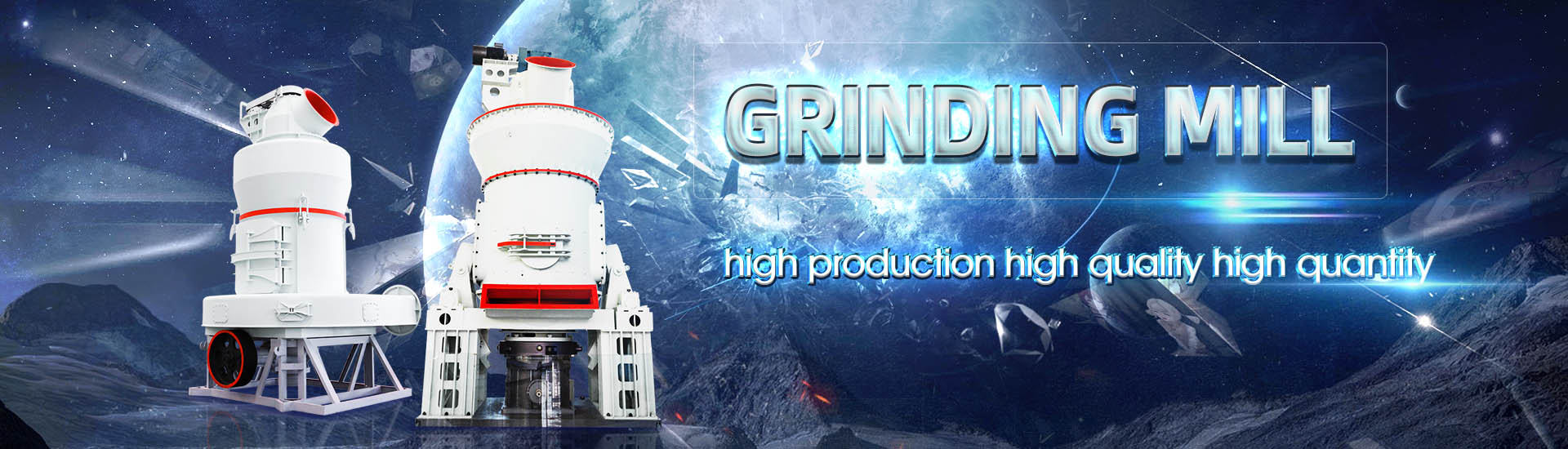
Silica medium speed mill
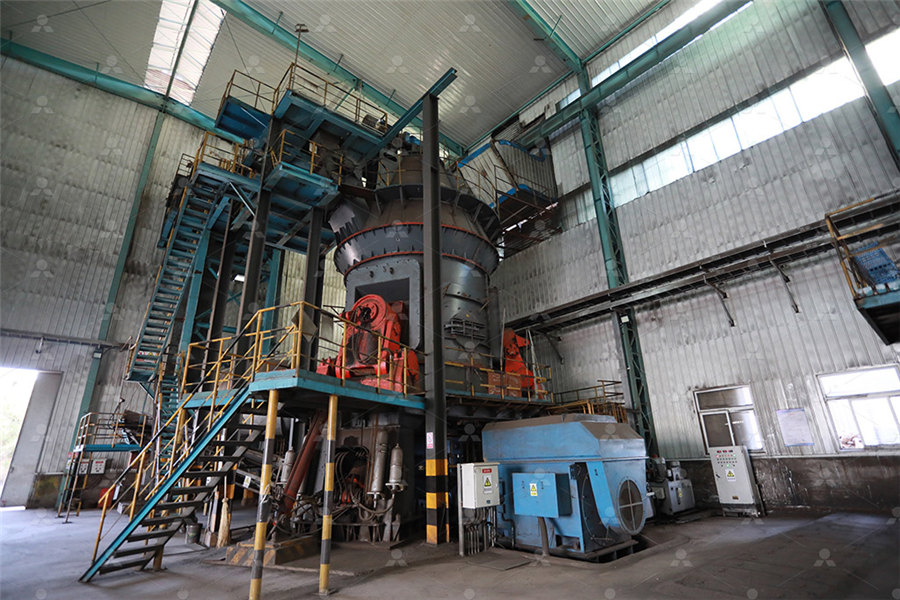
Comparative Study on Improving the Ball Mill Process Parameters
2021年2月19日 The optimum process parameters setting concluded that balls to powder weight ratio are 20:1, the optimum ball mill working capacity is 2 L while the optimum speed of the ball 2018年6月1日 In this article, alternative forms of optimizing the milling efficiency of a laboratory scale ball mill by varying the grinding media size distribution and the feed material particle size Effect of ball and feed particle size distribution on the milling Two types of silica powder with different structures, one crystalline (C1) and one amorphous (A1) were mechanically treated using a planetary type mill Three different rotation speeds (100, Mechanical modification of silica powders JSTAGEIn this paper, the grinding of dry silica sand in a batch type planetary ball mill is reported The effects of various technical parameters, such as ball size and density of ball material, The Mechanism and Grinding Limit of Planetary Ball Millingt J
.jpg)
Parameter Optimization of Ball Milling Process for Silica
2019年3月1日 The three main parameters applied in this study are Ball to Powder weight Ratio (BPR), time milling process, and rotational speed (rpm) The materials used in the study was The Vertical vibrating mill is a new design of vibrating mills which are used to produce micropowders, and nanopowders This paper studies the effect of four different parameters EXPERIMENTAL STUDY OF THE EFFECT OF BALL DIAMETER, 2020年1月15日 In this study a metallurgical grade silicon quality was milled in a planetary ball mill and the properties of the powder were investigated as a function of grinding time, grinding Silicon Powder Properties Produced in a Planetary Ball Mill as a 2020年10月1日 In this paper, we present a detailed investigation of the dry grinding of silica sand in an oscillatory ball mill We are interested in the evolution of specific surface area Evolution of grinding energy and particle size during dry ball
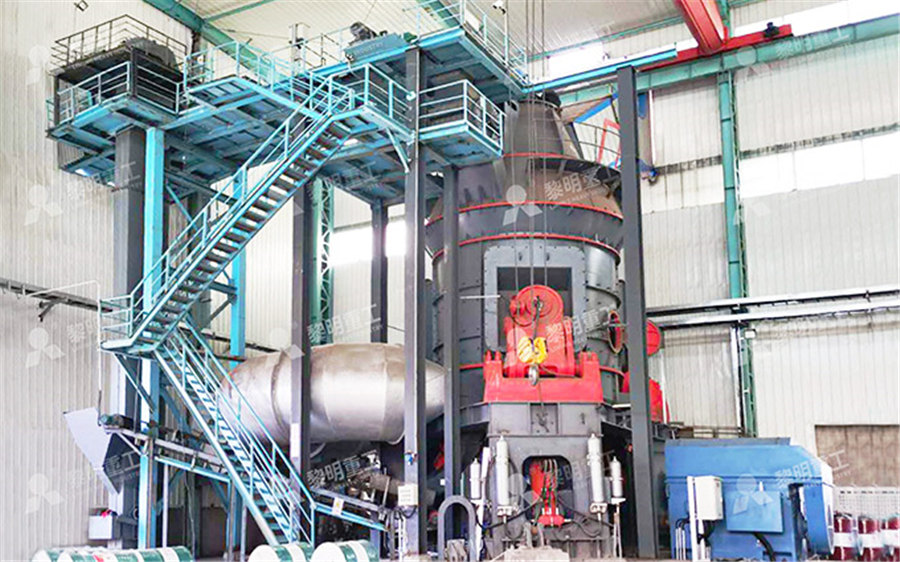
Mechanochemistry of silica on jet milling ScienceDirect
2008年8月26日 Fine grinding process of silica was carried out in a jet mill by varying the operational parameters such as feed rate, classifier rotational speed and grinding pressure 2023年1月12日 In this study, silica nanoparticles (SiO 2 NPs) were fabricated using a handmade ball mill as a novel, simple, rapid, costeffective, and green approach The sol–gel method was Facile, fast, and green preparation of highpurity and quality silica 2021年1月14日 Compared to regularsized silica beads, Four NEUM850 ceramicmedium stirred mills superseded the ball mills of second and Mill speed was again found to be a key operational factor for Effect of grinding media properties and stirrer tip speed on the 2022年11月5日 Surface modification of silica particles without a catalyst or solvent was the powder with the balls and modification agent was individually milled by rotating the pot at a speed of 150 rpm for 05, 1, 2, 3, 6, 12 Fig 5 shows the dispersity tests of the nonmodified and modified silica particles in the dispersion mediumSurface modification of silica powder by mild ball milling
.jpg)
Highefficiency and energyconservation grinding technology using
2022年1月1日 A pilotscale grinding technology of ceramic medium stirred mill was proposed in this study Based on the specific productivity and grinding efficiency, the appropriate grinding parameters were ascertained as follows: material ball ratio of 07, ceramic ball medium size ratio (10 mm: 15 mm: 20 mm = 3:2:5), stirring speed of 110 rpm, grinding concentration of 50%, 2017年8月1日 MPStype medium speed coal mills are widely used in the thermal power plants in China They are designed and manufactured by the German company Babcock This kind of coal mill has the characteristics of low energy consumption and smooth output and has a small effect on abrasive wear and an overhaul period [13], [14]Modeling of a medium speed coal mill ScienceDirectJet Mill, cyclone, bag filter and fan constitute a complete milling system After the compressed air is filtered and dried, it is sprayed into the milling cavity at high speed through Laval nozzles At the intersection of multiple highpressure airflows, the materials are repeatedly collided, rubbed, and sheared to be milledVertical Fluidized Bed Jet Mill ALPA micro silica powder 2023年10月27日 Imagine, for a moment, that you’re at the beach You pick up a handful of sand, and in that sand, there’s silica Now, imagine if thatFrom Sand to Storage: The Glass Revolution of Project Silica
.jpg)
Ball Mill Success: A StepbyStep Guide to Choosing the Right
2024年8月8日 Unlock the secrets to ball mill efficiency with our comprehensive guide on choosing the right grinding media Learn how material Additionally, evaluate the milling conditions, including the type of mill, speed, duration, and whether the process is wet or dry These factors will influence the selection of the most suitable 2015年6月20日 A Ball Mill Critical Speed (actually ball, rod, AG or SAG) is the speed at which the centrifugal forces equal gravitational forces at the mill shell’s inside surface and no balls will fall from its position onto the shell The imagery below helps explain what goes on inside a mill as speed varies Use our online formula The mill speed is typically defined as the percent of the Ball Mill Critical Speed 911MetallurgistThe feed exhibited bimodal particle size distributions, where the distribution was focused at 10–100 lm and 01–1 lm, two peaks being observed at 05 lm and 22 lm Fig 5 shows that the particles in the range 01–1 lm increased when silica was ground at low and medium levels of grinding pressure and classifier rotational speed, whilst at high grinding pressure and classifier Effect of operational parameters on the breakage mechanism of silica Find your silica mill easily amongst the 18 products from the leading brands on DirectIndustry, ball mill adopts special design and suitable proportion of grinding medium to achieve ideal grinding fineness; Rotational speed: 2,050 rpm Silica mill All industrial manufacturers
.jpg)
High Purity Silica from Palm Oil Mill Fly Ash for Catalyst ZSM5
Materials Science Forum, 2019 ZSM5 has been successfully synthesized by seeding method using coal bottom ash and rice husk as the sources of silica and aluminaSynthesis ZSM5 were performed by the hydrothermal method in autoclave autogenous at 180 °C for 36 h with molar ratio 10Na : 50SiO : 2Al2O3 : 500H2O with the addition of ZSM5 commercial as seed2020年1月15日 Mechanical milling is a promising route for production of submicron and nano sized silicon powders, but it is challenging to predict and control the product properties In this study a metallurgical grade silicon quality was milled in a planetary ball mill and the properties of the powder were investigated as a function of grinding time, grinding bead size (20 mm, 2 mm, Silicon Powder Properties Produced in a Planetary Ball Mill as a SpeedMill PLUS Homogenisierer der Wahl Die SpeedMill PLUS ist ein System für das hocheffiziente Homogenisieren unterschiedlichster Ausgangsmaterialien als Basis für eine nachfolgende Isolierung und Aufreinigung von DNA, RNA oder ProteinenSpeedMill PLUS – Homogenisierer für DNA/RNA IsolierungHorizontal installation of highprecision grading rotor, linear speed up to 80m/s, to ensure the accuracy of vertex cutting Features: Fine powder with good repeatability, stable and reliable; constant temperature or low temperature without medium crushing; It has the advantages of high energy utilization rate, wear resistance of equipment, closed crushing, clean and Horizontal Fluidized Bed Jet Mill ALPA micro silica powder
.jpg)
Effect of operational parameters on the breakage mechanism of silica
2008年4月1日 Fig 4 shows the span values for the ground silica at various operating parameters of the jet mill The span values for the ground silica ranged from 109 to 238 The minimum span value was obtained when silica was ground at a feed rate of 4 kg/h, a classifier rotational speed of 7000 rpm and grinding pressure of 4 bars2013年12月1日 Request PDF Mechanical Milling of Tronoh Silica Sand Nanoparticles Using Low Speed Ball Milling Process Silica sand nanoparticles are widely used as filler, coating and reinforcer to increase Mechanical Milling of Tronoh Silica Sand Nanoparticles Using Low Speed 2020年1月13日 The industrial dynamic matrix controller commissioned on the AG mill with a variable speed drive resulted in a 66% reduction in power and a 40% reduction in load standard deviation These are the Abstract and Figures ResearchGate2015年6月2日 NS was made using various procedures such as chemical precipitation process, solgel technique, vaporization with high temperature, and speed of the vertical rotating mill and planetary and ball (PDF) Synthesis of silica nanoparticles from malpe beach sand
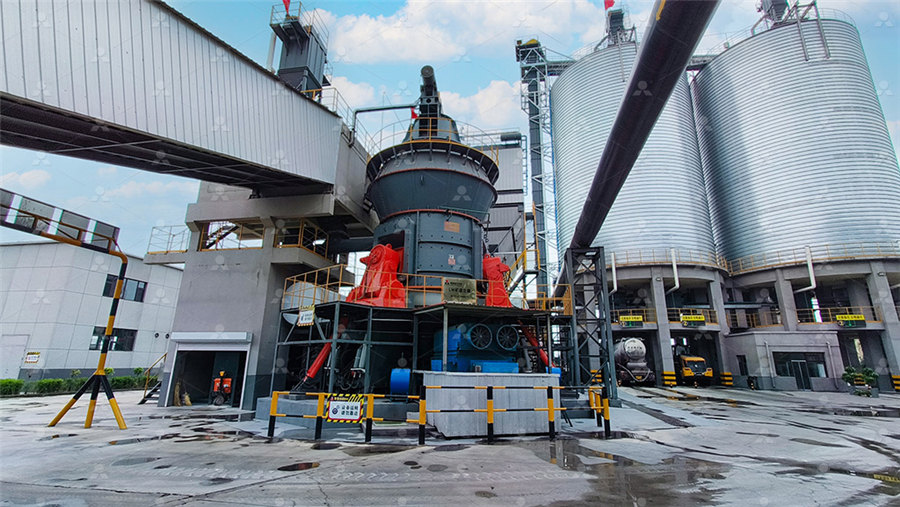
Silica removal from newsprint mill effluents with aluminum salts
2013年8月15日 The silica removal efficiency of softening depends on the solution pH Semblante et al, 2018) Aluminumbased coagulants had the highest efficiency at the highest dosage (5002500 ppm) and pH (83 MTW Series European Technology Trapezium Mill Threerings and Mediumspeed Micropowder Grinder Raymond Mill High Pressure Suspension Grinder Ball Mill Related Articles Pf 1214 Faridabad Based Sand Making Plant; Geology of quartz and hydrated silicabearing deposits near Silica And Quartz Deposit Of The Philippines Crusher Mills, 2018年2月1日 Agrowastes, especially ash containing silica, are promising sources of silica for synthetic amorphous silica production In this research, palm oil mill fly ash (POMFA) was used as a raw material Silica gel derived from palm oil mill fly ashThreerings and Mediumspeed Micropowder Grinder Raymond Mill High Pressure Suspension Grinder Ball Mill Related Articles Impact Crusher, Size And Shape; silica sand pulverizer– Rock Crusher Mill silica sand pulverizer liming is one of the biggest manufacturers in aggregate processing Machinery for the sand,mining,construction and Pulverizer Silica Quartz Processing Machinery Crusher Mills
.jpg)
Ball Milling Synthesis of Silica Nanoparticle from
2012年8月28日 The average particle size of the silica powders was around 70 nm, which decreases with increasing ballmilling time or mill rotational speed 55 Finally, the drug delivery capability of the This paper considers two finesized (d50 ∼10 µm) model drugs, acetaminophen (mAPAP) and ibuprofen (Ibu), to examine the effect of API dry coprocessing on their multicomponent medium DL (30 wt%) blends with fine excipients The impact of blend mixing time on the bulk properties such as flowability, bulk density, and agglomeration was studied The hypothesis tested is that Impact of Silica Dry Coprocessing with API and Blend Mixing Time 2018年6月1日 A number of researchers (Deniz, 2012; Bwalya et al, 2014; Petrakis et al, 2016) carried out studies about the effect of feed particle size and grinding media size on the grinding kinetics of different oresKhumalo et al, 2006 postulated that generally larger sized grinding media would break larger particles quicker but a finer product would be obtained by use of Effect of ball and feed particle size distribution on the milling Silica is one of the most fl exible active ingredients for a variety 2 – 4 % highspeed mixer Recommended literature Technical Information TI 1206: 15 – 35 % mediumshear mixer and mill Wettable powers (WP) and waterdispersible granules (WG) Carrier for activeSpecialty Silica
.jpg)
Retention aids for highspeed paper machines
silica and cationic starch were applied in combination In 1992, new types of specially designed structured colloidal silica (high microaggregation) were developed for 2Benefits obtained with CSM systems Improved runnability Lower furnish cost Increased wire life Increased machine speed Lower furnish cost filler content Decreased vacuums that the outermost medium attains a cascading state, whose motion curve is represented in Figure 1 Figure 1 Motion curve of outermost medium in the mill The calculation [810] reveals that when D (size of steel ball) = 25 mm and n (rotation speed of mill)PAPER OPEN ACCESS You may also like IOPscienceThe two types of silica powder (C1 and A1) used in the present investigation were supplied by TOSO Ltd, Japan Specification of the powders is shown in Table 1 A laboratory planetary mill (A FRITSCH Pulverisette 5, Germany) was used to mill the silica powders at room temperature Raw silica powders were milled in a 500ml zirconia potMechanical modification of silica powders JSTAGE2021年6月29日 The aim of this work was to observe the impact of the milling technique employed by the DESI 11 disintegrator on the properties of fly ash This type of mill is a highspeed pin mill with two Effects of Mill Speed and Air Classifier Speed on Performance of

Effect of grinding media properties and stirrer tip speed on the
2021年1月14日 Compared to regularsized silica beads, Four NEUM850 ceramicmedium stirred mills superseded the ball mills of second and Mill speed was again found to be a key operational factor for 2022年11月5日 Surface modification of silica particles without a catalyst or solvent was the powder with the balls and modification agent was individually milled by rotating the pot at a speed of 150 rpm for 05, 1, 2, 3, 6, 12 Fig 5 shows the dispersity tests of the nonmodified and modified silica particles in the dispersion mediumSurface modification of silica powder by mild ball milling2022年1月1日 A pilotscale grinding technology of ceramic medium stirred mill was proposed in this study Based on the specific productivity and grinding efficiency, the appropriate grinding parameters were ascertained as follows: material ball ratio of 07, ceramic ball medium size ratio (10 mm: 15 mm: 20 mm = 3:2:5), stirring speed of 110 rpm, grinding concentration of 50%, Highefficiency and energyconservation grinding technology using 2017年8月1日 MPStype medium speed coal mills are widely used in the thermal power plants in China They are designed and manufactured by the German company Babcock This kind of coal mill has the characteristics of low energy consumption and smooth output and has a small effect on abrasive wear and an overhaul period [13], [14]Modeling of a medium speed coal mill ScienceDirect
.jpg)
Vertical Fluidized Bed Jet Mill ALPA micro silica powder
Jet Mill, cyclone, bag filter and fan constitute a complete milling system After the compressed air is filtered and dried, it is sprayed into the milling cavity at high speed through Laval nozzles At the intersection of multiple highpressure airflows, the materials are repeatedly collided, rubbed, and sheared to be milled2023年10月27日 Imagine, for a moment, that you’re at the beach You pick up a handful of sand, and in that sand, there’s silica Now, imagine if thatFrom Sand to Storage: The Glass Revolution of Project Silica2024年8月8日 Unlock the secrets to ball mill efficiency with our comprehensive guide on choosing the right grinding media Learn how material Additionally, evaluate the milling conditions, including the type of mill, speed, duration, and whether the process is wet or dry These factors will influence the selection of the most suitable Ball Mill Success: A StepbyStep Guide to Choosing the Right 2015年6月20日 A Ball Mill Critical Speed (actually ball, rod, AG or SAG) is the speed at which the centrifugal forces equal gravitational forces at the mill shell’s inside surface and no balls will fall from its position onto the shell The imagery below helps explain what goes on inside a mill as speed varies Use our online formula The mill speed is typically defined as the percent of the Ball Mill Critical Speed 911Metallurgist
.jpg)
Effect of operational parameters on the breakage mechanism of silica
The feed exhibited bimodal particle size distributions, where the distribution was focused at 10–100 lm and 01–1 lm, two peaks being observed at 05 lm and 22 lm Fig 5 shows that the particles in the range 01–1 lm increased when silica was ground at low and medium levels of grinding pressure and classifier rotational speed, whilst at high grinding pressure and classifier Find your silica mill easily amongst the 18 products from the leading brands on DirectIndustry, ball mill adopts special design and suitable proportion of grinding medium to achieve ideal grinding fineness; Rotational speed: 2,050 rpm Silica mill All industrial manufacturers