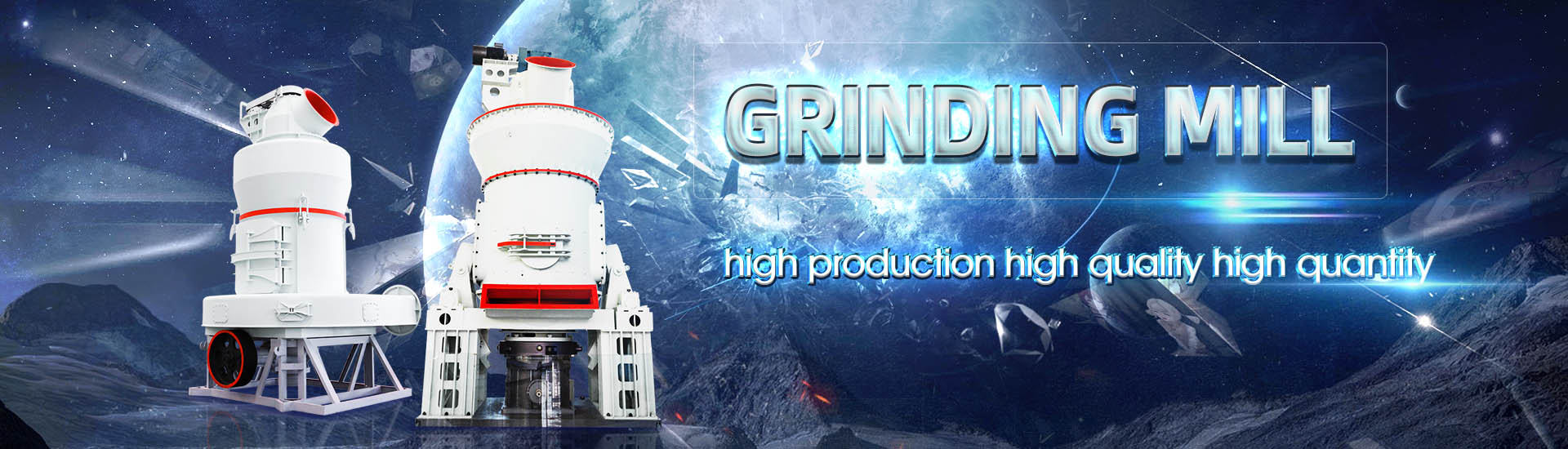
Cement plant raw material vertical mill maintenance
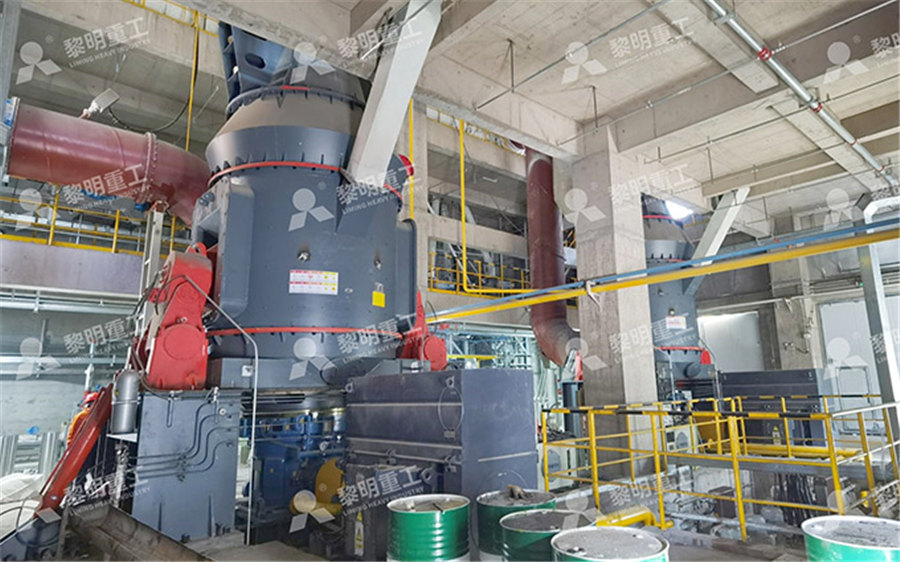
Vertical roller mill for raw Application p rocess materials
Vertical roller mills are adopted in 20 cement plants (44 mills) in Japan In the vertical roller mill which is widely used in the raw material grinding process, raw materials input grinding table 2020年5月30日 To find out the frequency of damage to the machine or the time interval between damage to the tool (MTBF) and the length of time used to repair the tool (MTTR), the Total Analysis of Raw Mill Machines Maintenance in Cement IndustryFor raw materials and cement clinker, the vertical roller mill is an excellent grinding solution because of the relatively lower cost of installation, ease of operation and maintenance, energy efficiency and product quality Further, our Vertical roller mills FLSmidth Cementraw materials, burning, grinding and quality control are supported by a range of chapters addressing critial topics such as maintenance and plant reporting, alongside a detailed The Cement Plant Operations Handbook International Cement
.jpg)
Review on vertical roller mill in cement industry its performance
2021年1月1日 Raw mix, high grade limestone, sand and iron ore are transported from their bins to raw mills for drying and further fine grinding The raw mill is either a Ball mill with two cement manufacture – 3 Portland cement in today’s world 2 Raw materials management system – 22 Concrete problems 16 1 Raw materials – 2 Raw mix – 3 Reserves – 4 Crushing – 5 Drying – 6 Preblending – 7 Storage and handling 3 Raw milling and blending 3 Computerised Maintenance Management Systems 30 1 Raw milling The Cement Plant Operations Handbook International Cement Cement Raw Vertical Mill Area Maintenance Dam Ring There is high wear and deformation in the dam ring segments new dam ring segments worn out and deformed dam rings segments 1 There is no expansion joint which Cement Raw Vertical Mill Area MaintenanceFig2 Schematic process flow of vertical roller mill for grinding of raw materials Vertical roller mills are adopted in 20 cement plants (44 mills) in Japan Results Table Energy saving effect of the vertical roller mill Ball mill Specific power Cost estimationVertical roller mill for raw Application p rocess materials
.jpg)
Raw milling and blending INFINITY FOR CEMENT EQUIPMENT
The main difference to cement mill operation is the need to dry rawfeed and assure transport of stightly moist materialwithin a mill Also, many raw materials are softer than clinker, and operations must avoid coarse residues in kiln feed that are difficult to combine in the kiln and would result in high clinkerfreelime, and/or excessive Cement Industry One of the primary applications of VRMs is in the cement industry, where they are used to grind raw materials and clinker to produce cement The VRM technology has significantly improved the efficiency and productivity of the cement manufacturing processVertical Roller Mill in Cement Plant ball mills supplierFLSmidth Cement flsmidthcement 3 OK™ Raw Mill QUALITY AND PROFITIMPROVING FEATURES Vertical Roller Mills (VRMs) have been the standard option for raw materials grinding in the cement industry for several decades FLSmidth Cement has supplied the global cement industry with leading VRM designs for allOK RAW AND CEMENT MILL2021年1月1日 Stacking Reclaiming of Raw material: Swing type stacker Reclaimer: Limestone other raw material are stored in open area into a longitudinal storage unit called stockpile through Stacker These are then extracted transversely from the stockpile through reclaimer: 3: Raw Meal Grinding Homogenization: Grinding Mill Vertical Roller Mill Review on vertical roller mill in cement industry its

VRM In Cement Plant Maximize Energy Saving CNBMSINOMA
Vertical roller mill manufacturers Vertical roller mill or VRM is a largescale grinding equipment designed for pulverizing cement raw meal, cement clinker, slag, coal, fly ash, limestone, and other hard grinding materialIt integrates grinding, drying, separation, and conveying in one machine The equipment is widely used in many industries such as cement, electric power, metallurgy The power consumption of raw material vertical mill system is 97Kwh/t lower than ball mill, that is to say: in one year, a 5000TPD cement plant can save energy in clinker grinding system: 97kWh/t * 5000t/d * 300d=14,550,000 kWh, that means the cement plant clinker grinding system can save 14,550,000 kWh electricity one yearVertical Raw Mill CHAENGfor Cement Plant Application Raw Material Cement Slag amcl Coal released easily, resulting in maintenance to be performed efficiently Vertical Roller Mill 1 Rotary Lock 2 Separator 3 Chute 4 Roller 5 Swing Lever 6 Table 7VERTICAL ROLLER MILLS AMCLFor drying the wet raw material it is necessary that prior to the mill start up the grinding plant isheated for some timeOtherwise the cold grinding plant would take away too much heat from the drying process and the finish product would PROCESS TRAINING for operators of Vertical RAW Mills
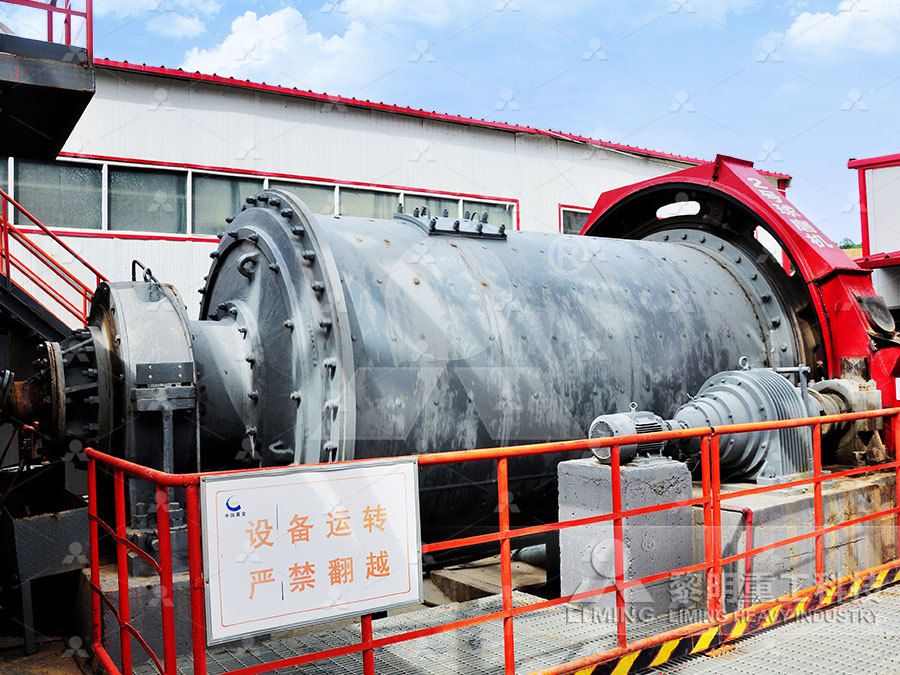
Raw mills for all requirements Gebr Pfeiffer
The cement raw material mixtures are ground, dried, and classified in the Pfeiffer vertical roller mill For drying the material, hot gases are directed into the mill Product fineness can be adjusted within a wide range (0063 to 02 mm)2023年7月4日 A cement vertical roller mill (VRM) is a type of grinding equipment commonly used in cement plants for raw material grinding and cement grinding It is an energyefficient alternative to traditional ball mills, as it utilizes rollers to Vertical Roller Mill in Cement Manufacturing PlantMombasa Cement Ltd ordered a QMK² 24/12 with three roller units for the 5,000 tons per day kiln line In addition, the raw material grinding process will be supported by a QMR² 48/24 For the 4,000 tons per day kiln line Shiva Cement Ltd contracted a quadropol® vertical roller mill for grinding pet coke with a QMK² 32/16quadropol® thyssenkrupp Polysius Grinding TechnologiesVertical mill merges fine crushing, drying, grinding and powder selecting into a single, which simplifies the production process It has the advantages of high grinding efficiency, low power consumption, large feed particle size, easy adjustment of grinding fineness, simple process, less land occupation, low noise, simple operation and maintenance, low cost and less wear Vertical Mill In Cement Plant Cement Vertical Mill AGICO Cement
.jpg)
Ball Mill, Vertical Roller Mill Cement Plant
2020年11月5日 Vertical roller mill Vertical roller mill, also called cement vertical mill, it grinds raw materials by the movement between grinding roller, millstone and grinding device In general the grinding efficiency of vertical roller mill is 80% as much power as cement ball mill, reduce about 30% power consumptionFor raw materials and cement clinker, the vertical roller mill is an excellent grinding solution because of the relatively lower cost of installation, ease of operation and maintenance, energy efficiency and product quality Further, our vertical roller mill solution for cement grinding has an ability to dry, grind and separate within a single Vertical roller mills FLSmidth CementApplication of Vertical Roller Mill in Cement Industry Vertical roller mill (VRM) technology has become an integral part of the cement industry, offering several advantages over traditional grinding mills Today, this type of grinding machine is becoming more and more popular in both the raw material grinding process and the cement grinding Application of Vertical Roller Mill in Cement Production2020年5月30日 In this study, the engine studied was the Raw Mill machine at plant The raw mill machine functions as a main material grinder in the initial milling process such as limestone, silica stone, clay Analysis of Raw Mill Machines Maintenance in Cement Industry
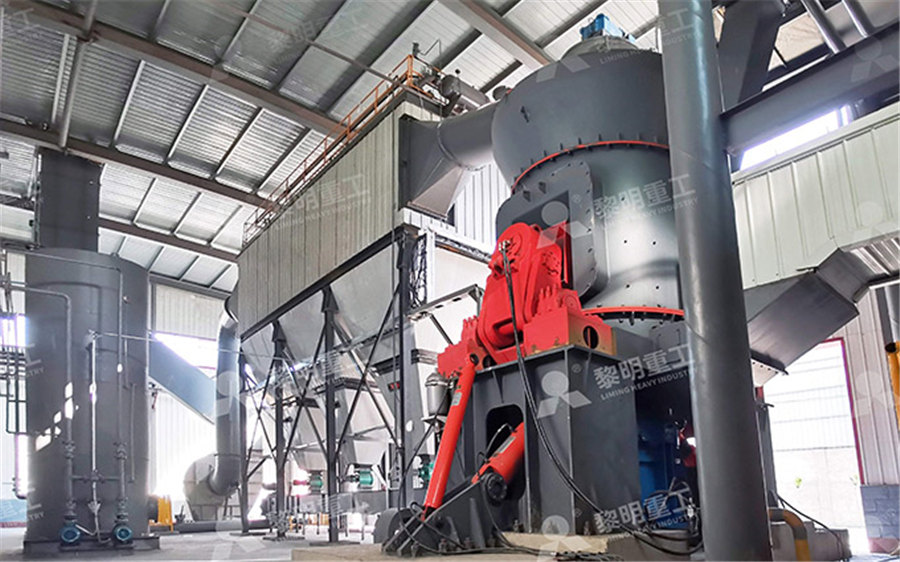
Raw Material Preparation in Cement Manufacturing Plant AGICO
The energy consumption of tube mill system is relatively high, which is about 2150 kWh/t, while the dry process cement production line usually uses vertical mill to prepare raw material, because its power consumption is l650 kWh/t, which is much lower than that of tube millThe vertical cement mill is largescale cement grinding machine With advantages of energyefficient and stable quality, vertical roller mill is widely applied to many industries, such as cement, power, metallurgy, chemical and nonmetallic Vertical Cement Mill2024年3月4日 Optimisation of Pfeiffer raw mill for cement plant Grindability of Raw Material •Grinding Fineness •Classifier Design •Grinding Bed Height / Variations •Dam Ring Height •Air Flow •Temperature Level •Maintenance Optimisation of Pfeiffer raw mill for cement plant2020年3月13日 The cement vertical mill can quickly grind different raw materials into the required the cement vertical mill has a low maintenance cost, the direct contact between abrasive parts is low, the damage rate is low, the wear life of Why Choose Cement Vertical Mill?
.jpg)
Cement Industry Loesche
The roller grinding mill technology, patented in 1928 and continuously developed since then, has become synonymous with Loesche‘s pioneering engineering knowhow CEMENT BLAST FURNACE SLAG CEMENT RAW MATERIAL7 // Almost any plant for the grinding of cement raw material is a combination of machines specially adapted to the particular physical properties of the material to be ground As a result, our plants work efficiently without any trouble » Highly efficient grinding, drying, and separating in one unit » Outstanding production capacities exceeding 1,400 t/h in one single millPFEIFFER MILLS FOR THE CEMENT INDUSTRYWhat Is Cement Vertical Mill The cement vertical mill is a type of grinding equipment that merges fine crushing, drying, grinding, and powder separating into a single, which simplifies the production process and has many irreplaceable advantages, such as high grinding efficiency, large feeding size, low power consumption (2030% less power than a cement ball mill), large Cement Vertical Mill Vertical Grinding Mill Vertical MillRaw Mill; Kiln System; Cooler; Clinker Storage; Cement Mill; Packing and Dispatch; Auxiliary Equipment; Detailed Cost Breakdown 1 Raw Material Extraction and Transportation This stage involves the extraction of raw materials like limestone, clay, and sand, and their transportation to the cement plant Equipment: Excavators, dump trucks, and The Comprehensive Guide to Cement Plant Costs: An InDepth
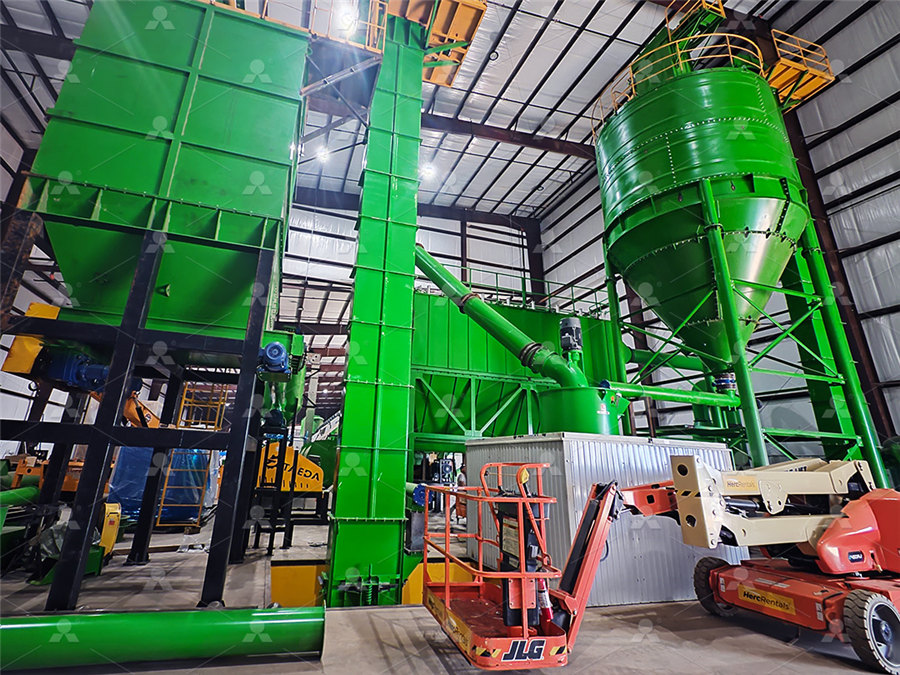
Vertical Roller Mills LNV TECHNOLOGY
Vertical Raw Mill: A vertical raw mill is mainly used in cement plants for raw material grinding Simple process flow, providing for drying, grinding and classifying all in one equipment; Minimum floor space requirement, compact layout and low investment in civil works; High grinding efficiency, low energy consumption and low wear on metal partsPrevious Post Next Post Contents1 Select your Favorite Type of 7 Different types of Vertical Mill11 1 Fuller 12 2 FLSmidth (atox Ok)13 3 Loesche GmbH LM (VRM)14 4 Gebr Pfeiffer MPS (VRM)15 5 thyssenkrupp Polysuis ( RDRM)16 6UBE Japanese vertical mill17 7 (CNBM ) Chinese vertical mill Select your Favorite Type of 7 Different types of Select your Favorite Type of 7 Different types of Vertical MillBulk material handling is a major activity and bins for raw materials, intermediate products and finished cement must reliably provide controlled flows of materials upon demand The tonnages of material to be stored at various process stages are outlined by Deolalkar in Chapter 13 of his book (Deolalkar,2009), while his Chapter 16 discusses the features of materials handlingsystemsCement Plant Raw materials INFINITY FOR CEMENT EQUIPMENTcement manufacture – 3 Portland cement in today’s world 2 Raw materials management system – 22 Concrete problems 16 1 Raw materials – 2 Raw mix – 3 Reserves – 4 Crushing – 5 Drying – 6 Preblending – 7 Storage and handling 3 Raw milling and blending 3 Computerised Maintenance Management Systems 30 1 Raw milling The Cement Plant Operations Handbook International Cement
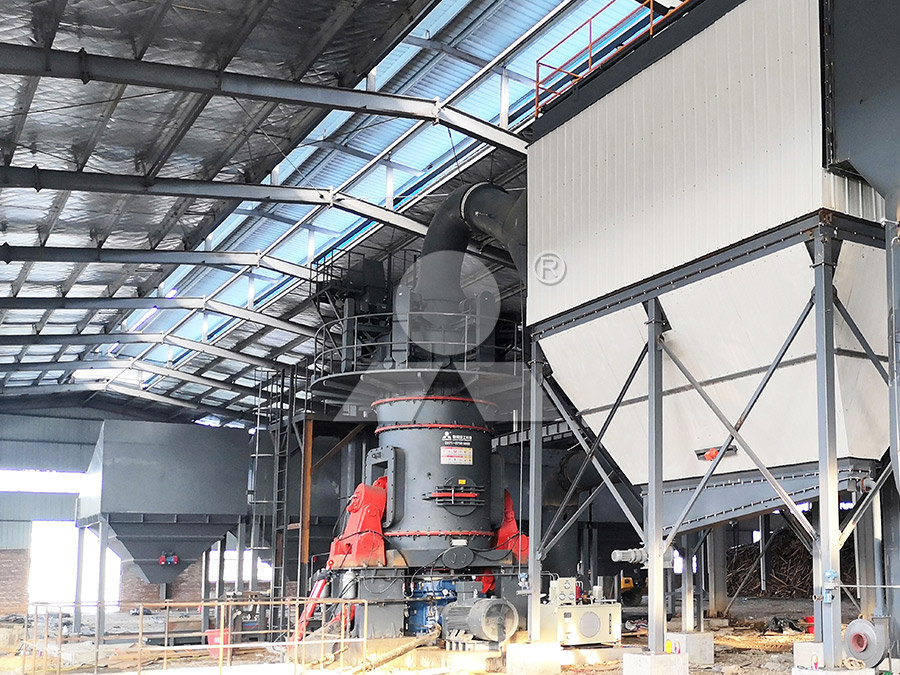
Cement Raw Vertical Mill Area Maintenance
Cement Raw Vertical Mill Area Maintenance Dam Ring There is high wear and deformation in the dam ring segments new dam ring segments worn out and deformed dam rings segments 1 There is no expansion joint which Fig2 Schematic process flow of vertical roller mill for grinding of raw materials Vertical roller mills are adopted in 20 cement plants (44 mills) in Japan Results Table Energy saving effect of the vertical roller mill Ball mill Specific power Cost estimationVertical roller mill for raw Application p rocess materialsThe main difference to cement mill operation is the need to dry rawfeed and assure transport of stightly moist materialwithin a mill Also, many raw materials are softer than clinker, and operations must avoid coarse residues in kiln feed that are difficult to combine in the kiln and would result in high clinkerfreelime, and/or excessive Raw milling and blending INFINITY FOR CEMENT EQUIPMENTCement Industry One of the primary applications of VRMs is in the cement industry, where they are used to grind raw materials and clinker to produce cement The VRM technology has significantly improved the efficiency and productivity of the cement manufacturing processVertical Roller Mill in Cement Plant ball mills supplier
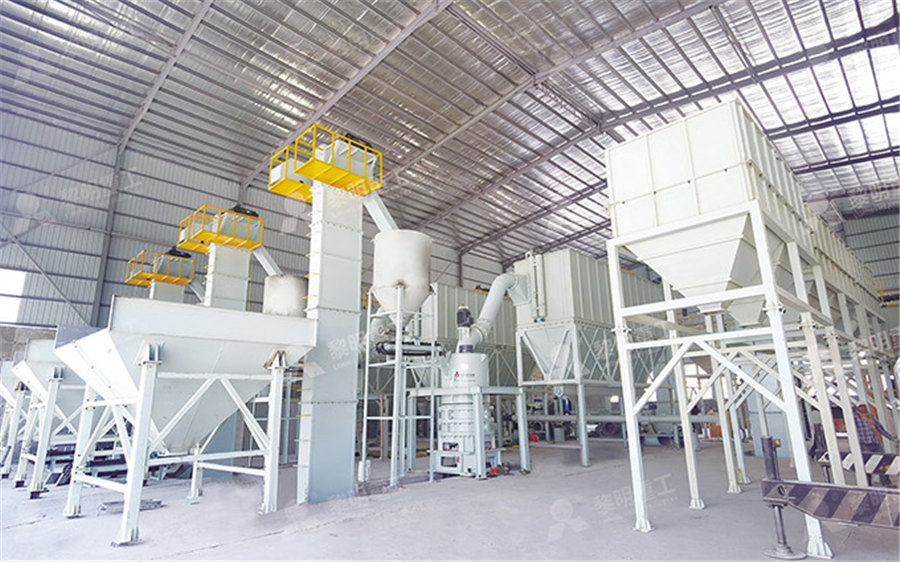
OK RAW AND CEMENT MILL
FLSmidth Cement flsmidthcement 3 OK™ Raw Mill QUALITY AND PROFITIMPROVING FEATURES Vertical Roller Mills (VRMs) have been the standard option for raw materials grinding in the cement industry for several decades FLSmidth Cement has supplied the global cement industry with leading VRM designs for all2021年1月1日 Stacking Reclaiming of Raw material: Swing type stacker Reclaimer: Limestone other raw material are stored in open area into a longitudinal storage unit called stockpile through Stacker These are then extracted transversely from the stockpile through reclaimer: 3: Raw Meal Grinding Homogenization: Grinding Mill Vertical Roller Mill Review on vertical roller mill in cement industry its Vertical roller mill manufacturers Vertical roller mill or VRM is a largescale grinding equipment designed for pulverizing cement raw meal, cement clinker, slag, coal, fly ash, limestone, and other hard grinding materialIt integrates grinding, drying, separation, and conveying in one machine The equipment is widely used in many industries such as cement, electric power, metallurgy VRM In Cement Plant Maximize Energy Saving CNBMSINOMAThe power consumption of raw material vertical mill system is 97Kwh/t lower than ball mill, that is to say: in one year, a 5000TPD cement plant can save energy in clinker grinding system: 97kWh/t * 5000t/d * 300d=14,550,000 kWh, that means the cement plant clinker grinding system can save 14,550,000 kWh electricity one yearVertical Raw Mill CHAENG
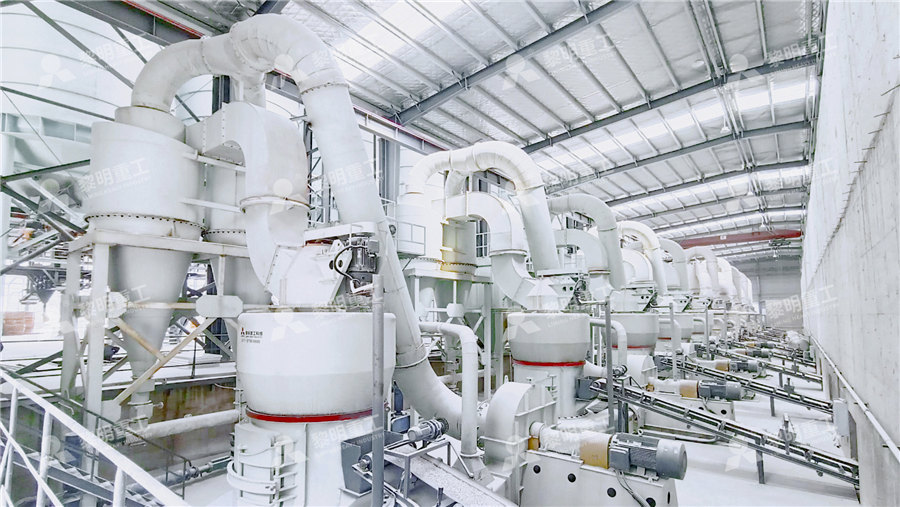
VERTICAL ROLLER MILLS AMCL
for Cement Plant Application Raw Material Cement Slag amcl Coal released easily, resulting in maintenance to be performed efficiently Vertical Roller Mill 1 Rotary Lock 2 Separator 3 Chute 4 Roller 5 Swing Lever 6 Table 7