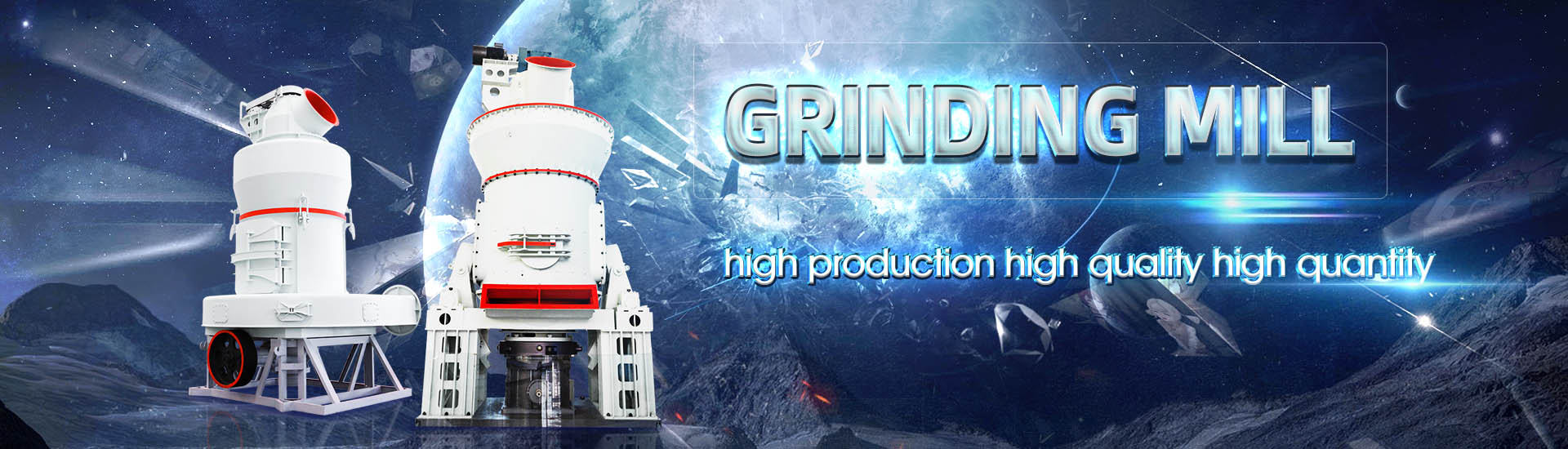
Ore grinding mills are generally started with reduced pressure.
.jpg)
Comminution and classification technologies of iron ore
2022年1月1日 High pressure grinding rolls (HPGR) technology was introduced to the minerals processing industry in the mid 1980s and has rapidly (for the mining industry) established itself It is performed in cylindrical steel vessels that contain a charge of loose crushing bodies—the grinding medium—which is free to move inside the mill, thus comminuting the ore particles Grinding Mill an overview ScienceDirect Topics2023年7月20日 Ore grinding is a process to further reduce and disperse the ore particle size In the mineral processing industry, ore grinding is the particle size preparation before the Ore Grinding SpringerLinkThis strategy is proving to be immensely beneficial for many operations resulting in improved mill throughputs (10–30 %), reduced grinding energy costs (10–20 %), improved metals Physical Processing: Innovations in Mineral Processing
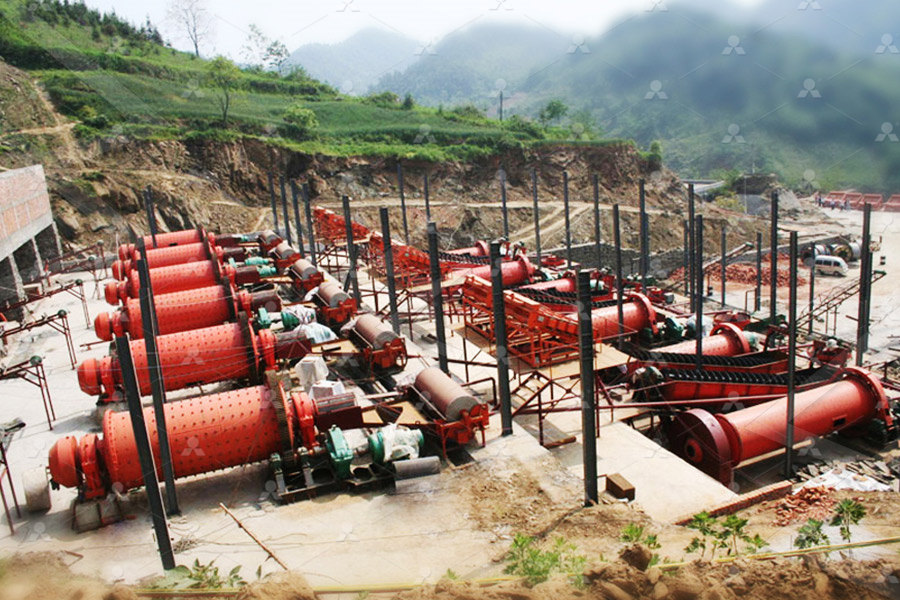
Chapter 7 Grinding Mills Wills' Mineral Processing Technology,
According to the ways by which motion is imparted to the charge, grinding mills are generally classified into two types: tumbling mills and stirred mills In tumbling mills, the mill shell is According to the ways by which motion is imparted to the charge, grinding mills are generally classified into two types: tumbling mills and stirred mills In tumbling mills the mill shell is Chapter 7: Grinding Mills GlobalSpecHigh pressure grinding rolls were successfully introduced in the cement industry in the late 1980s and enabled appreciable reduction in energy consumption Promptly enough their potential HIGH PRESSURE GRINDING ROLLS—A PROMISING AND COST 2022年8月31日 In addition, due to the depletion of highgrade ores and the growing needs of the industry for the processing of lowgrade finely dispersed ores, the development of fine/ultrafine Grinding Modeling and Energy Efficiency in Ore/Raw Material
.jpg)
HighPressure Grinding Roller Presses for Minerals Processing
HPGR Grinding Process Highpressure comminution of ores with High Pressure Grinding Roller Presses (HPGRs) is predominantly achieved through compression The process takes place between two counterrotating rollers, whereby the ore is chokefed between the rollers The feed material is compressed2016年5月10日 GRINDING AND CLASSIFICATION Grinding and classification of the minus ½” washed and crushed ore is accomplished in the usual manner, and generally no problems are encountered In some cases where this fraction of ore is low in fines it may be necessary to blend back some of the thickened primary slimeCrushing and Grinding Wet Sticky Ore 911MetallurgistRod, Ball and Pebble Mills The products from AG or SAG mills typically feed secondary grinding mills with particles that range in size from 5 cm down to below 100 microns (01 mm) The final particle size is determined by downstream Introduction to Mineral Processing or Beneficiation2021年7月7日 Industrial grinding mills generally include vertical roller mills, ultrafine grinding mills, highpressure suspension roller mills, Raymond mills, mediumspeed micro powder mills, and other types SBM specializes in the RD and production of various industrial milling equipment, which sells well at home and abroadWhat are the types of industrial grinding mills?
.jpg)
Ore mill, Ore grinding mill All industrial manufacturers
Rotational speed: 100 rpm 1,100 rpm FRITSCH Planetary Ball Mills – highperformance allrounder in routine laboratory work The Planetary Micro Mill PULVERISETTE 7 premium line with 2 grinding stations is designed for a broad range of 2023年4月23日 Harder ores have a larger grinding re sistance than soft ores ther efore, hard ores have lower breakage rates than soft ores Wear resistance depends on the stre ngth of the ore being ground [6 7 ](PDF) Grinding Media in Ball MillsA Review ResearchGate2023年7月10日 Stirred mills have unique designs and operations, which provide higher grinding efficiency, lower energy consumption, and reduced media consumption compared to traditional tumbling mills(PDF) EnergyEfficient Advanced Ultrafine Grinding of Particles Request PDF On Mar 15, 2015, Mathis Reichert and others published Research of iron ore grinding in a verticalrollermill Find, read and cite all the research you need on ResearchGateResearch of iron ore grinding in a verticalrollermill
.jpg)
Potential of HighPressure Grinding Roll (HPGR) for Size
2022年3月16日 21 Experimental Design The experimental planning with selected key factor like operating gap (X 1), applied load (X 2) and roll speed (X 3) was designed by CCD method to obtain the optimum conditions for grinding the BHQ iron ore in HPGRA full secondorder polynomial model was obtained by regression analysis for three factors by using the Design Grinding Mills Barry A Wills, James A Finch FRSC, FCIM, PEng, in Wills' Mineral Processing Technology (Eighth Edition), 2016 71 Introduction Grinding is the last stage in the comminution process where particles are reduced in size by a combination of impact and abrasion, either dry, or more commonly, in suspension in waterGrinding Mill an overview ScienceDirect Topics2016年7月14日 Additional options for highpressure grinding roll use in gold ore comminution circuits are illustrated in Figure 11 As indicated by Kapur et al (1992), highpressure roll grinding is likely to replace ball mills in increasing HPGR 911Metallurgist2017年2月20日 The CRRK series of wet grinding ball mills are tabulated below PEBBLE MILLS No steel grinding media is used in a fully autogenous mill When choosing primary autogenous grinding, run of mine ore up to 200300 mm in size is fed to the mill When using a crushing step before the grinding, the crusher setting should be 150200 mmGrinding Mill Design Ball Mill Manufacturer 911Metallurgist
.jpg)
(PDF) Effects of High Pressure ORE Grinding on the
2014年1月20日 grinding rolls started being the standard used on processing kimberlites, iron ore, copper, gold and other mineral resources The benefits of using the roller presses in ore processing systems2016年6月6日 Common convention generally refers to highaspect ratio mills as SAG mills (with diameter to effective grinding length ratios of 3:1 to 1:1), lowaspect ratio mills (generally, a mill with a significantly longer length than diameter) are also worth notingSAG Mill Grinding Circuit Design 911Metallurgist1970s, autogenous grinding mills (AG) and semiautogenous grinding mills (SAG) were largely used, and soon the comminution circuits with AG/SAG mills and ball mills became industrial standard flowsheets, due to their higher processing capacity [3] But at the same time there was also a constant pursuit by the researchers to address the issue Potential of HighPressure Grinding Roll (HPGR) for Size Grindability tests are generally designed to mimic the grinding mechanisms observed in industrial units The best examples of this can be observed in the Bond series, where ball mills, rod mills, and crushers are tested using similar laboratoryscale apparatuses Similarly, the MacPherson and media competency tests were designed to mimicSAG Mill Testing Test Procedures to Characterize Ore Grindability
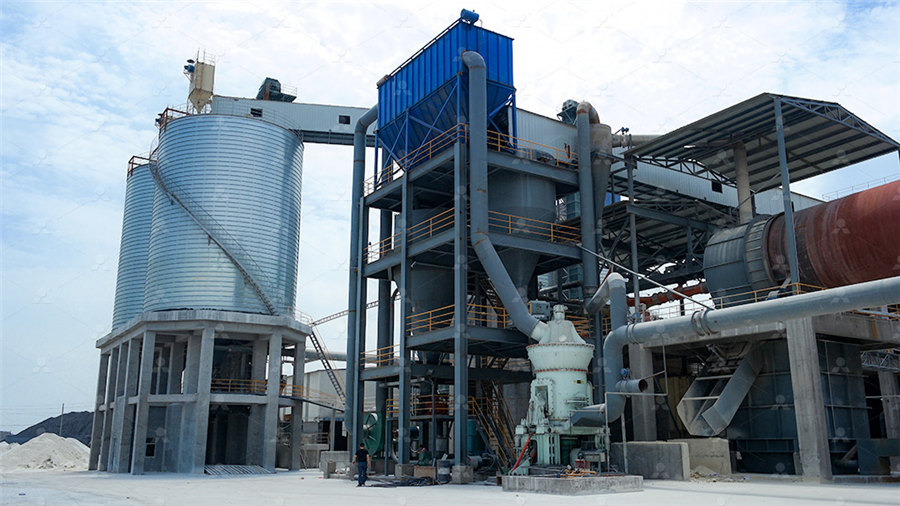
Grinding Mill Liners 911Metallurgist
2015年8月6日 The amount of unground material will slowly increase until the mill can no longer grind the bigger ore When this happens the liners will have to be changed If you ever have to start up a mill that has had a complete liner change I would suggest starting at a reduced tonnage and slowly bring the tonnage up to its maximum2015年2月2日 High pressure grinding rolls SAG and AG mills are generally installed in a primary milling duty receiving primary crushed (−250 mm) Ball mills are cylindrical tumbling mills with steel balls as the grinding media and a small fraction of ore feed material that is far smaller than the minution SpringerLink2021年11月3日 Phosphate mineral powder grinding mills includes ultrafine mills, vertical roller mills, highpressure mills, etc can grind ores into a fine powder +17 [ protected]Phosphate Mineral Powder Grinding Mill SBM Ultrafine 2013年12月18日 Fine grinding, to P80 sizes as low as 7 μm, is becoming increasingly important as mines treat ores with smaller liberation sizes This grinding is typically done using stirred mills such as the Isamill or Stirred Media Detritor While fine grinding consumes less energy than primary grinding, it can still account for a substantial part of a mill’s energy budget Overall Energy Use of Fine Grinding in Mineral Processing
.jpg)
(PDF) Reducing Grinding Energy and Cost
Traditionally, the lowest operating cost was achieved by multi stage fully autogenous grinding due to elimination of steel grinding media costs which may represent up to 50% of the grinding costSignificant reduction of the cost 2022年5月23日 Grinding experiments were conducted in a laboratoryscale stirred mill on a lowgrade PGE bearing chromite ore HighPressure Grinding Rolls (HPGR) product of −1 mm was used as feed material to Modeling and application of stirred mill for the coarse grinding of 2019年2月5日 PDF High Pressure Grinding Rolls (“HPGR”) is applied in all stages of iron ore size reduction, from coarse ore grinding down to pellet feed Find, read and cite all the research you need CONSIDERATIONS FOR MULTISTAGE HPGR is Enduron® High Pressure Grinding Rolls (HPGR) Partnering with our customers, Weir Minerals has extensive realworld experience gathered since the 1990s Introduction HPGR technology cuts direct energy consumption by up to 40% Even with the improvements in the design of SAG (SemiAutogenous Grinding) mills, adoptionEnduron High Pressure Grinding Rolls Weir Group
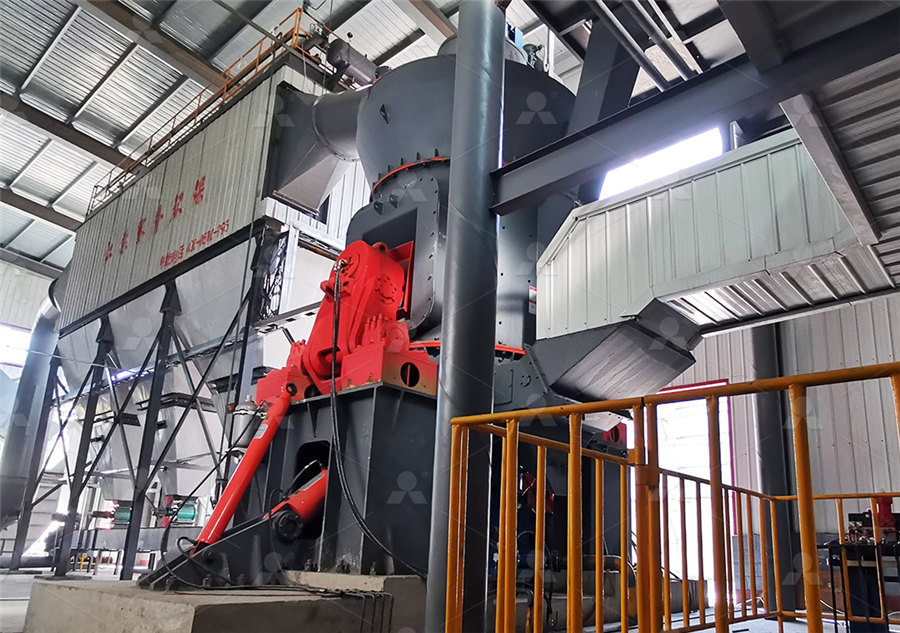
Beneficiation of Gold and Silver Ores SpringerLink
2019年12月15日 429 VertiMills Vertical mills were first designed in the 1950s for applications in fine and ultrafine grinding in Japan Lately, the vertical mill is making progress toward primary grind application and shown promise in energy reduction relative to ball mills, typical to what is normally seen in regrinding applications (Mazzinghy et al 2014)optimising the process, the grinding tools will have a significant impact on lower production costs as well as maintenance costs Ball mills and grinding tools Cement ball mills are typically twochamber mills (Figure 2), where the first chamber has larger media with lifting liners installed, providing the coarse grindingBALL MILLS Ball mill optimisation Holzinger Consulting2019年2月5日 The major new ore size reduction and separation technologies and practices implemented in the last 25 years include high intensity blasting, high pressure grinding rolls (HPGR), stirred mills and Case Study of Dry HPGR Grinding and Classification in Ore Processing2020年9月22日 Grinding machine has been widely used in gold mines in South Africa since 1905 At that time, the grinding machine used river pebble as the grinding medium, which was essentially a gravel mill Later, in order to improve the production capacity of the mill, cast iron balls were used as the medium, so normal gravel mills were evolved into ball mills and rod millsGrinding Machines: Types and Selection Principles Miningpedia
.jpg)
Replacement of Wet Ball Milling with HighPressure Grinding
2023年11月28日 In response to the Natural Resources Canada “Crush It Challenge,” Corem partnered with the University of British Columbia and led a project to develop and demonstrate the use of highpressure grinding to replace the workhorse of the industry, wet ball milling Two plant case studies, a small tonnage gold recovery operation and a large tonnage copper recovery 2011年9月25日 Apart from tertiary and quaternary crushing applications in a wide variety of ore types, High Pressure Grinding Roll (“HPGR”) technology is also applied in regrinding of iron ore pellet feed FEASIBILITY OF DRY HIGH PRESSURE GRINDING AND CLASSIFICATION HPGR Grinding Process Highpressure comminution of ores with High Pressure Grinding Roller Presses (HPGRs) is predominantly achieved through compression The process takes place between two counterrotating rollers, whereby the ore is chokefed between the rollers The feed material is compressedHighPressure Grinding Roller Presses for Minerals Processing2016年5月10日 GRINDING AND CLASSIFICATION Grinding and classification of the minus ½” washed and crushed ore is accomplished in the usual manner, and generally no problems are encountered In some cases where this fraction of ore is low in fines it may be necessary to blend back some of the thickened primary slimeCrushing and Grinding Wet Sticky Ore 911Metallurgist

Introduction to Mineral Processing or Beneficiation
Rod, Ball and Pebble Mills The products from AG or SAG mills typically feed secondary grinding mills with particles that range in size from 5 cm down to below 100 microns (01 mm) The final particle size is determined by downstream 2021年7月7日 Industrial grinding mills generally include vertical roller mills, ultrafine grinding mills, highpressure suspension roller mills, Raymond mills, mediumspeed micro powder mills, and other types SBM specializes in the RD and production of various industrial milling equipment, which sells well at home and abroadWhat are the types of industrial grinding mills?Rotational speed: 100 rpm 1,100 rpm FRITSCH Planetary Ball Mills – highperformance allrounder in routine laboratory work The Planetary Micro Mill PULVERISETTE 7 premium line with 2 grinding stations is designed for a broad range of Ore mill, Ore grinding mill All industrial manufacturers2023年4月23日 Harder ores have a larger grinding re sistance than soft ores ther efore, hard ores have lower breakage rates than soft ores Wear resistance depends on the stre ngth of the ore being ground [6 7 ](PDF) Grinding Media in Ball MillsA Review ResearchGate
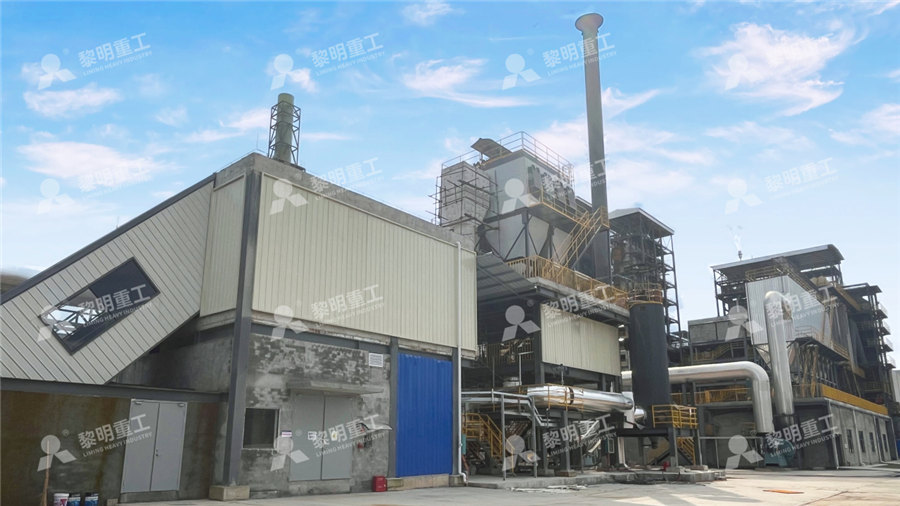
(PDF) EnergyEfficient Advanced Ultrafine Grinding of Particles
2023年7月10日 Stirred mills have unique designs and operations, which provide higher grinding efficiency, lower energy consumption, and reduced media consumption compared to traditional tumbling millsRequest PDF On Mar 15, 2015, Mathis Reichert and others published Research of iron ore grinding in a verticalrollermill Find, read and cite all the research you need on ResearchGateResearch of iron ore grinding in a verticalrollermill2022年3月16日 21 Experimental Design The experimental planning with selected key factor like operating gap (X 1), applied load (X 2) and roll speed (X 3) was designed by CCD method to obtain the optimum conditions for grinding the BHQ iron ore in HPGRA full secondorder polynomial model was obtained by regression analysis for three factors by using the Design Potential of HighPressure Grinding Roll (HPGR) for Size Grinding Mills Barry A Wills, James A Finch FRSC, FCIM, PEng, in Wills' Mineral Processing Technology (Eighth Edition), 2016 71 Introduction Grinding is the last stage in the comminution process where particles are reduced in size by a combination of impact and abrasion, either dry, or more commonly, in suspension in waterGrinding Mill an overview ScienceDirect Topics