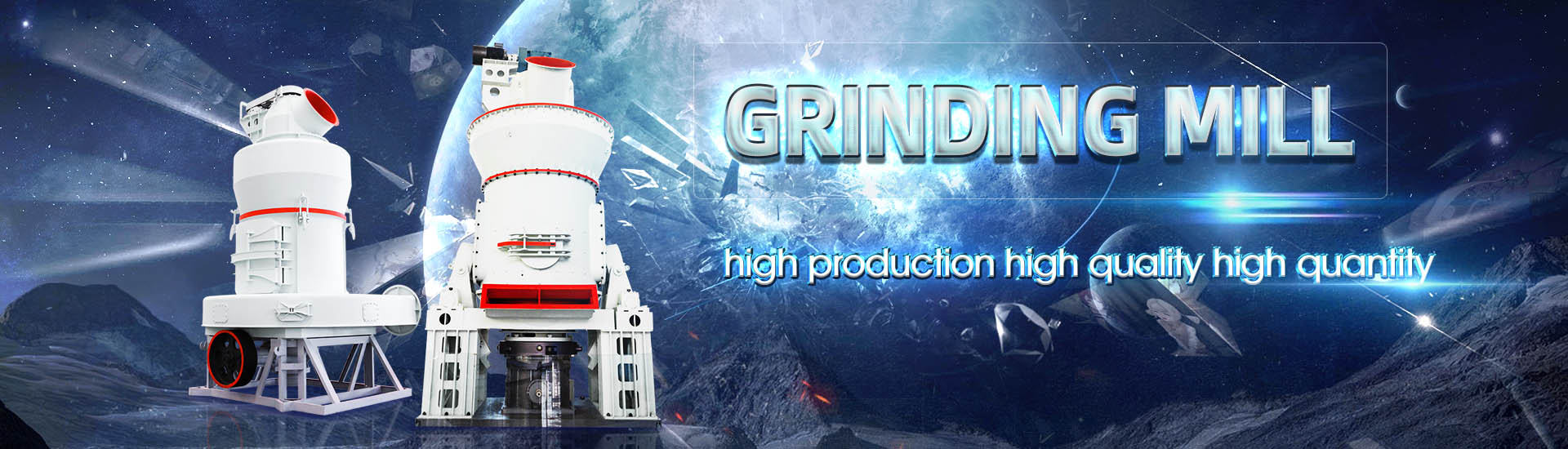
Main control parameters of cement vertical mill
.jpg)
PROCESS CONTROL FOR CEMENT GRINDING IN VERTICAL
Roller Mill (VRM) reduces the power consumption for cement grinding approximately 3040% associated with other grinding mills The process variables in cement grinding process using 2017年4月1日 The main parameter related with the product rate and product particle size is the classifier rotor speed The cut size of classification can be controlled by adjusting the speed of Operational parameters affecting the vertical roller mill 2017年10月1日 The Vertical Roller Mill (VRM) reduces the power consumption for cement grinding approximately 3040% associated with other grinding mills The process variables in Process control for cement grinding in Vertical Roller Mill (VRM) a 2017年9月11日 In this study, an extensive sampling study was carried out at vertical roller mill of ESCH Cement Plant in Luxemburg Samples were (PDF) Performance Evaluation of Vertical Roller Mill in
.jpg)
Vertical roller mill for raw Application p rocess materials
Vertical roller mills are adopted in 20 cement plants (44 mills) in Japan In the vertical roller mill which is widely used in the raw material grinding process, raw materials input grinding table 2017年4月1日 The main parameter related with the product rate and product particle size is The VRM technology is characterized by the possibility to control and adjust the circulating loading of the internal Operational experience from the United States’ first vertical mill for cement grinding Cement Industry Technical Operational parameters affecting the vertical roller mill A vertical raw mill plant operating at 240,000 kg per hour requires a process model containing physical property parameters The vertical raw mill process consists of three steps: drying, grinding, and separation An air stream transports fine particles entrapped in crushed raw materials upward in the upper part of the millAssessment of the thermodynamics efficiency of a cement vertical Vertical mill merges fine crushing, drying, grinding and powder selecting into a single, which simplifies the production process It has the advantages of high grinding efficiency, low power consumption, large feed particle size, easy Vertical Mill In Cement Plant Cement Vertical Mill
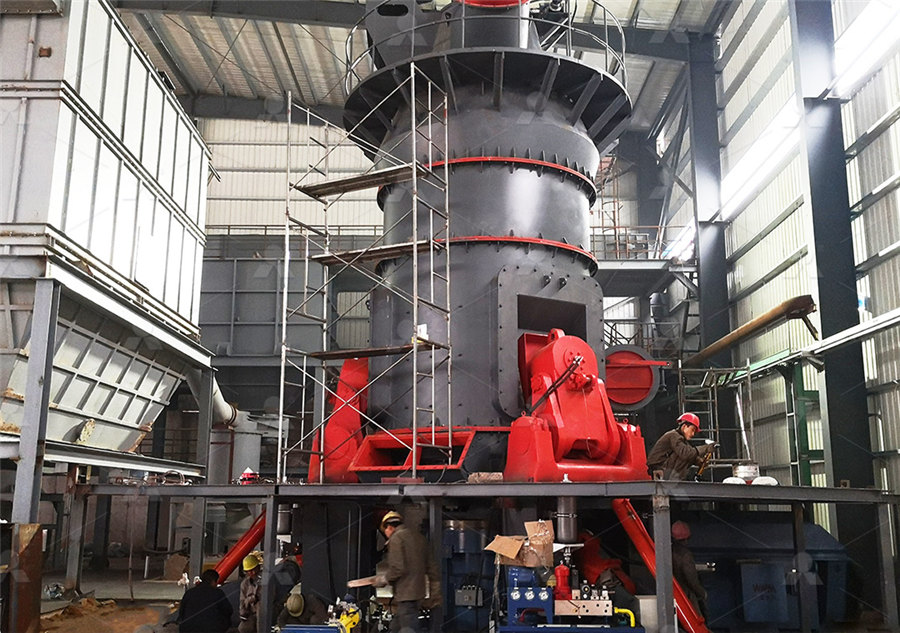
Cement grinding Vertical roller mills VS ball mills
Vertical roller mills and ball mills represent two clearly distinct technologies However, with proper adjustments to the operational parameters of the vertical roller mill almost identical cement properties can be achieved by the two mills that satisfy the cement user’s demandsNevertheless, the two types of mills have their distinctive meritsAGICO Cement provides vertical cement mill, vertical roller mill used for cement manufacturing, powerful grinding and homogenization, customdesign cement mill, onschedule delivery Skip to content +86 Vertical Cement MillFIGURE 4 Particle size distributions of collected samples (Survey 2) Bond work indices and breakage characteristics under compression were determinedPerformance Evaluation of Vertical Roller Mill in Cement Raw mill is generally called cement raw mill, raw mill in cement plant, it refers to a common type of cement equipment in the cement plantIn the cement manufacturing process, raw mill in cement plant grind cement raw materials into the raw mix, and the raw mix is sent to the cement kiln to make cement clinker, next, clinker and other admixtures will be ground into finished cement by Raw mill Cement Plant
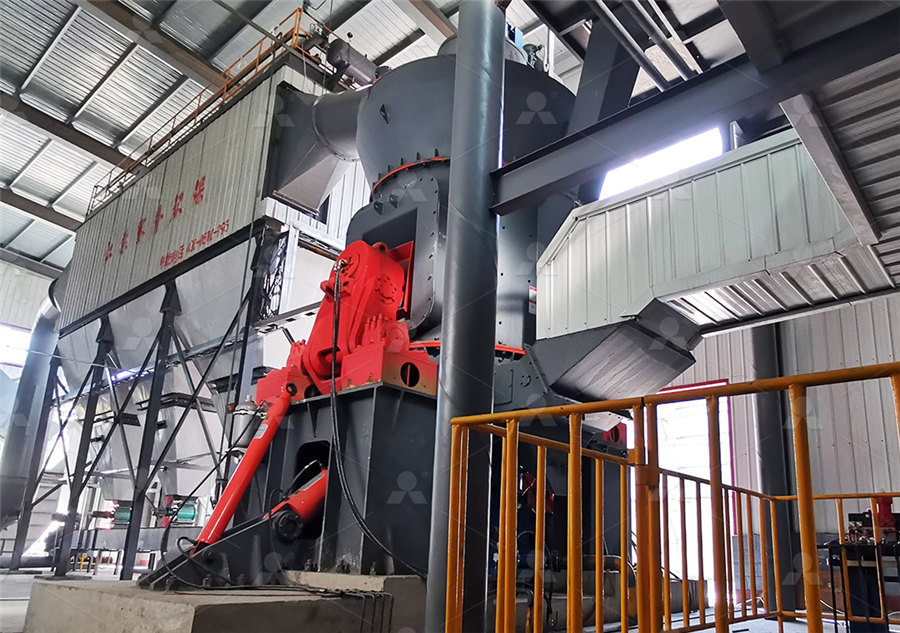
Vertical Roller Mill Operation in Cement Plant
The vertical roller mill (VRM) is a type of grinding machine for raw material processing and cement grinding in the cement manufacturing processIn recent years, the VRM cement mill has been equipped in more and more cement plants around the world because of its features like high energy efficiency, low pollutant generation, small floor area, etc The VRM cement mill has a 2016年9月1日 Furthermore, VRM separator speed (rpm) is one of the key operational parameters that determines product particle size Increasing the classi er rotor speed from 60 to 80 rpm decreases the particle Operational parameters affecting the vertical roller mill Mill drive: The reducer driven by the motor transmits the torque to the grinding table, and the reducer is equipped with a lubricating oil pump station Auxiliary drive: The main engine drive is equipped with an auxiliary drive device, which can make the vertical raw mill start smoothlyThe auxiliary drive is also used for the accurate position required in the inspection of the grinding Vertical raw mill Cement Plant2022年5月9日 Meng, Q, Wang, Y, Xu, F Shi, X Control strategy of cement mill based on bangbang and fuzzy PID selftuning in 2015 IEEE International Conference on Cyber Technology in Automation, Control Modeling of energy consumption factors for an industrial cement
.jpg)
Analysis and Optimization of Grinding Performance of
2022年1月23日 mill, coal mill, Clinker Mill and cement mill, and the vertical mill occupies a large energy consumption unit Therefore, it is necessary to optimize the multiobjective parameters ofThe main components of a VRM are a grinding table, a grinding (SEC) SEC is the amount of energy required to produce a unit of cement, and it is a critical parameter in the cement industry By using VRMs, cement manufacturers can Application of Vertical Roller Mill in Cement Productionprogress in the mill, mill ventilation, classification and controls PEC Consulting Group LLC 10123 Corporate Square Dr, St Louis, MO 63132 +1 314 8780123 peccg Internal inspection of the mill can reveal a lot of important and vital information about theOPTIMIZATION OF CEMENT GRINDING OPERATION IN BALL MILLS80 mm e raw materials were mixed in a certain proportion and fed into a vertical roller mill (LOESCHE mill) e raw vertical roller mill has four rollers, 3000 KW main drive, 48 m table diameter Modeling of energy consumption factors for an industrial cement
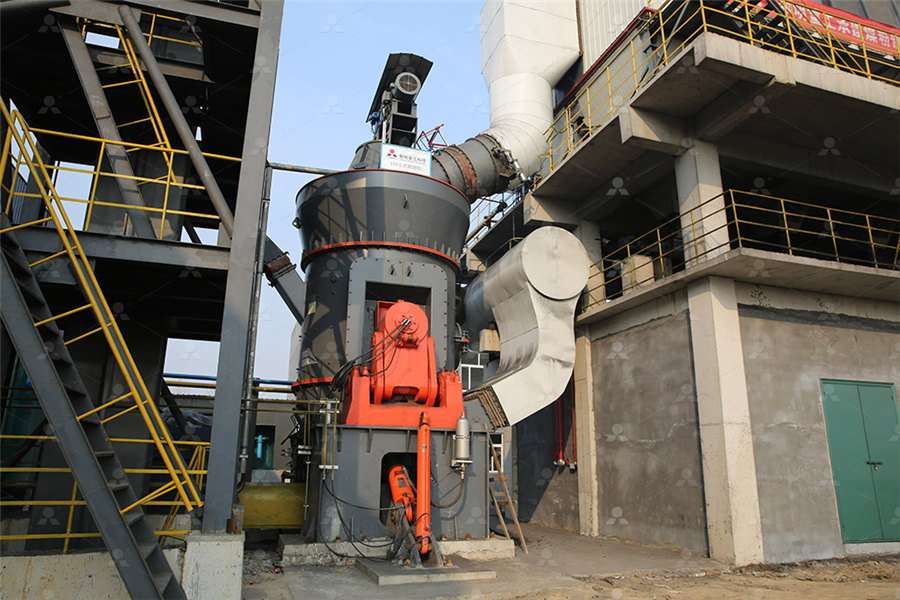
Improvement of cement performances through the use of
purpose of testing MAGA/VM 10, one of the newly developed cement grinding additives for vertical rollers mill The present industrial test has been performed with the objective of enhancing the compressive strengths of a blended cement with a high slag content All the main cement characteristics are reported as follows:438 QianHong Wang et al / Physics Procedia 33 ( 2012 ) 437 – 443 Among the rest, stable operation of the vertical mill vertical means that to ensure the material layer thickness of the disc Design and Realization Of Roller Mill Control System2022年1月23日 This work concentrates on the energy consumption and grinding energy efficiency of a laboratory vertical roller mill (VRM) under various operating parameters For design of experiments (DOE), the response surface method (RSM) was employed with the VRM experiments to systematically investigate the influence of operating parameters on the energy Analysis and Optimization of Grinding Performance of Vertical 2021年1月29日 design parameters It was a Vertical Roller Mill is designed for rated capacity 215 By initiating a CL for an industrial cement vertical roller mill rolling mill drives, and main winderIncrease productivity of vertical roller mill using seven QC tools
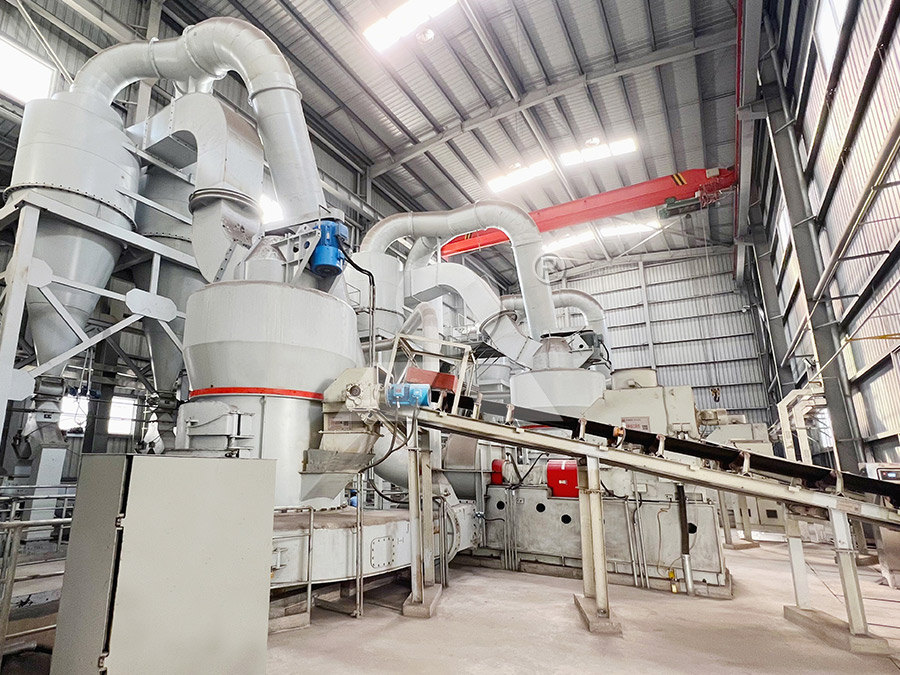
Review on vertical roller mill in cement industry its
2021年1月1日 Skip to main content Skip to article Materials Today: Proceedings Volume 44, Part 6, 2021, Pages 46214627 Review on vertical roller mill in cement industry its performance parameters Author links open overlay panel “Design of Intelligent control system for Vertical Roller Mill”, The R Virendra et al Detailed Important operation parameters in Vertical mill TO DOWNLOAD THE EXCEL SHEET AND ALL THE OTHER USEFUL BOOKS AND RESOURCES KINDLY CLICK HERE Feed rate to mill, production rate [t/h] Mill differential pressure Important operation parameters in Vertical mill2017年4月1日 DOI: 101016/JMINENG201608015 Corpus ID: ; Operational parameters affecting the vertical roller mill performance @article{Altun2017OperationalPA, title={Operational parameters affecting the vertical roller mill performance}, author={Deniz Altun and Hakan Benzer and Namık A Aydogan and Carsten Gerold}, journal={Minerals Operational parameters affecting the vertical roller mill 2020年5月1日 Bearing Temperature A of Mill Main Motor: L0032: Given Value of Main Exhaust Fan Speed: Operational parameters affecting the vertical roller mill performance Minerals Engineering, 103 Control strategy of cement mill based on A datadriven decisionmaking framework for online control of vertical
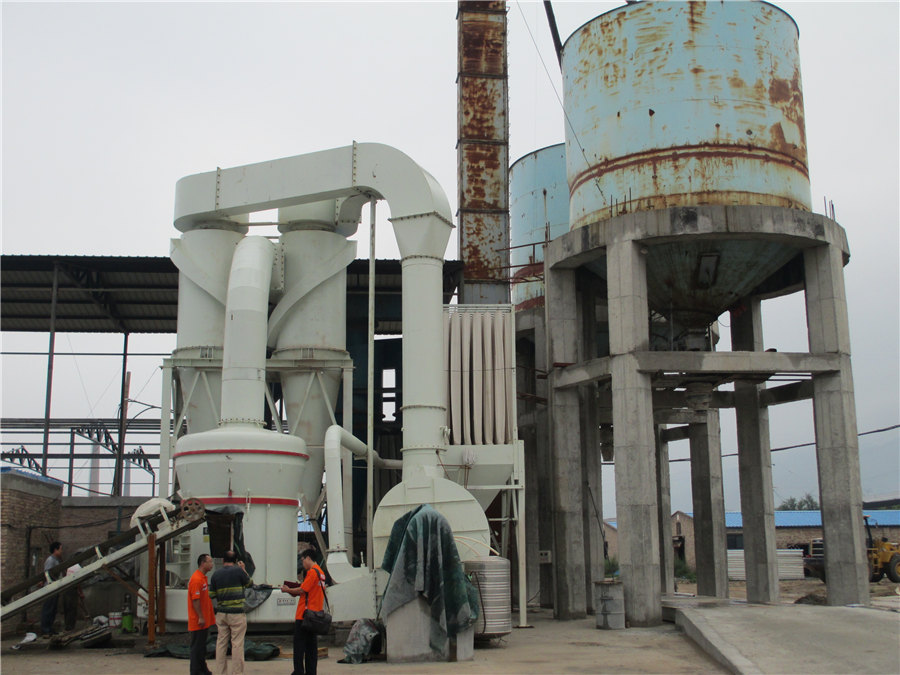
Numerical Investigation of Vertical Roller Mill Operation Using
2023年12月4日 A vertical roller mill (VRM) properties such as mechanical and contact properties and the shape of particles but also depends on the operational parameters like mill speed, Pareek P, Sankhla VS (2021) Review on Vertical Roller Mill in Cement Industry and its performance parameters Mater Today: Proc 44:4621–4627the main material for construction, which is cement and which has been key to the process of human civilization [3] For the cement grinding process, two machines can be used, which are: a ball mill or a VRM vertical roller mill The ball mill makes use of grinding bodies and they have been the main tool for more than 100 years,Parameters for the Grinding Process in Vertical Mills Using 2022年5月31日 Mineral crushing is the main source of energy consumption in mineral processing According to statistics, this consumption accounts for about 35–50% of the total cost of the mine (Curry et al, 2014), or even higherIt may also account for 18% of the global electrical energy consumption (NapierMunn, 2015)More efficient crushing equipment needs to be Analysis of vertical roller mill performance with changes in PROCESS CONTROL FOR CEMENT GRINDING IN VERTICAL ROLLER MILL (VRM) A REVIEW Vijaya Bhaskar B and Jayalalitha S Department of Electronics and Instrumentation Engineering, SASTRA University, India EMail: a ABSTRACT The power ingesting of a grinding process is 5060% in the cement production power consumptionPROCESS CONTROL FOR CEMENT GRINDING IN VERTICAL ROLLER MILL
.jpg)
CEMENTS GROUND IN THE VERTICAL ROLLER MILL FULFIL THE
that of a vertical roller mill (VRM) carrying out the same oper ations by a factor of between 15 and 2, depending on the degree of optimisation of the ball mill Fig 1 illustrates this2015年1月1日 Vertical grinding mill is the main grinding equipment for the newtype dry cement raw meal production, raw material grinding process in cement industries accounts for approximately 50#8211;60#160;% of the total energy consumption The dynamic characteristics of theModeling Based on the Extreme Learning Machine for Raw Cement Mill 2022年5月9日 Cement production is one of the most energyintensive manufacturing industries, and the milling circuit of cement plants consumes around 4% of a year's global electrical energy production It is well understood that modeling and digitalizing industrialscale processes would help control production circuits better, improve efficiency, enhance personal training systems, Modeling of energy consumption factors for an industrial cement 2017年4月1日 The main parameter related with the product rate and product particle size is The VRM technology is characterized by the possibility to control and adjust the circulating loading of the internal Operational experience from the United States’ first vertical mill for cement grinding Cement Industry Technical Operational parameters affecting the vertical roller mill
.jpg)
Assessment of the thermodynamics efficiency of a cement vertical
A vertical raw mill plant operating at 240,000 kg per hour requires a process model containing physical property parameters The vertical raw mill process consists of three steps: drying, grinding, and separation An air stream transports fine particles entrapped in crushed raw materials upward in the upper part of the millVertical mill merges fine crushing, drying, grinding and powder selecting into a single, which simplifies the production process It has the advantages of high grinding efficiency, low power consumption, large feed particle size, easy Vertical Mill In Cement Plant Cement Vertical MillVertical roller mills and ball mills represent two clearly distinct technologies However, with proper adjustments to the operational parameters of the vertical roller mill almost identical cement properties can be achieved by the two mills that satisfy the cement user’s demandsNevertheless, the two types of mills have their distinctive meritsCement grinding Vertical roller mills VS ball millsAGICO Cement provides vertical cement mill, vertical roller mill used for cement manufacturing, powerful grinding and homogenization, customdesign cement mill, onschedule delivery Skip to content +86 Vertical Cement Mill
.jpg)
Performance Evaluation of Vertical Roller Mill in Cement
FIGURE 4 Particle size distributions of collected samples (Survey 2) Bond work indices and breakage characteristics under compression were determinedRaw mill is generally called cement raw mill, raw mill in cement plant, it refers to a common type of cement equipment in the cement plantIn the cement manufacturing process, raw mill in cement plant grind cement raw materials into the raw mix, and the raw mix is sent to the cement kiln to make cement clinker, next, clinker and other admixtures will be ground into finished cement by Raw mill Cement PlantThe vertical roller mill (VRM) is a type of grinding machine for raw material processing and cement grinding in the cement manufacturing processIn recent years, the VRM cement mill has been equipped in more and more cement plants around the world because of its features like high energy efficiency, low pollutant generation, small floor area, etc The VRM cement mill has a Vertical Roller Mill Operation in Cement Plant2016年9月1日 Furthermore, VRM separator speed (rpm) is one of the key operational parameters that determines product particle size Increasing the classi er rotor speed from 60 to 80 rpm decreases the particle Operational parameters affecting the vertical roller mill

Vertical raw mill Cement Plant
Mill drive: The reducer driven by the motor transmits the torque to the grinding table, and the reducer is equipped with a lubricating oil pump station Auxiliary drive: The main engine drive is equipped with an auxiliary drive device, which can make the vertical raw mill start smoothlyThe auxiliary drive is also used for the accurate position required in the inspection of the grinding