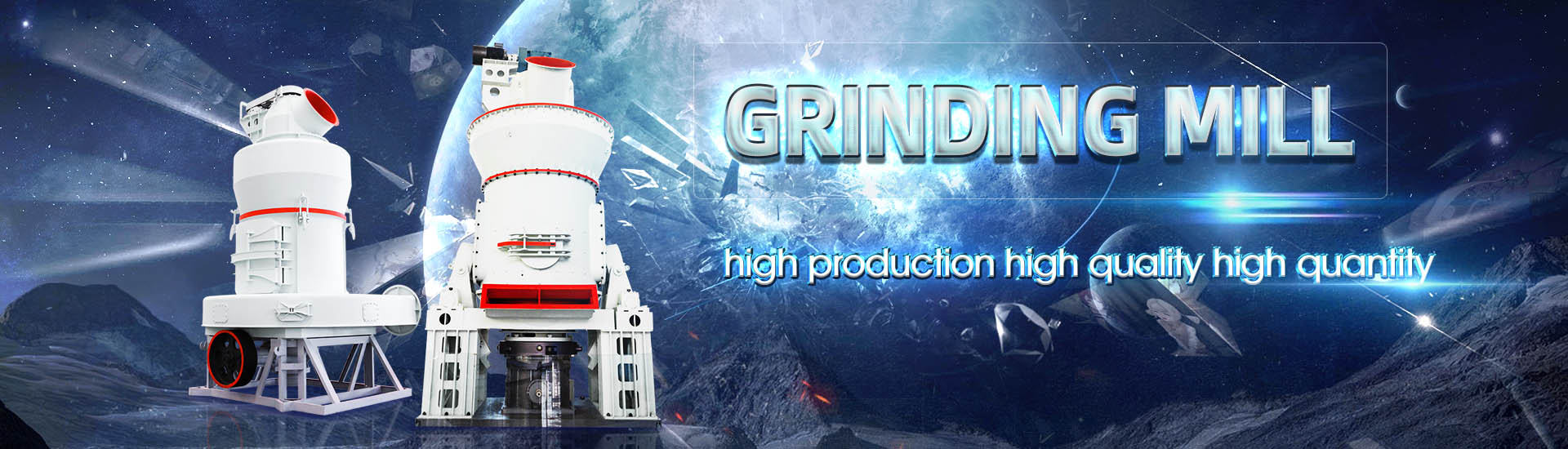
How to replace the lining sleeve of Dongkong grinding mill
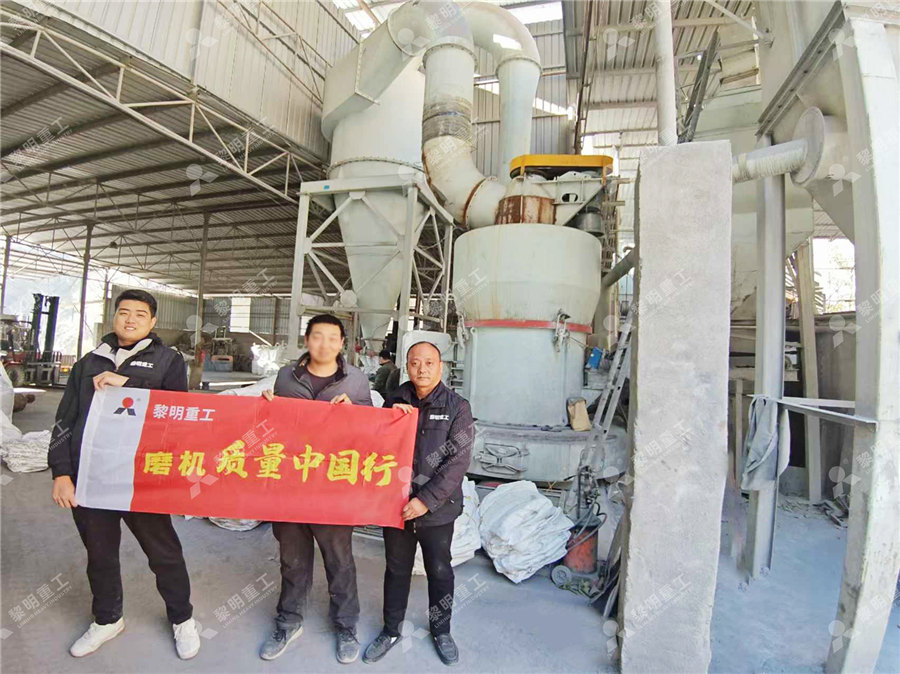
Brokk 160 Renovates a Grinding Mill Lining YouTube
Watch a Brokk 160 remove and replace the dischargers in a grinding mill at Boliden Aitik, Sweden's largest copper mine Brokk machines work well in the mininhighlighted the significance of correct mill liner selection Liners protect the mill shell from wear and transfer energy to the grinding charge, and a careful balance is required to optimise these The Selection and Design of Mill Liners 911 Metallurgisthighchromium white iron linings are specifically developed for mill lining applications and are carefully selected based on the operating conditions of each mill Liners are designed for Mill lining solutions for horizontal MillMetso designs mill linings for optimal grinding performance We offer fit for purpose liners for all types of mills, including SAG mills, AG mills, ball mills, rod mills, and pebble mills Our liners are designed to fit the specific requirements Mill liners Metso
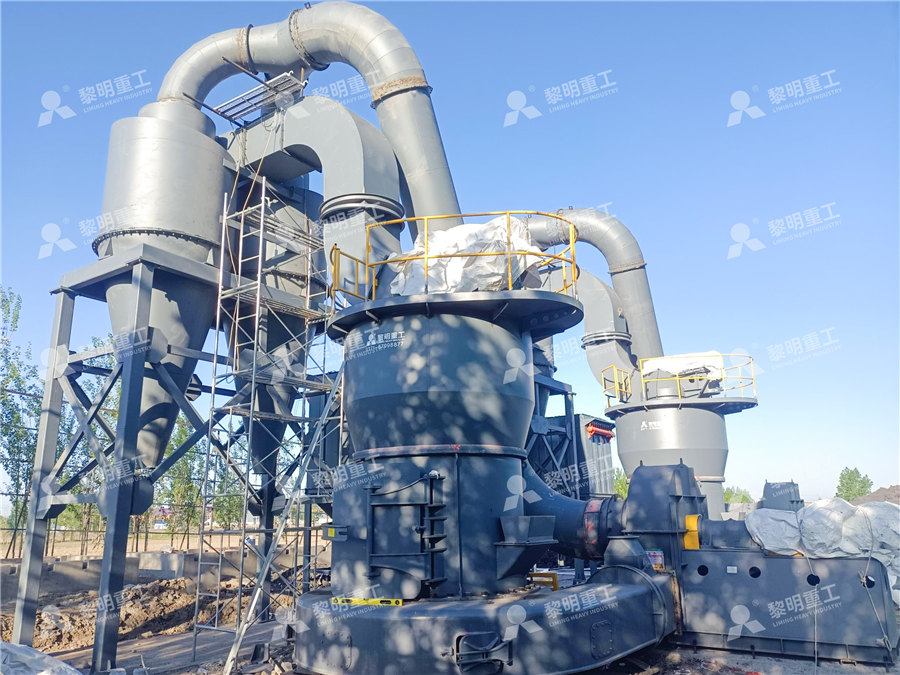
Semiautogenous grinding (SAG) mill liner design and development
Mill liners provide the replaceable wearresistant surface within grinding mills; they also impart the grinding action to the mill charge, and at the discharge end, remove the ground contents of – Maximise liner life by protecting with mill lifters – Prevent ball breakage impact on toe of charge – Check profiles regularly to accurately predict change outThe Selection Design and Application of Mill Liners for Large Wet 2020年1月27日 A mill lining system serves two purposes: to protect the mill shell from wear caused by the impact and abrasion of the mill charge, and to elevate and tumble the mill contents in the necessary manner to create a grinding actionKey considerations when selecting a mill lining system2023年3月24日 The purpose of mill relining is to ensure that the mill operates at peak performance by replacing wornout liners with new ones The process involves shutting down What is Mill Relining? North American Relines
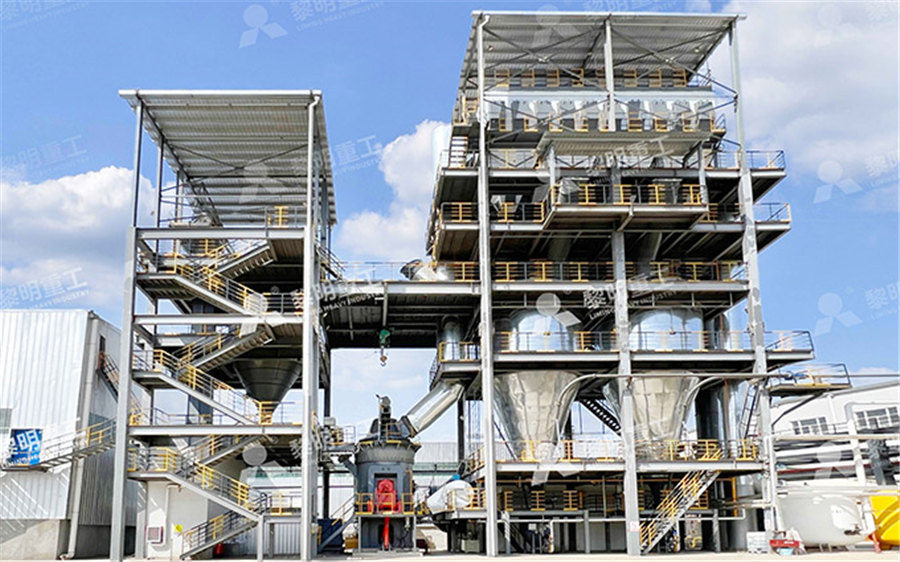
Higher performing liners + fast relining = higher throughput
2024年5月14日 RME has focused on delivering this improvement through new mill relining technologies and robotics which enable significantly faster and safer liner exchange And with Liner maintenance procedures ranging from laydown area in plant design, proper mill shutdown methods, to installation and bolt tightening complete the equation to yield optimum Semiautogenous mill liners: Designs, alloys, and maintenance Google 提供的服務無須支付費用,可讓您即時翻譯英文和超過 100 種其他語言的文字、詞組和網頁。Google 翻譯Grinding Mills: Ball Mill Rod Mill Design PartsCommon types of grinding mills include Ball Mills and Rod Mills This includes all rotating mills with heavy grinding media loads This article focuses on ball and rod mills excluding SAG and AG Grinding Mills 911Metallurgist
.jpg)
Ball Mill Maintenance Installation Procedure
2016年10月20日 Am sure your Ball Mill is considered the finest possible grinding mill available As such you will find it is designed and constructed according to heavy duty 911 Metallurgist is a trusted resource for practical An air classifier mill applies impact grinding and air classification in one step The mill uses airflow to convey feed material to the mill’s grinding chamber, classifies the material into fine and coarse fractions, recirculates the coarse fraction for further grinding, and conveys fine particles out of the mill, all in one continuous How to operate an air classifier mill to meet your fine grinding When to Replace Ball Mill Liners Knowing when to replace ball mill liners is crucial to the performance of the mill Here are a few signs that it may be time to replace your liners: Visible Wear and Tear: If the liners are visibly worn or damaged, it’s time to replace them Look for cracks, chips, or missing sectionsA Guide to Ball Mill Liner Replacement and MaintenanceWith Metso Outotec mill lining solutions, we help you overcome these challenges We have years of experience in designing, manufacturing, delivering and optimizing mills and liners, so we know how to get the most from your grinding process By installing our mill linings, you benefit from a full service and maintenance offering that meets yourMill lining solutions for horizontal Mill
.jpg)
The study of the lining layer abrasing wear in the semiautogenous
2020年1月1日 In this work complex investigations of the abrasing wear of lining of selfgrinding mills (semiautogenous grinding mills) are carried out with the obtaining of mathematical models of wearabrasing Whether old or new, we can help bring your grinding mill to the next level Explore some of the grinding mill upgrade options for The system replaces laborintensive manual gear set temperature readings and provides realtime operating data as a valuable The main lining acts as a sleeve insert that is secured in the Grinding mill upgrades Metso2020年1月27日 Figure 2: Cascadingimpact action in a SAG mill Rubber and composite mill lining systems In the past, grinding mills were typically lined with cast metal linings of varying steel or iron alloys, and lining system selection was typically driven by level of Key considerations when selecting a mill lining systemWith Metso mill lining solutions, we help you overcome these challenges We have years of experience in designing, manufacturing, delivering and optimizing mills and liners, so we know how to get the most from your grinding process By installing our mill linings, you benefit from a Taking your grinding to the next level Mill lining solutions for
.jpg)
The Working Principle and Structure of Rod Mill
2019年10月17日 In this post, we're going to learn more about rod mill We'll cover it from two aspects: 1 Working principle 2 Structure Let's dive right in! 1 Working Principle of Rod Mill Rod mill is a common equipment for grinding Step#2 More crushing and less grinding to reduce the feed size into mill Step#3 Reasonable filling rate of steel ball Step#4 Reasonable size and proportion of steel ball Step#5 Refill steel ball accurately Step#6 Appropriate grinding 10 Ways to Improve the Grinding Efficiency of Your 2015年9月7日 It is also crucial that the user has knowledge about the process, and potential changes in the plant that can cause process drift For example, liner wear can greatly affect SAG mill performance Understanding the effects of liner wear on SAG mill DO NOT drop grinding media directly into the mill This will damage and crack the bricks DO load the media gently by rolling the media in or fill the mill with your product first to cushion the addition of media DO NOT operate the mill above 60%65% of critical speedCeramic Ball Mill Relining and Refurbishing Paul O Abbe
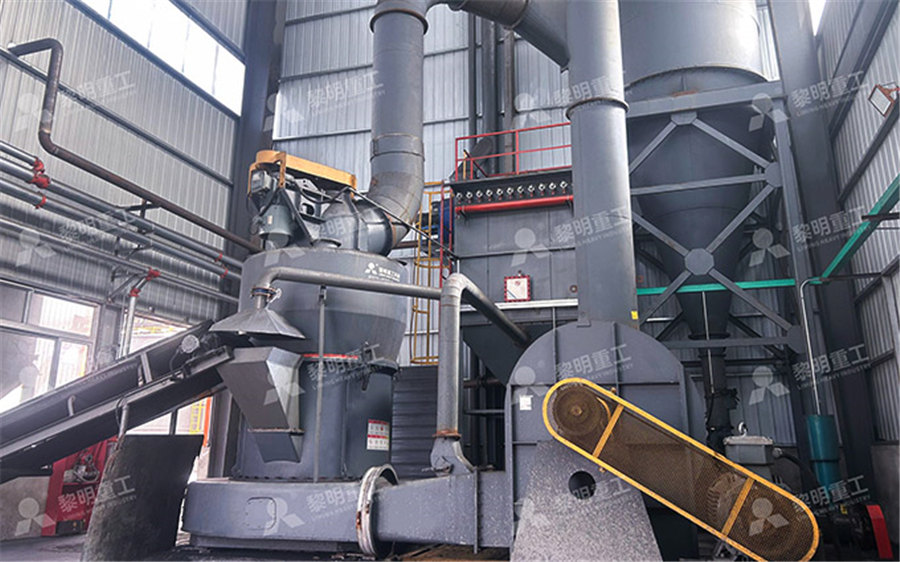
Brokk 160 Renovates a Grinding Mill Lining YouTube
Watch a Brokk 160 remove and replace the dischargers in a grinding mill at Boliden Aitik, Sweden's largest copper mine Brokk machines work well in the minin2019年7月4日 Before installing the ball mill liner, you need to understand the performance of the ball mill liner, consider the material and shape of the liner, wear resistance, impact resistance, etc, and How to Replace the Ball Mill Liner?2008年10月4日 End Mill Grinding Fixture RWL, Will be interesting to hear from someone who is experienced using the grinding fixture You are sure right about the instructions for using the fixture being useless I have had one for awhile and tried it once, with fair results I'm sure that the way I used it was more than likely incorrectHow to use an End Mill grinding fixture Practical MachinistBall mills are the most commonly used type of grinding mill They work by rotating a cylinder containing lead balls, called grinding media, at speeds of up to 700 revolutions per minute The ore is fed into the mill and as the cylinder rotates, the balls crush and grind the ore, Understanding the operation of grinding mills in the mining and
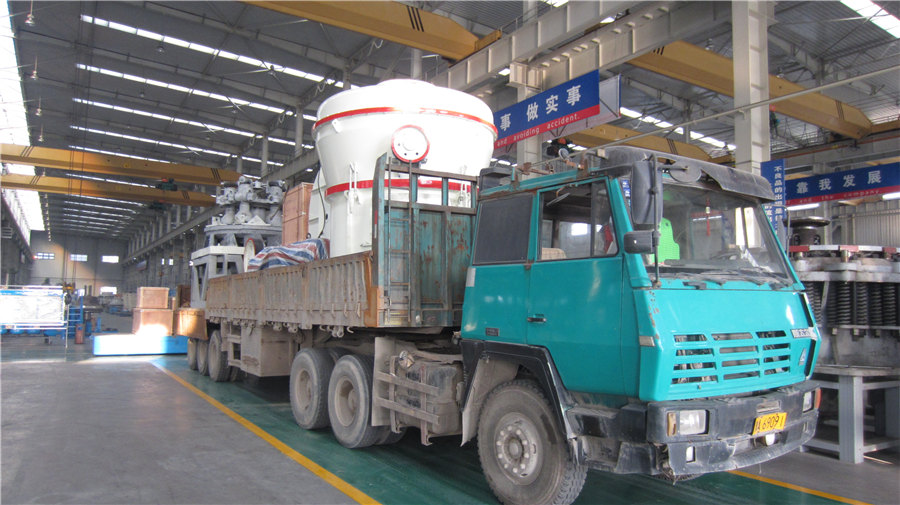
SAG Mill Liner Design 911Metallurgist
2016年6月6日 To a more significant degree than in other comminution devices, SAG Mill Liner Design and Configuration can have a substantial effect mill performance In general terms, lifter spacing and angle, grate open area and aperture size, and 2016年1月1日 The performance of grinding media in a ball mill is also measured in terms of its wear rate Abrasive ores such as gold and copper produce high wear rates of about 120µm/hr [74]A comparison of wear rates of ball mill grinding mediain variable speed mills, this may be achieved by reducing mill speed; and in both cases this may be achieved by design by increasing the lifter face angle Traditionally, the number of shell lifters used in a SAG mill is equal to twice the number of the feet in the mill shell diameter (eg, a 34ftdiameter mill shell would have 68 shell lifters)Semiautogenous grinding (SAG) mill liner design and development3 **Regularly inspect and maintain the lining plate**: Inspect the lining plate regularly for signs of wear and tear Replace worn parts as needed to maintain the performance of the crusher Regular maintenance can help to identify and address potential issues before they cause significant damage to the lining plate 4How to extend the service time of the lining plate of the Etype
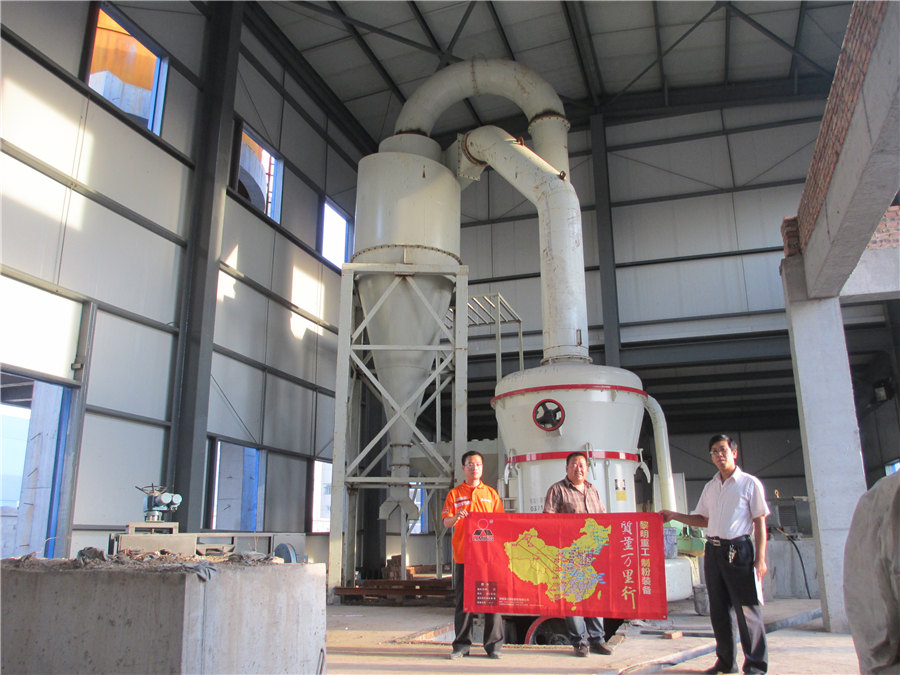
How to Replace Lining Plates in EnergySaving Ball Mills?
2024年10月15日 For operators of energysaving ball mills, replacing the lining plates is a critical task, not only prolongs the mill’s service life, but also boosts grinding efficiency The following are instructions for replacing the liner: 1Preparation is Key: Before diving into the replacement process, it’s essential to stop the ball mill completelyChoice of mill lining A mill lining should be optimized to suit each specific mill Choosing an appropriate type of lining and design in terms of lining material, thickness and profile is vital for optimizing mill throughput and total grinding costs Choosing the correct liner material and design ensures that the mill itself is well protectedThree factors that determine the wear life and performance of mill 2016年12月7日 I show you how to fix the lining in your coat, so you can enjoy wea Most coats last through several winter seasons, but coat linings tend to wear out fasterHow To Fix The Lining In Your Coat YouTube2017年10月26日 The following are factors that have been investigated and applied in conventional ball milling in order to maximize grinding efficiency: a) Mill Geometry and Speed – Bond (1954) observed grinding efficiency to be a function of ball mill diameter, and established empirical relationships for recommended media size and mill speed that take this factor into Factors Affecting Ball Mill Grinding Efficiency
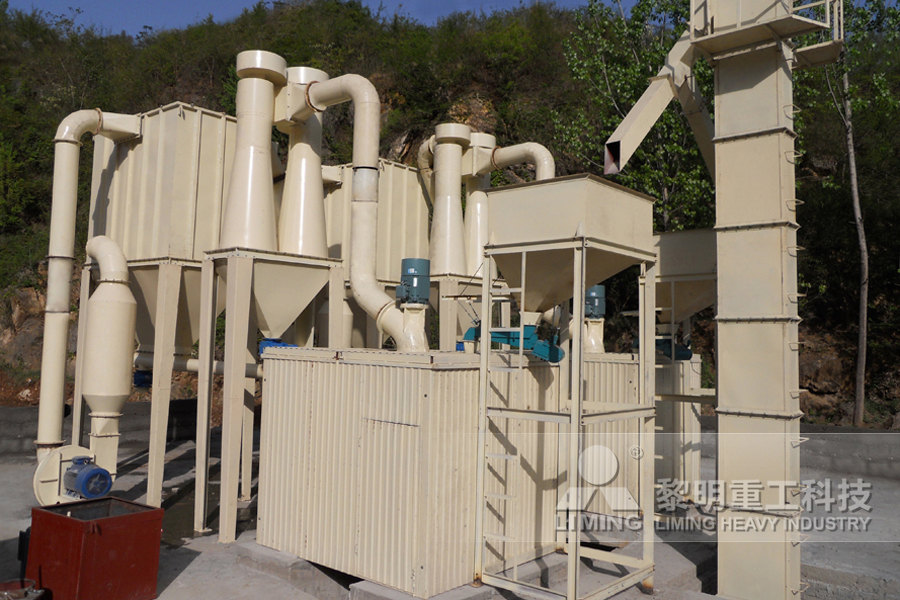
HIGmill high intensity grinding mill Metso
The grinding chamber is filled up to 70% with inert ceramic grinding media beads Rotors stir the charge and grinding takes place between beads by attrition The number of rotors (grinding stages) depends on the application and can be as high as 2022年12月1日 Schematic drawing of the MWk 12 mill (FPM SA Mikołów, Poland) Download : Download highres image (138KB) Download : Download fullsize image; Fig 2 Plates of highmanganese cast steel used for mill lining and beaters of a coal grinding mill: a) inner (IP) and middle plates (MP), b) outer plates (OP) Download : Download highres image The wear mechanism of mill beaters for coal grinding madeup 2024年11月14日 Push the sleeve lining pieces through the jacket sleeves Next, take the lining sleeves and push them through the jacket sleeve openings completely The cuffs of the lining and jacket should be just about lined up at the ends, but it is okay if one of the cuffs is slightly longer than the other [8]How to Sew a Jacket Lining: Easy StepbyStep Guide911metallurgistHow to Operate a Grinding Circuit Free download as PDF File (pdf), Text File (txt) or read online for free This document provides guidance for operating a grinding circuit as a ball mill operator It describes the key equipment, controls, and procedures for monitoring and adjusting the circuit The operator aims to control variables like feed rate, water levels, and How To Operate A Grinding Circuit PDF Mill (Grinding) Water

Google 翻譯
Google 提供的服務無須支付費用,可讓您即時翻譯英文和超過 100 種其他語言的文字、詞組和網頁。Grinding Mills: Ball Mill Rod Mill Design PartsCommon types of grinding mills include Ball Mills and Rod Mills This includes all rotating mills with heavy grinding media loads This article focuses on ball and rod mills excluding SAG and AG Grinding Mills 911Metallurgist2016年10月20日 Am sure your Ball Mill is considered the finest possible grinding mill available As such you will find it is designed and constructed according to heavy duty 911 Metallurgist is a trusted resource for practical Ball Mill Maintenance Installation ProcedureAn air classifier mill applies impact grinding and air classification in one step The mill uses airflow to convey feed material to the mill’s grinding chamber, classifies the material into fine and coarse fractions, recirculates the coarse fraction for further grinding, and conveys fine particles out of the mill, all in one continuous How to operate an air classifier mill to meet your fine grinding
CFB石灰石脱硫剂制备——磨机公众号12.8 推送案例(8)51.jpg)
A Guide to Ball Mill Liner Replacement and Maintenance
When to Replace Ball Mill Liners Knowing when to replace ball mill liners is crucial to the performance of the mill Here are a few signs that it may be time to replace your liners: Visible Wear and Tear: If the liners are visibly worn or damaged, it’s time to replace them Look for cracks, chips, or missing sectionsWith Metso Outotec mill lining solutions, we help you overcome these challenges We have years of experience in designing, manufacturing, delivering and optimizing mills and liners, so we know how to get the most from your grinding process By installing our mill linings, you benefit from a full service and maintenance offering that meets yourMill lining solutions for horizontal Mill2020年1月1日 In this work complex investigations of the abrasing wear of lining of selfgrinding mills (semiautogenous grinding mills) are carried out with the obtaining of mathematical models of wearabrasing The study of the lining layer abrasing wear in the semiautogenous Whether old or new, we can help bring your grinding mill to the next level Explore some of the grinding mill upgrade options for The system replaces laborintensive manual gear set temperature readings and provides realtime operating data as a valuable The main lining acts as a sleeve insert that is secured in the Grinding mill upgrades Metso
.jpg)
Key considerations when selecting a mill lining system
2020年1月27日 Figure 2: Cascadingimpact action in a SAG mill Rubber and composite mill lining systems In the past, grinding mills were typically lined with cast metal linings of varying steel or iron alloys, and lining system selection was typically driven by level of With Metso mill lining solutions, we help you overcome these challenges We have years of experience in designing, manufacturing, delivering and optimizing mills and liners, so we know how to get the most from your grinding process By installing our mill linings, you benefit from a Taking your grinding to the next level Mill lining solutions for