feeders drawing the ore from the stockpile The ball mill (PDF) Optimization and performance of grinding circuits: the
.jpg)
Grinding Media in Ball Mills for Mineral Processing
2023年11月24日 Factors that influence the grinding efficiency include mill design, liner design, mill speed, mineralogical composition of the ore, charge ratio, and grinding media properties The grinding efficiency of a ball mill is determined by the product size distribution, energy consumption, and the grinding costs13 RunOfMine Material and Minerals Generally, mineral processing begins when an ore is delivered from a mine, to a processing facility At this point, the ore is called runofmine material because there has been no treatment performed on it There are three primary types of runofmine materials: Runofmine consisting of useful materialsIntroduction to Mineral Processing or BeneficiationGold Mining Wet Pan Mill used for the material recrushing after the first crushing The capacity is 150 t/h The maximum feed size is 30 mm and the output size is 007406 mm wet pan mill is particularly suitable for grinding rock gold ore which cSinogomine Industrial Technology Co,LtdGold Mining Wet Pan MillKeywords: Mine call factor, minetomill integration, fragmentation, ore loss, dilution Introduction The mining of high gold grades is obviously very beneficial for the economic viability of an operation, but optimum recovery of the product is required to maximize profits (Chapman and Bindoff, 2010, p 13)Monitoring ore loss and dilution for minetomill integration in
.jpg)
Closed Circuit Grinding VS Open Circuit Grinding
2016年10月12日 An increase in the diameter of a mill gives greater economy in two ways : In the first place, the balls do more effective work in a large than in a small mill, because, falling from a greater height, they shatter the pieces of ore with greater force ; in the second place, the ratio of the deadweight of the mill to the weight of the ball charge decreases as the diameter increases 2017年7月3日 Batch Ball Mill Grinding Capacities and efficiencies in wet and dry ball milling at different speeds and ore charges have been discussed in the foregoing pages The results are summarized in table 16, which shows that in both capacity and efficiency grinding was at its best with small ore charges and high speedWet Grinding VS Dry Ball Mill Grinding 911MetallurgistWe have been designing and manufacturing Semi Autogenous Mill (SAG Mill) and Autogenous Mill (AG Mill) under the FullerTraylor brand since the early 1980s Semiautogenous grinding uses a minimal ball charge in the range of 615% while autogenous grinding uses ore onlySAG mills and AG mills – efficient grinding – FLS2016年6月3日 The principal method of grinding in a Tower mill is attrition (scrubbing of particles off material being ground), with the possibility of some shearing and 911 Metallurgist is a trusted resource for practical insights, Tower Mill Operating Work Index 911Metallurgist
.jpg)
Flexible, efficient grinding systems – FLS
Depending on the application, ore grinding can take place in a ball mill, SAG or AG mill, towe r mill, rod mill or HPGR Empowering the future of mining FLS is a leading, full flowsheet minerals processing supplier to the global mining industry2018年8月17日 Extreme temperatures, impact velocity, mill load, grinding media, ore types, and applications are some of the factors to be considered while installing new linersGrinding Mills — Types, Working Principle ApplicationsAutogenous Grinding (AG) Mill Wet or dry; Primary, coarse grinding (up to 400 mm feed size) Grinding media is grinding feed; AG/SAG mills are normally used to grind runoffmine ore or primary crusher product Wet grinding in an AG/SAG mill is accomplished in a AMIT 135: Lesson 6 Grinding Circuit – Mining Mill Operator 2017年2月20日 All Grinding Mill Ball Mill Manufacturers understand the object of the grinding process is a mechanical reduction in size of crushable material When choosing primary autogenous grinding, run of mine ore up to 200300 mm in size is fed to the mill When using a crushing step before the grinding, Grinding Mill Design Ball Mill Manufacturer 911Metallurgist
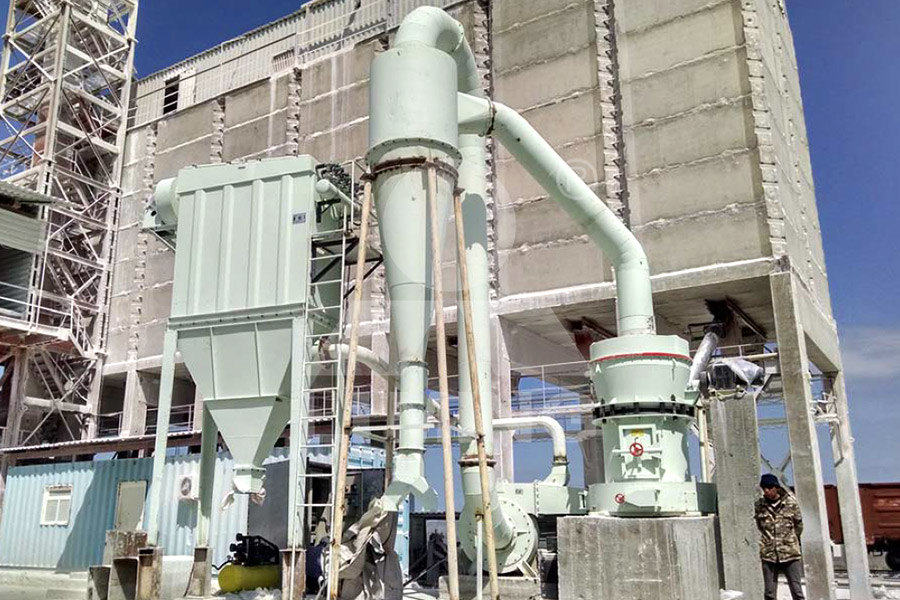
Autogenous Mill SpringerLink
2023年6月7日 The maximum particle size of the lump ore fed into autogenous mill is 300–350 mm In the grinding mill, the ore blocks sized >100 mm function as grinding medium The ore particles smaller than 80 mm but bigger than 20 mm have poor grindability and they cannot be easily ground by big lump ore, so such material is usually called “hardto 2023年4月23日 grinding media in a grinding mill with about 2630 wt% chrome by Chen et al [37] using a phosphate ore in a modified ball laboratory ball mill whose electrochemical potential could be controlled(PDF) Grinding Media in Ball MillsA Review ResearchGate2019年4月16日 Conference: Applying a Successful Technology from the Cement Industry: Advantages of Grinding Ore in a VerticalRollerMill; At: Antalya, Türkey(PDF) LEARNING FROM OTHER INDUSTRIES; WHY THE VRM2017年10月26日 The following are factors that have been investigated and applied in conventional ball milling in order to maximize grinding efficiency: a) Mill Geometry and Speed – Bond (1954) observed grinding efficiency to be a Factors Affecting Ball Mill Grinding Efficiency
.jpg)
Grinding Mill Liners 911Metallurgist
2015年8月6日 Rubber liners absorb the impact of the larger grinding media and thus protecting – the mill structure and prolonging it’s life Weight: Rubber weighs about 15% of an equivalent volume of steel This means that a rubber liner CM Mining Machinery specializes in the manufacture of crushers, grinding mill, mobile crushing plant, vsi and other equipment, and provides services such as production configuration, selection, and price analysis of these different types of equipmentCrusher,Mobile Crusher,Grinding Mill,Vsi Crusher Manufacturer2024年4月26日 The choice of grinding mill depends on factors such as the desired product size, capacity requirements, and energy consumption b Autogenous and SemiAutogenous Mills: In some cases, autogenous (AG) and semiautogenous (SAG) mills are used for grinding These mills utilize the ore itself as the grinding media, reducing the need for additional Iron Ore Processing: From Extraction to ManufacturingOne reason is the dry inbed grinding principle Results of extensive test works with two types of magnetite iron ores in a Loesche VRM are presented here Within these test works, mill parameters like grinding pressure, separator speed and dam ring height were varied, following a factorial design of the experimentsResearch of iron ore grinding in a verticalrollermill
.jpg)
Mineral processing Wikipedia
Crushing, a form of comminution, one of the unit operations of mineral processing Mineral processing is the process of separating commercially valuable minerals from their ores in the field of extractive metallurgy [1] Depending on the processes used in each instance, it is often referred to as ore dressing or ore milling Beneficiation is any process that improves (benefits) the 2022年9月1日 Waste rocks occupy space from ore in the grinding mill, thus lowering the mill’s ore grinding capacity and mineral concentrator’s concentrate production Moreover, in most cases, waste rock is harder and, consequently, more difficult to grind than the ore which is often found in the weaker areas of the rockTowards waterless operations from mine to mill ScienceDirect1 Grindability: The grindability of the ore affects the efficiency of the grinding mill Harder ores require more energy and longer grinding times, which can impact the mill's performance and operational costs 2 Media andliner Wear: The condition of the grinding media and liners affects the mill's efficiencyUnderstanding the operation of grinding mills in the mining and 2020年6月3日 Grinding mills are some of the most important equipment in mines, processing over a few thousand tons of ore every hour It is not uncommon to see these days that a single line of a grinding circuit consisting of a Semi Autogenous Grinding (SAG) mill followed typically by two ball mills generating over USD $1 million of revenues per dayHow grinding mill design changed over the last 30 years
.jpg)
UNDErsTaNDINg MINE TO MILL 911 Metallurgist
Understanding Mine to Mill is presented in five parts Part A – Setting the Scene provides some definitions of Mine to Mill (M2M) and the historical background A chronology of Mine to Mill developments is followed by brief descriptions of the very wide range of Mine to Mill applications which have been implemented over the last 15 years