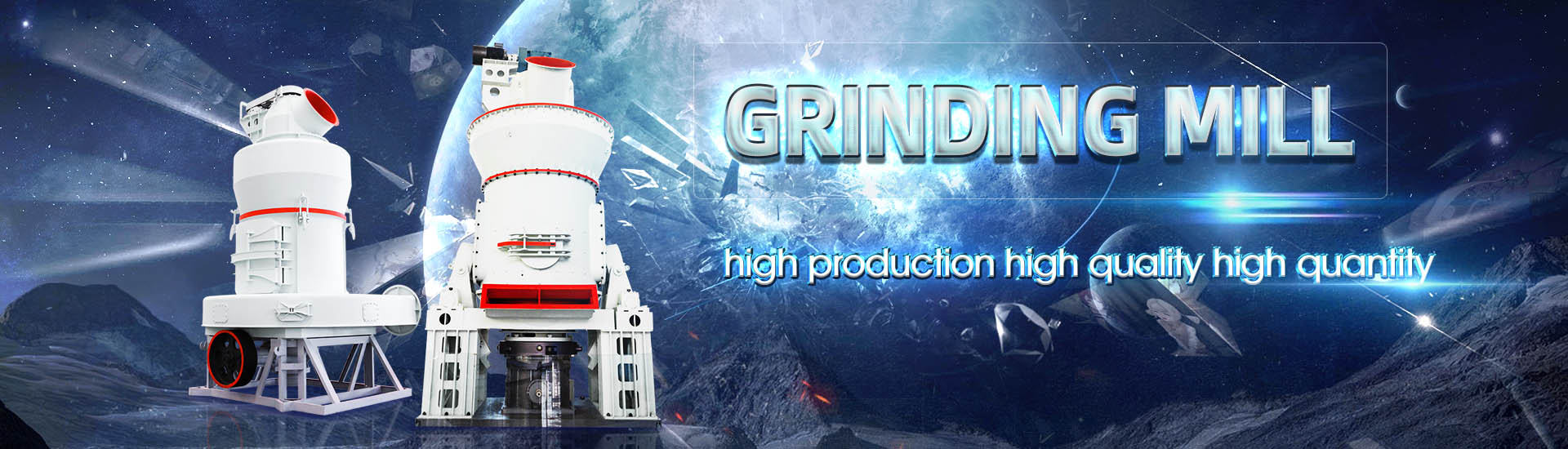
3.2x13m cement mill V selection and production
.jpg)
A decision support tool for cement industry to select
2020年3月1日 In this study, an integrated 3phase model is presented to address these shortcomings and assist the plant managers to select and invest in the most suitable projects The Cement Plant Operations Handbook is a concise, practical guide to cement manufacturing and is the standard reference used by plant operations personnel worldwide Providing a The Cement Plant Operations Handbook International Cement In cement plants, proper specification and supply of AC induction motors is critical to project schedules and providing efficient production This paper focuses on the selection of AC Selection of AC Induction Motors for Cement Plant ApplicationsCement is paramount for economic development and poverty reduction in emerging markets Along with aggregates and water, cement is the key ingredient in the production of concrete, IMPROVING THERMAL AND ELECTRIC ENERGY EFFICIENCY AT
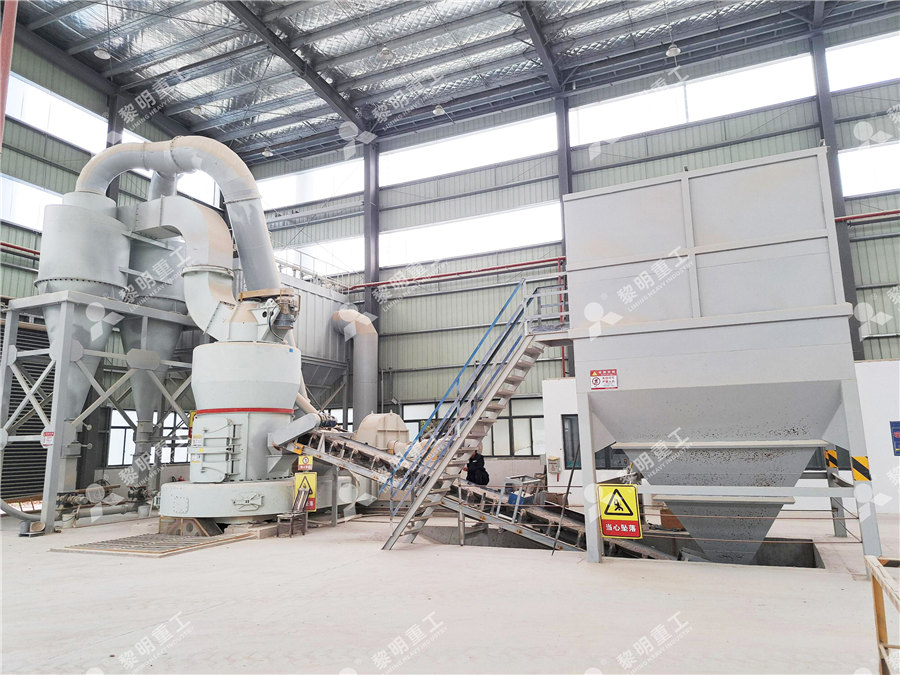
The Decision Algorithm of Cement Mill Operation Index Based
2023年1月25日 The optimization of the decision model of cement mill operation index based on the improved differential evolutionary algorithm is the process of making decisions on the mill systems with pre‑grinders (HPGR, roller presses, or VRM pre‑grinders) to increase cement production from about 30% to 100%, depending on the system installed As there are so many Thomas Holzinger, Holzinger Consulting, grinding system The cement production process 1 The Quarry: The cement production process begins with the extraction of limestone and clay from the quarry 2 Crusher and PreBlending: The material is A practical guide to improving cement manufacturing processes 2020年3月1日 Mills are designed depending on users' requirements, eg, the fineness of ground product, the production (or feed) rate and the environmental or spatial constraints for A scaleup and design basis of continuous tube mills in cement
.jpg)
Process technology for efficient and sustainable cement production
2015年12月1日 Over the years technology in the cement industry has been further developed with a growing focus on sustainable, cost and energyefficient production While significant Optimization of the Cement Ball Mill Operation Optimization addresses the grinding process, maintenance and product quality The objective is to achieve a more efficient operation and OPTIMIZATION OF CEMENT GRINDING OPERATION IN BALL MILLSPDF On Apr 1, 2017, Elita Amrina and others published Minimizing waste using lean manufacturing: A case in cement production Find, read and cite all the research you need on ResearchGateMinimizing waste using lean manufacturing: A case in 2023年7月10日 Cement manufacturing is a significant industrial activity that plays a vital role in the construction sector However, the process of cement production is associated with various environmental Cement Manufacturing Process and Its Environmental
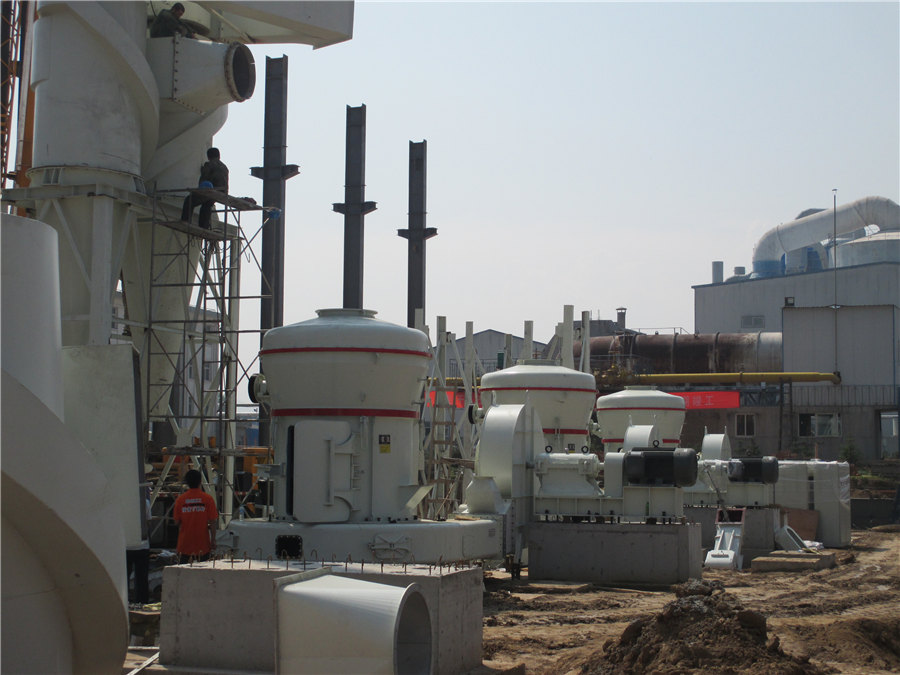
Heat Integration in a Cement Production
2018年10月10日 Heat transfer in cement production with raw mill considering the minimum temperature difference 1Hot composite curve; 2cold composite curve, 3heat exchangers (developed after [30])Chemical process industries are running under severe constraints, and it is essential to maintain the endproduct quality under disturbances Maintaining the product quality in the cement grinding process in the presence of clinker heterogeneity is a challenging task The model predictive controller (MPC) poses a viable solution to handle the variability This paper addresses the Predictive Controller Design for a Cement Ball Mill Grinding 2023年1月25日 Abstract An improved differential evolutionary cement mill operation index decision algorithm based on constraint control and selection strategy is proposed to address the problem that the operation index is usually decided by manual experience in the cement mill operation process, which causes unqualified cement specific surface area and excessive The Decision Algorithm of Cement Mill Operation Index Based2024年6月1日 Cement production involves the combustion of fossil fuels and the calcination of limestone, leading to the release of large amounts of carbon dioxide (CO 2) Simultaneously, optimising aggregate selection, a substantial portion of concrete volume, involves choosing materials with lower embodied carbonDecarbonising cement and concrete production: Strategies,
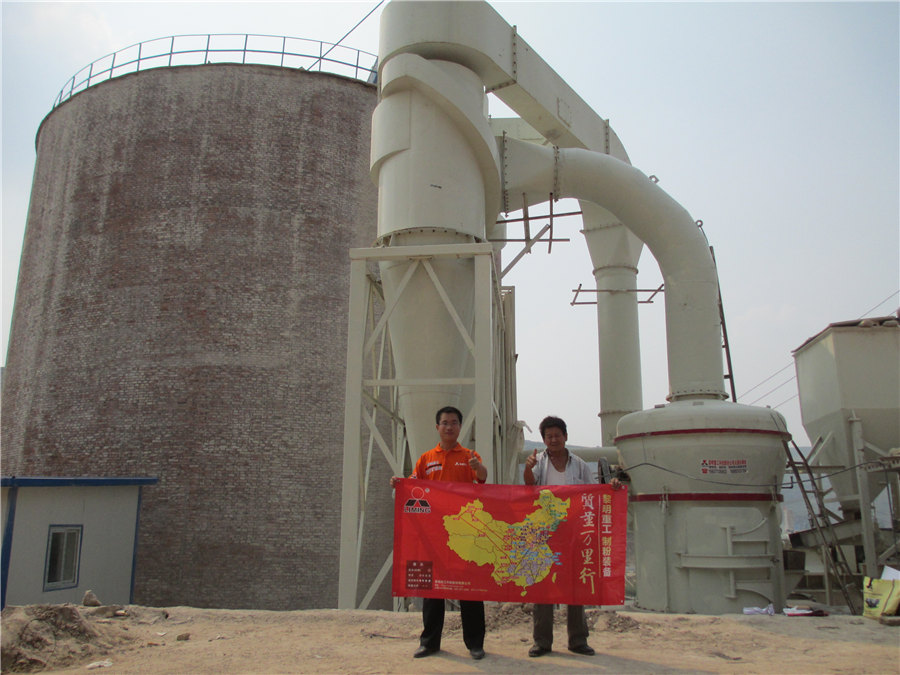
Process technology for efficient and sustainable cement production
2015年12月1日 With 460 new mill orders in 2012, China's local market is not only much bigger than the rest of the world's, but in addition, a share of over 60% of the cement is produced on grinding systems with HPGRs [51], [1] The technology of cement production will without doubt be developed further in future years, as it has in the past2022年5月15日 Cement production in China reached 233 billion tons in 2018, accounting for more than half of the global production (China Building Materials Federation, 2019)In 2019, over 95% of all cement clinker was produced from cement plants using new dry clinker production process (Ghazvini et al, 2020, Cai et al, 2020, Li et al, 2019)In the cement plants using this Mercury emission characteristics and mechanism in the raw mill 2015年8月1日 The results show that approximately 248t, 469t, and 341t of materials are required to produce a ton of the product in raw material preparation, clinker production, and cement grinding stages (PDF) Analysis of material flow and consumption in cement production 2020年1月1日 The demand for cement, which is one of the key components of concrete, is high in Ethiopia, but it is the most expensive and environmentally unfriendly construction materialAssessment on Cement Production Practice and Potential Cement
.jpg)
Cement mill Wikipedia
Portland clinker is the main constituent of most cements In Portland cement, a little calcium sulfate (typically 310%) is added in order to retard the hydration of tricalcium aluminateThe calcium sulfate may consist of natural gypsum, anhydrite, or synthetic wastes such as fluegas desulfurization gypsum In addition, up to 5% calcium carbonate and up to 1% of other 2018年4月4日 Cement Types, Composition, Uses and Advantages of Nanocement, Environmental Impact on Cement Production, and Possible SolutionsCement Types, Composition, Uses and Advantages Mill performance test Steps 1 Recording of related operational data 2 Air flow measurement 3 Crash stop and visual inspection in mill 4 Sampling in mill 5 Evaluation of test 1 Recording of related operational dataTube Mill Feed Cement Separator Ball Mill Optimization2020年11月5日 As you all know, the process of a cement manufacturing plant can be divided into several steps, including crushing, raw milling, clinker calcining, cement milling (or cement grinding), packing and etc In the complete cement production line, the cement mill process plays a very important role The design of cement milling and cement mill process will produce a 3 Necessary Cement Milling Comparison Ball Mill, Vertical Roller Mill
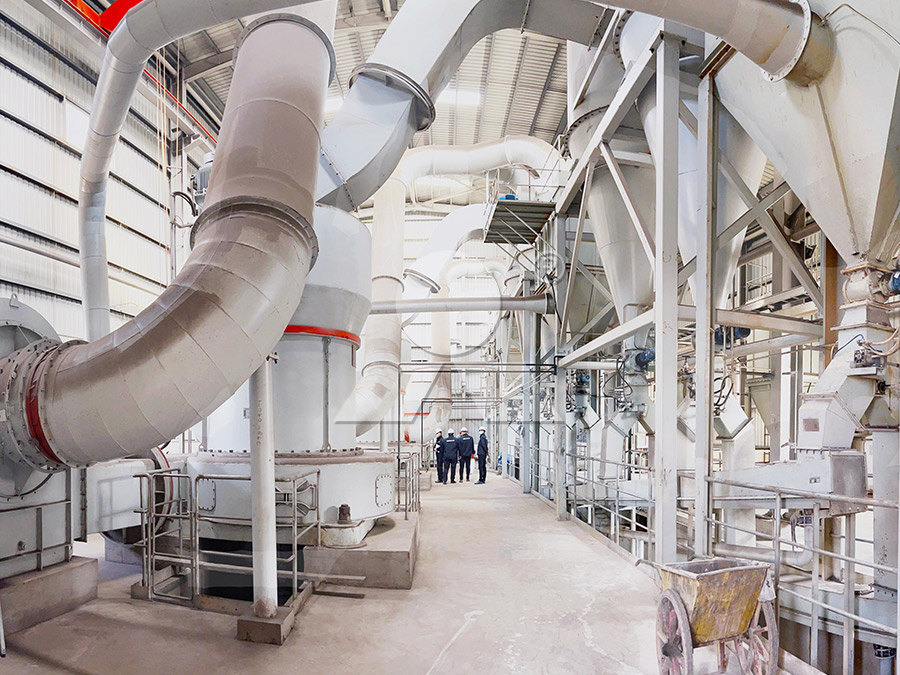
(PDF) Cement Quality Control By Using Modern Radiation
2019年3月1日 An essential part of modern quality management system in cement production is stateoftheart radiation measurement technologies based on methods of neutron activation, Xray fluorescence and X PDF On May 13, 2021, Elshan Moradkhani and others published Intelligent Modeling of Cement Plant Mill Unit Using Artificial Neural Networks and Real Data Find, read and cite all the research Intelligent Modeling of Cement Plant Mill Unit Using Artificial 2021年3月1日 put while in Malaysia, cement production reached up to 1866 thousand tonnes by July 2020 as shown in Table 1 [12] As the demand for cement supply is continually growing, thisEnvironmental impact of cement production and Solutions: A 2024年3月1日 We’ve found that our cement production articles are some of the highest viewed content on our blog site So, we’ve put together a list of our blog articles related to the cement production process and analysis Here are the top 15 of our most read cement articles, in no particular order:Everything about Cement Production Thermo Fisher Scientific
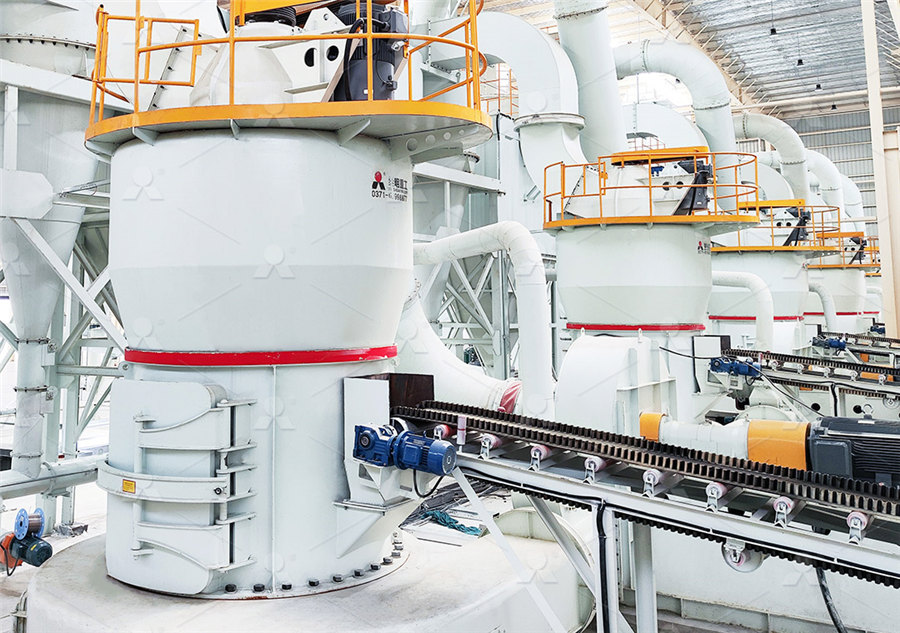
A Survey and Analysis on Electricity Consumption of Raw Material Mill
2021年1月22日 In the whole process of cement production, the electricity consumption of a raw material mill accounts for about 24% of the total Based on the statistics of the electricity consumption of the raw 2019年4月14日 The current world consumption of cement is about 15 billion tonnes per annum and it is increasing at about 1% per annum The electrical energy consumed in cement production is approximately (PDF) Investigating and comparing the effect of process October 2023; Journal of the Southern African Institute of Mining and Metallurgy 123(9):471478A study of different grinding aids for lowenergy The cement production process 1 The Quarry: The cement production process begins with the extraction of limestone and clay from the quarry 2 Crusher and PreBlending: The material is then crushed to reduce particle sizes and blended to reduce variability in composition 3 Raw Mill and Kiln: Raw materials and additives areA practical guide to improving cement manufacturing processes
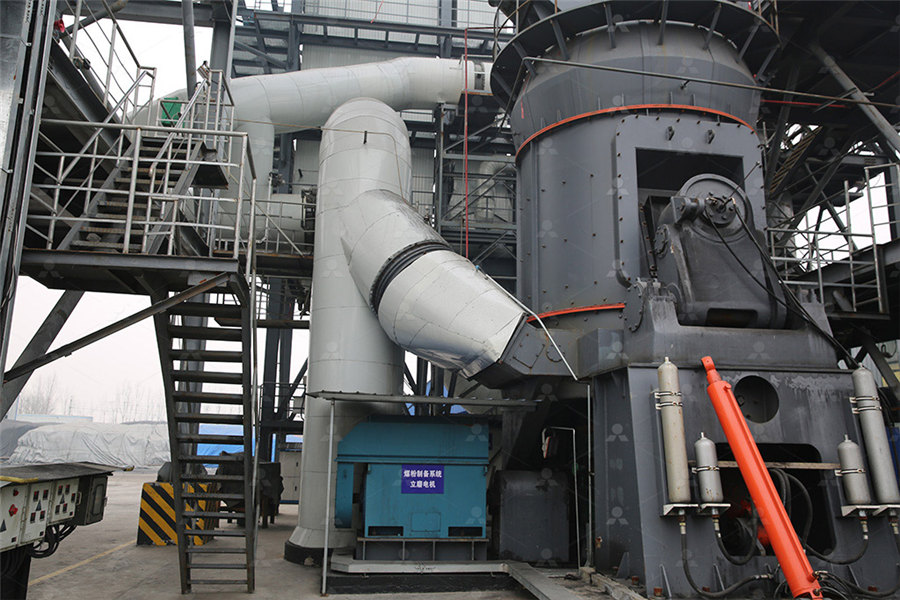
Deep decarbonisation of industry: The cement sector Europa
sharp decline in cement production over the last 15 years, from a peak of 262Mt in 2007 to 168Mt in 2017, equivalent to a reduction in cement per capita from 05 to 03 tonnes per person (3) The CO 2 intensity of cement production over that period has improved by about 7% (06t of CO 2 emitted per tonne of cement in 2017) (2)2024年4月18日 ⌀35m×13m cement ball mill 32x13m cement 3x11m slag grinding mill for Portland cement manufacturing production and then enter the highefficiency powder separator for powder selection⌀35m×13m cement ball mill 32x13m cement clinker millliving in the modern world [3] Cement is widely used in developed countries and is therefore considered as one of the most frequently utilized substances in many construction areas [4,5], applications for decoration [6, 8], and medicine [9, 11] There are many economic benefits of cement production thatImpacts of Cement Production on the Environment with Practical 2015年6月1日 identifying environmental impacts of cement production with life cycle assessment: literature reviewIDENTIFYING ENVIRONMENTAL IMPACTS OF CEMENT PRODUCTION
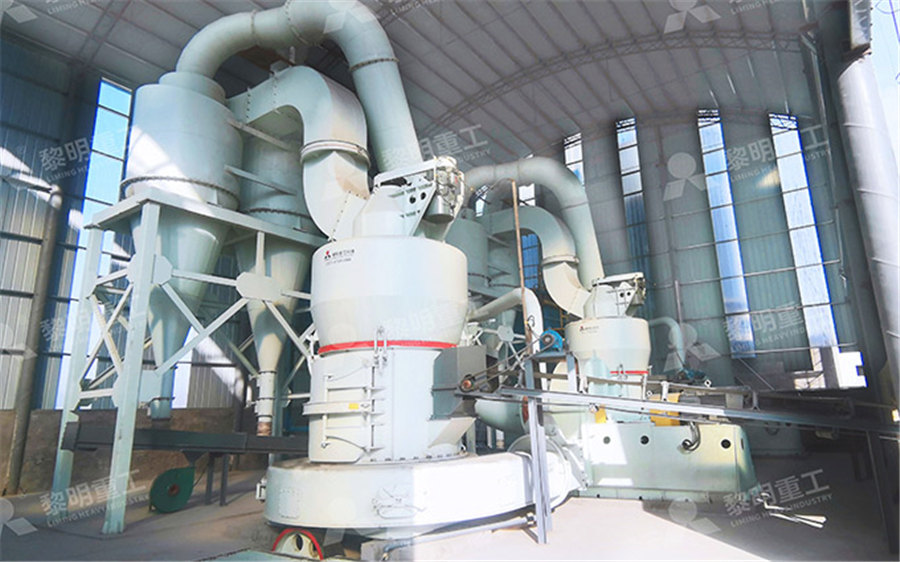
The selection and design of mill liners Academia
The Selection and Design of Mill Liners Malcolm Powell*, Ian Smit#, Peter Radziszewski§, Paul Cleary†, Bruce Rattray+, KlasGoran Eriksson‡ and Leon Schaeffer٭ *Mineral Processing Research Unit, University of Cape Town, Cape Town, South Africa, Anglo Research, Johannesburg, South Africa § Department of Mechanical Engineering, McGill Stage of Cement Manufacture There are six main stages of the cement manufacturing process Stage 1: Raw Material Extraction/Quarry The raw cement ingredients needed for cement production are limestone (calcium), sand and clay (silicon, aluminum, iron), shale, fly ash, mill scale, and bauxite The ore rocks are quarried and crushed into smaller pieces of about 6 inchesHow Cement is Made Cement Manufacturing ProcessWith the increase of cement mill specifications and the requirement of energy saving, high yield, and high quality of cement grinding plant, the closedcircuit grinding is an inevitable trend of cement grinding unitThe essential equipment of a closedcircuit grinding system is a cement classifier, also known as a cement separatorThe function of the cement classifier is to select How To Measure Your Cement Mill And Cement Classifier? AGICO CEMENTIn cement plants, proper specification and supply of AC induction motors is critical to project schedules and providing efficient production This paper focuses on the selection of AC induction motors for cement mill applications, with reference to fan, kiln and vertical mill applications The criteria for motor selection includes:Selection of AC Induction Motors for Cement Plant Applications
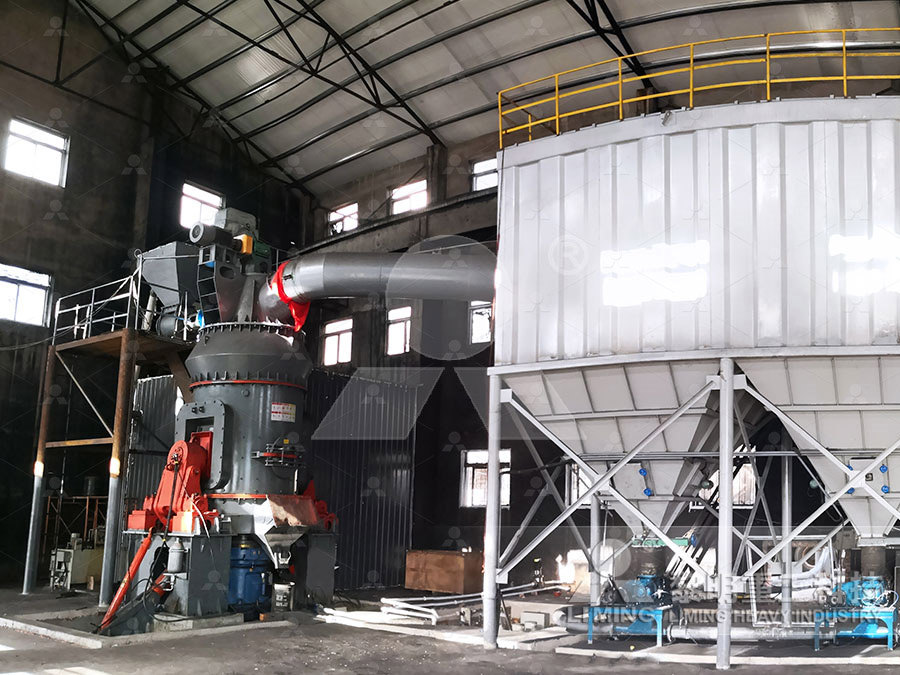
Minimizing waste using lean manufacturing: A case in
PDF On Apr 1, 2017, Elita Amrina and others published Minimizing waste using lean manufacturing: A case in cement production Find, read and cite all the research you need on ResearchGate2023年7月10日 Cement manufacturing is a significant industrial activity that plays a vital role in the construction sector However, the process of cement production is associated with various environmental Cement Manufacturing Process and Its Environmental 2018年10月10日 Heat transfer in cement production with raw mill considering the minimum temperature difference 1Hot composite curve; 2cold composite curve, 3heat exchangers (developed after [30])Heat Integration in a Cement ProductionChemical process industries are running under severe constraints, and it is essential to maintain the endproduct quality under disturbances Maintaining the product quality in the cement grinding process in the presence of clinker heterogeneity is a challenging task The model predictive controller (MPC) poses a viable solution to handle the variability This paper addresses the Predictive Controller Design for a Cement Ball Mill Grinding
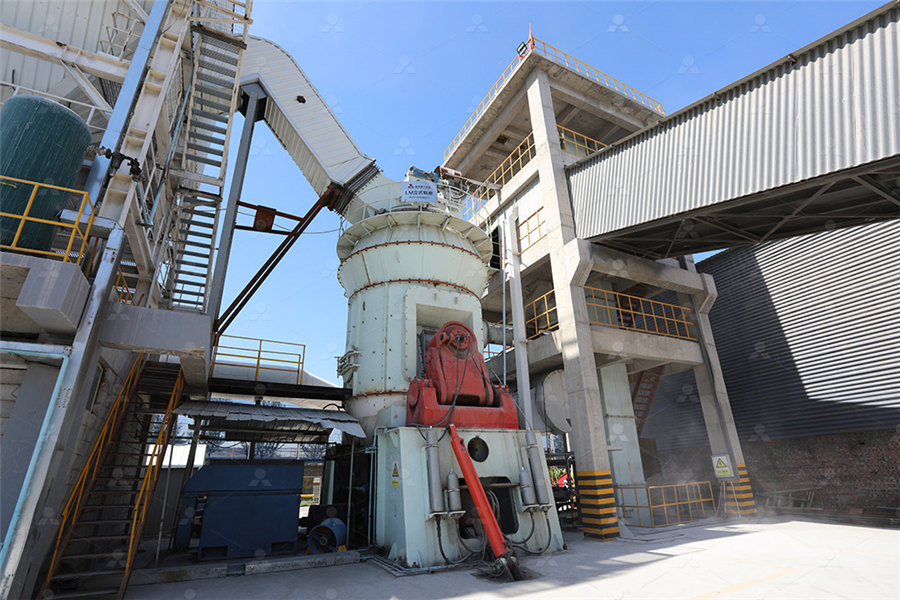
The Decision Algorithm of Cement Mill Operation Index Based
2023年1月25日 Abstract An improved differential evolutionary cement mill operation index decision algorithm based on constraint control and selection strategy is proposed to address the problem that the operation index is usually decided by manual experience in the cement mill operation process, which causes unqualified cement specific surface area and excessive 2024年6月1日 Cement production involves the combustion of fossil fuels and the calcination of limestone, leading to the release of large amounts of carbon dioxide (CO 2) Simultaneously, optimising aggregate selection, a substantial portion of concrete volume, involves choosing materials with lower embodied carbonDecarbonising cement and concrete production: Strategies, 2015年12月1日 With 460 new mill orders in 2012, China's local market is not only much bigger than the rest of the world's, but in addition, a share of over 60% of the cement is produced on grinding systems with HPGRs [51], [1] The technology of cement production will without doubt be developed further in future years, as it has in the pastProcess technology for efficient and sustainable cement production2022年5月15日 Cement production in China reached 233 billion tons in 2018, accounting for more than half of the global production (China Building Materials Federation, 2019)In 2019, over 95% of all cement clinker was produced from cement plants using new dry clinker production process (Ghazvini et al, 2020, Cai et al, 2020, Li et al, 2019)In the cement plants using this Mercury emission characteristics and mechanism in the raw mill
.jpg)
(PDF) Analysis of material flow and consumption in cement production
2015年8月1日 The results show that approximately 248t, 469t, and 341t of materials are required to produce a ton of the product in raw material preparation, clinker production, and cement grinding stages 2020年1月1日 The demand for cement, which is one of the key components of concrete, is high in Ethiopia, but it is the most expensive and environmentally unfriendly construction materialAssessment on Cement Production Practice and Potential Cement