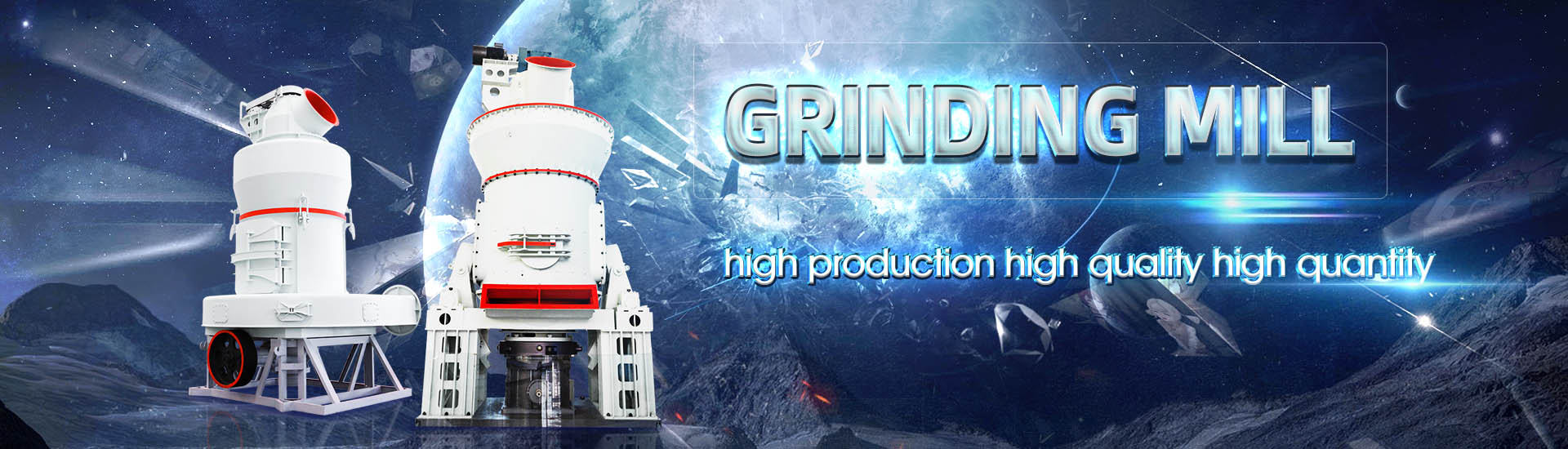
Water slag grinding process
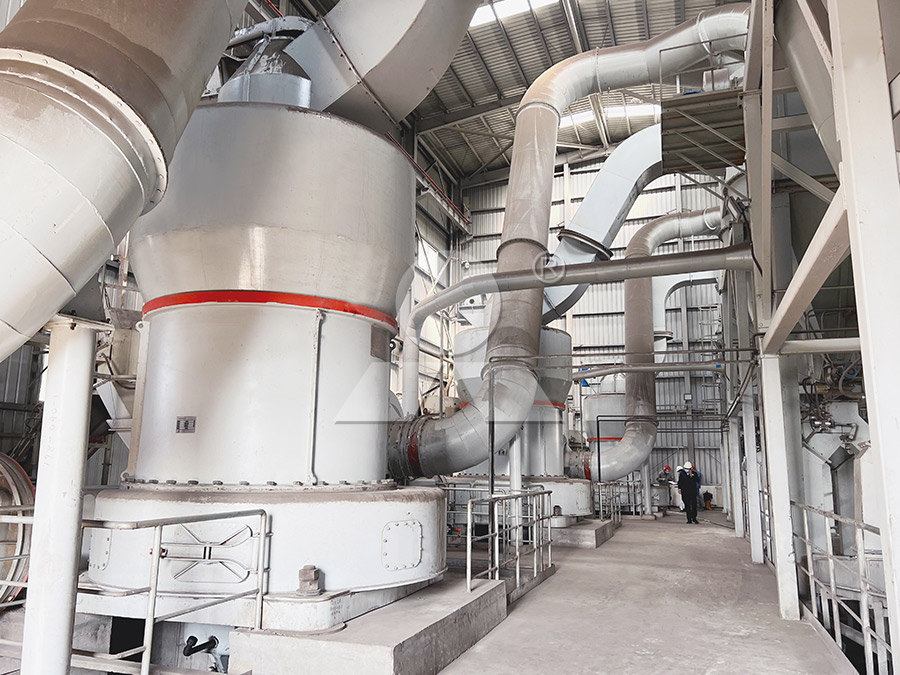
A new technological approach to the granulation of slag melts of
2021年11月3日 It is shown that the main advantage of the proposed HVG process is the provision of forced highspeed vortex convection of water, with the effect of vertical suction, crushing, and degassing of the threephase (water–slag granules–water vapor) heterogeneous 2021年9月1日 In this paper, the wet extractive grinding method for efficient recovery of calcium from steelmaking slags was studied This work supports the Sustainable Development Goal of Detailed performance analysis of the wet extractive grinding 2023年1月18日 In the study, the influencing factors of wetgrinding phosphorus slag (PS) and reaction kinetics on the early hydration of Portland cement were investigated The results The effect of wetgrinding phosphorus slag on the hydration Based on these results, we developed a new water granulation system for production of water granulated slag with the unit weight 140 kg/l or more and average grain diameter of 2 mm or more as a raw material for coarse, high Effect of Water Granulation Conditions on Density and
.jpg)
Iron recovery from lead smelting waterquenching slag by
2024年4月15日 This study explored the recovery of valuable metal elements in the lead smelting waterquenching slag using the method of “roasting–grinding–magnetic separation” at a In blunt box, high pressure water from porous nozzle jet will quench the molten BF slag In the next case, water quenching slag pours through graining tank and flows into the settling pond A Review of Granulation Process for Blast Furnace Slag Semantic 2019年12月9日 The granulation processes employ mechanical impact or highpressure fluids (eg air or water) to break up the slag into small granules of typically 1–5 mm There are Granulation and Heat Recovery from Metallurgical SlagsIn metallurgical operation, the molten slag produced in the furnace is rapidly quenched by water to reduce its size for easier handling and to change its structure into glassy state This procedure Dry Fine Grinding of Granulated Blast Furnace Slag Quenched by
.jpg)
Process Concept for the Dry Recovery of Thermal Energy of Liquid
2021年6月24日 With the innovative approach presented in this work, it is possible to recover thermal heat from liquid slags The process concept consists of a slag tundish and four 2019年5月23日 Steel slag is the waste generated in the steelmaking process and includes ferric oxide and the impurities of some infusible matters It is the byproduct when slagforming Comprehensive Utilization Technology of Steel Slag2023年3月12日 Aluminum has a variety of uses in the building, transportation, electric power, packaging, national security, and hightech industries due to its unique chemical and physical properties []Cryolitealumina molten salt Recovery of Carbon and Cryolite from Spent Carbon 11ügranulated slag Figure 2 INBA process 4 Dry granulation process On the blast furnace slag treatment technology, for a long time, water quenching process has token the leading position However, there are many defects of waterquenching slag method, which can be roughly concluded as follow: a mass of sensible heat unrecovered, highA Review of Granulation Process for Blast Furnace Slag Semantic
.jpg)
Detailed performance analysis of the wet extractive grinding process
2021年9月1日 Then, CaO from the slag powder is selectively extracted using a NH 4 Clwater solvent, and the slag leaching residue is removed by filtering the solution and plastic production In this paper, the focus is on the further improvements on the wet extractive grinding process, wherein grinding of the slag is combined with the Ca 2024年7月12日 The valuable metals copper and zinc were successfully recovered from a waterquenched lead smelting slag containing zinc in Gansu Province This study focuses on the application of the direct reduction roastingflotation process for extracting these metals from the slag phase To comprehend the recovery principle of copper and zinc minerals in the slag Recovery of Zinc and Copper from Lead Slag by the Combined Process 2023年2月15日 Slag bricks Slag brick production process Slag brick is made by mixing, watering, grinding and pressing slag and limestone In the production process of slag brick, the particle size of the slag is generally smaller than 8 mm, and the steam temperature injected into the kiln is about 80 ℃ to 100 ℃, the maintaining time is about 12 hoursHow to Process Slags (with detailed process)? Fote MachineryWater slag is an important material for the production of mineral powder, and is also a relatively ideal cementing material at present, can be widely used in slag grinding treatment The whole set of slag grinding treatment process includes crushing, drying, grinding, grading, transportation, collection, storage and other steps, Application Of Slag Grinding Mill Introduction To Treatment Process
.jpg)
Wet extractive grinding process for efficient calcium recovery
2020年5月1日 This paper presents a process improvement of the pHswing process (referred to as X2PCC) wherein a steelmaking slag is used as a source of calcium oxide for the mineral carbonation of CO 2We first dissolve Ca from the slag, then separate the solid phase by filtering, and, finally, bubble CO 2 into the Carich solution to precipitate it as CaCO 32021年6月7日 Besides, it is very uneconomical to process steel slag by drygrinding [14] The wetgrinding steel slag and water were settled into a 20℃ chamber to ensure the temperature of specimens were constant before the mix 246 Compressive strength The water to binder ratio of specimens was 04Effect of wetgrinding steel slag on the properties of Portland Our slag grinding plant integrates crushing, drying, and grading, it also has high crushing efficiency and strong drying ability our slag grinding plant realizes the ultrafine grinding technology with a simplified process, small floor space, low investment, and longer service lifeSlag Grinding Plant GGBS Plant Slag Mill, Slag Grinding MillIn the production process, slag ball mill can not only grind the slag separately, but also mix grinding with cement clinker and gypsum It has been widely used in cement industry For the grinding equipment of slag materials, we also produce watergranulated blast furnace slag ball mill and steel slag ball mill, which are used for grinding Blast Furnace Slag Ball Mill
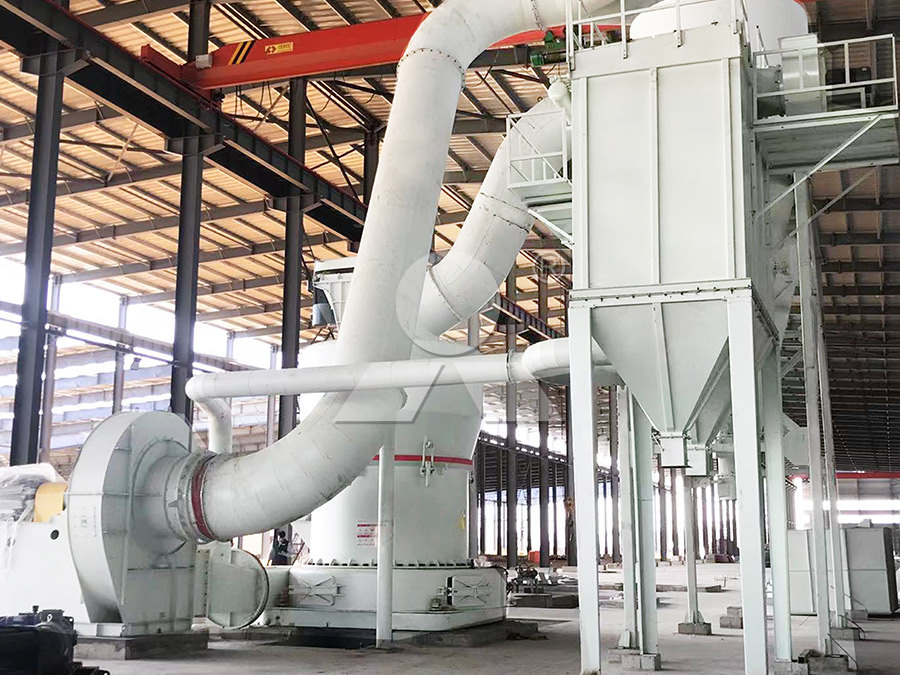
Utilization of lithium slag by wetgrinding process to improve the
2018年12月20日 The results show that lithium slag with D(05) of 304 μm, which is extremely difficult to be prepared in drygrinding system, can be easily obtained with wetgrinding process; the ions dissolution of lithium, aluminum, and silicon phase can also be significantly facilitated in wetgrinding process2019年12月20日 Ground granulated blast furnace slag (GGBS) as one of the most widely used byproducts has been used in building construction for recent two decades [15], [16], [17]GGBS can partly replace cement and use as supplementary cementitious materials, which not only reduces the CO 2 emissions, but also improves the durability of system due to its potential Compressive strength and hydration process of ground granulated The open circuit grinding process is the earliest slag powder grinding technology It has the advantages of simple process, low technical requirements for operators, and low investment cost The unit power consumption of this system is about GGBS Production Line Slag Mill for Slag Powder 2022年6月24日 Grinding is a manufacturing process which significantly contributes in producing high precision and durable components required in numerous applications such as aerospace, defence and automobiles(PDF) A comprehensive review on the grinding process:
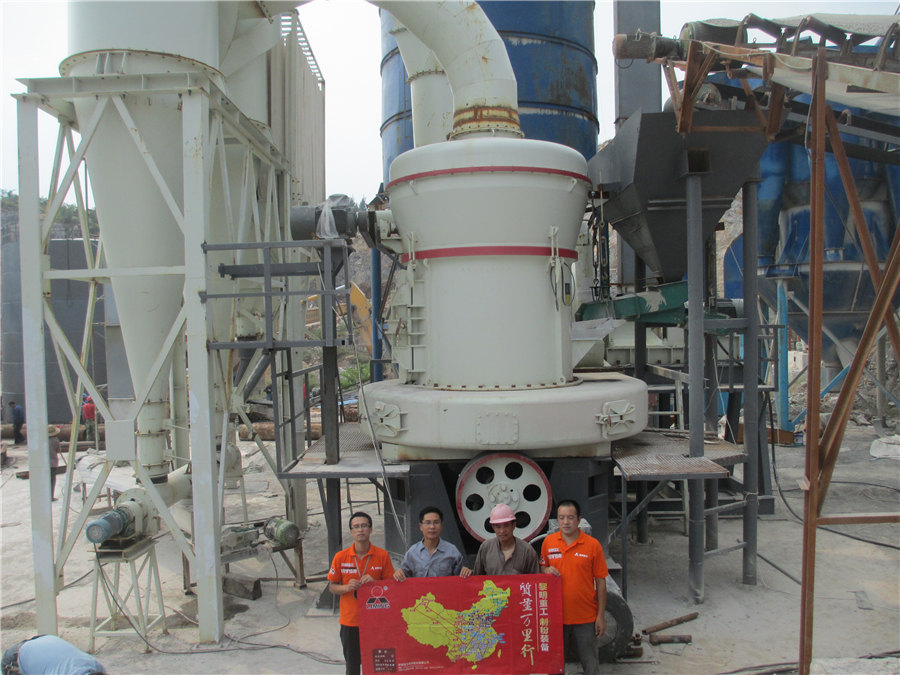
GRINDING Grinding options for slag and pozzolan PEC
Grinding options for slag and pozzolan While the use of supplementary cementitious materials is increasingly popular, the use of granulated blastfurnace slag and pozzolans presents extra challenges to the grinding process A careful assessment of grinding options available is key to efficient grinding operations2022年6月1日 Although the grinding energy per kg of slag was low (0016 kWh/kg slag), the low efficiency of calcium extraction during leaching (below 10%) caused a large grinding specific energy consumption (21 – 24 kWh/kg Ca(OH) 2), underscoring the importance of improving the calcium extraction from slag to decrease the energy consumption and CO 2 footprint of the A pilotprocess for calcium hydroxide production from iron slag balls The reaction between the ground slag and water, by which calcite is formed in the drying process, becomes active with the progress of grinding KEY WORDS: Grinding Aids, Dry Fine Grinding, Blast Furnace Slag, Xray Diffraction, Mechanochemical Effect, Ball Mill 1 Introduction Blast furnace slag is obtained as metallurgical waste producDry Fine Grinding of Granulated Blast Furnace Slag Quenched by Water 2024年2月25日 This is an article in the field of mineral processing engineering According to the principle of mechanochemistry, the waterquenched silicomanganese slag is ground by vibrating mill The effect of grinding time on the specific surface area, particle size distribution and activity evaluation of the waterquenched silicomanganese slag is studied, and the specific surface Mechanical Grinding Characteristics of Water Quenched SiManganese Slag
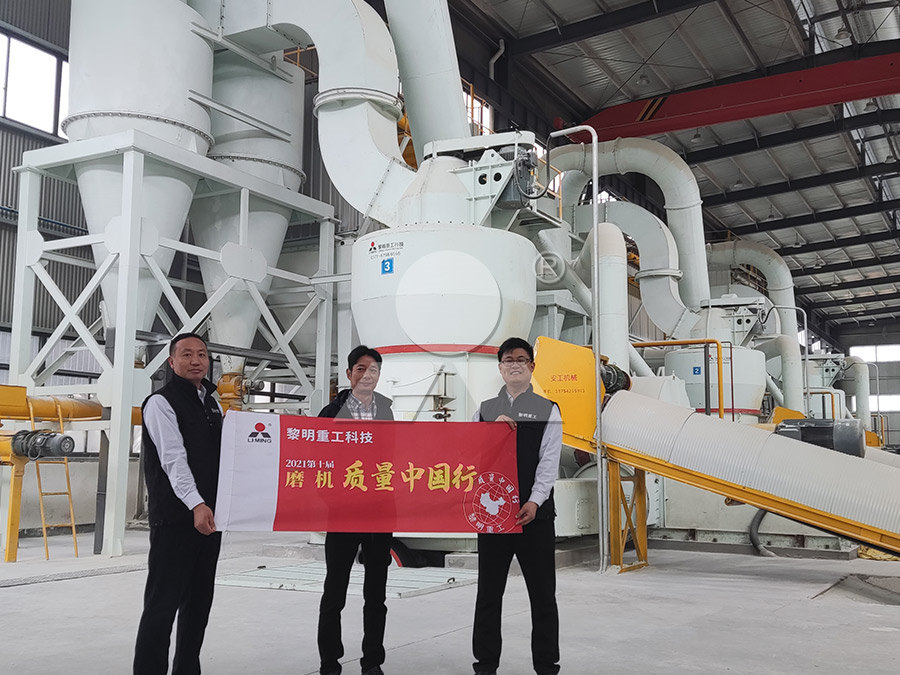
The slurry and physicalmechanical performance of autoclaved aerated
2019年9月10日 Some previous studies have been conducted on preparation and characterization of carbide slag based AAC products Fan Junjie has prepared AAC with compressive strength of over 20 MPa and density of about 600 kg/m 3 by utilizing 22% content of carbide slag [7]Changlong Wang has produced AAC (579 kg/m 3, 447 MPa) by using 25% 2020年7月1日 PDF Slag powder is a process with characters of multivariables, strongly coupling and nonlinearity the grinding roller pressure has a large impact on the material layer thickness TheAnalysis and multiobjective optimization of slag powder process2020年3月29日 The molten slag was not water quenched after tapping and directed into a ground bay to be air cooled The collected samples were thoroughly characterised for evaluation of different Study of iron ore mixtures behavior in the grinding pelletizing process Miner Process Extr Metall Rev, 38 (2017), pp 3035, 101080/ Utilisation perspective on water quenched and aircooled blast 2023年11月23日 The wetgrinding process was performed in a vertical stirred mill, as can be seen in Figure S2 The spherical zirconia (ZrO 2) balls with diameters between 12 mm and 14 mm were adopted as grinding mediaThe weight ratio of raw steel slag, water and ZrO 2 balls was 1:1:2 The grinding time was set as 60 min at the speed of 400 rpmSimultaneously enhanced mechanical and electromagnetic
.jpg)
Process Concept for the Dry Recovery of Thermal Energy of Liquid
2021年6月24日 Industrialscale applications incorporating the recycling of those byproducts are common since many decades and include examples like (1) the grinding of waterquenched blast furnace slag (GGBFS) to receive hydraulic properties for their use in cement, (2) using stabilized slags as aggregates in roads and civil installations, (3) using freelime and phosphorous 2020年11月19日 As the titanium industry rapidly develops, lowgrade ilmenite resources are drawing global attention The direct use of lowgrade ilmenite can result in low production efficiency and heavy pollution In addition, the production of hightitanium slag via electric furnace melting consumes significant energy and possesses low production efficiency Therefore, a HighTitanium Slag Preparation Process by CarbothermicMixed GGBS and water into a wetgrinding tank, and ground at a speed of 400 r/min for 30 min and 60 min to prepare GGBS slurries (WT1 and WT2) Fig 2 Utilization of lithium slag by wetgrinding process to improve the early strength of sulphoaluminate cement paste J Effect of ground granulated blastfurnace slag slurries by wetgrinding 2020年5月1日 This paper presents a process improvement of the pHswing process (referred to as X2PCC) wherein a steelmaking slag is used as a source of calcium oxide for the mineral carbonation of CO 2We first dissolve Ca from the slag, then separate the solid phase by filtering, and, finally, bubble CO 2 into the Carich solution to precipitate it as CaCO 3Wet extractive grinding process for efficient calcium recovery
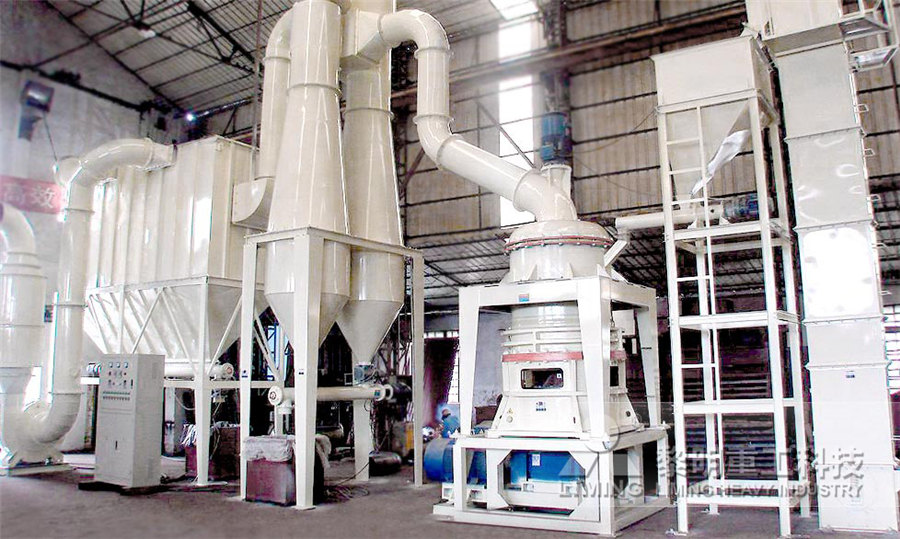
Utilisation perspective on water quenched and aircooled blast
2020年7月20日 Efficient utilisation and recycling of industrial waste along with minimum exploitation of natural resources are major challenge towards the circular economy and sustainability of the planet Blast furnace slag is a byproduct of the ironmaking process while producing pig iron The present research provides an understanding of the two different types The main challenge of the steel industry for the next decade is the steel production transformation process, starting in Europe The CO 2 intensive blast furnace/basic oxygen furnace (BOF) route will be substituted by a combination of Direct Reduced Iron (DRI), based on natural gas, later on “green” hydrogen, with an Electric Arc Furnace (EAF) or a Submerged Arc Furnace (SAF), The steel production transformation process in Europe: New slag Some manufacturers grind the raw materials dry, while others use a wetgrinding process involving water Quarrying Cement manufacturers quarry raw materials including limestone, clay, and sand including fly ash, blast furnace slag, and other byproducts CrushingHow Cement is Made Portland Cement AssociationThe recycle or reuse of silicon slag is in urgent need Tan et al [13] studied the hydrogen production reaction of MGSRS and water during the wet grinding process, e Reaction diagram of silicon with water during the grinding process
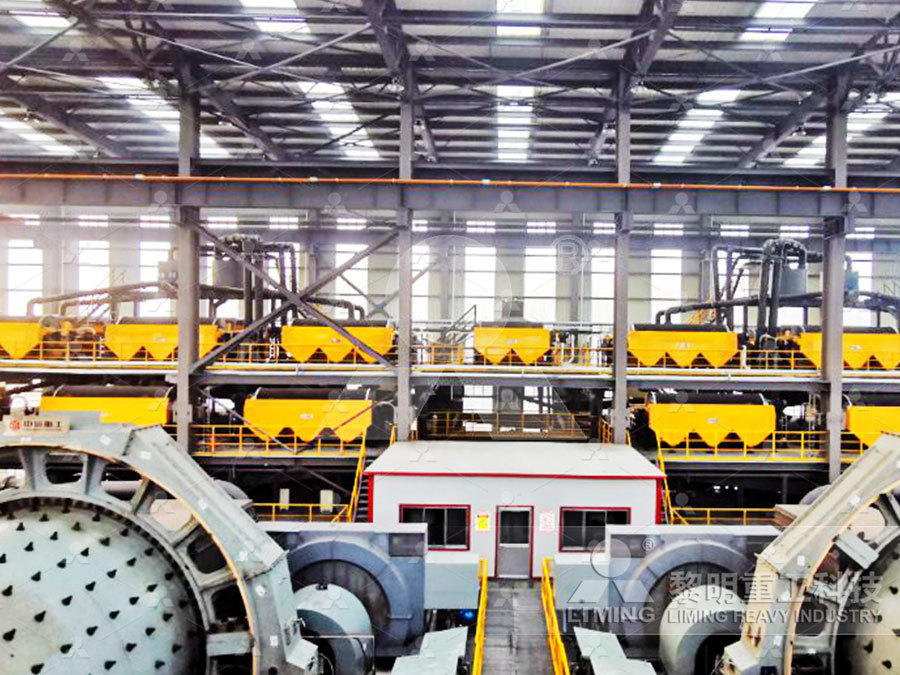
Recovery of Carbon and Cryolite from Spent Carbon
2023年3月12日 Aluminum has a variety of uses in the building, transportation, electric power, packaging, national security, and hightech industries due to its unique chemical and physical properties []Cryolitealumina molten salt 11ügranulated slag Figure 2 INBA process 4 Dry granulation process On the blast furnace slag treatment technology, for a long time, water quenching process has token the leading position However, there are many defects of waterquenching slag method, which can be roughly concluded as follow: a mass of sensible heat unrecovered, highA Review of Granulation Process for Blast Furnace Slag Semantic 2021年9月1日 Then, CaO from the slag powder is selectively extracted using a NH 4 Clwater solvent, and the slag leaching residue is removed by filtering the solution and plastic production In this paper, the focus is on the further improvements on the wet extractive grinding process, wherein grinding of the slag is combined with the Ca Detailed performance analysis of the wet extractive grinding process 2024年7月12日 The valuable metals copper and zinc were successfully recovered from a waterquenched lead smelting slag containing zinc in Gansu Province This study focuses on the application of the direct reduction roastingflotation process for extracting these metals from the slag phase To comprehend the recovery principle of copper and zinc minerals in the slag Recovery of Zinc and Copper from Lead Slag by the Combined Process
.jpg)
How to Process Slags (with detailed process)? Fote Machinery
2023年2月15日 Slag bricks Slag brick production process Slag brick is made by mixing, watering, grinding and pressing slag and limestone In the production process of slag brick, the particle size of the slag is generally smaller than 8 mm, and the steam temperature injected into the kiln is about 80 ℃ to 100 ℃, the maintaining time is about 12 hoursWater slag is an important material for the production of mineral powder, and is also a relatively ideal cementing material at present, can be widely used in slag grinding treatment The whole set of slag grinding treatment process includes crushing, drying, grinding, grading, transportation, collection, storage and other steps, Application Of Slag Grinding Mill Introduction To Treatment Process 2020年5月1日 This paper presents a process improvement of the pHswing process (referred to as X2PCC) wherein a steelmaking slag is used as a source of calcium oxide for the mineral carbonation of CO 2We first dissolve Ca from the slag, then separate the solid phase by filtering, and, finally, bubble CO 2 into the Carich solution to precipitate it as CaCO 3Wet extractive grinding process for efficient calcium recovery 2021年6月7日 Besides, it is very uneconomical to process steel slag by drygrinding [14] The wetgrinding steel slag and water were settled into a 20℃ chamber to ensure the temperature of specimens were constant before the mix 246 Compressive strength The water to binder ratio of specimens was 04Effect of wetgrinding steel slag on the properties of Portland
.jpg)
Slag Grinding Plant GGBS Plant Slag Mill, Slag Grinding Mill
Our slag grinding plant integrates crushing, drying, and grading, it also has high crushing efficiency and strong drying ability our slag grinding plant realizes the ultrafine grinding technology with a simplified process, small floor space, low investment, and longer service lifeIn the production process, slag ball mill can not only grind the slag separately, but also mix grinding with cement clinker and gypsum It has been widely used in cement industry For the grinding equipment of slag materials, we also produce watergranulated blast furnace slag ball mill and steel slag ball mill, which are used for grinding Blast Furnace Slag Ball Mill