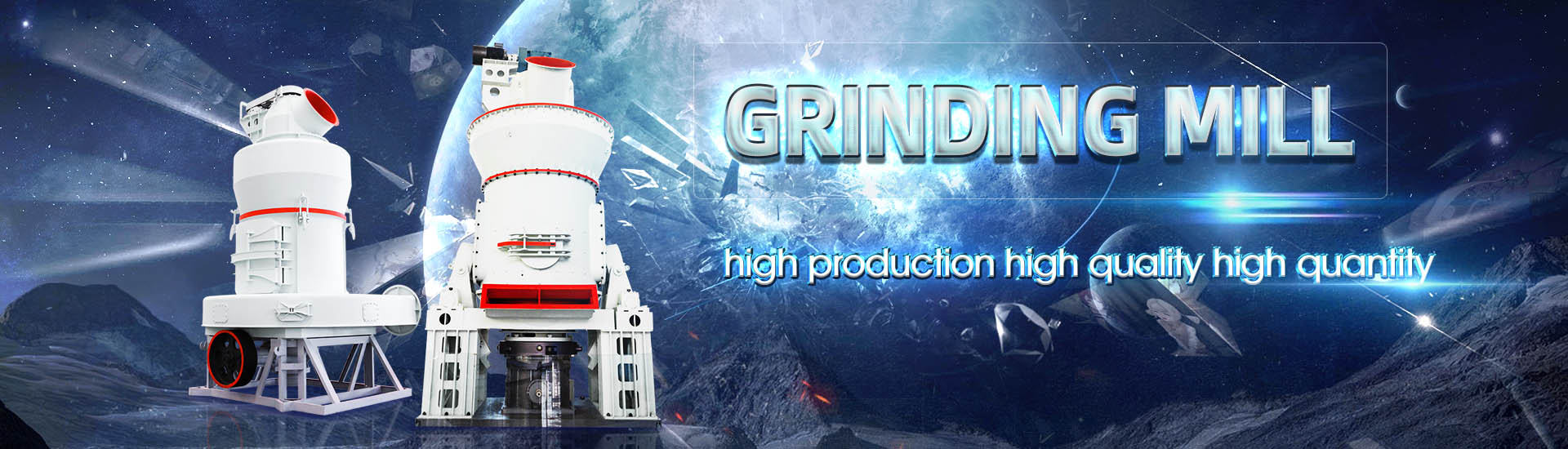
Operation process of slag yard
.jpg)
Working process of slag yard Download Scientific
Download scientific diagram Working process of slag yard from publication: Risk Factors of Vapor Explosion of Molten Slag in Slag Yard for Steelworks Explosions and Nebulizers and Vaporizers2008年8月1日 In this article, the authors review the scientific studies dedicated to the hot stage of slag processing in order to show that the slag recycling potential can be enhanced by (a) Hot stage processing of metallurgical slags ScienceDirect2019年12月9日 Traditionally, metallurgical slags have been air cooled in slag pots or large yards Slag pot cooling is a slow process thus allowing crystallisation of various mineral Granulation and Heat Recovery from Metallurgical SlagsA slag yard consists of a large pit into which the slag is poured by tilting a slagpot at one end The hot slag will flow from one end to the other (Fig 1) Typically, a layer covers most of the yard A Quantitative Model for Slag Yard Cooling JSTAGE
.jpg)
Risk Factors of Vapor Explosion of Molten Slag in Slag Yard for
slag was a controlled to visualize its environment, relationship the chain coolants such as of coolant, factory fresh water and general tap water to investigate spontaneous explosion Slag generated from basic oxygen furnace (BOF) or LinzDonawitz (LD) converter is one of the recyclable wastes in integrated steel plants This paper deals with the present and possible use of LDFlowchart of slag production in a modern steel plantScrap type (HMS, shredded, Home return, bushlings, etc) Scrap origin ( Supplier, country, etc) Target slag composition: (B2: 18, B3: 15, MgO > 12%) Fluxing additions : Burnt lime “Optimization and Modelling of Slag Composition for2004年5月14日 Steel slag is a byproduct from either the conversion of iron to steel in a basic oxygen furnace, or the melting of scrap to make steel in an electric arc furnace This paper Steel Slag—Its Production, Processing, Characteristics, and
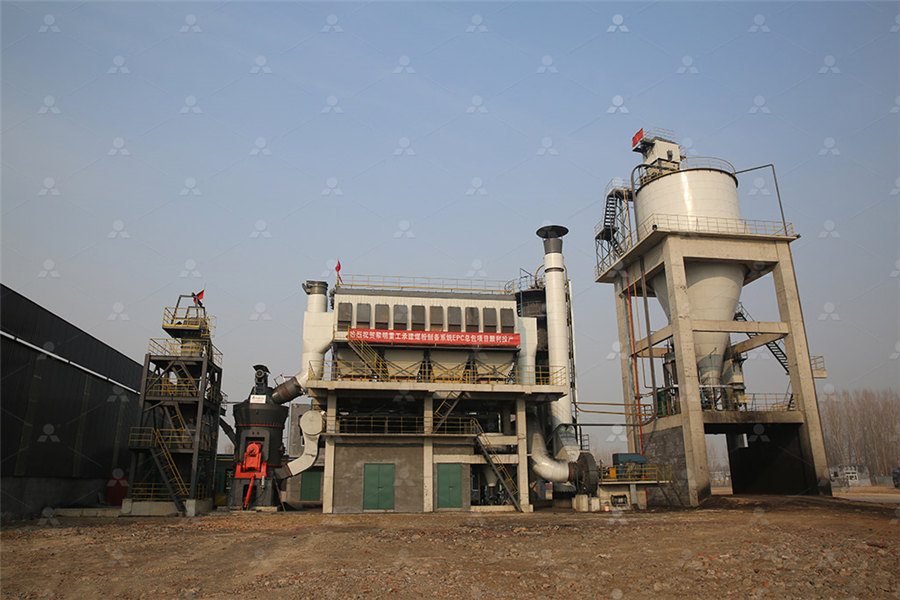
Measures for Operation, Maintenance and Management of Slag
This paper introduces the systematic and standardized management of engineering slag materials from excavation to stacking in the excavation II slag yard of Lianghekou hydropower station, 2005年2月1日 Steelmaking slag, an important metallurgical byproduct, is composed of a large amount of valuable components, including CaO, Fe t O, MnO, and MgO, all of which are required in the steelmaking (PDF) Industrial uses of slag The use and reuse of 2019年12月9日 Metallurgical slags are produced at a massive rate of over 750 Mt/year, and carry a thermal energy equivalent to 40 Mt/year of coal The potential mineral and thermal energy values of slags are in the order of $22 b and $3–6 b per year Such attractive figures, together with tightening legislation on disposal of slag and the carbon footprint associated with the loss Granulation and Heat Recovery from Metallurgical Slags2008年8月1日 To avoid landfill costs and ecological issues, the slags are usually processed into a secondary resource (Fig 1)The first step in this slag treatment is often the recovery of valuable and hazardous metals from the slag (Shen and Forssberg, 2003)The metal fraction can be recovered by mechanical and/or physical processes including crushing, grinding, magnetic Hot stage processing of metallurgical slags ScienceDirect
.jpg)
ON NEW SLAG YARD OPERATION
NEW SLAG YARD OPERATION Document No:UT3 Prepared By Date22/10/20 Approved By Steel Melting ShopI Bokaro Steel Plant PROCESS FLOW CHART OF NEW SLAG YARD Jammed or Empty pot Placement of Receipt of load pot from Conv5/Conv1 Movement of SPTC SLAG BAY Lifting position2022年6月25日 “Steel smelting is a process with many interconnected components And if one of them does not work, it will affect the others Without a slag yard and its efficient operation, steel smelting is impossible Therefore, the good news for the converter shop was the end of the reconstruction of the slag yard №1”, the message readsArcelorMittal has completed the reconstruction of the slag yard №1Let us first examine the aircooling process at a slag yard at a macroscopic level The high temperature slag is poured from a slag pot onto a previous slag bed in consecutive layers of several centimetres (Figure 2) Due to the steep temperature gradient between the slag and the surrounding air atmosphere, heat is extracted from the slagANALYSIS OF THE AIRCOOLING PROCESS OF BASIC SLAGS2021年6月14日 Hightemperature molten steel slag is a large amount of industrial solid waste containing available heat energy and resources This paper introduces an efficient and comprehensive utilization process of hightemperature molten steel slag The waste heat energy in the hightemperature molten steel slag can be fully recovered through the threestage heat ThreeStage Method Energy–Mass Coupling HighEfficiency Utilization
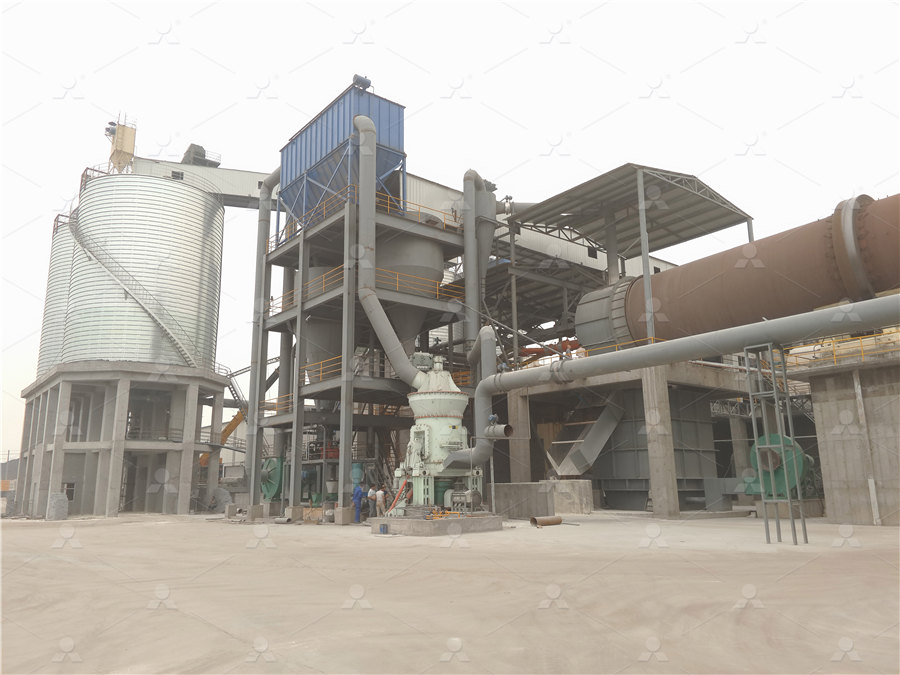
Design and Operation of Dry Slag Granulation Pilot Plant
2019年2月22日 CSIRO has been working on a dry granulation process, integrated with heat recovery, since 2002 It involves a rotary disc that atomizes molten slag to produce liquid droplets, which are rapidly quenched to become solid granules The hot granules are fed to a countercurrent moving packed bed heat exchanger, where they are further cooled and finally 2020年7月31日 The amount of copper flash smelting slag has increased during the recent years along with an increasing slagtometal ratio During slag tapping, some copper sulfide is mechanically entrained As a result, it is necessary to recover copper matte from the slag by suitable methods At present, the most common way is slow, controlled cooling in a transfer Effect of Cooling Rate and Slag Modification on the Copper Converter process for steelmaking is a rapid process and slag formation is extremely essential to ensure slag’s ie from the moment of slag/metal separation to complete cooling at the slag yard 2001) The cost of such an operation would be far lower than that of the borate additions However, the limited heat content and heat Hot stage processing of metallurgical slags AcademiaThe slag yard process consists of three phases: skimming, cooling, and loading Figure 7 shows each phase sequentially progressed for 8 hours In the skimming process, Before a loading operation, slag is mixed using heavy equipment to cool the core of the slag evenlyRisk Factors of Vapor Explosion of Molten Slag in Slag Yard for
.jpg)
Sinter Plant Operations: Raw Materials SpringerLink
2016年9月3日 Therefore, a proper treatment is required to separate ZnO and PbO before putting the cake and slurry into the sintering process 144 Slag and Slag Tailing Blast furnace slag This section will give a brief introduction to Maintaining the correct levels of stock needed in the slab yard for optimal production An innovative slab yard process for the receiving, storing and locating of the slabs Ensure slabs are identifiable and accessible at all times and can be retrieved with minimum effort Optimized layout, material flow and handlingImproving the operations of a Slab Yard through the implementation of 2019年1月1日 During converter steelmaking process, large amounts of slags are generated which take away heat and iron resources from molten bath The slagremaining operation is a kind of hot slag recycling(PDF) Effect of slagremaining operation on dephosphorization 2022年8月11日 As a site for concentrated accumulation of slag, the waste slag yard is often large Sliding can cause serious damage to nearby residents and infrastructure In order to explore the law of sliding movement of the waste slag yard, the discrete element software PFC2D was used to study the blocking efficiency of the slag blocking walls in the waste slag yard The blocking efficiency of slag blocking wall of the waste slag yard
.jpg)
PROCESS FOR CONTROLLED SLOW COOLING OF NONFERROUS
[57] ABSTRACT A process for controlled slow cooling of nonferrous smelting slags, such as copper slags, for the recovery of the nonferrous metals contained therein by subsequent crushing, milling and ?otation operations is disclosed The process comprises the steps of pouring the molten slag into a ladle, allowing the slag to slowly cool and solidify in the ladle at least to 2021年9月30日 The effect of slag composition under M’O (monoxide, M = Fe,Mg) saturation and fully liquid conditions on dephosphorization and slag foamability was evaluated in an electric arc furnace (EAF) steelmaking plant operation by considering thermodynamics and phase equilibria It was confirmed that M’O saturation slag is more favorable for higher dephosphorization than Effect of Slag Composition on Dephosphorization and Springer2020年12月24日 Frequent slag sampling and analysis is still the most common method used to investigate and improve slag operation in electric arc furnaces (EAFs) for lowalloyed carbon steelmaking(PDF) Visualization of Slag Data for Efficient Monitoring and Measures for Operation, Maintenance and Management of Slag Yard for Excavation Ⅱ of Lianghekou Hydropower Station Lili Wang Geba Group 2 nd Engineering Co, Ltd, Chengdu, Sichuan, , China Abstract This paper introduces the systematic and standardized management of engineering slag materials from excavation to stacking in theMeasures for Operation, Maintenance and Management of Slag Yard
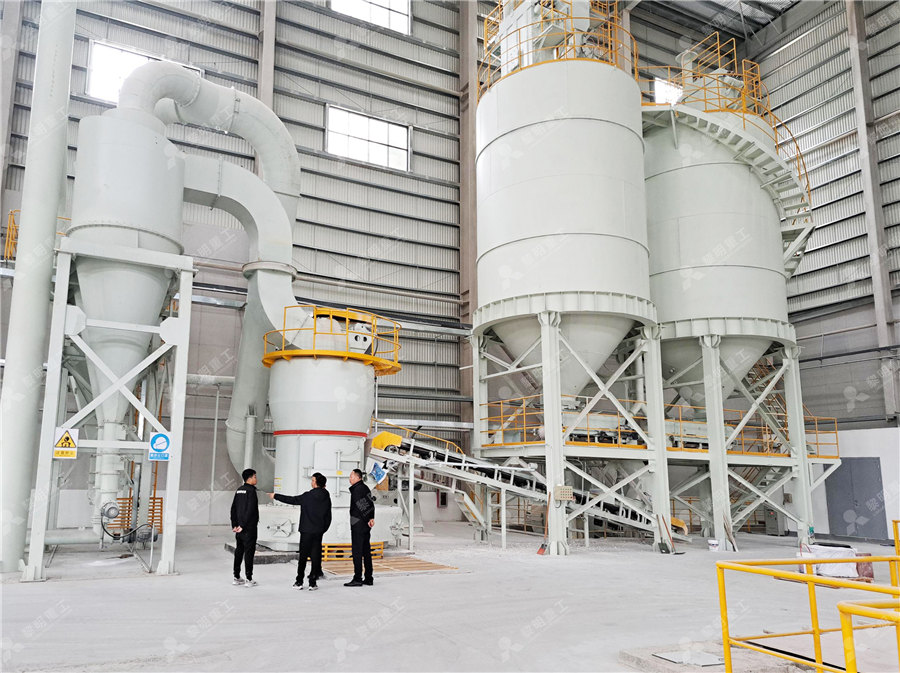
(PDF) Application of UAV and ArcGIS in Soil and Water
2019年12月17日 Taking the 1# slag yard of a hydropower station in Dadu River as an example, this paper discusses the applicability of UAV and ArcGIS technology in soil and water conservation monitoring of large 2023年2月22日 Copper smelting slag is the largest solid waste produced in coppermaking process, and slow cooling beneficiation technology is the most widely used method in recovering remaining treasures from the slag The phase transition law and element distribution behaviors of the copper smelting slag in the cooling process have significant importance, and they have The Phase Transition and Element Distribution of Copper Smelting Slag This accident occurred when a large amount of vapor generated during the process of cooling molten slag blocked the vision of a payloader driver who was passing through Yard C, as shown in Figure 1Slag yard workplace accident area Download 2012年1月1日 Basic procedure of ilmenite smelting and rational Ti slag grade in pyrometallurgical process have been summarized and analyzed The rational Ti slag grade is related to reduction degree, FeO A literature review of titanium slag metallurgical
.jpg)
Flow Properties of Entrained Flow Gasifier Fine Slag and Network
2023年8月5日 The entrained flow gasification has been identified as the most promising gasification technology Serious environmental pollution and waste of land resources are caused by the increasing amount of storage and production of coal gasification slag The aim of this work is to explore the feasibility of hightemperature combustion and melting technology for treating Steelmaking slag, or steel slag, is a byproduct from the production of steel during the conversion of hot metal to crude steel in a basic oxygen furnace, or during the melting of scrap in an EAFThe slag is generated as a melt and is a complex solution of silicates and oxides that solidify upon cooling 11 Depending on the specific steel production process, three different types of steel Steelmaking Slag an overview ScienceDirect Topics2023年4月21日 Large amounts of copper slag are produced every year and major fractions of it are currently disposed, not withstanding the multiple ways the material can be used Application of the slag is often limited by the presence of hazardous elements and their leaching behavior so they can potentially pollute soil, surface water and underground water To remove such Sustainable and Comprehensive Utilization of Copper Slag: AMaintaining the correct levels of stock needed in the slab yard for optimal production An innovative slab yard process for the receiving, storing and locating of the slabs Ensure slabs are identifiable and accessible at all times and can be retrieved with minimum effort Optimized layout, material flow and handlingImproving the operations of a Slab Yard through the
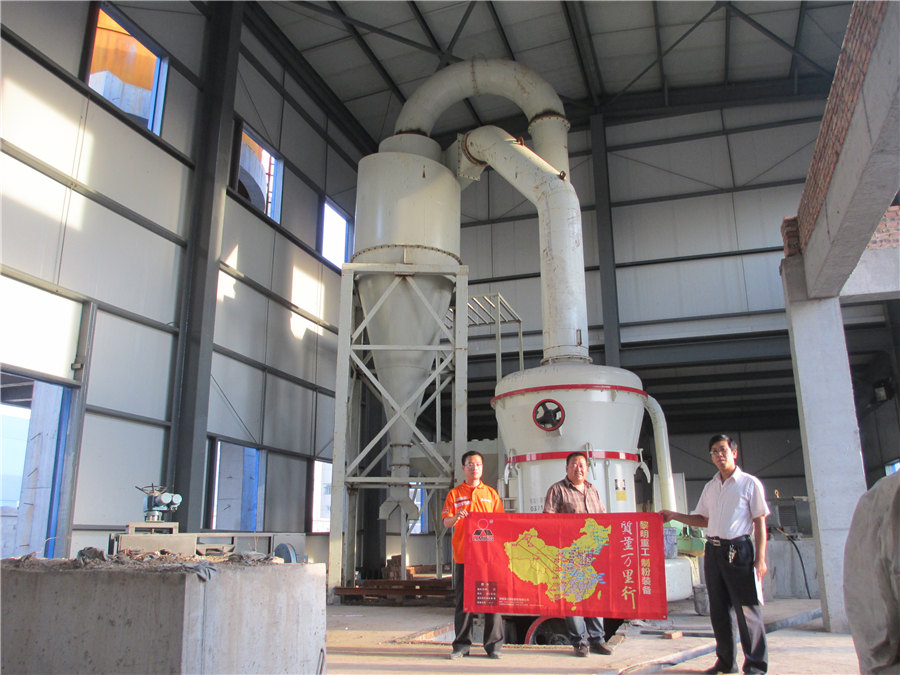
Influence of slagchanging operation during LF refining on the
2019年1月1日 The influence of refining slagchanging operation on the compositions of 82B steel and inclusions were studied on the basis of plant trials combined with thermodynamic analysis2002年7月1日 Experimental operation of a top blown BOF with 300tons heats is described in which slag samples were taken at different moments during the blowing process Two schemes oflime addition are (PDF) Analysis of Slag Foaming During the Operation of an 2020年11月29日 Decreasing the slag rate can lead to a lower fuel rate and higher productivity in the blast furnace (BF) Indian iron ore is known to have adverse alumina–silica ratio(PDF) FactSage Studies to Identify the Optimum Slag2005年2月1日 Steelmaking slag, an important metallurgical byproduct, is composed of a large amount of valuable components, including CaO, Fe t O, MnO, and MgO, all of which are required in the steelmaking (PDF) Industrial uses of slag The use and reuse of
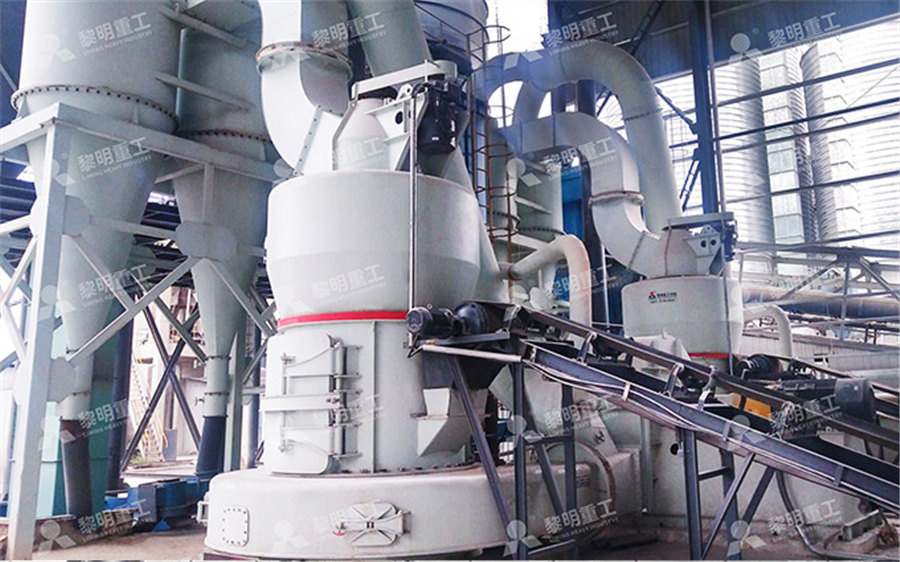
Granulation and Heat Recovery from Metallurgical Slags
2019年12月9日 Metallurgical slags are produced at a massive rate of over 750 Mt/year, and carry a thermal energy equivalent to 40 Mt/year of coal The potential mineral and thermal energy values of slags are in the order of $22 b and $3–6 b per year Such attractive figures, together with tightening legislation on disposal of slag and the carbon footprint associated with the loss 2008年8月1日 To avoid landfill costs and ecological issues, the slags are usually processed into a secondary resource (Fig 1)The first step in this slag treatment is often the recovery of valuable and hazardous metals from the slag (Shen and Forssberg, 2003)The metal fraction can be recovered by mechanical and/or physical processes including crushing, grinding, magnetic Hot stage processing of metallurgical slags ScienceDirectNEW SLAG YARD OPERATION Document No:UT3 Prepared By Date22/10/20 Approved By Steel Melting ShopI Bokaro Steel Plant PROCESS FLOW CHART OF NEW SLAG YARD Jammed or Empty pot Placement of Receipt of load pot from Conv5/Conv1 Movement of SPTC SLAG BAY Lifting positionON NEW SLAG YARD OPERATION2022年6月25日 “Steel smelting is a process with many interconnected components And if one of them does not work, it will affect the others Without a slag yard and its efficient operation, steel smelting is impossible Therefore, the good news for the converter shop was the end of the reconstruction of the slag yard №1”, the message readsArcelorMittal has completed the reconstruction of the slag yard №1
.jpg)
ANALYSIS OF THE AIRCOOLING PROCESS OF BASIC SLAGS
Let us first examine the aircooling process at a slag yard at a macroscopic level The high temperature slag is poured from a slag pot onto a previous slag bed in consecutive layers of several centimetres (Figure 2) Due to the steep temperature gradient between the slag and the surrounding air atmosphere, heat is extracted from the slag2021年6月14日 Hightemperature molten steel slag is a large amount of industrial solid waste containing available heat energy and resources This paper introduces an efficient and comprehensive utilization process of hightemperature molten steel slag The waste heat energy in the hightemperature molten steel slag can be fully recovered through the threestage heat ThreeStage Method Energy–Mass Coupling HighEfficiency Utilization 2019年2月22日 CSIRO has been working on a dry granulation process, integrated with heat recovery, since 2002 It involves a rotary disc that atomizes molten slag to produce liquid droplets, which are rapidly quenched to become solid granules The hot granules are fed to a countercurrent moving packed bed heat exchanger, where they are further cooled and finally Design and Operation of Dry Slag Granulation Pilot Plant2020年7月31日 The amount of copper flash smelting slag has increased during the recent years along with an increasing slagtometal ratio During slag tapping, some copper sulfide is mechanically entrained As a result, it is necessary to recover copper matte from the slag by suitable methods At present, the most common way is slow, controlled cooling in a transfer Effect of Cooling Rate and Slag Modification on the Copper
.jpg)
Hot stage processing of metallurgical slags Academia
Converter process for steelmaking is a rapid process and slag formation is extremely essential to ensure slag’s ie from the moment of slag/metal separation to complete cooling at the slag yard 2001) The cost of such an operation would be far lower than that of the borate additions However, the limited heat content and heat