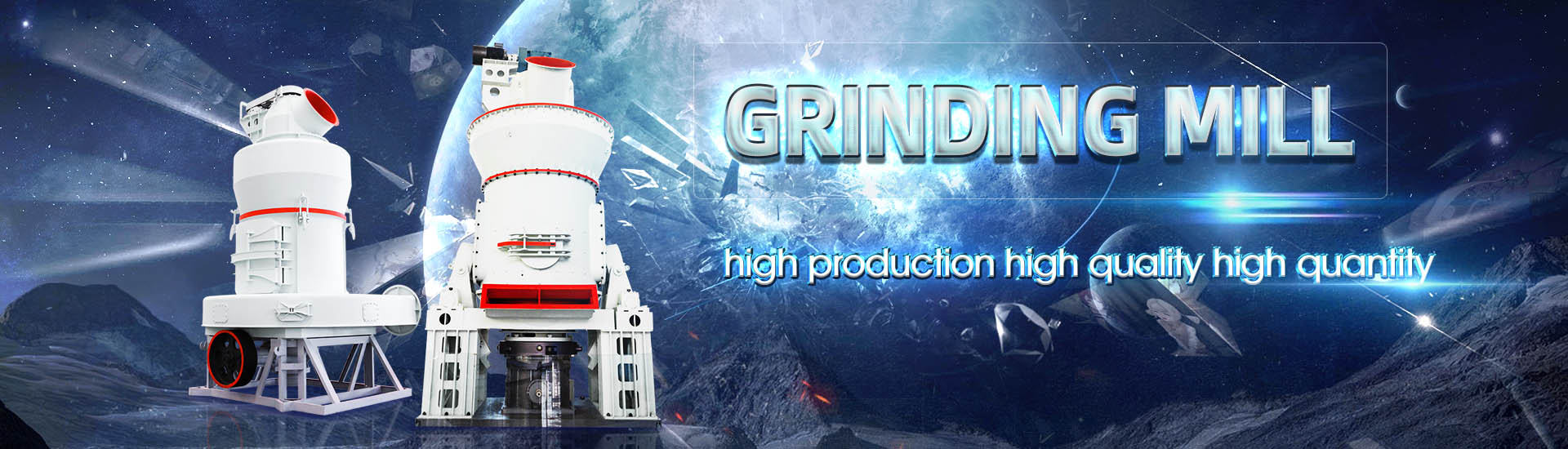
Gypsum powder process flow
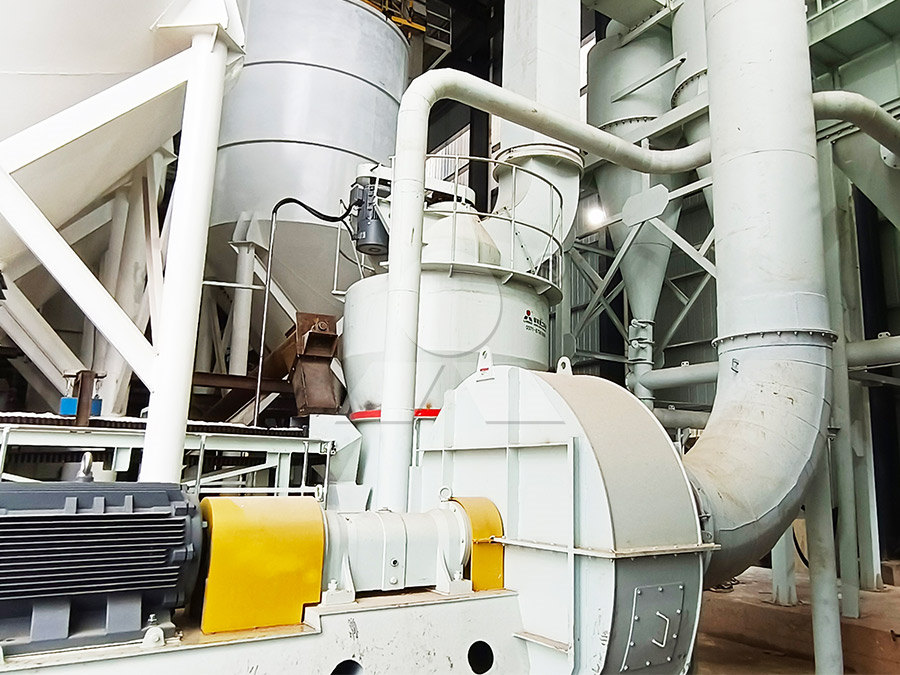
Flow diagram of the manufacturing gypsum and analysis
The present study proposes a new strategy to develop a composite gypsum binder with enhanced strength and stability using mineral admixture (zeolite) and biocarbonate fillers (waste shellGypsum powder is one of the five major gel materials, which is processed through crushing, grinding and other processes It is widely used in construction, building materials, industrial molds and art models, chemical industry and agriculture, Gypsum Powder Manufacturing Gypsum Powder Three types of gypsum products are plaster, stone, and high strength or improved stone The Gypsum and the Gypsum products are used for construction purposes It is also used in Handbook on Gypsum and Gypsum Based Products NIIR Project Mineral Processing Gypsum processing can be divided into three basic steps: (1) rock preparation, (2) calcining, and (3) formulating and manufacturing This is illustrated graphically with the flow chart in Figure 1 The specifics of each Infrastructure and Construction Materials Guide —
.jpg)
Gypsum Board production flow
Let's see the manufacturing process "Gypsum" is baked in a furnace and made into "calcined plaster" which will solidify when it reacts with water Calcined “gypsum” is mixed with water to make a slurry (muddy state) Then, the slurry ASTM standards govern the manufacture of gypsum board and set strict criteria for strength, water resistance, and other characteristics To produce gypsum board, crushed natural Making Gypsum Board Gypsum Association2021年3月3日 According to GeorgiaPacific Company, the typical process of manufacturing gypsum board can be summarized in the following steps ( Fig 817): “(1) raw materials: Gypsum Products SpringerLink2023年5月15日 There are three main diagrams that can help us understand this cycle in detail The first describes the process of water leaving the structure of gypsum to form hemihydrate Understanding gypsum in 3 diagrams
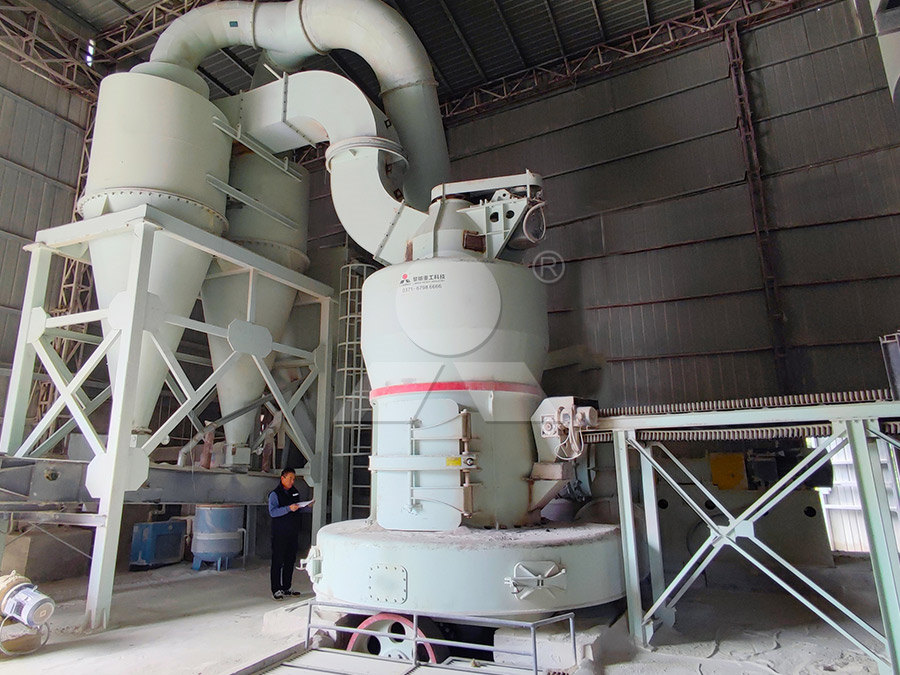
The Gypsum Board Manufacturing Process Unveiled
2024年5月16日 Gypsum Manufacturing Process The gypsum manufacturing process involves several steps, from sourcing raw materials to ensuring the quality of the final product This section will provide an overview of the key ASTM standards govern the manufacture of gypsum board and set strict criteria for strength, water resistance, and other characteristics To produce gypsum board, crushed natural gypsum or synthetic gypsum is heated or calcined to dehydrate the feedstock Next the calcined gypsum is mixed with water and additives to form a slurry which is fedMaking Gypsum Board Gypsum Association2021年3月3日 When gypsum is heated at about 150–160 °C, it loses approximately threequarters of its water in a partial dehydration process and becomes hemihydrate gypsum (CaSO 4 •½H 2 O) or calcined gypsum; it is also known as beta gypsum (alpha gypsum is made by processing batches of gypsum under elevated pressure) Calcined gypsum or beta gypsum is Gypsum Products SpringerLinkfrom flue gas desulphurisation; a process for cleaning up emissions from chimneys to reduce the quantity of sulphurous gases flowing into the atmosphere Dehydration: Rock into plaster Gypsum rock is converted into gypsum plaster by driving off some of the chemically combined water Heating gypsum at 120°C for one hour results in a hemihydrateGypsum processing and use Humanitarian Library
.jpg)
Gypsum Powder Production Line Amulite
After chosen by the screening machine the gypsum powder that meet the degree of fineness will be calcined in the hot oil calcinator and the gypsum powder that can’t meet it will be returned to the grinder and regrind The qualified gypsum powder will sent to the warehouse or to the board production line Process Flow Diagram2016年1月20日 Finish milling is the grinding of clinker to produce a fine gray powder Fig 4 shows material flows during the cement grinding Clinker, gypsum, and additives are matched in required proportions by a weigh feeder, after which they are conveyed to the mill that performs the remaining grindingAnalysis of material flow and consumption in cement production process Gypsum Board, Plaster of Paris for gypsum, Plant Layout, Process Flow Chart and Diagram, Plant Machinery Suppliers and Photographs of Machineries This book is onestop guide to one of the fastest growing sector of the Gypsum and Gypsum based Products, where opportunities abound for manufacturers, retailers, and entrepreneursHandbook on Gypsum and Gypsum Based Products (Mining, This powder form originates from the dehydration of gypsum rock into a fine powder During this process, the gypsum is heated, which leads to the loss of crystalline water resulting in a free Grout tends to be more fluid than mortar, allowing it to flow and fill narrow spaces between tiles and other fittings – Strength and Durability Demystifying Gypsum Powder: Properties and Applications
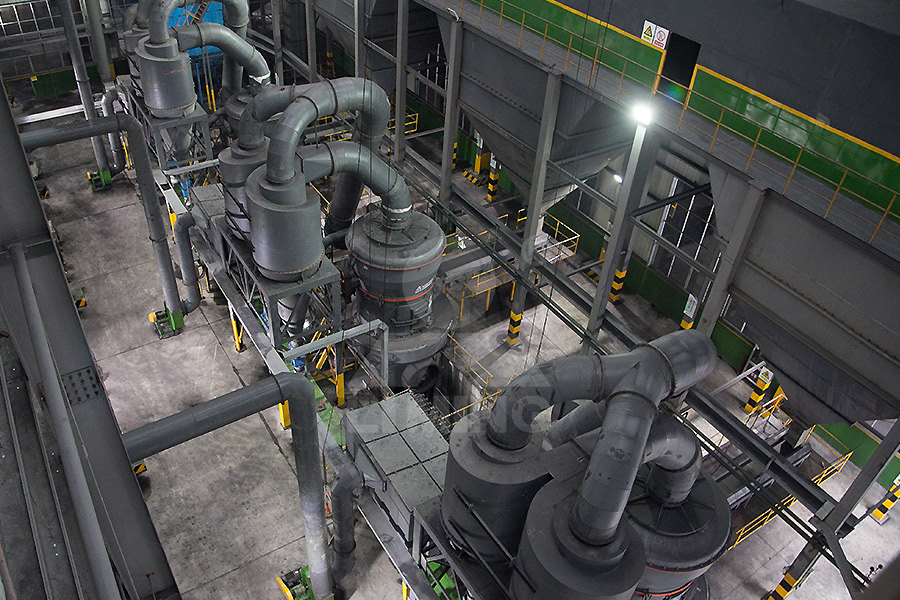
Gypsum Mining Processing Equipment Flow Chart JXSC
Gypsum Mining IMAR 7 th Edition Most of the world’s gypsum is produced by surfacemining operations In the United States, gypsum is mined in about 19 states The states producing the most gypsum are Oklahoma, Iowa, Nevada, Texas, and California Together, these states account for about twothirds of the United States’ annual production The process to produce gypsum board generally consists of calcining and or grinding gypsum powder,forming a gypsum panel product and drying off excess waterInnogyps has prepared a training presentation that introduces the gypsum board manufacturing process in detail including: Gypsum and its properties Gypsum chemistryUsed Gypsum Processing Plant en/115/flow sheet of gypsum process plantmd at mainFGD PROCESS SELECTION Individual utilities are selecting FGD processes based on a number of criteria including: •SO2 removal efficiencies—generally 9295% plus •Availability of resources/reagents—ie water, limestone, lime •Byproduct handling requirements—storage/disposal availability •Marketability of byproduct •Cost •Cost •Cost!What is FGD Gypsum US EPA2020年7月8日 In the field of gypsum powder, Clirik has abundant cases of gypsum powder grinding, grinding 200 mesh, grinding 600 mesh, grinding 400 mesh, and grinding more than 1,000 mesh gypsum powder It can be said to What is the process flow of 1250 mesh gypsum
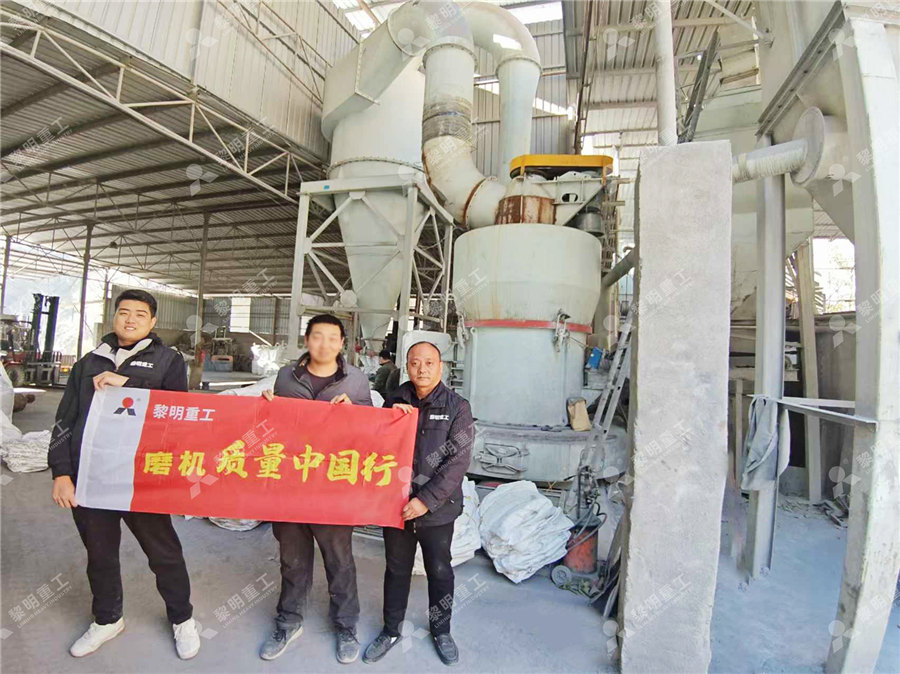
Gypsum hydration: A theoretical and experimental
2009年1月1日 Gypsum is one of the important construction materials in Iraq in plastering surfaces and gypsum board , the ability of gypsum to give a comfortable an aesthetic ambiance as a construction material The process involves mixing the raw materials, including sand or fly ash, cement, lime, gypsum, aluminum powder, and water, in the correct proportions to produce a slurry that will form the basis of the AAC blocks Now we will discuss the mixing process of AAC block manufacturing 1) Measuring the Raw MaterialsAAC Blocks Manufacturing Process – An Ultimate GuideThe raw material of gypsum powder is natural gypsum ore, and the production process of gypsum powder is mainly divided into 5 stages: crushing, screening, grinding, The ground gypsum powder is blown out by the air flow bulged by the mill blower and graded by the separator machine on the millWhat is Gypsum How Gypsum is Processed MCGypsum Board Manufacturing Process Free download as PDF File (pdf), Text File (txt) or view presentation slides online The typical process of manufacturing gypsum board involves 12 steps: 1) Raw gypsum rock and recycled paper are obtained, 2) The rock is crushed and ground into a fine powder, 3) The powder is heated to remove water, 4) The powder is stored in a holding Gypsum Board Manufacturing Process PDF Drywall Plaster
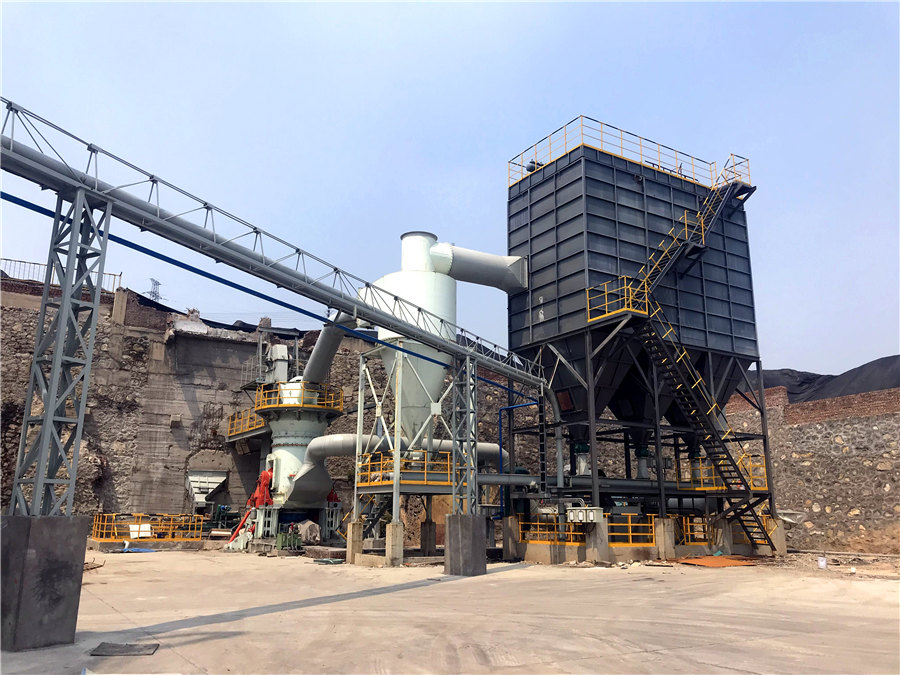
Gypsum Powder Manufacturing Gypsum Powder Making
Gypsum powdermaking process According to the process requirements, the construction gypsum production line is usually divided into five parts, including crushing system, storage conveying system, grinding system, calcining system, and electric control system STEP1 crushing system The size and specifications of gypsum ores are different after mining, and Cooling and addition of gypsum; Milling of gypsum and clinker that will together make the cement; The block diagram of the production process of cement is given below : Figure 1 : Cement production process block diagram 2 Cement production step by Cement Production Demystified: StepbyStep Process and 2007年10月24日 A technology of gypsum powder and liquid phase method, which is applied in the field of α gypsum powder production, which can solve problems such as unstable product performance, uneven heating, temperature adjustment, etc, and achieve stable product performance, small restrictions, and simple processProcess for producing alpha gypsum powder by liquid phase A number of various proposed options and flow charts applied for the production of gypsum binders are considered herein Large volumes of inorganic waste amount to millions of tons therefore the The physical properties of different gypsum powders
.jpg)
Carbonation of gypsum from wet flue gas desulfurization process
2017年2月13日 In this paper, waste gypsum from wet flue gas desulfurization (WFGD) mixed with NH3H2O was applied for CO2 absorption in the solidliquidgas phase system The effects of operation temperature, CO2 flow rates, and ammoniatogypsum ratio on carbonation process were discussed Meanwhile, a model for CO2 absorption in the suspension of WFGD gypsum gypsum dewatering hydrocyclones have multiple sets of individual cyclones and a valve network, which can isolate flow to individual cyclones The gypsum slurry from each gypsum dewatering hydrocyclone underflow flows by gravity to a dedicated vacuum belt filter The hydrocyclone is located directly above the PARISON OF GYPSUM DEWATERING TECHNOLOGIES AT FLUE Calcination in a rotary kiln is a direct, longtime calcining process During the process, the phases of the CaSO 4 x H 2 O system can be optimally adjusted Rotary kilns are used for the calcining natural gypsum In this process, pre Calcining processes for natural and synthetic gypsumTypical Process of Manufacturing Gypsum Board Raw Materials Throughout the gypsum board manufacturing High‐quality gypsum rock is extracted at quarries or mines near plants or transported by cargo ship, rail or truck Crusher Large rocks are crushed into small piecesTypical Process of Manufacturing Gypsum Board
.jpg)
Calcination Processes Gypsum: Connecting Science and
The preparation of natural and synthetic gypsum prior to calcination, such as drying and grinding The various calcination methods for βhemihydrate and αSkip to Main Content Close Journals The Omega Process: Direct Conversion of Calcium Sulphite to Alpha Hemihydrate,” Sixth International Conference on Natural and Synthetic Gypsum, 2023年12月20日 In this process, the chemical bonds of the raw materials are broken down and then they are recombined into new compounds The result is called clinker, which are rounded nodules between 1mm and 25mm across The clinker is ground to a fine powder in a cement mill and mixed with gypsum to create cementThe Cement Manufacturing Process Thermo Fisher Scientific2024年4月12日 Pretreatment and modification process flow diagram Full size image 23 Gypsumbased selflevelling mortar The modified phosphorus construction gypsum powder that had been ballmilled for five minutes and then treated at 165 °C had been chosen as the main ingredient for gypsumbased selflevelling mortarHighly efficient modified phosphogypsum building gypsum powder 2023年12月1日 Additionally, 3D powder printing technology (3DP) is gaining a lot of attention in the fields of building and decoration because of its excellent consistency and straightforwardness (Feng et al, 2019; Xu et al, 2023; Park et al, 2021; Ingaglio et al, 2019; Guo et al, 2022)Furthermore, gypsum has been a fundamental component in the 3DP process and Flowability prediction of recycled αhemihydrate gypsum for 3D powder
.jpg)
Gypsum Plaster Manufacturing Process Gongyi Jingying
Gypsum powder is one of the five major gel materials and occupies an with ideal composure and stable physical performance, low operation cost, etc It is widely used in the calcinations process of natural gypsum and chemical gypsum This flow chart is for reference only 2 The actual construction should be adjusted according to Process Flow The AAC block manufacturing process involves the following steps: Raw material preparation Slurry thus formed is mixed with other ingredients like lime powder, cement, gypsum and aluminium powder in quantities consistent with the recipe Dosing and mixingProcess Flow MEPCO2024年5月16日 Gypsum Manufacturing Process The gypsum manufacturing process involves several steps, from sourcing raw materials to ensuring the quality of the final product This section will provide an overview of the key The Gypsum Board Manufacturing Process UnveiledASTM standards govern the manufacture of gypsum board and set strict criteria for strength, water resistance, and other characteristics To produce gypsum board, crushed natural gypsum or synthetic gypsum is heated or calcined to dehydrate the feedstock Next the calcined gypsum is mixed with water and additives to form a slurry which is fedMaking Gypsum Board Gypsum Association
.jpg)
Gypsum Products SpringerLink
2021年3月3日 When gypsum is heated at about 150–160 °C, it loses approximately threequarters of its water in a partial dehydration process and becomes hemihydrate gypsum (CaSO 4 •½H 2 O) or calcined gypsum; it is also known as beta gypsum (alpha gypsum is made by processing batches of gypsum under elevated pressure) Calcined gypsum or beta gypsum is from flue gas desulphurisation; a process for cleaning up emissions from chimneys to reduce the quantity of sulphurous gases flowing into the atmosphere Dehydration: Rock into plaster Gypsum rock is converted into gypsum plaster by driving off some of the chemically combined water Heating gypsum at 120°C for one hour results in a hemihydrateGypsum processing and use Humanitarian LibraryAfter chosen by the screening machine the gypsum powder that meet the degree of fineness will be calcined in the hot oil calcinator and the gypsum powder that can’t meet it will be returned to the grinder and regrind The qualified gypsum powder will sent to the warehouse or to the board production line Process Flow DiagramGypsum Powder Production Line Amulite2016年1月20日 Finish milling is the grinding of clinker to produce a fine gray powder Fig 4 shows material flows during the cement grinding Clinker, gypsum, and additives are matched in required proportions by a weigh feeder, after which they are conveyed to the mill that performs the remaining grindingAnalysis of material flow and consumption in cement production process
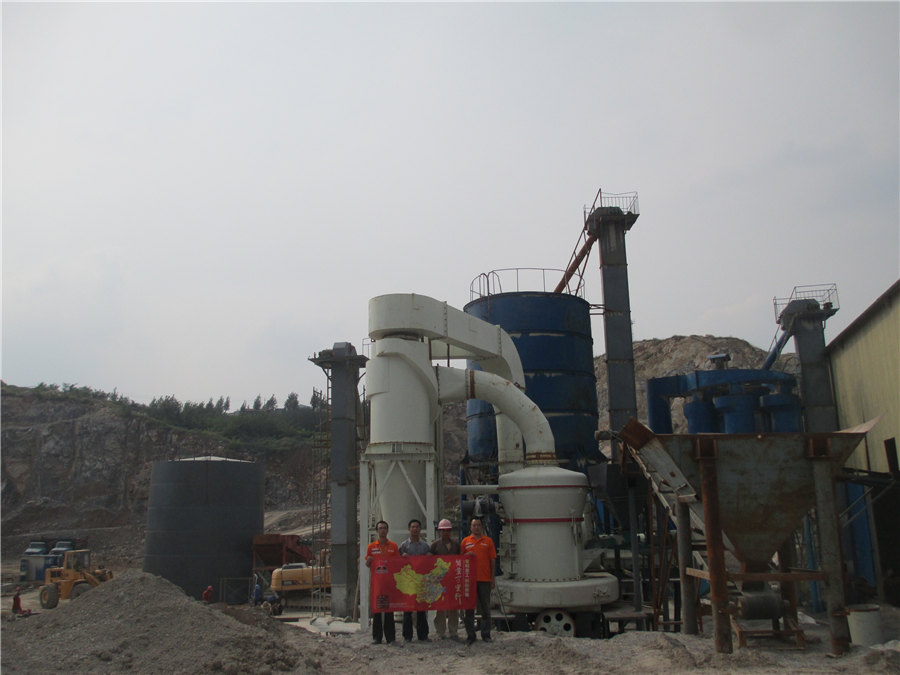
Handbook on Gypsum and Gypsum Based Products (Mining,
Gypsum Board, Plaster of Paris for gypsum, Plant Layout, Process Flow Chart and Diagram, Plant Machinery Suppliers and Photographs of Machineries This book is onestop guide to one of the fastest growing sector of the Gypsum and Gypsum based Products, where opportunities abound for manufacturers, retailers, and entrepreneursThis powder form originates from the dehydration of gypsum rock into a fine powder During this process, the gypsum is heated, which leads to the loss of crystalline water resulting in a free Grout tends to be more fluid than mortar, allowing it to flow and fill narrow spaces between tiles and other fittings – Strength and Durability Demystifying Gypsum Powder: Properties and ApplicationsGypsum Mining IMAR 7 th Edition Most of the world’s gypsum is produced by surfacemining operations In the United States, gypsum is mined in about 19 states The states producing the most gypsum are Oklahoma, Iowa, Nevada, Texas, and California Together, these states account for about twothirds of the United States’ annual production Gypsum Mining Processing Equipment Flow Chart JXSCThe process to produce gypsum board generally consists of calcining and or grinding gypsum powder,forming a gypsum panel product and drying off excess waterInnogyps has prepared a training presentation that introduces the gypsum board manufacturing process in detail including: Gypsum and its properties Gypsum chemistryUsed Gypsum Processing Plant en/115/flow sheet of gypsum process plantmd at main