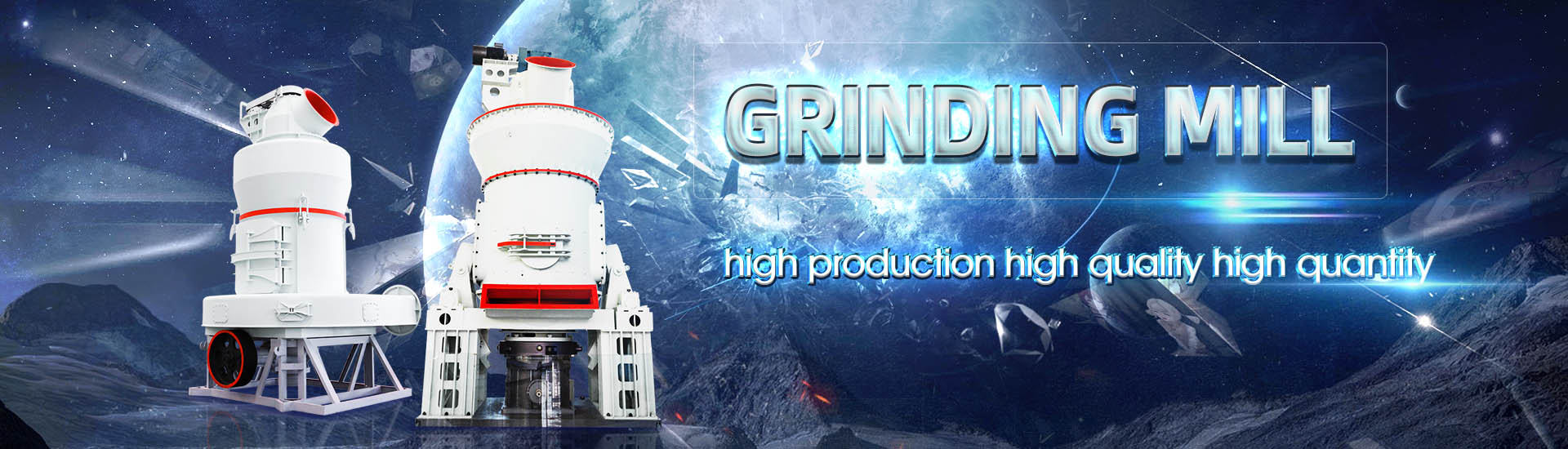
Production of reduced iron oxide process equipment
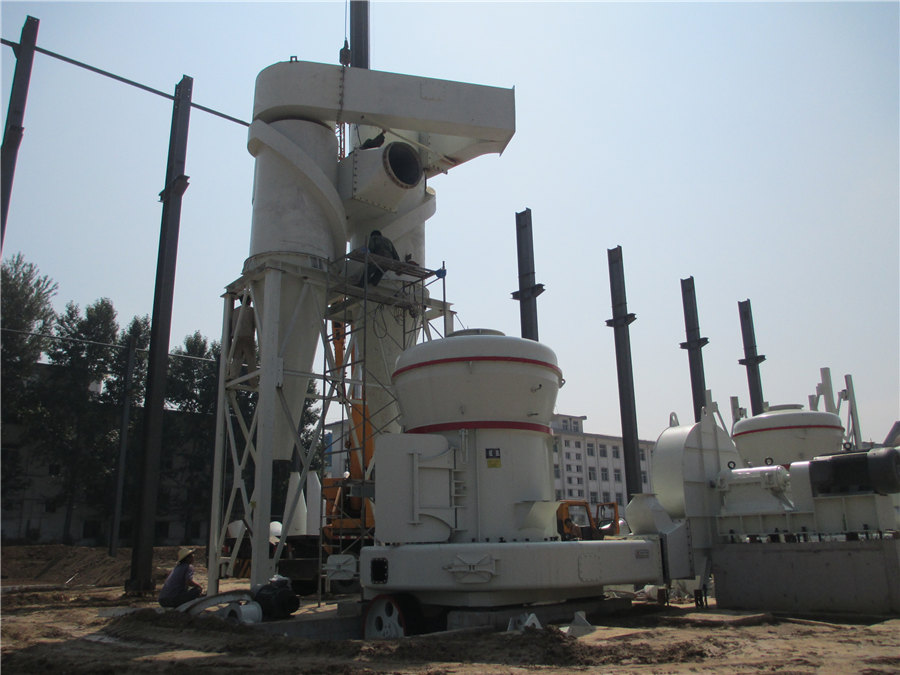
ENERGYEFFICIENT TECHNOLOGY OPTIONS FOR DIRECT
Direct reduction of iron (DRI) forms an important subsector of the Indian steel sector, accounting for about 33% of the total steel production, which is about 3415 million tonne of steel produced in2024年8月28日 Among hydrogen metallurgical approaches, the hydrogenbased direct reduction iron (HDRI) process stands out for its substantial carbon reduction capabilities and established technological maturity The present Development and Application of HydrogenBased 2016年3月30日 During the last four decades, a new route of ironmaking has rapidly developed for direct reduction (DR) of iron ore to metallic iron by using (PDF) i) Direct Reduced Iron: Production ResearchGate2023年9月1日 In this study, mill scale waste produced in steel companies was recycled into spheroidal high metallization reduced iron that can be used as a feed stock in the iron and Production of reduced iron from mill scale waste using tilting
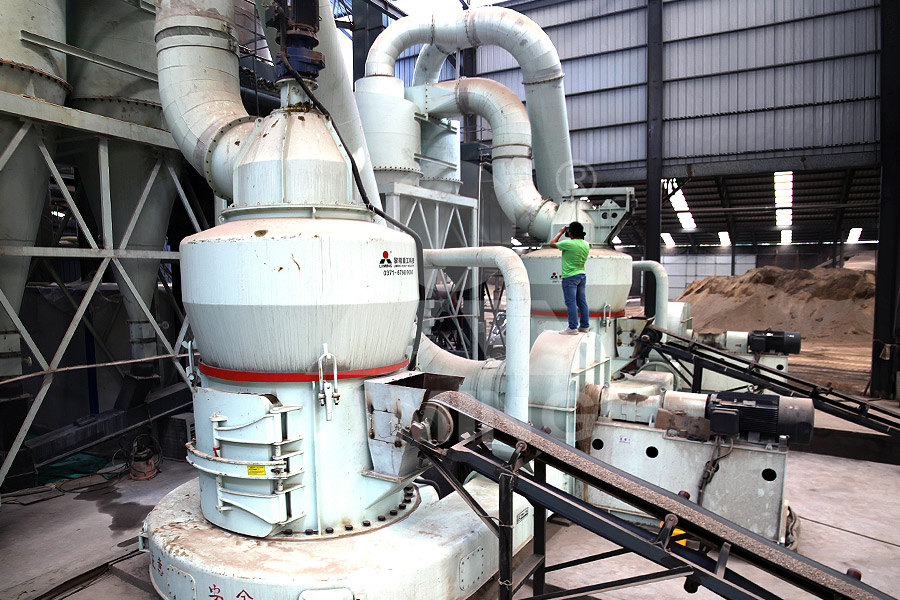
Direct reduction of iron to facilitate net zero emissions in the steel
2024年2月15日 Coalbased direct reduced iron (DRI) reduces CO 2 emissions by 38 % compared with traditional blast furnace–basic oxygen furnace (BFBOF) ironmaking Using a Iron ore is usually a mixture of iron and vast quantities of impurities such as sand and clay referred to as gangue The iron found in iron ores are found in the form of iron oxides As a result of these impurities, iron must be first separated from the gangue and then converted to pure ironIron Production Chemistry LibreTexts2024年8月7日 Synthesis of aluminium oxide: iron oxide A similar combustion process, as described above using natural urea fuel, is adopted to synthesise aluminium oxide: iron oxide nanoparticlesHighly efficient visible light active iron oxidebased 2023年9月1日 Production of reduced iron from mill scale waste using tilting rotary furnace The main equipment used in the production process was a tilting rotary furnace The outer layer of the formed spheres bonds with reduced iron, iron oxide and carbon bearing material forming a surface subjected to reducing gasesProduction of reduced iron from mill scale waste using tilting
.jpg)
Development and Application of HydrogenBased Direct Reduction Iron Process
2024年8月28日 The conventional iron and steel industry (ISI), driven by coal utilization as its predominant feedstock, constitutes a substantial source of greenhouse gas emissions Hydrogen metallurgy presents the opportunity to mitigate carbon emissions in ISI from the origin Among hydrogen metallurgical approaches, the hydrogenbased direct reduction iron (HDRI) process 2023年3月23日 Hydrogenbased direct reduced iron (H2DRI) is an alternative pathway for lowcarbon steel production Yet, the lack of established process and business models defining “green steel” make it Green steel: design and cost analysis of hydrogenbased direct iron 2024年3月20日 Electrochemical production of iron metal can support a decarbonized process for steelmaking Here, we report a lowtemperature, electrochemical cell that consumes lowcost and abundant iron oxide, salt, and water, while producing both iron and the alkaline electrolyte needed for efficient operation of the cell Coproduction of iron, lye, and chlorine leads to a process Electrochemical chloriron process for iron production from iron oxide 2019年7月19日 Direct reduced iron (DRI) is also known as sponge iron (Hasambeigi et al 2014) This high porous material has a metallization degree in the range 85–95% with a carbon content in the range 05–4% depending on the processing route During the process, the iron oxides are reduced at the solid stateDirect Reduced Iron: Most Efficient Technologies for Greenhouse
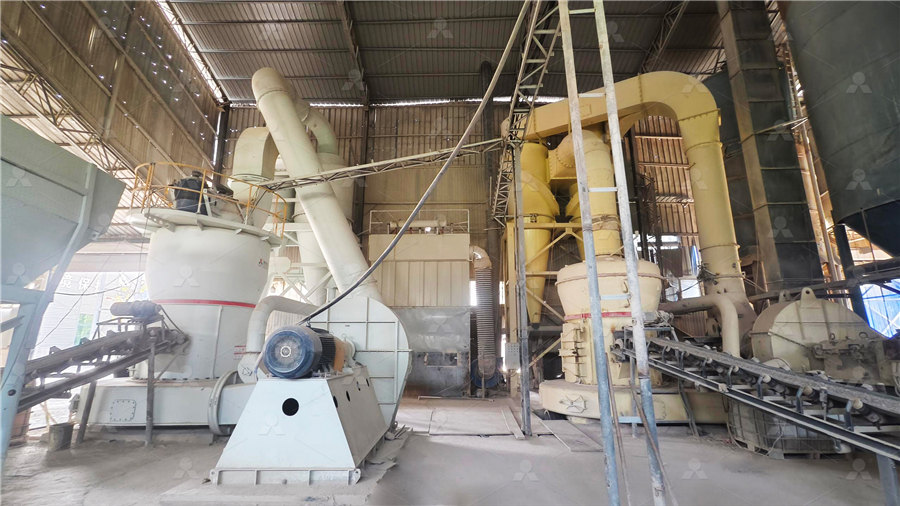
DIRECT REDUCED IRON ORE: Production ResearchGate
2023年11月10日 The common feature of all of these techniques is that the iron ore is reduced in the solid state and the product obtained iron sponge must then be melted, usually in an electric furnace, for 2024年8月5日 The transition to green steel production is pivotal for reducing global carbon emissions This study presents a comprehensive technoeconomic analysis of various green steel production methods, including hydrogen reduction and three different electrolysis techniques: aqueous hydroxide electrolysis (AHE), molten salt electrolysis, and molten oxide electrolysis Economics of Electrowinning Iron from Ore for Green Steel Production2021年1月1日 Mill Scale, generated in a rolling steel mill can be a potential material for iron powder production Mill scale is a combination of different oxides like Hematite (Fe 2 O 3), Magnetite (Fe 3 O 4), and Wustite (FeO) [2], [3]Besides, this multioxide mill scale's conversion into single oxide (Fe 2 O 3) is the bestsuited route for further reduction into iron powder due to Overview on production of reduced iron powder from mill scale 2017年10月17日 Figure 1: Steelmaking byproducts for blast furnace (BF), basic oxygen furnace (BOF) and electric arc furnace (EAF) processes Source: World Steel Association (worldsteel) The first step in the production of steel or cast From Ore to Iron with Smelting and Direct Iron
.jpg)
Production of reduced iron from mill scale waste using tilting
reducing gases and the iron oxide Production scale furnace 10 equipment depreciation 27 SUM 806175 15 Production cost of SRI The production cost of SRI was around 8000 EGP(250 USD) per tone Production of reduced iron from mill scale waste using tilting rotatory furnace2024年1月1日 If iron oxide is reduced directly to metal using hydrogen, a dense iron phase forms on the surface of the pellet, making it difficult for reduction to proceed However, if the H 2 /H 2 O ratio is chosen to make wüstite instead, this layer is porous and reduction to metal can occur rapidly afterward [73] The Direct Reduction of Iron ScienceDirect2024年2月5日 Electrochemical chloriron process for iron production from iron oxide and salt water Electrochemical production of iron metal can support a decarbonized process for steelmaking Summary of the chloriron process (A) Fe is reduced from Fe 2O 3 at the cathode, while NaCl is oxidized to Cl 2 at the anode, producingElectrochemical chloriron process for iron production from iron oxide 2024年6月17日 For direct reduced iron production, shaft furnaces use iron ore pelle ts, lumps, briquettes, and sinters as iron oxide input material The following features of the feed materials have a (PDF) Industrial Project Report on Metallurgical Review: Production
.jpg)
Fact sheet Electrolysis in ironmaking
that use electrical energy to reduce iron ore In electrolysis, iron ore is dissolved in a solvent of silicon dioxide and calcium oxide at 1,600°C, and an electric current passed through it Negativelycharged oxygen ions migrate to the positively charged anode, and the oxygen bubbles off Positivelycharged iron ions migrate to the negatively2023年8月1日 The main equipment used in the production process was a tilting rotary furnace reduced the iron oxide The reaction between iron oxide and coal also (PDF) Production of reduced iron from mill scale waste using 2015年6月10日 Thermal Reduction of Iron Oxide under Reduced Pressure and Implications on Thermal Conversion Efficiency for Solar Thermochemical Fuel Production June 2015 Industrial Engineering Chemistry (PDF) Thermal Reduction of Iron Oxide under Reduced Pressure THE MIDREX DIRECT REDUCTION PROCESS Currently, over 90% of iron production is through the BF route, with direct reduction having a growing share since its commercialisation in the 1970s: In 1990 DRI production made up slightly over 3% of the total iron production, rising to over 6% in 2000 and nearly 8% in 2019MIDREX H2 – The Road to CO2free Direct Reduction
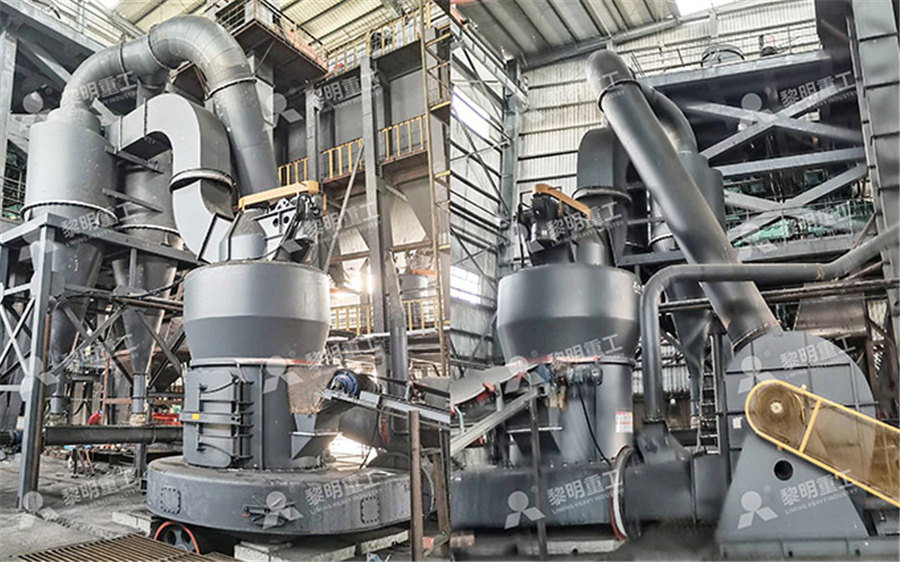
Production of Reduced Graphene Oxide by Using Three Different
2023年8月18日 Despite the huge and efficient functionalities of reduced graphene oxide (RGO) for bioengineering applications, the use of harsh chemicals and unfavorable techniques in their production remains a major challenge Microbial production of reduced graphene oxide (RGO) using specific bacterial strains has gained interest as a sustainable and efficient method The 2022年5月1日 Iron oxide nanoparticles are becoming progressively significant for the improvement of innovative biomedical and nanotechnology requests The keywords iron oxide nanoparticles, Fe 3 O 4 nanoparticles and magnetite nanoparticles have been utilized as a research object in the gross database of articles from the Web of Science The results of these Iron oxide nanoparticles: Preparation methods, functions, 2023年1月1日 The main equipment used in the production process was a tilting rotary furnace reduced the iron oxide The reaction between iron oxide and coal also (PDF) Production of Reduced Iron from Mill Scale Waste Using Table 181 shows the most common titanium minerals along with their chemical compositions (Lakshmanan et al 2014)Titanium dioxide is produced from the following ores: Ilmenite (FeTiO 3), rutile, anatase, and leucoxene (TiO 2 Innovative Process for the Production of Titanium
.jpg)
Production of Iron in the Blast Furnace SpringerLink
2020年8月19日 The Iron Age began when the humans, probably by chance, discovered iron sponge when they were heating iron ores that were easily reduced From that Meanwhile, the blast furnace has assimilated new technologies of process and production control, by means of a descending charge, which comprises a mixture of iron oxide, Iron Production CL Nassaralla, in Encyclopedia of Materials: Science and Technology, 2001 2 Direct Reduction Processes Direct reduction (DR) is defined as any process in which metallic iron is produced by the reduction of iron ore at temperatures below the iron melting point The product of a DR process is called direct reduced iron (DRI)Direct Reduction Process an overview ScienceDirect Topics2024年5月17日 This paper focuses on the study of current knowledge regarding the use of hydrogen as a reducing agent in the metallurgical processes of iron and steel production This focus is driven by the need to introduce environmentally suitable energy sources and reducing agents in this sector This theoretical study primarily examines laboratory research on the An Overview Analysis of Current Research Status in Iron Oxides 2008年6月19日 Experimental results performed with a fluidizedbed reactor supported the feasibility of the three processes including direct reduction of iron oxide by char, H 2 production by the steam−iron Hydrogen Production from the Steam−Iron Process with Direct Reduction
.jpg)
Direct Reduced Iron (DRI) Midrex Technologies, Inc
2024年11月1日 Direct Reduced Iron (DRI) is the steel industry’s most flexible metallic charge material, and the MIDREX Process can produce, discharge and transport DRI in the form best suited to the application Direct Reduced Iron (DRI) is a premium orebased metallic (OBM) raw material made by removing chemicallybound oxygen from iron oxide pellets and lump ores 2024年11月26日 Currently, the iron ore used in BFBOF production is BFgrade iron ore, while DRI production typically requires iron ore with 67% Fe or greater [34] Considering that Direct reduced (DR)grade iron ore only accounts for 4% of current global seaborne trade and the available reserves of highgrade ore are decreasing with cumulative extraction, the supply of The role of hydrogen in iron and steel production: Development Iron processing, use of a smelting process to turn the ore into a form from which products can be fashioned Included in this article also is a discussion of the mining of iron and of its preparation for smelting Iron (Fe) is a relatively dense metal with a silvery white appearance and distinctiveIron processing Definition, History, Steps, Uses, FactsIron ore is usually a mixture of iron and vast quantities of impurities such as sand and clay referred to as gangue The iron found in iron ores are found in the form of iron oxides As a result of these impurities, iron must be first separated from the gangue and then converted to pure ironIron Production Chemistry LibreTexts
.jpg)
Highly efficient visible light active iron oxidebased
2024年8月7日 Synthesis of aluminium oxide: iron oxide A similar combustion process, as described above using natural urea fuel, is adopted to synthesise aluminium oxide: iron oxide nanoparticles2023年9月1日 Production of reduced iron from mill scale waste using tilting rotary furnace The main equipment used in the production process was a tilting rotary furnace The outer layer of the formed spheres bonds with reduced iron, iron oxide and carbon bearing material forming a surface subjected to reducing gasesProduction of reduced iron from mill scale waste using tilting 2024年8月28日 The conventional iron and steel industry (ISI), driven by coal utilization as its predominant feedstock, constitutes a substantial source of greenhouse gas emissions Hydrogen metallurgy presents the opportunity to mitigate carbon emissions in ISI from the origin Among hydrogen metallurgical approaches, the hydrogenbased direct reduction iron (HDRI) process Development and Application of HydrogenBased Direct Reduction Iron Process2023年3月23日 Hydrogenbased direct reduced iron (H2DRI) is an alternative pathway for lowcarbon steel production Yet, the lack of established process and business models defining “green steel” make it Green steel: design and cost analysis of hydrogenbased direct iron
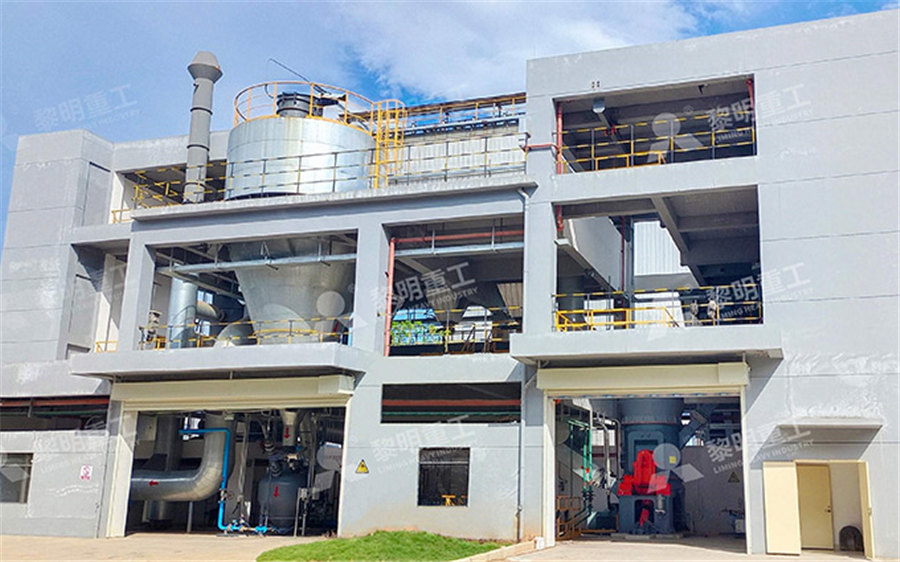
Electrochemical chloriron process for iron production from iron oxide
2024年3月20日 Electrochemical production of iron metal can support a decarbonized process for steelmaking Here, we report a lowtemperature, electrochemical cell that consumes lowcost and abundant iron oxide, salt, and water, while producing both iron and the alkaline electrolyte needed for efficient operation of the cell Coproduction of iron, lye, and chlorine leads to a process 2019年7月19日 Direct reduced iron (DRI) is also known as sponge iron (Hasambeigi et al 2014) This high porous material has a metallization degree in the range 85–95% with a carbon content in the range 05–4% depending on the processing route During the process, the iron oxides are reduced at the solid stateDirect Reduced Iron: Most Efficient Technologies for Greenhouse 2023年11月10日 The common feature of all of these techniques is that the iron ore is reduced in the solid state and the product obtained iron sponge must then be melted, usually in an electric furnace, for DIRECT REDUCED IRON ORE: Production ResearchGate2024年8月5日 The transition to green steel production is pivotal for reducing global carbon emissions This study presents a comprehensive technoeconomic analysis of various green steel production methods, including hydrogen reduction and three different electrolysis techniques: aqueous hydroxide electrolysis (AHE), molten salt electrolysis, and molten oxide electrolysis Economics of Electrowinning Iron from Ore for Green Steel Production
.jpg)
Overview on production of reduced iron powder from mill scale
2021年1月1日 Mill Scale, generated in a rolling steel mill can be a potential material for iron powder production Mill scale is a combination of different oxides like Hematite (Fe 2 O 3), Magnetite (Fe 3 O 4), and Wustite (FeO) [2], [3]Besides, this multioxide mill scale's conversion into single oxide (Fe 2 O 3) is the bestsuited route for further reduction into iron powder due to