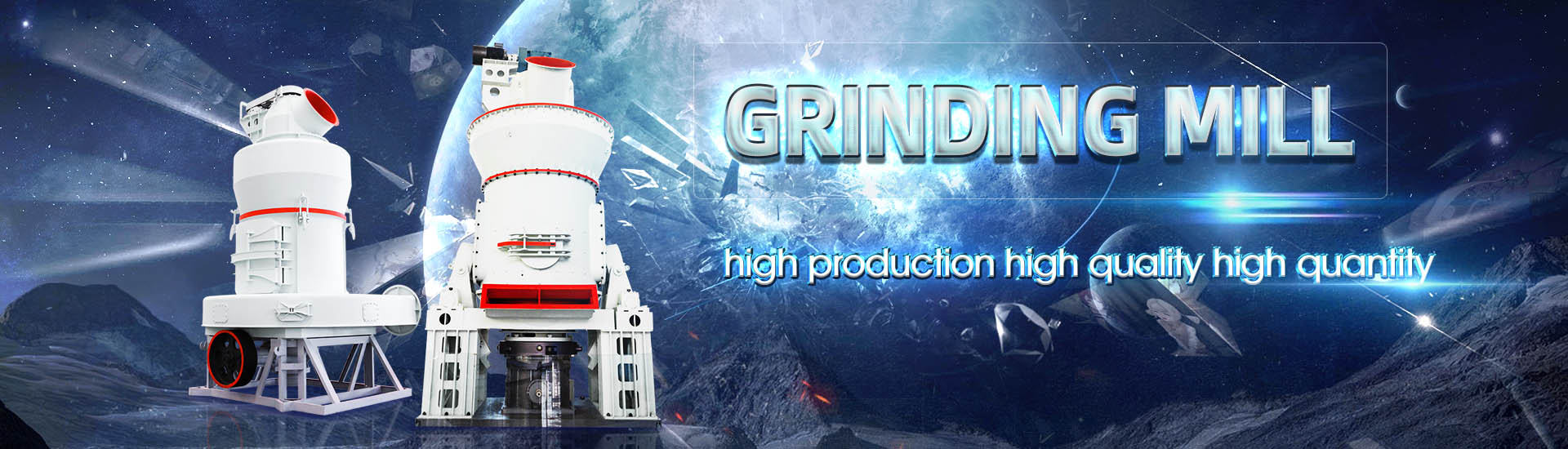
HOME→PGY medium pressure energysaving ore mill drive roller device diagram Jiangsu Lianyungang tungsten processing grinding equipment
PGY medium pressure energysaving ore mill drive roller device diagram Jiangsu Lianyungang tungsten processing grinding equipment

Roller Mill SpringerLink
2023年7月4日 The basic structure of the roller mill includes the grinding roller, the grinding body, the force generation and transmission mechanism, airflow, and the device for easy High Pressure Grinding Rolls (HPGR) technology is accepted as an energyefficient and costeffective alternative for treating specific mineral ore types HPGR technology has been A Review of the Modeling of High Pressure Grinding Rolls JSTAGE2023年1月1日 This paper presents the commercial implementation of a novel comminution circuit with high pressure grinding rolls (HPGR) followed by tower mill in a copper–lead–zinc Evaluating the performance of an industrialscale high pressure 2023年11月1日 This paper demonstrates the feasibility of using a ceramic medium stirring mill to reduce the energy consumption of grinding operations through an industrial verification Energy conservation and consumption reduction in grinding
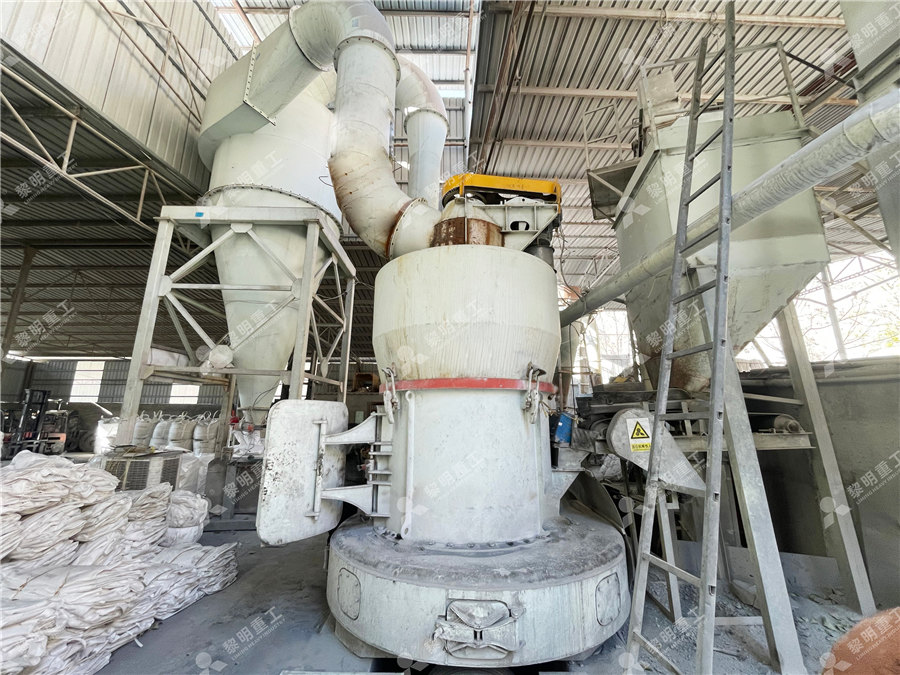
Quantification of HPGR energy efficiency effects on downstream
The paper presents investigations on grinding energy consumption, size distribution and microfracturing of HPGR products, which affect the efficiency of the whole comminution and 2022年3月16日 HPGR has been found to be efficient size reduction equipment compared to conventional size reduction equipments due to its potential processing benefits in terms of Potential of HighPressure Grinding Roll (HPGR) for Size Reduction ABB’s GMD is the most powerful mill drive system in the market to power semiautogenous (SAG), ball and autogenous (AG) mills, This ’workhorse’ for grinding operations combines a robust, Gearless mill drives Grinding ABBEnduron® high pressure grinding rolls (HPGR) can handle a wide variety of ores and particle sizes from fine pellet feed all the way up to coarse grinding of 75mm magnetite iron ore When Our Dynamic HPGR Technology for Mineral Grinding Weir
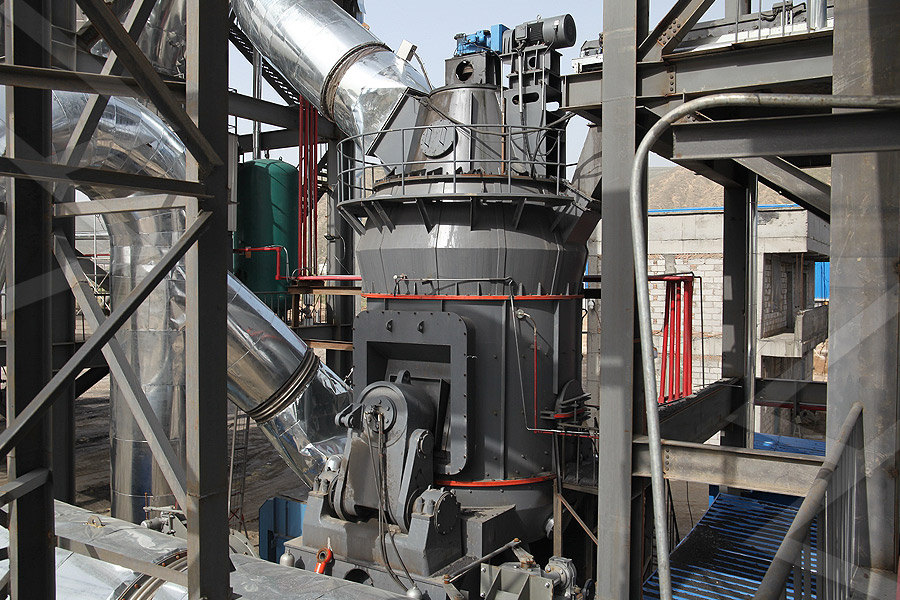
Metso comminution solutions Grinding
Stirred mills have proven to provide energy savings when compared with traditional grinding mills Metso engineers and manufactures both types of stirred mills, delivering industryleading 2018年1月1日 This paper presents and discusses a mathematical model for capacity management based on different costing models (ABC and TDABC) A generic model has been Energy efficiency of stateoftheart grinding processes2018年8月17日 Stage 1 — Drilling This is the stage where it all begins A rock cutting process, drilling sets the stage for the next steps in the mineral processing operationGrinding Mills — Types, Working Principle 2014年10月1日 In a test performed in the Loesche test center in Germany, copper slag grinding saved 229% energy in an airswept model and 344% energy in an overflow model [13,14]Copper Ore Grinding in a Mobile Vertical Roller Mill Pilot Plant
.jpg)
Energy Efficiency Analysis of Copper Ore Ball Mill Drive Systems
Energy savings may also be found in the ball mill drive systems In the scale of a processing plant, the electric motors of these drive systems account for 95% of the totalSession 11 Optimisation of Roller Press System Free download as PDF File (pdf), Text File (txt) or view presentation slides online This document discusses roller presses, which are compaction tools used primarily as pregrinders in cement production to increase grinding capacity Key points: Roller presses apply high pressure to compact and crack raw materials, Session 11 Optimisation of Roller Press System PDF Mill (Grinding HPGM series high pressure grinding roll is a new type of energysaving grinding equipment designed by the principle of highpressure material layer pulverization It consists of two squeezing rolls that rotate synchronously at a low speed One is a stationary roll and the other is a movable roll, which are both driven by a highpower motorSeries PGM Single Driving High Pressure Roller Mill2016年7月14日 HPGR test results published by Grier (1992) on gold ores from the Mt Todd project showed significant energy savings for a HPGR/Ball Mill circuit as compared to a SAG/Ball Mill plant By adding a Polycom highpressure grinding roll, the throughput of existing plants can be increased by as much as 150% while simultaneously reducing the power consumption by HPGR 911Metallurgist
.jpg)
Drive system for high pressure grinding rolls Increased roller
4 Intelligent operation and protection features Drive system for high pressure grinding rolls Drive system for high pressure grinding rolls Intelligent operation and protection features 5 Intelligent operation and protection features Ensuring increased roller life and productivity To leverage the benefits of using HPGRs in comminutionMarcelo Perrucci, Global Product Line Manager Grinding “Installing GMDs potentially means using less onsite mechanical equipment, and thus a reduced footprint in terms of mechanical space It is a more efficient technology in terms of energy How digitalized gearless drive technology results in energy savings after the thirdstage ne crushing operation to reduce the particle size of ball mill feed and improve the processing capacity of grinding operation The optimal process parameters of high pressure grinding roll and magnetic separation were determined to be a 10 mm of roller surface spacing, a 105 Mpa of roller surface pressure, a 14 r/min of High Pressure Grinding Roll and Magnetic Separation for Energy Saving Energy Saving Mining Processing Equipment Grinding Ball Mill HZE manufacture standard wet ball mills with high efficiency, low energy consumption, stability and reliability for grinding minerals of precious metals, base metals and nonmetal It can also be specially designed and customized according to the special requirements of the customersEnergy Saving Mining Processing Equipment Grinding Ball Mill
.jpg)
Highpressure mill, Highpressure grinding mill All
Output: 6 t/h 350 t/h Motor power: 75 kW 3,300 kW Machine length: 2,400 mm 7,200 mm WTM intelligent vertical mill is dedicated to the highefficiency dissociation of minerals, providing users with energysaving, consumption 2023年11月1日 Grinding operation is the last preparation stage before beneficiation In this stage, the material undergoes the combined action of impact and grinding, so that the ore particle size is diminished and the qualified materials is provided for succeeding beneficiation operations [1, 2]Generally, the quality of the grinding product is also an important factor to determine the Energy conservation and consumption reduction in grinding The document provides installation and operation instructions for the HRM1700M Vertical Roller Coal Mill It describes the mill's technical parameters, components, structure, working principles, and installation process Key aspects include grinding rollers that can be removed for maintenance, a hydraulic system that controls grinding pressure, and a separator that Operation Manual: HRM1700M Vertical Roller Coal Mill2006年2月1日 Highpressure grinding rollers have the advantage of energy saving (Aydoğan, Ergün, and Benzer 2006; Von Michaelis 2009;Wang et al 2013), and their products have a higher fine particle content High pressure grinding rolls (HPGR) applications in the cement industry
.jpg)
A Review on the Development of High Pressure Roller Mill
2013年8月1日 For the effect of application in nonferrous and ferrous ores, the high pressure roller mill will be widely applied in the future Skip to search form Skip to main content Skip to account menu Semantic Scholar's Logo 222,534,667 papers One contribution to minimise the increase is to use more efficient comminution equipment Verticalrollermills (VRM) are an energyefficient alternative to conventional grinding technology One reason is the dry inbed grinding principle Results of extensive test works with two types of magnetite iron ores in a Loesche VRM are presented hereResearch of iron ore grinding in a verticalrollermillThis paper presents an industrial verification test, adding a high pressure grinding roll and magnetic separation operation after the thirdstage fine crushing operation to reduce the particle size of ball mill feed and improve the processing capacity of grinding operation The optimal process parameters of high pressure grinding roll and magnetic separation were determined to High Pressure Grinding Roll and Magnetic Separation for Energy Saving GM14060 High Pressure Grinding Roll The project was being retrofitted in 2010 The type of ore has mineral hardness of f=1416, silicon content of approximately 48%, and is strongly abrasive The high pressure roller mill was put into operation in August 2011, the roller surface has been subjected to continuous improvementsHigh Pressure Grinding Roll Grinding Mill Supplier CITIC HIC
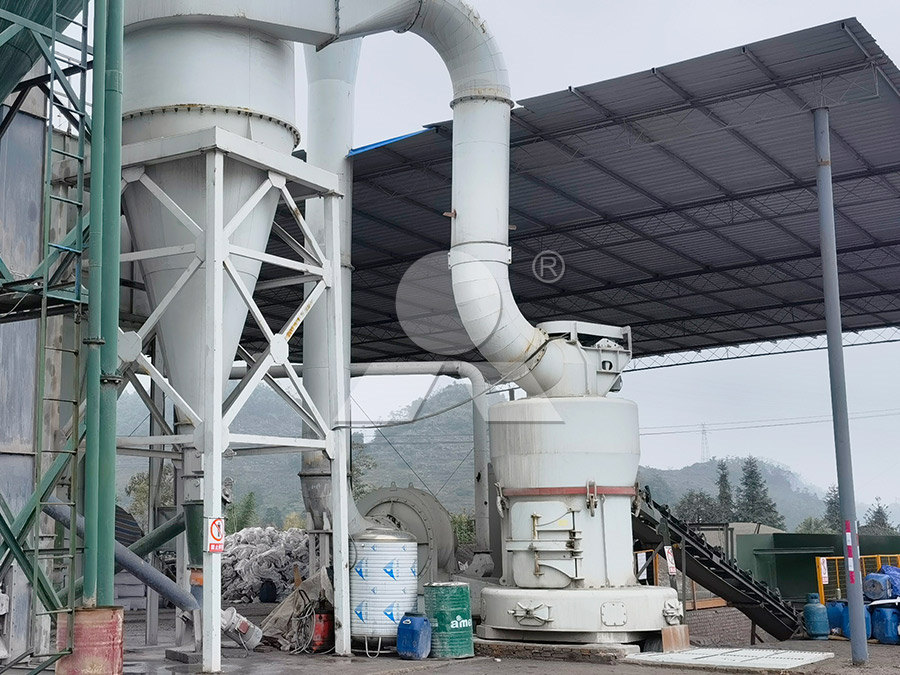
Schematic diagram of the drive system allowing the use of a fluid
Schematic diagram of the drive system allowing the use of a fluid coupling for mill startup: 1asynchronous motor 630 kW 1000 RPM, 2fluid coupling, 3gearbox, 4ball millProduct introduction:YGM high pressure micro powder mill is referred to as micro powder mill or super fine grinding millThe high pressure micro grinder is mainly used for the ultrafine powder processing of more than 500 kinds of materials such as feldspar talc barite marble limestone carbon black and clayYGM High Pressure Grinding MillVanguard MachineryFind your roller mill easily amongst the 185 products from the leading brands (WAMGROUP, Brabender, LONGI, providing users with energysaving, consumptionreducing, qualityenhancing and efficiencyenhancing solutions, roller horizontal for ore highpressure grinding mill WGM series Output: 30 t/h 7,400 t/h Motor power: 45 kW Roller mill, Roller grinding mill All industrial manufacturers3RollerPressFlSmidthpdf Free download as PDF File (pdf), Text File (txt) or read online for free The document discusses the layout and calculations for a roller press used in comminution processes It describes the 3 Roller Press FL Smidth PDF PDF Mill (Grinding)
.jpg)
Energy Efficiency Analysis of Copper Ore Ball Mill Drive Systems
Figure 5 Startup of the LSPMSM SMH1732T motor with a filled ball mill after two hours of downtime: (a) active power, (b) current intensity, (c) voltage "Energy Efficiency Analysis of Copper Ore Ball Mill Drive Systems"2022年1月23日 This work concentrates on the energy consumption and grinding energy efficiency of a laboratory vertical roller mill (VRM) under various operating parametersAnalysis and Optimization of Grinding Performance of Vertical Roller 2022年3月1日 High Pressure Grinding Rolls (HPGR) circuits have the potential to reduce the Mining Industry’s CO2 emissions by up to 345 megatonnes/year, or 435% when compared to the established Autogenous Helping to reduce mining industry carbon emissions: A stepby Closed mill housing pressureshock proof up to 35 bar: 3: Mill drive: up to 2,000 kW: Number of grinding rollers: 3: Feed size: up to 100 mm: Feed moisture: MPS 180 GC vertical roller mill for the grinding, drying and calcining of gypsum, Knauf Knin, CroatiaCoal mill, gypsum mill, clay mill, etc Pfeiffer MPS mills
.jpg)
(PDF) THE PERFORMANCE OF THE HIGH PRESSURE ROLL MILL
1998年1月1日 The high pressure roll mill, HPRM, a newly invented size reduction equipment, has been recently added to the list of comminution machines and is classified as a highly efficient equipment2013年7月15日 The energy saving resulting from the replacement of cyclones with screens in a closed ball mill circuit was estimated to be in the range of 10 to 25% (Jankovic and Valery, 2012a) An analysis of the(PDF) Energy Efficient Ball Mill Circuit – Equipment Sizing 2009年5月1日 Ball mills in HPGRBall mill circuits tend to have more installed capacity than their counterparts in AG/SAGBall mill circuits This is because the product size distribution from AG/SAG mills Predicting the overall specific energy requirement of crushing, 2019年8月1日 Furthermore, all deposits mentioned above are located in arid regions, which restricts the application of wet processing methods An option to simultaneously limit overgrinding and save water INVESTIGATION ON FLOTATION BEHAVIOR OF A COPPER SULFIDE ORE
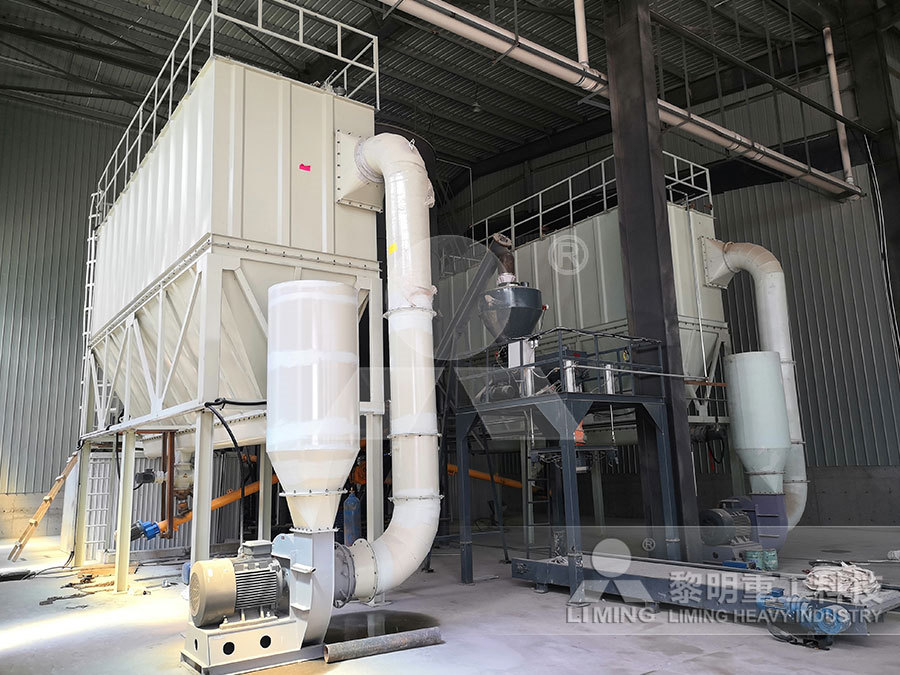
Grinding Mills — Types, Working Principle
2018年8月17日 Stage 1 — Drilling This is the stage where it all begins A rock cutting process, drilling sets the stage for the next steps in the mineral processing operation2014年10月1日 In a test performed in the Loesche test center in Germany, copper slag grinding saved 229% energy in an airswept model and 344% energy in an overflow model [13,14]Copper Ore Grinding in a Mobile Vertical Roller Mill Pilot PlantEnergy savings may also be found in the ball mill drive systems In the scale of a processing plant, the electric motors of these drive systems account for 95% of the totalEnergy Efficiency Analysis of Copper Ore Ball Mill Drive SystemsSession 11 Optimisation of Roller Press System Free download as PDF File (pdf), Text File (txt) or view presentation slides online This document discusses roller presses, which are compaction tools used primarily as pregrinders in cement production to increase grinding capacity Key points: Roller presses apply high pressure to compact and crack raw materials, Session 11 Optimisation of Roller Press System PDF Mill (Grinding
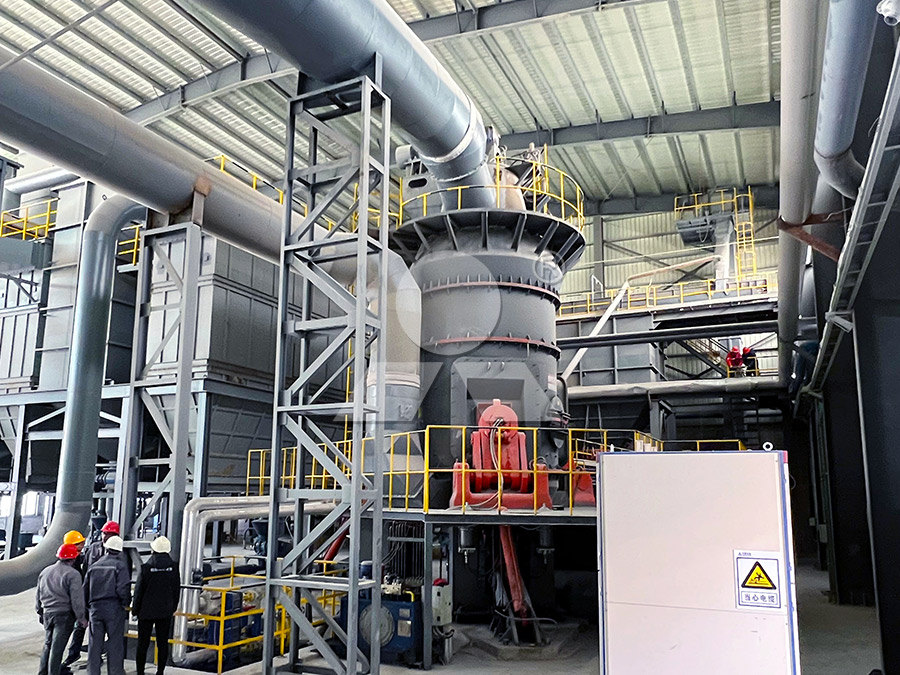
Series PGM Single Driving High Pressure Roller Mill
HPGM series high pressure grinding roll is a new type of energysaving grinding equipment designed by the principle of highpressure material layer pulverization It consists of two squeezing rolls that rotate synchronously at a low speed One is a stationary roll and the other is a movable roll, which are both driven by a highpower motor2016年7月14日 HPGR test results published by Grier (1992) on gold ores from the Mt Todd project showed significant energy savings for a HPGR/Ball Mill circuit as compared to a SAG/Ball Mill plant By adding a Polycom highpressure grinding roll, the throughput of existing plants can be increased by as much as 150% while simultaneously reducing the power consumption by HPGR 911Metallurgist4 Intelligent operation and protection features Drive system for high pressure grinding rolls Drive system for high pressure grinding rolls Intelligent operation and protection features 5 Intelligent operation and protection features Ensuring increased roller life and productivity To leverage the benefits of using HPGRs in comminutionDrive system for high pressure grinding rolls Increased rollerMarcelo Perrucci, Global Product Line Manager Grinding “Installing GMDs potentially means using less onsite mechanical equipment, and thus a reduced footprint in terms of mechanical space It is a more efficient technology in terms of energy How digitalized gearless drive technology results in energy savings
.jpg)
High Pressure Grinding Roll and Magnetic Separation for Energy Saving
after the thirdstage ne crushing operation to reduce the particle size of ball mill feed and improve the processing capacity of grinding operation The optimal process parameters of high pressure grinding roll and magnetic separation were determined to be a 10 mm of roller surface spacing, a 105 Mpa of roller surface pressure, a 14 r/min of Energy Saving Mining Processing Equipment Grinding Ball Mill HZE manufacture standard wet ball mills with high efficiency, low energy consumption, stability and reliability for grinding minerals of precious metals, base metals and nonmetal It can also be specially designed and customized according to the special requirements of the customersEnergy Saving Mining Processing Equipment Grinding Ball Mill